
книги / Методы и инструменты поиска инновационных решений
..pdf
только в том, что положительный эксперимент приносит прибыль на инвестированный капитал.
90 % всех промышленных экспериментов являются однофакторными, двухуровневыми.
Результатом является математическая модель, позволяющая результативно и эффективно исследовать отношения между множеством входных переменных и выходами.
4.29. «КАНБАН»
Система «Канбан» (Canban, тянущая система, pullsystem) –
наиболее распространенная разновидность системы «точно в срок», обеспечивающая организацию непрерывного материального потока при отсутствии запасов: производственные запасы подаются небольшими партиями непосредственно в нужные точки производственного процесса, минуя склад, а готовая продукция сразу отгружается покупателям. Порядок управления производством продукции – обратный: от i-й стадии на (i–1)-й.
В настоящее время наметилась четкая тенденция к росту затрат на хранение запасов, что и стало причиной разработки систем «мгновенного» управления запасами, к которым относится рассматриваемая система Canban, разработанная корпорацией Toyota Motors – одна из первых попыток практического внедрения системы «точно в срок» [19].
Сущность системы Canban состоит в том, что все производственные подразделения предприятия снабжаются материальными ресурсами только в том количестве и к такому сроку, которые необходимы для выполнения заказа. Заказ на готовую продукцию подается на последнюю стадию производственного процесса, где производится расчет требуемого объема незавершенного производства, которое должно поступить с предпоследней стадии. Аналогично предпоследней стадии идет запрос на предыдущий этап производства на определенное количество полуфабрикатов,
281
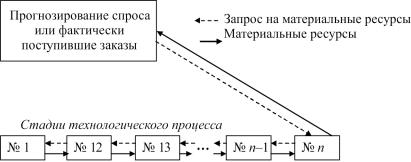
т.е. размеры производства на данном участке определяются потребностями следующего производственного участка.
Таким образом, между каждыми двумя соседними стадиями производственного процесса существует двойная связь (рис. 4.26):
сi-й стадии на (i–1)-ю запрашивается («вытягиваются») требуемое количество незавершенного производства;
с(i–1)-й стадии на i-ю отправляются материальные ресурсы в требуемом количестве.
Рис. 4.26. Схема передачи информации в системе
Средством передачи информации в системе Canban являются специальные карточки («canban» в переводе с японского языка – карточка). Применяют два вида карточек. Карточки производственного заказа, в которых указывается количество деталей, которое должно быть изготовлено на предшествующей стадии производства. Карточки производственного заказа отправляются с i-й стадии производства на (i–1)-й этап и являются основанием для формирования производственной программы (i–1)-го участка. Карточки отбора, в которых указывается количество материальных ресурсов (компонентов, деталей, полуфабрикатов), которое должно быть взято на предшествующем участке обработки (сборки). Карточки отбора показывают количество материальных ресурсов, фактически полученных i-м производственным участком от (i–1)-го. Таким
282
образом, карточки могут циркулировать не только внутри предприятия, использующего систему Canban, но и между ним и его филиалами, а также между сотрудничающими корпорациями.
Предприятия, использующие систему Canban получают производственные ресурсы ежедневно или даже несколько раз в течение дня. Таким образом, запасы предприятия могут полностью обновляться 100–300 раз в год или даже чаще, тогда как на предприятии, использующем системы MRP или MAP – только 10–20 раз в год. Например, в корпорации Toyota Motors на один из производственных участков в 1976 г. ресурсы поставлялись трижды в день, а в 1983 г. – уже каждые несколько минут.
Стремление к снижению запасов становится, кроме того, методом выявления и решения производственных проблем. Накопление запасов и завышенные объемы производства позволяют скрывать частые поломки и остановки оборудования, производственный брак. Поскольку в условиях минимизации запасов производство может быть остановлено из-за брака на предыдущей стадии технологического процесса, основным требованием системы Canban, кроме требования «ноль запасов», становится требование «ноль дефектов». Систему Canban практически невозможно реализовать без одновременного внедрения комплексной системы управления качеством.
Важные элементы системы Canban:
♦информационная система, включающая не только карточки, но и производственные, транспортные и снабженческие графики, технологические карты;
♦система регулирования потребности и профессиональной ротации кадров;
♦система всеобщего (TQM) и выборочного (Дзидока) контроля качества продукции;
♦система выравнивания производства.
Основные преимущества системы Canban:
♦ короткий производственный цикл, высокая оборачиваемость активов, в том числе запасов;
283
♦отсутствуют или чрезвычайно низки издержки хранения производственных и товарных запасов;
♦высокое качество продукции на всех стадиях производственного процесса.
4.30. «ХАНСЭЙ»
«Хансэй» – один из инструментов совершенствования производства. Это один из элементов производственной системы Toyota (TPS), согласно которому необходимо признавать собственные ошибки и планировать улучшения. Иначе говоря, это процесс самоанализа, который позволяет постоянно совершенствовать себя, становиться лучше [21].
