
книги из ГПНТБ / Антифрикционные пористые сплавы Е. Ф. Меркулов. 1960- 6 Мб
.pdfТаблица 13
Химический состав антифрикционных чугунов
|
|
|
|
|
Компоненты в % |
|
|
|
Наименование |
|
^общ |
Si |
Мп |
р |
S |
Сг |
|
|
|
|
||||||
Ферритный |
се |
3,3-3,6 |
3,0—3,5 |
0,4—0,6 |
0,8—1,0 |
_ |
_ |
|
рый чугун .... |
||||||||
Перлитный |
се |
3,2—3,6 |
2,2—2,4 |
0,6—0,9 |
0,15—0,20 |
До 0,12 |
0,2—0,35 |
|
рый чугун Ц1 |
. , |
|||||||
Перлитный |
се |
3,2—3,6 |
2,2—2,4 |
0,6-0,9 |
0,15—0,20 |
До 0,12 |
0,2—0,35 |
|
рый чугун Ц2 . . |
||||||||
Перлитный |
се |
3,2—3,6 |
2.4—2,9 |
0,8—1,0 |
0,15-0,20 |
До 0,12 |
0,2—0,35 |
|
рый чугун ЦЗ . . |
||||||||
Ферритный ков |
2,6 |
1,0 |
0,8 |
0,07 |
0,075 |
|
||
кий чугун .... |
— |
|||||||
Перлитный ков |
|
— |
0,7—1,0 |
|
|
— |
||
кий чугун .... |
— |
— |
— |
|||||
То же................ |
— |
— |
1,1 —1,4 |
— |
— |
— |
||
Перлитно-фер- |
|
|
|
|
|
|
||
ритный |
ковкий |
2,6—3,0 |
1 — 1,10 |
|
|
|
|
|
чугун .................... |
0,9-1,0 |
До 0,07 |
0,008 |
— |
||||
|
|
|
Компоненты в % |
Твер |
Предел |
Относи |
||
|
|
|
|
|
|
|||
Наименование |
|
|
|
дость |
пг очности |
тельное |
||
Ni |
Си |
А1 |
по |
при рас |
удлинение |
|||
|
|
|
Бриьелю |
тяжении |
||||
|
|
|
|
|
|
в кг/мм2 |
в кг/мм2 |
в % |
Ферритный |
се |
— |
— |
— |
|
|
|
|
рый чугун .... |
150—160 |
|
|
|||||
Перлитный |
се |
|
|
|
|
|
|
|
рый чугун |
Ц1 . . |
0,3-0,4 |
0,2—0,3 |
0,1-0,15 |
170—230 |
|
— |
|
Перлитный |
се |
|
— |
— |
|
|
_ |
|
рый чугун |
Ц2 . . |
0,3-0,4 |
170-230 |
69 |
||||
Перлитный |
се |
|
|
|
|
|
|
|
рый чугун |
ЦЗ . . |
0,3—0,4 |
0,7—0,9 |
0,1-0,15 |
170—230 |
— |
— |
|
Ферритный ков |
— |
— |
— |
|
|
|
||
кий чугун .... |
180—190 |
50 |
7 |
|||||
Перлитный ков |
|
— |
— |
|
|
|
||
кий чугун .... |
— |
180—200 |
48—60 |
15—20 |
||||
То же................ |
— |
— |
— |
240—260 |
70-80 |
4-7 |
||
Перлитно-фер- |
|
|
|
|
|
|
||
ритный |
ковкий |
|
|
|
|
|
|
|
чугун .................... |
|
— |
100-200 |
49—53 |
6-7 |
|||
|
|
|
— |
|
39
Для успешного использования антифрикционных чугунов всех:
типов в подшипниках требуется надежная смазка, точная механиче ская обработка и тщательный монтаж.
Важной особенностью чугуна как антифрикционного материала является затрудненная прирабатываемость, требующая применения специальных мер, как например, приработка на холостом ходу или
на облегченных режимах.
Хорошие результаты дают специальные смазки для приработки, травление поверхности, покрытие поверхности чугунного подшип ника пластичными металлами.
