
книги / Технология автоматизированного производства лопаток газотурбинных двигателей
..pdfЗдесь деталь, в частности блок сопловых лопаток, своими техноло гическими базами устанавливается в контрольное приспособление. Кон тролируемая деталь определена в нем однозначно, система координат детали совмещена с системой координат приспособления. В этом поло жении отклонения контура сечения спинки или корыта от соответствую щего шаблона выявляют визуально, на просвет или щупом, т.е. смещение определяют путем прокладки щупа между поверхностями пера и шаб лона.
При таком методе контроля обнаруживается комплексная погреш ность отклонения профиля, так как выявить по отдельности смещение контура пера по осям У и X, а также разворот по оси 7 и погрешность формы невозможно.
Более совершенным методом и средством контроля являются опти ко-механический способ и прибор для его осуществления ПОМКЛ-4. В нем одновременно контролируются профиль сечения пера, смещение и угол закрутки [7].
Длительное время эти приборы оставались наиболее распространен ными средствами контроля лопаток. Однако в современных условиях данные приборы не гарантируют возможности контроля лопаток, изго товляемых по первому классу точности.
Кроме того, сегодняшние технологии изготовления проточной части лопаток методами литья по выплавляемым моделям обеспечивают высо кую повторяемость геометрических размеров лопаток, изготовляемых в пределах одной партии, что позволяет вести статистический, выбороч ный контроль деталей.
С этой целью в настоящий момент все большее применение находят координатно-измерительные машины (КИМ), причем используют для контроля лопаток в первую очередь цеховые КИМ. Это значительно уменьшает затраты на специальные помещения с искусственным клима том, транспортирование деталей и изделий при контроле.
Более того, контроль одной и той же детали, осуществленный сна чала в литейном цехе, а затем в механическом, носит объективный харак тер, не вызывает споров между различными производственными подраз делениями по поводу методики и средств измерения, так как в том и дру гом случаях измерения проведены на КИМ от одной и той же САБмодели.
Современные КИМ представляют собой высокоточные устройства, управляемые компьютерами, с развитыми библиотеками программ для
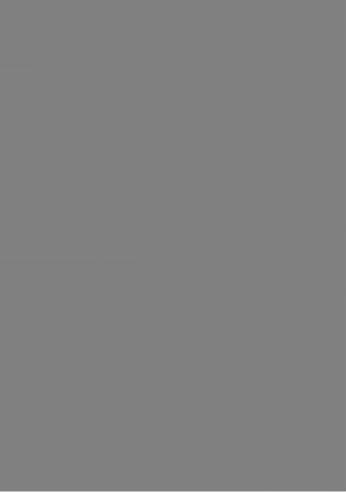
2.Контролируемая деталь базируется (совмещается) с ее CADмоделью.
На этом этапе на CAD-модели оператором КИМ отмечаются шесть базовых точек, лежащих в трех различных плоскостях. Точки выбирают ся таким образом, чтобы с их помощью можно было построить трехмер ную систему координат, в которой располагается CAD-модель. Коорди наты каждой базовой точки CAD-модели заносятся в компьютер.
На физической контролируемой детали, установленной на столе КИМ в ручном режиме, оператор касается щупом шести аналогичных точек, выбранных приблизительно, т.е. точки выбираются по аналогии с CAD-моделью, чтобы с их помощью можно было построить трехмерную систему координат, в которой располагается физическая деталь.
Затем осуществляется непосредственно процесс выравнивания CAD-модели и контролируемой детали, что выполняется с помощью функции итеративного выравнивания. В процессе выравнивания система координат физической детали совмещается с системой координат CADмодели.
После завершения этого процесса контролируется его выполнение. Для этого в автоматическом режиме КИМ касается щупом измеритель ной головки шести точек на детали, координаты которых соответствуют шести базовым точкам CAD-модели. Отсутствие отклонений физической детали с моделью свидетельствует о завершении процесса выравнивания.
