
книги из ГПНТБ / Антифрикционные пористые сплавы Е. Ф. Меркулов. 1960- 6 Мб
.pdfТаблица 7
Карта замеров коренных и шатунных шеек коленчатого вала, работавшего на вкладышах из алькусипа на двигателе ЗИЛ-120 №04,
после пробега автомашины 27 340 км
№ шеек коленча того вала
1
Номиналь |
Размеры диаметров |
Конусность |
Эллипсность |
Износ |
|||||
ный размер |
шеек в мм после |
||||||||
диаметров |
пробега автодвига |
в мм |
в мм |
в мм |
|||||
шеек в мм |
теля 27 340 км |
|
|
|
|
|
|
||
корен-, шатун |
коренных |
шатун |
корен шатун |
корен |
шатун |
корен шатун |
|||
ных |
ных |
ных |
ных |
ных |
ных |
ных |
ных |
ных |
|
65,95 |
61,91 |
65,84—83 61,76—76 |
0,01 |
0,01 |
0,03 |
0,02 |
0,12 |
0,15 |
|
65,86—86 |
61,77—78 |
|
|
|
65,85—875 61,78—785 |
|
|
|
|
|
|
||
2 |
65,95 |
61,92 |
65,87—89 |
61,81—805 0,025 0,005 0,02 |
0,03 |
0,10 |
0,14 |
||||
3 |
65,96 |
61,93 |
65,86—85 |
61,71—705 |
0,01 |
0,015 |
0,02 |
0,045 |
0,11 |
0,225 |
|
65,87—87 |
61,755—74 |
||||||||||
4 |
65,96 |
61,93 |
65,91—91 |
61,79—79 |
0,02 |
— |
0,03 |
0,02 |
0,05 |
0,14 |
|
65,94—92 |
61,81—81 |
||||||||||
5 |
65,96 |
61,93 |
65,89—87 |
61,84—835 |
0,02 |
0,01 |
0,02 |
0,03 |
0,09 |
0,095 |
|
65,90—89 |
61,87—86 |
||||||||||
6 |
65,94 |
61,92 |
65,87—88 |
61,825—79 |
0,01 |
0,03 |
0,02 |
0,02 |
0,07 |
0,13 |
|
65,89—90 |
61,84—81 |
||||||||||
7 |
65,95 |
— |
65,89—88 |
— |
0,01 |
— |
0,02 |
— |
0,07 |
— |
|
65,91—90 |
|||||||||||
|
|
|
|
|
|
|
|
|
|
с Б83. Износ же шеек коленчатых валов у последующих автодвига телей, собиравшихся нормальным для алькусипа способом, оказался
меньше приведенных в картах замеров. |
|
срок |
|
Нельзя не отметить, |
что если в весьма тяжелых условиях |
||
работы вкладышей из |
Б83 составлял в среднем |
22 000 км, то |
|
вкладыши из алькусипа |
работали без замены до |
34 000 км |
про |
бега. |
|
|
|
Учитывая, что теплопроводность и теплоемкость у алюминия
выше, чем у олова, при эксплуатации двигателей на алькусиповых вкладышах необходима более обильная смазка, йто обязывает,
в частности, водителей автомашин внимательно следить за давле нием масла, не допуская его падения.
