
книги / Технология автоматизированного производства лопаток газотурбинных двигателей
..pdfСтанки этой серии наряду со станками других фирм позволяют вес ти четырехкоординатную обработку неподвижных деталей различных габаритных размеров. Эрозионную обработку на них осуществляют про волочным электродом, протягиваемым через направляющие втулки с высокой скоростью. Перемещение направляющих втулок, удерживаю щих проволоку, выполняют в двух координатах, параллельных друг дру гу. Это позволяет формировать поверхности детали как перпендикулярно к базовой поверхности, так и под углом к ней. Данное оборудование и его система ЧПУ позволяют: останавливать установку в случае обрыва про волоки; автоматически заправлять проволоку; автоматически измерять и корректировать положение проволоки; осуществлять адаптивное управ ление процессом обработки и оптимизацию технологических режимов.
Такие технологические возможности данного вида оборудования, возможность его круглосуточной непрерывной работы в автоматическом режиме способствуют широкому внедрению рассмотренной технологии в производство лопаток турбин ГТД.
2.6. ТЕХНОЛОГИЧЕСКИЕ ОПЕРАЦИИ ОБРАБОТКИ ПЕРФОРАЦИОННЫХ ОТВЕРСТИЙ НА ВХОДНОЙ КРОМКЕ И
БАНДАЖНЫХ ПОЛКАХ ЛОПАТОК ТУРБИН
Жаропрочные сплавы на никелевой основе, используемые для изго товления лопаток турбин ГТД, плохо поддаются резанию. Поэтому про шивка перфорационных отверстий во входной кромке и бандажных пол ках лопаток ГТД представляет серьезную технологическую проблему. На сегодняшний момент общепризнанной и наиболее широко применяемой технологией получения этих отверстий является электроэрозионная об работка.
Схема обработки и используемое для ее реализации оборудование определяются конструкцией лопатки, в частности взаимным расположе нием отверстий и их диаметрами. В том случае, если отверстия во вход ной кромке лопатки находятся на одной линии, параллельны друг другу, то технологическая схема обработки предусматривает их одновременную прошивку.
Такая схема широко используется и реализуется на эрозионных станках мод. 4Г721, 4Е723 сплошными электродами из меди, латуни, вольфрама. Гребенка электродов набирается в специальной державке, установленной на вертикальном суппорте станка; электроды выравнива-
Рис. 2.45. Схема перемещений лопатки при прошивке охлаждающих отверстий на входной кромке:
1 ...3 - положения лопатки относительно электрода при последовательной прошивке отверстий
ются по высоте в линию, эквидистантную линии расположения отверстий на входной кромке, и одновременно прошиваются все отверстия на дета ли, погруженной в ванну с диэлектрической жидкостью [7].
Новое поколение ГТД содержит детали более сложной конструкции (рис. 2.45).
Имеющиеся в них отверстия расположены в несколько рядов, под углом друг к другу и разного диаметра. Все это требует постоянной вза имной ориентации детали и инструмента друг относительно друга в про цессе наладки, т.е. перед началом рабочего цикла. В связи с этим схема обработки перфорационных отверстий претерпела существенные изме нения, а ее реализация потребовала новый тип эрозионных станков для прошивки отверстий (рис. 2.46).
Рис. 2.46. Схема обработки перфорационных отверстий на эрозионном станке с пятью одновременно управляемыми осями
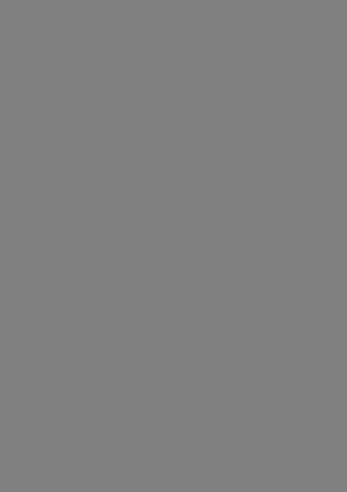
Наличие параллельной оси 2 на кондукторной втулке обусловлено необходимостью поддержания постоянного зазора между торцом втулки и поверхностью детали. Кинематика станка позволяет формировать про жигаемое отверстие путем планетарного движения электрода, что дает высокую геометрическую точность прошиваемых отверстий. Технологи ческие возможности станка позволяют обрабатывать отверстия диамет ром 0,2...2,0 мм; с углами наклона от -45 до + 45°, толщиной стенок до 10 мм; обеспечиваемая при этом шероховатость поверхности составляет по Яа 3,2.
Обработка глубоких отверстий малого диаметра, характеризую щихся соотношением глубины А к диаметру отверстия с! величиной > 10, обеспечивается благодаря струйной электроэрозионной обработке. Суть последней заключается в обработке отверстий полыми электродами, че рез которые прокачивается диэлектрическая жидкость под высоким дав лением.
