
книги / Надежность и диагностика технологических систем
..pdf10.2. Системы технической диагностики и контроля |
361 |
Человек получает возможность активно участвовать во всех стадиях подготовки и управления производством, максимально используя широкие возможности современных технических средств автоматизации.
При проектировании ТП и подготовке УП последовательно выполняются типовые этапы и специальные функции:
1)разработка маршрутной технологии — определение соста ва и последовательности операций;
2)разработка операционной технологии с расчетом режимов резания;
3)расчет траектории движения режущих инструментов — координат опорных точек;
4)формирование технологических команд и функций;
5)кодирование информации в кодах ISO;
6)запись УП на программоноситель (или в память ЭВМ);
7)проверка и отладка УП (внесение коррекции).
При разработке маршрутной технологии определяют состав операций, целесообразность выполнения которых на станках с ЧПУ устанавливают на основе технико-экономических расче тов. При автоматизированном проектировании ТП обработки на станках с ЧПУ требуется большая детализация: разбиение всего процесса на операции, установы, позиции, переходы, рабочие и вспомогательные ходы, технологические и вспомогательные команды.
Чертеж изготовляемой детали представляют в виде получен ной от САПР технической документации (на магнитных или электронных носителях). Визуальный контроль такого чертежа (и технической документации) возможен с помощью дисплея ЭВМ.
Программирование ТП изготовления деталей на станках с ЧПУ — качественно новый этап, когда выполняется часть рабо ты (см. этапы 3-7), перенесенная из сферы производства в область технологической подготовки. Действия рабочего при обработке заготовки на обычном станке (после этапов 1-2) выполняются на станках с ЧПУ в автоматическом режиме по УП.
Подготовка УП требует переработки большого объема специ фической информации. Применение ЭВМ для автоматизации про граммирования и подготовки УП потребовало разработки для решения различных технологических и геометрических задач специальных видов обеспечения.
362 |
10. Научный подход и принципы диагностирования ТС |
Совокупность математического и программного обеспечения, а также проблемно-ориентированного языка для записи и ввода в ЭВМ исходной информации при подготовке УП называют си стемой автоматического программирования (САП). В на стоящее время в мире разработаны десятки видов САП, которые различаются степенью и уровнем автоматизации этапов подго товки УП.
Если чертеж изготовляемой детали представлен в традици онном виде, то данные чертежа вводятся в САП с помощью кла виатуры. САП перерабатывает данные чертежа и выдает УП в коде ISO (стандарт ISO 6983). Полученная УП от САП обычно фиксируется в накопителе на магнитном диске (НМД — гибкая дискета или жесткий диск).
Ввод УП производится либо путем установки в дисковод УЧПУ станка ЧПУ, либо путем пересылки УП из САП (жесткого диска) в оперативное запоминающее устройство (ОЗУ) процессорного мо дуля УЧПУ, где формируются сигналы управления и подаются на автоматический привод станка. При одновременном управ лении движением по, двум координатам можно обрабатывать конические и криволинейные поверхности.
Надежность ТС и ТП повышается за счет диагностической информации, поступающей непрерывно от датчиков внутренней и внешней информации, контролирующих состояние основных узлов ТС, а также за счет коррекции УП.
АСД выдает постоянную информацию о состоянии режущего инструмента и основных элементов ТО, участвующего в процес се изготовления деталей.
САК обеспечивает надежный (регламентируемый) контроль точности изготовления деталей и по результатам измерений вы дает информацию для принятия решений в процессе функцио нирования ТС.
Повысить общий уровень надежности при разработке и управ лении ТП позволит информация, накопленная в специальных АСНИ объектов металлообработки и БД.
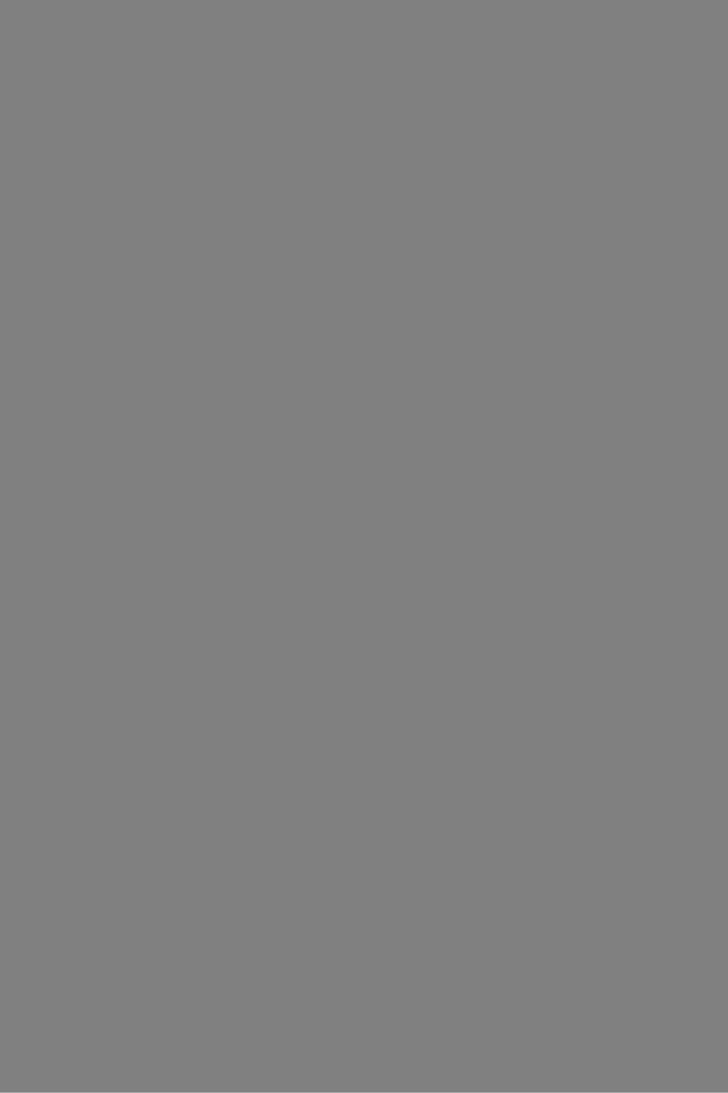

366 10. Научный подход и принципы диагностирования ТС
вающий поддержание на требуемом уровне степени эксплуата ционной готовности системы. В программе эксплуатации закла дываются режимы эксплуатации, контроль и диагностирование состояния системы, выявление отказов и повреждений, обеспе- - чение ее ремонта и восстановления.
