
Курс лекций Трубы и арматура ФГОС3
.pdf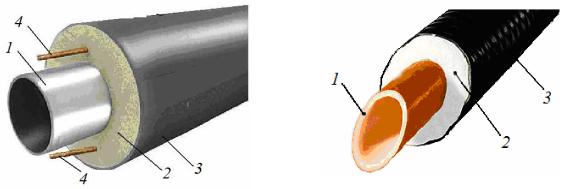
Труба металлопластиковая применяется в любых инженерных системах (отопление, горячее и холодное водоснабжение и. т. д.). Системы могут быть как комбинированные (с применением труб из разного материала), так и только из металлопластика.
Металлопластиковая труба соединяется с помощью фитингов. Фитинги выпускаются двух видов: обжимные и пресс-фитинги. Монтаж производится с помощью специального инструмента.
Преимущества металлопластиковых труб:
1.Термостойкость, позволяющая применять трубы для монтажа систем горячего водоснабжения отопления и, в том числе, даже в котельных;
2.Высокая прочность.
3.Тепловое расширение меньше, чем у других типов труб.
4.Теплопроводность 0,43 Вт/м К ниже, чем у стальных труб.
5.Газонепроницаемость и высокая стойкость к химическим воздействиям.
6.Устойчивость к образованию накипи и стиранию рабочих поверхностей.
7.Полное отсутствие электропроводности.
8.Высокая пластичность, что позволяет изготавливать колена с очень маленьким радиусом изгиба, при этом сечение в месте изгиба остается постоянным.
9.Низкая шероховатость внутренней поверхности –более чем в 20 раз ниже, чем у стальных.
Предварительно изолированные трубопроводы
Предварительно изолированные трубопроводы используются в тепловых сетях как при бесканальной подземной прокладке, так и при надземной прокладке. В практике строительства тепловых сетей применяются трубопроводы с пенополиуретановой теплоизоляцией типа «труба в трубе» (трубы ППУ). Трубопровод состоит из трубы, пенополиуретановой теплоизоляции и защитной оболочки (рис. 3). Применяются стальные или полимерные (для ГВС) трубы. Между трубой и оболочкой устанавливаются центрирующие опоры из полиэтилена.
Рис.32. Предварительно изолированные трубопроводы:
1 – труба, 2 - тепловая изоляция, 3 – полиэтиленовая оболочка; 4 – сигнальный провод СОДК
Предварительно изолированные трубопроводы обеспечивают следующие преимущества перед существующими конструкциями:
• повышение долговечности (ресурс трубопроводов) в 2-3 раза;
21
•снижение тепловых потерь в 2-3 раза;
•снижение эксплуатационных расходов в 9 раза (удельная повреждаемость снижается в 10 раз);
•снижение капитальных затрат в строительстве в 1,3 раза;
•наличие системы оперативного дистанционного контроля над увлажнением теплоизоляции.
Предварительно изолированные трубы успешно используются для строительства:
•сетей теплоснабжения;
•систем горячего водоснабжения;
•технологических трубопроводов;
•нефтепроводов.
Тепловую изоляцию наносят на всю длину стальных труб и фасонных изделий за исключением концевых участков, равных 150 мм при диаметре труб до 219 мм, и 210 мм при диаметре 273 мм и более. Места стыков теплоизолируются на месте строительства, после сварки и испытания трубопровода. Изолирование участков труб со сварными стыками может производиться по одному из методов: установкой изолирующих скорлуп из жесткого пенополиуретана с нанесением гидроизолирующего материала; установкой полиэтиленовых муфт с заливкой в полость муфты пенополиуретана.
Защитные оболочки изготавливаются в виде тонкостенных труб из полиэтилена высокой плотности. Они предназначены для трубопроводов непосредственно расположенных в земле, обеспечивая их водонепроницаемость и механическую защиту.
Для трубопроводов, расположенных над поверхностью земли, применяют защитную оболочку из оцинкованной стали с толщиной цинкового покрытия не менее 70 мкм.
Трубопроводы из стальных труб оснащаются системой оперативного дистанционного контроля намокания изоляции, состоящей из двух медных проводов (один из которых электроизолирован, а второй без изоляции) и электронного блока сигнализации. При намокании изоляции вследствие коррозии трубы или нарушения целостности защитной оболочки, изменяется омическое сопротивление системы, что фиксируется блоком сигнализации.
