
10936
.pdfИ.В. Шкода
ФГБОУ ВО «Нижегородский государственный архитектурно-строительный университет»
СРАВНИТЕЛЬНЫЙ АНАЛИЗ ДЕФОРМАТИВНО-ПРОЧНОСТНЫХ ХАРАКТЕРИСТИК РАЗЛИЧНЫХ ВАРИАЦИЙ ИСПОЛНЕНИЙ ФЛАНЦЕВОГО УЗЛА ИЗ ПРЯМОУГОЛЬНЫХ ГНУТОСВАРНЫХ ТРУБ
Фланцевое соединение представляет собой две пластины, приваренные к присоединяемым элементам, которые стягиваются болтами. Такие соединения имеют массу преимуществ перед другими типами соединений, а именно: обеспечивают возможность возведения каркаса здания при любых климатических условиях и возможность его демонтажа без повреждения несущих элементов; характеризуются высокой надежностью; обладают наименьшей трудоемкостью; а также крайне удобны при ремонте, т.к. они позволяют быстро вычленить один элемент и заменить его другим.
Во фланцевом соединении внешние растягивающие усилия передаются через предварительно натянутые пакеты «фланец-болт», а сжимающие – через плотное касание фланца [1].
Фланцевая пластина в растянутой зоне соединения работает по пространственной схеме, в следствии чего при ее расчете необходимо учитывать дополнительные факторы, такие как: наличие касательных напряжений в пластине; работа фланца как упруго-защемленной пластины из-за податливости болтов; появление изгибных напряжений в теле болта. Учесть все эти факторы при расчете фланцевых узлов ручным методом довольно сложно, поэтому единственной возможностью экспрессного анализа напряженного состояния фланцевого соединения чаще всего является компьютерное математическое моделирование [2].
Для решения поставленной задачи в программном комплексе IDEA StatiCa смоделированы и проанализированы шесть вариантов исполнения фланцевого узла из прямоугольных гнутосварных труб (рис. 1):
1.Непрорезной фланец без ребер жесткости;
2.Прорезной фланец без ребер жесткости;
3.Непрорезной фланец с ребрами жесткости по 1 варианту;
4.Прорезной фланец с ребрами жесткости по 1 варианту;
5.Непрорезной фланец с ребрами жесткости по 2 варианту;
6.Прорезной фланец с ребрами жесткости по 2 варианту.
а) |
б) |
в) |
90

г) |
д) |
е) |
Рис. 1 - варианты конструкций фланцевого узла из гнутосварных труб прямоугольного сечения: а) непрорезной узел без ребер жесткости; б)
прорезной узел без ребер жесткости; в) непрорезной узел с ребрами жесткости по первому варианту; г) прорезной узел с ребрами жесткости по первому варианту; г) непрорезной узел с ребрами жесткости по второму варианту; е) прорезной узел с ребрами жесткости по второму варианту
Данная статья представляет собой продолжение исследования [3], объектом которого выступает фланцевый узел купола из круглых труб.
Материал труб - сталь С255, пластина фланца выполнена из стали С345, болты – М36 класса прочности 10.9. Катет сварных швов 6 мм. Усилия, возникающие в элементах купола, получены в расчётном комплексе SCAD и приложены к модели узла. Условия закрепления узла соответствуют его расчетной схеме. Согласно СП 294.1325800.2017 для данного исследования принимаемые в расчете наибольшие допускаемые пластические деформации равны = 5% [4, 5].
Результаты расчета представлены на графиках 1-5.