Цель метода – совершенствование деятельности организации путем выявления упущений, открытого признания собственных ошибок и планирования путей их предупреждения в процессе дальнейшей работы, искренне веря, что вы никогда не повторите свою ошибку. Результат: повышение эффективности производства и обеспечение конкурентных преимуществ на мировом рынке.
План действий: благодаря принципу гэнти гэмбуцу сотрудники организации могут, рассмотрев ситуацию, увидеть недостатки производственного процесса и применить хансэй (размышление) (рис. 4.27).
При этом сотрудники:
1)должны признать, что существует разрыв между ожиданиями и достижениями, и быть открытыми для обратной связи;
2)добровольно взять на себя личную ответственность и испытывать глубокое сожаление из-за упущений в работе;
3)совместно с коллективом разработать конкретный план действий по предупреждению повторения ошибок в будущем.
Достоинства. «Хансэй» – это ориентация на людей. Этот подход позволяет немедленно учитывать и исправлять свои ошибки и упущения в регулярно повторяющихся и непродолжительных циклах разработки продукции.
284
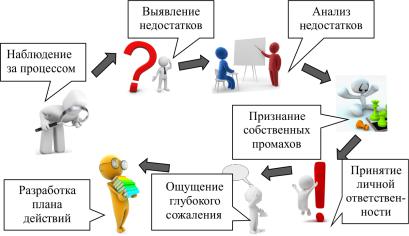
Рис. 4.27. Схема процесса хансэй
Недостатки. При использовании этого метода, уделяя основное внимание недостаткам и упущениям, обычно не обращают внимания на то, что сделано хорошо. Руководству необходимо также подчеркивать и достигнутые успехи сотрудников.
4.31. РЕИНЖИНИРИНГ БИЗНЕС-ПРОЦЕССОВ
Реинжиниринг бизнес-процессов – это фундаментальная ре-
конструкция бизнес-процессов организации с целью улучшения таких важных критериев производительности, как стоимость, качество услуги и скорость. Понятие «Реинжиниринг бизнес-процессов» введено в научный оборот М. Хаммером и Д. Чампи в 1990 г. Концепция предполагает революционные перемены в основных бизнес-про- цессах организации для качественного скачка в организационном развитии и включает несколько этапов [101].
Цель подхода – повышение конкурентоспособности компании за счет внутренней перестройки всех бизнес-процессов.
285
Технология подхода
Первый этап заключается в разработке видения «новой» организации, которая способна достичь поставленных стратегических целей. Этап включает проведение анализа внешней среды (клиентов, конкурентов, отрасли), на основе которого формируются цели и стратегия развития организации, разрабатываются сценарии возможного развития событий, выявляются риски и ключевые факторы успеха в достижении целей.
На втором этапе проводится анализ состояния бизнеспроцессов «как есть» и описание функционирования организации. Результатом проведения работ на данном этапе является модель существующей организации.
На третьем этапе происходит проектирование бизнес-про- цессов организации «как должно быть». Суть заключается в наложении видения «новой» организации на модель существующего бизнеса, в результатечегорождаетсямодельновойорганизации.
На четвертом этапе внедряются новые процессы, выполняются тестирование и доработка новой схемы функционирования организации. Основной сложностью последнего этапа является переход от старых процессов к новым.
По данным различных источников, правильное применение реинжиниринга бизнес-процессов приводит к значительному снижению затрат, сокращению длительности производственного цикла, числа ошибок, увеличению показателей деятельности компании. Однако применять столь радикальный подход следует с особой осторожностью. По различным оценкам, порядка 50–70 % компаний, которые решились на кардинальные перемены, не добились значимых результатов или завершили свою деятельность.
4.32. ФУНДАМЕНТАЛЬНЫЙ МЕТОД МЭТЧЕТТА
Фундаментальный метод Мэтчетта – это системный под-
ход к анализу и решению проблем, основанный на сбалансированном сочетании рациональных и иррациональных приемов и графической интерпретации мышления [28].
286
Цель метода – научить человека понимать и контролировать свой образ мыслей и более точно соотносить с задачами проектирования с целью выявления существенных характеристик изучаемого объекта и устранения ненужных элементов. Метод направлен как на исследование и преобразование собственно объекта, так и на совершенствование мыслительной деятельности проектанта. В результате возможно создание принципиально новых объектов.
В частной школе Мэтчетта (Великобритания) проходят подготовку специалисты ведущих компаний мира самого различного спектра профессиональной деятельности. Как правило, после прохождения курса обучения результативность специалистов резко возрастает. Технология обучения является закрытой по двум причинам:
а) коммерческая тайна; б) в процессе обучения используются психологические мето-
ды воздействия, что небезопасно для здоровья человека при их неправильном применении.
Специалистов обучают освоению следующих режимов мышления:
–мышление в параллельных плоскостях;
–мышление «образами»;
–мышление в основных элементах.
Содержание режима мышления следует из его названия. Достоинства метода: резко повышается мастерство проек-
танта за счет сознательного управления самим процессом мышления, учитывающего индивидуальные психологические особенности человека.