Срок службы тепловой изоляции труб и фасонных изделий должен составлять не менее 25 лет. Пенополиуретан не оказывает вредного влияния на окружающую среду и обеспечивает высококачественную эксплуатацию изоляции при температурах до 130 °С.
22
Лекция 4 СПОСОБЫ И ТИПЫ СОЕДИНЕНИЙ ТРУБОПРОВОДОВ
Прямолинейные участки труб соединяются между собой, с арматурой, технологическим оборудованием, контрольно-измерительными приборами и средствами автоматики. Соединения бывают:
•неразъемные – сварка, пайка, склеивание;
•разъемные – фланцевые, муфтовые, штуцерные, дюритовые и др. Неразъемные соединения используют на труднодоступных при ремонте
участках трубопровода, или на участках, не требующих ремонта при нормальной эксплуатации системы. Для металлических труб основным неразъемным соединением следует считать сварное соединение, а для пластмассовых труб – сварное и клееное. Неразъемные соединения снижают вес системы и сокращают затраты на изготовление. К недостаткам таких соединений следует отнести трудность выполнения сварки и склеивания при монтаже, трудность ремонта и контроля качества соединений, а также то, что даже у хорошо сваренного стыкового шва коэффициент прочности составляет 0,6…0,7.
Разъемные соединения применяют в местах, где при эксплуатации системы и ее ремонте производят монтажно-демонтажные работы, так как эти соединения обеспечивают простоту разборки и сборки составляющих трубопровод элементов.
Сварные соединения стальных труб.
Процесс сварки основан на заполнении сварочного шва между свариваемыми трубами или их деталями металлом расплавляемого электрода или сварочной проволоки. В связи с тем, что расплавление металла при сварке происходит только в самом шве, а весь остальной объем свариваемых изделий остается в твердом состоянии, температурный режим свариваемых деталей по их длине (или объему) оказывается крайне неравномерным.
|
Наиболее распространенными при монтаже и ремонте трубопроводов яв- |
ляются следующие способы сварки: |
|
• |
ручная электродуговая сварка (плавящимся металлическим электродом); |
• |
автоматическая сварка под слоем флюса; |
• |
полуавтоматическая сварка в среде углекислого газа; |
• |
ручная аргонодуговая сварка; |
• |
автоматическая и полуавтоматическая аргонодуговая сварка; |
• |
газовая сварка. |
|
Электродуговая ручная сварка труб наиболее распространенный вид сварки. |
Число слоев и диаметры электродов выбирают в зависимости от толщины метала. Сварка труб с толщиной стенок до 8 мм производится в один слой, а для труб с толщиной стенок от 8 мм и выше – в два-три слоя. Поверхность каждого слоя, кроме последнего, должна быть вогнутой и зачищенной от шлака. Последний слой должен иметь выпуклую равномерную поверхность. По окончании сварки сварщик обязан выбить около стыка (на расстоянии 30…50 мм у каждого сваренного стыка) присвоенное ему клеймо.
23
Автоматическая сварка под слоем флюса представляет собой процесс, при котором сварочная дуга горит, окруженная жидкой оболочкой расплавленного шлака, изолирующего расплавленный металл от влияния газов атмосферы. Под воздействием высокой температуры дуги происходит плавление как присадочного, так и основного металла трубы. При включении электрического тока сварочной дуги в процессе охлаждения они разделяются на шлак, который всплывает и кристаллизуется, образуя стекловидную шлаковую корку, и на металл, который, кристаллизуясь, образует сварочный шов. Автоматическая сварка ведется при непрерывном вращении трубы, над которой установлена неподвижно сварочная головка. Автоматическую сварку ведут в заводских условиях на автосварочных установках.
Сварка труб в среде углекислого газа (газоэлектрическая) – способ, при ко-
тором электрическая дуга горит в струе углекислого газа и защищает расплавленную ванну металла от воздействия кислорода и азота воздуха.
Ручная аргонодуговая сварка является дуговой сваркой, в которой защита зоны сварки производится с помощью инертного газа аргона. Ручная аргонодуговая сварка производиться неплавящимся вольфрамовым электродом. К сварочной горелке подаются сварочный ток и инертный газ, а вторая фаза сварочного тока «закорочивается» на трубопровод. Между электродом и свариваемой деталью горит дуга, проволока-присадка вручную подаётся в зону сварочной дуги.
