
книги из ГПНТБ / Семко, М. Ф. Обработка резанием электроизоляционных материалов
.pdfТаблица 22
конструктивные размеры и геометрические параметры режущей части цилиндрической винтозубой комплектной фрезы с пластинками из твердого сплава
|
|
|
|
|
|
Размеры, .м.и |
|
|
|
D |
d |
2 |
в в. |
Р |
к |
/И a |
“ п |
|
7 |
75 |
27 |
8 |
30 26 |
2 |
2 |
25 18° |
2 0 ° |
СЛ |
JL о |
90 |
32 |
10 |
|||||||
|
|
|
|
|
|
|
|
|
о |
125 |
40 |
14 |
|
|
|
|
|
|
|
ши
Не более
20—30° 0,05
нон (BiK4) дисковой отрезной фрезы конструкции завода «Электро-
тяжмаш» им. В. И. Ленина (а = 18°, cti=3°, (pi=2°30', ф2=4°, у=5°,
Я.=1Г5°, / л не более 0,1 м м ) .
В условиях индивидуального и мелкосерийного про изводств удобна в эксплуатации универсальная фреза кон струкции ХПИ с отрезными (III) ножами (см. рис. 41).
Для обработки пазов и уступов обычно применяют стандартные дисковые пазовые цельные фрезы из быст рорежущей стали (ГОСТ 3755-59), сборные со вставны ми ножами из быстрорежущей стали (ГОСТ 1669-59) и сборные со вставными ножами, оснащенные пластинка ми из твердых сплавов (ГОСТ 5348-60). Специальные конструкции дисковых фрез из быстрорежущей стали и твердых сплавов принципиально не отличаются от стан дартных.
Угловые фрезы почти всегда делают прямозубыми, принимая за основу конструкции инструментальных угловых фрез по нормалям машиностроения МН 405-60 и МН 2107-61. Углы заточки можно принимать такими же, как у цилиндрических фрез. По технологическим сообра жениям ленточки делают более широкими /л= 0,2н- 0,3 мм. Стружечные канавки у угловых фрез увеличи вать в 'большинстве случаев не следует, так как отвод стружки не затруднен.
Торцовые фрезы применяются для обработки плоско стей, скосов, уступов,.широких канавок, торцов пакетов заготовок из листов или плит твердой электроизоляцни.- В большинстве случаев используются стандартные тор цовые металлорежущие фрезы, но при этом обязательно изменяют геометрию режущей части зубьев. В основном это относится к изменению главных и вспомогательных задних углов. Они должны быть увеличены до 20—25° (главные задние) и 12—15° (вспомогательные задние).
101
Передние углы при обработке вязких и эластичных д и электриков следует назначать равными 8—12°, хрупких-
и твердых — 0—5°. |
Стандартные |
конструкции сборных |
торцовых фрез с |
ножами ыз |
быстрорежущей стали |
(ГОСТ 3474-60, ГОСТ 1092-57, ГОСТ 3876-55) и цельные быстрорежущие торцовые фрезы (ГОСТ 9304-59), а так же специальные конструкции торцовых фрез могут успешно применяться, если они удовлетворяют основным требованиям, изложенным выше. При торцовом фрезе ровании стружка имеет более благоприятные условия схода, чем при цилиндрическом и дисковом фрезерова нии. Однако если стружечные пространства малы и пло хо отделаны, это может стать препятствием нормально му сходу образующейся стружки и приведет к резкому ухудшению качества обработки.
Концевые фрезы применяются для прорезки пазов, канавок, уступов, выемок и др. В большинстве случаев используются цельные н составные фрезы. Цельные де лают из быстрорежущей, а иногда и из малолегированпой стали по ГОСТ 8237-57, составные — из конструкци онной стали и припаянных инструментальных пластинок из быстрорежущей стали (ГОСТ 2379-67) или из твердо го сплава (ГОСТ 2209-66). Зубья этих фрез делают обычно прямыми и реже — винтовыми. Для твердосплав ных винтовых зубьев используют коронки формы № 35 или винтовые пластинки формы № 36. Концевые фрезы работают в стесненных условиях резания и при плохом отводе стружки. Поэтому правильное назначение геомет рических параметров режущей части зубьев и их числа, объема стружечных канавок, направления и угла подъ ема их винтовой линии имеет большое значение.
