
книги / Плазменная химико-термическая обработка
..pdftотк = 2,3 |
Vкам |
|
1,013 105 |
|
+ |
Vкам |
1 |
− |
1 |
|
|
|||
|
S |
lg |
p |
|
C |
|
|
|
|
, (2.13) |
||||
p |
1,013 105 |
|||||||||||||
|
|
|
н |
|
пред |
|
|
|
|
пред |
|
|
|
|
где Vкам – объем вакуумной камеры, м3; Sн – скорость откачки на-
соса, м3/с либо л/с; рпред – предельное давление, Па, при котором режим течения газа остается вязкостным, определяется по фор-
муле (2.8); C – величина, характеризующая геометрию трубопровода, C = 1360d4/l, d – диаметр, м; l – длина, м.
При расчете времени откачки камеры по формуле (2.13) в качестве значения Sн можно использовать уменьшенную на 10–15 % номинальную скорость откачки насоса (паспортную), т.е. принимать коэффициент использования насоса на уровне 0,85–0,9. Расчеты по (2.13) показывают, что время откачки вакуумной камеры с объемом 2 м3 до предельного давления 30 Па составляет 12–15 мин, а камеры объемом 5 м3 – 30–35 мин, что при выдержке садки в течение 14–16 часов является несущественным при ионном азотировании.
Однако если процесс проводится при давлении 250–800 Па, то для обеспечения баланса «расход газа – давление» при скорости откачки порядка 20 л/с (см. рис. 2.5) необходимо существенно увеличивать расход газа. Это с точки зрения обеспечения необходимого количества химически активной среды (атомарного азота) является совершенно неоправданным и приводит к значительному перерасходу газов. Более оптимальный вариант – управление скоростью откачки путем использования откачного агрегата, состоящего из двух насосов – форвакуумного и двухроторного (типа ДВН-50 (НВР-200)), соединенных последовательно. В таком случае, изменяя частоту вращения ротора насоса ДВН-50, можно управлять скоростью откачки вакуумного агрегата, состоящего из двух насосов. Зависимость эффективной скорости откачки вакуумного агрегата, состоящего из насосов ADVAVAC-75 и ДВН-50, от частоты напряжения, питающего электродвигатель насоса ДВН-50, представлена на рис. 2.7 [76].
91
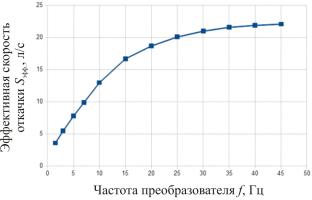
Рис. 2.7. Частотная зависимость скорости откачки агрегата ADVAVAC-75 + ДВН-50
Как видно, путем изменения частоты вращения ротора можно в широких пределах управлять скоростью откачки вакуумного агрегата и эффективной скоростью откачки системы «насос–вакуумная магистраль». Это обеспечивает независимое управление расходом газа, скоростью откачки и, следовательно, давлением в камере. Кроме того, позволяет проводить азотирование как при низком давлении и большом расходе газа, так и при высоком давлении в камере при относительно небольших расходах плазмообразующего газа. Все эти факторы в целом обеспечивают: широкие пределы параметров процесса ИПА по величине площади обрабатываемых деталей; минимизацию расхода активных газов и электроэнергии для питания вакуумных насосов. Это в свою очередь является важным моментом, поскольку с ростом скорости откачки насоса увеличивается и мощность электродвигателя.
Таким образом, с одной стороны, давление определяется параметрами насоса, откачной магистрали и расхода газа, а с другой – оно должно обеспечить существование тлеющего разряда в «аномальном» виде.
92
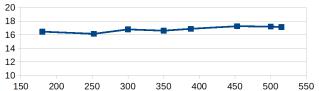
2.3. Взаимосвязь параметров тлеющего разряда и газодинамических характеристик процесса ионного азотирования
Как было сказано ранее, для «аномального» тлеющего разряда (постоянного или пульсирующего тока) рабочий диапазон «ток-напряжение» должен быть в области, где имеет место возрастающая вольт-амперная характеристика (см. рис. 1.27). В свою очередь вольт-амперная характеристика разряда зависит от рабочего давления в камере. Как было установлено в [77], для обеспечения необходимой температуры садки на стадии выдержки затрачивается мощность разряда, незначительно изменяющаяся в зависимости от давления в камере (рис. 2.8) [77].
Рразр., кВт
р, Па
Рис. 2.8. Изменение мощности тлеющего разряда при повышении давления в камере при обработке деталей
при температуре садки 530 °С
Для тлеющего разряда в различных газах существует определенная взаимосвязь параметра j/р2 и величины катодного падения потенциала (см. рис. 1.28). Как видно из представленных на рисунке данных для азота, аргона и водорода, в достаточно большом интервале значений j/р2 величина катодного падения потенциала вначале незначительно отличается от значений нормального катодного падения (на графике это обозначено кружками). Затем наблюдается увеличение значения катодного падения потенциала. Это означает, что при определенных значениях давления и тока разряд может существовать в двух видах: аномальном и частично нормальном. Увеличение прикладываемого на-
93
пряжения будет приводить лишь к росту тока. При определенных сочетаниях ток-давление на части садки разряд может вообще отсутствовать, что недопустимо (см. рис. 2.1) [60].
