
В папку для зачета / CO-MILLING GREEN WOOD CHIPS (Сивков)
.pdf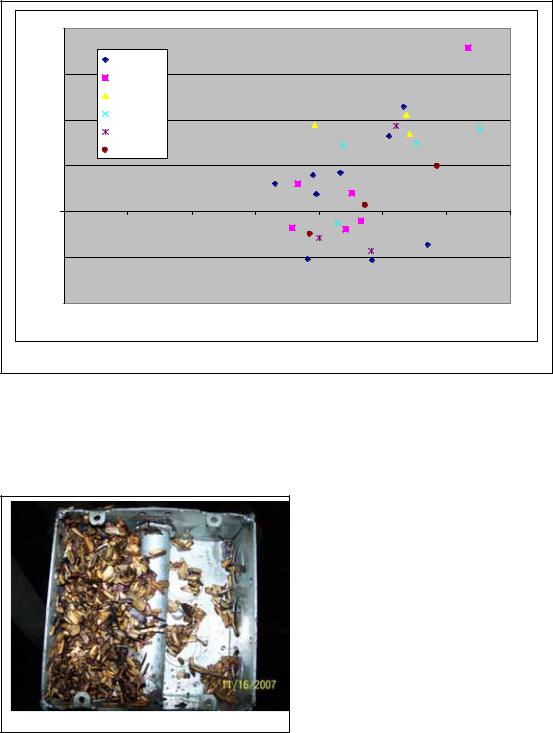
|
4 |
|
|
|
|
|
|
|
|
|
Coal |
|
|
|
|
|
|
|
3 |
10% WT |
|
|
|
|
|
|
|
|
8% WT |
|
|
|
|
|
|
|
2 |
15% WT |
|
|
|
|
|
|
|
10% clean |
|
|
|
|
|
|
|
(%) |
|
|
|
|
|
|
|
|
|
15% clean |
|
|
|
|
|
|
|
Opacity |
1 |
|
|
|
|
|
|
|
|
|
|
|
|
|
|
|
|
|
0 |
|
|
|
|
|
|
|
|
0 |
1 |
2 |
3 |
4 |
5 |
6 |
7 |
|
-1 |
|
|
|
|
|
|
|
|
-2 |
|
|
|
|
|
|
|
|
|
|
|
|
O2 (%) |
|
|
|
Fig 44 Opacity versus O2
Direct Injection
A brief test was conducted of injecting wood chips into the furnace through an existing biomass system previously used for switchgrass tests. In this switchgrass system, a
hammermill grinds the biomass to a relatively fine consistency, and deposits it in a metering bin. The system meters the ground biomass fuel with augers to the inlet of a transport fan. The fuel is then pneumatically conveyed to specially designed burners in the boiler where it burns in suspension.
In August, approximately 1.5 tons of woodchips were processed through the hammermill and stored in the metering bin. Unfortunately, problems at the plant caused the test to be postponed until
November. At that time, the switchgrass system was activated and the material introduced into the furnace at 5% auger speed, an estimated very low rate of about 1500 lb per hour. The unit was at full load, and observations were made of the wood injected inside the furnace.
41
Unfortunately, much of the injected wood fell to the furnace bottom, unburned and essentially un-ignited. The wood inside the furnace could be seen from a lower observation port as a cloud of unburned particles swirling in the lower furnace. The sample in the picture was taken from a heap of wood that accumulated on the furnace bottom.
Some of the difficulty in igniting the wood is probably related to injecting some of the fuel through the lower biomass burner. Switchgrass entering the furnace through the lower burner port had a greater tendency to fall into the bottom ash. Another factor is undoubtedly wood particle size. The unignited particles were nearly all greater than about 1/4” in length. This suggests that the particles of green wood need to be reduced to somewhat less than this size in order to be co-fired successfully by direct injection in this furnace. A similar result was found with direct injection testing of dry wood at Plant Kraft, in which pieces larger than about ¼” fell charred but unburned into the furnace bottom. With proper grinding of the wood, direct injection may offer potential for cofiring wood as well as grass. Green wood has been successfully co-fired in at least one other power plant (Greenidge). However, at Gadsden it will probably require a wood handling system to screen and regrind oversized material
42
CONCLUSIONS
Based on this series of tests, the following conclusions are made:
1.Green wood chips were successfully co-fired in blends with coal at 8%, 10% and 15% by weight at Plant Gadsden Unit 2. Types of wood co-fired included whole tree (with needles) and clean (approximately needle free) chips. Wood energy was about 3% and 5% of the input energy, and represented about 2.1 to 3.5 MW renewable generation at full load.
