
10694
.pdf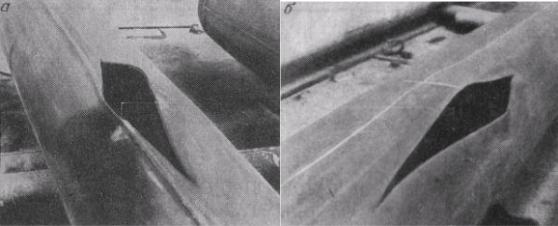
81
материала при разрушении (относительное увеличение периметра до 7,5% и уменьшение толщины стенки в месте разрыва до 10-15%). Разрушение происходило как в зоне сварного соединения, так и по основному металлу, что говорит о качественной сварке и снятии эффектов концентрации и изгибных эффектов в процессе статического нагружения.
Все испытанные трубы удовлетворяют условиям прочности, что доказало правильность применения расчетов при стационарном нагружении. Однако в реальных условиях продуктопроводы подвержены циклическим нагрузкам, связанным с особенностями работы компрессорных и насосных станций.
Разрушения труб в эксплуатации по своему внешнему виду соответствуют разрушениям под действием внутреннего давления при статическом нагружении до разрыва [4]. При этом трещины, как и при статическом разрыве, образуются в продольном направлении. Характерным является появление эксплуатационных трещин, как правило, в зоне сварного соединения. Длина разрывов в процессе эксплуатации может составлять, как и при статическом разрыве, до нескольких метров.
Однако, рассмотрение характера мест разрушения показывает существенные отличия эксплуатационных разрывов труб от разрывов при статическом нагружении до разрушения. Основной особенностью эксплуатационных разрывов является отсутствие значительных пластических деформаций как в месте разрыва, так и по периметру трубы. Изломы имеют выраженные зоны очага разрушения и дорыва.
Рис. 1. Разрушение труб при статическом разрыве в зоне сварного соединения (а) и по основному металлу (б)
В исследованиях [1] наряду с испытаниями на статичную нагрузку, были проведены испытания труб с циклической нагрузкой избыточным внутренним давлением. Данная часть испытаний показала существенное различие в характере разрушения по сравнению со статическим нагружением. Анализ мест разрушения показал, что разрушение начиналось с внутренней полости трубы в продольном сварном шве в месте перехода от наплавленного металла к основному и распространялось по толщине стенки по нормали к поверхности трубы (рис 2).
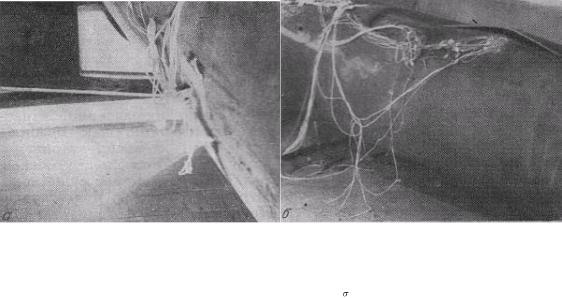
82
Анализ местной напряженности [1] позволил установить, что в зависимости от геометрии сварного соединения в зоне шва появляются выраженные моментные зоны. По мере приближения к шву уровни нагруженности труб получаются существенно зависящими от конфигурации сварного соединения. Местное возмущение напряженного состояния в сварном соединении трубы обусловлено концентрацией напряжений из-за наличия усиления шва и изгиба, вызванного смещением кромок в шве, угловатостью в области продольного сварного шва, а также овальностью сечения.
Рис. 2. Разрушение труб при малоцикловом нагружении.
По данным испытаниям, удалось определить теоретический коэффициент концентрации напряжений для четырех исследуемых
труб на циклическую нагрузку( =2÷8). Полученные в работе [1]
величины коэффициентов концентрации и максимальные деформации в сварных соединениях труб показывают, что ответственными за малоцикловое разрушение являются максимальные деформации, возникающие в околошовной зоне, где и наблюдалось образование малоцикловой трещины.
