
книги / Металлургия, технология угля и неметаллических полезных ископаемых
..pdfменяют охлаждение брикетов только на сетчатом конвейере с обдувкой их воздухом или обрызгиванием водой. В этом случае продолжительность процесса охлаждения сокращается до не скольких минут. Мелочь и бой брикета на сетчатой ленте отсеи ваются и возвращаются в процесс брикетирования.
В последние годы в ряде стран за рубежом начинают приме нять эмульсионный способ обработки брикетов, который в комп лексе с обдувкой воздухом значительно сокращает период их ох лаждения. Сущность этого метода заключается в кратковремен ном выдерживании горячих брикетов в масляной эмульсии. Тон кая пленка масла обволакивает брикеты и предохраняет их и от слипания.
§ 8. Технологические схемы брикетных фабрик
Производство брикетов с твердым каменноугольным пеком
Типичная технологическая схема фабрики для брикетирования каменных углей с твердым каменноугольным пеком, показана на рис. 158.
/ — ленточный |
конвейер для подачи |
на фабрику угля |
марки |
Т; 2 — то |
же, |
для углей |
|||||||||||||
марок |
ПС, Г, |
Д; |
3 — бункер |
оборудованный тарельчатым питателем |
для |
угля |
мар |
||||||||||||
ки Т ; |
4 — газовая |
барабанная |
сушилка; |
5 — топка сушилки; |
6 — циклоны; |
7 — венти |
|||||||||||||
лятор-дымосос; |
|
8 — батарейный |
циклон; |
9 — бункер |
для |
углей |
марок ПС, Г, Д; |
||||||||||||
10 — бункер для |
мелочи и |
боя |
брикетов; 11 — шнековый смеситель; 12 — бункер |
для |
|||||||||||||||
пека; |
13 — двухвалковая |
зубчатая |
дробилка; |
14 — элеватор; 15— молотковая |
дро |
||||||||||||||
билка; |
16 — смеситель для |
угля |
и пека |
(дезинтегратор |
или |
шнек); |
/7 — элеватор |
для |
|||||||||||
брикетной шихты; |
18 — распределительный скребковый |
конвейер; |
19— паровые смеси |
||||||||||||||||
тели; |
20 — охладительные |
винтовые |
конвейеры; |
21 — вальцовые |
прессы; |
22 — решетка |
|||||||||||||
для отсева мелочи |
от брикетов; |
23 — сетчатый |
конвейер; 24 — элеватор |
для |
возврата |
||||||||||||||
|
|
|
|
|
|
|
мелочи |
и боя |
брикетов |
|
|
|
|
|
|
|
|
||
Брикетная |
фабрика |
перерабатывает каменный |
уголь |
|
марки Т |
||||||||||||||
с присадкой к нему углей марок ПС, Г или Д. |
|
|
уголь, |
измель |
|||||||||||||||
На |
фабрику |
поступает |
раздельно по |
маркам |
ченный до крупности <6 мм. Уголь марки Т сушится в газовой барабанной сушилке и затем вместе с присадочными углями пере
мешивается с каменноугольным пеком, измельченным до крупно сти <1 мм в зубчатых двухвалковых и молотковых дробилках (или в дезинтеграторах).
Брикетная шихта направляется в паровой вертикальный сме ситель, где перемешивается и пропаривается. Отсюда она охлаж дающим винтовым конвейером направляется в распределительную чашу вальцового пресса для прессования.
Брикеты охлаждаются на сетчатом конвейере и направляются на погрузку в ж.-д. вагоны или на склад. Отсев мелочи и бой брикетов возвращаются в процесс брикетирования.
Производство брикетов с жидким нефтяным битумом
Технологическая схема брикетной фабрики, на которой приме няется в качестве связующего жидкий нефтяной битум, показана на рис. 159.