Увеличивать задние углы у концевых фрез и делать их больше 18—20° не следует из-за снижения прочности режущих кромок и ухудшения условий теплоотвода. Вспомогательный задний угол и вспомогательный угол
вплане должны быть примерно в таких пределах: ai=
=12ч-15°, ф1 = 4ч-6°. Число зубьев, исходя из условий
размещения стружки, следует назначать по возможности меньшим 2—4. В ряде случаев рационально уменьшить в 2 раза число зубьев у стандартных шестиили четы рехзубых концевых фрез путем вышлифовывания. Стру жечные канавки нужно полировать для уменьшения на липания стружки и пыли. С увеличением угла подъема винтовой стружечной канавки улучшается транспорти
102
рование по ней стружки. Но при этом увеличивается пе редний угол, что ухудшает теплоотводящее действие ре жущего клина, интенсифицируется износ. Поэтому угол подъема винтовой линии зуба со не должен быть менее
20° и более 40°. |
При |
обработке |
хрупких |
материалов |
с неадгезирующей |
с |
инструментальным |
материалом |
|
стружкой со = 20-т-30°. |
На вершине |
(«уголке») в месте |
сопряжения главной и вспомогательной режущих .кро мок желательно делать фаску шириной от 0,5 до 3 мм под углом 45° или радиус сопряжения кромок г равным 0,5—2 мм. Это уменьшает интенсивность износа и су щественно улучшает чистоту обработки.
Фасонные фрезы для обработки деталей из пластмасс и других электроизоляционных материалов применяются весьма редко. Зачастую предпочитают разделять одну сложную операцию с применением сложнопрофильного режущего, инструмента на несколько операций с исполь зованием простых однолезвийных инструментов. На не которых электромашиностроительных заводах, например на московском электромеханическом заводе им. Влади мира Ильича, трудоемкий технологический процесс изго товления клиньев пазовой электроизоляцни электрома шин осуществляют с применением фасонных фрез, одно временно разрезающих и срезающих скосы с фасками. Такое совмещение операций повышает точность изделия, обеспечивая достаточно высокую производительность ре зания при удовлетворительной чистоте обработанной по верхности и глубине деструкцированного слоя.
Большинство фасонных фрез делают из быстрорежу щей стали. Твердосплавные фрезы из-за трудоемкости изготовления применяются пока мало, несмотря на боль шие их преимущества но сравнению с фрезами из ин струментальных сталей. Стойкость твердосплавных фрез в несколько десятков раз больше, чем у быстрорежущих и у фрез из малолепированной стали при меньшем (в 2— 4 раза) критерии затупления, а следовательно, лучшем качестве поверхностного слоя изделия.
Целесообразно твердосплавные фрезы с несложным профилем делать с острозаточенными зубьями и больши ми (12—20°) задними .углами. У них выше стойкость и лучше качество обработки. Алмазная заточка значитель но упрощает их изготовление.
При применении острозаточенных и затылованных фасонных фрез с малым числом зубьев и пластинками из
Щ
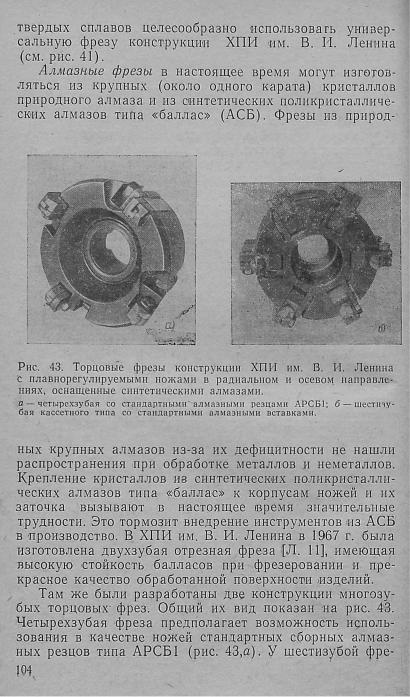
зы кассетного типа применены стандартные с цилиндри ческими державкайи алмазные резцы с припаянными
к ним стандартными вставками АСБ |
(рис. 43,6). |
У обеих этих фрез одинаковый |
диаметр — около |
100 мм. Обе конструкции предполагают возможность бес ступенчатого (плавного) регулирования положения ре жущих кромок ножей как в радиальном, так и в осевом направлениях. Число ножей и диаметр фрез могут быть изменены. Задние и передние углы, а также главные и вспомогательные углы в плане получаются соответст вующей установкой стандартной вставки АР.СБ1 в гнез де ножа. Вставка либо механически закрепляется при хватом, либо припаивается. На обеих фрезах режущая часть ножей имела следующие геометрические пара метры: а=12°, ai=12°, у=0°, ср=,6'0о, 4)1=40°, А =±4° (у четырехзубой) и A,=var (у шестизубой).