Газовая сварка относится к сварке плавлением. Источником нагрева при газовой сварке служит пламя сварочной горелки, получаемое сжиганием горючего газа (ацетилена) в смеси с технически чистым кислородом. Газовую ручную сварку применяют для соединения тонкостенных (до 3,5 мм) стальных труб с условным проходом до 80 мм, где не может быть использована электродуговая сварка. Ограниченность применения газовой сварки объясняется тем, что механические свойства сварного шва при газовой сварке ниже, чем при электродуговой. При газовой сварке наплавленный металл сварного шва в исходном состоянии имеет меньшее удлинение и меньшую ударную вязкость, чем основной металл. Технология газовой сварки заключается в том, что кромки свариваемых деталей нагреваются газокислородным пламенем и расплавляются, зазор между ними заполняется металлом присадочной проволоки, вводимой в зону нагрева.
Сварные соединения (рис. 1) могут быть различных видов: стыковые, раструбные, в некоторых случаях угловые (приварка штуцеров, плоских фланцев). В зависимости от толщин стенок свариваемых труб и элементов трубопроводов, а также условного давления среды применяются различные формы разделки их кромок, которые определяются отраслевыми стандартами. В некоторых случаях сварка производится при помощи подкладных колец, вводимых внутрь трубы и предназначенных для предотвращения образования грата (застывших капель и нитей металла) внутри трубы.
Подкладные кольца привариваются к трубе и остаются в ней. В некоторых случаях применяются так называемые инвентарные кольца, изготовляемые из непривариваемых к стали материалов (медные и др.), которые после выполнения сварного шва удаляются.
24
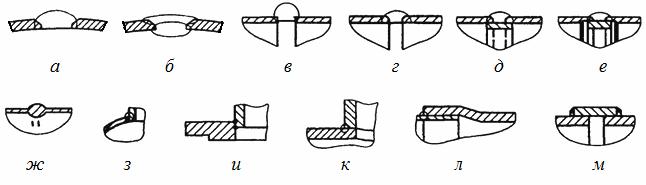
Рис. 1. Виды неразъемных сварных соединений труб и деталей трубопроводов:
а – стыковое продольное с односторонним швом; б – стыковое продольное с двусторонним швом; в – стыковое поперечное с односторонним швом без скоса кромок; г – стыковое поперечное с односторонним швом со скосом кромок; д – стыковое поперечное с подкладным кольцом без расточки; е – стыковое поперечное с подкладным кольцом с внутренней расточкой; ж – стыковое контактное; з – угловое одностороннее без скоса кроток; и – угловое двустороннее без скоса кромок; к – угловое од-
ностороннее со скосом кромок; л – раструбное (в стакан); м – раструбное с муфтой
Контроль качества сварных швов осуществляет строительно-монтажная организация в течение всего периода сварочных работ. Проверке подлежат: качество применяемых материалов, техническое состояние сварочного оборудования и инструмента; квалификация сварщиков; сварные швы. В сварных соединениях могут наблюдаться следующие дефекты: несплавление наплавленного и основного металлов, непровары в корне шва, раковины, шлаковые включения, трещины, подрезы и прожоги, несоответствие шва проектным требованиям.
Фланцевые соединения.
Фланцевые соединения (рис. 2, а) состоят из двух фланцев 3 и 4, прокладки 5 или уплотнительного кольца, соединительных болтов 2 (или шпилек) с гайками. Фланцы – круглые или прямоугольные диски, которые привариваются или свободно сидят на отбортованной трубе или приваренном к ней бурте. Герметичность соединения достигается за счет прокладок в виде колец из упругого материала (резины, паронита, винипласта, полиэтилена, меди или других материалов в зависимости от параметров проводимой среды), установленных между торцовыми поверхностями фланцев. Фланцы используют для соединений труб как одного, так и разных проходов, а также в качестве заглушек, временно или постоянно закрывающих трубопроводы. Фланцевые соединения облегчают разборку и сборку трубопроводов.
Конструкция фланцев зависит от рабочих параметров и физико-химических свойств транспортируемого вещества, материала труб и других факторов.
Недостатки фланцевых соединений: большой расход металла, высокая стоимость изготовления, а также меньшая по сравнению с неразъемными сварными соединениями надежность в эксплуатации. При частом изменении температуры или давления транспортируемого вещества возможно ослабление соединения и как следствие, возникновение утечек, поэтому приходится периодически подтягивать стяжные болты и шпильки, чтобы предотвратить нарушение герметичности соединения.