2* |
19 |
Таблица 8 Карта замеров коренных и шатунных шеек коленчатого вала, работающего
на вкладышах из алькусипа на двигателе ЗИЛ-120 №01, после пробега автомобиля 26 962 км
№ шеек колен чатого вала
Номиналь |
Размер диаметров |
Конусность |
Эллипсность |
Износ |
||||
ный размер |
шеек после пробега |
|||||||
диаметров |
автодвигателя |
|
мм |
мм |
|
мм |
||
шеек в мм |
26 962 км |
|
|
|
|
|
||
корен шатун |
коренных |
шатун |
корен шатун |
корен шатун |
корен шатун |
|||
ных |
ных |
ных |
ных |
ных |
ных ных |
ных |
ных |
1 |
65,99 |
61,93 |
65,84—83 61,73—72 0,01 |
0,01 |
0,06 |
0,02 |
0,16 |
0,21 |
||
|
65,985 |
|
65,90—89 61,75—74 |
|
|
|
|
|
|
|
2 |
65,985 |
61,935 |
65,86-85 61,72—75 |
0,01 |
0,03 |
0,02 |
0,02 |
0,135 |
0,215 |
|
|
65,98 |
|
65,88—87 61,74—77 |
|
|
|
|
|
|
|
3 |
65,99 |
61,93 |
65,88—86 61,78—73 0,02 |
0,05 |
0,02 |
0,04 |
0,13 |
0,20 |
||
|
65,98 |
|
65,89—88 61,82—77 |
|
|
|
|
|
|
|
4 |
65,975 |
61,94 |
65,89—87 61,79—78 |
0,02 |
0,01 |
0,02 |
0,02 |
0,105 |
0,16 |
|
|
65.965 |
|
65,91—89 61,81—80 |
|
|
|
|
|
|
|
5 |
65,99 |
61,94 |
65,86—87 61,83—83 |
0,02 |
0,01 |
0,02 |
0,03 |
0,13 |
0,11 |
|
|
65,98 |
|
65,87—89 61,85—86 |
|
|
|
|
|
|
|
6 |
65,98 |
61,93 |
65,87—875 61,83—83 0,005 |
0,01 |
0,015 |
0,04 |
0,11 |
0,19 |
||
|
65,985 |
|
65,885—89 61,78—79 |
|
|
|
|
|
|
|
7 |
65,985 — |
65,88—88 |
— |
0,01 |
— |
0,02 |
— |
0,105 |
— |
|
|
65,98 |
|
65,90—89 |
|
|
|
|
|
|
|
7.Физико-механические и металлографические свойства алькусипа
Втабл. 9 дано сопоставление физико-механических свойств алькусипа и высокооловянистых баббитов марок Б83 и Б90.
Таблица 9 Физико-механические свойства алькусипа и высокооловянистых баббитов
Наименование свойств Алькусип Б90 Б83
Удельный вес........................................ |
|
2,75—2,80 |
7,30 |
7,38 |
Начало затвердевания в |
°C................ |
625-623 |
342 |
370 |
Конец затвердевания в °C................ |
600—610 |
241 |
240 |
|
Предел прочности при |
растяжении |
13,1 — 14,6 |
9,2 |
9,0 |
в кг/мм*......................................................... |
|
|||
Относительное удлинение в % . . . |
12—16 |
9,0 |
6,0 |
|
Твердость по Бринелю в |
кг/мм1 . . |
28,6—34,5 |
27 |
30 |
Коэффициент трения со смазкой . . |
0,003 |
— |
0,005 |
20
Из этой таблицы видно, что алькусип обладает большим отно сительным удлинением при большем пределе прочности на растя жение, т. е. лучшими первичными механическими свойствами при
твердости, близкой к твердости оловянных баббитов.
Опыт эксплуатации грузовых автомобилей показал, что вкладыши из алькусипа с повышенной, по сравнению с Б83 и Б90, твердостью
в работе не только значительно устойчивее, но и меньше изнашивают шейки коленчатого вала. Шатунные вкладыши из алькусипа должны иметь меньшую твердость, нежели коренные вкладыши, что дости гается соответствующим увеличением содержания свинца.
Коэффициент трения со смазкой алькусипа выгодно отличается как от оловянных баббитов, так и от других антифрикцион
ных алюминиевых сплавов и малооловянистых биббитов, что видно из табл. 10.