Электрод, используемый в процессе эрозионной обработки, гаран тирует очень высокую производительность. В качестве рабочей жидкости применяются диэлектрические жидкости на водной основе, что позволяет достичь минимально возможного износа электродов. В качестве электро дов служат трубки диаметром 0,2...2,0 мм с толщиной стенки 0,05...
0,1 мм. Материал электродов - латунь, вольфрам. Глубина измененного слоя при струйной обработке составляет порядка 10 мкм и зависит от ее режимов, а именно от частоты импульсов, подаваемых на электрод. При частоте > 200 Гц глубина измененного слоя равна 2...3 мкм.
После перфорации входной кромки и бандажной полки возникает необходимость удаления из отверстий дефектного слоя.
Кроме того, после удаления стержня из охлажденных лопаток тре буется выполнить плавные переходы в трактовых полостях лопатки, со прягаемых со щелью на выходной кромке. Это тем более обязательно, так как конструкторской документацией на охлажденные лопатки турби ны предусмотрена равномерность истечения воздуха по всей длине кромки.
С целью скругления острых кромок во внутренних трактовых по лостях лопаток в технологический процесс их изготовления вводят опе рации абразивно-жидкостного полирования. Из них наиболее распро странен метод гидроабразивной обработки. Он реализуется путем про качки через внутренние полости лопатки абразивно-жидкостной смеси.
Рис. 2.48. Схема экструдхонингования внутренних полостей лопатки турбины
Смесь прокачивается под давлением порядка 0,6 МПа через тракто вую полость с выходом через щель на выходной кромке. Скорость съема металла определяет давление, под которым подается абразивно жидкостная смесь, и зернистость абразива.
Недостатком данного метода является то, что абразивно-жидкостная смесь выходит на выходной кромке через те каналы, где она встречает наименьшее сопротивление.
Соответственно, эти каналы заполировываются гораздо быстрее, чем другие, поэтому и расход охлаждающей среды через них выше, чем у соседних. Все это снижает эксплуатационные характеристики деталей.
Эти дефекты исключаются при полировании внутренних полостей лопаток методами экструдхонингования (рис. 2.48).
Здесь абразивная масса 1, смешанная с жидкостями на основе мине ральных масел (медиум), продавливается через внутренние полости ло патки 2 под действием гидравлического поршня 5, совершающего воз вратно-поступательные перемещения. Выдавленная масса благодаря спе циальной конструкции поршня 3 и гильзы 4 перетекает при обратном ходе поршня в рабочую камеру и вновь продавливается через внутренние полости лопатки.
Процесс протекает с небольшими скоростями, равномерность рас хода продавливаемой массы по длине выходной кромки контролируется визуально. В случае необходимости отверстие, через которое наблюдает
ся наибольший расход, "глушится" Соответственно, вся продавливаемая масса направляется в более узкие каналы. Это позволяет избирательно проводить процесс полирования. Шероховатость внутренних полостей по Яа в процессе хонингования может быть повышена с 3,2 до 0,2...0,3 мкм в течение 10... 15 мин обработки.
После экструдхонингования проверяется расход охлаждающей сре ды через внутренние полости лопатки. Проверка осуществляется на спе циальных установках под постоянным давлением. В ходе операции кон тролируется общий расход охлаждающей среды (воды) через внутрен нюю полость лопатки. Расход измеряется количеством прокачанной жид кости в единицу времени. Одновременно фиксируется равномерность истечения жидкости через выходную кромку лопатки. Этот параметр контролируется на соответствие установленному конструктором эталону. В случае несоответствия задаваемым параметрам лопатка подвергается повторному хонингованию. Если она признается годной, то на нее нано сят соответствующее покрытие.
2.7.СПЕЦИАЛЬНЫЕ И КОНТРОЛЬНЫЕ ОПЕРАЦИИ
2.7.1.Технологические операции нанесения покрытий
Технологический процесс изготовления лопаток турбины заверша ется осуществлением специальных операций, связанных с нанесением на рабочие поверхности лопаток (прежде всего на проточную часть лопат ки) жаропрочных покрытий.
В целях дальнейшего улучшения рабочих характеристик газовых турбин и, в частности, повышения надежности лопаток, которые работа ют при высоких (1000... 1300 °С) температурах, подвергаются коррози онному и эрозионному разрушению и испытывают знакопеременные на грузки, в настоящее время применяют теплозащитные покрытия, состоя щие из жаростойкого металлического подслоя системы Ме-Сг-А1-У и термобарьерного керамического покрытия гЮг-УгОз-
Их применение обусловливается тем, что металлический подслой защищает материал лопатки от интенсивного окисления при воздействии высоких температур, а керамический слой обладает коррозионной стой костью и противостоит эрозионному воздействию частиц пыли, кокса и окалины, содержащихся в газовом потоке. Такие покрытия обеспечивают повышение долговечности лопаток ГТД в 2,5...3 раза по сравнению с лопатками без покрытий.