Технологические дефекты — подрезы, непровары, несплавления и трещины создают значительную концентрацию напряжений и снижают долговечность соединений. При определенных условиях дефекты типа пор и шлаковых включений, не опасных при статическом нагружении, могут вызвать преждевременные усталостные разрушения. Ниже приведены данные о влиянии непроваров, подрезов и пор на усталостную прочность сварных соединений с учетом упомянутых факторов.
Усталостная прочность швов с подрезами зависит от глубины подреза, уровня остаточной напряженности и вида соединения. В случае стыковых соединений влияния концентрации напряжений и остаточных напряжений могут быть соизмеримыми. Приводятся результаты испытания образцов с подрезами различной глубины, расположенными в зонах высокой и сравнительно низкой остаточной напряженности (рис. 3)

83
Рис. 3. Влияние подрезов на предел выносливости стыковых соединений из стали 09Г2С, сваренных проволокой Св-08ГА под флюсом АН-348А:
а – швов без подрезов б – швов с подрезами глубиной 1 - 1,5 мм., остаточные
растягивающие напряжения ниже 1000 кгс/см2 в – образцы с подрезами глубиной 2 – 3,5 мм., остаточные
напряжения ниже 1000 кгс/см2 г – образцы с подрезами глубиной 2 – 3,5 мм., остаточные
напряжения 1500 – 2000 кгс/см2 ○ – образцы толщиной 20 мм.
● – образцы толщиной 30 мм.
Под влиянием изменения глубины подреза с 1—1,5 мм до 2—3,5 мм предел выносливости снижается дополнительно на 15%. Падение предела выносливости такого же порядка наблюдалось и в результате изменения растягивающих остаточных напряжений с 5,0 до 20 кгс/мм2. Суммарное влияние этих факторов может привести к снижению предела выносливости соединения вдвое.
Анализ проводится при помощи современного компьютерного программного комплекса ANSYS.
На основе полученных результатов, на данном этапе развития вычислительной техники можно провести с помощью расчетных комплексов аналогичные испытания. В данном случае, актуальна задача разработки методики оценки усталостного ресурса, базирующегося на математическом моделировании реальных физических процессов.
Литература
1.Гусенков, А.П. Прочность при изотермическом и неизотермическом нагружении/ А.П. Гусенков. – М.: Наука, 1979. – 295с.
2.Серенсен, С.В. К основам расчѐта на прочность при малоцикловом
нагружении/ С.В. Серенсен, Н.А. Махутов, Р.М. Шнейдерович. – М.: Машиноведение, 1972. – № 5.
3. Аистов, А.С. Исследование малоцикловой усталости труб газо- и нефтепроводов/ А.С. Аистов, Г.А. Маковкин// Вестник ВГАВТ: Надежность и ресурс в машиностроении. – Н. Новгород, 2009. – Вып. 24. – С.12-24.

84
4. Аистов, А.С. О расчѐте напряжѐнного состояния труб высокого давления, имеющих овальность/ А.С. Аистов// Матер. науч.-техн. конф. проф.-препод. состава ГИИВТ (1972 – 1973 уч.г.). – Горький, 1973. –
С. 244-245.
УДК 728:693.1/2+692.2
О.В. Талалушкина
Причины разрушения кирпичной облицовки многослойных стеновых конструкций на примере дома №5 на б-ре Заречный в г.Н.Новгороде
Проект 16-этажного жилого дома № 5 на бульваре Заречный разработан для строительства во II климатическом районе c расчетной зимней температурой наружного воздуха – 310С, расчетной снеговой нагрузкой для IV климатического района 2,4 кПа, расчетного скоростного порыва ветра для I климатического района 0,23 кПа.
Здание кирпичное 16-этажное, 8-секционное, с поперечными несущими стенами, с подвалом. Планировочная схема каждой секции – ортогональная, прямоугольная, компактная. Фундаменты под стенами здания свайные из забивных железобетонных призматических свай длиной 7 и 9 м с ленточными монолитными железобетонными ростверками, замкнутыми по контуру капитальных стен. Наружные стены кирпичные, 3-слойные. Несущая часть наружных стен и внутренние стены выполнены из силикатного кирпича на цементно-песчаном растворе.
