
388
.pdf4.ГРУЗОПОДЪЕМНЫЕ МАШИНЫ
4.1.Башенные краны
Башенные краны применяют в качестве одного из основных грузоподъемных устройств в жилищном и промышленном строительстве.
Эти краны делятся на передвижные, передвигающиеся по прямолинейным наземным или криволинейным рельсовым путям; стационарные приставные, прикрепляемые к возводимому объекту; вертикальные подвижные самоподъемные.
Башенные краны различают по типу башен - на краны с поворотной башней и неповоротной с поворотным оголовком, а также по типу конструкции стрелы - на краны с подъемной стрелой и балочной стрелой.
Передвижные башенные краны различают по типу ходового оборудования: рельсовые, автомобильные, пневмоколесные, гусеничные.
Эксплуатационная сменная производительность башенного крана (т/см) определяется по формуле:
Пэ.см= Q * nц* kг*kв,
где Q - грузоподъемность крана, т; nц - число циклов за 1 час работы;
kг - коэффициент использования крана по грузоподъемности; kв- коэффициент использования крана по времени за смену
(kв= 0,75...0,8).
Число циклов в час определяется по формуле:
пц = 60 / Тц,
где Тц - продолжительность одного цикла, мин:
Тц=Тм + Тр,
где Тм,Тр- соответственно продолжительность всех операций,
31
выполняемых машиной (машинное время) и время, затрачиваемое на выполнение ручных операций, мин.:
Тм=tв+tпов+tп; Тр = tc + ty;
где tв - время вертикального перемещения крюка, мин; tпов- время на поворот стрелы, мин;
tп- время передвижения крана, мин;
tc - время, затрачиваемое на строповку груза, мин;
ty - время, затрачиваемое на установку в рабочее положение и отсоединение грузозахватных приспособлений, мин.
Время вертикального перемещения крюка:
tв = H’/v1 + H”/v2,
где Н’, Н” - соответственно, длина пути крюка при подъеме и опускании, м;
v1, v2 - соответственно, скорость подъема и опускания крюка, м/мин.
Время на поворот стрелы:
tпов = 2 * α / 360 * n ,
где α - угол поворота стрелы в одну сторону, град (а = 120°); n- частота вращения поворотной части крана, мин-1.
Время передвижения крана:
tп= L / vn,
где L - путь передвижения крана, м;
vn - скорость передвижения крана, м/мин.(18-30 м/мин.).
Коэффициент использования крана по грузоподъемности:
kr = Qcp.в/ Q,
где Qcp.в- средневзвешенная грузоподъемность крана, т:
Qcp.в= ∑
где Qi - средняя нагрузка при каждом цикле, т;
mi- процентное содержание одинаковых средних значений нагрузки в течение смены (табл. 23), %.
32
Таблица 23
Процентное содержание
Доля грузоподъемности Qj, т |
0.2*Q |
0.4*Q |
0.6*Q |
0.8*Q |
Q |
|
|
|
|
|
|
mi,% |
8 |
18 |
36 |
28 |
12 |
Годовая выработка крана:
Пгод=Пэ.ч.* Тгод,
где Пэ.ч- эксплуатационная часовая производительность крана, т/ч; Тгод- рабочее время крана в течение года, ч;
Пэ.ч.= Пэ.см./Тсм.год,
Тгод = Тсм. * hсм*(365 - (T1 + Т2+ Т3+ Т4)),
где hсм - среднее число смен работы в сутки в течение года; Т1 - выходные, праздничные дни; Т2 - число дней простоев по метеорологическим причинам
(сильный ветер, мороз, дождь, туман); Т3 - время перебазировки крана, сут.;
Т4 - затраты времени на ремонтные работы, сут.; Тсм.год- средняя продолжительность смены работы крана в течение года, час.
Задача 8
Определить эксплуатационную сменную и годовую производительность башенного крана.
