
9372
.pdf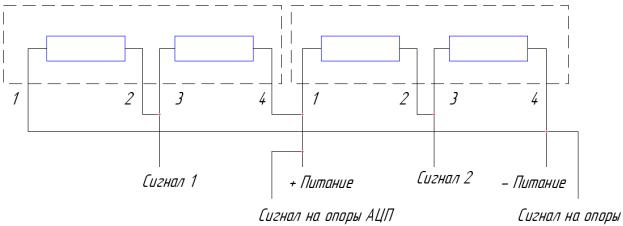
81
Рисунок 3.10 – Мостовая схема включения датчиков
Тензорезисторы датчиков включены в мостовую схему. К одной диагонали моста подключается питание и, одновременно, снимается сигнал опорного напряжения АЦП (аналогового цифрового преобразователя). За счѐт этого достигается компенсация погрешности соединительных кабелей.
Электрический сигнал разбаланса моста снимается с выводов Датчик М1,
М2. Электрические сигналы разбаланса моста и сигналы опоры АЦП поступают на разъѐм ДАТЧИК в блок весового терминала.
Весовой терминал расположен в специальном корпусе, имеющем класс защиты 1Р65. В корпусе расположены:
–плата блока питания;
–плата процессора;
–плата предварительных усилителей.
Главным элементом системы управления является IBM –
совместимый индустриальный компьютер, в котором находится управляющая программа бетоносмесительного узла, а также сервисное и диагностическое программное обеспечение. Индустриальный компьютер хранит базу данных системы и настроен таким образом, что при включении питания автоматически загружается программа управления бетоносмесительного узла. Индустриальный компьютер может быть включен в локальную сеть Ethernet 10/100 Mb.
82
Индустриальный компьютер содержит интеллектуальную плату АЦП,
на которую поступают сигналы с датчиков и усилителей веса, объема,
влажности, тока и температуры.
Индустриальный компьютер содержит модули дискретного ввода /
вывода сигналов TTL уровней. Входные дискретные сигналы поступают через модули сопряжения от датчиков, выключателей и органов управления системы. Выходные дискретные сигналы выдаются через модули ключей и далее через модули твердотельных реле на исполнительные механизмы
(пускатели и пневмораспределители).
Команды оператора системы вводятся через стандартную клавиатуру.
Информация о состоянии бетоносмесительного узла и значения, вводимых оператором данных, выводятся на SVGA монитор.
Каналы измерения веса содержат тензорезисторные датчики веса и нормирующие усилители с выходным сигналом (0…5) В. Канал измерения объема содержит ультразвуковой датчик уровня и обеспечивает линейное измерение уровня заполнения дозатора, пересчет данных в объем обеспечивает индустриальный компьютер. Канал измерения влажности содержит СВЧ влагомер с унифицированным выходным сигналом (4…20)
мА. Каналы измерения тока содержат трансформатор тока и согласующий усилитель с выходным сигналом (0…5) В. Каналы измерения температуры содержат медное термосопротивление с унифицированным выходным сигналом (4…20) мА.
Контроллер управления подачей материалов и транспортом,
расположенный в шкафу управления системы, обеспечивает управление соответствующими подсистемами. Контроллер по собственной программе опрашивает интеллектуальные модули цифрового ввода / вывода и аналогового ввода и выдает необходимые управляющие команды. Для связи контроллера с модулями используются два сегмента RS-485. Контроллер связан с индустриальным компьютером по каналу RS-232.
83
Пульт ручного управления предназначен для ручного управления исполнительными механизмами дозаторного и смесительного отделений и включается в работу после поворота специального ключа. Дозирование компонентов с пульта ручного управления возможно только после ввода заявки на приготовление бетонной смеси. Пульты ручного управления складом заполнителей, подачей материалов и транспортом включаются в работу поворотом специального ключа, при условии разрешения ручной работы соответствующей подсистемы оператором.
В качестве примера реализации системы управления с обратной связью рассмотрим систему управления БСУ Besser.
