
книги из ГПНТБ / Круглов, Евгений Николаевич. Устройство швов в цементобетонных дорожных покрытиях
.pdfженный бетон покрытия. Эта операция производится после заклю чительного прохода бетоноотделочной машины и поэтому структур
ная прочность бетона на кромках шва нарушается, а вытесненная виброножом смесь становится источником образования неровно стей на покрытии. Эти неровности — принципиальный недостаток такого способа устройства швов, снижающий эксплуатационные качества многих построенных цементобетонных покрытий.
В1957—1958 гг. в Союздорнии проведена работа по устройству
швов путем нарезки в затвердевшем бетонном покрытии. В .этом случае готовую бетонную полосу через несколько часов после ее уплотнения, на стадии ухода за бетоном, распиливают с помощью абразивных режущих дисков, вращающихся с высокой скоростью.
Основными достоинствами нарезки швов являются:
1)долговечность конструкции шва, так как распиловка затвер
девшего покрытия не вызывает разрушения кромок бетона;
2)геометрически правильные и минимально необходимые раз меры швов, придающие покрытию хороший внешний вид и высокие эксплуатационные качества;
3)значительное упрощение процесса отделки покрытия, так как исключаются все операции после заключительного прохода бетоноотделочной машины;
4)возможность применения средств ухода за бетоном сразу же после окончания механизированного процесса уплотнения и отдел ки покрытия. Это особенно важно в жаркую погоду и при отрица тельных температурах воздуха;
5)резкое сокращение ручного труда при строительстве по крытия.
Недостатком следует считать сравнительную дороговизну, свя занную с необходимостью применять дефицитные абразивные ма
териалы.
Процесс распилки бетонных и железобетонных плит, а также
каменных материалов (гранита, мрамора) с помощью абразивных режущих дисков не является новым. В нашей стране имеется целый ряд предприятий, осуществляющих эту распилку в промышленных масштабах. Устройство швов цементобетонных покрытий автомо бильных дорог и аэродромов аналогичными методами впервые на чали применять в 1952 г. в США. С тех пор этот способ нашел за рубежом широкое распространение, и для распилки швов там при меняют разнообразные машины, как самоходные, так и передви гаемые вручную, снабженные одним или несколькими абразивными дисками (рисунки 12 и 13).
Втекущем году Николаевский завод дорожных машин Херсон ского совнархоза приступил к серийному выпуску однодисковой машины Д-432, специально предназначенной для устройства швов
вбетонных покрытиях. Нарезчик швов Д-432 (рис. 14) представ ляет собой тележку на трехколесном ходу с приводом для передви жения вручную. Машина оборудована электродвигателем мощно стью 18,0 кет, клиноременной передачей от двигателя к валу режу щего инструмента,, шпинделем, на вал которого монтируется режу-
19
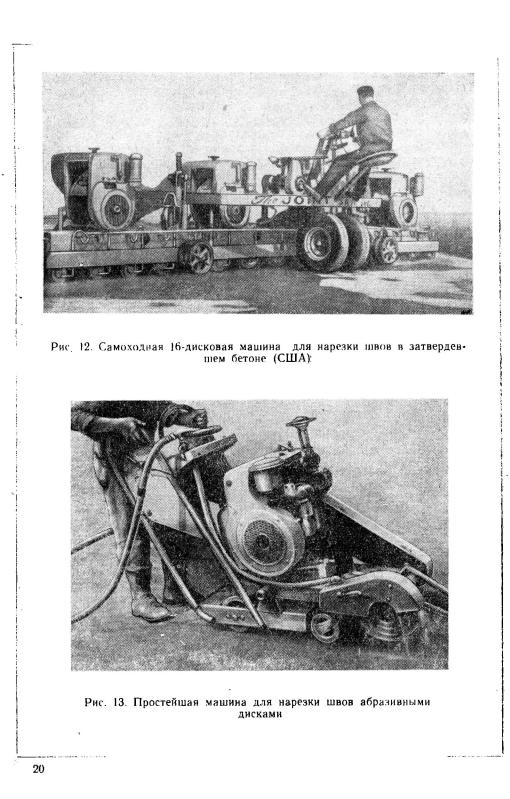

щий инструмент — абразивный диск, водяным насосом и механиз
мом передвижения машины. В. комплект оборудования входят лег кие направляющие рельсы, по которым машина перемещается во время работы.