В случаях тяжелых условий работы и необходимости повысить
износостойкость предпочтение отдается чугуну с шаровидным гра
фитом и возможно меньшим содержанием феррита.
Однако все вышеописанные антифрикционные чугуны не могут
полностью заменить оловянистые бронзы, так как они, как правило, могут работать при спокойной нагрузке с окружной скоростью,
не превышающей 0,25 м/сек, и при удельной нагрузке 400—450 кг/см2.
Если же окружная скорость равна 1 м/сек, то удельное давлениене должно превышать 100—120 кг/см2, а при окружной скорости 3 м/сек удельное давление не должно быть более 20 кг/см2. Крометого, смазка при применении этих антифрикционных чугунов должна подаваться непрерывно и в большем количестве, а шейки валов,
или осей должны иметь твердость большую, чем у чугунных втулок.
Вот почему для замены оловянистых бронз и был предложен, испытан и применен пористый антифрикционный чугун, обеспечи
вающий просачивание смазки. |
|
|
15. |
Химический состав антифрикционного пористого |
чугуна |
|
и технология его полученияВ |
|
В |
процессе всего срока эксплуатации двигателей, |
собранных |
на вкладышах из того или иного антифрикционного материала, начи ная от высокооловянистых баббитов марки Б83 и до антифрикцион ного чугуна включительно, вопросы циркуляции смазки, ее нагрева, и того, как нагреваются и охлаждаются вкладыши подшипников,
получают доминирующее значение. От них в значительной степени зависит правильная, нормальная и бесперебойная работа двига теля.
Пористость антифрикционного материала, в том числе и пористостьантифрикционного чугуна, обеспечивающая рациональный и полный теплообмен смазки путем просачивания масла через поры, — необхо димое качество хорошего антифрикционного сплава.
На основе изложенного и был предложен антифрикционный пори стый высокопрочный чугун.
Для образования пор и повышения антифрикционных свойств,
был применен свинец (РЬ) и поташ (К2СО0).
Химический состав антифрикционного пористого чугуна приво
дится в табл. 14.
40
Таблица 14
Химический состав антифрикционного высокопрочного пористого чугуна
Наименование |
Собщ |
Si |
Мп |
Р |
S |
РЬ |
|
Антифрикцион |
|
|
|
|
|
|
|
ный |
высокопроч |
|
|
|
|
|
|
ный |
пористый |
|
|
0,2—0,4% |
0,5—1% До 0,12% |
0,5—1,0% |
|
чугун ................ |
2,2—2,8% |
3-4% |
Плавка чугуна производится в обычных вагранках. Могут быть
использованы и другие плавильные агрегаты, обеспечивающие наибо лее надежно заданный химический состав. Шихтовка на заданный химсостав пористого антифрикционного чугуна ведется по аналогии с шихтовкой обычных чугунов. При расчете шихты за основу должен быть принят серый и половинчатый чугун с добавкой 10—20% сталь ного лома.
Что касается фосфора (Р) и свинца (РЬ), то таковые вводятся в ковш с жидким металлом перед заливкой форм. Кроме того, металл обрабатывается в ковше поташом (КгСО3).
Таким образом, на каждые 100 кг жидкого расплавленного чугуна,
при шихтовке должно быть заготовлено:
1)фосфора (Р) 0,5—1 кг (с надбавкой на угар);
2)свинца (Pb) 1—2 кг, т. е. в 2 раза больше заданного по химсо
ставу, исходя из учета его интенсивного выгорания и испарения; 3) поташа (КгСО3) 1 кг в прокаленном порошкообразном виде..
Ввиду того, что поташ вводится в ковш перед самой заливкой литейных форм, его надлежит предварительно развесить по емкости ковшей в специальные литейные «колокольчики» (колпачки), дающие
возможность опускать поташ на дно ковша.
Итак, в очередную плавку заготовленные для пористого антифрик ционного чугуна специальные калоши в середине или в конце плавки одна за другой загружаются в вагранку.
Температуру металла на желобе вагранки желательно иметь. 1370—1380° С.
