
книги / Перспективные композиционные и керамические материалы
..pdf12.Классификация пористых материалов.
13.Две основные группы способов получения пористыхматериалов.
14.Нарисуйте техническую схему изготовления ВПЯМ.
15.Основные области применения ВПЯМ.
16.Какие методы применяются при получении керамических мем-
бран?
17.Области применения мембранных процессов.
18.Что такое биомиметика?
19.Приведите примеры природных нанопористых и нанокомпозиционных материалов.
20.Какие требования предъявляют к материалам, имплантируемым
вживой организм?
141
Глава 5. ПЕРСПЕКТИВНЫЕ КОМПОЗИЦИОННЫЕ МАТЕРИАЛЫ
5.1. Керамические композиционные материалы
Керамика – перспективный материал для изготовления деталей машин и механизмов, предназначенных для эксплуатации в условиях высоких температур и коррозионно-активных сред, для создания техники нового поколения. Ограничения в использовании керамики связаны главным образом с ее хрупкостью. Поскольку хрупкость керамики обусловлена особенностями межатомного взаимодействия, при разработке керамических конструкционных материалов основное внимание уделяется повышению сопротивления хрупкому разрушению (трещиностойкости), достижению такого уровня трещиностойкости, который обеспечил бы такую же высокую эксплуатационную надежность, как и у металлических конструкционных материалов.
Наиболее эффективный способ повышения трещиностойкости – формирование композиционных структур. Введение второй (упрочняющей) фазы в структуру керамики может обеспечить протекание процессов, затрудняющих распространение трещины (микрорастрескивание матрицы и фазовые превращения в дисперсной фазе, инициируемые полем напряжений у вершины трещины в так называемой «зоне процесса»; переориентация трещины по отношению к направлению действия внешней нагрузки в результате взаимодействия фронта трещины с различными препятствиями), а также процессов, приводящих к увеличению затрат на преодоление сил трения, например, при вытягивании волокон армирующей фазы из матрицы (рис. 5.1). Для реализации таких механизмов особое значение имеют состояние и структура границ раздела матричной и второй фаз.
Под керамическими композиционными материалами понимают широкий круг гетерофазных материалов, изготавливаемых как из индивидуальных компонентов, формирующих структуру, так и методами in situ (например, кристаллизацией стекол, эвтектик и т.д.).
По структуре керамические композиционные материалы подразделяются следующим образом:
– дискретно-армированные волокнами, нитевидными кристаллами, частицами, в том числе пластинчатой формы;
142
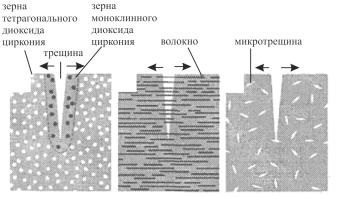
а |
б |
в |
Рис. 5.1. Схемы упрочнения композиционных керамических материалов:
а– трансформационное упрочнение; б – упрочнение волокнами;
в– создание микропористой структуры
–слоистые и слоистогранульные материалы;
–однонаправленноили перекрестно-армированные непрерывными волокнами и армированные объемными волокнистыми каркасами.
5.1.1. Композиционные материалы, упрочненные частицами
Среди керамических композиционных материалов типа керамикакерамика с упрочнителем в виде дисперсных частиц особое место занимает группа так называемых трансформационно-упрочненных материалов. Термин трансформационное упрочнение используется для обозначения явления повышения прочности и вязкости разрушения за счет введения в керамическую матрицу частиц, претерпевающих под нагрузкой полиморфное превращение мартенситного типа. Эффект упрочнения достигается за счет рассеяния энергии у фронта растущей трещины при встрече ее с включением, претерпевающим фазовое превращение.
Классическим примером этого типа керамики является частично стабилизированный диоксид циркония. Он представляет собой крупнозернистый поликристаллический материал (фракция 50–100 мкм) на основе кубического диоксида циркония, в зернах которого диспергированы мелкие включения (< 0,1 мкм) метастабильной тетрагональной фазы. Материал получают спеканием при температуре выше 1700 °С порошков ZrO2 со стабилизирующей добавкой (MgO, CaO, Y2O3), ко-
143
личество которой недостаточно для полной стабилизации кубической модификации. После спекания для выращивания тетрагональных включений в кубической матрице материал подвергают обжигу при промежуточной температуре (1000–1300 °С). Предел прочности материала составляет 600–1000 МПа и вязкость разрушения 8÷15 МПа·м1/2.