Недостатки: большая психологическая нагрузка; отсутствие четких правил по выявлению и оценке взаимосвязей между элементами; отсутствие критериев оценки выполнения операций.
4.33. ПРИЧИННО-СЛЕДСТВЕННАЯ ДИАГРАММА
Причинно-следственная диаграмма – это инструмент, обес-
печивающий системный подход к определению фактических причин возникающих проблем [49].
287
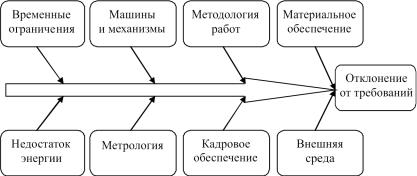
Цель метода – изучить, отобразить и обеспечить технологию поиска истинных причин рассматриваемой проблемы с целью эффективного ее разрешения
Причинно-следственная диаграмма – это ключ к решению возникающих проблем. Диаграмма позволяет в простой и доступной форме систематизировать все потенциальные причины рассматриваемых проблем, выделить из них самые существенные и провести поуровневый поиск первопричины (рис. 4.28).
Рис. 4.28. Диаграмма причинно-следственных связей
В соответствии с принципом Парето среди множества потенциальных причин, порождающих проблемы, лишь две-три являются наиболее значимыми. Их поиск и должен быть организован. Для этого осуществляется: сбор и систематизация всех причин, прямо или косвенно влияющих на исследуемую проблему; группировка этих причин по причинно-следственным блокам; ранжирование их внутри каждого блока; анализ получившейся картины.
Достоинства метода: диаграмма позволяет стимулировать творческое мышление; выявить взаимосвязь между причинами и сопоставить их относительную важность.
Недостатки: не рассматривается логическая проверка цепочки причин, ведущих к первопричине, т.е. отсутствуют правила проверки в обратном направлении – от первопричины к результатам.
288
ГЛАВА 5. ЭКОНОМИЧЕСКИЕ ИНСТРУМЕНТЫ МЕНЕДЖМЕНТА
В условиях рынка главная цель любой компании – делать деньги. Выделяют две группы критериев оценки эффективности предприятия: финансовые критерии и операционные критерии. Финансовые критерии – это чистая прибыль, прибыль на инвестированный капитал и поток денежных средств. Операционные критерии – это выручка, товарно-материальные запасы и операционные расходы. В рамках данной главы собраны методы, так или иначе связанные с экономическим анализом эффективности деятельности предприятия. Такие категории, как «денежная рентабельность инвестиций», «свободный денежный поток», «экономическая добавленная стоимость», рассмотренные ниже, в настоящее время широко используются на практике.
5.1. ДЕНЕЖНАЯ РЕНТАБЕЛЬНОСТЬ ИНВЕСТИЦИЙ (CFRO)
Денежная рентабельность инвестиций (CFRO) представ-
ляет собой экономический показатель эффективности компании и, по сути, попытки отразить средние основные уровни рентабельности инвестиционных проектов компании [103].
Технология применения метода
Расчет CFRO состоит из пяти шагов:
1.Оценка среднего экономического срока полезного использования активов компании.
2.Расчет ежегодных валовых денежных потоков, скорректированных на индекс инфляции, поступление которых ожидается
втечение срока полезного использования активов компании.
3.Расчет совокупных валовых инвестиций компании, скорректированных на индекс инфляции, а для многопериодного под-
289
хода – распределение валовых инвестиций между амортизируемыми и неамортизируемыми активами.
4.Прогнозирование конечной стоимости компании, скорректированной на индекс инфляции, равной реализации неамортизированных активов (земли) и рабочего капитала.
5.Определение CFRO с помощью или многопериодного метода (RR), или однопериодного метода.
Затем сравнивают CFRO с реальной, в противоположность номинальной, стоимостью капитала или с уровнями рентабельности по отрасли или подобных компаний.
5.2. МЕТОД ПОЭЛЕМЕНТНОГО ЭКОНОМИЧЕСКОГО АНАЛИЗА
Метод поэлементной обработки объекта (метод системно-
го и экономического анализа и поэлементной отработки конст-
руктивных решений). Автор Ю.М. Соболев (СССР), 1948 г. Это метод решения задач по поиску конструкторских решений, разработке и совершенствованию технологических процессов изготовления изделий. Суть метода заключается в системном техникоэкономическом анализе и поэлементной отработке конструкции каждого узла, каждой детали [7].
Цель метода – выявить экономически необоснованные решения, принятые разработчиком. Достичь максимально эффективного функционирования объекта при минимальных затратах. Результатом применения метода являются выявление и ликвидация экономически необоснованных элементов конструкции, снижение затрат и повышение качества изделий, улучшение технологии изготовления деталей и повышение коэффициента использования оборудования.
План действий
1.Анализируемый объект делится на отдельные элементы.
2.Определяются функции, выполняемые этими элементами.
3.Элементы делятся на две группы: основные и вспомогательные.
290