График 1 – Зависимость напряжений в теле трубы, в пластине фланца и в сварных швах от варианта исполнения фланцевого узла
91
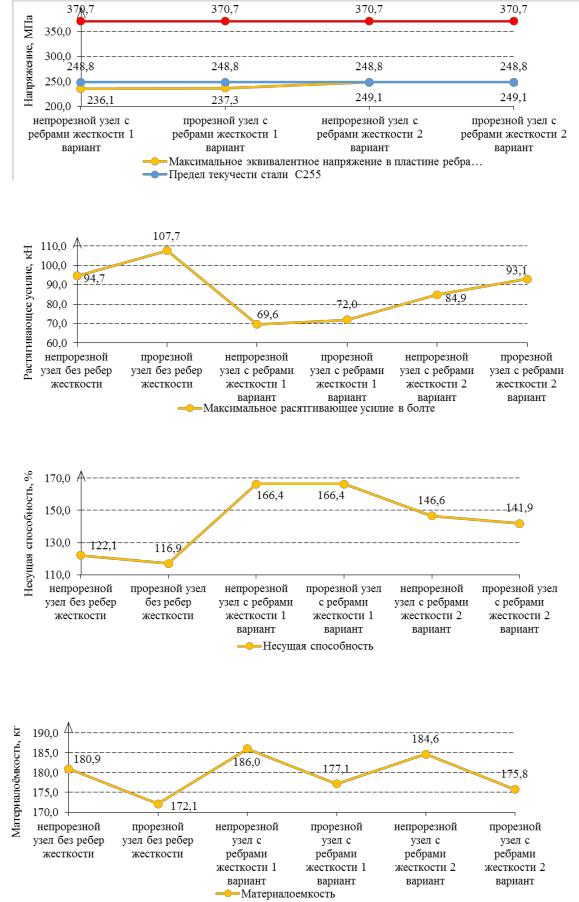
График 2 – Зависимость напряжений в ребрах жесткости от варианта исполнения фланцевого узла
График 3 – Зависимость растягивающих усилий в болтах от варианта исполнения фланцевого узла
График 4 – Зависимость несущей способности от варианта исполнения фланцевого узла
График 5 – Зависимость материалоемкости от варианта исполнения фланцевого узла
92
По результатам численного расчета сделаны следующие выводы:
•Наибольшие напряжения в пластине фланца для всех видов исполнения узлов локализованы около болтов и достигают 107,6 МПа для прорезного узла с ребрами жесткости по 2 варианту;
•В узлах с ребрами жесткости по 1 варианту исполнения напряжение
впластине уменьшается в 1,5-1,7 раза по отношению к узлам без них и к узлам с ребрами жесткости по 2 варианту;
•Наибольшее напряжение в сварном шве между трубой и пластиной фланца наблюдаются в прорезном узле без ребер жесткости – 228,5 МПа;
•При добавлении ребер жесткости, напряжение с сварных швах между пластиной фланца и телом трубы уменьшается, так как часть усилий перераспределяется на сварные швы ребер жесткости;
•Наибольшее растягивающее усилие в болтах возникает в прорезном узле без ребер жесткости – 107,7 кН, наименьшее – у непрорезного фланцевого узла с ребрами жесткости по 1 варианту – 69,6 кН;
•Несущая способность узлов с ребрами жесткости по 1 варианту на 44 % превышает несущую способность узлов без ребер жесткости и на 20 % превышает несущую способность узлов с ребрами жесткости по 2 варианту;
•Наибольшей материалоемкостью обладает непрорезной узел с ребрами жесткости по 1 варианту – 186,0 кг; наименьшей – прорезной без ребер жесткости – 172,1 кг;
•Ребра жесткости следует располагать вдоль углов профиля, что подтверждается численными результатами данной работы и рекомендациями по расчету фланцевых соединений [1].
Литература
1.Рекомендации по расчету, проектированию, изготовлению и монтажу фланцевых соединений стальных строительных конструкций / СО Стальмонтаж, ВНИПИ Промстальконструкция, ЦНИИПСК им. Мельникова. – М., 1988. – 83 с.
2.Расчёт узлов стальных конструкций компонентным методом конечных элементов [Электронный ресурс] - Режим доступа: http://isicad.ru/ru/articles.php?article_num=20749 (Дата обращения
23.08.2020)
3.СП 16.13330.2017. Стальные конструкции. Актуализированная редакция СНиП II -23-81* – М.: МРРРФ «НИЦ «Строительство», 2017.
4.Шкода И.В. Сравнительный анализ различных вариантов исполнений фланцевого узла / И.В. Шкода, Е.Н. Облетов // Журнал «Студенческий вестник»: научный журнал. – № 16(114). Часть 8. Москва, Изд. «Интернаука», 2020. – С. 11-16.
5.СП 294.1325800.2017. Конструкции стальные. Правила проектирования. – М.: ЦНИИСК им Кучеренко, 2017. – 158 с.
93
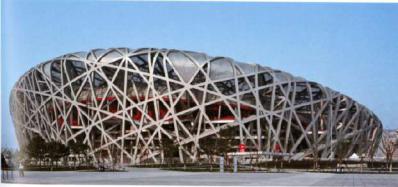
АГЕЕВА Е.Ю., ЛЕОНТЬЕВА Н.Н.