Основу системы составляет промышленный компьютер ROBO-2000
(IPC2U), в котором установлен адаптер дискретного ввода-вывода PCI-7296 и
сетевая карта. Компьютер соединѐн через пульт ручного управления со шкафом УСО, в котором расположены модули ввода-вывода G5 с
гальванической развязкой (Opto 22). Шкаф управления кабелями соединѐн с датчиками и исполнительными механизмами. Каналы измерения веса компонентов построены на основе тензорезисторных S-образных датчиков
RL20000 и весовых терминалов «Тензо-М», подключѐнных к промышленному компьютеру через адаптер RS-232/RS-485. Канал измерения влажности использует цифровые высокоточные СВЧ-датчики влажности песка HP-02 и бетонной смеси HM-06, которые объединены по интерфейсу
RS-485; через преобразователь RS-485/USB обработанная информация о влажности поступает в компьютер. Свободный аналоговый выход датчика
HM-06 выведен на цифровой индикатор ручного пульта управления для дополнительного визуального контроля. Канал измерения расхода воды построен на основе датчика PFT-1E (Badger Meter), а каналы измерения расходов добавок и красителей — на основе акустических счѐтчиков жидкости с частотным выходом. В системе предусмотрен пульт ручного управления исполнительными механизмами с индикацией их состояния и переключением режимов работы. В качестве концевых датчиков
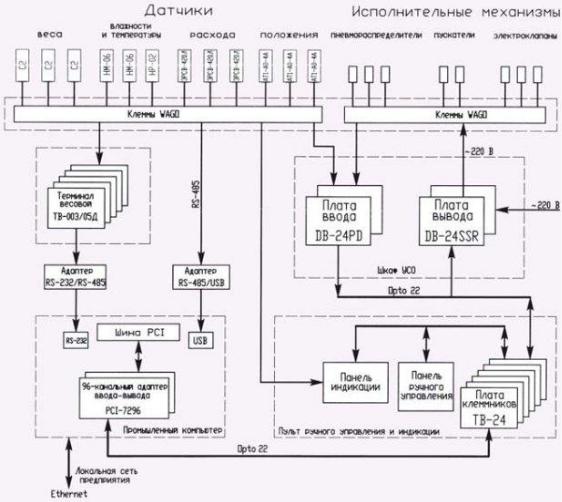
84
применяются индуктивные датчики фирмы Omron или отечественный аналог датчиков немецкой фирмы Balluff – индуктивные датчики фирмы «Мега-К».
Для контроля уровня в бункере цемента используются датчики Pointek VLS
200.
Программное обеспечение системы Besser написано на языке С++ и
функционирует в среде MS Windows XP на ПЭВМ стандартной конфигурации, расширенной оборудованием для цифрового ввода-ввода и связи с весовыми терминалами.
В качестве более простого примера современной системы автоматизации БСУ рассмотрим систему Dozer. Структурная схема этой системы представлена на рисунке 5.7.
Рисунок 3.11 – Структурная схема системы управления БСУ Dozer
|
|
85 |
|
Основу |
системы |
составляет промышленный |
компьютер с |
процессором Pentium 4/2,4 ГГц, в котором установлены два адаптера дискретного ввода-вывода PCI-7296 на 96 каналов каждый, совместимые с
Opto 22. Компьютер через пульт ручного управления, в котором расположены платы клеммников ТВ-24, соединѐн с 24-канальными платами ввода DB-24PD и 24-канальными платами вывода DB-24SSR, находящимися в шкафу со степенью защиты IP66. Шкаф кабелями соединѐн с индуктивными датчиками положения AT1-A0-4A и исполнительными механизмами, для подключения которых в местах установки оборудования используются монтажные корпуса Schroff с установленными на DIN-рейке клеммами WAGO. Каналы измерения веса компонентов построены на основе
тензорезисторных датчиков |
и весовых терминалов, |
подключѐнных |
с |
|||||
промышленному компьютеру через адаптер RS-232/RS-485, а канал |
||||||||
измерения |
влажности |
использует СВЧ-датчики HP-02 |
и |
HM-06, |
||||
объединѐнные по интерфейсу RS-485 и через преобразователь RS-485/USB |
||||||||
подключѐнные к компьютеру. На сегодняшний день |
цифровые СВЧ- |
|||||||
датчики HM-06–единственные |
датчики, |
которые |
|
работают |
в |
|||
отечественных бетоносмесителях типа СБ-138. |
Каналы |
измерения |
расхода |
воды и добавок построены на основе электромагнитных счѐтчиков жидкости ЭРСВ-420Л, сигналы с частотных выходов которых через адаптер дискретного ввода-вывода поступают в компьютер. В системе предусмотрен пульт ручного управления исполнительными механизмами с индикацией их
состояния и переключением режимов работы
(ручной/автоматический); рабочее место оператора, где установлен пульт ручного управления, также имеет панель индикации веса материалов в дозаторах, расходов воды и добавок, влажности бетонной смеси.
Система автоматизации Dozer проще в реализации, но основными ее недостатками являются отсутствие обратной связи по влажности и темпера-
туре при дозировании компонентов бетонной смеси и невозможность распы-
ла воды в смесителе, необходимого при приготовлении жѐстких смесей.
