
книги / Неформованные огнеупоры. Т. 1 Общие вопросы технологии
.pdf0 О |
О о °о й о °0< $ 4 _ |
СЬ° 0о0 2>о |
0 |
‘ |
^ <5\ . ° |
7 6 ^ (0 |
|
~ооо'оаъОо_о0ъ°* |
|||||||
Ч Г \ П ( \ |
Л ~ Л Л Т 1 " |
|
|
||||
|
|
ОООо ° 0 0 4) 0 о |
0" Я0 |
|
|
||
|
|
/ |
Оо а о |
|
|
||
|
|
0О ° *°о0 О |
0о0 |
|
|
|
Горячая сторона
Рис. 2.16. Возможные варианты армирования изделий из огнеупорных бетонов: 1— предварительно напряженная стальная арматура; 2 - стальная арматура; 3 — волокнистое армирование (беспорядоч ное стальное волокно)
ускорения процесса сушки и уменьшения вероятности образования эффекта “взрыв ного разрушения” [2.3]. При введении стальных волокон повышается термостойкость и износостойкость. Следует отметить, что при изготовлении крупногабаритных бето нов в ряде случаев применяют их армирование. Возможности армирования огнеупор ных бетонов по [2.44] проиллюстрированы на рис. 2.16.
В зависимости от условий службы и, прежде всего, температуры по толщине бето на, могут применяться различные варианты армирования, приведенные на рис. 2.16.
2.8. Торкрет-массы (торкрет-бетоны)
Торкретирование как способ формования или ремонта огнеупорных футеровок, зак лючается в переносе огнеупорного материала к формуемому телу или поверхности сжатым воздухом с образованием плотного слоя (массы или бетона). В зависимости от состояния огнеупорного материала различают сухое торкретирование и мокрое (пульповое). В самое последнее время разработан и применен способ полусухого (полумокрого) торкретирования. Он состоит в том, что на стадии предварительного ув лажнения к огнеупорному материалу добавляют около 40-50 % от всего требуемого количества воды, а остальную часть вводят в сопло [2.20]. В зависимости от темпера туры транспортирующего газа различают холодное и горячее торкретирование. По аналогии с огнеупорными бетонами торкрет-бетоны могут быть плотными и легкими (теплоизоляционными).
Касаясь исторического аспекта технологии торкретирования применительно к об ласти металлургии и огнеупоров, следует отметить, что этот способ очень широко применяется в самых различных областях. Его применяют, например, при проведе нии работ, связанных с разработкой газовых и нефтяных месторождений, с созданием укреплений откосов рыхлых и скальных пород в виде бетонных покрытий толщиной 50-500 мм, при строительстве искусственных бетонных русел рек и каналов, при стро ительстве дамб, дорог и т.д.
Термин “торкретирование” впервые введен в 1921 г. фирмой “ТогкгеГ, которая пред ложила этот способ [2.5]. Впервые в нашей стране метод торкретирования был приме нен при строительстве Волховской ГЭС в 1924 г. Согласно данным [2.51] ,этот метод для торкретирования футеровок мартеновских печей инженером Г. С. Байбаковым был применен в 1930 г. Систематические исследования процесса торкретирования метал лургических агрегатов начаты ВИО в 1934 г. [2.12], а в дальнейшем и УкрНИО в 1939-
1952 гг. Полная разработка технологии процесса торкретирования впервые осуществ лена в 1954-1956 гг. на предприятиях Норильского горно-металлургического комби ната [2.12]. К 1940 г. относится начало работ по факельному (пламенному) способу торкретирования [2.12].
Историко-хронологический аспект развития и применения технологии торкретиро вания применительно к футеровке тепловых агрегатов рассмотрен в работе [2.12].
Расширение применения способа торкретирования в области металлургии обуслов лено несколькими факторами: высокой его производительностью, возможностью ме ханизации и автоматизации; относительно малой энергоемкостью; эффективностью использования способа для ремонта футеровки с целью достижения длительного сро ка службы тепловых агрегатов [2.20].
В развитии технологии торкретирования исключительно важным этапом явилась разработка в Японии (фирма “8Ыпа§а^а КеГгасЮпез”) способа мокрого торкретиро вания на основе бетонов (масс) с низкой влажностью. Этот метод, имеющий различ ные наименования (мокрый способ, шоткастинг, шотклин, шоткетинг и т.д.) запатен тован в Японии в 1976 г., в 90-е годы получил широкое распространение в США, а в усовершенствованном виде начиная с 1996 г. применяется в черной металлургии Япо нии [2.20].