ФГБОУ ВО «Нижегородский государственный архитектурно-строительный университет»
ОСОБЕННОСТИ ВОЗВЕДЕНИЯ СТАДИОНА «ПТИЧЬЕ ГНЕЗДО» В ПЕКИНЕ
В центре Пекина один из смелых новаторских дизайнов имеет стадион «Птичье гнездо» (Рис.1). Его построили в 2008 году для Олимпийских игр. В данной статье будет рассмотрен процесс строительства стадиона, особенности его конструкции и трудности, с которыми пришлось столкнуться проектировщикам и строителям. 42 тыс. тонн стальных балок сплелись, образовав форму птичьего гнезда.
Фасад здания имеет стальной скелет. Вместимость 91 тыс. зрителей.
Рис.1. Стадион «Птичье гнездо»
На стальную крышу натянули высокотехнологическое мембранное покрытие. Оно пропускает солнечные лучи, удерживает энергию внутри стадиона и не дает проникать внутрь дождю и ветру. Фасад здания открыт, что помогает осуществлять естественную вентиляцию.
Трибунные и подтрибунные помещения сделаны из железобетона. Согласно проекту архитекторов, массивные балки скручиваются и
изгибаются хаотично вокруг стадиона диаметров 300м. Первое семейство балок устанавливаются снаружи: 24 опор окружают бетонную чашу – это «костяк» конструкции(Рис.2). Второе семейство балок заполняет промежутки между балками первого семейства. Они связывают опоры, образую структуру плетения. Третье семейство балок поддерживает лестницы, соединяющие многочисленные этажи здания и составляет каркас для мембранного покрытия. Их главное назначениеразбить все промежутки между опорами вторым семейством на участки, которые достаточно малы для натяжения крыши[1].
94
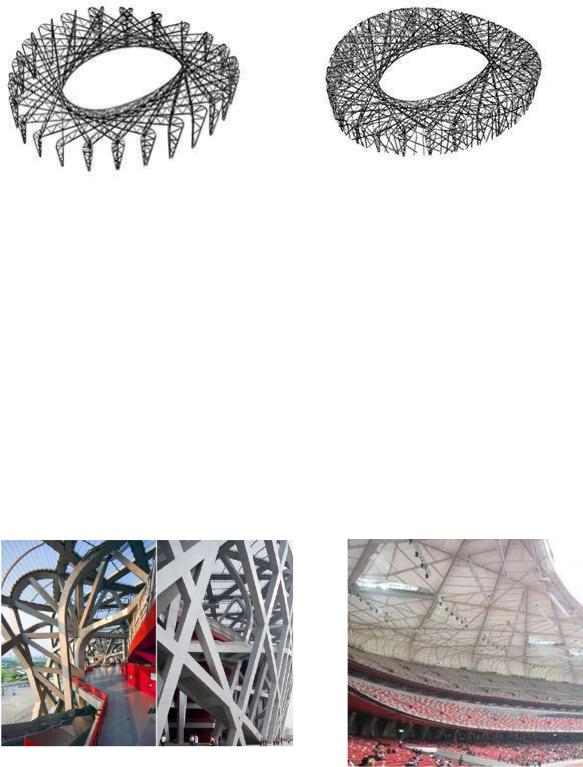
Рис.2. Двадцать четыре фермы — опоры здания переплетены «стяжками»
Для «Птичьего гнезда» было создано новый тип стали Q460. Он достаточно прочен, чтобы выдерживать напряжения на сгибах, и в то же время достаточно гибок, чтобы не разрушаться во время землетрясений.
«Птичье гнездо» может колебаться и это не будет представлять никакой опасности, так как гибкость стали не даст конструкции разрушиться [2].
Конструкция состоит из нескольких тысячи различных элементов. В ней нет ни одной прямолинейной балки.
Криволинейные балки сделаны в виде коробчатой конструкции, что дает требуемый вид «прутьев» и прочность(Рис.3). 4 стальных листа стороной и длиной в 1,2 м изгибаются и свариваются. Так получается криволинейная коробчатая секция, которая транспортируется на строительную площадку[3]. На месте рабочие сваривают короба между собой.
Рис.3.Криволинейные коробчатые |
секции, |
Рис.4.Переплетение с натянутыми пле |
сваренные в единую конструкцию фасада |
нками из этилентетрафторэтилена |
Так получаются более крупные секции, образующие опоры, некоторые из них достигают 12 метров в длину[4]. Затем кран поднимает их, чтобы установить на нужное место, затем секция сваривается к основной конструкции.
95
Покрытие кровли сделано из светопрозрачной плёнки, которые закреплены между балками конструкций(Рис.4).