3.Проводится контроль детали. На этом этапе указываются сече ния, в которых необходимо измерить отклонения; задаются предельные значения отклонений; рассчитывается программа перемещения щупа из мерительной головки в каждом контролируемом сечении; осуществляет ся перемещение щупа измерительной головки по программе. Процесс измерения отображается на экране в реальном масштабе времени в виде текущих значений положения щупа и отклонения формы.
4.Параллельно создается протокол измерений в форматах Microsoft, Word или Exei с отметками превышения предельных значений, графиками отклонений, гистограммами разброса результатов.
Пример такого протокола приведен на рис. 2.53.
Из протокола, представленного на рис. 2.53, следует, что деталь по толщине профиля соответствует чертежу, однако сам профиль смещен по осям Л' и У, и одновременно имеет разворот по оси Z. С учетом допусков на смещения по этим осям и по углу, которые суммарно не превышают верхней границы теоретического профиля, в данном сечении лопатка может быть признана годной.
Рис. 2.53. Графический протокол измерения отклонений профиля проточной части лопатки турбины в одном из сечений:
1 - теоретический профиль лопатки; 2 , 3 - соответственно верхняя и нижняя границы теоретического профиля лопатки; 4 - фактический профиль лопатки в контролируемом сечении
Так же проверяются и остальные сечения проточной части лопатки в направлении I. В каждом сечении после измерения на КИМ оформляется аналогичный протокол или протокол в виде таблицы. На основе их ана лиза и принимается окончательное решение о соответствии контроли руемой детали конструкторской документации.
На лопатках турбин кроме проточной части лопаток необходимо контролировать:
-размеры хвостовиков по длине;
-углы установа хвостовиков;
-перекос рабочих поверхностей зубьев одной гребенки относитель но другой на длине хвостовика типа "елка";
-взаимное смещение зубьев одной гребенки относительно другой в направлении плоскости симметрии хвостовика типа "елка";
-конусность зубьев по роликам, по длине хвостовика типа "елка". Контроль хвостовиков этого типа в условиях серийного производст
ва чаще всего осуществляют универсальными измерительными и индика торными приборами с применением специальной оснастки и эталонов. Так, толщина хвостовика типа "елка" контролируется при помощи изме рительных роликов и микрометра. Углы расположения рабочих поверх ностей зубьев гребенки хвостовика, а также радиусы впадин и вершин зубьев измеряются на универсальных микроскопах. Погрешности смеще ния и перекрещивания профилей зубьев одной гребенки относительно другой контролируют на специальной оснастке посредством индикатор ных приборов.
Данные методы измерения хвостовиков несовершенны из-за боль шой трудоемкости контроля, недостаточной объективности и точности. Однако альтернативы применяемой оснастке в реальном производстве пока нет. Поэтому в процессе контроля размеров хвостовиков осуществ ляется их 100 %-ная проверка.
Для выявления трещин, раковин, пор, включений, а также для кон троля толщины стенок и покрытий на лопатках применяют в основном капиллярные, ультразвуковые, вихретоковые и другие методы неразру шающего контроля.
Так, для выявления дефектов, выходящих на поверхность лопатки в виде пор, трещин, волосовин, используется капиллярный метод ЛЮМ10В. Он основан на проникновении индикаторной жидкости в поверх ностные полости контролируемой детали и ее последующем свечении под действием ультрафиолетового света. Метод общепризнан и применя ется повсеместно при изготовлении лопаток турбин [4]. Таким методом в первую очередь контролируют на наличие дефектов проточную часть лопатки.
Контроль поверхностных дефектов в пазах елочного профиля осу ществляют методом вихревых токов. Вихретоковый метод основан на анализе взаимодействия внешнего электромагнитного поля с электромаг нитным полем вихревых токов, наводимых в объекте контроля. Для кон троля вихретоковым методом испольуется прибор ВД4-20М, разработан ный на предприятии "Салют" (г. Москва). Прибор позволяет выявить де фекты нарушения сплошности по всему пазу. Максимальная толщина об наруживаемой трещины 0,8; глубина 0,1; ширина 0,001 мм [7].