Достоинство этого метода состоит в том, что при этом достигаются свойства, анало гичные литым или вибролитым НЦОБ. Это сочетается с высокой производительнос тью, характерной для торкретирования. В случае обычной технологии футеровку из готавливают способом налива (виброналива) в установленную опалубку или шаблон. Несмотря на высокие показатели свойств такой футеровки, технология ее выполне ния в данном случае проблематична, так как требует много времени на операции уста новки шаблона, выдержки бетона для набора прочности, демонтажа шаблона. В слу чае же торкретирования шаблон не нужен, а производительность процесса существенно выше. Схема установки для мокрого торкретирования согласно [2.20] показана на рис. 2.17.
Приготовленная в смесителе 1 торкрет-масса с низкой (6-12 %) влажностью при помощи бетононасоса 2 по гибкому трубопроводу (шлангу) 3 транспортируется к со пловому наконечнику фурмы 4. Отдельная система служит для ввода в торкрет-массу раствора активатора схватывания.
Рис. 2.17, Новый способ мокрого торкретирования (фирма “Кго5ак1 Согр”, Япония): 1— смеситель; 2 — бетононасос; 3 — шланг для подачи материала; 4 — сопло; 5 — воздушный компрессор; б — сжатый воздух; 7— насос подачи активатора
|
|
|
|
|
Т а б л и ц а 2.12 |
|
Свойства бетонов высокой плотности для мокрого торкретирования |
|
|||||
|
фирмы “8№па§а\уа КеГгас(опе$”, Япония |
|
|
|
||
|
Чугунный желоб |
Сталеразливочный |
Промежуточный |
|||
Показатели |
ковш |
|
ковш |
|
||
|
|
|
|
|||
торкретирование |
торкретирование |
торкрети |
|
торкрети |
|
|
|
налив |
налив |
||||
|
(шлаковая зона) |
(зонаметалла) |
рование |
|
рование |
|
Массовая доля, %: |
|
|
|
|
|
|
А120 з |
18 |
80 |
92 |
92 |
68 |
68 |
ЗЮ2 |
1,5 |
1,5 |
1 |
1 |
28 |
28 |
$1С+ С |
77,5 |
17 |
— |
— |
— |
____ |
м е о |
— |
— |
5 |
5 |
— |
— |
Предел прочности при |
|
|
|
|
|
|
сжатии, МПа: |
|
|
|
|
|
|
1000 °С — 3 ч |
29 |
25 |
18,9 |
47,7 |
34,7 |
67,9 |
1500 °С — Зч |
28 |
27 |
51,7 |
81,2 |
40,8 |
68,2 |
Открытая пористость, % |
|
|
|
|
|
|
1000 °С — Зч |
20,1 |
20,9 |
21,3 |
19,9 |
19,8 |
18,4 |
1500 °С — Зч |
19,9 |
20,8 |
24,9 |
22,4 |
20,2 |
19,1 |
Сопоставительный анализ свойств торкрет-бетона, полученного по описанному спо собу, с обычным (наливным) применительно к монолитной футеровке сталеразливоч ных и промежуточных ковшей приведен в табл. 2.12. Там же приведены данные по торкрет-бетонам для ремонта чугунного желоба доменной печи.
Из таблицы следует, что бетоны как для торкретирования, так и налива характеризу ются равным химическим составом. Показатели предела прочности при сжатии после термообработки как при 1000, так и при 1500 °С существенно выше для наливного варианта футеровки, что обусловливается разницей в пористости: для футеровки стальковша— 1,4-2,5 %; промковша— 1,1-1,4 %.
Согласно же данным огнеупорной фирмы “Кгозак1 Согр.” (Япония) и металлурги ческой фирмы “БаШо 81ееГ, сопоставительные испытания наливного и торкрет-бето на корундошпинельного состава в футеровке сталеразливочного ковша показали даже некоторое преимущество торкрет-бетона при службе. При сопоставимых значениях пористости и прочности бетонов скорость износа торкрет-бетона составила 1,57 мм/ плавку против 1,61 для наливного. При этом стойкость составила 42 и 40 наливов соответственно.