Исходные данные:
Номер |
Q, т |
H’=H”, м |
L, м |
Vl, |
V2, |
n, мин- |
tc, |
tу, |
варианта |
|
|
|
м/мин |
м/мин |
1 |
мин |
мин |
|
|
|
|
|||||
|
|
|
|
|
|
|
|
|
1 |
5 |
21 |
32 |
20 |
31 |
0,7 |
1,2 |
8 |
2 |
4 |
24 |
24 |
26 |
30 |
0,6 |
1,0 |
7 |
3 |
5 |
30 |
18 |
28 |
18 |
0,5 |
0,8 |
6 |
4 |
4 |
22 |
23 |
26 |
30 |
0,7 |
1,2 |
8 |
5 |
5 |
31 |
32 |
20 |
31 |
0,6 |
1,0 |
6 |
33
4.2.Самоходные стреловые краны
Самоходные стреловые краны являются основными машинами, используемыми на монтажных и погрузочноразгрузочных работах.
Подъемные краны выбирают по 3-м параметрам:
a) грузоподъемность крана GK должна соответствовать массе бадьи с бетонной смесью, т.е.:
GK≥(G6.с. + G6),
где: G6.c., G6- соответственно масса бетонной смеси в бадье и масса бадьи (приложение 8. табл. 2), т;
б) необходимая высота подъема Н, м:
H = Hc + h1+h2,
где Нс - высота части бетонируемого сооружения, расположенной выше уровня стоянки крана, м;
h1 - высота бадьи с подъемными приспособлениями, м;
h2 - запас над верхней частью бетонируемого сооружения по условиям производства работ и техники безопасности
(h2 = 1...2 м);
в) требуемый вылет стрелы R, м:
R = Вс + b1 / 2 + b2,
где Вс - ширина зоны части бетонируемого сооружения или всего сооружения, м;
b1- ширина полосы, занимаемой ходовой частью подъемного крана, м;
b2 - запас между краном и бетонируемым сооружением, определяемый конфигурацией котлована, габаритами хвостовой части крана, положением наклоняющейся стрелы крана,
34
условиями безопасности работ, м. Выбирают кран по приложению 8 (табл. 3).
Производительность кранаПк, (м3/ч):
IIK=60*G/tk,
где G = Gб.с. / γб.с - полный объем перемещаемого груза,
м3;
γб.с. - плотность бетонной смеси, т/м3;
tk - продолжительность цикла крана, мин.
В обычных условиях работы продолжительность tk одного цикла кранов составляет 3...4 минуты при грузоподъемности до 2 т; 4.. .6 минут - до 5 т; 6...10 минут - свыше 5 т.
Количество потребных кранов (округляют до целого числа):
nk = Пб.с./Пк,
где Пб.с- количество бетонной смеси, доставляемой за
час работы (часовая производительность бетонного узла), м3/ч:
Пб.с = Пб х nб ,
где Пб - часовая производительность бетоносмесителя,
м3/ч;
nб - число бетоносмесителей.
Пб = Vб*n3/1000,
где V6- объем одного замеса, л (табл.1, приложение 8); n3- число замесов за час (табл.1, приложение 8). Количество автосамосвалов для перевозки бетонной
смеси определяют как в задаче 2. Марку автосамосвала подбирают по приложению 2 (табл. 2).
35
Задача № 9
Подобрать вертикальный транспорт (кран) для бетонной смеси и автотранспорт для ее доставки, определить их количество.