Литература
1.Конструктивная система стадиона – изнутри и снауржи [Электронный ресурс] : [сайт]. – Режим доступа : https://infopedia.su/16x3325.html
2.6 увлекательных фактов о стадионе, более известный как «Птичье гнездо» [Электронный ресурс] : [сайт]. – Режим доступа : https://novate.ru
3.Строительство «Птичьего гнезда» [Электронный ресурс] : [сайт]. – Режим доступа : http://stadiums.at.ua
4.Стадион “Птичье гнездо(Наячао)” [Электронный ресурс] :
[сайт]. – Режим доступа : http://my-china.ru/national-stadium-birds-nest.html
А.П. ФЕОКТИСТОВА, Д.В. ГРИНЮК, Е.О. СУЧКОВА
ФГБОУ ВО «Нижегородский государственный архитектурно-строительный университет»
СОВРЕМЕННЫЕ МЕТОДИКИ ЗАКРЕПЛЕНИЯ ВЛАЖНЫХ И ВОДОНАСЫЩЕННЫХ ГРУНТОВ
В настоящее время строительство зданий и сооружений происходит на территориях с различными геологическими условиями, в том числе на влажных и водонасыщенных грунтах. Такие грунты опасны тем, что под действием статической нагрузки дают значительные осадки, а при промерзании неравномерно вспучиваются, что вызывает серьезные повреждения зданий и сооружений.
Для решения этих проблем были разработаны различные методы закрепления грунтов. Закреплением грунтов называют искусственное изменение строительных свойств грунтов различными физикохимическими способами. В результате таких преобразований увеличивается прочность и устойчивость грунтов, а также происходит уменьшение сжимаемости и водопроницаемости. Рассмотрим некоторые из современных методов, которые применяются для закрепления влажных и водонасыщенных грунтов.
Первый метод – это использование грунтовых свай-дрен или, как их еще называют, щебеночных свай. Этот способ идеально подходит для работ в сложных геологических условиях. Устройство щебеночных свай происходит за счет подачи щебня на дно скважины, сформированной обработкой грунта методом глубинной вибрации (рис. 1).
96
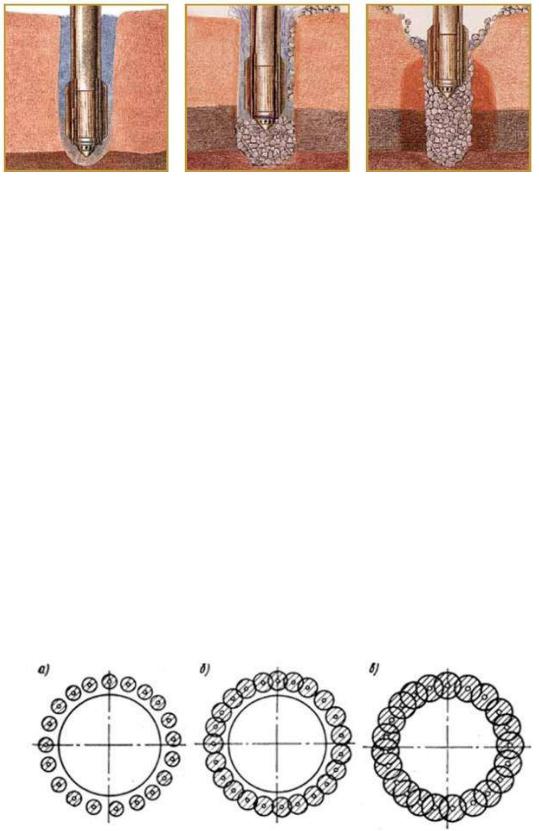
Рис. 1. Последовательность изготовления щебеночных свай
Щебеночные сваи применяют для обеспечения общей устойчивости и снижения деформаций основания, а также для передачи нагрузок на более прочные слои. К преимуществам использования щебеночных свай относятся снижение стоимости проекта за счет сокращения сроков и объемов земляных работ, уменьшение осадки в несколько раз, а также предотвращение резких снижений физико-механических характеристик грунта во время землетрясений [1]. Примером устройства щебеночных свай является возведение Крымского моста, строительство которого происходило в условиях влажных грунтов в сейсмически активном районе.
Следующий метод – искусственное замораживание грунтов. При этом методе происходит замораживание грунтов с помощью замораживающих колонок. В результате создается ледогрунтовый массив, который имеет большую механическую прочность и полностью водонепроницаем.