Как показал наш опыт, прочность режущей части но жей фрез из балласов вполне достаточна для торцового фрезерования самых различных электроизоляционных материалов, начиная от эластичных термопластов и кон чая асбестоцементом и керамикой. После тщательных лабораторных и производственных испытаний фрезы бы ли внедрены на массовых операциях по обработке плос костей деталей из асбестоцемента и стеклотекстолита на харьковских заводах «Электромашина» и «Электротяжмаш» им. В. И. Ленина.
При алмазном фрезеровании глубина резания огра ничивается сравнительно небольшой длиной режущей ■кромки кристалла АСБ. Глубина фрезерования может быть увеличена в несколько раз за счет разделения при пуска. Обе конструкции балласовых фрез ХПИ позволя ют делить припуск, увеличивая глубину резания до 5— 8 мм. Ножи в пазах шестиили четырехзубой фрезы сме щаются таким образом, что главные режущие кромки последующих зубьев как бы являются продолжением главной режущей кромки первого зуба. При этом первые зубья разделенных групп зубьев выполняют роль фор мирующих профиль обрабатываемой поверхности.
Применение крупнозернистых сверхтвердых инстру ментальных материалов для фрезерования твердой элек троизоляции несомненно будет расширяться, так как оно обеспечивает значительное повышение стойкости инстру мента, увеличение производительности и качества обра ботки, существенно снижает инструментальные расходы.
105
I
4S. СПЕЦИАЛЬНЫЕ И СЛЕСАРНЫЕ ИНСТРУМЕНТЫ
При механической обработке деталей электро машин и аппаратов наряду с широким использованием стандартных режущих инструментов часто применяются и специальные. На предприятиях по изготовлению элек тротехнической и электроизоляционной аппаратуры ши роко применяются «упрощенные» станки и режущие инструменты для резки заготовок, снятия заусенцев у деталей, отлитых под давлением, прессованных, полу ченных экструзией и др.
Резцы для снятия облоя, грата и заусенцев обычно представляют собой стержни прямоугольного сечения из углеродистой или быстрорежущей стали с нулевым пе редним углом, задним — 10—20° и главным углом в пла не— 45°. Резцу сообщают только одну радиальную по дачу (механическую или ручную), и он снимает фаску на торце детали. Подобные упрощенные резцы приме
няются для |
отрезки, прорезки канавок, калибрования |
||||
(расточки) отверстий и др. |
|
|
|
|
|
На Харьковском электромеханическом |
у |
заводе |
для |
зачистки |
|
внутренней цилиндрической поверхности |
деталей |
типа |
крышек |
||
из фенопласта |
на настольном станке |
с |
ножным |
управлением |
применяется резец оригинальной конструкции. Он представляет собой сегмент, одна из плоскостей которого является передней поверх
ностью, а радиус криволинейной части |
(задней поверхности) равен |
|
внутреннему диаметру зачищаемого изделия. |
Резец перемещается |
|
в радиальном направлении и удаляет |
все |
прессовочные налипы, |
грат и другие дефекты.
Широко применяются специальные круглые и призматические фасонные резцы для одновременной проточки канавок, фасонных поверхностей, снятия заусенцев и для отрезки изделия, а также для получения стабильных размеров у отлитых прессованных или выдав ленных деталей. В некоторых случаях для этой цели применяется сборный фасонный резец, протачивающий одновременно базовую ка навку и зачищающий полусферу детали из поликапролактама. Эта несложная операция, выполняемая на очень простом настольном станке, позволила повысить точность отлитой детали с пятого до третьего — третьего «а» класса.
