
книги / Трещиностойкость железоуглеродистых сплавов
..pdf
сталлического скола (см. рис. 5.7, а). После двухступенчатого отпуска при 300 и 500 °С (рис. 5.7, в) на поверхности излома наряду с субтранскристаллическими бороздками наблюдаются также и транскри- сталлитно-разрушенные фасетки. При более высоких значениях K в районе Парисова участка диаграммы после отпуска при 440 °С наблюдается сплошной транскристаллитный бороздчатый рельеф (см. рис. 5.7, б). После двухступенчатого отпуска на поверхности излома наряду с транскристаллитным бороздчатым рельефом появляются участки, разрушенные путем транскристаллитного скола (рис. 5.7, г).
Рис. 5.7. Рельеф поверхности усталостных изломов стали ЭП-678 после отпуска 440 °С (а, б) и двойного отпуска 300 °С + 500 °С (в, г): а, в − околопороговый участок; б, г − Парисов участок
В заключение необходимо отметить, что МСС отличаются очень хорошей трещиностойкостью по сравнению с традиционными высокопрочными среднеуглеродистыми сталями. Главной причиной такого высокого сопротивления МСС развитию трещины является полное отсутствие пластинчатого мартенсита, который является причиной интеркристаллитного хрупкого развития трещины Разработка сталей с низким содержанием углерода дает возможность получить при их закалке пакетный мартенсит, который полностью исключает появление фасеток межзеренного скола, характерных для нагружения в присутствии пластинчатого мартенсита.
Очень сильное измельчение некогерентных интерметаллидных фаз, полученных по схеме двухступенчатого отпуска (НТО + ВТО), нежелательно, так как в этом случае при незначительном увеличении
351

на 10–15 % прочности материала существенно снижается его трещиностойкость.
5.4.Влияние рафинирования на прочность
итрещиностойкость МСС
Необходимо отметить, что при традиционном использовании металлургической технологии вакуумно-дугового переплава для окончательного получения слитков, которые после этого подвергаются ковке, характерно наличие неоднородности в свойствах, особенно ударной вязкости. Это вызвано главным образом неравномерным распределением включений и ликвацией примесей. Для того чтобы избежать этих дефектов в структуре слитка, были опробованы два новых металлургических процесса:
–вакуумный электронно-лучевой переплав;
–вакуумно-дуговой переплав в электромагнитном поле.
Таблица 5.6
Результаты статистического анализа динамической и статической трещиностойкости для стали 03Х11Н10М2Т
после различных видов переплава
Температура |
|
Параметры трещиностойкости |
|
|||
отпуска, оС |
КСТ |
SKCT |
WKCT |
KIñ |
SKIñ |
WKIñ |
|
Дж/см2 |
|
МПа.м1/2 |
|
||
|
Вакуумно-электронно-лучевой переплав |
|
||||
500 |
24 |
10 |
0,4 |
86 |
4,2 |
0,05 |
560 |
40 |
8 |
0,2 |
111 |
11,2 |
0,10 |
Вакуумно-дуговой переплав в электромагнитном поле |
|
|||||
500 |
23 |
4 |
0,16 |
88 |
1,2 |
0,014 |
560 |
41 |
3 |
0,07 |
105 |
3,3 |
0,03 |
Примечания: |
S – |
среднеквадратичное отклонение; W |
– коэффициент ва- |
|||
риации. |
|
|
|
|
|
|
Результаты, полученные при исследовании МСС 03Х11Н10М2Т, показывают, что средние значения традиционных стандартных механических свойств, а также трещиностойкость металла, произведен-
352
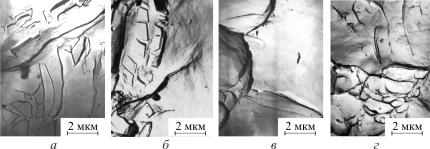
ного с помощью этих металлургических технологий, практически одинаковы. При этом значительна разница в разбросе результатов (табл. 5.6), о чем можно судить по величине среднеквадратического отклонения S .
Рис. 5.8. Рельеф поверхности изломов стали ЭП-678 различных способов переплава (а, б – ВЭЛП; в, г – ВДП в ПФП) после испытаний на динамическую трещиностойкость: а, в – закалка 950 °С, вода; б, г – отпуск 500 °С
Причиной нестабильности уровня трещиностойкости при использовании электронно-лучевого переплава являются скопления неметаллических включений, которые, как утверждают авторы [211, 212], представляют собой карбосульфиды и нитриды титана (рис. 5.8, а, б). При получении металлических слитков с помощью вакуумно-дугового переплава в электромагнитном поле такие скопления неметаллических включений не наблюдаются (рис. 5.8, в, г), что уменьшает разброс характеристик трещиностойкости. Следовательно, для получения изделий с устойчиво высокими значениями трещиностойкости целесообразно, чтобы вакуумно-дуговой переплав был заменен своей модификацией – вакуумно-дуговым переплавом вэлектромагнитном поле.