Толщина несущей части наружных стен 510 мм в пределах с 1 по 12 этаж и 380 мм в пределах с 13 по 16 этаж. Облицовка толщиной в полкирпича опирается на горизонтальные разгрузочные пояса, выполненные из стального уголка.
При обследовании наружных стен в кирпичной облицовке глухих (без оконных проѐмов) несущих торцовых стен были обнаружены вертикальные трещины с раскрытием до 25 мм, рассекающие лицевую кладку по всей высоте с 1-го по 12-й этаж на 3 части (фото 1, 2).
Причинами образования вертикальных трещин являются:
1.Первая и главная причина - отсутствие в облицовке вертикальных температурных швов, разрезающих облицовку на отдельные температурные отсеки.
2.Вторая причина - 3-рядная кладка облицовки, не обладающая достаточной прочностью и жесткостью:
из-за отсутствия перевязки вертикальных растворных швов; из-за отсутствия армирования облицовки горизонтальными
арматурными сетками.
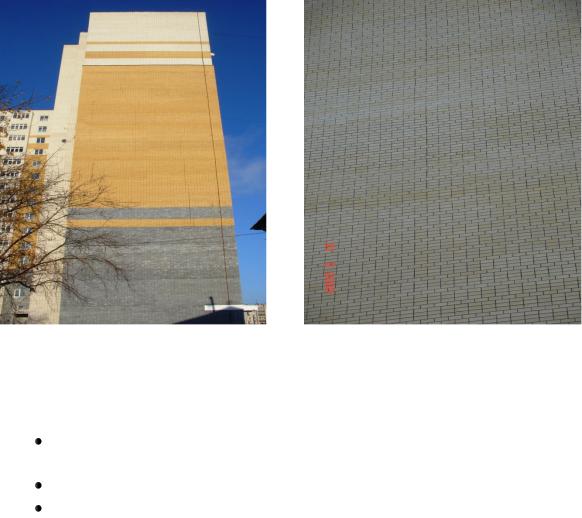
85
Фото 1, 2. Торцовая стена на участке в осях «А»/«42»-«46»
На отдельных горизонтальных полосообразных участках, ориентированных вдоль разгрузочных металлических поясов, облицовка деформируется и разрушается:
происходит отклонение облицовки из вертикальной плоскости (с выпиранием наружу);
образуются горизонтальные трещины; из облицовки выдавливаются отдельные кирпичи и растворные
швы.
Все вышеперечисленное может привести к потере устойчивости облицовки и еѐ обрушению. Причинами деформации и разрушения такого рода являются:
1. Первая и главная причина - отсутствие горизонтальных деформационных швов под металлическими разгрузочными поясами, компенсирующих:
неравномерное сжатие и неравномерную усадку несущей части стены и кирпичной облицовки;
податливость металлических разгрузочных поясов.
2.Недостаточная прочность и жесткость многорядной кладки облицовки.
3.Отсутствие армирования облицовочной кладки.
4.Податливость анкеров в деформированной области облицовки.
5.Отсутствие вентиляционных отверстий (щелей) в кладке облицовки (предусмотренных в рабочем проекте), из-за чего в воздушной прослойке стен скапливается конденсат, превращающийся при отрицательных температурах в лѐд.
Расчетами деформаций сжатия несущей части торцовых стен и кирпичной облицовки были подтверждены вышеприведенные выводы.

86
В выполненных расчѐтах модуль упругости кладки Е0,i при кратковременной нагрузке принят равным для неармированной кладки
(п. 3.20 СНиП II-22-81):
Е0,i= Ru , |
(1) |
где - упругая характеристика кладки, принимаемая по п. 3.21, табл. 15
СНиП II-22-81.
Модуль деформации Еi сечения определѐн по формуле (п. 3.22
СНиП II-22-81):
, |
(2) |
|
|
Относительные деформации кладки εi с учетом ползучести |
|
определены по формуле (п. 3.23 СНиП II-22-81): |
|
(3)
,
где ζ – напряжение, при котором определяется εi ,
ν – коэффициент, учитывающий влияние ползучести кладки (п. 3.23
СНиП II-22-81).