Для контроля толщины наносимых покрытий используют радиаци онные методы, в частности рентгеновский толщиномер РТ-1. Прибор основан на взаимодействии рентгеновского излучения от малогабаритной рентгеновской трубки с вольфрамовым или серебряным анодом прострельного типа. Регистрируется излучение, рассеянное материалом по крытия и подложки. Прибор годится и для контроля многокомпонентных покрытий путем определения концентрации отдельных компонентов по глубине [7].
Завершается процесс контроля лопаток нанесением клейма, свиде тельствующего о качестве изготовления. Места нанесения клейм, метод клеймения, высота шрифта указываются в габаритных размерах лопатки.
В настоящий момент при изготовлении лопаток турбин наибольшее применение нашел электрохимический метод. Глубина гравировки при данном методе составляет < 0,03 мм. Прижоги и микротрещины отсутст
вуют. Серьезную альтернативу данному методу в ближайшем будущем составит лазерный метод клеймения. Скорость нанесения информации с помощью лазерного маркера может достигать 20 знаков в секунду. Глу бина гравировки при этом составляет 0,015...0, 03 мм, а глубина изме ненного слоя < 0, 002 мм. Выпускает такие маркеры фирма ТазсЬапег Ре&с11 (Германия) - сер. ТР.
2.8.ТЕХНОЛОГИЯ ИЗГОТОВЛЕНИЯ ЛОПАТОК ТУРБИН
НА МНОГОЦЕЛЕВЫХ СТАНКАХ
Пооперационная технология изготовления рабочих и сопловых ло паток турбин описывает порядок выполнения операций в рамках серий ного и крупносерийного производств. В условиях единичного, опытного и мелкосерийного производств данная технология неприемлема. Она не обеспечивает необходимой гибкости (переналаживаемости) мощностей, требует продолжительной и дорогостоящей подготовки производства, а также имеет длительный цикл изготовления деталей.
Названные проблемы решаются при реализации процесса изготов ления лопаток турбины на многоцелевых обрабатывающих центрах, в частности в фирмах Мй§ег1е, В1ош, ЕЬВ-ЗсИЖ (рис. 2.54).
Машинообрабатывающие центры этих фирм имеют до пяти одно временно управляемых координат, несколько механизмов правки, шпин дельные узлы, способные разместить ряд шлифовальных кругов или ин струментальные магазины на шесть-восемь планшайб.
В то же время, приспособления для установки и закрепления дета лей обеспечивают единство технологических баз при переустановке де талей. В первую очередь это достигается посредством закрепления дета лей в кассете (брикете).
Установка и закрепление детали путем заливки в брикет позволяют при обработке лопатки на многоцелевом станке осуществить обработку практически всех ее поверхностей за одну установку, не меняя техноло гических баз. Здесь операции обработки торцов хвостовика со стороны входной и выходной кромок, шлифование плоскостей и клина хвостовика со стороны спинки корыта, обработка "елочного" профиля замка со сто роны спинки и корыта, обработка зигов и другие операции могут быть выполнены за один установ брикета. Ограничением числа совмещенных переходов здесь является число шлифовальных кругов в магазине станка, имеющих соответствующий той или иной операции профиль круга.
Рис. 2.54. Технологический процесс обработки сопловой лопатки на многоцелевом станке:
/... VIII - соответственно первый-восьмой переходы
Однако такой способ можно применять не на всех типоразмерах де талей и конструкциях лопаток, в частности блоки лопаток соплового ап парата, состоящие из трех-шести деталей, заливать в брикет явно нецеле сообразно. В этом случае число переустановок при смене технологиче ских баз должно быть минимально, лучше две.
При соблюдении этих условий обработка лопаток сопловых аппара тов на многоцелевом станке также приводит к концентрации операций, превращению технологических операций предыдущих технологических процессов в технологические переходы. Пример такой технологии при веден на рис. 2.55.
