
книги / Технология целлюлозно-бумажного производства. Введение в специальность
.pdfния целлюлозы называется делигнификацией соответствующего растительного сырья (древесины, соломы хлебных злаков, тростника и т. п.). Продукт делигнификации называется технической целлюлозой. Техническую целлюлозу получают в процессе варки, под которой понимают обработку древесного или другого растительного сырья раствором химических реагентов при повышенных температуре и давлении по специальному режиму в аппаратах периодического или непрерывного действия. Применяемый раствор химикатов называется варочным раствором.
В результате варки растительного сырья получают небеленую целлюлозу, представляющую собой продукт с относительно низкой белизной, все еще содержащий большое число компонентов древесины, сопровождающих целлюлозу. Освобождение от них в ходе продолжения варочного процесса связано со значительным разрушением целлюлозы и как следствие – снижением выхода и ухудшением ее свойств. Для получения целлюлозы с высокой белизной – беленой целлюлозы, наиболее освобожденной от лигнина и экстрактивных веществ, – техническую целлюлозу подвергают отбелке химическими отбеливающими реагентами.
Для характеристики свойств и качества технической целлюлозы, определяющих ее потребительскую ценность, применяют целый ряд различных показателей. Наиболее важные из них: массовые доли лигнина, пентозанов, смолы, степень полимеризации, механические свойства.
Методы производства технической целлюлозы
Применяемые в промышленности и исследованные в лабораторных условиях методы производства технической целлюлозы многочисленны. Все они основаны на свойстве лигнина гораздо легче, чем целлюлоза, поддаваться разрушительному действию многих химических реагентов. В основу классификации методов производства целлюлозы в нашей стране положены
41
вид и свойства применяемых химических реагентов, а при использовании нескольких реагентов – последовательность обработки ими растительного сырья. По виду и свойствам применяемых растворов химических реагентов 'различают щелочные, нейтральные и кислотные методы варки. Фактором, определяющим принадлежность конкретного метода варки к щелочным, нейтральным или кислотным, является концентрация водородных ионов (активная кислотность) в применяемом варочном растворе, характеризуемая водородным показателем рН. Методы варки технической целлюлозы, получившие промышленное распространение, охватывают в настоящее время весь интервал значений рН, что дает возможность успешно варить любые древесные породы и получать широкий ассортимент волокнистых полуфабрикатов с различным целевым применением.
В основу щелочных методов варки положено действие щелочи на древесину. В этой группе наиболее широкое применение получил сульфатный метод варки, в котором активным варочным реагентом служит водный раствор смеси едкого натра NaOH и сульфида натрия Na2S. Этим методом получают более половины производимой в мире целлюлозы.
По значимости второе место принадлежит сульфитному методу варки, относящемуся к группе кислотных. Активным варочным реагентом в сульфитном методе служит раствор сернистой кислоты H2SO3, содержащий некоторое количество одного из бисульфитов (гидросульфитов) кальция Са(НSО3)2, магния
Mg(HSO3)2, натрия NaHSO3 или аммония NH4HSO3. В бисуль-
фитном методе варки, представляющем также кислотный метод, варочным реагентом является водный раствор бисульфита магния, натрия или аммония.
Окислительные методы производства целлюлозы пока не получили широкого промышленного применения, но усиленно исследуются и разрабатываются. В качестве активных реагентов для делигнификации растительного сырья в них используются окислители, отличающиеся высокой избирательно-
42
стью по отношению к лигнину. Среди них следует назвать ки- слородно-содовый, кислородно-щелочной, гидротопный, окислительного аммонолиза и другие методы (без применения серосодержащих реагентов), с которыми связывают будущее целлюлозного производства.
Древесное сырье и его характеристика
Главным видом сырья для производства технической целлюлозы является древесина хвойных и лиственных пород. Запасы хвойных пород древесины в нашей стране сосредоточены в северо-восточных районах европейской части, в Западной и Восточной Сибири и на Дальнем Востоке. Отсутствие фенолов и низкое содержание смолы в древесине ели и пихты, на долю которых приходится соответственно 14 и 5 % всех лесных запасов, делают их главным видом сырья для сульфитцеллюлозного производства и производства белой древесной массы. В дальнейшем преимущественное использование ели и пихты для производства белой древесной массы, сульфитной и бисульфитной целлюлозы будет сохраняться. Большая часть лесных запасов России (около 58 %) приходится на сосну и лиственницу, являющихся преобладающей древесной породой в районах Восточной Сибири и Дальнего Востока. Из-за наличия в их древесине фенолов, высокого содержания смолы и водоэкстрактивных веществ (у лиственницы) сосна и лиственница плохо поддаются сульфитной варке и поэтому не применяются в качестве сырья для сульфитного метода.
