
книги / Надежность и диагностика технологических систем
..pdf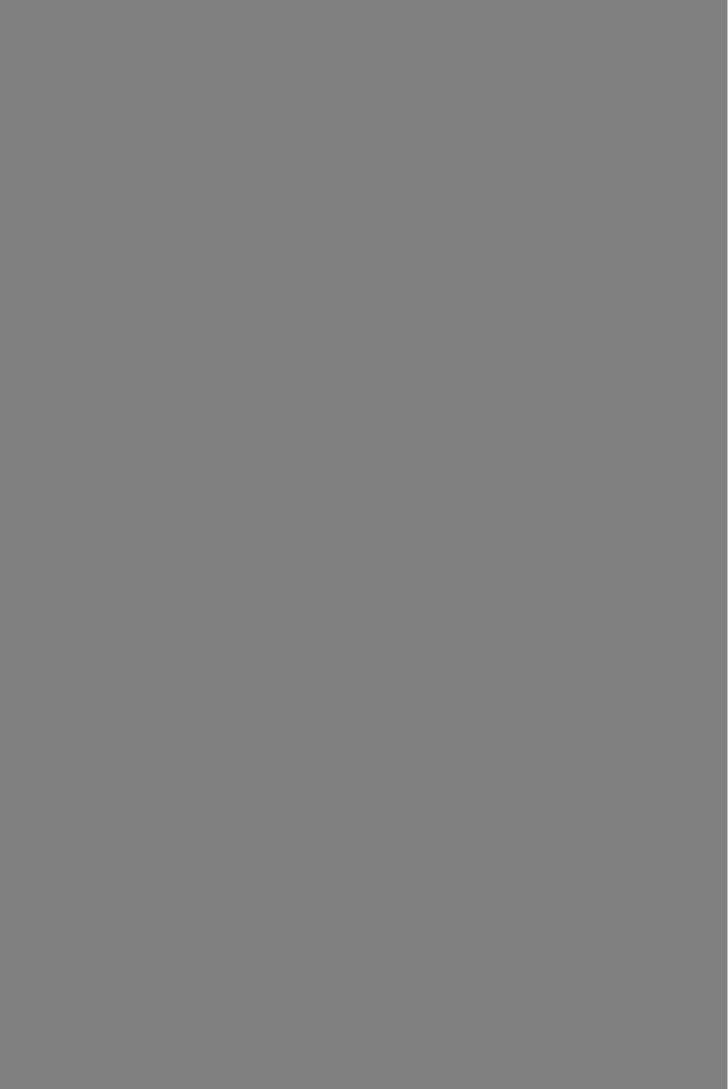
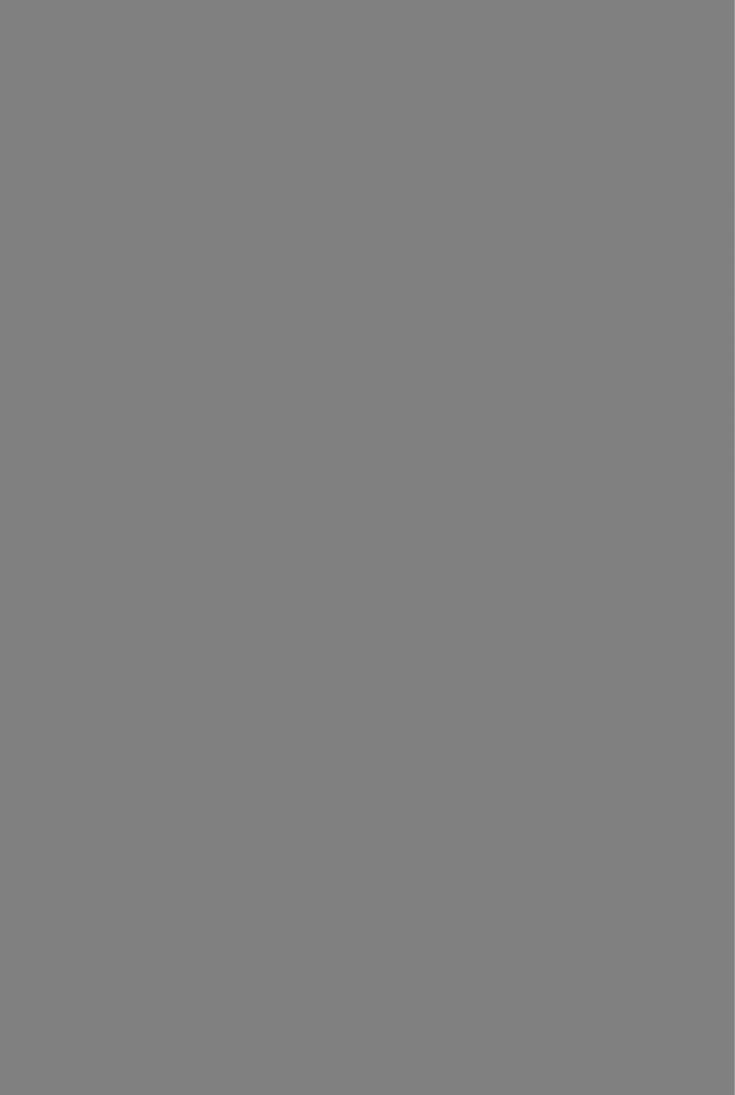

484 14. Управление точностью ТС на основе диагностической информаиии
ческого износа ТКЛ1. Чтобы не допустить брака из-за износа резца, поломок или аварийных ситуаций, менять резец необходимо в зоне At, когда есть еще запас AU (резерв резца по точности) до вхождения в зону ГКЛ1.
Участок Тн<р соответствует нормальной скорости износа, про порциональной пути L, пройденному инструментом при среза нии материала. Для повышения качества и производительности обработки деталей необходимо увеличивать протяженность уча стка Тн.р и уменьшать угол наклона кривой износа а, т.е. сокра щать интенсивность износа. Для удобства сравнения размерной стойкости инструмента пользуются значением удельного износа, под которым понимают величину износа на пути резания 1000 м.
На практике снизить влияние фактора размерного износа по зволяет использование инструмента с меньшей величиной удель ного износа. Например, при точении стали удельный износ сплава Т30К4 равен 0,004 мм, Т15К6 — 0,007 мм, Т5К10 — 0,01 мм, ВК4 — 0,03 мм.
Увеличение размерной стойкости инструмента достигается за счет повышения качества его изготовления, снижения режимов резания, выбора оптимальных режимов заточки и доводки ре жущих кромок, улучшения геометрии, правильного подбора и применения СОТС.