Рис. 14. Машина Д-432 для нарезки швов в затвердевшем бетонном покрытии
Абразивный круг заглубляют рычагам, положение которого
фиксируют при помощи зажимного штурвала.
Техническая характеристика нарезчика швов Д-432
Тин машины |
.............................................................. |
|
|
|
|
Ручная с приводом аб |
|
|
|
|
|
|
|
разивного |
круга от |
Рабочий орган—абразивный круг: |
|
электродвигателя |
|||||
. |
320 |
|
|||||
диаметр, |
мм |
|
.......................................... |
|
|
||
число оборотов в минуту |
............................... |
|
3490 |
|
|||
Окружная скорость, м/сек ................................... |
|
заглуб- |
58 |
|
|||
Подъем в транспортное положение и |
Вручную при |
помощи |
|||||
■ ление рабочего |
органа..................... |
. . ; . . |
|||||
Максимально-возможная величина заглубле |
рычага |
|
|||||
80 |
|
||||||
ния, мм...................................................... |
|
|
|
|
. . . |
|
|
Дорожный просвет, мм; |
направляющего |
|
|
||||
от рамы |
до |
|
основания |
90 |
|
||
рельса ....................................... |
|
|
|
........................ |
|
||
от рамы до |
опорной поверхности |
ходо |
70 |
|
|||
вых колес . . ....................................................... |
|
||||||
Скорость резания |
(скорость |
подачи |
инстру |
|
|
||
мента), м/члс; |
|
|
|
|
14—16 |
||
при нарезке швов 8—10 мм ....................... |
|
||||||
при нарезке швов 14 мм............................... |
|
13—14 |
|||||
Электродвигатель: |
|
|
|
А063-А |
|||
тип.......................................................................... |
|
|
|
|
|
||
мощность, кет................................................... |
|
|
18-20 |
||||
число оборотов в минуту |
............................... |
|
1460 |
|
|||
напряжение, |
в |
................... |
|
|
220/380 |
21
Габаритные размеры в рабочем положении, мм:
длина....................................................................... |
|
2755 |
ширина....................................................... |
,............................... |
91'5 |
высота .......................... |
1305 |
|
Вес машины, кг . |
|
713 |
Обслуживающий персонал, чел.............................. |
1 |
|
В июле-августе 1958 г. под Москвой проведены междуведомст |
||
венные испытания |
нарезчика швов Д-432, |
которые показали, что |
эта машина обеспечивает высокое качество нарезки, имеет простую и надежную конструкцию и может успешно применяться при строительстве бетонных покрытий. Вместе с тем выявлены и неко торые существенные недостатки этой машины: низкая производи тельность, недостаточная маневренность и необходимость наличия электростанции.
Эти недостатки уже сегодня ставят перед машиностроителями задачу создания более совершенного механизма, производитель
ность которого должна быть значительно увеличена путем распил ки шва 2—4 режущими дисками одновременно. Повысить произ водительность можно также увеличением окружной скорости вра щения диска. Мобильность машины может быть значительно улуч шена путем монтажа ее на тележке, передвигающейся по рельс-
формам, так как рекомендуемое время распилки швов наступает до распалубки покрытия.
Режущим инструментом для распилки швов являются, как было указано, абразивные диски. В 1958 г. Ленинградский филиал ВНИИСтройдормаш провел работу по выбору наиболее устойчи вых составов для их изготовления. Исследованию подвергли раз личные рецепты абразивов, приготовленные из карборунда на
бакелитовой связке. Выяснили, что наилучшую устойчивость дисков при распилке дорожного бетона (на гранитном щебне) обеспечи вает следующий состав абразивной массы:
1) |
карбид кремния (карборунд) черный №24) |
Весовое |
соотношение |
|
2) |
электрокорунд нормальный № 80 |
( |
75:25 |
|
3) |
жидкий бакелит, вязкостью 10—15 сек. |
7%) |
От общего веса карбо- |
|
4) |
алебастр.......................................................... |
6% > |
рунда |
и электроко- |
5) |
пульвербакелит........................................... |
7% ) |
рунда |
|
Технология изготовления абразивных дисков состоит из следую щих операций: приготовление абразивной массы, формование, прес сование и термическая обработка дисков.
