
книги / Плазменная химико-термическая обработка
..pdf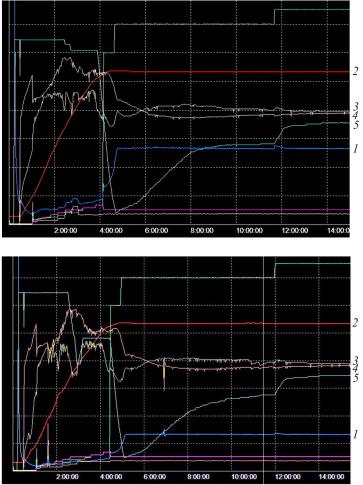
Характер изменения частоты вращения является одинаковым для разных процессов (рис. 2.18).
а
б
Рис. 2.18. Графический протокол процессов ионного азотирования в газовой смеси азот + водород + аргон садки деталей площадью 24 м2на установках ИОН-100 (а)
и ИОН-100И (б) (обозначения те же, что на рис. 2.17)
111
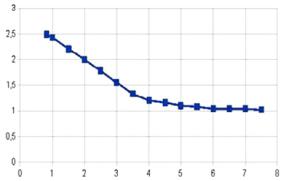
Как видно из представленных данных, активная фаза поглощения азота продолжается более 4 ч с момента начала процесса выдержки. Расчет изменения расхода газа в зависимости от частоты вращения насоса и давления в камере позволил установить, что в первые моменты насыщения суммарное поглощение азота составляет порядка 50 л/ч, а удельное, соответственно, на уровне 2–2,5 л/ч·м2 (рис. 2.19). Рассчитанное значение плотности потока азота для данного режима составило ПN = 2,62 л/ч·м2 (параметры процесса: плотность тока 3,61 А/м2, доля азота 0,81). Таким образом, в первые часы выдержки поглощение азота составляет почти 95% от рассчитанной плотности потока азота [54].
Общее количество азота MN, продиффундировавшего в глубь металла за время τ,определяется выражением [9]
MN = 2 (CNпов – CNсердц ), |
(2.36) |
где CNпов и CNсердц – соответственно концентрация азота на поверхности и в сердцевине.
ПN, л/ч·м2
τ, ч
Рис. 2.19. Удельная скорость поглощения азота в процессе азотирования
Из этого выражения следует, что чем больше градиент концентрации азота на поверхности относительно сердцевины дета-
112

ли, тем больший его поток продиффундирует внутрь металла за некоторое фиксированное время τ. Таким образом, управляя потоком активного азота на поверхность (особенно в первые моменты насыщения), можно создавать высокую концентрацию азота на поверхности, соответственно, и в глубине металла вследствие большого градиента концентрации. Это возможно при раздельной подаче азота и других компонентов газовой смеси с возможностью независимой регулировки расхода каждого из компонентов. Благодаря этому обеспечивается необходимая глубина азотированного слоя и распределение твердости по глубине за относительно непродолжительное время насыщения, существенно меньшее, чем при газовом азотировании.
2.5.Взаимосвязь параметра «плотность потока азота»
ихарактеристик обрабатываемой стали
Известно, что при разогреве садки и в первые моменты стадии выдержки при высокой плотности потока азота на поверхность возможно образование сплошного «белого» слоя нитридов железа, который существенно замедляет проникновение азота в глубь металла [87]. Такая ситуация имеет место как при газовом, так и при ионном азотировании [31, 34, 35]. Поэтому разогрев садки и изотермическую выдержку следует организовать таким образом, чтобы избежать преждевременного образования «белого слоя».
Согласно [88], из решения уравнения Фика для диффузии при граничном условии х = 0 (поверхность металла) можно получить параметр Ncr – «критическую» плотность потока азота, которую можно считать равной растворимости азота в ά-твердом растворе железа Сα–Fe.
|
2П |
|
|
|
τ |
|
|
N(0, τ) = Ncr = |
|
N |
|
|
, |
(2.37) |
|
|
D |
||||||
|
π |
|
|
|
|
и после преобразований получим выражение
113

ПN = 0,89 |
Cα − Fe Dα − Fe |
, |
(2.38) |
|
|||
|
τ |
|
где Сα–Fe – растворимость азота в ά-твердом растворе легированного железа, г/м3; Dα–Fe – коэффициент диффузии азота в альфа-твердом растворежелезавзависимостиоттемпературы(м2/с); τ– время, с.