2.Rain on the fuel pile increased the wood moisture from 50% to up to 65%. The pine needles appeared to absorb the additional moisture more readily than the wood chips.
3.Pine needles in the wood complicate bunker flow, increasing the tendency of the fuel in the bunker to bridge, to rat hole, and to adhere to walls. Whole tree production chips at 15% wood by weight required air hoses to empty the bunkers, which was unacceptable.
4.Mill amps increased by 10% to 15% when co-firing green wood chips, believed caused by buildup of wood in the pulverizer bowl. Mill motors must have sufficient reserve or must be upgraded to carry the additional load to avoid derate.
5.Unit full load operation requires much higher volume of fuel when co-firing, due to the low density and the low heating value of the wood. Mixes of 15% clean chips and whole tree chips by weight required 20% and 30% more volume respectively than coal alone for the same unit load. Coal feeders and pulverizers must have sufficient capacity or must be upgraded to move this much volume to avoid unit derate. The effective storage capacity of the bunker will be reduced by these percentages.
6.Operating stability on automatic controls was the most difficult challenge faced in these tests. Adding green wood chips to the coal reduces the fuel energy density (Btu/volume) and increases fuel moisture. Modifications to the unit control system will be required to establish stable operations.
7.The high moisture content of the green wood resulted in low mill temperatures and increased mill under-bowl pressures. Full load was reduced by about 5% when co-firing 15% green wood due to these mill issues.
8.No blockage of fuel lines or pulverizer riffles was observed. Wood chip size did not appear to be a significant factor in mill operation for the sizes tested.
9.Boiler exit temperatures fell with increased wood in the fuel. This was probably due to the high moisture content of the wood reducing the adiabatic flame temperature.
10.Boiler efficiency was approximately the same when co-firing 10% green wood chips as for coal alone operation. At 15% wood, boiler efficiency was reduced roughly 0.3 to 0.7 percentage points, depending on load. In all cases, increased losses associated with the fuel moisture and ash unburned carbon were offset by the reduction in dry gas losses up the stack.
11.Mercury and sulfur were reduced in the fuel when wood was blended with the coal. NOx was essentially unchanged with co-firing. Data suggest that co-firing these wood chips increased CO at normal plant operating conditions. Co-firing
43
will reduce sulfur emissions. Particulate loadings were measured to be less than with coal alone, while opacity was essentially unchanged.
12. Direct injection of green wood seems to require pieces smaller than ¼”.
RECOMMENDATIONS
Some recommendations are made for further studies
1.Adjustments should be made to the unit control system to verify that the stability problems can be overcome or at least minimized. Stability tests should be run with wood of other moisture contents as well for comparison.
2.With stable operation, determine if the co-firing CO and NOx curves are improved.
3.Run abbreviated tests co-firing sawdust, both dry and green, to separate out those factors on the pulverizer and stability problems that were encountered.
ACKNOWLEDGEMENTS
The authors are grateful for the support of the partners in this study, which included: US Forestry Service USDA Forest Service, National Forests in Alabama; Auburn University; Precision Husky Corporation; USDA Forest Service, Forest Products Lab; USDA Forest Service, Southern Research Station; CAWACO RC&D; Forest Based Economic Development Services; University of Alabama, Center for Economic Development; Auburn University, Forest Products Development Center; Reynolds Wood Products; and Temple-Inland Inc.
The authors would also like to acknowledge help and consultation that helped make this project possible. Gary Dougherty, Ken Snelling and John Cagel were members of the Southern Company test team who were tireless in their instrumenting and testing the boiler. Ron Hunter of the Alabama Power Company Environmental Labs handled the enormous task of analyzing and keeping straight all these samples.
In addition, we received good advice from Don Varner and Larry Monroe. We would also like to thank Loretta Aultman, Philip Garrett, and Hunter and Frances Lowenstein for their contributions to this project.
Above all, this project could not have been completed without the active support and creative ideas of the staff of Plant Gadsden. Our thanks to them and to the plant manager, Wayne Edwards.
44
BIBLIOGRAPHY
Sharer, Michael, “ALABAMA POWER COMPANY GADSDEN STEAM PLANT, UNIT NO. 2, BIO-MASS FUEL PROJECT – DIRTY AIR / ISOKINETIC FUEL SAMPLING”, Innovative Combustion Technologies Report # 2k7-130.