Таблица 10
Сопоставление физико-механических свойств алькусипа с другими антифрикционными алюминиевыми сплавами и малооловянистыми баббитами
Сплавы
Физические
константы
Удельный вес . . |
|
|
|
|
9,55 |
9,29 |
|
9,6 |
10 |
10,5 |
2,75—2,80 |
|
Предел прочности |
|
|
|
|
|
|
|
|
|
|
|
|
при |
растяжении |
9,6 |
6,3 8,3 |
8,1 |
10,7 |
7 |
7,8 |
8 |
6,8 |
4,2 |
10 |
13,1—14,6 |
в кг/ммг ...... |
||||||||||||
Относительное |
9,1 |
2,0 16,7 |
13,9 |
21,9 |
1 |
0.2 |
2 |
0,2 |
0,6 |
2,5 |
12—16 |
|
удлинение в % . . . |
||||||||||||
Твердость по Бри- |
34,3 34,9 28,3 31,4 |
33,3 |
29 |
30 |
25 |
32 |
20 |
32 |
28,6—34,5 |
|||
нелю в кг/мм2 . . . |
||||||||||||
Коэффициент тре |
|
|
|
|
0.006 |
0,005 |
0,009 |
0,005 |
0,007 |
0,004 |
0,003 |
|
ния со смазкой . . . |
|
|
|
|
Низкий коэффициент трения алькусипа объясняется его хоро шими антифрикционными свойствами и микропористостью.
Работа трения, характеризующая напряженность работы подшип ников в зависимости от технических и эксплуатационных условий,
для алькусипа колеблется в пределах 100—180 кем!см2 сек.. Эта работа
выражается формулой
А = pv,
где р — удельное давление кг/см2, v — скорость м/сек.
Алькусип обладает высокой коррозионной стойкостью, оценка
которой была произведена путем определения потери веса образцов после 60-часового их пребывания в искусственно окисляемом автоле. Установлено, что алькусип не подвержен коррозии в окисляемом масле.
21
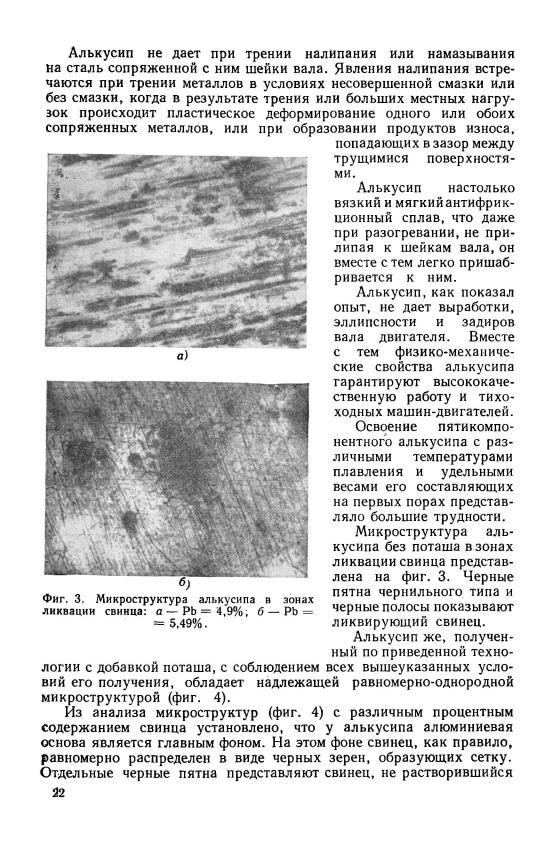
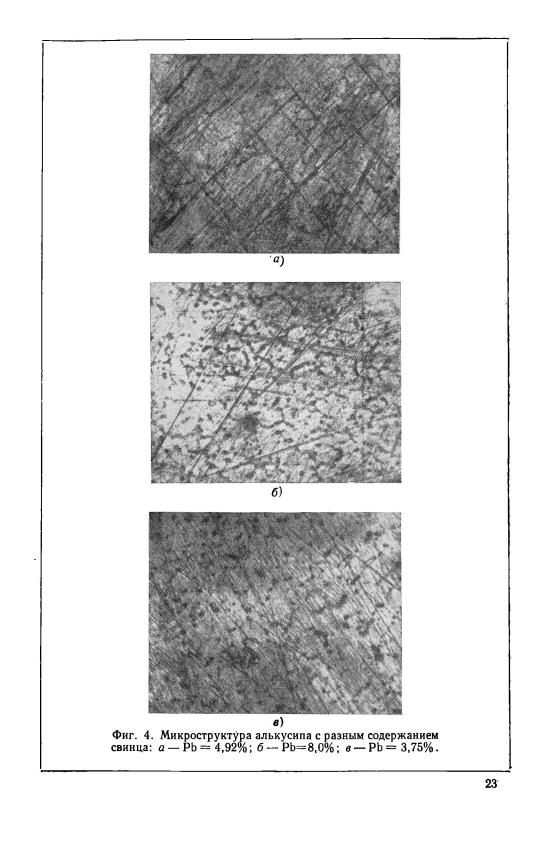
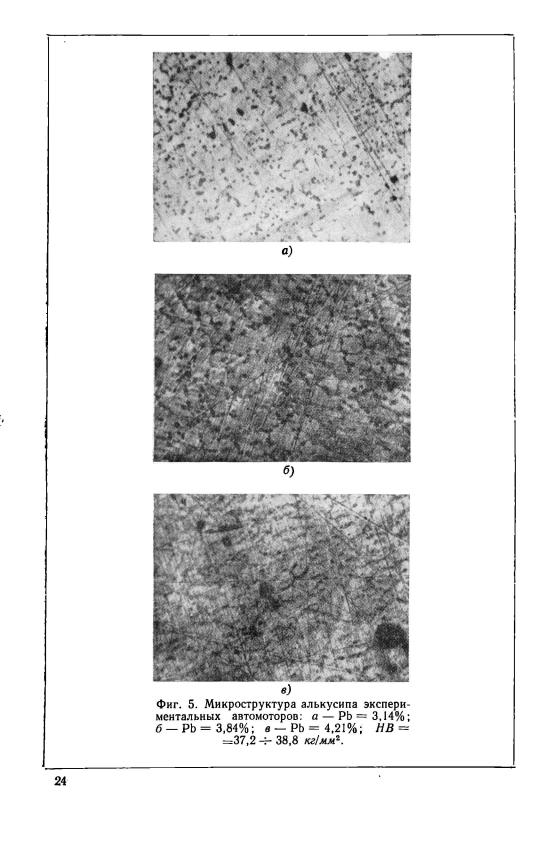
из-за несовершенства ведения плавок и в первую очередь из-за плохого перемешивания поташа и свинца при их вводе в тигель или в ковш. Однако такие пятна ничего общего с ликвацией свинца
не имеют.
Что касается других компонентов сплава, как медь, железо, кремний, то незначительное изменение их дозировки как в сторону уменьшения, так и в сторону увеличения никакого влияния на харак тер строения сетки не оказывает.