Рис. |
159. |
Технологическая схема |
брикетной |
фабрики, |
применяющей |
|||||||
|
|
|
в качестве |
связующего |
жидкий |
нефтяной битум: |
|
|||||
/ — газовая |
барабанная |
сушилка; |
2 — грохот; |
3 |
— дробилка; |
4 — дозировочные |
||||||
бункера; |
5 — автодозаторы; 6 — шнекн-смеснтелн; |
|
7 — паровые |
смесители; |
8 — |
|||||||
винтовые |
охладительные |
конвейеры; |
9 — вальцовые |
прессы; |
10 — сетчатый |
кон |
||||||
вейер; |
// — грохот; 12 — погрузочная |
стрела; |
13 |
— ж.-д. вагон; |
14 — приемный |
|||||||
резервуар |
для битума; 15 — шестеренчатый насос; |
16 — питающий |
резервуар; |
/7— |
||||||||
|
|
|
дозировочные |
насосы; 18 — форсунки |
|
|
|
Рядовой каменный уголь поступает на брикетную фабрику и сушится в газовой барабанной сушилке, после чего он дробится до крупности <3 мм. Предварительно перед дроблением от угля отсеивается на грохотах класс 0—3 мм.
Дробленый уголь поступает в дозировочные бункера, откуда подается для смешения с подогретым до температуры 180° С би тумом в шнеки-смесители.
Брикетная шихта из шнеков-смесителей направляется в паро вой вертикальный смеситель, где она перемешивается и пропари вается, нагреваясь до температуры 75—80° С. Далее шихта ох лаждается в винтовом конвейере до температуры 65—70° С и по ступает в вальцовые прессы.
Полученные брикеты после охлаждения на сетчатом конвейере направляются на погрузку в ж.-д. вагоны или на склад.
Нефтяной битум поступает на брикетную фабрику в цистернах с паровым обогревом и сливается в приемный резервуар, где пре дусмотрен подогрев его до температуры 140—150° С.
Из приемного резервуара битум шестеренчатым насосом по дается в питающий резервуар брикетной фабрики. Все трубопро воды для перекачивания битума и питающий резервуар термоизо лированы и обогреваются паром.
Подача битума в шнеки-смесители производится высоконапор ными дозировочными насосами. Распыление битума при смешении
его с углем осуществляется форсунками. |
|
|
пенетрацию |
||||||
Битум |
имеет температуру |
размягчения 68—72° С, |
|||||||
около 2 мм. |
|
|
|
|
|
|
|
||
Технико-экономические показатели производства каменноугольных брикетов |
|||||||||
Исходный |
уголь (концентрат): |
|
|
|
От 0—3 до 0—13 |
||||
крупность, мм |
|
|
|
|
|||||
зольность, |
% |
|
|
|
|
|
10—20 |
||
влажность, |
% . . |
|
............................................. |
5—15 |
|||||
Влажность сушонки, % . . . . . |
2—4 |
||||||||
Температура размягчения связующего |
(пека, |
нефтебитума), °С |
90—65 |
||||||
Расход на |
1 |
т |
брикетов: |
|
|
|
|
|
1,1—1,3 |
угля, |
т . . . . |
|
|
|
|
|
|||
связующего, % |
|
|
|
|
|
5—10 |
|||
пара, |
к |
г ................. |
|
|
|
|
|
90—120 |
|
электроэнергии, к е т |
|
|
|
|
|
6—12 |
|||
Температура брикетов, °С: |
|
|
|
|
50—60 |
||||
до охлаждения . |
|
|
|
|
|
||||
после охлаждения . |
|
|
|
|
|
25—40 |
|||
Время охлаждения, мин |
|
|
|
|
|
20—60 |
|||
|
|
|
|
|
Г л а в а |
III |
|
|
|
|
|
|
БРИКЕТИРОВАНИЕ ТОРФА |
|
|
||||
|
|
|
|
§ 1. Общие сведения |
|
|
|||
Залежи |
торфа |
имеются |
почти на всей |
территории СССР |
|||||
(в Эстонии, Белоруссии, Центральных областях и др.). |
|||||||||
Торф |
ввиду его |
малой плотности, |
значительного |
содержания |
|||||
в нем влаги и нетранспортабельности |
является |
преимущественно |
местным видом топлива и используется главным образом для пы левидного сжигания на электростанциях,
Для повышения качества торфа как топлива его подвергают брикетированию. Получаемые брикеты используются коммуналь ными и бытовыми потребителями.