Диагностирование повышает уровень надежности, что обес печивает новое качество функционирования ТС: возможность управления процессом функционирования ТС посредством свое временного введения в действие резервных элементов; сигнали зация о моменте наступления отказа, его быстрое обнаружение и локализация; предупреждение о возможном появлении повре ждения или отказа. Например, используя вибродиагностическую аппаратуру, можно заранее по величине вибросигналов спрог нозировать (предсказать) момент наступления отказа.
При наличии средств контроля и диагностики состояния инструмента появляется возможность своевременно в автомати ческом режиме ввести в действие резервный инструмент. Напри мер, в ГПС при организации «безлюдного» функционирования для выполнения одного и того же перехода может быть преду смотрено до 5...6 комплектов резервного инструмента.
Контроль целостности осевого инструмента, выполняемый с использованием фотоэлектрических датчиков или датчиков момента резания, позволяет вовремя зарегистрировать момент поломки.
Диагностирование состояния блоковсистемы ЧПУ позволяет программным способом установить место неисправности с боль шой глубиной проникновения в структуру системы ЧПУ. Боль шими возможностями самодиагностирования обладают совре менные компьютеры и локальные компьютерные сети.
При разработке УП закладываются специальные диагности рующие подпрограммы, позволяющие проводить диагностику основного ПО. Эксплуатация ТС может быть организована на основе применения трех основных стратегий, значительно раз личающихся по своей экономической и технической эффектив ности.
Первая стратегия основывается на календарном времени эксплуатации ТС. Так, при работе АЛ с жесткой связью и высо ким коэффициентом загрузки оборудования может быть реализо ван почасовой или суточный график проведения регламентных работ по очистке АЛ от загрязнений и стружки, смазке станка,
10.4. Организационные стратегии повышения надежности ТС |
367 |
смене, наладке и подналадке режущих инструментов. Режимы резания могут быть рассчитаны и учтены в календарном графи ке проведения регламентных работ.
Для оборудования с высокой степенью надежности (напри мер, для универсальных металлорежущих станков) реализуется система планово-предупредительного ремонта (текущего, сред него, капитального), который проводится по специально установ ленной календарной схеме в течение года или даже ряда лет.
Вторая стратегия основывается на учете фактического вре мени работы основных элементов ТС. С этой целью обеспечива ется учет фактического времени работы каждого контролируемого или диагностируемого элемента. Как только время фактической эксплуатации некоторого элемента системы достигает установ ленного заранее предельного уровня, выдается сигнал о необхо димости замены этого элемента или проведения регламентных работ. Такая стратегия достаточно часто используется в автомати зированном производстве. При этом заранее необходимо устано вить с достаточной степенью надежности ресурсные характеристи ки элементов ТС и вести регистрацию времени их использования по своему служебному назначению. Подобная стратегия эконо мически целесообразна при достаточно малых диапазонах рас сеяния контролируемых параметров.
Третья стратегия использует возможности диагностирова ния ТС. Она базируется на контроле текущего и предельного со стояния элементов ТС. При этом контроль и диагностика могут проводиться как непрерывно, так и периодически. Чем стабиль нее во времени основная характеристика параметра, тем реже может проводиться его контроль.
Могут применяться комбинированные варианты стратегий. Например, механические элементы станков контролируются
иобслуживаются по первой стратегии, электромеханические
иэлектронные блоки — по второй, а режущие инструменты — по третьей.