Аналогичные инструменты применяются на сверлиль ных, фрезерных и'других операциях. Особенно разнооб разны и оригинальны специальные конструкции комби нированных «перок» (перовых сверл) для обработки отверстий в неметаллических материалах. Нередко в одном перовом сверле сконцентрировано две — четыре операции. При этом следует иметь в виду, что точность взаимного расположения обработанных таким инстру-
1.06
ментом поверхностей очень высока. Сам по себе ком бинированный режущий инструмент — «перка» весьма прост по конструкции и технологии изготовления. Упро щаются изготовление и заточка комбинированных ин струментов, если они представляют сборную конструкцию.
При опиловке детален из неметаллов и особенно из пласт масс стружечные канавки напильников забиваются налипающей стружкой и пылыо, абразивные наполнители быстро изнашивают насечку напильников из углеродистых и легированных инструмен тальных сталей. При этом рабочему приходится затрачивать боль шее усилие из-за роста силы резания. Хорошие результаты при об работке абразивных диэлектриков обеспечивает применение напиль ников, оснащенных пластинками из твердого сплава с двойной (основной м вспомогательной) насечкой, которая может быть полу чена непосредственно при их прессовании или путем алмазного шли фования. Передний угол основной насечки допускается отрицатель ным, iro он не должен быть больше— 10°, а задний— в пределах
30—35°.
Доводочный инструмент (доводка или шабер) обычно представ-,
ляет собой стальной (сталь |
У10А — У12А), |
закаленный (твердость |
50—62 I-IRC) и шлифованный стержень с |
тщательно доведенными |
|
до 9—10 классов чистоты |
рабочими (торцовыми) поверхностями. |
Угол заострения шаберов чаще всего равен 90°. Обычно их режущие кромки прямолинейны, но они могут быть выпуклыми, а иногда и вогнутыми при обработке наружных, цилиндрических и выпуклых фасонных поверхностей. Острые режущие кромки и рабочие по верхности доводок (шаберов) получают за счет предварительного и окончательного шлифования и последующей их доводки на чугун ных притирах с применением эльборовой (кубический нитрид бора) пасты зернистостью 28/20 или 60/40 (Л. 1]. Чтобы исключить «зава лы» режущих кромок у плоской доводки, ее следует притирать сов местно с чугунным кубиком. Доводка алмазной пастой дает худшие результаты, чем доводка эльборовой пастой. Пасты ГОИ и ВИАМ-2 обеспечивают хорошее качество доводки, но они требуют более про должительной притирки, чем пасты из сверхтвердых инструмен тальных материалов. '
Для ручного строгания ряда нетвердых диэлектриков более эф фективно применение электрических рубанков. Пенопласты, пено полистиролы и мипорты мож'Но строгать обычными ручными не элек трическими рубанками и фуганками с режущими пластинками из инструментальной углеродистой стали, имеющими задний угол 2 0 —
30° и передний 35—50°. Пластинку нужно затачивать и доводить только со стороны заднего угла. Угол заострения при этом должен быть 25—35°.
Г Л А В А Т Р Е Т Ь Я
РЕЖИМЫ РЕЗАНИЯ
При выборе режима резания могут иметь место два случая. Первый включает такие режимы резания, при назначении которых происходит полное использование режущих свойств инструмента и недо-
107
использование при этом мощности станка. Второй объе диняет режимы, которые обеспечивают полное исполь зование мощности станка и частичное использование режущих свойств инструмента. Как исключение может иметь место и третий случай, при котором режимы резания таковы, что полностью используются как режу щие свойства инструмента, так и вся мощность станка.
При расчете режима резания следует руководство ваться только условиями, • определяющими наиболее полное использование режущих свойств инструмента, и сознательно пренебрегать недоиспользуемой мощностью металлорежущих станков, на которых в подавляющем' большинстве случаев в настоящее время обрабатыва ются электроизоляционные материалы.