Из-за технической неграмотности и незнания специфики суще ствовало мнение, что преимущества станков с ЧПУ якобы заклю чаются в ужесточении режимов резания, повышенных мощно стях. Это глубоко ошибочное и опасное заблуждение. Наоборот, режимы резания на станках с ЧПУ целесообразно немного (на 15-20 % ) занижать. Таким образом, можно организационными мерами искусственно, целенаправленно, научно обоснованно по вышать уровень надежности и безопасности процесса обработки. Такой подход вытекает из самой специфики станков с ЧПУ и эко номической целесообразности. Нельзя допускать отказа станка с ЧПУ из-за предельного износа инструмента (особенно в усло виях «безлюдной» технологии). Экономически целесообразнее сделать лишний раз автоматическую смену инструмента, чтобы только не допустить отказа ТС из-за поломки или затупления инструмента. На практике иногда даже черновую (грубую) об работку выполняют вначале на универсальных станках, а затем продолжают обработку уже на станках с ЧПУ. Это позволяет
14.2. Методы управления точностью технологических процессов |
485 |
дольше сохранить точностные возможности станков с ЧПУ, высо кий уровень надежности и использовать их более эффективно.
Тепловые деформации резца (и оборудования в целом) вносят постоянно меняющуюся и значительную составляющую в общую (суммарную) погрешность обработки. Удлинение резца за счет тем пературных деформаций достигает значительной величины, зачас тую соизмеримой с требуемой точностью обработки (рис. 14.4, а). Удлинение резца при обработке партии деталей зависит от вре мени, в течение которого резец находится в работе, и перерывов между обработкой двух деталей. Однако рассчитать точно вели чины погрешностей от тепловых деформаций на практике не пред ставляется возможным. Но важно исследовать характер, специ фику и выявить роль тепловых деформаций.
