
10694
.pdf
71
Принята следующая высота этажей: для нижних общественных этажей 5,3 м для остальных этажей до 4,5м. Это объясняется тем, что под перекрытием будет размещаться балочная клетка и все инженерные коммуникации здания.
Несущий остов здания составляют три ядра жесткости, состоящих из группы колонн, объединенных в единый пятигранник Расчетная схема принята стержневая, а в пределах этажа – в виде ростверка. Первоначально схема была вычерчена в AutoCAD и импортирована в ППП SCAD. В первом приближении сечение основных колонн принято из электросварных труб по ГОСТ 10704-91 диаметра 426х11. Контур здания опоясывают фермы, выполняющие роль связей и фахверковых конструкций.
Крепление колонн к фундаментам, ригелей к колоннам – жесткое, крепление ригелей на нижележащие (вышележащие) конструкции фермы – жесткое (рис. 7).
Рис. 7. Схема фермы для первого этажа для одной
Перекрытия выполнены в виде балочной клетки (рис. 8).
Рис. 8. Фрагмент схемы опирания этажей на вертикальные фермы, n-номер этажа
По конструктивному решению все элементы лежат в одной плоскости.
Сбор нагрузок производится по СП 13330-2011.

72
Общие данные:
Проектируемое здание расположено в субарктическом поясе России.
Климатический район II2. Ветровой район – VI.
Тип местности – А (согласно п.6.5 СП 13330-2011).
Снеговой район – не учитывается, т.к. форма здания позволяет не учитывать в расчетах снеговую нагрузку.
Класс ответственности здания – I.
Сопряжение колонн с ригелями и между собой – жесткое. Полезная нагрузка собирается на 1м2 согласно СП 13330-2011:
1)для общественных этажей – 2,0 кПа;
2)для жилых этажей – 1,5 кПа;
3)для этажей секции 3 и 4 – 2,0 кПа.
Литература
1.СП 20.13330-2011 Нагрузки и воздействия Актуализированная редакция СНиП 2.01.07-85*: свод правил: утв. Минрегион России
27.12.2010: дата введ 20.05.2011 – М.:2011
2.СП 16.13330.2011 Стальные конструкции. Актуализированная редакция СНиП II-23-81*: свод правил: утв. Минрегион России 27.12.2010:
дата введ 20.05.2011 – М.:2011
УДК 624.953
О.Н. Рябова
Уторный узел с кольцевым компенсатором вертикальных цилиндрических резервуаров
В настоящее время вопросам энергетической безопасности в России уделяется все более серьезное внимание. Особое ключевое место при этом занимает проблема повышения эффективности и безопасности хранения нефтепродуктов.
Самым распространенным типом резервуаров для хранения нефтепродуктов является вертикальный стальной цилиндрический резервуар (РВС). Для конструктивных частей резервуара характерно сложное напряженно-деформированное состояние (НДС).
Тенденция к увеличению объѐма вновь строящихся РВС, а не их количества позволяет снизить металлоемкость конструкций, стоимость хранения нефтепродуктов, сэкономить полезную площадь нефтебаз. Но рост единичной вместимости конструкций РВС приводит к снижению их пространственной жесткости и эксплуатационной надежности.
73
Аварии небольших по объѐму резервуаров наносят значительный материальный ущерб, но аварии крупных резервуаров можно классифицировать как промышленную катастрофу, наносящую огромный материальный ущерб и приносящую большой урон окружающей среде.
Поэтому строительство крупных резервуаров должно сопровождаться улучшением качества проектирования, изготовления, монтажа и испытаний, что обеспечит их надежную работу, долговечность при эксплуатации, а также снижение потерь нефти и ее продуктов.
Для выявления действительной несущей способности резервуарных конструкций применяются два метода экспериментальных исследований - на реальных конструкциях и на моделях.
Исследования в реальных условиях имеют свои преимущества, так как в данном случае рассматривается непосредственно натурная конструкция резервуара, на которой устанавливаются необходимые измерительные приборы. Однако, данный метод исследований оправдывает себя лишь для РВС небольшой вместимости. Для крупных конструкций РВС исследования несущей способности в реальных условиях имеют следующие недостатки [1]:
-для исследований несущей способности оболочки резервуара требуются значительные трудовые и капитальные затраты, необходимые для ее изготовления и испытания;
-в случае негативных результатов исследований теряются безвозвратно сотни тонн высококачественной стали;
-технически затруднена реализация различных видов нагружений натурных конструкций резервуаров;
-значительна продолжительность эксперимента во времени;
-существенно влияние на постановку эксперимента климатических воздействий и т.д.