Итак, при строгом соблюдении литейной технологии с введением в сплав поташа свинец с алюминием образует эвтектический раствор.
Пористость алькусипа в результате воздействия на него поташа
обнаруживается даже невооруженным глазом, а при пользовании простой лупой или микроскопом можно легко замерить диаметр пор, который колеблется в пределах от 0,1 до 0,2 мм.
С увеличением количества вводимого поташа увеличивается пори стость в алькусипе, что оказывает благоприятное влияние, как пока зал опыт, на условия эксплуатации автомобилей, увеличивая как сроки службы коленчатых валов, так и продолжительность работы вкладышей.
Таким образом, алькусип имеет не только небольшие капилляр ные ходы, но и поры, по которым просачивается смазочное масло,
уменьшающее |
трение в |
подшипниках, что |
придает вкладышам |
из этого сплава свойства сетчатых подшипников. |
|||
На фиг. 5 |
приводятся |
микроструктуры |
алькусиповых шатун |
ных коренных вкладышей первых экспериментальных автомоторов,
на которых грузовые автомобили ЗИЛ-150 сделали по 34 000 км пробега. Была достигнута более легкая и надежная работа двига
телей на подъемах и полное отсутствие стука в них.
8. Выводы
Условия работы шатунных вкладышей подшипников коленчатого вала автомобильных двигателей являются исключительно тяжелыми
в силу наличия касательного знакопеременного ускорения поршня
двигателя, в результате которого создаются значительные добавоч ные силы инерции и динамические нагрузки, воздействующие как на подшипники, так и на их вкладыши. И по режиму эксплуа тации автомобильные двигатели работают в более тяжелых по срав
нению со всеми другими машинами-двигателями условиях. Поэтому алькусип, показавший исключительно хорошие результаты при испытаниях на плохих дорогах, получил широкое применение не только как заменитель высокооловянистых баббитов Б83 и Б90, но и как новый более дешевый рентабельный алюминиево-свинцово- медный баббит взамен дорогостоящих остродефицитных оловяни-
стых бронз.