25
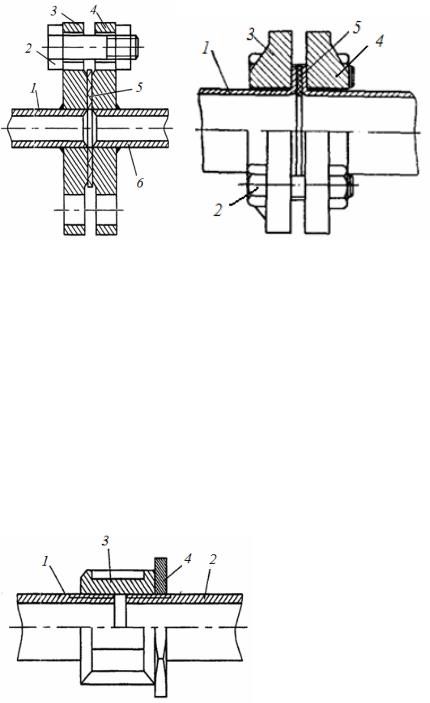
Рис. 2. Фланцевое соединения трубопроводов:
|
|
а – круглые фланцы; б – на |
|
|
отбортованной трубе; |
|
|
1, 6 – трубы; 2 – болт с гай- |
|
|
кой; 3, 4 – фланцы; 5 – про- |
а |
б |
кладка |
|
Муфтовое резьбовое соединение.
Муфтовое резьбовое соединение (рис. 3), применяемое для металлических водогазопроводных труб, служит для соединения труб между собой, с арматурой и фасонными частями в трубопроводах с условным проходом Dу ≤ 80 при давлениях до Ру ≤ 1,0 МПа. Муфтовые соединения могут быть использованы и для пластмассовых трубопроводов, кроме труб из винипласта, поскольку ударная прочность этих труб резко падает при надрезах на их поверхностях.
Для более плотного соединения муфту монтируют с подмоткой из пропитанной суриком на натуральной олифе льняной пряди или фторопластовой ленты (ленты ФУМ). Для более плотной посадки муфты на трубе в соединении имеется контргайка, которая одновременно служит стопором муфты.
Рис. 3. Муфтовое соединения трубопрово-
дов: 1, 2 – трубы; 3 – муфта; 4 – контргайка
Штуцерные соединения.
Штуцерные соединения (рис. 4) используют в трубопроводах с условными проходами Dу= 3…32 мм, работающих при различных давлениях.
Детали штуцерного соединения изготовляют из стали, бронзы и латуни. В этих соединениях при высоких давлениях сред применяют прокладки из меди; в водяных, масляных и паровых трубопроводах в качестве прокладок используют паронит, в трубопроводах из легких сплавов – листовой полиэтилен и винипласт.
Детали этих соединений такие, как ниппели и штуцеры могут привариваться или припаиваться к трубам (рис. 4, а и рис. 4, б), либо монтироваться без при-
26
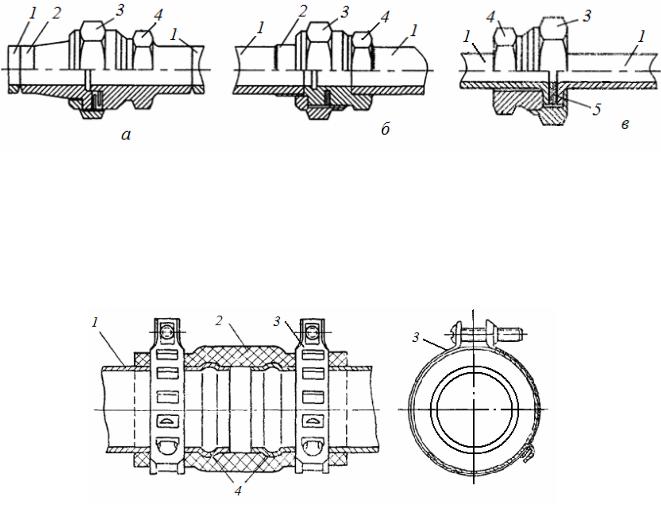
варки, например, на отбортованных трубах (рис. 4, в). Кроме того, ниппели при помощи резьбы ввертывают в бобышку, приваренную к трубе.
Штуцерные соединения обеспечивают плотность путевого соединения, обладают малым весом и технологичны. Их используют для монтажа импульсных трубок систем автоматизации, а также для крепления гибких шлангов.