Существует два способа замораживания грунта, которые отличаются видом хладоносителя. Для начала рассмотрим «рассольный» способ искусственного замораживания грунтов. В данном способе хладоноситель представляет собой высококонцентрированный раствор хлористого кальция или натрия, который предварительно охлаждают до температуры -25ºC. С помощью замораживающих колонок создается прочное ограждение из замороженного грунта (рис. 2).
Рис. 2. Последовательность образования ледогрунтового кольцевого массива а – начальный период: б – середина процесса; в – конец замораживания
97
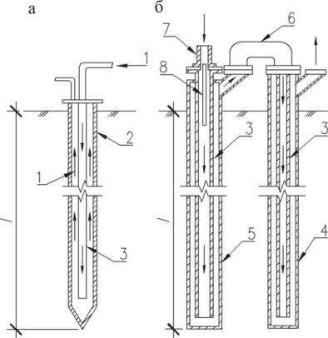
Такие «ледовые стены» создаются благодаря специальным холодильным машинам (рис. 3). Эти установки основаны на испарении хладогента, который, в свою очередь, забирает у окружающей среды тепло. В качестве хладагента используются аммиак или фреон. Затем пары вновь конденсируют с помощью компрессора и конденсатора, а пониженная температура, образовавшиеся в испарителе, поступает на охлаждение незамерзающего рассола. Такая система позволяет примерно за месяц создать ледогрунтовую монолитную массу, защищающую от проникновения грунтовых вод. Такое оборудование поддерживает заморозку грунтов, пока не будут произведены соответствующие работы по укреплению и гидроизоляции стен.
Второй и более современный способ замораживания грунтов – низкотемпературное замораживание с использованием в качестве хладагента жидкого азота (рис. 3). Его температура испарения очень низкая, примерно -195,8ºС. Главное отличие этого способа в том, что хладагент используют без повторного применения. Жидкий азот применяют не в замкнутой системе, а в открытой среде.
Данный способ отличается от рассольного тем, что для него не требуются замораживающие установки и сети трубопроводов. Хладагент сразу запускают в замораживающие колонки. Скорость заморозки выше, чем у рассольного способа. Так же он нетоксичен и не горюч [2].
Рис. 3. Конструкции замораживающих скважин при рассольном способе (а) и замораживании с использованием жидкого азота (б): 1 — направление движения рассола; 2 — замораживающая колонка; 3 — питающая труба; 4 — колонка для
газообразного азота; 5 — колонка для жидкого азота; 6 — соединительная труба; 7 — входная труба; 8 — теплопроводное устройство; l — глубина скважины
98
Оба способа замораживания грунтов являются универсальным средством закрепления водонасыщенных грунтов. Однако, эти способы на ряду с достоинствами имеют и недостатки:
•вследствие замораживания грунтов, происходит их расширение, что может вызвать пучение;
•после оттаивания возможна осадка, которая может привести к деформациям поверхностных сооружений;
•сложность подготовительных работ;
•длительный процесс замораживания грунтов;
•высокая стоимость.
Каждый из рассмотренных методов имеет ряд преимуществ и недостатков в сравнении друг с другом. Выбор способа закрепления зависит от района строительства и его геологических условий.
Литература
1.Комплексное геотехническое проектирование. ГЕОИЗОЛ проект [Электронный ресурс]. – Режим доступа: https://geoizolproject.ru/
2.Московское метро [Электронный ресурс]. – Режим доступа: http://www.metro.ru/
МАКАРОВ П.В., ПРОТАСОВА Е.П.
ФГБОУ ВО «Нижегородский государственный архитектурно-строительный университет»
ОЦЕНКА ВЛИЯНИЯ ЧЕЛОВЕЧЕСКОГО ФАКТОРА НА ТРАВМАТИЗМ В СТРОИТЕЛЬНОЙ ОТРАСЛИ
В настоящее время строительство относится к одной из самых травмоопасных отраслей экономики. Высокий уровень травматизма можно объяснить спецификой выполнения строительных работ это: временным характером рабочих мест, необходимостью выполнения работ повышенной опасности, работ на высоте, в сложных климатических условиях и т.д.
Исследования подтверждают, что наиболее значимый из всех факторов является человеческий. Примерно 80% всех аварий и несчастных случаев происходит именно из-за него.
Важнейшим условием безаварийной работы потенциально опасных объектов является обеспечение надежности их персонала. На надежность персонала влияет совокупность эмоциональных, волевых, мотивационных, интеллектуальных и других личностных качеств, обеспечивающих точное, безошибочное, адекватное восприятие сложившейся ситуации.
Надежность персонала исследуют с различных позиций: принятия
99