Сразу же в ковш у вагранки загружается фосфор, который тща тельно перемешивается, затем после некоторого выстаивания с по верхности ковша удаляется шлак, и ковш с металлом транспорти руется к месту заливки.
В поставленный для заливки ковш вводится в «колокольчике» поташ, тщательно перемешиваемый. После перемешивания и реакции поташа на поверхности металла образуется слой шлака, который счи щается лопаточкой.
И наконец перед самой заливкой вводится нарезанный кусочками свинец; свинец перемешивается вместе с горячим чугуном по всемуковшу, и металл разливается в формы.
41
Весь дальнейший процесс литейной технологии производится «обычно принятыми способами, т. е. происходит заливка, выбивка
■форм, очистка и обрубка отливок.
Естественно, что литейная технология меняется в зависимости ют плавильного агрегата.
16. Термообработка антифрикционного пористого чугуна
Термообработка антифрикционного пористого чугуна (АПЧ)
находится в функциональной зависимости от того, какую микро
структуру хотят получить в соответствии с техническими условиями.
Поэтому при желании получить перлитную структуру с содержа нием феррита не более 15% АПЧ подвергают нормализации, а для
получения феррито-перлитной структуры по аналогии со структу рой ковкого чугуна АПЧ подвергают отжигу.
Нормализация придает АПЧ однородную для данной партии деталей мелкозернистую структуру, так как перлит при нормализа ции приобретает тонкое мелкозернистое строение.
Охлаждение деталей АПЧ после нагрева и выдержка при норма лизации производятся на воздухе.
Несмотря на то, что в настоящее время нормализация распро странена в машиностроении больше, чем отжиг, так как она является гораздо более производительной операцией, требует меньших произ водственных площадей, меньше оборудования и рабочей силы,
однако при получении мелких деталей втулок и вкладышей из анти фрикционного пористого чугуна следует отдать предпочтение отжигу
этих деталей, при котором получается структура ковкого чугуна. Как известно, ковким чугуном называется вязкий, хорошо сопро
тивляющийся разрыву и ударной нагрузке чугун, отличающийся наличием в ферритной или перлитной основной структуре хлопье видных графитных выделений, получаемый путем отжига белого чугуна.
Термообработка АПЧ аналогична одному из способов получения ковкого чугуна. Известно, что ковкий чугун получается длительным
отжигом чугунных деталей в высших окислах железа (Fe2O3 или
в Fe3O4) или в песке. При отжиге в окислах железа ковкость чугуна и улучшение его механических свойств достигается за счет выгора ния углерода с поверхностных слоев отливок, а при отжиге в песке происходит преобразование карбид-углерода в аморфный углерод.
При термообработке отливок из антифрикционного пористого чугуна был принят их отжиг в песке, как лучший, в силу того, что наряду с появлением новых механических свойств (ковкости, тягу чести и вязкости), улучшением и повышением временного сопротивле ния на разрыв микроструктура отливок получалась однородной по всему сечению. Перлитно-графитный антифрикционный пористый чугун, особенно в случаях мелкопластинчатого строения перлита и мелких графитных выделений, обладает высокими механическими
■свойствами и износостойкостью и вместе с тем хорошо обрабатывается режущим инструментом.
42
Кроме того, во время отжига получается увеличение диаметра пор чугуна от 1,0—1,25 мм до 1,5—1,75 мм.
Термообработка — отжиг в песке отливок из антифрикционного
пористого чугуна — производится по нижеследующему тепловому режиму.
1.Отливки после их обрубки и очистки укладываются в железные ящики, пересыпаются просеянным сухим кварцевым песком и загру жаются в отжигательную печь.
2.В течение первых 2—4 час. производится нагрев загруженных
вотжигательную печь отливок до температуры 850—900° С.
Фиг. 9. Кривая отжига деталей из антифрикционного пористого чугуна.
3.В последующие 12—16 час. при постоянной температуре
850—900° С производится отжиг чугунных отливок.
4.Затем отливки в ящиках охлаждаются вместе с термопечью>
до цеховой температуры или же охлаждаются в железных ящиках до той же температуры с выгрузкой ящиков из печи.