Алькусип является универсальным антифрикционным сплавом,
а потому он применяется не только в автомобильных двигателях,
но и в металлорежущих станках.
25
Так, |
втулки из |
алькусипа, |
установленные |
на валики привода |
|
и фрикциона токарного станка |
вместо трех |
бронзовых |
втулок, |
||
показали |
хорошие |
результаты, |
оказались устойчивыми в |
работе |
при большой нагрузке по изготовлению тормозных чугунных бара банов.
В другом случае были применены втулки из алькусипа на валике фрикциона токарного станка «Красный Пролетарий» взамен бронзовых втулок. Этот станок работал на алькусипе с большой нагрузкой по изготовлению шестерен и по обточке болванок диаметром 250 мм
при длине I — 550 мм и весе 150—160 кг.
Если при бронзовых втулках станок вследствие большой нагрузки
быстро нагревался, а фрикционы горели, то втулки из алькусипа
даже не грелись. Мало того, никаких изменений в сторону сработан ности и заеданий алькусиповых втулок не обнаруживалось.
Алькусип дал возможность подтвердить отличное от правила Шарли положение: антифрикционный сплав может увеличить и улуч шить свои антифрикционные свойства и в том случае, если его струк тура будет состоять из сравнительно мягких включений определен ных размеров и в определенном количестве, равномерно рассеян ных в относительно более твердой основе.
Свинец в алькусипе образует с медью и алюминием при введении
поташа в количестве 1—5% не эмульсионный, а эвтектический раствор. Кроме того, с увеличением ввода поташа свинец в большом
количестве усваивается в алькусипе.
Алькусип не только имеет небольшие капиллярные ходы, по кото рым просачивается смазочное масло, уменьшающее трение в подшип никах, но обладает пористостью, вследствие чего вкладыши из этого сплава получают свойства сетчатых подшипников.
Необходимо иметь в виду, что при эксплуатации двигателей на вкладышах из алькусипа нужна более обильная смазка.
Новый антифрикционный сплав — алькусип (алюминиево-свинцо-
во-медный баббит) — обладает следующими преимуществами по срав нению с баббитом Б83: не содержит олова, при массовом производстве обходится в 15—20 раз дешевле, не расплавляется при перегреве,
обладает морозостойкостью, в 2—3 раза устойчивее, расход алькусипа в 2—2,5 раза меньше, чем баббита Б83.
Алькусип может и должен получить применение в автомобиль
ных, тракторных и авиационных двигателях, судовых и стационар ных установках, во всех машинах-двигателях и машинах-орудиях не только как подшипниковый антифрикционный сплав, но и как заменитель дорогостоящих оловянистых бронз марок Бр.ОЮ,
Бр.ОЦ10-2 и Бр.ОЦ8-4.
Внедрение алькусипа даст народному хозяйству ежегодно эко номию, исчисляемую многими тоннами остродефицитного олова и миллионами рублей.
ГЛАВА II
ПОРИСТАЯ АНТИФРИКЦИОННАЯ АЛЮМИНИЕВО-СВИНЦОВАЯ
БРОНЗА
9.Химический состав
Вотличие от алькусипа другой разработанный автором анти фрикционный сплав — алюминиево-свинцовая бронза 1 — является более простым по технике приготовления, так как пониженное содер
жание свинца в сплаве и более высокое содержание железа и кремния облегчают условия получения заданного химического состава. Алю миниево-свинцовая бронза содержит 92—93%А1; 5,0—5,5% Си;
0,5—0,6% Fe; 0,4—0,5% Si и 1—1,5% Pb. Она может быть реко мендована взамен дорогостоящих остродефицитных оловянистых бронз марок Бр.ОЮ, Бр. 010-2, Бр.08-4.