Брикетированию подвергается фрезерный торф, получивший свое название от способа его добычи путем фрезерования (раз рыхления) торфяной залежи фрезерными машинами, естественной сушки и уборки полученной крошки торфа.
Крупность кусков фрезерного торфа не превышает 50 мм, влажность не более 53%, зольность (на сухую массу) до 15— 20%, плотность (при условной влажности 40%) не менее 0,2 г/см3, засоренность (пни, корни, очес) не более 5%.
Брикетирование торфа производится без связующих веществ, как и бурых углей.
Технологическая схема производства торфобрикетов включает операции подготовки торфа к брикетированию — дробление и сушка, прессование сушонки, охлаждение и погрузка брикетов в ж.-д. вагоны или на склад.
§ 2. Подготовка торфа к прессованию
Подготовка торфа к прессованию включает операции дробле ния и сушки торфа.
Дробление торфа
Торф доставляют на торфобрикетные заводы ж.-д. транспортом узкой колеи. Разгрузка торфа из вагонов производится в бункера или на склад. Полезная емкость бункеров рассчитывается на 1— 3-часовую производительность завода. Из бункеров торф круп ностью 50 мм пластинчатыми конвейерами подается в дробильно сортировочное отделение торфобрикетного завода, где дробится до <8 мм. Дробление торфа производится в одну стадию. Пред варительно перед дроблением от торфа отсевается класс <8 мм. Дробленый торф подвергается контрольному грохочению.
Для дробления торфа применяют обычно молотковые бесколосниковые дробилки, а для грохочения — различные типы гро хотов (вибрационно-эксцентриковый, ГУП-1 и др.).
Сушка торфа
Сушку торфа производят до влажности не более 18%.
Для сушки торфа применяют паровые барабанные трубчатые сушилки, пароводяные сушильные установки и газовые трубысушилки.
Все виды сушилок снабжены сепараторными устройствами для отделения высушенного торфа от газового потока, уносящего до 25% тонких фракций подсушенного торфа. Устанавливаются пыле осадительные камеры, циклоны (ВТИ, ЛИОТ, системы Давидсона,
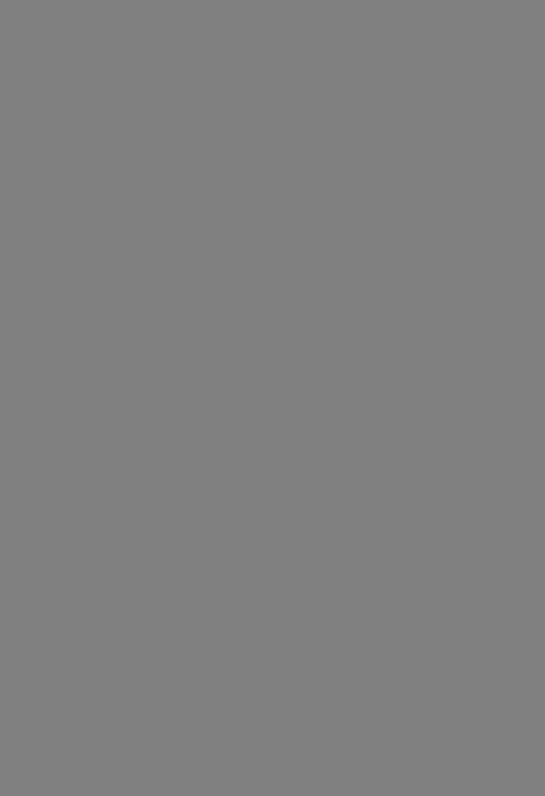
Сушка торфа осуществляется в сушильных трубках в потоке горячего воздуха, нагреваемого стенками трубок, просасываемого через трубки вентиляторами. Торф вместе с воздухом проходит по сушильным трубкам через все колонны, отдавая свою влагу горячему воздуху.