16. МЕТОДИКА РАСЧЕТА РЕЖИМА РЕЗАНИЯ
Оптимальный .режим резания при обработке электроизоляционных материалов с учетом наиболее полного использования режущих свойств инструмента и обеспечения технологических требований к качеству обработки устанавливается в следующей последова тельности:
1)назначается глубина резания. В подавляющем большинстве практических случаев ее следует выбирать такой, чтобы весь припуск был снят за один проход, если это допускают технологические и другие условия обработки;
2)выбирается подача, исходя главным образом пз условия выполнения технологических требований к чи стоте обработанной поверхности и качеству кромок изделия на выходе из него режущего инструмента;
3)рассчитывается скорость резания. Она больше других влияет на износ режущего инструмента, оказы вает заметное воздействие на состояние поверхностного слоя у нетеплостойких обрабатываемых материалов.
Следует подчеркнуть, что в процессе резания многих электроизоляционных материалов н особенно пластиче ских масс в зависимости «скорость—-стойкость» v(T)
имеет место так называемый «перелом». Графически это
•представляется «переломом» линии v(T). Так, например, при точении гетинакса резцом ВК8 это происходит при
скорости резания 150 |
м/мин ,[Л. 20], при фрезерова |
нии гетинакса фрезой |
ВК4 — при скорости резания |
108
около 650 м/мин [Л. 7]. При токарной обработке высоко прочных стеклопластиков также обнаруживается пере лом в зависимости «подача — стойкость». Расчеты, свя занные с составлением таблиц и построением номограмм режимов резания с «переломом» сложны, трудоемки и почти не отражены в отечественной литературе по обра ботке материалов резанием. Ниже кратко излагается их методика.
Рис. 44. Стойкостная зависимость v(T) с точкой перелома при реза нии неметаллических материалов.
о — при одном значении подачи и глубины резания; 6 — для диапазона подач и глубин резания.
При обработке материалов резанием частная стойкостная зависимость выражается формулой (36). Гра фически, в логарифмической системе координат она ото бражается прямой линией, наклоненной под некоторым отрицательным углом к абсциссе. Тангенс этого угла наклона равен показателю степени т.
Определение скорости резания по такой математиче ской зависимости во всем диапазоне стойкости инстру мента не вызывает затруднения.
Однако при резании многих электроизоляционных материалов, в том числе большинства слоистых пласти ков, асбестоцемента, микалекса и других стойкостная зависимость имеет перелом [Л. 7, 20, 22, 31]. Это озна чает, что при определенных условиях резания наступает такой момент, когда изменяется интенсивность изнаши вания режущего инструмента.
Стойкостная зависимость v (Т) с переломом состоит из двух пересекающихся прямых с разными' углами
109
I
наклона к оси абсцисс (рис. 44). Точка перелома услов но указывает на плавное изменение интенсивности изна шивания режущего инструмента
м/мин-, |
(45) |
Йг,. м/мин, |
(46) |
где Cj и С2— постоянные коэффициенты; Т — стойкость инструмента, мин-, гщ и т 2— показатели относител.ьнрй стойкости.
Величины показателей 1Щ и /п2 определяются танген-. сом угла наклона прямых в диапазоне скоростей реза ния v\—о0 и и0—Vi (см. рис. 44,а). Они устанавливаются путем определения продолжительности резания при раз личных скоростях до принятого критерия затупления инструмента. Устанавливаемая скорость резания в диа пазоне стойкости Тi—Т% всегда определяется прямой или ломаной линией. Любые значения скорости резания при постоянной глубине и неизменной подаче, например для диапазона стойкости 7\—Тп, всегда лежат на лома ной линии В.
Если изменять только глубину резания или только подачу, считая при этом, что зависимости «стойкость — подача» и «стойкость — глубина резания» во всем диа пазоне скоростей резания не имеют перелома, то графи ческая зависимость «скорость — стойкость» будет пере мещаться параллельно самой себе по абсциссе с орди натой Vo-
Таким образом, скорость резания в рассматривае мом диапазоне стойкости инструмента Тi—Т2 рассчиты вается по обобщенным формулам обычного вида (47), (48), соответствующим интенсивности изнашивания для каждого участка ломаной линии:
Д Л Я Vj.— Vo
V - |
С'К |
; |
(47) |
д л я V0 — V2 |
TmisBitx‘ |
|
|
|
|
|
|
V - |
С>К . |
(48) |
|
|
jm %sy2 |
|
|
Всевозможные значения скоростей резания (рис.44,6) . при различных подачах и глубинах резания для диапа зона стойкости Т\—Т2 заключены между положениями линий В и С.
110