В представленном на данном рисунке технологическом процессе весь контур лопатки соплового аппарата обрабатывается за две операции.
Рис. 2.55. Технологический процесс обработки сопловой лопатки на многоцелевом станке:
а- первая операция, первый переход; б - первая операция, второй переход;
в- первая операция, третий переход; г - первая операция, четвертый переход; д - первая операция, пятый переход; е - вторая операция, первый и второй
переходы
Первая операция состоит из пяти переходов, вторая из двух. При первой операции технологическими базами являются: точки 1...3 на бандажных плоскостях (установочная база); точки 4 и 5 на торцах верхней и нижней бандажных полок (направляющая база); точка 6 на верхней бандажной полке со стороны проточной части (опорная база).
При смене операций технологические базы переходят на аналогич ные поверхности, противоположные тем, которые являлись базами пер воначально. Пять переходов на первой операции выполняются благодаря тому, что деталь и инструмент имеют возможность перемещаться друг относительно друга в пяти координатах, а на шпинделе станка или в ма
газине может быть размещено несколько абразивных кругов, на которых правящие ролики постоянно или дискретно нарезают пять режущих фа сонных поверхностей.
На второй операции обрабатываются поверхности, закрытые при ба зировании детали на первой операции. Здесь они обрабатываются круга ми из сверхтвердых материалов на режимах высокоскоростного шлифо вания (vK= 80 м/с). В качестве режущего инструмента при этом исполь зуются шлифовальные круги из кубического нитрида бора на гальвани ческой связке. Физико-механические характеристики кубического нитри да бора значительно выше, чем абразивных материалов.
Так, например, микротвердость кубического нитрида бора 900 МПа, электрокорунда 200 МПа; модуль упругости нитрида бора 7200 МПа, электрокорунда 3200 МПа; коэффициент теплопроводности нитрида бора 0,1 кал/(см с °С), электрокорунда 0,047 кал/(см-с-°С).
Следовательно, разрыв по твердости у обрабатываемого материала и инструментального (кубического нитрида бора) значительно выше, чем у остальных абразивов, поэтому возможна более высокая скорость резания. В частности, обработка никелевых сплавов кругами из кубического нит рида бора составляет порядка 60...80 м/с, абразивными кругами < 30 м/с. Образующаяся при этом тепловая энергия уходит не только в срезаемые слои металла, но и в круг, который выполняется на металлической связке.
По сравнению с кругами на керамической связке это обеспечивает не только высокий отвод теплоты из зоны резания, но и высокую проч ность режущей системы зерно-связка. При этом используемый для дан ной обработки машинообрабатывающий центр должен иметь:
-возможность взаимного перемещения деталей не менее чем в пяти координатах;
-систему управления, обеспечивающую одновременное перемеще ние детали и инструмента в пяти координатах;
-магазин инструментов или возможность размещения на шпинделе станка ряд инструментов;
-несколько механизмов правки, работающих в непрерывном и дис
кретном режимах;
-возможность регулирования частоты вращения шпинделя в широ ком диапазоне без потери мощности привода;
-специальную систему подачи и очистки СОЖ.
Такие технологические возможности обеспечивают машинообраба тывающие центры фирм Blom (серии Profimat), ELB-Schliff (серии Com pact-Master); Magerle (серии MFC), а также отечественные станки мод. ЛШ-220, модернизованные фирмой "Станковед" (г. Москва). Например,
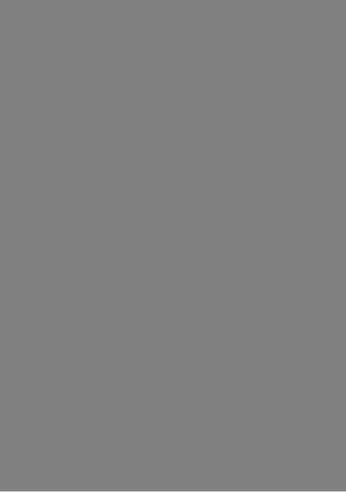