Следует отметить, что обычные торкрет-бетоны, применяемые для ремонта моно литных футеровок, например, главных желобов доменных печей, значительно уступа ют по стойкости виброналивным огнеупорным бетонам аналогичного состава. Это характерно в том числе и для керамобетонных, наливных и торкрет-масс, применяе мых для этой цели.
Если в подавляющем большинстве случаев применения торкрет-масс ставится за дача получения на их основе плотной футеровки или ремонтного слоя, то примени тельно к их службе в промежуточных ковшах ставится обратная задача — получение достаточно пористого теплоизоляционного рабочего торкрет-покрытия с ограничен ным (до 8-10 плавок) ресурсом службы.
Составы и свойства импортных торкрет-масс для промковшей МНЛЗ
|
|
Я |
м |
|
я-В |
Фирма- |
|
|
|
|
|
Марка |
1 |
“ |
5 |
Насып» плотность, |
|
произво |
5 |
« |
а |
|
|
массы |
1 Ц |
|
|
||
дитель |
|
|
|||
РНЬпсо |
РНпа^ |
1700 |
|
1,7 |
|
(Австрия) |
Ь\У/ОЬ |
|
|
|
|
РПЬпсо |
РП та^ |
1700 |
|
1,6 |
|
(Австрия) |
Ти1^ип |
|
|
|
|
Баиззап |
ОохзоНге |
1700 |
|
1,16 |
|
(Франция) |
1400 |
|
|
|
1,34 |
Ригше(а11 |
КераПх |
1680 |
|
||
|
1,6 |
||||
(Германия) |
5Ь60/30 |
|
|
|
|
Ригте(а11 |
КераПх |
1600 |
|
1.6 |
|
(Германия) |
РН705 |
|
|
|
|
УейзсЬег |
АпсегШп |
1750 |
|
1,4 |
|
(Австрия) |
ЬТС |
|
|
|
|
УекзсЬег |
АпсегШп |
1750 |
|
— |
|
(Австрия) |
МТС |
|
|
|
|
Nагсо |
|
|
|
|
|
(США) |
|
|
|
|
|
5(а\уегша |
|
|
|
|
|
(Чехия) |
|
|
|
|
|
СОМАТ |
СОМАТ |
— |
|
— |
|
(Турция) |
Типзргау |
|
|
|
|
РЕ1ЛЮ |
|
|
|
|
|
ОК1ЕЫТ |
5ргау |
|
|
|
|
АЬга51Уе5 |
та85 |
|
|
|
|
2 |
| |
Количеств»3воды затворе»1ИЯ, л/100кг |
|
с |
|
>Х 2 |
|
|
|
|
|
3 |
* |
|
8 |
§"* |
|
1 |
* |
|
Я |
= -ё |
|
5 |
о. |
|
Й |
ЛЬ* |
|
2 |
и |
|
|
|
|
ЗЕ |
п |
|
| |
| о - |
|
X |
О. |
|
|
||
о |
о |
|
|
е«=: §— |
М&О |
5 |
5 |
|
1 |
||
0,5 |
15-25 |
1,68 |
77 |
||
0,5 |
28 |
1,45 |
75 |
||
0,5 |
18-20 |
|
|
65-70 |
|
1 |
|
25 |
|
1,4 |
60 |
1 |
|
— |
|
— |
70 |
0,3 |
|
— |
— |
70 |
|
0,3 |
|
|
|
|
(71)* |
|
— |
|
— |
84,5 |
|
0,5 |
|
25-28 |
|
|
60 -70 |
0,5 |
|
|
|
|
80-90 |
0,3 |
|
— |
— |
77 |
|
0,3 |
|
|
|
|
85-90 |
0,3 |
|
|
|
|
72 |
* Верхний и и1И Ж Н И Н п р еделы с<эдержания.