Рассмотрим типичные значения параметров процесса ИПА на промышленном оборудовании. Например, при обработке садки деталей суммарной площадью 24 м2 (см. рис. 1.26). При температуре изотермической выдержки 540 °С сила тока разряда составляет 85 А, напряжение – 380 В. Определим диапазон давлений, который обеспечит существование тлеющего разряда в форме аномального. При катодном падении потенциала на уровне85 % от приложенного напряжения величина Uкпп для азота (составляющего 80 % в газовой смеси азот-аргон-водород) будет равна 323 В. Из данных рис. 1.28
для азота значению Uкпп = 323 В соответствует приведенная плотность тока j/р2 = 1,53 · 10–3 А/м2·Па2. Из этого значения j/р2 можно
рассчитать приведенное давление, соответствующее температуре катода-садки540 °С:
P |
= P |
300 |
, |
(2.14) |
прив |
изм T |
|
|
|
|
|
кат |
|
|
где Pизм – измеренное давление в холодной зоне камеры, Па; Ткат – температура садки-катода, К.
При j = 3,54 А/м2 и Ткат = 813 К измеренное значение давления, Pизм, должно быть 130 Па. Следовательно, повышение давления сверх данного значения может привести к тому, что значение j/р2 уменьшится. Как это видно из зависимостей на рис. 1.28, величина катодного падения потенциала будет близка к нормальному. Это может привести к тому, что на части садки разряд может не существовать и упрочняющая обработка не пройдет. Поэтому для получения азотированного слоя на всей поверхности всех деталей в садке необходимо, чтобы выполнялось условие
j |
≥ jN2 |
(P,T ), |
(2.15) |
разр |
норм |
|
|
где jразр – плотность разрядного тока, А/м2; jнорм – нормальная плотность тока для азота, А/м2.
94
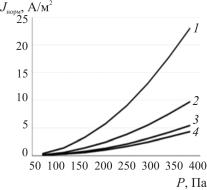
Азот, как компонент рабочей смеси, имеет максимальное значение jнорм при определенном давлении в камере и температуре садки. Выполнение этого условия обеспечит при разогреве садки и ее выдержке плотное «облегание» поверхности катода (в данном случае деталей садки) аномальным тлеющим разрядом.
На рис. 2.9 приведены значения нормальной плотности тока jнорм, A/м2, для азота, рассчитанные по формуле, применяемой для разрядов с плоскими электродами [78],
j |
= 4 |
P |
Tн |
, |
(2.16) |
|||
|
P |
|||||||
норм |
|
T |
|
|
|
|||
|
|
|
н |
|
|
|
|
где Р – рабочее давление, Па; Рн = 133 Па; Тн = 300 К; Т – температура газа в катодной области разряда, которая принималась равной температуре катода.
Рис. 2.9. Расчетные значения нормальной плотности тока jнорм в зависимости от давления для разной температуры катода, °С:
1 – 100; 2 – 300; 3 – 500; 4 – 600
Видно, что при одинаковом давлении по мере повышения температуры в камере плотность тока, обеспечивающая существование разряда в виде аномального, снижается. С другой стороны, при одинаковой температуре рост давления в камере приво-
95
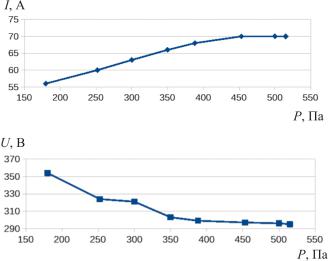
дит к повышению плотности тока, что необходимо учитывать при выборе режима обработки. На рис. 2.10 показано изменение силы тока разряда и напряжения при повышении давления в камере [77]. На рис. 2.11 приведены расчетные значения нормальной плотности тока как функции температуры.
а
б
Рис. 2.10. Изменение силы тока (а) и напряжения (б) при повышении давления в камере при постоянной температуре садки Т = 530 °С
Повышение давления в камере приводит к росту плотности тока, поэтому при высоком рабочем давлении тлеющий разряд может существовать частично в формах нормального и аномального, если катодное падение потенциала близко к нормальному значению. Сравнение реальной плотности тока с расчетной при обработке различных по массе и площади поверхности садок при температуре 530 ºС показало, что чем ниже рабочее давление, тем большую «степень аномальности» разряда К можно обеспечить при одинаковой температуре садки (табл. 2.1).
96
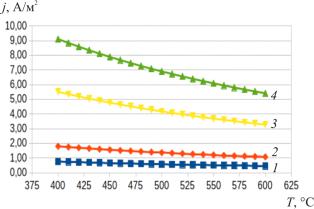
K = |
jэксп |
, |
(2.17) |
|
jрасч |
||||
|
|
|
где jэксп – экспериментальное значение плотности тока, A/м2; jрасч – расчетное значение плотности тока для азота при конкретных значениях температуры и давления, A/м2.