б
5 10 15 t, мин
Рис. 14.4. Тепловые деформации резца:
а — при непрерывной работе; б — в режиме работа — останов; Н^.-Нз — пе риоды кратковременной работы (нагрев); (^...Оз — периоды кратковремен ных остановов (охлаждение)
Тепловые деформации Дти износ зависят в первую очередь от режимов резания:
Дт = f(v, s, *).
Доминирующим фактором здесь является скорость резания v. Кривые нагрева и охлаждения при тепловых деформациях носят экспоненциальный характер (рис. 14.4, б и 14.5, б).
В результате трения стружки о переднюю грань резца и его задней грани о заготовку происходит износ резца по передней и задней грани. Критерием изнашивания по задней грани резца является площадка износа Л3 (рис. 14.5, а). Размерным износом Лр
486 14. Управление точностью ТС на основе диагностической информации
считается радиальное уменьшение резца по задней грани. Посколь ку резец укорачивается, то фактический размер Пф становится больше теоретического DT(на величину hp) и режущая кромка резца сдвигается из точки 1 в точку 2.
б
Рис. 14.5. Одновременное действие износа и тепловых деформаций на параметр *точность размера»
Фактический размер 1)ф формируется под действием одновре менно двух векторных величин — износа Ди и тепловых дефор маций Др. Векторы действуют в противоположных направлениях: износ Ди увеличивает, а тепловые деформации Друменьшают раз мер заготовки Пф непосредственно во время формообразования,
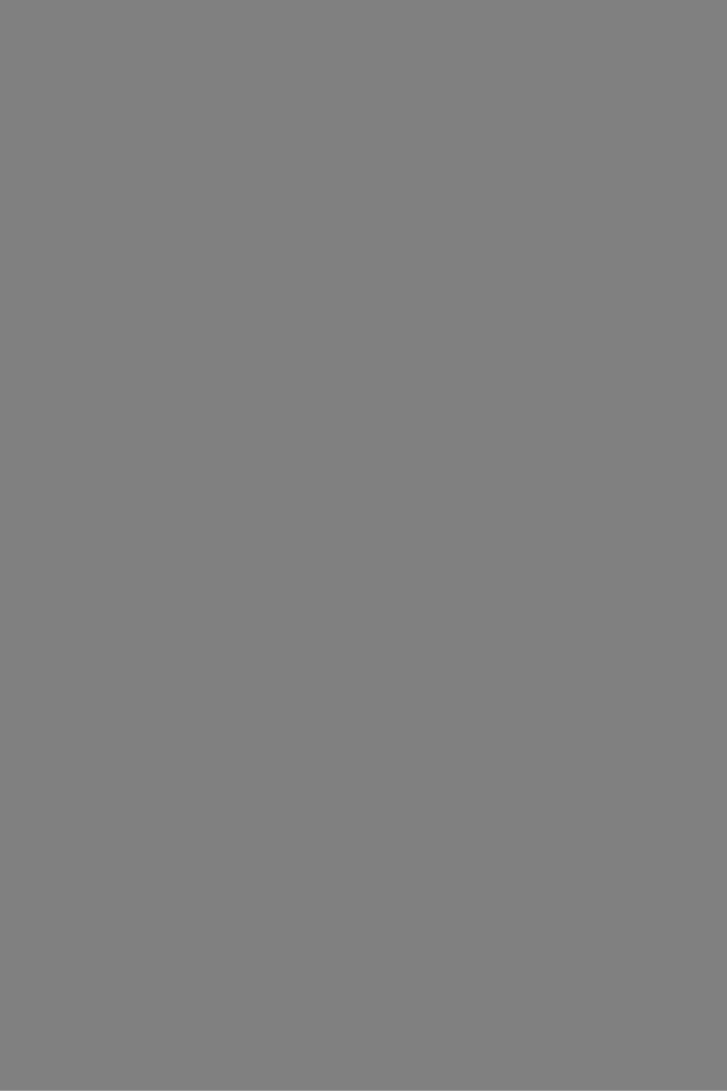
488 14. Управление точностью ТС на основе диагностической информации
и ее анализ. Такой процесс происходит непрерывно. Блок-схема алгоритма опроса датчиков АСД технического состояния РТК приведена на рис. 14.6. Количество датчиков, подключаемых к одному устройству связи с объектом (УСО), равно 15. УСО
Рис. 14.6. Блок-схема алгоритма опроса датчиков АСД технического состояния оборудования:
ОС — операционная система; УС — устройства связи (каналы)
14.3. Алгоритмы управления состоянием и точностью оборудования |
489 |
позволяет компоновать системы различной конфигурации. Для подключения дополнительных датчиков необходимо использо вать УСО.