После охлаждения отливки очищаются и направляются на меха
ническую обработку.
Тепловой режим отливок из антифрикционного пористого чугуна: может быть представлен кривой (фиг. 9).
На данной диаграмме кривая abed, изображающая изменение тем пературы во времени, является теоретической примерной кривой, ибо количество часов, требующихся для нагрева, отжига и охлаждения,,
будет изменяться в зависимости от габарита и веса отливок. Необхо
димо учитывать, что охлаждение отливок надо вести возможно мед
леннее. Температура отжига в целях ускорения процесса термообра ботки может быть повышена; однако при этом надо иметь ввиду, что
при высокотемпературном отжиге получается ферритная структура чугуна, понижающая износостойкость и механические свойства АПЧ.
Отжиг деталей из АПЧ при массовом производстве может произво диться в обыкновенных камерных печах и в печах непрерывного действия с защитной атмосферой, а также в электропечах.
43.
В печах с защитной атмосферой и электрических печах отливки
из АПЧ могут отжигаться без упаковки и засыпки, благодаря чему сокращается длительность отжига й уменьшается расход топлива.
17. Механическая обработка и сборка деталей из антифрикционного
пористого чугуна
Заготовки из АПЧ отливаются в виде сплошных цилиндров (бол ванок), втулок и фасонных заготовок.
При отливке втулок и болванок может применяться как дождевая,
так и сифонная заливка.
Станочная обработка заготовок из антифрикционного пористого чугуна должна вестись на больших оборотах при максимальных ско ростях резания и при малых подачах порядка 0,1 мм.
Что касается глубины резания, то она принимается аналогичной
обработке обычных чугунных отливок.
Механическая обработка должна обеспечивать чистоту рабочей поверхности подшипника не ниже 7-го класса по ГОСТ 2789—59.
При монтаже подшипников со втулками из АПЧ требуется соблю дение следующих условий.
1.Во избежание задиров края поверхности скольжения должны быть закруглены.
2.Также во избежание задиров и разрыва масляного слоя края смазочных канавок не должны быть острыми.
3.Зазор между втулкой и шейкой вала должен быть на 20—50% больше, чем при применении бронзовых втулок, где величина зазора составляет обычно около 0,003 диаметра вала.
4.При сборке необходимо особенно тщательно отделать рабочую поверхность чугунных втулок шабровкой, а шейку вала отшлифо
вать; кроме того, нельзя допускать перекосов, при которых часть трущейся поверхности вследствие уменьшения зазора окажется без смазки, результатом чего явятся задиры и быстрый износ.
5.Смазка должна подаваться принудительно в достаточном коли честве; предпочтение следует отдавать густой смазке. Канавки для смазки должны быть прорезаны на ненагруженной стороне под
шипника, обычно в верхней половине.
6.Для предупреждения задиров шейки вала необходима предва
рительная приработка втулок как вхолостую, так и при нагрузке.
Время приработки зависит от мощности механизма и колеблется от 4 до 12 час. Для улучшения прирабатываемости чугунного под шипника рекомендуется производить травление его поверхности 10—15-процентным раствором азотной кислоты в течение 2—3 мин. с последующей промывкой в проточной воде, нейтрализацией и про
варкой в масле при 120—130° С в течение 1—2 час.
7.Приработку втулок надлежит вести на смазке с добавлением
•0,1—0,3 графита.
8.После приработки втулок для удаления механических приме
сей, образовавшихся в процессе приработки, необходимо сменить
смазку.
44
При сборке на втулках из антифрикционного пористого чугуна коренных подшипников коленчатого вала автомоторов необходимо производить холодную обкатку без нагрузки и горячую обкатку
•с нагрузкой на испытательных стендах и первые 1000—1500 км про
бега вести с неполной нагрузкой автомашины.
Шатунные подшипники в силу особо тяжелых условий их работы при резко переменных нагрузках и усилиях коленчатого вала соби рать на втулках или вкладышах из антифрикционного пористого чугуна не следует, ибо это создает преждевременный износ дорого стоящего вала и его возможные задиры при эксплуатации.