Частицы из метастабильного диоксида циркония используются для упрочнения и других керамических матриц. Наиболее эффективные результаты получены при введении их в корундовую матрицу. Материалы в системе Al2O3-ZrO2 характеризуются сочетанием высоких значений прочности (600–1200 МПа) и трещиностойкости (до 12 МПа м1/2).
Упрочнение материалов типа Al2O3-ZrO2 обусловлено эффектом превращения тетрагонального ZrO2 в моноклинный, происходящего в напряженной керамической матрице в условиях воздействия внешней нагрузки. Возникающие в результате сжимающие напряжения тормозят распространение трещины. Микротрещины, которые могут образовываться в матрице у частиц ZrO2, также приводят к затруднению распространения трещины.
По микроструктуре все материалы в системе Al2O3-ZrO2 могут быть подразделены на несколько типов: с дисперсными частицами нестабилизированного Т-ZrO2; с дисперсными частицами PSZ; с агломерированными частицами PSZ.
Немонотонность изменения трещиностойкости при одновременном непрерывном снижении прочности материала объясняют тем, что основным механизмом диссипации энергии является микрорастрескивание, инициируемое превращением Т→М (рис. 5.2). Поэтому для достижения максимального эффекта повышения трещиностойкости необходимо, чтобы дисперсные частицы ZrO2 имели размер больше некоторого критического размера Rc.
Для систем с нестабилизированным диоксидом циркония экспериментально установлено, что критический размер частиц ZrO2, при котором инициируется микрорастрескивание Al2O3-матрицы, зависит от термической предыстории материала и содержания, вводимого в композит ZrO2. От этих же факторов зависит и размер образующихся микротрещин. Если объемное содержание частиц ZrO2 определенного размера меньше критического, образующиеся микротрещины являются стабильными и их коалесценция не происходит. При дальнейшем увеличении содержания ZrO2 расстояние между микротрещинами умень-
144
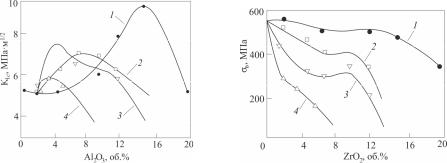
шается и происходит их спонтанная коалесценция, приводя к резкому снижению прочности. Трещиностойкость материала при этом не снижается. Критическое содержание частиц ZrO2 возрастает с уменьшением их размера.
а |
б |
Рис. 5.2. Зависимость прочности и трещиностойкости керамики Al2O3–ZrO2 от объемного содержания частиц ZrO2, мкм: а – трещиностойкость;
б – прочность; 1 – 1,25; 2 – 1,75; 3 – 2,85; 4 – 5,4
Существенно большее упрочнение достигается в системах на основе Al2O3 с частично стабилизированным диоксидом циркония. Механизм повышения прочности и трещиностойкости в таких материалах – поглощение энергии деформации в результате полиморфного превращения Т-ZrO2→М-ZrO2 в поле напряжений. Кроме того, частицы ZrO2 тормозят ростзерна при спекании, что также обусловливаетупрочнение.
Как и для рассмотренных выше материалов, механические свойства Al2O3-PSZ зависят от объемного содержания, размера частиц PSZ и степени их стабилизации. С увеличением объемной доли PSZ сверх критической для данного размера частиц может инициироваться автокаталитическое превращение Т→М из-за достижения некоторого критического уровня внутренних напряжений.
Максимум как прочности, так и трещиностойкости материалов Al2O3-PSZ достигается при одинаковых параметрах микроструктуры. Необходимо, чтобы частицы PSZ были распределены равномерно и располагались по границам зерен Al2O3. Для Al2O3-матрицы предпочтительна структура с мелким (~5 мкм) равноосным зерном (рис. 5.3).
Уровень К1С таких материалов при комнатной температуре достигает 8–15 МПа м1/2, прочность составляет 800–1100 МПа.
145
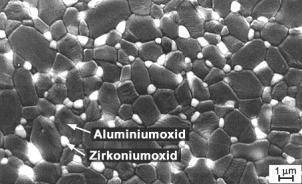
В материалах с агломерированными частицами PSZ (размер агломератов 20–50 мкм) не достигается столь высокий уровень механических свойств, особенно прочности (~400 МПа), как в материале с дисперсными частицами.
Рис. 5.3. Микроструктура композиционного материала на основе Al2O3 с частично стабилизированным ZrO2
Существенное улучшение механических характеристик получено также при введении частиц тетрагонального диоксида циркония в дру-
гие керамические матрицы: муллит, алюмомагниевую шпинель (прочность 500 МПа, К1С = 4,6 МПа·м1/2), нитрид кремния (прочность
950МПа, К1С = 8,5 МПа·м1/2), борид циркония, титанат алюминия.