Для придания сплаву пористого строения в процессе плавки в него вводят поташ.
Химический состав пятикомпонентной пористой антифрикцион ной алюминиево-свинцовой бронзы зависит от ее назначения и тех нико-эксплуатационных требований к ней.
При назначении ее в качестве заменителя высокооловянистых
бронз и малооловянистых баббитов типа Б16 химический состав
бронзы рекомендуется следующий (в %): А1—92,5; Си — 5; Fe — 0,6; Si — 0,4 и Pb — 1,5, т. е. с наибольшим процентным содержа нием свинца; в этом случае поташ вводится во время плавки в коли
честве 1—1,5% от веса шихты. Бронза указанного состава пригодна для вкладышей коренных подшипников грузовых автомашин.
Для тракторных двигателей и других машин-двигателей как
стационарного, |
так и транспортного типа |
с числом |
оборотов |
|
до 1200 об/мин. |
наилучшие опытные результаты показала бронза |
|||
с содержанием (в |
%): А1 — 92,5; Си — 5,25; |
Fe — 0,55; |
Si —0,45; |
|
Pb — 1,25. |
во всех остальных случаях и в первую очередь при |
|||
И, наконец, |
работе металлорежущих станков для замены обыкновенных бронзо-
1 Авторское свидетельство № 105711 Комитета поделай изобретений и открытий при Совете Министров СССР по Госреестру от 16 марта 1957 г.
27
вых втулок, например на валиках их фрикционов, при особо тяже
лых ударных нагрузках ставится бронза с химсоставом, дающим большую твердость: А1—92,5%; Си—5,5%; Fe — 0,6%; Si —
0,4%; Pb —1,0%.
10. Шихтовка, плавка и заливка
Пористую антифрикционную алюминиево-свинцовую бронзу можно получать в тигельных печах, в печах типа «Мечта», в электро
печах, а при ремонтных работах, в случаях отсутствия цеха цветного литья — в простых нагревательных печах и горнах, обеспечивающих температуру расплавления меди. Для плавки могут использоваться
не только графитовые или шамотовые, но даже самодельные тигли. Таким образом, алюминиево-свинцовая бронза может быть полу
чена даже в полевых и походных условиях.
Учитывая интенсивное выгорание свинца и ферросилиция, ших товку бронзы при ее приготовлении в шахтных печах типа Калимана (на опыте многочисленных плавок, проделанных автором) устанавливают следующей:
1)первичный алюминий — 87%;
2)красная медь — 5%;
3)ферросилиций (75-процентный)—2%;
4)свинец — 6%;
Вполне очевидно, что чем плавильный агрегат более совершенен и чем опытнее плавильщик и заливщик, тем меньше будет угар элементов шихты. В шихту добавляется поташ в количестве 1 % ■от ее веса.
При использовании в шихте алюминиевого лома следует иметь в виду, что вес его не должен превышать 25% от веса всего шихтуе мого алюминия.
Перед плавкой производят тщательную подготовку шихты: све жий первичный алюминий разрубают на куски весом по 1,5—5 кг,
-а алюминиевый лом разбивают на мелкие куски с удалением из алю миния всех инородных включений; красную медь рубят на мелкие полосы или куски; ферросилиций толкут до порошкообразного состояния и просеивают через мелкое сито; свинец заготовляют
в кусочках весом 0,3—0,5 кг; поташ, обладающий большой гигро скопичностью, должен быть предварительно хорошо просушен
и прокален, а затем истолчен в порошок и положен во избежание его всплывания в «колокольчик». Поташ настолько гигроскопичен,
что и после прокаливания, перед самой плавкой или даже во время
плавки, его надо подсушивать или заново прокаливать.
Кроме того, перед плавкой в целях предохранения от окисления и выгорания элементов, составляющих шихту, следует обязательно заготовить толченый древесный уголь для покрытия им «зеркала»
металла. |
|
производиться |
|
не |
Такая заготовка шихтуемых материалов должна |
||
только |
при ведении тигельной плавки в печи |
Калимана, но |
|
и |
в более |
элементарных плавильных агрегатах, |
ибо она обеспе |
28