18. Физико-технические и металлографические свойства
антифрикционного пористого чугуна
Свойства и качества |
АПЧ характеризуются следующими дан |
||
ными: |
|
|
|
Удельный |
вес.................................... |
7,1 —7,15 |
|
Диаметр |
пор........................................ |
• |
0,75 — 1,5 мм |
Временное |
сопротивление разрыву |
40—50 кг/мм2 |
|
Относительное |
удлинение................ |
10—15% |
|
Твердость по Бринелю........................ |
100—120 НВ |
||
Коэффициент трения со смазкой . . . |
0,004—0,005 |
||
Микроструктура |
................................ |
Перлитно-феррит- |
ная перлитная и перлитно-графит ная
В табл. 15 дается сопоставление твердости АПЧ с твердостью раз личных антифрикционных чугунов, ибо твердость является одним из основных дополнительных кон трольных факторов как для иссле дования микроструктуры, так и для эксплуатации антифрикцион ных материалов.
Из анализа данной таблицы видно, что АПЧ обладает понижен ной по сравнению с другими анти фрикционными чугунами твердо стью.
Другим не менее важным фак тором любого антифрикционного
материала, в особенности с точки зрения условий его эксплуатации,
является напряженность работы подшипников, определяемая, как известно, по величине удельной нагрузки и окружной скоро сти (р и о).
Допустимые удельные давлении
скорости для |
различных |
марок |
Фиг. |
10. Допустимые значения удель |
|
антифрикционного чугуна |
выби |
||||
ного |
давления и окружной скорости |
||||
раются по фиг. |
10. |
|
для антифрикционных чугунов. |
45
Таблица 15
Твердость антифрикционных чугунов
Группа
Чугун с пластинчатым гра фитом
Чугун с шаровидным гра фитом
Чугун с графитом в виде углерода отжига (ковкий чугун)
Антифрикционный пористый чугун
Марка
СЧЦ-1
СЧЦ-2
Титаномедистый
Влитом состоянии После нормализации
Нелегированный, перлитноферритный
' Медистый
Титаномарганцовистый со сфероидизированным перлитом
АПЧ перлитный и перлитноферритный
Твердость - (верхний предел)
| НВ
229
229
229
229
269
229
260
200
120
На фигуре кривая 1 соответствует СЧЦ-1 и СЧЦ-2; 2 — титаномедистому; 3 — с шаровидным графитом и нелегированному ковкому чугуну; 4 — антифрикционному пористому чугуну.
Таким образом, АПЧ может с точки зрения допустимых удельных давлений и скоростей применяться во всех узлах трения, включая детали, подвергающиеся нагреву до 300° С с удельным давлением до 90 кг/см2 и окружными скоростями до 4 м/сек, а работоспособность подшипников из антифрикционного пористого чугуна, как это сле дует из кривой 4 (фиг. 10), будет ро > 90 кгм/см2 сек.
Антифрикционный пористый чугун, как указывалось выше, в зависимости от его назначения можно получить с перлитной, пер-
литно-ферритной, а в некоторых случаях и ферритно-графитной
микроструктурой. Наиболее желательной с точки зрения меха нических свойств является перлитная структура и перлитно-фер- ритная с содержанием феррита не более 15%.