86
Описание функционирования системы Dozer:
В начале смены оператор вводит необходимые данные для инициали-
зации системы, такие как наличие компонентов в расходных бункерах, влаж-
ность компонентов по данным лаборатории для тех из них, которые не кон-
тролируются датчиками влажности. Оператор также вносит заявки на приго-
товление бетонной смеси и, если необходимо, корректирует порядок выгруз-
ки компонентов из весовых дозаторов в смеситель, временную диаграмму выгрузки компонентов в смеситель, параметры технологического процесса.
Система рассчитывает параметры замеса и общее количество замесов, учи-
тывает влажность компонентов, контролирует выполнение необходимых ус-
ловий для начала технологического процесса.
При последующей работе основная задача оператора – ввести заявки на приготовление бетонной смеси и контролировать процесс приготовления смеси в каждом из бетоносмесителей. Затем открываются затворы расходных бункеров и производится двухстадийное (грубое и точное) дозирование ком-
понентов бетонной смеси по весу (кроме воды и добавок). После оконча-
ния процесса дозирования исходные компоненты из дозаторов перегружают-
ся в смеситель. Оператор в реальном времени видит на экране монито-
ра график изменения влажности компонентов бетонной смеси. Водоцемент-
ное отношение контролируется по показаниям установленного в смесителе СБ-138 датчика HM-06, а не по изменению нагрузки на двигатели смесителя.
Датчик влажности HM-06 также выдаѐт текущую температуру смеси.
Весь технологический процесс постоянно контролируется. При любых отклонениях его текущих параметров или ошибках в работе оборудова-
ния система управления выдаѐт соответствующее сообщение оператору и в случае выхода значений текущих параметров за заранее установленные пре-
дельные значения запрашивает вмешательство оператора. После каждого за-
меса или после выполнения всей заявки система формирует и записывает со-
ответствующие отчѐты. Это позволяет вести полный учѐт заявок, отгрузок потребителю, расхода компонентов и выхода бетона.
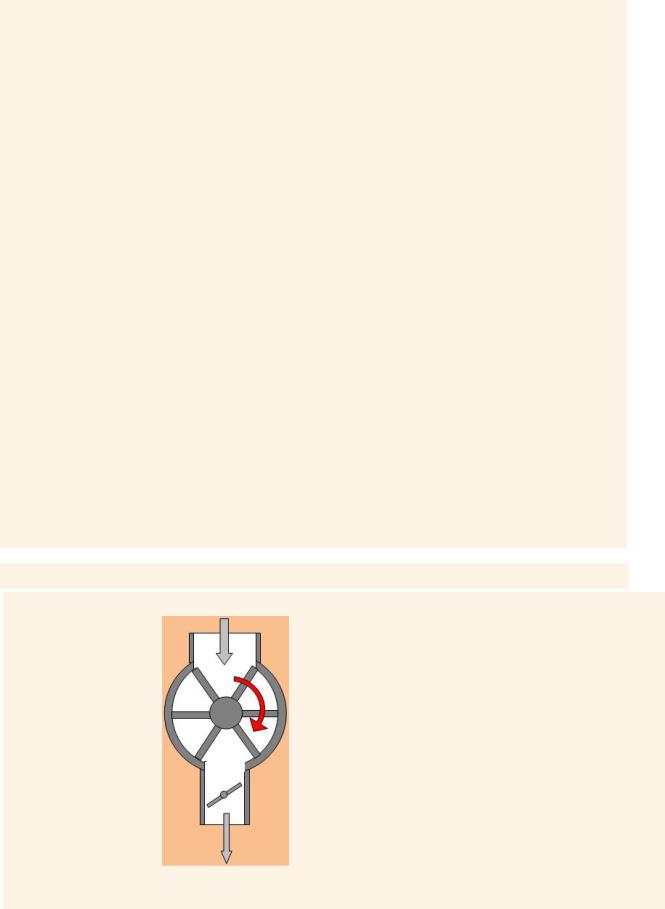
87
Технические новшества
ООО «Фирма «Скалес» занимается разработкой и модернизацией как самого оборудования, так и систем автоматизации для различных по произ-
водительности бетонных заводов – от крупных стационарных предприятий до небольших мобильных РБУ и БСУ, асфальтобетонных заводов (АБЗ), ас-
фальтосмесительных установок типа ДС-158, ДС117, «Тельтомат» и т. п.,
является производителем бетонных заводов СДМ-40.