|
Химический состав, мас.% |
|
|
||
5Ю2 |
РегОэ |
А12Оз |
СаО |
N3:0 |
ДгПпрв |
16 |
3 |
— |
— |
0,4 |
2,1 |
— |
3,5 |
2,5 |
1,0 |
— |
— |
15-18 |
>4 |
|
|
|
|
31 |
5,5 |
1 |
<1 |
<0,5 |
1,73 |
23 |
4 |
<1 |
1 |
<0,6 |
— |
17,0 |
3,2 |
0,9 |
1,5 |
— |
|
(15,4)* |
(2,85)* |
(1,02)* |
(1,41)* |
|
(6,26)* |
3,45 |
5,53 |
0,92 |
5,65 |
— |
— |
20-25 |
4 -5 |
2 -5 |
1-3 |
|
1-3 |
3 -10 |
|
|
1-3 |
|
|
21 |
— |
1-1,2 |
— |
— |
|
|
|
(сумма) |
|
|
|
16 |
3,5 |
0,5 |
1,3 |
|
|
Предел прочности |
еплопроводностьТ 900приВт/(мК) °С |
яе |
|
|
при сжатии, МПа, |
|
|||
|
а |
|
||
при температуре, °С |
|
X |
0 |
|
|
л |
|||
|
|
|
5 |
р |
|
|
|
8 -8 |
|
1100 |
1500 |
|
я |
у |
|
X |
|
||
|
|
|
2 |
|
1,1 |
— |
0,60 |
оливин |
|
|
|
|
периклаз |
|
4,0 |
7,0 |
0,47 |
периклаз |
|
0,55 |
|
|
Оливин |
|
|
|
|
периклаз |
|
0,5 |
— |
— |
Оливин |
|
|
|
|
периклаз |
|
— |
— |
— |
— |
|
— |
— |
— |
— |
—— — —
Оливин
периклаз
слюда
Периклаз монтичеллит
—— — Оливин
периклаз
Плавле
ный
периклаз
Периклаз
дунит
В табл. 2.13 по данным [2.31] приведены данные по составам и свойствам зарубеж ных торкрет-масс для промковшей МНЛЗ.
Все они изготавливаются преимущественно на магнезиальной основе (содержание М§0 колеблется в пределах 65-90 %). Фазовый состав и структура торкрет-покрытия формируются в процессе службы. С учетом того, что содержание 8Ю2 для большин ства колеблется в пределах 15-31 %, в процессе службы протекает прежде всего низ котемпературное (>1150 °С) образование форстерита. Массы характеризуются тонко зернистым зерновым составом (с1тлхв пределах 0,3-1 мм) и низкой кажущейся плотно сти рк в сформировавшемся торкрет-покрытии.
Показатели рк подобных масс находятся в пределах 1,40-1,68 г/см3, что соответству ет пористости 45-55 %. Торкрет-покрытия характеризуются низкой механической проч ностью как в исходном состоянии, так и после службы. Высокая пористость покрытия при структурообразовании достигается благодаря высокому водосОдержанию исход ных масс (20-30 %), чему способствует основной характер минерального состава масс (оливин, периклаз) и введение добавок распушенного стекловолокна, усиливающего тиксотропные и прочностные свойства исходных формовочных систем. Торкрет-мас сы, используемые во всех вариантах холодного торкретирования (сухой, полусухой, мокрый) наряду с ранее рассмотренными несомненными достоинствами имеют и ряд недостатков, в числе последних — низкая прочность сцепления с футеровкой и высо кая пористость из-за отрицательного влияния водяного пара при выполнении ремон тов на горячей футеровке. В этой связи более перспективными являются способы фа кельного торкретирования и различные варианты термокерамического торкретирова ния [2.20, 2.52, 2.53], которые позволяют нанести плотный слой высокопрочного и устойчивого к коррозии материала.
Принцип горячего (факельного) торкретирования состоит в том, что в газовую струю подают одновременно топливо (твердое, жидкое или газообразное), воздух, обогащен ный кислородом, и огнеупорный порошок [2.12]. В зависимости от вида топлива раз личают: жидкостное горячее торкретирование, когда топливом служит керосин; газо вое, когда топливо — природный газ; и твердоугольное, когда топливом служит уголь ная пыль. При горении топлива образуется факел. В факеле частицы огнеупорного материала частично оплавляются, что обусловливает хорошую прилипаемость торк- рет-слоя к огнеупорной футеровке и меньший поток частиц. При этом на торкретиру емой поверхности образуется прочный и плотный (пористость до 3 %) торкрет-слой. Однако последний часто оказывается нетермостойким, трескается и частично отслаи вается. При введении же в факел 20-30 % коксового порошка торкрет-слой получает ся более пористым, но более термостойким [2.12].