Исходные данные:
варианта |
Плот- |
Марка |
Марка |
Число |
Параметры зоны бетонирования |
|||
ность бе- |
бето- |
бадьи |
бето- |
|
|
|
|
|
тонной |
носме- |
|
носме- |
|
|
|
|
|
смеси, γ |
сителя |
|
сителей, |
Вс, м |
b1,м |
b2,м |
Нс, м |
|
№ |
б.с, т/м3 |
|
|
n6 |
|
|
|
|
|
|
|
|
|
|
|
|
|
1 |
2,0 |
СБ-15 |
БПВ-0,5 |
3 |
4,5 |
2,5 |
2,25 |
7,0 |
2 |
2,1 |
СБ-31 |
БПВ-1,0 |
2 |
3,2 |
3,0 |
2,5 |
70,0 |
3 |
2,2 |
СБ-17 |
БНВ-0,5 |
3 |
8,0 |
3,0 |
3,5 |
11,5 |
4 |
2,3 |
СБ-35 |
БНВ-1,0 |
3 |
4,5 |
3,0 |
4,0 |
16,0 |
5 |
2,4 |
СБ-91А |
БПВ-1,5 |
2 |
7,5 |
4,0 |
4,0 |
18,0 |
36
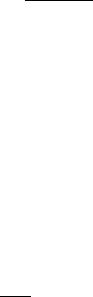
5. МАШИНЫ И ОБОРУДОВАНИЕ ДЛЯ БЕТОННЫХ РАБОТ
5.1.Дробильно-размольное оборудование
Для измельчения каменных материалов применяют камнедробилки (щековые, конусные, валковые, молотковые, ударные), бегуны сухого и мокрого помола, шаровые и стержневые мельницы, а также вибромельницы тонкого помола. Измельчение каменных материалов в дробилках достигается раздавливанием, раскалыванием, изгибом, истиранием, ударом.
В щековых дробилках дробление камня производится раздавливанием, а в некоторых конструкциях частично истиранием между дробящими плитами подвижной и неподвижной щек.
Щековые камнедробилки служат для измельчения пород средней и большой твердости; применяются как на первой, так и на последующих ступенях дробления.
Частота вращения эксцентрикового вала (мин-1) определяется по формуле:
n = 66,5 *√
гдеα - угол захвата (а = 15°...25°);
s - максимальный отход подвижной щеки, м; Производительность щековой дробилки:
П = 60*V*n*µ *γ,
где V - объем призмы материала, выпадающего из дробилки за один отход подвижной щеки, м3;
V = |
|
*h*b, |
|
при:
h= ;
37
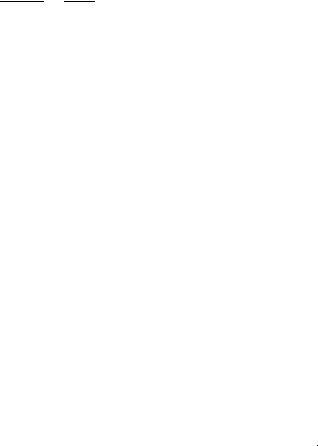
V= * * b;
где е - минимальный зазор между дробящими плитами; b - длина разгрузочного отверстия дробилки;
n - частота вращения эксцентрикового вала, мин-1;
µ - коэффициент разрыхления дробимого материала (µ= 0,3...0,65); Меньшее значение µ применяют при более крупном дроблении;
γ - плотность раздробленного материала, кг/м3 (табл.
24).
|
|
|
|
Таблица 24 |
|
Характеристика горных пород |
|
||
Порода |
|
γ,кг/м3 |
σ,МПа |
Е, МПа |
|
|
|
|
|
Известняк мягкий |
|
1400 |
40…60 |
35000…50000 |
|
|
|
|
|
Песчаник |
|
2000 |
50…80 |
34000…50000 |
|
|
|
|
|
Сланец глинистый |
|
1200 |
25…40 |
11000…19000 |
|
|
|
|
|
Известняк прочный |
|
2700 |
100…120 |
35000…50000 |
|
|
|
|
|
Г ранит мелкозернистый |
|
3300 |
180…200 |
60000…70000 |
|
|
|
|
|
Мощность щековой дробилки
Для дробилок с длиной загрузочного отверстия до 1000
мм мощность определяется по формуле:
N = σ2*n*b* (D2 - d2) / 0,23 * Е,
где σ - предел прочности дробимого материала, МПа
(табл. 24);
n - частота вращения эксцентрикового вала, мин-1;
D - диаметр загружаемых в дробилку камней, м (обычно
D= 0,8...0,9 *а);
а- ширина загрузочного отверстия, м; b - длина загрузочного отверстия, м;
d - диаметр раздробленного материала, м;
dcp.= |
|
- средний диаметр раздробленного мате- |
|
||
риала; |
|
|
|
38 |
d= dcp= |
|
е+0,5s; |
|
Е - модуль упругости дробимого материала, МПа (табл.