Рис. 2.11. Расчетные значения нормальной плотности тока в зависимости от температуры катода-садки при различных давлениях, Па: 1 – 130; 2 – 200; 3 – 350; 4 – 450
Таблица 2.1
Значения экспериментальных и рассчитанных величин плотности тока разряда
|
|
|
|
Р, Па |
jэксп, А/м2 |
jрасч, А/м2 |
К = jэксп/jрасч |
194 |
3,36 |
1,15 |
2,92 |
194 |
3,4 |
1,15 |
2,96 |
196 |
4,3 |
1,16 |
3,7 |
197 |
3,6 |
1,2 |
3,0 |
200 |
4,26 |
1,3 |
3,28 |
313 |
5,18 |
3,1 |
1,67 |
318 |
5,68 |
3,2 |
1,78 |
342 |
5,1 |
3,7 |
1,38 |
362 |
5,0 |
4,2 |
1,19 |
97
Из табл. 2.1 видно, что при давлении р = 196 Па величина К = 3,7, а при давлении р = 362 Па К = 1,19. Таким образом, чем выше рабочее давление при азотировании, тем больше шансов разряду быть частично «аномальным» и частично «нормальным». В этом случае не вся поверхность садки может быть охвачена разрядом, особенно ее верхняя часть. Все эти факторы необходимо учитывать при разработке конкретных режимов азотирования на промышленном оборудовании.
Практический опыт обработки садок деталей различной конфигурации показал, что при конкретной мощности разряда на стадии выдержки плотность тока должна быть минимум в два раза выше значения нормальной плотности тока при данном давлении. Это будет гарантированно обеспечивать существование разряда в виде аномального на всей поверхности катода-садки.
2.4. Формирование азотированного слоя при азотировании в тлеющем разряде
Модели управления структурой азотированного слоя с помощью индекса азотирования (азотного потенциала), которые имеются для описания процесса газового азотирования в аммиаке, для ионного азотирования в разряде не подходят. Это обусловлено тем, что, в отличие от газового азотирования, происходящего в равновесных условиях, процесс ионного азотирования является неравновесным и в нем появляется новые составляющие – электрические параметры процесса (плотность тока тлеющего разряда и катодное падение потенциала). Эти параметры тлеющего разряда наряду с концентрацией азота являются определяющими для процесса ионного азотирования.
Таким образом, параметром, характеризующим интенсивность процесса ионного азотирования при тлеющем разряде, может быть плотность потока азота, которая определяется взаимосвязанными параметрами (давлением, составом газовой среды, температурой процесса и плотностью тока).
98
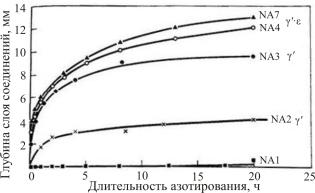
Состав насыщающей среды (доля азота в составе смеси газов) существенно влияет на кинетику формирования азотированного слоя. Это наглядно иллюстрируют зависимости глубины нитридного слоя на конструкционной стали 42CrMo4 от времени выдержки при температуре 570 ºC при разных азотирующих атмосферах (смеси азота и водорода) (рис. 2.12). Показано, что по мере увеличения доли азота в составе смеси растет глубина нитридного слоя.
Рис. 2.12. Влияние насыщающей способности среды на глубину нитридного слоя на стали 42CrMo4 в зависимости от длительности азотирования: NA 1; 2; 3; 4; 7 – обозначения азотирующих сред по мере возрастания доли азота в смеси с водородом [35]
На рис. 2.13 показано влияние процентного содержания азота в смеси с водородом на формирование упрочненного слоя на инструментальнойсталиН– 13 (отечественныйаналог4Х5МФ1С) [79].
Таким образом, приведенные литературные данные наглядно демонстрируют тот факт, что процентное содержание азота в газовой смеси с водородом существенно влияет как на глубину слоя, так и на образование на поверхности нитридного (белого) слоя.
Отсюда следует, что и при ионном азотировании, как и при газовом, существует взаимосвязь между содержанием азота в
99
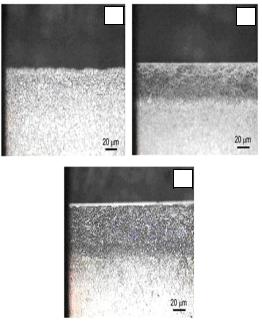
смеси и временем образования нитридного слоя. Доказательством тому служат кривые «азотного потенциала» (содержание азота в смеси с водородом), определяющие области с формированием нитридного слоя и без него при азотировании инструментальных сталей D–2 (отечественный аналог – сталь Х12М) и сталей Н–13 (рис. 2.14). Следует отметить, что эти данные относятся лишь применительно к данному конкретному оборудованию, на котором приводилась обработка, и конкретной загрузке камеры. При других параметрах процесса конкретные значения процентного содержания азота, при которых начинает формироваться белый слой, будут другими, но характер влияния содержания азота на образование белого слоя останется таким же.
а б
в
Рис. 2.13. Вид азотированного слоя на стали Н–13 после обработки в течение 3 ч при температуре 520 ºC; а – 25 % азота в смеси с водородом; б – 50 %; в – 75 %
100