В настоящее время метод конечных элементов служит универсальным средством анализа конструкций. Программы конечноэлементного анализа общего назначения позволяют выполнить анализ статики и динамики конструкций.
Анализ статистики аварий [2, 3] говорит о том, что взрыв сопровождается двумя типами разрушений: в узле сопряжения стенки и днища (уторный узел) или в узле сопряжения стенки и крыши. Разрыв узла крыши со стенкой не наносит такого катастрофического ущерба как разрыв стенки с днищем. Поэтому изучение НДС уторного узла является приоритетной задачей. Многие научные школы страны занимаются этой проблемой [4, 5]. Существующие нормы расчѐта НДС корпуса резервуаров и, в частности, [6] не учитывают дополнительных напряжений, которые могут возникать в стенке от краевого момента, от очагов концентрации и «остаточных» напряжений в стенке резервуара, а также от зон локальной и общей потери устойчивости стенки РВС в случае еѐ перенапряжения от неравномерной деформации грунтового основания.
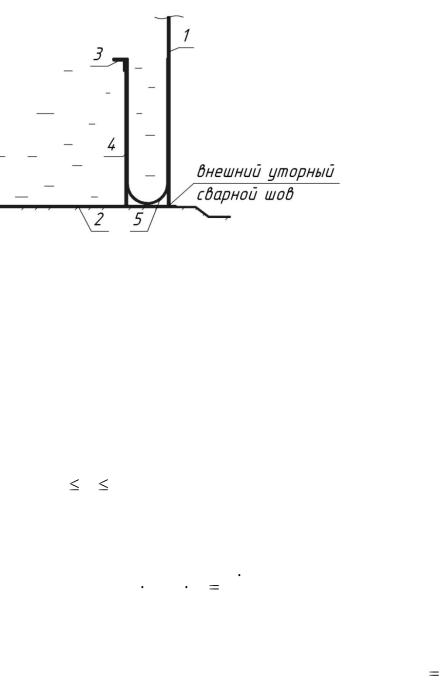
74
В диссертации Землянского А.А. [7] выполнен анализ НДС РВС большого объѐма с помощью общей теории расчѐта коротких цилиндрических оболочек. Показано, что уторный узел сопряжения стенки и днища практически у всех типовых резервуаров большого объѐма работает не в упругой, а в пластической стадии деформирования металла. Была разработана новая конструкция уторного узла сопряжения стенки 1 и окрайки 2 (рис. 1) с использованием кольцевого компенсатора 5 и одноступенчатой гермозоны, характеризуемая высокой технологичностью при изготовлении, низкой материалоемкостью и высокой эксплуатационной надежностью [7].
Рис.1. Конструктивная схема уторного узла с компенсатором по [7]
В предложенной конструкции уторного узла вертикальная стенка изза одностороннего внешнего закрепления работает шарнирно. В случае локального разрушения внешнего сварного шва не происходит утечки хранимого нефтепродукта, так как имеется кольцевой компенсатор. Это позволяет без вывода резервуара из эксплуатации восстановить разрушенный сварной шов.
Алгоритм расчѐта новой конструкции узла сводится к следующим основным моментам:
1. Назначаем диаметр d формообразования нижней зоны
компенсатора 5 – 15 см |
d 50 см (рис. 2). |
|
|
|
2. Составляем |
условие |
равновесия |
стенки |
компенсатора, |
удерживаемого в проектном положении только за счѐт еѐ трения о кольцевое ребро жесткости 4 и вертикальную стенку 1:
q hmin |
f |
q d |
(1) |
|
|
|
|||
2 |
|
|||
|
|
|
|
|
где q - интенсивность гидравлической нагрузки от нефтепродукта; |
|
|||
hmin - минимальная высота вертикальной стенки компенсатора 5; |
||||
f - коэффициент трения стали о сталь, в соответствии с [8] f |
0,18 ; |
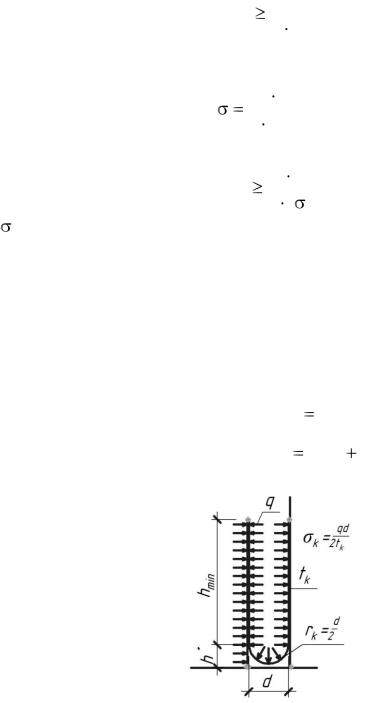
75
hmin |
|
|
d |
|
|
|
|
(2) |
|
|
|
|
|
|
|
|
|||
2 |
f |
||||||||
|
|
||||||||
3. Определяем уровень меридиональных напряжений в нижней зоне |
|||||||||
компенсатора: |
|
|
|
|
|
|
|
|
|
|
q d |
|
|
|
|
(3) |
|||
|
|
|
|
|
|
|
|
||
|
2 tmin |
|
|
|
|
||||
|
|
|
|
|
|
||||
где tmin - минимальная толщина рабочей стенки компенсатора 5; |
|
||||||||
tmin |
|
|
q |
d |
(4) |
||||
|
|
|
|
|
|
|
|||
2 [ |
] |
||||||||
|
|
где [ ] - допустимое меридиональное напряжение в материале компенсатора.