Рис. 4. Штуцерные соединения трубопроводов:
а – приварные встык, б – приварные в раструб, в – на отбортованных трубах; 1 – соединяемые трубы, 2 – ниппель, 3 – накидная гайка, 4 – штуцер, 5 – прокладка
Дюритовые соединения.
Дюритовые соединения применяют в трубопроводах с условными проходами Dу =10…80 мм при давлениях Ру≤10 (рис. 5).
Рис. 5. Дюритовое соединение:
1 – труба; 2 – муфта дюритовая; 3 – хомутик; 4 – «зиги»
Соединяющим элементом между трубами служит отрезок шланга, состоящего из нескольких слоев прорезиненной ткани. Шланг крепят к трубам и арматуре хомутами. Плотность соединения трубопроводов, не подверженных давлению, обеспечивается обжатием шланга хомутом на гладкой поверхности трубы без «зигов» и буртов.
Дюритовые соединения легко монтируются, они эластичны и способствуют уменьшению вибрации трубопроводов. Однако прорезиненные шланги делают соединение недолговечным, так как резина растрескивается со временем и разрушается от воздействия нефтепродуктов.
Соединение напорных асбоцементных труб
Для соединения асбестовых напорных труб применяют напорные самоуплотняющиеся асбестовые муфты САМ с проточенными пазами и резиновыми
27
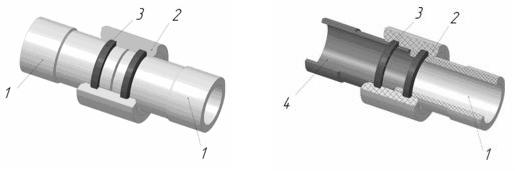
кольцами (рис. 6) . При монтаже трубопроводов горячего водоснабжения и теплоснабжения используют специальные теплостойкие резиновые кольца. Самоуплотнение достигается благодаря давлению воды в трубопроводе. Давление передается на стенки цилиндрических углублений в резиновых кольцах и плотно прижимает их к уплотнительным поверхностям труб и муфт.
Рис. 6. Соединение напорных асбоцементных труб:
1 – асбестовая напорная труба; 2 – асбестовая напорная муфта; 3 – кольцо резиновое типа САМ; 4 – металлическая труба
Соединительную асбестовую муфту и резиновыми кольцами, работающими по принципу самоуплотнения, размещают на стыкуемых трубах, оставляя монтажный зазор между стыками труб 10…12 мм. Правильное положение муфты после установки ее на место определяют по меткам, которые делают на расстоянии равном (0,5l–5) мм (где l – длина муфты) от края трубы. Муфту надвигают на конец уложенной трубы на длину несколько более длины самой муфты, затем укладывают вторую трубу и при помощи шаблона отмечают карандашом рабочее положение муфты. После надевания муфты трубы центрируют. Натяжение муфты на стык осуществляют винтовыми домкратами, которые закрепляют на присоединяемой трубе.
Муфта САМ может использоваться и для соединения асбоцементой напорной трубы со стальной или чугунной трубой. Для соединения конец металлической трубы протачивают до диаметра, равного диаметру асбоцементой трубы или к металлической трубе приваривают патрубок, наружный диаметр которого равен диаметру стыкуемой асбоцементой трубы.
Сварка полимерных труб
Существует три способа сварки полимерных труб:
•стыковая сварка;
•раструбная или муфтовая сварка;
•электрофузионная или электромуфтовая сварка.
Свариваемые элементы трубопроводов должны быть совместимы в химическом и физическом отношении. Необходимо также, чтобы трубы имели одинаковые толщину стенки и диаметр.
Стыковая сварка (рис. 7) рекомендуется для соединения труб наружным диаметром более 50 мм и толщиной стенки более 4 мм.
28
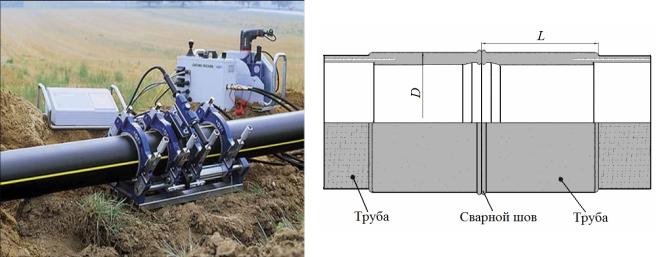
Рис. 7. Стыковая сварка полимерных труб
Процесс стыковой сварки делится на пять этапов:
•Торцевание трубы – выравнивание торца трубы для максимально плотного соприкосновения свариваемых поверхностей трубы.