В настоящее время существует два способа так называемого термокерамического торкретирования [2.20]: факельное торкретирование и керамическая сварка.
Факельное торкретирование впервые применили на коксовых печах, но впослед ствии распространили его на агрегаты доменного и сталеплавильного производства, например, установки порционного и циркуляционного вакуумирования, конвертеры, сталеразливочные ковши, доменные воздухонагреватели [2.12,2.20].
При высокотемпературной керамической сварке (ВКС), как и при факельном торк ретировании, происходит расплавление ремонтного материала. Принципиальное раз личие состоит в механизме подвода тепла для расплавления. В данном случае оно
- 1 0
11
12
с
Рис. 2.18. Схема установки для факельного торкретирования: 1— ремонтируемая поверхность; 2 — торкрет-слой; 3 — факел; 4 — горелка; 5 — фурма; б — огнеупорный порошок; 7 — бункер; 8 — регулятор; 9 — подвод воды; 10 — отвод воды; 11 — пропан; 12 — кислород
осуществляется за счет тепла экзотермической реакции окисления порошкообразного металлического “горючего”, входящего в состав наносимого при ВКС порошка [2.52, 2.53].
Таким образом, сущность ВКС состоит в том, что на изношенный участок в горячей печи наносят керамический материал в смеси с металлическими порошками в среде окислителя (чаще всего — кислорода). Принципиальная схема процесса показана на рис. 2.18.
В этом процессе металлические порошки играют роль горючего материала, поток кислорода поддерживает горение, а керамический материал используется как запол нитель. При этом температура поверхности ремонтируемой футеровки должна быть достаточной для того, чтобы смесь воспламенилась и началась экзотермическая реак ция [2.52,2.53].
Рассмотренный процесс ВКС начиная с 1980 г. успешно применяется на коксохими ческих предприятиях мира для горячего ремонта коксовых печей. Процесс запатенто ван фирмой “С1ауегЬе1” (Бельгия). В России также создана технология ВКС не только для коксовых печей, но и для сталеразливочных ковшей, конверторов, нагреватель ных печей [2.53]. На Украине аналогичный метод назван керамической наплавкой, он используется на коксохимических предприятиях для восстановления динасовой и шамотной кладки [2.53].
2.9. Другие неформованные огнеупорные материалы
В ряде стран в отдельный класс неформованных огнеупоров выделяют так называ емые “формуемые материалы” [2.5-2.8]. Последние включают пластичные массы, набивные массы и леточные массы.
2.9.1. Пластичные массы
Пластичные массы являются самыми первыми неформованными огнеупорами, ко торые были широко реализованы на практике. Впервые они были созданы в США в 1914 г. (фирма “РПЬпсо”). Они, как правило, состоят из огнеупорного заполнителя и пластичной глины как матричной (и одновременно вяжущей) системы. Дополнитель но могут вводиться и другие связующие. Они, как правило, производятся в виде уп лотненных пластичных (изолированных пленкой) брикетов или заготовок, получае мых методом экструдирования пластичных масс. Иногда их поставляют и в гранули рованном состоянии. Их применяют, например, для локального ремонта разрушенной футеровки (без применения шаблона) методом набивки (пневмотрамбования), а в ряде же случаев при изготовлении сплошных футеровок из пластичных масс применяют и виброуплотнение.