Рассмотрим возможности и оценим эффективность каждой из трех приведенных стратегий (рис. 10.3). Допустим, что кон тролируемый по лимитирующему параметру элемент ТС имеет произвольную случайную функцию Р - F(t) своей реализации во времени, характеризуемую математическим ожиданием М(£), средним квадратическим отклонением а (£) и автокорреляци онной функцией К [*i(£), x2(f)]. Допустим, что практические
368 |
10. Научный подход и принципы диагностирования ТС |
пределы рассеяния установлены с некоторой достаточно малой зо ной риска, которая меньше погрешности измерения параметра. Учитывая нестабильность процесса, которая всегда присутствует при обработке, можно установить зоны проведения регламент ных работ для всех трех стратегий эксплуатации ТС.
Рис. 10.3. Схема реализации стратегий эксплуатации
технологических систем по i-му параметру
Зона I соответствует стратегии, основывающейся на кален дарном времени эксплуатации системы. Момент начала ее реа лизации Ti можно определить по формуле
Ti = М т-1 /2г1а:(0 - г2с2(£)- АТХ,
где Мт— математическое ожидание времени достижения кон тролируемым элементом (параметром) ТС предельного состояния при гамма-процентном ресурсе 50 %; гъ Gi (£) — соответственно уровень риска и среднее квадратическое отклонение поля рас сеяния контролируемого параметра в направлении временной оси; г2, с2(£) — соответственно уровень риска и среднее квадра тическое отклонение поля рассеяния в направлении оси t при непрерывной работе рассматриваемого элемента ТС; ДТХ— по грешность измерения времени фактической работы ТС.
Рассеяние с параметром a2(t) связано с тем, что фактическое время непрерывной работы ТС за некоторый календарный срок есть величина переменная. Это обусловлено случайным харак-
10.4. Организационные стратегии повышения надежности ТС |
369 |
тером загрузки оборудования. Кроме того, часто устанавливают запас по стойкости инструмента в автоматизированном производ стве. При работе ГПС в третью смену (без людей) принимают рег ламент смены инструмента порядка 50-70 % от его фактической стойкости. За счет этого надежность функционирования ГПС значительно возрастает.
Время Т2начала реализации второй стратегии эксплуатации элемента ТС, который подвергается контролю, определяется с уче том ряда особенностей. Необходимо учесть конкретную величину математического ожидания М т времени Тмдостижения контро лируемым элементом предельного состояния, действительную величину поля рассеяния этого же показателя rLOi(t), а также погрешность контроля фактического времени работы рассмат риваемого элемента АТ2. С учетом перечисленных параметров время
Т2 = Мт— —АТ2.
Математическое ожидание времени срабатывания диагности рующего сигнала по третьей стратегии Т3 зависит от погрешно сти АР контроля параметра. Ей соответствует погрешность ДГ3. Используя обратную функцию (if) = Ф(Р) = Р-1(^), величину АТ3 можно определить по формуле
АТ3 =Ф(Р)-Ф(Р-АР)
или
Т3= Мг —АТ3.
Очевидно, что Т1 < Т2< Т3. Следовательно, ресурс контроли руемого элемента по третьей стратегии используется полнее.
Производительность ТС при применении любой стратегии экс плуатации ее элемента будет меньше теоретической из-за затрат времени на замену отказавшего элемента. Если взять достаточно большой отрезок времени эксплуатации Тэ(год), значительно пре вышающий ресурс эксплуатации элемента ТС (например, инст румента), то за этот период общие непроизводительные потери времени на его замену по каждой из трех стратегий соответст венно равны:
T„i=t,TJTu Тп2 = t0T,/T2, Г„з = t,TJT3,
где t3 — время замены отказавшего инструмента.
370 |
10. Научный подход и принципы диагностирования ТС |
Потери производительности в годовом исчислении можно рас считать по каждой стратегии следующим образом:
ДЩ = Тп1/Тц, ДЦ2 = |
, ДП3 —Упз/Тц, |
где Гц — длительность цикла обработки.
Экономические потери связаны с уменьшением производи тельности ТС и повышенным расходом рассматриваемых эле ментов. Например, годовые затраты на инструмент Яи в случае массового производства деталей одного наименования по каж дой стратегии можно определить по формуле
Cpi = N{(H +П •K)T0/[Ti(K+ 1)] + ДПГ Сд /Г ц},
где N — годовая программа выпуска деталей; Сд— себестоимость рассматриваемой операции, руб.; Н — прейскурантная стоимость инструмента (определяется по данным завода-изготовителя ин струмента), руб.; П — затраты на переточку инструмента; К — число переточек до полного износа (определяется по справоч никам для каждого типоразмера инструмента); — стойкость инструмента между двумя переточками; Т0 — основное время обработки детали на рассматриваемой операции.
Срок окупаемости Ток при внедрении диагностирования по стра тегии третьего типа (по сравнению с первой без применения ТД) можно определить по формуле
Гок=К3/(Ср1-С р2),
где К3— разовые капитальные затраты на внедрение устройства ТД для контроля состояния инструмента при выполнении рас сматриваемой операции.
Очевидно, что срок окупаемости затрат на внедрение СТД дол жен быть небольшим. В условиях массового производства такие затраты в большинстве случаев экономически оправданны. Для условий серийного производства средства СТД должны обладать относительно невысокой стоимостью, универсальностью примене ния и не требовать существенных затрат времени на подготовку и настройку при переходе на изготовление других изделий.