Для предприятий, занимающихся выпуском бетона, растворобетон-
ных и асфальтобетонных смесей, в условиях высокой конкурентности наибо-
лее важным является производство качественной продукции и бесперебойная работа оборудования. Качество производимых смесей напрямую зависит от точности дозирования ингредиентов и поддержания в норме всех технологи-
ческих параметров. При этом не менее важными становятся возможность управления дозированием компонентов бетонных смесей в ручном, полуав-
томатическом и автоматическом режимах работы, накопления и хранения информации по событиям и авариям, а также учет затрат материалов в про-
цессе приготовления бетонных смесей. Обеспечить выполнение всех этих требований может только АСУ.
Дозирование цемента
.
Вход материала из расходного бункера D = 250 мм, выход материала в дозатор D
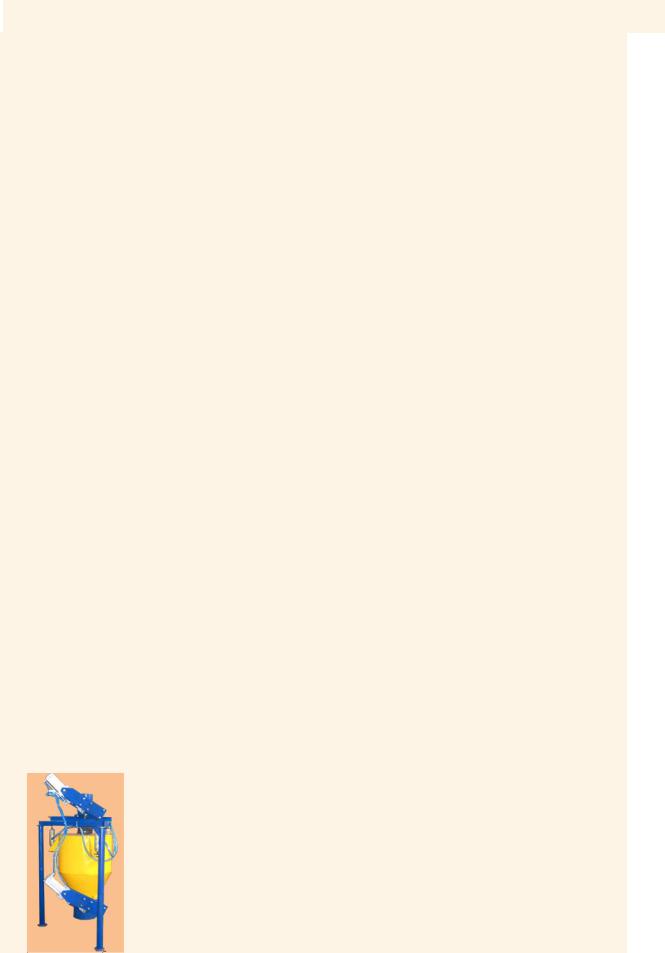
88
= 150 мм.
Подача цемента в дозатор осуществляется шлюзовым (камерным) пи-
тателем.
Материал (цемент) попадает в питатель самотѐком под действием си-
лы тяжести через входную трубу диаметром не менее 250 мм. Для более лучшего наполнения питателя можно применять аэрацию. Наиболее эффек-
тивна аэрация импульсами 1 сек.-подача воздуха, 1 сек –пауза в течение 50%
набора дозы. Камеры питателя герметично защищены друг от друга, поэтому цемент, даже под давлением не проникает в выходную трубу при неподвиж-
ном роторе.
-Скорость вращения ротора 0,7 об/сек.
-Производительность 800 кг/мин.
-Коэффициент наполнения камер 0,5.
Поскольку объѐм одной камеры фактически вмещает около 6 кг це-
мента, то дискрета дозирования может быть максимально равна объѐму ка-
меры. Для повышения точности дозирования необходимо применение за вы-
ходной трубой питателя герметичного затвора «баттерфляй», открываемый синхронно с включением двигателя питателя.
Основными преимуществами данного питателя перед шнековым транспортѐром, оснащенным затвором «баттерфляй» является простота об-
служивания. Снятие боковой крышки питателя для удаления инородинород-
ных предметов (ботинок, электродов, камней и т.п.) занимает не более 2-5
минут. Так же удаление инородных предметов возможно с помощью вклю-
чения реверса двигателя питателя.