Вданном случае время τ – это то время, в течение которого азот будет поглощаться поверхностью и диффундировать в глубь металла, не образуя на поверхности сплошной нитридный слой. Согласно моделям азотирования [1–5], первоначально азот растворяется в альфа-фазе, образуя твердый раствор азота в железе. Затем формируются нитриды легирующих элементов, и после этого начинается формирование вначале зародышей, а затем и сплошного слоя нитридов железа («белого слоя»), который существенно замедляет проникновение азота из газовой фазы в металл. Таким образом, параметры обрабатываемого материала: растворимость азота, коэффициент диффузии (зависящие от температуры, количества и типа легирующих элементов), а также время обработки, определяют выбор необходимой плотности потока азота, которую должен обеспечить тлеющий разряд, чтобы формировался диффузионный слой без образованияслоянитридовжелеза.
Вработе [89] приведены данные о влиянии легирующих
элементов в стали на значения величин Сα–Fe и Dα–Fe азота в α-фазе стали и методика расчета этих параметров:
−4575 |
+ 3 |
|
10 |
−( Ki(ni ) +...+ Kn(ni ) ) |
, |
(2.39) |
|
Сα – Fe = exp |
T |
|
|
||||
|
|
|
|
|
|
|
где Ki(ni ) – коэффициент активности легирующего элемента.
Dα − Fe = D0 |
B(ni ) + ... + B(nn ) |
|
|
|||
exp |
i |
n |
|
, |
(2.40) |
|
T |
|
|||||
|
|
|
|
|
|
где Bi(ni ) – коэффициент влияния легирующего элемента; D0 – коэффициент диффузии в чистом армко-железе [90].
114
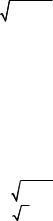
Исходя из химического состава стали обрабатываемых деталей можно рассчитать для температуры изотермической выдержки комплекс:
0,89Cα − Feлег · Dα − Feлег ,
где Dα − Feлег – коэффициентдиффузии; Cα − Feлег – растворимостьазота.
Рассчитанное значение этого комплекса позволит определить состав насыщающей среды (процент азота) на стадии выдержки. Чтобы за это время не сформировался преждевременно «белый» нитридный слой, необходимо, чтобы плотность потока азота ПN2+ в размерности (л/ч·м2), обеспечиваемая разрядом, была равна рассчитанной, котораяучитываетхарактеристикиазотируемойстали, т.е.
|
Cлег |
|
|
Dлег |
|
|
%N2 = |
α − Fe |
|
α − Fe |
, |
(2.41) |
|
|
j |
|
||||
|
|
τ |
|
где %N2 – доля молекулярного азота в составе газовой смеси, например: 0,25; 0,5 и т.п.; Cαлег− Fe – растворимость азота в легированном железе (стали); Dα − Feлег – коэффициент диффузии; j – плот-
ность тока тлеющего разряда; τ – время, в течение которого при заданной плотности тока разряда будет подаваться газовая смесь с таким содержанием азота, чтобы не сформировался преждевременно «белый» нитридный слой.
Таким образом, рассчитанное значение растворимости азота и коэффициента диффузии позволяют выбрать время и величину плотности потока азота таким образом, чтобы в первые моменты выдержки не смог образоваться слой нитридов железа.
Темп разогрева садки и предварительный выбор давления на выдержке определяются геометрией деталей, массой садки и ее площадью, т.е. величиной загрузки камеры. Например, на стадии выдержки известна мощность разряда и площадь садки. Из значений нормальной плотности тока для азота (см. рис. 2.9 и 2.11) выбираем рабочее давление с таким расчетом, чтобы плотность
115
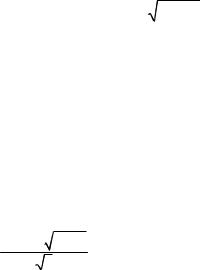
тока разряда была минимум в два раза больше нормальной плотности тока для данного давления и температуры. Это значение плотности тока и будет фигурировать в расчете необходимой плотности потока азота.