353
ГЛАВА 6 АУСТЕНИТ КАК ФАКТОР ПОВЫШЕНИЯ ТРЕЩИНОСТОЙКОСТИ
ЖЕЛЕЗОУГЛЕРОДИСТЫХ СПЛАВОВ
6.1. Состояние вопроса
Остаточный аустенит (Аост), который в разных количествах всегда присутствует в структуре закаленной стали, естественно, оказывает влияние на механические свойства. Так, в [226] показано, что прочность и пластичность хромникельмолибденовых сталей повышается, если у границ мартенситных кристаллов располагается Аост иглообразной или пластинчатой формы. Криогенные стали, которые имеют в структуре точечные участки Аост, обладают очень высокой ударной вязкостью – более 2,5 мДж/м2 [227]. В подшипниковых сталях при определенном содержании Аост значительно повышается срок службы в условиях трения качения [228].
Наличие равномерно распределенного Аост в структуре цементированного слоя на поверхности стали вызывает повышение как прочности и пластичности самого слоя [229], так и ударной устало-
сти [230].
В[231] исследованы стали 08Г2Б и 30Х3H3, в которых после за-
калки получено примерно 10 % Аост. В процессе механических испытаний этот аустенит превращается в мартенсит. При этом ударная вязкость увеличивается вдвое по сравнению с ударной вязкостью образцов, структура которых предварительно была полностью мартенситной. Интересно отметить, что максимальные значения ударной вязкости получаются, если после испытания в структуре металла со-
храняется половина исходного количества Аост, то есть в данном случае 5%.
Вряде исследований отмечено положительное влияние остаточного аустенита при его стабилизации. Показано, что увеличение количест-
ва тонких слоев Аост благодаря легированию аустенита стабилизаторами (Mn, Ni) повышает ударную вязкость [232]. Отпуск при 200 °С, который вызывает стабилизацию Аост в инструментальных сталях, также сопро-
354
вождается увеличением ударной вязкости [233]. В случаях когда зерно измельчается, объемная часть Аост увеличивается благодаря его стабилизации на участках, расположенных возле границ зерна [234, 235]. Комбинация мелкого зерна с повышенным количеством Аост является причиной сочетания высокой прочности и вязкости [232]. В некоторых исследованиях [201, 202, 204] показано, что повышение температуры аустенизации в среднеуглеродистых конструкционных сталях приводит к увеличению количества Аост, что является причиной почти двукратного повышения KIc. Авторы этих работ считают, что это повышение связано с интенсивным ветвлением трещины при переходе ее на участки, занятые остаточным аустенитом. В других публикациях [236, 243] рост KIc связывают со способностью Аост «тормозить» в себе растущую в мартенсите трещину. Ее дальнейшее подрастание требует увеличения нагрузки. Если сталь низкоуглеродистая, легированная никелем [237], высокие значения KIc и вязкий характер разрушения даже при криогенных температурах обеспечиваются наличием в структуре ~ 8 % Аост, который в процессе испытания превращается в пакетный мартенсит. В [238] проведено подробное исследование влияния Аост на статическую и циклическую трещиностойкость закаленных на мартенсит сталей 50Х, 50ХН и ШХ15. После закалки стали обрабатывали холодом с последующим отпуском при 150 оС. С понижением температуры обработки холодом количество Аост непрерывно уменьшается. При этом снижается пластичность, сопротивление пластической деформации слегка увеличивается, а прочность на растяжение почти не изменяется. Зависимость KIc имеет экстремальный характер с максимумом. При этом температура обработки холодом, при которой KIc имеет максимальные значения, зависит от содержания углерода в стали: чем меньше содержание углерода, тем ниже температура. Аналогично изменяется и циклическая трещиностойкость, причем разница в скоростях развития усталостной трещины наиболее значительна на втором и третьем участках диаграммы усталостного разрушения. На низкоамплитудном (первом) участке кинетика роста усталостной трещины не зависит от температуры обработкихолодом.