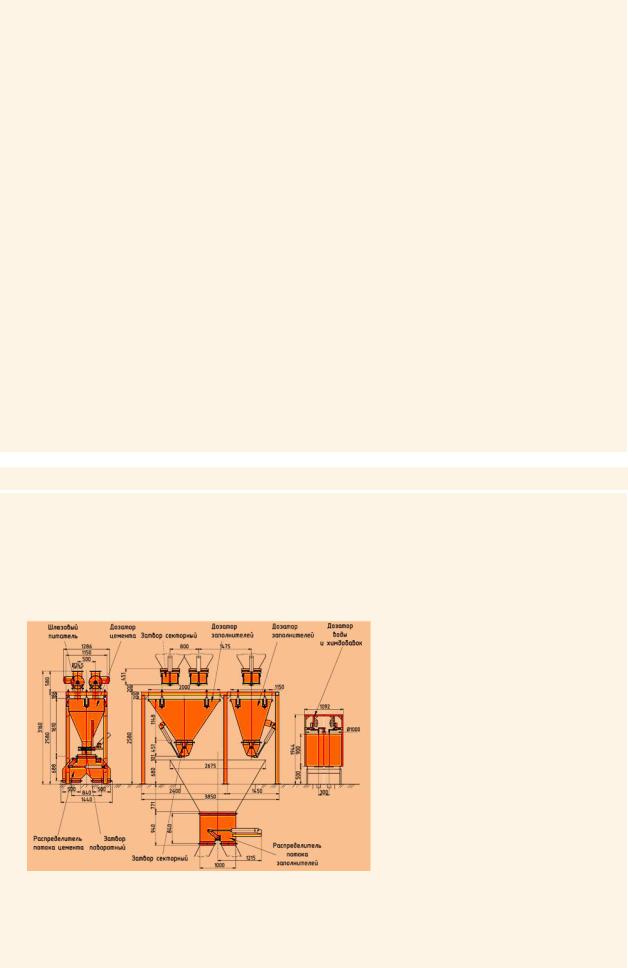
89
Дозирующая ѐмкость дозатора вывешивается на три датчика растяже-
ния. Ёмкость вмещает в себя 600 кг. цемента для работы с бетоносмесителем
1,0 м3 по выходу. Выходная труба D = 250 мм. Оснащена герметичным дис-
ковым затвором. Объѐм дозирующей ѐмкости и объѐм за герметичной за-
слонкой сообщаются между собой «дыхательной» трубой Dу = 80 мм.
Скорость выхода цемента из дозатора примерно 150-250 кг./сек.
Дозирующая ѐмкость вместе с питателями смонтирована на единой раме устанавливаемой на пол дозировочного отделения
Недостатком питателя является невозможность размещение дозатора цемента в стороне от выходного отверстия расходного бункера (склада це-
мента).
В целом дозатор обеспечивает дозирование цемента от 10 до 600 кг за время не более
40 сек. с точностью +/- 1 кг.
Дозирование заполнителей
Как правило, на БСУ заполнители дозируются из 6 расходных бунке-
ров. Наиболее целесообразно использовать два дозатора, один на дозирова-
ние четырѐх компонентов и другой на два компонента с наибольшими пре-
делами дозирования 2500 кг и 2000 кг соответственно.
Четыре расходных бункера оснащаются датчиками влажности. Мате-
риал из данных расходных бункеров используется для изготовления из делий сборного железобетона из жѐстких бетонов. Два других бункера датчиками

90
влажности не оснащаются, и материал из бункеров используется для приго-
товления товарного бетона и бетонов на полигон.
Секторные затворы расходных бункеров выполняются с противовеса-
ми. Секторные затворы дозирующих бункеров выполняются без противове-
сов.
Четыре расходных бункера оснащаются датчиками влажности. Мате-
риал из данных расходных бункеров используется для изготовления изделий сборного железобетона из жѐстких бетонов. Два других бункера датчиками влажности не оснащаются, и материал из бункеров используется для приго-
товления товарного бетона и бетонов на полигон.
Секторные затворы расходных бункеров выполняются с противовеса-
ми. Секторные затворы дозирующих бункеров выполняются без противове-
сов.
Конусная часть расходного бункера песка оснащается навесным виб-
ратором, включаемый совместно с приводом заслонки расходного бункера.
Автоматика дозирования должна обеспечивать и автоматически выбирать как минимум 3-5 способов загрузки дозирующего бункера. Это связано с тем, что часто требуется дозировать один из компонентов в пределах 100-300
кг. при летящей не взвешенной массе компонента около 250 кг.
Для более точного дозирования песка наиболее целесообразно приме-
нять ленточный питатель. Выходная щель питателя один раз в сезон на-
страивается в зависимости от подвижности песка, напрямую связанную с влажностью.
Фактическое время дозирования трѐх компонентов составляет 15-25 с.
При точности дозы каждого компонента +/- 5 кг.