Составляющие материалы для приготовления абразивной мас сы загружают в мешалку в порядке, указанном в нумерации
состава смеси. Время перемешивания массы — 6—8 мин. Затем массу протирают через сетку с размерами ячейки в свету 1,5— 2,0 мм и формуют круги с помощью специальных пресс-форм, раз меры которых диктуются требуемым диаметром и толщиной режу щего диска. В пресс-форму укладывают металлическую основу, на
которую с обеих сторон наклеивают абразивную массу, и устанав
ливают под гидравлический пресс мощностью 100—200 т, с помо щью которого уплотняют диски. Термическую обработку дисков
22
осуществляют в электропечи (бакелизаторе) в течение 8 час. с ко
нечной температурой +190°.
Конструктивные размеры швов сжатия и расширения опреде ляются требованиями Технических правил по устройству бетонных покрытий (ВТП 102—57). Следует, однако, иметь в виду, что гео
метрические размеры (ширина и глубина) паза в значительной степени влияют на производительность и стоимость нарезки.
Глубина продольных и поперечных швов сжатия, устраиваемых по типу «ложных швов», для покрытия автомобильных дорог равна
40 мм при условии применения специальных деревянных реек,
устанавливаемых на основание в сечении шва. При отсутствии та ких реек глубину нарезки увеличивают до 50 мм.
Рис. 15. Схема шва расширения: а — до нарезки паза; б — после нарезки паза в затвердевшем бетоне
Ширина швов сжатия зависит от толщины применяемых абра зивных дисков. Так, при дисках толщиной 6 и 8 мм швы получают ся соответственно 6,5 и 8,5 мм.
Для типовых конструкций дорожного бетонного покрытия ши рину швов расширения назначают 20—25 мм, и во всех случаях
она должна точно соответствовать толщине прокладки шва расши рения. Для обеспечения совпадения в плане паза шва с прокладкой:
ее рекомендуется изготавливать конической формы (рис. 15, а). Коничность прокладки и малая толщина бетонного слоя над ней обеспечивают через несколько часов после устройства покрытия образование тонкой трещины точно над прокладкой. При нарезке паза шва расширения эта трещина служит точным ориентиром. Во время нарезки шва расширения абразивным диском прорезают бе тон и частично, на необходимую глубину, деревянную прокладку
(рис. 15, б).
Важнейшим вопросом, технологии нарезных швов является вы
бор времени нарезки, т. е. оптимального интервала между уплот нением бетона в покрытии и нарезкой шва. Очевидно, что из эконо мических соображений, а также в целях предупреждения усадоч ных температурных трещин желательна как можно более ранняя нарезка шва. Однако слишком ранняя нарезка приводит к выкра шиванию бетона, к появлению рваных кромок шва.
В общем случае оптимальное время нарезки швов зависит от целого ряда факторов: температуры воздуха, времени года и дня, скорости ветра, марки и жесткости бетона, водоцементного отно-
23-
тения, свойств и расхода цемента, характеристики крупного запол нителя, методов ухода за бетоном и т. д. Ввиду многообразия этих
•факторов время нарезки определяют для каждого случая отдельно.
В среднем для летних условий швы нужно нарезать через 10-
20 час. после укладки бетонной смеси. При пониженных темпера турах воздуха и пасмурной погоде этот интервал может быть уве личен до 2—3 суток.
Последовательность нарезки швов также диктуется соображе
ниями предупреждения усадочных и температурных деформаций.
С этой целью готовую полосу бетонного покрытия рекомендуется
разрезать поперечными швами по принципу постепенного уменьше ния длины плиты. В соответствии с этим в первую очередь наре зают так называемые «контрольные» швы, делящие бетонную пли ту (т. е. часть бетонной полосы между поперечными швами расши рения) пополам; затем нарезают остальные поперечные швы сжа тия и расширения и в последнюю очередь — продольный шов.
Ввиду того, что продольные швы в гораздо меньшей степени, ■чем поперечные, подвергаются воздействию автомобиля и практи
чески не влияют на скорость его движения, проектом о>рганцзации работ может быть предусмотрено в одном потоке сочетание двух методов устройства швов: нарезки в затвердевшем бетоне попереч
ных швов и обычным способом, т. е. в овежеуложенном бетоне с помощью вибродиска, — продольных.
Как показали испытания нарезчика швов Д-432, его производи тельность по нарезке шва шириной 6 мм и глубиной 40 мм в бетон
ном покрытии |
марки 350 на гранитном щебне составляет 12— |
14 пог. м за 1 |
час чистой, работы. Исходя из этого на дорогах |
1—II категорий на полную 7-метровую ширину со скоростью по тока 175 пог. м в смену нужно иметь 4 машины Д-432. Без нарезки
?1родольного шва достаточно двух машин.