Роль Аост при формировании свойств сталей с бейнитной структурой также велика. В работах В.Д.Садовского [240, 241] отмечено,
355
что получение при изотермической закалке повышенного содержания Аост является причиной увеличения ударной вязкости стали 38ХМЮА. В [240] высказано предположение, что сам по себе бейнитный феррит хрупок, но значительное количество Аост компенсирует эту хрупкость. В [241] обращено внимание на то, что влияние Аост на ударную вязкость усложняется тем обстоятельством, что в процессе самих испытаний Аост может превращаться в мартенсит, при этом тем больше, чем ближе температура испытания к мартенситной точке. Повышение ударной вязкости в стали 38ХМЮА, подвергнутой изотермической закалке при 400 и 425 оС, при повышении температуры испытания до 200 оС может быть связяно с обстоятельством, что деформация в процессе испытания может не вызвать γ → α превращения, если она протекает при температурах, достаточно удаленных от мартенситной точки Мн.
В [242] для стали 40ХГН, дополнительно легированной 1–3 % Si, после изотермической закалки при 300 оС показано влияние Аост на повышение KIc. Авторы объясняют этот эффект торможением развития трещины в Аост и уменьшением сопротивления пластической деформации.
Проведенные за последнее время исследования показывают, что структура с низкоуглеродистой реечной α-фазой могут получаться не только в сталях с низким содержанием углерода. Так, из исследований, проведенных в работах [242, 244], следует, что такая структура может быть получена в среднеуглеродистых и даже в высокоуглеродистых сталях. Причина этого кроется в особом влиянии некоторых легирующих элементов, главным образом кремния, на протекание бейнитного превращения. Эти легирующие добавки вызывают выделение карбидной фазы, в результате чего в сталях, содержащих кремний, после определенного изотермического охлаждения в бейнитном температурном интервале могут быть получены структуры, которые состоят из α-фазы различной морфологии и обогащенной углеродом γ-фазы, сохраняющейся после охлаждения до комнатной температуры как Аост. Эта структура определена как бескарбидный бейнит – название, которого мы будем придерживаться в наших исследованиях.
356

6.2. Исследование влияния режима изотермической обработки на количество
истабильность остаточного аустенита
вкремнистых сталях с различным содержанием углерода
Исследовали три марки кремнистых сталей: 38ХС, 60С2 и 70С2. Изменение объемной доли Аост, сохранившегося при охлаждении до комнатной температуры после изотермической выдержки, практически одинаково для всех сталей: при выдержке от 5 до 10 минут Аост увеличивается, в интервале от 10 до 20 минут количество Аост почти не меняется и при дальнейшем увеличении времени выдержки наблюдается уменьшение Аост (табл. 6.1).
Таблица 6 . 1
Влияние режима изотермической закалки на твердость и количество Аост в кремнистых сталях
tизот, |
τз, |
|
38ХС |
|
60С2 |
70С2 |
|||
оС |
мин. |
HRC |
|
Аост+20 , % |
HRC |
|
Аост+20 ,% |
Аост+20 ,% |
Аост−196 ,% |
350 |
5 |
– |
|
8 |
– |
|
– |
30 |
19 |
|
10 |
43 |
|
17 |
– |
|
– |
34 |
29 |
|
20 |
42 |
|
16 |
– |
|
– |
28 |
28 |
|
40 |
– |
|
10 |
– |
|
– |
24 |
24 |
375 |
5 |
42 |
|
12 |
– |
|
20 |
– |
– |
|
10 |
40 |
|
21 |
38 |
|
30 |
– |
– |
|
20 |
40 |
|
22 |
37 |
|
28 |
– |
– |
|
40 |
40 |
|
18 |
– |
|
22 |
– |
– |
400 |
1 |
– |
|
– |
– |
|
– |
28 |
15 |
|
5 |
– |
|
16 |
– |
|
24 |
47 |
40 |
|
10 |
38 |
|
29 |
33 |
|
34 |
42 |
42 |
|
20 |
37 |
|
28 |
33 |
|
32 |
15 |
15 |
|
40 |
34 |
|
21 |
– |
|
26 |
3 |
3 |
425* |
1 |
– |
|
– |
– |
|
– |
50 |
– |
|
5 |
– |
|
19 |
– |
|
28 |
10 |
– |
|
10 |
38 |
|
28 |
31 |
|
36 |
5 |
– |
|
20 |
39 |
|
28 |
31 |
|
29 |
3 |
– |
|
40 |
– |
|
22 |
– |
|
16 |
3 |
– |
Примечание: * для стали 70С2 tизот= 450 оС. |
|
|
|||||||
|
|
|
|
|
|
|
|
|
357 |

Повышение температуры изотермической выдержки приводит к увеличению максимального количества Аост, и эта тенденция усиливается с увеличением содержания углерода. В стали 38ХС максимальное количество Аост после изотермической выдержки при 375 оС составляет 20–22 %, в то время как после выдержки при 425 оС – 28 %. Повышение углерода в стали 60С2 после выдержки при 375 оС приводит к содержанию Аост 28–30 %, а после выдержки при 425 оС количество Аост достигает 36 %.