Так как в соответствии с проектом облицовочный слой опирается на несущие металлические пояса из закладных деталей МН1, МН3, МН4, монтирующихся по наружному периметру здания в уровне перекрытий 1, 3, 5, 7, 9, 11 этажей, деформации сжатия кирпичной облицовки определены для соответствующих горизонтальных сечений. При этом учтено, что нагрузка от облицовки, расположенной выше 12-го этажа, приходится на несущую часть стены.
Значения деформаций сжатия несущей части стены приведены в табл. 1.
|
|
|
|
|
|
Таблица 1 |
|
Деформации сжатия несущей части стены. |
|
|
|||
Сечение |
Модуль |
Модуль |
Относительная |
|
εi×hi, м |
εi×hi, |
|
упругости |
деформации |
деформация |
|
|
м |
|
кладки, Е0,i (kПа) |
кладки, Еi (кПа) |
кладки, εi |
|
|
|
1-1 |
3600000 |
2880000 |
0,001067 |
|
0,003200 |
0,003200 |
2-2 |
3600000 |
2880000 |
0,001000 |
|
0,002999 |
0,006199 |
3-3 |
3300000 |
2640000 |
0,001017 |
|
0,003052 |
0,009251 |
4-4 |
3300000 |
2640000 |
0,000944 |
|
0,002833 |
0,012084 |
5-5 |
3000000 |
2400000 |
0,000958 |
|
0,002875 |
0,014959 |
6-6 |
2550000 |
2040000 |
0,001033 |
|
0,003098 |
0,018057 |
7-7 |
2550000 |
2040000 |
0,000938 |
|
0,002815 |
0,020872 |
8-8 |
2550000 |
2040000 |
0,000844 |
|
0,002531 |
0,023403 |
9-9 |
2250000 |
1800000 |
0,000849 |
|
0,002547 |
0,025949 |
10-10 |
2250000 |
1800000 |
0,000742 |
|
0,002225 |
0,028174 |
11-11 |
1950000 |
1560000 |
0,000732 |
|
0,002196 |
0,030371 |
12-12 |
1950000 |
1560000 |
0,000608 |
|
0,001825 |
0,032196 |
13-13 |
1650000 |
1320000 |
0,000694 |
|
0,002081 |
0,034277 |
14-14 |
1650000 |
1320000 |
0,000531 |
|
0,001593 |
0,035869 |
15-15 |
1650000 |
1320000 |
0,000368 |
|
0,001105 |
0,036974 |
16-16 |
1650000 |
1320000 |
0,000193 |
|
0,000116 |
0,037090 |
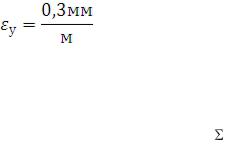
87
Значения деформаций сжатия кирпичной облицовки приведены в табл. 2.
|
|
|
|
Таблица 2. |
|
|
Деформации сжатия кирпичной облицовки. |
|
|
||
Сечение |
Модуль |
Модуль |
Относительная |
εi×hi, м |
|
|
упругости |
деформации |
деформация |
|
|
|
кладки, Е0,i (kПа) |
кладки, Еi (кПа) |
кладки, εi |
|
|
1-1 |
3000000 |
2400000 |
0,000025 |
0,000148 |
|
|
|
|
|
|
|
3-3 |
3000000 |
2400000 |
0,000037 |
0,000334 |
|
|
|
|
|
|
|
6-6 |
3000000 |
2400000 |
0,000037 |
0,000334 |
|
|
|
|
|
|
|
9-9 |
3000000 |
2400000 |
0,000037 |
0,000334 |
|
|
|
|
|
|
|
12-12 |
3000000 |
2400000 |
0,000037 |
0,000334 |
|
|
|
|
|
|
|
В то же время кладка из силикатного кирпича, из которого выполнены как несущая часть стены, так и облицовка, подвержена деформациям усадки или набухания (в зависимости от влажности).
Деформации усадки для кладок из силикатного кирпича следует принимать по п. 3.26 СНиП II-22-81:
(4)
Значения деформаций усадки несущей части стены приведены в табл. 3.