Рассмотрим пример расчета параметра 0,89Cα− Feлег · Dα− Feлег на
основании имеющихся литературных данных. В работе [91] приведены данные о азотировании в тлеющем разряде сталей различной степени легированности. Для стали типа «нитраллой» (отечественный аналог – сталь 38Х2МЮА) для температуры Т = 525 ºС получено значение коэффициента диффузии азота D = 1,04·10-12 м2/с, а расчетное значение растворимости азота в ά-твердом растворе для этой стали, полученное по (2.35), составляет величину Сά-Fe = 0,28 мас. %. Расчет растворимости в размерности (литр N2 в м3), проведенный по формуле (2.35), дает значение Cα-Feлег, равное 18 946. Рассчитаем те-
перьзначениепараметраплотностипотокаазота:
ПN = 0,89 Cα − Fe × τ Dα − Fe .
Для интервала времени τ = 1 ч (это время выдержки, в течение которого плотность потока азота должна быть ПN)
ПN = 0,89·18946·√1,04·10–12/√3600 = 2,87·10–4 лN2/м2с
(или 1,03 лN2/м2 ч).
Следует отметить, что это значение плотности потока азота оказалось меньше, чем определенное ранее из распределения концентрации азота по глубине азотированного слоя и равное ПN = 1,7 л/ч·м2. Возможно, это обусловлено тем, что при расчете рассматривается образование нитридов стехиометрического состава. В реальности, как это отмечено в [32], количество азота, аккумулируемого сталью в диффузионном слое, намного превышает необходимое для образования нитридов легирующих элементов стехиометрического состава.
116

Таким образом, для организации режима изотермической выдержки необходимо задать плотность потока азота, которую формирует тлеющий разряд, равную полученной расчетным путем: ПN+2 разр. должна быть равна ПN2расч.
ПN+2 (л/ч·м2)разряда = 0,897·j (А/м2) · (%N2) =
= ПN |
2 |
(л/ч·м2)расч = 0,89 ·Cα–Fe |
лег |
· √Dα–Fe |
лег |
/√τ. |
(2.42) |
|
|
|
|
|
После преобразований получим выражение, связывающее искомую долю азота в смеси активных газов, как функцию плотности тока разряда, времени азотирования τ и характеристик азотируемой стали Cα–Feлег и Dα–Feлег:
(%N2 ) = Cα− Feлег Dα− Feлег / j τ. |
(2.43) |
Для приведенного выше примера расчета параметра ПN процентное содержание азота в смеси газов будет зависеть от величины плотности тока. Так, например, для плотности тока j = 5 А/м2 доля азота в смеси должна быть %N2 = 1,03:0,897:5 = 0,23, а при плотности тока j = 3,5 А/м2 соответственно %N2 = 0,33. Таким образом, чем меньше плотность тока, тем больше должна быть доля азота в составегазовойсмеси.
Таким образом, для каждой марки стали, в зависимости от температуры процесса и загрузки камеры, которые определяют мощность разряда, заданной плотности потока азота соответствует определённое время τ. В течение этого времени азот будет эффективно поглощаться поверхностью деталей без образования нитридного (белого) слоя.
Выражение (2.43) и есть «азотный потенциал» тлеющего азотсодержащего разряда для конкретной марки стали при ионном азотировании.
Для каждой марки стали существует определённый диапазон значений плотности потока азота, обеспечивающий предельную концентрацию азота в α-твёрдом растворе. Для определения влияния величины плотности потока азота в разряде на характеристики
117
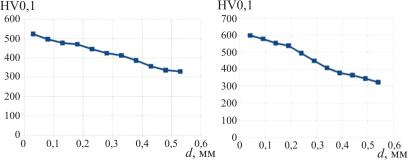
азотированного слоя проводились эксперименты по азотированию стали 40Х при одинаковой температуре (535 °С), одинаковом процентном содержании азота в смеси с водородом и аргоном, но при различном давлении – 125 и 185 Па. Это обусловило разную плотность тока, и, как следствие, различную величину плотности потока азота. Параметрыпроцессовотраженывтабл. 2.4.
Параметры процесса отражены в табл. 2.4.
|
|
|
Таблица 2.4 |
Параметры процессов азотирования стали 40Х |
|||
|
|
|
|
Шаг |
Длительность, |
ПN2(л/ч·м2) – режим 1 |
ПN2(л/ч·м2) – режим 2 |
выдержки |
ч |
(давление 185 Па) |
(давление 125 Па) |
1 |
1 |
1,33 |
1,03 |
2 |
0,5 |
3,19 |
2,58 |
3 |
5 |
1,97 |
1,62 |
4 |
7,5 |
1,59 |
1,33 |
Распределение микротвердости по глубине азотированного слоядлярежимов1 и2 табл. 2.4 представленонарис. 2.20.