24);
Для дробилки длиной загрузочного отверстия более
1000 мм:
N = σ2*n* (D3– d3) / 0,23*Е
Задача № 10
Определить производительность щековой дробилки и еемощность.
Исходные данные
№ |
Дробительный |
α, |
S, мм |
е, мм |
Размер загрузочного отвер- |
|
варианта |
материал |
град. |
|
|
|
стия а*в, мм |
|
|
|
|
|
|
|
1 |
Известняк |
20 |
20 |
35 |
250*400 |
|
|
|
|
|
|
|
|
2 |
Песчаник |
18 |
15 |
60 |
400*600 |
|
|
|
|
|
|
|
|
3 |
Г ранит |
20 |
20 |
180 |
900*1200 |
|
|
|
|
|
|
|
|
4 |
Песчаник |
18 |
25 |
120 |
600*900 |
|
|
|
|
|
|
|
|
5 |
Известняк |
22 |
15 |
40 |
250*900 |
|
|
|
|
|
|
|
|
Приложение |
|
|
|
|
|
|
|
|
|
|
|
|
|
№ Варианта |
|
σ, МПа |
|
|
Е, МПа |
|
|
|
|
|
|
|
|
|
1 |
|
60 |
|
|
35000 |
|
|
|
|
|
|
|
|
2 |
|
80 |
|
|
50000 |
|
|
|
|
|
|
|
|
3 |
|
120 |
|
|
60000 |
|
|
|
|
|
|
|
|
4 |
|
100 |
|
|
50000 |
|
|
|
|
|
|
|
|
5 |
|
70 |
|
|
45000 |
|
|
|
|
|
|
|
В валковых дробилках камень раздавливается и частично истирается в пространстве между вращающимися навстречу друг другу валками.
Максимальная крупность дробимого материала зависит от диаметра дробящих валков, состояния их поверхности и зазора между валками:
-при гладких валках: d = (1/20...1/25) * D + е; -при рифленых валках: d = (1/10...1/12) * D + е;
39

-при зубчатых валках: d = (1/2...1/5) * D + е; Производительность валковой дробилки, м3/ч:
П = 3600 * (е + S) * L * υ * µ,
где е -расстояние между валками;
S - отход подвижного валка (для твердых материалов S = 0,25 *е; для мягких и хрупких материалов S = 0,002...0,004
м);
L -длина валка;
υ -окружная скорость на ободе вала; D -диаметр валка;
µ - коэффициент, учитывающий наличие пустот между камнями
(µ = 0,2...0,5)
υ = π * D * n/60, м/с,
где n -частота вращения валков, об./мин.
n = 308* √ ,
где f - коэффициент трения дробимого материала о поверхность валков;
f = 0,4; г = 0,5*d, м; R = 0,5*D, м.
Задача № 11
Определить производительность валковой дробилки.
Исходные данные
№ вари- |
D, м |
L, мм |
е, мм |
Поверхность |
Дробимый |
γ, кг/м3 |
анта |
|
|
|
валков |
материал |
|
|
|
|
|
|
|
|
1 |
480 |
500 |
15 |
Ребристая |
Песчаник |
2100 |
|
|
|
|
|
|
|
2 |
500 |
600 |
25 |
Гладкая |
Известняк |
1600 |
|
|
|
|
|
|
|
3 |
600 |
750 |
20 |
Ребристая |
Гранит |
2600 |
|
|
|
|
|
|
|
4 |
800 |
710 |
30 |
Ребристая |
Песчаник |
2000 |
|
|
|
|
|
|
|
5 |
1000 |
800 |
20 |
Ребристая |
Мрамор |
2400 |
|
|
|
|
|
|
|
5.2. Сортировочные машины
Грохоты служат для разделения каменных материалов по крупности. Они разделяются на плоские и цилиндриче-
40