Вдисперсно-упрочненной керамике в качестве матрицы используют, как правило, компоненты с высоким модулем упругости, не взаи-
модействующие с ZrO2 при температурах спекания и эксплуатации. Трансформационное упрочнение материалов с частицами ZrO2
происходит только в области низких температур (примерно до 200 °С). Поэтому в качестве упрочняющей фазы могут применяться частицы других керамических материалов, обладающих полиморфизмом мартенситного типа с высоким объемным эффектом превращения, напри-
мер двухкальциевый силикат Ca2SiO4, сульфид никеля NiS, энстатит MgSiO3, бораты лантаноидов LnBO3 и др. Для высокотемпературной трансформационно-упрочненной керамики перспективны некоторые оксиды редкоземельных элементов.
Трансформационно-упрочненные композиционные материалы являются частным специфическим случаем более обширного класса дис- персно-упрочненных композитов керамика–керамика. Эффект улучшения показателей физико-механических свойств достигается и при вве-
146
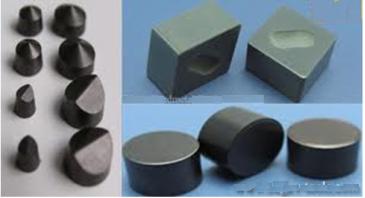
дении в керамическую матрицу частиц другой фазы, не испытывающих фазовых превращений. В этом случае механизм упрочняющего эффекта связан с торможением и ветвлением трещины при встрече с микровключением, что задерживает превращение ее в магистральную с потерей устойчивости.
В композиционных материалах с оксидной матрицей широко используются частицы тугоплавких карбидов, нитридов. В частности, для упрочнения Al2O3 используют частицы карбида и нитрида титана и карбида кремния. Введение дисперсных карбидных частиц позволяет повысить прочность матричного материала в среднем на 20 % при росте вязкости разрушения вдвое. Это существенно улучшает эксплуатационные характеристики режущих пластин для механической обработки, для которых в основном используются такие материалы (рис. 5.4).
Рис. 5.4. Режущие пластины из керамики Al2O3 с TiC
Из композиционных материалов с карбидными матрицами широкое распространение получила керамика на основе карбида кремния: SiC-TiB2, SiC-TiC, SiC-AlN, SiC-BN, SiC-B4C и др. Из материалов на основе карбида кремния изготавливают оснастку для литья цветных металлов и стали, детали электротермического оборудования, формы для горячего прессования, высокоточные направляющие для станков, пары трения, инструмент. Введение дисперсных частиц бескислородных соединений во многих случаях улучшает механические свойства, коррозионную стойкость, износостойкость и трибологические характеристики карбида кремния. Подобный эффект наблюдается также и для материалов на основе бескислородной керамики других составов: боридов, нитридов и т.п.
147
5.1.2. Армированные керамические композиционные материалы
Наиболее эффективным способом повышения трещиностойкости керамики является ее армирование. Известны данные о повышении уровня трещиностойкости керамических композитов до 30–50 МПа·м1/2, то есть до уровня трещиностойкости ряда промышленных алюминиевых сплавов и чугуна (табл. 5.1).
|
|
|
|
|
Таблица 5.1 |
Армированные керамические композиционные материалы |
|||||
|
|
|
|
|
|
Материал |
Армирующий |
Метод |
Предел |
К1С, |
Рабочая |
матрицы |
компонент |
получения |
прочности, |
МПа·м1/2 |
температура, °С |
|
|
|
МПа |
|
|
Al2O3 |
Без армирования |
ГИП |
500 |
4 |
1400 |
Al2O3 |
С-SiC(40%) |
ГИП |
500…650 |
10 |
1400 |
Al2O3 |
Nicalon |
ХПП |
497 |
9,5 |
1300 |
SiC |
Без армирования |
ГИП |
250 |
4 |
1000 |
SiC |
Муллит (30 %) |
ГИП |
350 |
6,5 |
1100 |
SiC |
SiC |
ХПП |
250…450 |
10 |
1100…1300 |
Si3N4 |
Без армирования |
ГИП |
450…600 |
5 |
1200 |
Si3N4 |
SiC (35 %) |
ГИП |
600…1200 |
9…11 |
1200…1400 |
Si3N4 |
SiC (20 %) |
ХПП |
800…1050 |
12,5 |
1205…1350 |
ХПП – химическая пропитка полимерами.