Обслуживающий персонал машины Д-432 состоит из оператора м его помощника — дорожного рабочего IV разряда. Для обеспече ния нарезчика Д-432 энергией нужно иметь одну электростанцию мощностью 50—100 кет и цистерну с водой емкостью 3—4 ,и3 на колесном ходу.
Нарезке шва должна предшествовать тщательная разметка ли нии нарезки и очистки покрытия от песка. В случае ухода за бето ном с помощью лакопленок или эмульсий очистка не нужна. Затем устанавливают направляющий рельс и нарезают шов с постепен
ным заглублением абразивного диска до требуемой отметки. По перечные швы нарезают за два приема, от оси покрытия к кромке.
Во время работы машины диск должен быть надежно закрыт защитным кожухом, а все рабочие должны находиться с тыльной части машины. Во избежание преждевременного износа диска сле дует следить за равномерностью подачи воды к диску и за его
центрировкой.
Небольшая ширина нарезных швов (6—8 мм) обязывает к по вышенному качеству их заполнения, что должно сказаться в более
24

тщательном приготовлении мастики и в усовершенствовании про
цессов заполнения шва.
Дальнейшее уменьшение ширины нарезных швов, к которому следует стремиться, потребует изменения технологии их заполне ния. Это должно найти выражение в поисках других менее вязких составов горячих мастик или в применении эмульсий, а также в заполнении швов под давлением (рис. 16).
Среди факторов, влияющих на стоимость нарезки швов, устраи ваемых в затвердевшем бетоне, решающими являются устойчивость-
карборундовых дисков |
и |
скорость |
нарезки |
шва. Эти факторы |
в свою очередь зависят |
от |
марки и |
возраста |
дорожного бетона; |
Рис. 16. Заполнение швов мастиками под давлением
и прочности породы каменного заполнителя. В общем способ на резки швов в затвердевшем покрытии следует считать экономиче ски целесообразным, так как работоспособность покрытия при
этом повышается, а расходы на его эксплуатацию значительно сни жаются. Как показали опыты, применяя в качестве крупного запол нителя известняковый щебень вместо гранитного, при одинаковой прочности бетона в суточном возрасте можно увеличить скорость резания более чем в 4 раза, а устойчивость диска — более чем
в10 раз.
Втабл. 3 приведены необходимые ресурсы и указана примерная стоимость 1 пог. м шва, нарезанного в затвердевшем бетоне и в свежеуложенном. В основу расчетов принята нарезка швов в бетоне марки 350 в возрасте 1 суток. Глубина шва 40 мм, ширина 6—8 мм."
Ресурсы подсчитаны исходя из скорости потока в смену 175 пог. м
покрытия шириной 7,0 м, при условии применения нового комплек та машин Николаевского завода.
Анализ стоимости нарезки швов в затвердевшем бетоне показы-
25.
Способ устройства швов
В свежеуложенном бе
тоне ........................
Взатвердевшем покры тии из бетона М-350 на гранитном щебне
То же, в бетоне на из вестняковом щебне .
Скорость
устройства шва в смену
350 пог. я
шва
350 лог. м
шва
350 лог. м
шва
Основные |
ресурсы |
|
|
механизмы |
рабочая сила |
|
|
Машина для устройства швов |
Оператор |
—1 |
|
Д-377-1 |
Бетонщики V разр.- 2 |
|
|
|
Дорожные рабочие—3 |
|
|
|
Всего |
6 |
чел. |
Нарезчики швов Д-4-32—4 |
Операторы |
—4 |
|
Карборундовые диски—1 диск |
Электрик |
—1 |
|
на 1b пог. м шва |
Дорожные рабочие—2 |
|
|
Электростанция ПЭС-100 —1 |
Всего |
7 |
чел. |
|
|||
Нарезчики швов Д-432—2 |
Операторы |
—2 |
|
Карборундовые диски-1 диск |
Электрик |
—1 |
|
на 40 пог. м шва |
Дорожные рабочие —1 |
|
|
Электростанция мощностью |
|
|
|
50 кит—1 |
Всего |
4 |
чел. |
|
Таблица
Примерная стой мость 1 пог. м шва без учета стоимости запол нения, руб.—коп
1-26
2-21
1-17
вает, что она может быть снижена путем применения более произ
водительных машин с несколькими режущими дисками и путем уве личения устойчивости дисков за счет изысканий новых рецептов
абразивной массы и новых конструкций дисков.