Т а б л и ц а 2.14
Характерные свойства пластичных огнеупорных масс
|
|
|
Массы |
|
Показатель |
высокоглино |
Алюмосили |
высокоглино |
хромитовые |
|
||||
|
земистые А |
катные |
земистые Б |
|
|
|
|||
Содержание,% |
|
|
|
|
А120 3 |
82 |
41 |
84 |
Сг20 3 28 |
5Ю: |
12 |
49 |
12 |
|
Максимальная температура |
1850 |
1680 |
1700 |
1600 |
использования,°С |
|
|
2,80 |
2,95 |
Кажущаяся плотность, т/м3 |
2,85 |
2,20 |
||
после сушки при 110 °С |
|
|
|
|
Предел прочности при изгибе, |
|
|
|
|
МПа, при температуре, °С: |
|
|
|
4 |
110 |
4,5 |
1,8 |
7 |
|
1000 |
5,0 |
3,0 |
И |
5 |
1500 |
7,0 |
4,5 |
15 |
10 |
Дополнительное изменение |
|
|
|
|
размеров, %, при температуре, |
|
|
|
|
°С: |
|
|
|
-2,0 |
110 |
-1,1 |
-1,3 |
-1,1 |
|
1000 |
-1,2 |
-1,3 |
-1,0 |
-2,4 |
1300 |
-1,2 |
-1,3 |
-0,9 |
-2,4 |
Коэффициент тимического |
8,0 |
5,7 |
7,5 |
7,5 |
расширения, 10 /°С |
|
|
|
|
Теплопроводность, Вт/(м°С), |
|
|
|
|
при температуре, °С: |
|
|
|
1,54 |
500 |
1,28 |
0,74 |
1,2 |
|
1000 |
1,42 |
0,93 |
1,36 |
1,65 |
Время вызревания масс до |
В любое |
Непосредственно после набивки |
В любое |
|
розжига печи, ч |
время |
|
|
время |
Способ нанесения |
Набивка |
Набивка, местный ремонт путем |
Набивка |
|
|
|
|
заделки |
|
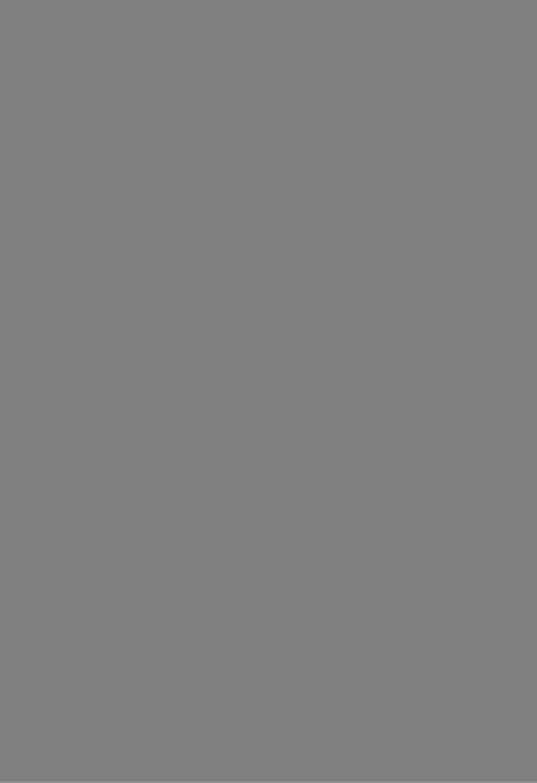
фикаторов), вяжущих веществ и влаги, и поэтому они требуют больших энергозатрат при формовании.
В отечественной практике к набивным огнеупорным массам причисляют и песко метные материалы [2.12], хотя за рубежом их выделяют в отдельную группу неформо ванных огнеупоров [2.5, 2.18,2.19]. Этот метод получил в СССР исключительно ши рокое практическое применение в связи с выполнением монолитных футеровок ста леразливочных ковшей [2.12]. Наиболее совершенной для этой цели считается маши на типа “Орбита” конструкции НЛМК, с помощью которой еще в 80-е, начале 90-х годов набивалась преобладающая часть монолитных футеровок из масс кислого хи мического состава [2.1, 2.12]. Эти футеровки, хотя и в значительно меньшем количе стве, но еще и сейчас используются на некоторых заводах России и Украины.
Аналогичные пескометные установки (ЗНп^ег) для монолитных футеровок стале разливочных, чугуноразливочных ковшей использовались до 90-х годов и в других странах при использовании высококремнеземистых, пирофиритовых и цирконсодер жащих масс [2.19]. Принцип действия пескометов состоит в том, что массе придается определенная скорость, и когда она под действие центробежной силы срывается с го ловки массомета, то ее кинетическая энергия расходуется на уплотнение. При скоро сти бросания пакета массы пескометом 60 м/с развивается давление, эквивалентное около 10 МПа статической нагрузки. Пескометную массу забрасывают в зазор между шаблоном и стенкой печи, в результате чего образуется футеровка, которая после суш ки и разогрева подвергается эксплуатации [2.12]. Для футеровки сталеразливочных ковшей применяют кремнеземистые массы, расширяющиеся при нагревании и уплот няющие футеровку в процессе службы. Для обеспечения формуемости в массу вводят огнеупорную глину, ортофосфорную кислоту, сульфат магния и т.д. Содержание ЗЮ2 в массе составляет 90±2 %, влажность 8-12 % [2.12].