Таблица 3
Деформации усадки несущей части стены.
Сечение |
Расчетное значение |
εу×h |
εу×h |
|
усадки, εу, мм/м |
|
|
|
|
|
|
1-1 |
0,3 |
0,9 |
0,9 |
|
|
|
|
2-2 |
0,3 |
0,9 |
1,8 |
|
|
|
|
3-3 |
0,3 |
0,9 |
2,7 |
|
|
|
|
4-4 |
0,3 |
0,9 |
3,6 |
|
|
|
|
5-5 |
0,3 |
0,9 |
4,5 |
|
|
|
|
6-6 |
0,3 |
0,9 |
5,4 |
|
|
|
|
7-7 |
0,3 |
0,9 |
6,3 |
8-8 |
0,3 |
0,9 |
7,2 |
|
|
|
|
9-9 |
0,3 |
0,9 |
8,1 |
|
|
|
|
10-10 |
0,3 |
0,9 |
9,0 |
|
|
|
|
11-11 |
0,3 |
0,9 |
9,9 |
12-12 |
0,3 |
0,9 |
10,8 |
|
|
|
|
13-13 |
0,3 |
0,9 |
11,7 |
|
|
|
|
14-14 |
0,3 |
0,9 |
12,6 |
|
|
|
|
15-15 |
0,3 |
0,9 |
13,5 |
|
|
|
|
16-16 |
0,3 |
0,9 |
14,4 |
|
|
|
|
Значения деформаций усадки кирпичной облицовки приведены в табл. 4.
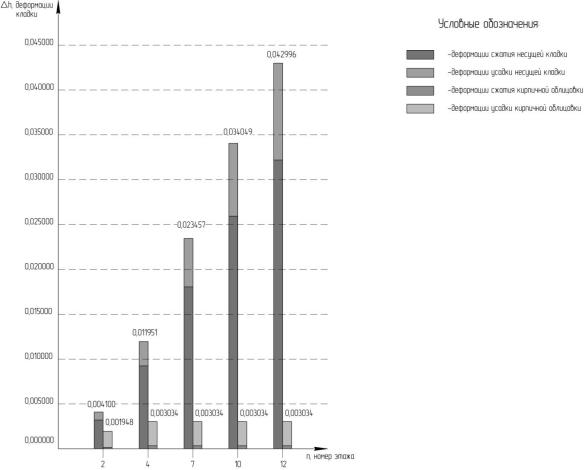
88
Таблица 4
Деформации усадки кирпичной облицовки.
Сечение |
Расчетное значение усадки, |
εу×h |
|
εу, мм/м |
|
|
|
|
1-1 |
0,3 |
1,8 |
|
|
|
3-3 |
0,3 |
2,7 |
|
|
|
6-6 |
0,3 |
2,7 |
|
|
|
9-9 |
0,3 |
2,7 |
|
|
|
12-12 |
0,3 |
2,7 |
|
|
|
Сравнение суммарных деформаций сжатия и деформаций усадки несущей кладки и кирпичной облицовки, определѐнных для расчѐтных сечений, представлено в виде диаграммы на рис. 1.
Рис.1. Сравнение деформаций несущей кладки и кирпичной облицовки.
В результате расчета было установлено, что несущая часть кладки находится под действием большей нагрузки, чем кирпичная облицовка. Вследствие этого несущая кладка сжимается на большую величину, что приводит к деформации опорных металлических поясов, закрепленных в теле кладки несущей части стены, а так же к разрушению кирпичной облицовки.
89
УДК 624.011.2
А.В. Тихонов
Углепластик в деревянных конструкциях
Углепластик – полимерный композиционный материал из переплетенных нитей углерода, расположенных в матрице из полимерных (например, эпоксидных) смол.