ИЗОЛЯЦИЯ ТЕМПЕРАТУРНЫХ ШВОВ
Попадание воды через швы в основание покрытия способствует возникновению деформаций земляного полотна. Для того чтобы
предотвратить попадание влаги и избежать засорения швов, их за полняют гидроизолирующими материалами. Материалы для запол
нения швов должны обладать следующими основными качествами: длительное время сохранять упругие свойства;
хорошо сцепляться с боковыми плоскостями смежных бетонных плит;
не пропускать воду; не растрескиваться в холодную погоду;
не вытекать из швов при высоких температурах.
Наиболее распространенными материалами, применяемыми в настоящее время для заполнения швов цементобетонных дорожных
покрытий, являются битумные мастики. Битумные мастики долж ны состоять из 3—4 компонентов, так как смеси из двух компонен
тов, как правило, вытекают из швов в летнее время при температу рах воздуха более 20—25°.
В качестве основных материалов для приготовления мастик сле дует применять:
битум марки 2 или 3, удовлетворяющий требованиям ГОСТа на
битумы дорожные;
минеральный порошок, удовлетворяющий требованиям к запол нителю для асфальтобетона;
асбестовую крошку; отходы резины (крышка или пыль), получаемые при ее реге
нерации.
Мастику приготавливают на базе под наблюдением лаборато
рии, которая принимает готовую продукцию и несет ответствен ность за ее качество. При приготовлении мастики с добавлением резины процесс варки нужно продолжать в течение 2,5—3 час. Это необходимо для того, чтобы резина набухла и произошло лучшее взаимодействие битума и резины.
Перед заливкой швов необходимо подогреть мастику до 160—
170°. Подогревают мастику в передвижных битумных котлах, тща
тельно перемешивая ее во избежание оседания минерального порошка. Примерные составы мастики для заливки швов приве дены в табл. 4.
Центральные лаборатории дорожных' строек должны предвари тельно подбирать несколько составов мастики из местных материа лов, отличающихся количественным расходом составляющих ком понентов. В некоторых случаях в зависимости от свойства материа
лов количество битума может быть уменьшено до 50—45%.
27
|
|
|
'Г а б л и ц а 4 |
|
|
|
|
Температура |
Климати |
|
|
|
размягчения |
ческая зо |
Состав |
Состав |
мастики |
мастики на |
на, где ре |
|
приборе коль |
комендует |
||
|
|
|
цо и шар, |
ся приме |
|
|
|
град. |
нять масти |
ку
1Битума марки 2 — 60% Минерального порошка (известня
ка) - 20% 75-85 III—IV
Асбестовой крошки 6—7-го сорта20 %
2Битума марки 2 — 60% Минерального порошка (известня
ка) — 25% |
60—65 |
11 |
Асбестовой крошки — 10% Резиновой крошки —5%
3Битума марки 2—60% Минерального порошка (извест
няка) — 25% 60-65 н
Асбестовой крошки — 15%
Для заливки швов, нарезанных в твердом бетоне, можно реко
мендовать следующие составы мастик.
Для швов шириной 8—10 м.м.'. |
|
70% |
битума марки 2.................................................................. |
• |
|
резиновой крошки............................... |
5% |
|
минерального порошка.......................................................... |
|
25% |
температура размягчения мастики этого состава на |
58—60° |
|
приборе кольцо и шар.......................................................... |
|
|
Для швов шириной 6 — 8 мя: |
|
83% |
битума марки 2 .............................................................. |
|
|
резиновой крошки.................................................................. |
' |
7% |
минерального порошка................ |
10% |
|
температура размягчения ................................................... |
|
55° |
Основными показателями, |
характеризующими |
свойства мате |
риалов для заполнения швов, являются текучесть при положитель ных температурах от 45' до 50° и растяжимость при низких темпе ратурах. Температуроустойчивость мастики, проверяемая на при боре кольцо и шар, для II климатической зоны должна быть не ни же 60°, а для III и IV зон не ниже 70°. Текучесть (растекаемость) мастики при температуре от 45 до 50° определяют по расплыву ша рика из мастики или по величине сплава мастики по наклонной плоскости.
По первому способу текучесть мастики определяют по измене нию размера шарика из мастики. С этой целью из 150 г мастики изготавливают три шарика весом по 50 г, укладывают их на стек лянную пластинку размером 10 X 15 см, толщиной 3—5 мм и поме
щают в термостат на 1 и на 24 час. Термометр устанавливают на
28