В водяных колоннах отработанный горячий воздух после очистки его от торфа выбрасывается в атмосферу. В паровых колоннах отработанный воздух проходит последовательно от ко лонны № 5 к колонне № 3, очищается при этом от торфа в цикло нах и поступает в скруббер для окончательной очистки, где он отдает свое тепло циркулирующей в скруббере воде. Последняя через теплообменник нагревает чистую воду, поступающую для обогрева междутрубного пространства в водяных сушильных ко лоннах.
Техническая характеристика пароводяной сушильной установки приведена в табл. 43.
|
|
|
Т а б л и ц а |
43 |
|
Техническая характеристика пароводяной сушильной установки |
|
||||
|
|
Сушильные колонны |
|
||
Показатели |
№ 1 |
|
|
|
|
|
№ 2 |
№ 3 |
№ 4 |
№ 5 |
|
Диаметр колонн, мм . . |
1830 |
1830 |
1830 |
1750 |
1700 |
Число сушильных трубок . |
627 |
627 |
588 |
554 |
515 |
Поверхность нагрева, м2 |
1047 |
1047 |
982 |
925 |
860 |
Темперетура горячей воды 5 е»—60° С, температура |
пара (р — 2 ати) |
1 60° С. |
|
|
Расход тепла на испарение влаги 580—620 ккал/кг.
Производительность по испаренной влаге при исходной влажности торфа, от 44,6 до 50,3% — 8 ,4 —9,3 т/ч.
Г а з о в ы е т р у б ы-с у ш и л к и для сушки торфа аналогичны сушилкам для бурого угля. Из этих сушилок на торфобрикетных заводах применяются обычные трубы-сушилки, сушилки с раз мольным вентилятором и сушилки с шахтной мельницей.
Обычная труба-сушилка имеет две ветви — восходящую дли ной 15 м и нисходящую длиной 13 м. Сушилки с размольным вен тилятором имеют три ветви, длиной соответственно 5,2; 7,8 и 13 и*. В нижней части второй ветви устанавливают размольный венти лятор. В газовых трубах-сушилках можно сушить очень влажный торф (Wll3i4==z70%) до конечной влажности около 15%.
Основные параметры сушки торфа в газовых трубах-сушилках
Трубы-сушилки . |
|
Обычная |
С размольным |
|
Размеры трубы-сушилки: |
|
|
вентилятором |
|
|
300 |
750 |
||
диаметр, |
мм . |
|
||
длина, м |
. . . . |
. |
28 |
26 |
Производительность по испаренной влаге, кг/ч |
452—1250 |
1590—3790 |
||
Напряжение объема трубы по влаге, кг/м 3*ч |
210-316 |
139—330 |
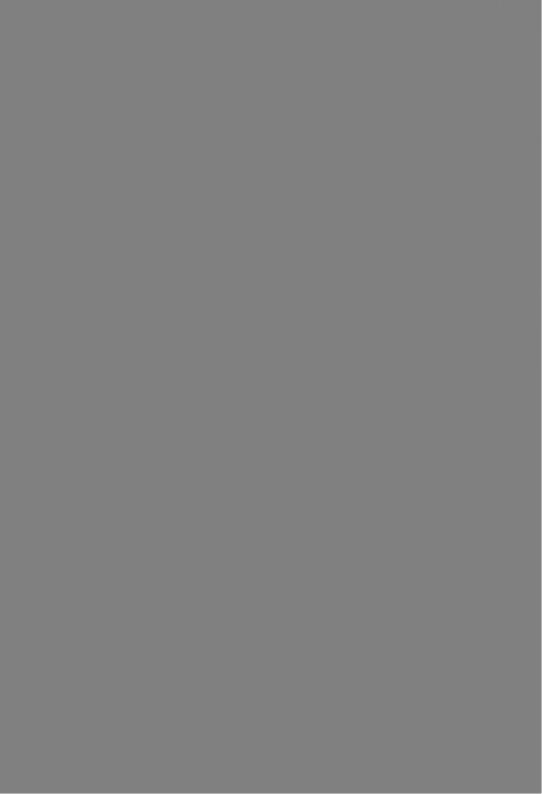
Испытание на крошимость производят в барабане длиной 410 мм, имеющем форму неправильного эллипса. В барабан за гружают 7 кг торфяных брикетов и вращают его со скоростью 25 об/мин в течение 10 мин. После этого содержимое барабана взвешивают и определяют величину крошимости, как отношение веса крошки к общему весу брикетов.