Основная составляющая часть углепластика – это нити углерода (по сути, то же самое что и, например, стержень в карандаше). Такие нити очень тонкие, сломать их очень просто, а вот порвать достаточно трудно. Из этих нитей сплетаются ткани. Они могут иметь разный рисунок плетения (ѐлочка, рогожа и т.п.). Для придания еще большей прочности данные ткани из нитей углерода кладут слоями, каждый раз меняя угол направления плетения. Слои скрепляются с помощью эпоксидных смол. Нити углерода обычно получают термической обработкой химических или природных органических волокон, при которой в материале волокна остаются главным образом атомы углерода.
Температурная обработка состоит из нескольких этапов.
Первый из них представляет собой окисление исходного (полиакрилонитрильного, вискозного) волокна на воздухе при температуре 250 °C в течение 24 часов. В результате окисления образуются лестничные структуры.
После окисления следует стадия карбонизации – нагрева волокна в среде азота или аргона при температурах от 800 до 1500 °C. В результате карбонизации происходит образование графитоподобных структур.
Процесс термической обработки заканчивается графитизацией при температуре 1600-3000°С, которая также проходит в инертной среде. В результате графитизации количество углерода в волокне доводится до
99%.
Помимо обычных органических волокон (чаще всего вискозных и полиакрилонитрильных), для получения нитей углерода могут быть использованы специальные волокна из фенольных смол, лигнина, каменноугольных и нефтяных пеков.
Детали из карбона превосходят по прочности детали из стекловолокна и обходятся значительно дороже аналогичных деталей из стекловолокна.
Дороговизна карбона вызвана, прежде всего, более сложной технологией производства и большей стоимостью производных материалов.
Например, для проклейки слоев используются более дорогие и качественные смолы, чем при работе со стеклотканью, а для производства деталей требуется более дорогое оборудование, к примеру, такое как автоклав.
90
Недостатком карбона является его боязнь точечных ударов. В отличие от металлических деталей или деталей из стеклоткани, восстановить первоначальный вид карбоновых деталей невозможно. Поэтому, после даже незначительного повреждения всю деталь придется менять целиком. Кроме того, детали из карбона подвержены выцветанию под воздействием солнечных лучей.
Данный композиционный материал нельзя назвать революционно новым. Впервые получение и применение углеродных волокон было предложено и запатентовано известным американским изобретателем Томасом Алва Эдисоном в 1880 г. в качестве нитей накаливания в электрических лампах. Однако в полной мере интерес к углеродным волокнам проявился лишь в конце 1950-х годов.
Они оказались наиболее подходящим армирующим материалом композитов для изготовления ракетных двигателей, поскольку обладают высокой термостойкостью, хорошими теплоизоляционными свойствами, коррозионной стойкостью к воздействию газовых и жидких сред, высокими удельными прочностью, сопротивлением усталости и жесткостью.
По сравнению с обычными конструкционными материалами, например, алюминием или сталью, композиты с углеродными волокнами обладают некоторыми весьма полезными свойствами:
1)Они имеют исключительно высокую термостойкость: в инертных средах или в вакууме до 3000°С (температура плавления стали 1500°С), а
на воздухе до 450°С;
2)Удельное электрическое сопротивление можно задать от 0,02
Ом*м*10-6 (сопротивление меди) до 1,0 Ом*м*109 (сопротивление полупроводника).
Углеродные волокна превосходят все известные жаростойкие
волокнистые материалы благодаря своим характеристикам: большой активной поверхности до 2500 м2/гр и невероятной прочности (3,6 Гн/м2) в 2 раза выше прочности стали (1,8 Гн/м2) и при этом в 4 миллиона раз легче стали (плотность 1,9 г/м3,а плотность стали 7,82 т/м3). Также они являются прекрасными сорбентами (1 гр. поглощает до 50 гр.
нефтепродуктов).
Это предопределяет возможность применения углеродных волокон в качестве тепловых экранов и теплоизоляционного материала в высокотемпературной технике.
В настоящее время углепластик в виде ламелей или углеродистого волокна, очень широко используется в реконструкции и усилении железобетонных конструкций большого пролета, таких как: мосты, балки с недостаточным армированием, железобетонные колонны с образовавшимися трещинами и т.д.
Подобного рода усиления продлевают жизнь конструкциям, делая процесс реконструкции простым, доступным и относительно дешевым.