Армирование имеет ряд преимуществ и по сравнению с эффектами, достигаемыми в трансформационно-упрочненных керамических материалах, поскольку эффект армирования реализуется в широком диапазоне температур.
Армирующие элементы
Для армирования различных керамических матриц используют в основном керамические волокна или нитевидные кристаллы. Керамические волокна изготавливают из прочных тугоплавких, химически стойких материалов: оксидов алюминия и циркония, нитрида бора, карбидов бора и кремния, других карбидов, нитридов и оксидов.
Для успешного применения керамических волокон в создании таких инновационных материалов, помимо химической и термической стабильности при повышенных температурах, к ним предъявляется ряд других требований. Первым из них является достаточная гибкость изготовление заготовок различной формы и размеров для дальнейшего
148
формования композита. Достаточную гибкость, даже для материалов с высоким модулем упругости, обеспечивает малый диаметр волокон, так как гибкость обратно пропорциональна четвертой степени диаметра волокна. Например, для получения волокна из оксида алюминия или карбида кремния с модулем упругости 300 ГПа требуется диаметр 10 мкм. Также для большей технологичности процесса получения композитов регламентируется минимальное значение относительного удлинения волокна до разрушения: оно не должно быть ниже 1 %. Это влечет за собой требование к прочности волокна: минимальная прочность на разрыв волокна с модулем упругости 200 ГПа должна составлять 2 ГПа. Для облегчения создаваемых материалов и конструкций предъявляются также требования к плотности волокна – не должна превышать 5 г/см3. Необходимыми являются долговременная химическая и термическая стабильность и сопротивление ползучести при температуре свыше 1100 °С.
По структуре керамические волокна делят на поликристаллические
имонокристаллические. По сравнению с массивными объектами керамические волокна, имеющие поликристаллическое строение, обладают более высокой прочностью, однако, в отличие от монокристаллических усов, их прочность меньше.
Поликристаллические волокна имеют структуру спеченной бес-
пористой керамики с неориентированными зернами.
Существует несколько методов производства поликристаллических керамических волокон.
Золь-гель технологии. Необходимой стадией золь-гель процесса является получение золя гидратированного оксида алюминия, который затем формуют в предкерамические волокна, как непрерывные, так
иштапельные. В целом золь-гель процесс получения волокон включает следующие стадии:
1)приготовление прядильного раствора – золя на основе вязкого металлорганического раствора либо на основе суспензии тонкодисперсного порошка с органическим связующим, в том числе с добавками (полимеров, ПАВ);
2)формование с получением гелевых волокон, где используют экструзионные (для получения непрерывных волокон), дутьевые и механические (центробежные) методы (для получения штапельных волокон) и электроформование (для получения тонких 2D-материалов);
149
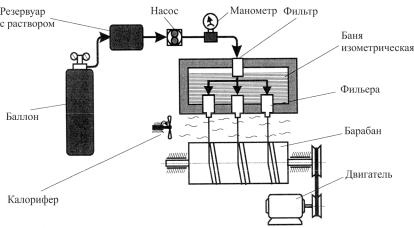
3) обжиг гелевых волокон проводят в несколько стадий и при невысоких скоростях нагрева. Это позволяет равномерно удалять растворитель и органические компоненты из волокон и, как следствие, минимизировать образование трещин и пор.
Этим методом получают непрерывные волокна оксидов металлов диаметром 5–30 мкм, волокна карбидов диаметром 100–160 мкм.
Схема процесса получения поликристаллического волокна из оксида алюминия приведена на рис. 5.5.
Рис. 5.5. Схема установки для экструзии непрерывных волокон
В резервуаре находится исходный материал, представляющий собой раствор формоацетата алюминия Al(ОН)(СНО2)(С2Н3О2) в воде с добавками 10%-ной винной кислоты, вакуумированный до вязкости 200...250 Па·с. Азот, поступающий из баллона, продавливает раствор в шестеренчатый насос. С помощью насоса раствор поступает в фильтр, задерживающий твердые частицы осадка, и далее в фильеры (платиновые стаканчики). В дне фильеры имеются отверстия, через которые продавливаются волокна диаметром 127 мкм. Выходящие из отверстий фильер волокна обдуваются теплым воздухом калорифера. В результате испарения жидкости формируется твердое волокно. В процессе намотки на барабан волокна вытягиваются, их диаметр становится рав-
ным 10...25 мкм.
Следующий этап – спекание волокна. Волокно медленно нагревают до 1500 °С. Выгорание органических веществ происходит при 500...700 °С. В дальнейшем имеет место образование γ- и α-модифика-
150