Остальные испытания торфяных брикетов производят по ана логии с испытаниями угольных брикетов.
§ 4. Технологические схемы торфобрикетных заводов
Технологическая с х е м а т о р ф о б р и к е т н о г о з а вода , оборудованного паровой трубчатой сушилкой, не отличается по последовательности операций от аналогичной схемы производства буроугольных брикетов.
Т е х н о л о г и ч е с к а я с х е м а торфобрикетного завода с па роводяной сушильной установкой приведена на рис. 162.
Торф в саморазгружающихся вагонах доставляется на торфо брикетный завод и поступает в бункера, откуда конвейерами по дается в молотковые дробилки. Дробленый до крупности <8 мм торф винтовым конвейером распределяется в питатели контроль
ных грохотов. Надрешетный продукт |
грохотов |
направляется в |
топку, а подрешетный продукт — на |
сушку в |
пароводяную су |
шильную установку. |
|
|
Торфяная сушонка, выделенная в последнем из циклонов су шильной установки, поступает на цепной конвейер, распределяю щий сушонку в винтовые питатели над штемпельными прессами. Торфяные брикеты после охлаждения в желобах направляются на
склад или потребителю. |
т о р ф о б р и к е т н о г о з а |
Т е х н о л о г и ч е с к а я с х е ма |
|
в о д а с газовой трубой-сушилкой |
с размольным вентилятором |
(рис. 163) имеет преимущество перед другими схемами в том, что размольный вентилятор не только создает тягу дымовых газов в трубе-сушилке, но и дополнительно измельчает торф, обеспечивая более интенсивную и равномерную его сушку.
Торф в саморазгружающихся вагонах доставляется на торфо брикетный завод и разгружается в бункера. Затем он дробится и конвейерами ленточным и скребковым подается на грохот. Над решетный торф используется для топки трубы-сушилки, а под решетный торф скребковым конвейером направляется в бункер трубы-сушилки, откуда винтовым питателем направляется в су шилку. По выходе из трубы-сушилки торфяная сушонка допол нительно измельчается размольным вентилятором и выделяется из газового потока в трех последовательно установленных цик лонах. Далее сушонка поступает в бункер и оттуда в штемпель ный пресс. Брикеты по охладительным желобам направляются на склад готовой продукции или потребителю.
Предусмотрено обеспыливание штемпельного пресса и улавли вание торфяной пыли.
|
Рис. |
162. Технологическая схема |
торфобрикетного завода с |
пароводяной |
сушильной установкой: |
||||||
/ — конвейер |
для |
рядового |
торфа; 2 |
— молотковые |
дробилки; |
3 — распределительный винтовой конвейер; 4 — питатели; |
5 — грохоты; 6 — |
||||
конвейер для |
подачи торфа |
в |
топку; |
7 — винтовой |
конвейер; |
8 — питатель; 9 — с; шильные |
колонны сушильной установки; |
10 — вентиляторы; |
|||
// — циклоны; |
12 — выхлопные |
трубы |
циклонов; 13 — скруббер; 14— насосы для |
горячей |
воды; |
15 — теплообменник; 16 — цепной конвейер; |
|||||
|
|
|
|
17 — винтовой конвейер; /Я — штемпельные прессы; |
19 — охладительные желоба |
|