Сопоставительные исследования методов формования монолитных футеровок ста леразливочных ковшей показали [5] ,что по показателям пористости материала, а так же по скорости его износа по службе метод пескометной набивки уступает другим методам — механической набивке (трамбованию), а также вибролитью. Кроме того, для футеровок сталеразливочных ковшей стали применять более дорогие и высоко стойкие материалы, чем с использованием пескометных машин. В связи с этим за рубежом данный метод уже не применяют.
Применительно к набивным массам преимущественное распространение получили пневматические трамбовки со съемными бойками. Длина хода поршня трамбовки со ставляет 100-150 мм, давление воздуха 0,5-0,8 МПа, диаметр бойка 50-100 мм. Фор ма бойка — сферическая или с волнисто-шероховатой поверхностью [2.18, 2.19].
Существует две разновидности способа трамбования: послойный и непрерывный. При первом способе вся футеровка разбивается на несколько слоев (примерно 60 мм) и каждый слой уплотняется отдельно. Согласно второму способу массу трамбуют не прерывно, подавая ее небольшими порциями. Благодаря этому создается возможность выполнять сравнительно толстую бесшовную футеровку с равномерной плотностью без слоевых соединений [2.18,2.19]. По данным, представленным в работе [2.54] при менительно к магнезитовым набивным массам непрерывный метод характеризуется несколько (1,1 %) меньшей пористостью и большей прочностью уплотненного мате риала.
Рис. 2.20. Влияние влажности формовоч ной смеси IV на пористость образцов кремнеземистого керамобетона после сушки Я, полученных набивкой (/), ста тическим прессованием под давлением 100 (2) и 10 МПа (5)
На результаты уплотнения набивных масс сильное влияние оказывает влажность массы, содержание и вид вяжущего. В зависимости от минерального состава и назна чения набивных масс применяют как неорганические, так и органические вяжущие (связки). Применительно к набивным массам на основе кварцита [2.55] и боксита [2.32] весьма успешно применяют пластифицирующие добавки огнеупорных глин. В рабо те [2.56] проведены сопоставительные исследования влияния способа уплотнения (фор мования) на пористость кремнеземистых масс на основе пластифицированных ВКВС кварцевого песка. При этом изучены методы как набивки (пневмо(вибро)трамбования), так и статического прессования при различных давлениях. Как следует из рис. 2.20, при всех изученных значениях влажности исходных формовочных смесей минимальные значения пористости достигнуты при использовании метода набивки.
Т а б л и ц а 2.15
Свойства огнеупоров, полученных из набивных масс
Тип материала |
А |
в |
С |
О |
Е |
Основное сырье |
Шамот |
Шамот, |
Муллит |
Боксит |
Корунд |
|
|
корунд |
|
|
|
Максимальная температура |
1450 |
1600 |
1700 |
1650 |
1800 |
применения, °С |
|
|
|
|
|
Вид вяжущего |
Керами |
Химичес |
Химичес |
Керами |
Керами |
|
ческая |
кая |
кая |
ческая |
ческая |
Потребность материала, т/м3 |
2,5 |
2,65 |
2,55 |
2,80 |
3,25 |
Содержание, %: |
|
|
|
|
|
А120з |
50 |
62 |
70 |
80 |
95 |
$Ю2 |
47 |
34 |
28 |
15 |
4 |
Ре20з |
0,9 |
0,7 |
0,4 |
1,5 |
0,2 |
Предварительный обжиг, °С |
1350 |
1500 |
1500 |
1400 |
1500 |
Кажущаяся плотность, г/см3 |
2,35 |
2,47 |
2,38 |
2,68 |
3,07 |
Открытая пористость, % |
14 |
14 |
13 |
17 |
14 |
Предел прочности при изгибе, |
9 |
8 |
13 |
7 |
10 |
Н/мм2 |
|
|
|
|
|
Предел прочности при сжатии, |
40 |
50 |
65 |
50 |
150 |
Н/мм2 |
|
|
|
|
|
Остаточное изменение |
-0,6 |
±0 |
-0,3 |
+0,4 |
-0,4 |
размеров (усадка, рост) |
|
|
|
|
|