Как известно, в металлографии различают три основные разно
видности перлита, а именно: перлит мелкопластинчатый (фиг. 11, а), крупнопластинчатый (фиг. 11, б) и очень крупнопластинчатый (фиг. 11, в), из которых мелкопластинчатой разновидности отдается
предпочтение. Перлитный чугун не требует отжига; для получения
перлитного антифрикционного пористого чугуна достаточна его нормализация. В силу большой сопротивляемости истирающим уси лиям перлитный АПЧ можно с успехом применять для тех деталей,
46
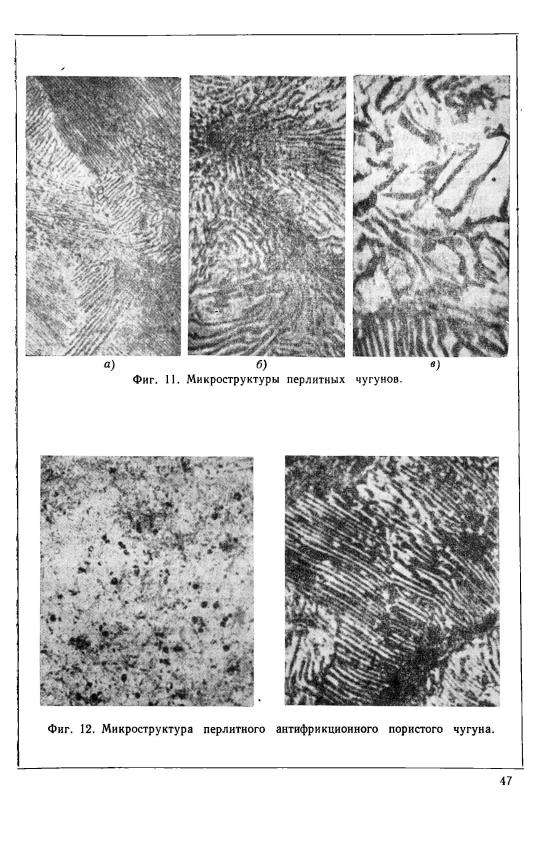
которые совершают значительную работу трения скольжения, как например поршни, поршневые кольца, цилиндры, зубчатые колеса, салазки. Перлитный АПЧ легко обрабатывается.
Пороком микроструктуры готовых деталей из АПЧ является
присутствие цементита; оно приводит к повышенной твердости и хруп
кости и является следствием недостаточного отжига или повышен
ного содержания марганца. Утяжины, загрязнения и наличие пла
стинчатого графита также являются пороками микроструктуры АПЧ.
Если детали из АПЧ должны подвергаться в работе резкому истиранию, то перлитная структура на его поверхности крайне полезна, так как она повышает износостойкость чугуна.
АПЧ с мелкими выделениями пластинчатого графита, структурой тонкого сорбитообразного перлита (фиг. 12) и повышенной твердостью» хорошо сопротивляется износу и в первую очередь может приме няться' в качестве антифрикционного материала для подшипников скольжения. Однако необходимо учитывать, что пластинки гра
фита |
могут вызвать выкрашивание металлической основы чугуна |
и ее |
разрушение при трении. В этом отношении АПЧ с шаровид |
ным графитом обладает лучшими антифрикционными свойствами,
так как в силу шаровидной формы графита сплошность металли ческой основы чугуна почти не нарушается и выкрашивание ее
не происходит. Поэтому модифицирование антифрикционного пори стого чугуна магнием дело ближайших лет. Необходимо отметить,
что можно придать желаемую пористость путем введения поташа (К2СО3) любым сортам антифрикционных чугунов. Если эти чугуны будут удовлетворять техническим условиям и требованиям их эксплуатации, их можно получать без дополнительного введения свинца.
19. Область применения антифрикционного пористого чугуна
По своим антифрикционным и эксплуатационным качествам АПЧ предназначается в первую очередь для замены остродефицитных
идорогостоящих оловянистых бронз.
Втабл. 16 приводится перечень испытанных в работе деталей
из антифрикционного пористого чугуна, примененного взамен дру гих материалов с указанием характера нагрузки.
■ При переводе подшипников с бронзы на антифрикционный пори стый чугун надо иметь возможность обеспечить надлежащую.механи ческую обработку, зазоры и тщательность монтажа. Кроме того, надо учитывать такие элементы режима эксплуатации, как удельное давление, скорость, условия смазки, состояние сопряженной детали,
а также учитывать производственные возможности завода, т. е. воз можности литейного цеха в отношении получения отливок и возмож
ности механического цеха в отношении точности обработки деталей. Антифрикционный пористый чугун найдет наряду с другими анти фрикционными чугунами широкое применение в нижеследующих
машинах и механизмах:
1) токарных, фрезерных, зуборезных, шлифовальных, точильных,
сверлильных и долбежных станках;
48