а |
б |
Рис. 2.20. Распределение микротвердости по глубине азотированного слоя: а – режим 1; б – режим 2 (табл. 2.4)
Как видно из представленных данных, изменение величины плотности потока азота в разряде позволяет управлять не только величиной поверхностной твердости, но и распределением твердости по глубине слоя.
118
2.6. Влияние состава газовой смеси при разогреве садки на формирование азотированного слоя
Рассмотрим влияние состава газовой смеси при разогреве садки деталей на параметре азотированного слоя широко используемой стали 38Х2МЮА. Считается, что диффузия азота в глубину металла начинается уже при температуре 350 ºС, оказывает значительное влияние на процесс формирования азотированного слоя [31, 35]. В работе [92] показано, что при газовом азотированииуже на стадии разогрева садки деталей может сформироваться γ'-Fe4N-слой, что будет препятствовать дальнейшему процессу азотирования вследствие снижения коэффициента диффузии азота в γ'-Fe4N-слое [31]. Следует учитывать тот факт, что при газовом азотировании используется аммиак, взаимодействующий с поверхностью металла при разогреве, а степень взаимодействия зависит от кратности газообмена в печи [31, 35]. При ионном азотировании могут быть использованы аммиак NH3 и различные азотсодержащие газовые смеси – диссоциированный NH3 (смесь газов – 25 % N2 + 75 % Н2), Ar+N2++H2, Ar+N2, N2 + H2, Ar+NH3 вразличныхпропорцияхидр.
Ранее было показано (2.42), что при азотировании желательно плотность потока азота в разряде задавать равной или близкой к расчетному значению, зависящему от степени легированности стали и температуры, т.е необходимо задать плотность потока азота, которую формирует тлеющий разряд, равную полученной расчетным путем: ПN2+разр должна быть равна
ПN2расч. А так как в выражение для расчетной плотности потока
азота ПN2расч = 0,89·Cα–Feлег · √Dα–Feлег /√τ входят такие характеристики стали, как растворимость азота и его коэфффициент диф-
фузии, то их необходимо рассчитать для температурного интервала от 350 ºС, когда уже возможна диффузия азота из разряда в металл, до температуры изотермической выдержки.
Расчет растворимости азота и его коэффициента диффузии в легированной стали проводился по методике, изложенной в [89],
119
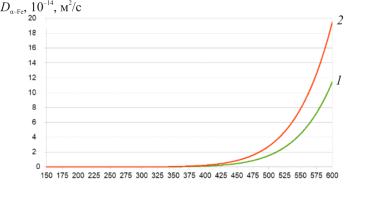
при этом коэффициент диффузии азота (м2/с) в чистом железе принимался из [90]:
Dα = 6,6 10 |
−7 |
|
−77900 |
|
, |
(2.44) |
|
exp |
RT |
|
|||
|
|
|
|
|
|
гдеR – газоваяпостоянная, R = 8,31 Дж/моль·К; Т– температура, К. Используя данные по коэффициентам легирования для разных элементов [89], получили значение коэффициента диффузии азота в альфа-твёрдом растворе стали 38Х2МЮА в зависимости от температуры для максимальной и минимальной концентрации легирую-
щихэлементоввсоответствиисГОСТ4543-2016 (рис. 2.21).
K, °C
Рис. 2.21. Зависимость коэффициента диффузии Dα-лег от температуры и содержания легирующих элементов: 1 – коэффициент диффузии длямаксимальнойконцентрациилегирующихэлементов; 2 – коэффициент диффузиидляминимальнойконцентрациилегирующихэлементов
В соответствии с данными из [89] рассчитана также растворимость азота в альфа-твёрдом растворе стали 38Х2МЮА в зависимости от температуры для максимальной и минимальной концентрации легирующих элементов и также для нелегированного железа (рис. 2.22).
Плотностьпотокаазота, л/ч·м2, рассчитываласьпоформуле(2.29):
ПN+2 разр = 0,897·j·(%N2).
120