Блок разъемов УСО рассчитан на установку нескольких ин терфейсных блоков специальной конструкции, в том числе — минимум одного магистрального расширителя, обеспечивающего связь интерфейсных блоков с расположенными на них контрол лерами для управления внешними объектами, о чем выдается сообщение на экран дисплея. Эта функция системы является сер висной и охватывает ряд процедур:
•выдача информации о составе системы (типах и количестве датчиков);
•перечень сообщений, выдаваемых на экран и рекомендуемые действия, которые необходимо предпринять (т.е. диспетчерские функции);
•стирание неверно набранных символов;
•диагностика при наборе неверно набранных символов.
ВСД предусмотрена система прерываний. Каждому объекту диагностирования, а соответственно и датчику, заранее при сваивается приоритет в зависимости от важности объекта (эле мента) в ТС и ТП. Приоритет задается при проектировании АСУТП. На основании анализа элементов объекта по степени важности выбираются контролируемые параметры и последова тельность их обработки.
Алгоритм опроса датчиков предусматривает программную реа лизацию в рамках ОС. Изменение приоритета датчиков (последо вательности опроса) возможно техническими и программными средствами.
Управление объемом снимаемой информации осуществляется заданием соответствующих значений содержимого оперативной памяти ЭВМ. Блоки 3, 4, 7, 9, 10, 11 (рис. 14.6) практически реализуются на одном из алгоритмических языков (например, паскаль, бейсик, ассемблер, СИ). Блок 3 содержит переменную iyc, которая представляет собой ячейку памяти, характеризую щую канал УСО, с которого в данный момент производится ра бота.
Загрузка программ для указанных выше блоков в оператив ную память ЭВМ производится после загрузки ОС в соответствии
синструкцией. Блоки 5 и 6 реализуются в соответствии с видом диагностического признака и алгоритмом оценки технического
490 14. Управление точностью ТС на основе диагностической информации
состояния объекта. В блоке 2 задаются начальные параметры контроля: количество каналов УСО; количество датчиков в ка ждом канале Ыд.
При обнаружении неисправности в нескольких объектах (по ступили прерывания от нескольких датчиков) обработка прерыва ний происходит в соответствии с приоритетом. Вначале обрабаты вается прерывание с более высоким приоритетом, а остальные прерывания временно запоминают.
При обнаружении прерываний на экран дисплея выдается сообщение, а информация о неисправности хранится в памяти машины. Об информации на экран дисплея пользователь сооб щает системе нажатием определенных клавиш, после чего ин формация о неисправности стирается.
В блоке 14 по результатам анализа информации о состоянии контролируемых элементов принимается окончательное реше ние о продолжении (или завершении) процесса контроля.
Совершенствование структуры управления РТК и повышение информативности. Повысить эффективность производства, обеспе чить надежность функционирования оборудования и стабильность выполнения ТП можно за счет организационной структуры авто матизированных ТС, повышения степени информативности и раз работки специальных алгоритмов управления.
Повысить надежность РТК можно за счет создания специаль ной организационной структуры его функционирования, предот вращающей аварии (рис. 14.7). Для этого при управлении роботом нужны дополнительные информационные потоки о состоянии основных элементов РТК (их положении и исправном состоянии, точности срабатывания и выполнения команд, соответствии па раметров и норм). Для повышения надежности предусмотрена специальная система проверки готовности робота еще до начала его работы по УП. Это позволяет исключить нештатные и аварий ные ситуации. Следует иметь в виду, что робот представляет собой объект повышенной опасности. Его надежность должна быть высокой.
Стабильность процесса обработки определяется уровнем на дежности элементов РТК. Повысить надежность можно за счет повышения информативности о состоянии отдельных элемен тов РТК (и точности выполнения заданных функций), исполь зуя специальные технические средства — датчики внутренней и внешней информации.