4. Задаѐмся толщиной кольцевого ребра жесткости 4, принимая во внимание необходимость увеличения жесткости днища в зоне уторного шва и тот факт, что рассматриваемый кольцевой элемент находится практически в полностью уравновешенном состоянии, с учѐтом принципа равнопрочности. Наиболее рационально указанную толщину принять равной толщине стенки резервуара именно в зоне уторного шва.
5. |
h* |
|
d |
|
(5) |
|
|
|
|
|
|||
|
2 |
|
|
|||
|
|
|
|
|
|
|
6. |
h |
h |
min |
h* |
(6) |
|
|
полн |
|
|
|
7.Проводим численный расчѐт в программном комплексе.
Рис.2. Расчѐтная схема уторного узла с компенсатором
С помощью системы трехмерного твердотельного моделирования КОМПАС-3D была создана модель уторного узла (рис. 3).
Представляет интерес численный расчет конструкции узла в программном комплексе MSC/Nastran с учетом геометрической неизменяемости и упругой работы материала.
Задачи расчета и конструирования уторного узла являются важными и актуальными, особенно в резервуарах больших объѐмов.
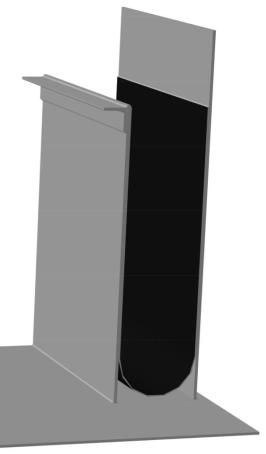
76
Рис. 3. Трехмерная твердотельная модель уторного узла с компенсатором
Литература
1.Дмитриев, Н.Н. Методика моделирования нефтяных стальных вертикальных цилиндрических резервуаров для испытания их конструкций на прочность в условиях лаборатории : автореф. дис. канд… техн. наук / Н. Н. Дмитриев. – М., 1985.
2.Купреишвили, С.М. Механика разрушения вертикальных цилиндрических резервуаров / С.М. Купреишвили // Промышленное и гражданское строительство. – 2004. – № 5. – С. 40-42.
3.Землянский, А.А. Оценка напряжѐнно-деформированного состояния нефтеналивных резервуаров/ А.А. Землянский// Промышленное
игражданское строительство. – 2004. – № 11. – С. 37-41.
4.Холопов, И.С. Обеспечение несущей способности узла сопряжения стенки и днища взрывозащищѐнных вертикальных цилиндрических стальных резервуаров / И.С. Холопов, Э.Я. Еленицкий, О.А. Ковальчук, С.Э. Еленицкий // Промышленное и гражданское строительство. – 2010. – № 7. – С. 52– 54.
5.Колесов, А.И. Напряженно-деформированное состояние зоны сопряжения стенки и днища вертикального сварного цилиндрического резервуара низкого давления/ А.И.Колесов, М.А.Агеева, И.А. Ямбаев // Приволжский научный журнал – 2010. – № 3. – С. 50-56.
77
6.ПБ 03-605-03. Правила устройства вертикальных цилиндрических стальных резервуаров для нефти и нефтепродуктов: [Электронный ресурс] утв. Госгортехнадзором России 09.06.03: взамен ПБ 03-381-00. – Режим доступа: Стройконсультант.
7.Землянский, А.А. Принципы конструирования и экспериментально-теоретические исследования крупногабаритных резервуаров: автореф. дис. канд… техн. наук/ А.А. Землянский. – Балаково, 2006.