Рис. 6.1. Результаты оценки термической стабильности остаточного аустенита стали 38ХС (а) и 60С2 (б): 1 – изотермическая закалка 370 °С, 20 мин (стабильныйАост); 2 – изотермическаязакалка420 °С, 20 мин(нестабильныйАост)
На рис. 6.1 оценено количество Аост после дополнительного охлаждения до данной температуры в интервале от комнатной (24 оС) до температуры кипения жидкого азота (–196 оС). Исследовали стали 38ХС и 60С2. Из полученных зависимостей видно, что изотермическая закалка от 420 оС с последующим охлаждением приводит к непрерывному уменьшению количества Аост. Следовательно, в этом случае не наблюдается стабилизации аустенита. После изотермической закалки при 370 оС количество аустенита уменьшается только при охлаждении до –80 оС, после чего он стабилизируется и его количество сохраняется при охлаждении до –196 оС.
358

6.3. Структура бескарбидного бейнита в кремнистых сталях
Электронно-микроскопическое исследование сталей 38ХС и 60С2 показывает, что подобно традиционному бейниту с карбидной фазой необходимо делать разницу между нижним и верхним бескарбидным бейнитом. В качестве примерной границы между областями существования этих двух видовбейнита можно принятьтемпературу 400 оС.
Структура нижнего бескарбидного бейнита, полученная в результате изотермической закалки при 370 оС, включает рейки α-фазы, объединенные в пакет, и прослойки аустенита, расположенные между рейками α-фазы (рис. 6.2, а). Толщина реек и размер пакетов больше, чем в сталях, закаленных на мартенсит.
Рис. 6.2. Структурастали38ХСпослеизотермическойзакалкипри370 °С(а, б) и420 °С(в, г): а, в, г− выдержка20 мин.; в− выдержка24 ч
359
Плотность дислокаций внутри реек меньше, чем плотность дислокаций в пакетном мартенсите. Толщина прослоек Аост в 2–3 раза меньше толщины самих реек α-фазы (рис. 6.2, б). В соответствии с работами [244, 247] содержание углерода в α-фазе бескарбидного бейнита не превышает 0,1 %. Как показали рентгенографические исследования, содержаниеуглерода в Аост в данном случае составляло 1,46 %.
Продолжительная изотермическая выдержка при 370 оС в течение 24 часов вызывает формирование цементитного карбида на месте Аост (см. рис. 6.2, б). С увеличением содержания углерода в стали продолжительность изотермической выдержки, при которой формируется карбидная фаза, резко снижается. Например, в стали 60С2 карбиды начинают образовываться после выдержки 30–40 минут.
Структура верхнего бескарбидного бейнита, сформированная в результате изотермической обработки при 420 оС, характеризуется сильной микроструктурной неоднородностью: параллельно с микрообъемами, в которых наблюдаются признаки реечного строения, встречаются обширные области, в которых α-фаза и Аост часто принимают сфероидальную форму (рис. 6.2, в, г), размеры которой изменяются от 0,5 до 5 мкм, а содержаниеуглерода в Аост составляет 1,38 %.
Повышение стабильности Аост, которая наблюдается с понижением температуры изотермической обработки, объясняется влиянием двух факторов: первый состоит в известном увеличении содержания углерода в аустените, а второй (основной) – в реечной форме Аост. В этом случае прослойки Аост испытывают всесторонние сжимающие напряжения со стороны окружающей их α-матрицы, в результате чего для инициирования мартенситного превращения в Аост необходимы более высокие напряжения от внешнего нагружения.
6.4. Механические свойства бескарбидных бейнитных кремнистых сталей
Исследовали стали 38ХС и 60С2 (табл. 6.2), обработанные в следующих режимах: аустенитизация при 900 оС 20 минут и изотермическая закалка при 370 и 420 оС в течение 20 минут с последующим охлаждением в воде. Эти режимы термообработки обеспечивают
360