Среди лиственных пород древесины наибольшее промышленное значение приобрела береза, занимающая более 13 % лесных площадей, второе место принадлежит осине. В южных районах страны промышленное значение могут иметь тополь, ольха, эвкалипт.
43
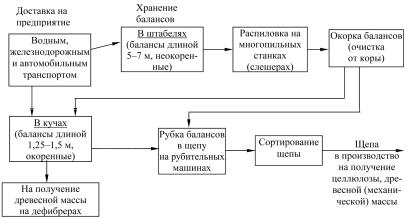
Подготовка древесины для производства волокнистых полуфабрикатов
Принципиальная схема подготовки древесины приведена на рис. 23.
Рис. 23. Подготовка древесины для получения полуфабрикатов
Доставка, выгрузка и хранение древесного сырья. Заго-
товленные в лесу балансы (рис. 24) в виде долготья (длина бревен 4,5–6 м) или коротья (длина бревен 1,25–1,5 м), а также технологическая щепа и дрова из соответствующих лесозаготовительных или деревообрабатывающих предприятий доставляются на цел- люлозно-бумажные комбинаты водным, железнодорожным или автомобильным транспортом (рис. 25, 26, 27). Наиболее экономичным видом транспорта является сплав древесины по рекам и озерам в буксируемых плотах или баржах.
Хранение древесного сырья осуществляется на лесных складах, представляющих собой открытую сухую (незатопляемую) площадку. На лесной бирже производятся выгрузка сырья из транспортных средств, распределение и укладка его на биржевой площадке, хранение и подача в производство (рис. 28).
44
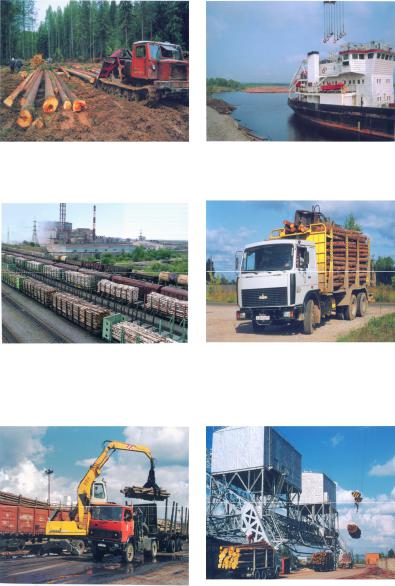
Рис. 24. Заготовкадревесинывлесу Рис. 25. Водныйспособдоставки
Рис. 26. Железнодорожныйспособ |
Рис. 27. Автомобильныйспособ |
доставкидревесины |
доставкидревесины |
Рис. 28. Разгрузка древесины на бирже
45
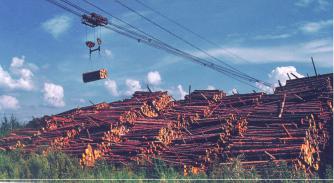
Существует четыре метода хранения древесного сырья:
вштабелях, в кучах, водный, открытый.
Вштабелях могут храниться неокоренные и окоренные балансы в виде долготья (длина бревен 4,5–6 м), в кучах – окоренные в виде коротья (1,25–1,5 м) (рис. 29).
Рис. 29. Хранение древесины в штабелях в виде неокоренного баланса длиной 4–6 м
Организации хранения балансов и технологических дров
вкучах отдают предпочтение при строительстве современных целлюлозно-бумажных предприятий, так как этот способ обеспечивает лучшее использование складских помещений и высокую степень механизации. В кучах балансы хранятся только
вокоренном виде в свободно насыпаемых кучах высотой до 30 м и шириной в основании до 100 м (рис. 30).
Водное хранение древесины используется в странах с незамерзающей водной акваторией (рис. 31).
Выгружаемые из воды или с железнодорожных платформ пучки древесины поступают на раскатный стол и далее на лесо-
транспортер многопильного станка (слешера), где распиливают-
ся на чураки длиной 1,25–1,5 м. Распиленные балансы направляются на окорку. Окоренные балансы попадают на ленточный лесотранспортер, а с него – на цепной конвейер, транспор-
46
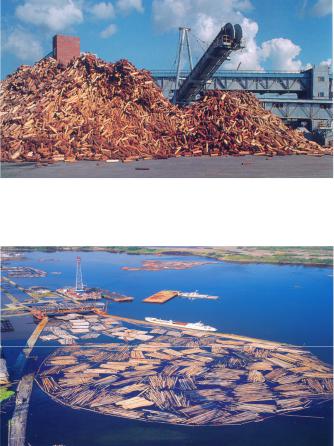
тирующий их к кучеукладчику (стаккеру). Кучеукладчик состоит из платформы, передвигающейся вдоль и над конвейером по рельсовым путям, к нижней части опор которой прикреплена металлическая ферма с изменяющимся углом наклона к горизонту (от 0 до 30°). На ферме смонтирован пластинчатый цепной транспортер.