8.СНиП II – 23 - 81*. Стальные конструкции: строит. нормы и правила: утв. Госстроем СССР 14.08.81: взамен СНиП II - В.3 - 72; СНиП II
-И.9 - 62 ; СН 376 - 67: дата введ. 01.01.82. – М.: ЦИТП Госстроя СССР,
1990. – 96 с.
УДК 691.33
Д.А. Самиев
Исследование шлакощелочных вяжущих из отходов производства
Одним из важнейших строительных материалов является портландцемент. Однако в последние годы цена на него необоснованно росла. К тому же периодически возникает дефицит цемента, что ведѐт к появлению на рынке некачественных, недомолотых, а то и поддельных цементов. Это несѐт угрозу снижения качества при производстве изделий из бетона.
Альтернативой портландцементу может стать шлакощелочной цемент – цемент, состоящий преимущественно из отходов производства: золы, шлака, молотого стекла и т.п., затворяемый водными растворами щѐлочи, кальцинированной или каустической соды, фтористого натрия, метасиликата натрия или отходами производства щелочей.
Прочность шлакощелочных бетонов может достигать 150 МПа, морозостойкость – 1000 циклов. Из шлакощелочного цемента можно изготавливать как плотные, в т.ч. лѐгкие, так и ячеистые бетоны.
С целью оценки возможности и перспектив применения шлакощелочных цементов из местных отходов производств была проведена серия опытов.
В качестве вяжущего применялись молотое силикатное строительное стекло и зола одной из ТЭЦ. В качестве добавок применялись молотый керамзит, гипс и жидкое натриевое стекло с плотностью 1,5 г/см³. Затворителем служил раствор едкого натра.
На первом этапе исследовалась прочность цементного камня на молотом стекле и золе при различном расходе едкого натра. Составы смесей приведены в табл. 1. Во всех составах добивались одинаковой консистенции теста корректировкой расхода раствора едкого натра.
78
|
|
|
|
|
Таблица 1 |
|
|
|
Составы смесей |
|
|
|
|
Номер |
|
|
Расход на замес, г |
|
|
|
состава |
Молотое |
Зола |
Молотый |
Гипс |
Концентрация |
|
|
стекло |
|
керамзит |
|
раствора NaOH |
|
1 |
85 |
- |
18 |
5 |
32 |
|
2 |
- |
108 |
- |
- |
40 |
|
3 |
85 |
- |
18 |
5 |
32 |
|
4 |
- |
108 |
- |
- |
40 |
|
5 |
85 |
- |
18 |
5 |
32 |
|
6 |
- |
108 |
- |
- |
40 |
|
7 |
85 |
- |
18 |
5 |
32 |
|
8 |
- |
108 |
- |
- |
40 |
|
9 |
85 |
- |
18 |
5 |
34 |
|
10 |
- |
108 |
- |
- |
40 |
|
В табл. 2 приведены результаты испытаний на прочность образцов – кубов с ребром 2 см, изготовленных из этих смесей, выдержанных 3 суток при комнатной температуре и пропаренных при температуре изотермической выдержки 85 °С.
|
|
|
Таблица 2 |
|
|
Результаты испытаний |
|
|
|
№ состава |
Вяжущее (основной |
Концентрация |
Предел прочности при |
|
компонент) |
NaOH, % |
сжатии, МПа |
|
|
|
|
|||
1 |
Молотое стекло |
25 |
31,8 |
|
2 |
Зола |
6,1 |
|
|
|
|
|||
3 |
Молотое стекло |
30 |
23,3 |
|
4 |
Зола |
8,4 |
|
|
|
|
|||
5 |
Молотое стекло |
35 |
29,7 |
|
6 |
Зола |
17,1 |
|
|
|
|
|||
7 |
Молотое стекло |
40 |
40,8 |
|
8 |
Зола |
15,0 |
|
|
|
|
|||
9 |
Молотое стекло |
50 |
29,6 |
|
10 |
Зола |
15,7 |
|
|
|
|
Очевидно, что молотое стекло позволяет получить прочность в 2-
5раз бόльшую, чем зола.
Сувеличением концентрации щѐлочи до (35 – 40) % возрастает прочность камня. Исключение составил состав № 1, что требует дальнейшей проверки.
На втором этапе исследовалась прочность строительных растворов на молотом стекле. Одновременно изучалось влияние тонкости помола компонентов вяжущего на прочность строительных растворов. Составы приведены в табл. 3.