•Нагрев трубы под давлением для образования буртика (валика).
•Нагрев трубы без давления. На этом этапе происходит глубокое прогревание свариваемого пластика.
•Сварка трубы под давлением с образованием стыкового валика. При этом происходит образование сварочного валика и молекулярных связей, обеспечивающих однородность основной массы и сварного шва.
•Остывание трубы с сохранением позиционирования трубы.
Стыковая сварка используется при монтаже водо- и газопроводов из полиэтилена, а также сварки ненапорных труб из полиэтилена или полипропилена. При этом не требуется высокое качество стыка, соответствующее требованиям для напорного трубопровода.
Электрофузионная или электромуфтовая сварка используются для соеди-
нения полиэтиленовых и полипропиленовых труб. При электромуфтовой сварке разогрев труб обеспечивается за счёт применения полиэтиленовых фасонных частей из материала основной массы соединяемой трубы с заделанными в них при изготовлении нагревательными элементами (рис.8).
В процессе нагрева нагревательного элемента (обычно проволоки с высоким сопротивлением), часть пластиковой массы расплавляется и соединяется с общей массой трубы с образованием сварного соединения. Вследствие того, что электрофузионная муфта после сварки остается на трубе, подобное соединение получается высококачественным, что важно при сварке газовых труб. Этот способ позволяет проводить сварку и врезку в газопроводы под давлением, а также ремонт пластиковых трубопроводов.
29
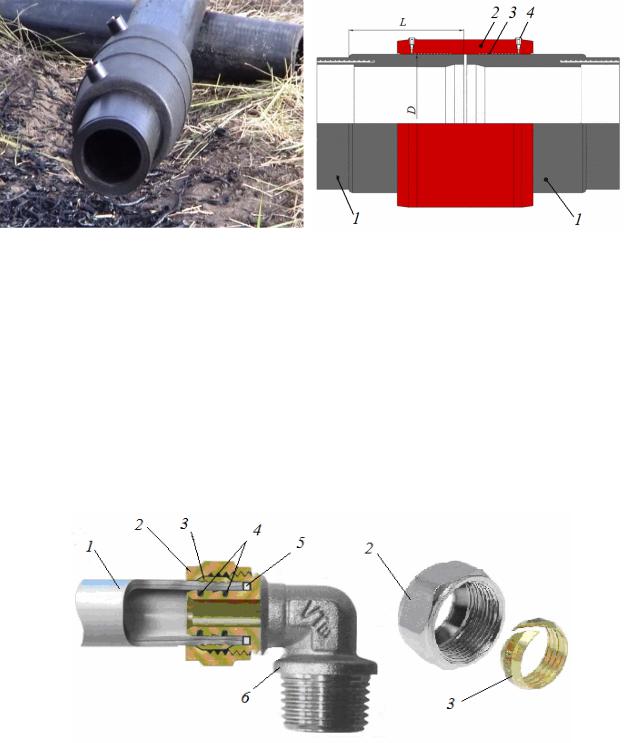
Рис. 8. Электрофузионная или электромуфтовая сварка:
1 – труба; 2 – электромуфта; 3 – нагревательный элемент; 4 – электроконтакты
Соединение металлопластиковых труб
Металлопластиковые трубы выпускаются в бухтах и поэтому их требуется соединять только с фитингами. По способу соединения фитинги делятся на:
•винтовые (компрессионные или цанговые).
•прессующиеся (пресс-фитинги).
При использовании винтового (или цангового) фитинга (рис. 9) соединение достигается за счет давления, возникающего при закручивании гайки 2 на разомкнутом обжимном кольце 3.
Рис. 9. Винтовое (цанговое) соединение металлопластиковых труб 1 – труба; 2 – гайка; 3 – обжимное кольцо; 4 – резиновые уплотнительные кольца; 5 – тефло-
новая изоляционная прокладка; 6 – фитинг
Для герметичности наконечник фитинга имеет специальный удерживающий профиль с радиальной насечкой и двумя уплотнительными резиновыми кольцами 4, прилегающими непосредственно к трубе. Плотному соединению корпуса фитинга с наконечником служит специальная прокладка 5. Это прокладка исключает прямой контакт алюминиевой прослойки с металлом фитинга и тем самым предотвращает электрохимическую коррозию. Обычно ее делают из тефлона.
30