Рис. 30. Кучевое хранение в виде коротких окоренных балансов
Рис. 31. Водное хранение древесины
47

Подготовка древесины к переработке. Хранение древеси-
ны на лесных складах является одной из главных операций по подготовке древесины к переработке. Дальнейшие операции по подготовке балансов к процессу варки целлюлозы или полуцеллюлозы сводятся к распиловке, окорке, рубке балансов в щепу, сортировке щепыидополнительному измельчениюкрупнойщепы.
Распиловка древесины. На рис. 32 показано устройство и принцип действия многопильного станка (слешера), получившего наибольшее распространение для распиловки балансов. Слешер состоит из смонтированного на наклонной деревянной или металлической раме многоцепного транспортера.
Рис. 32. Устройство и принцип действия многопильного станка: 1 – пилы; 2 – продольный транспортер; 3 – наклонная рама; 4 – захват; 5 – многоцепной транспортер; 6 – звездочка
Захваченные балансы с постоянной скоростью (около 0,2 м/с) поочередно надвигаются на вращающиеся дисковые пилы, распиливаются на отрезки определенной длины.
Окорка древесины. Балансы перед измельчением в щепу или перед дефибрированием должны быть очищены от коры (окорены), которая плохо проваривается по сульфатному методу и совершенно не проваривается по сульфитному, сильно засоряя целлюлозу.
48
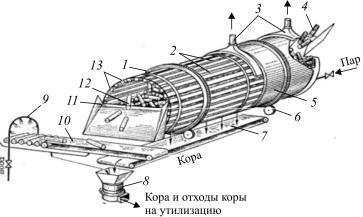
Наиболее широко применяются непрерывно работающие окорочные барабаны, позволяющие окаривать как коротье (барабаны со свободным заполнением) (рис. 33), так и длинник (барабаны с параллельной укладкой баланса).
Рис. 33. Устройство и принцип действия барабана для сухой окорки баланса: 1 – открытая окорочная секция; 2 – щели для удаления коры; 3 – вытяжная вентиляция; 4 – неокоренный баланс; 5 – закрытая секция; 6 – опорный ролик; 7 – транспортер отходов окорки; 8 – корорубка; 9 – кольцевой спрыск;
10 – транспортер окоренных балансов; 11 – подвижный затвор; 12 – окоренный баланс; 13 – профильные балки
Балансы длиной от 1 до 2,5 м подаются с торца барабана в закрытую секцию, заполняя барабан на 50–60 %, и за счет вращения барабана, переваливаясь и ударяясь о его стенки и один о другой, медленно продвигаются к противоположному, выгрузочному концу. При таком характере передвижения балансов происходит интенсивное разрушение и сдирание с них коры.
Рубка балансов в щепу. Задачей рубки является измельчение окоренных балансов в щепу, однородную по размерам (длина 16–20 мм, ширина 20–25 мм, толщина 2–3 мм) и с гладким отрубом. Повсеместно на целлюлозных заводах балансы из-
49
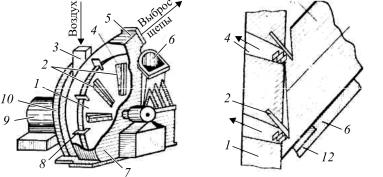
мельчают дисковыми многоножевыми рубительными машинами (рис. 34, 35). Рабочим органом рубительной машины является стальной диск с радиально расположенными ножами. Диск закреплен на горизонтальном стальном валу в трех подшипниках и приводится в движение приводом. Диаметр диска составляет 2–4 м, число ножей от 8 до 16, частота вращения до 650 мин–1.
Рис. 34. Устройство дисковой многоножевой рубительной машины и принцип измельчения балансов: 1 – стальной диск; 2 – ножи; 3 – всасывающий воздухопровод; 4 – прорезь в диске; 5 – патрубок; 6 – питающий патрон; 7 – кожух; 8 – лопатка; 9 – привод; 10 – диск-маховик; 11 – баланс; 12 – упорныйнож
Балансы по наклонно расположенному (угол наклона от 45 до 50° к горизонту) питательному патрону один за другим подаются к диску и попадают под удары ножей. Режущие кромки ножей, взаимодействующие с упорным ножом, отрубают от бревна шайбы толщиной 15–25 м, которые фасками ножей раскалываются вдоль волокон на отдельные кусочки, проскакивают сквозь прорези диска на его другую сторону и, ударяясь о стенки кожуха, дробятся в щепки. Толщина отрубаемых шайб регулируется выступом ножа над диском. Лопатками, укрепленными на ободе диска, по патрубку щепа вместе с потоком воздуха вы-
50