79
|
|
|
|
|
|
|
|
Таблица 3 |
|
|
|
|
Составы смесей |
|
|
|
|||
|
|
|
|
Расход на замес, г |
|
|
|
||
Номер |
Молотое |
Молотый |
|
Гипс |
NaOH |
|
Песок |
Жидкое |
|
замеса |
стекло |
керамзит |
|
|
40 %-ный |
|
речной |
стекло |
|
|
|
|
|
|
раствор |
|
|
|
|
18 |
851 |
181 |
|
5 |
32 |
|
- |
- |
|
19 |
852 |
181 |
|
5 |
33 |
|
- |
- |
|
20 |
851 |
182 |
|
5 |
32 |
|
- |
- |
|
21 |
852 |
182 |
|
5 |
33 |
|
- |
- |
|
24 |
94 |
20 |
|
5,5 |
38 |
|
120 |
- |
|
25 |
76 |
16 |
|
4,5 |
35 |
|
144 |
- |
|
26 |
63 |
13 |
|
4 |
33 |
|
160 |
- |
|
27 |
94 |
20 |
|
5,5 |
38 |
|
120 |
5 |
|
28 |
94 |
20 |
|
5,5 |
39 |
|
120 |
10 |
|
29 |
94 |
20 |
|
5,5 |
35 |
|
120 |
15 |
|
30 |
94 |
20 |
|
5,5 |
32 |
|
120 |
20 |
|
1 Материал, не разделенный на фракции |
после помола. |
|
|
|
|||||
2 Материал, прошедший сквозь сито № 005. |
|
|
|
Из замесов формовались образцы – кубы с ребром 2 см, которые после 3-суточной выдержки при комнатной температуре пропаривались и испытывались на прочность при сжатии. Результаты испытаний приведены в табл. 4.
Таблица 4
|
Результаты испытаний |
№ состава |
Предел прочности при сжатии, МПа |
18 |
65 |
19 |
68 |
20 |
52 |
21 |
66 |
24 |
39 |
25 |
35 |
26 |
20 |
27 |
45 |
28 |
36 |
29 |
47 |
30 |
60 |
Как и следовало ожидать, уменьшение среднего размера зѐрен стекла приводит к повышению прочности камня на 5-27 %, несмотря на повышение водопотребности на 3 %.
Увеличение тонкости помола керамзита, наоборот, привело к снижению прочности камня на 2-20 %, при этом водопотребность теста не изменилась. Таким образом, можно сделать вывод о том, что в данной системе частицы молотого керамзита не проявляют химической активности, и их введение в состав вяжущего нецелесообразно.
80
Увеличение доли песка в составе раствора закономерно снижает прочность материала: с 65 МПа при Ц (молотые стекло и керамзит + гипс):
П = 1 : 0 до 20 МПа при Ц : П = 1 : 2.
Добавка жидкого стекла оказала неоднозначное влияние на прочность строительных растворов. При расходах 4 – 8 % от массы вяжущего водопотребность смеси практически оставалась постоянной, а прочность изменялась в пределх от минус 8 до плюс 15 %. При расходах жидкого стекла 13 и 17 % водопотребность уменьшилась соответственно на 8 и 16 %, а прочность выросла на 21 и 54 %.
Таким образом, молотое силикатное стекло проявило значительно бόльшую активность по сравнению с золой при использовании в качестве вяжущего.
УДК 539.3
С.М. Синягин, Т. В. Сухова
Анализ экспериментально-теоретических условий разрушений трубопроводов с целью разработки методики оценки их долговечности
Растущие мощности промышленных производств, а так же прикладных наук позволяют на данном этапе развития проектировать как новые виды конструкций трубопроводов, отвечающих новым условиям прочности и долговечности, так и совершенствовать уже производящиеся. Долговечность работы конструкции зависит от множества факторов, и влияние дефектов на долговечность стоит в этом вопросе, не на последнем месте.
Данное исследование является продолжением работы Аистова А.С., посвященное исследованию малоцикловой усталости труб магистральных газо- и нефтепроводов. Работа основных элементов линейной части конструкций (труб большого диаметра) обуславливается нестационарностью нагружения их внутренним давлением. Известно [1, 2], что циклическая долговечность сварных труб большого диаметра зависит от величины местных деформаций в зоне сварного шва. Местное возмущение напряженного состояния в сварном соединении трубы обусловлено наличием усиления шва, дефектов в виде подрезов и непроваров шва, смещением кромок в шве, угловатостью в области продольного сварного шва, а также овальностью сечения.
В работе [3] были проведены натурные испытания сварных труб большого диаметра на стационарную и нестационарную нагрузку. Испытания показали, что разрушение данных конструкций происходит по различным сценариям в зависимости от вида нагружения.
Типичное разрушение для стационарного избыточного внутреннего давления представляет собой разрыв металла с большими пластическими деформациями (рис 1). Характерным является выраженная пластичность