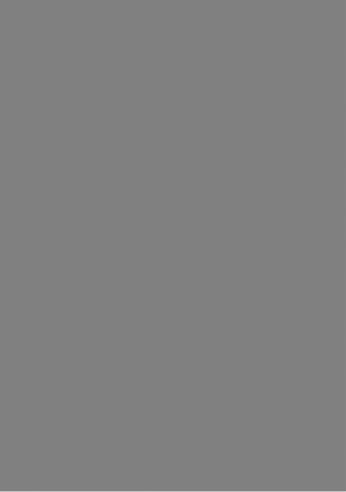
Поворотный стол, на котором располагается деталь, может переме щаться как в непрерывном режиме, так и дискретно. Параметрами вра щения управляет контроллер робота-манипулятора. Установка оснащена плазмотроном мод. ¥4 мощностью 55 кВт. Плазмотрон охлаждается дис тиллированной водой, циркулирующей в замкнутом контуре охлаждения. Заданная температура воды поддерживается специальным блоком охла ждения. Дозатор порошка данной установки имеет две линии подачи по рошка, которые могут работать раздельно и совместно. Установка имеет четыре линии плазмообразующих газов, в качестве которых можно ис пользовать аргон, водород, азот, гелий.
Комплекс плазменного напыления оснащен системой программного управления режимами напыления и роботизированным манипулятором перемещения плазмотрона. Система А-3000Б может работать в ручном и автоматическом режимах. В автоматическом режиме параметры напыле ния выбираются из памяти компьютера, которая позволяет хранить до 100 параметров процесса. Благодаря этому каждую последующую деталь в партии и каждую следующую партию деталей можно обрабатывать на строго определенных режимах с возможностью вывода параметров про цесса напыления на принтер для контроля.
Перед нанесением покрытия лопатки должны проходить струйно-абразивную обработку электрокорундом. В НПО "Сатурн" для этой цели используют установку для пескоструйной обработки мод. КБА У-700 Н800 швейцарской фирмы Би1гег Ме1со (рис. 2.50).
Установка позволяет осуществлять автоматическую обработку как трехмерных, так и плоских деталей. Габаритные размеры камеры 1100 х х 1100 х 600 мм; масса детали до 100 кг. После обдувки абразивом дан ная установка дает возможность удалить его остатки дополнительным обдувом сжатым воздухом. При этом программируемый контрольный блок Б табс Б7 со всеми параметрами процесса сохраняет в памяти до 50 программ обдувки различных деталей. Установка оснащена двумя писто летами N10 100 с соплами из карбида бора, коллектором пыли N10 2000 для удаления мелкой фракции пескоструйного материала. В установке могут использоваться все промышленные пескоструйные материалы. Применение данной установки позволяет подготавливать под напыление тонкостенные детали (толщиной 0,8... 1,0 мм) без коробления, что ис ключает их последующую правку [1].
После обдувки в установке плазменного напыления на детали нано сят покрытие с использованием порошков системы Со-Сг-А1-Б1-У и гЮг + У20з, например производства НПФ "Материалы-К" (г. Тула). Тол-
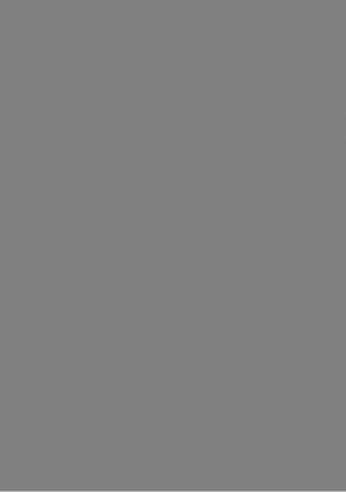
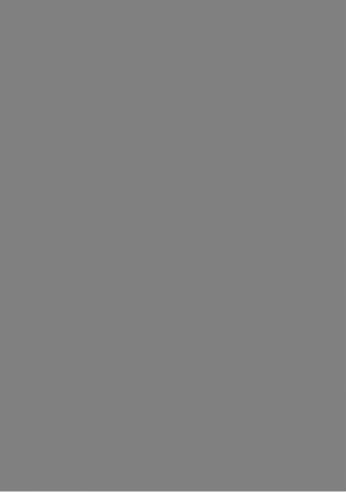