Jeremy Clark, “ALABAMA POWER COMPANY GADSDEN STEAM PLANT, UNIT NO. 2, BIO-MASS FUEL PROJECT – HVT TRAVERSES”, Innovative Combustion Technologies Report # 2K7-130(A).
Sanders Engineering & Analytical Services; Particulate Emissions Test Results for Alabama Power Company Gadsden Steam Plant Unit 2, November 8, 2007.
Boylan, Doug, Zemo, Bill, and Eastis, Jack, “Switchgrass Co-firing at Alabama Power Company’s Plant Gadsden – Final Report,” Southern Company Report, August, 2001.
45
Appendix 1: Wood Properties
Sample Date |
Oct |
30-Oct |
8-Nov |
8-Nov |
11-Nov |
Aug |
|
|
August |
|
|
|
|
middle of |
|
|
|
|
Long Fiber |
|
|
|
|
Fluor |
cut pile |
|
|
|
|
|
|
|
|
|
test chips |
|
|
|
|
Whole |
|
|
|
|
|
Green |
Test 30/31 |
|
Yellow |
Long Fiber |
|
|
||
|
|
Short |
Short fiber |
Long |
Production |
Short Fiber |
Whole Tree |
Tree test |
|
Long Fiber |
Dry Basis |
|
Whole |
WT |
w/needles |
Chip |
Clean |
Chips |
22 |
production |
Clean |
Ash, Dry |
|
2.6 |
1.54 |
0.72 |
1.05 |
0.79 |
0.51 |
1.25 |
0.82 |
0.45 |
Heat of Combustion, Dry |
8990 |
8856 |
8459 |
8549 |
8842 |
8522 |
8584 |
8640 |
8316 |
|
Carbon, Dry Basis |
55.59 |
54.93 |
54.54 |
55.93 |
64.75 |
53.6 |
56.55 |
56.73 |
54.81 |
|
Hydrogen, Dry Basis |
5.31 |
5.53 |
5.55 |
4.65 |
2.25 |
5.85 |
5.07 |
4.44 |
5.28 |
|
Nitrogen, Dry Basis |
0.97 |
0.98 |
0.92 |
1.09 |
1.48 |
0.82 |
1.18 |
1.01 |
0.9 |
|
Oxygen, Dry Basis |
35.31 |
36.96 |
38.24 |
37.22 |
30.71 |
39.21 |
35.89 |
36.97 |
38.55 |
|
Carbon Fixed, Dry |
26.68 |
22.55 |
21.14 |
22.03 |
21.72 |
20.8 |
22.51 |
22.01 |
20.35 |
|
Volatiles, Dry Basis |
70.72 |
75.91 |
78.14 |
76.92 |
77.49 |
78.69 |
76.24 |
77.17 |
79.2 |
|
Sulfur, Dry Basis |
0.22 |
0.06 |
0.03 |
0.06 |
0.02 |
0.01 |
0.06 |
0.03 |
0.01 |
|
As Received |
|
|
|
|
|
|
|
|
|
|
Moisture, Total |
43.41 |
52.1 |
48.46 |
58.64 |
66.08 |
51.54 |
56.99 |
53.84 |
56.03 |
|
Ash, As Received |
1.47 |
0.74 |
0.37 |
0.43 |
0.27 |
0.25 |
0.54 |
0.38 |
0.2 |
|
Heat of Combustion, As |
5087 |
4242 |
4360 |
3536 |
2999 |
4130 |
3692 |
3988 |
3657 |
|
Carbon, As Received |
31.46 |
26.31 |
28.11 |
23.13 |
21.96 |
25.97 |
24.32 |
26.19 |
24.1 |
|
Hydrogen, As Received |
3 |
2.65 |
2.86 |
1.92 |
0.76 |
2.83 |
2.18 |
2.05 |
2.32 |
|
Nitrogen, As Received |
0.55 |
0.47 |
0.47 |
0.45 |
0.5 |
0.4 |
0.51 |
0.47 |
0.4 |
|
Oxygen, As Received |
19.98 |
17.7 |
19.71 |
15.39 |
10.42 |
19 |
15.44 |
17.07 |
16.95 |
|
Carbon Fixed, As Recei |
15.1 |
10.8 |
10.9 |
9.11 |
7.37 |
10.08 |
9.68 |
10.16 |
8.95 |
|
Volatiles, As Received |
40.02 |
36.36 |
40.27 |
31.81 |
26.28 |
38.13 |
32.79 |
35.62 |
34.82 |
|
Sulfur, As Received |
0.12 |
0.03 |
0.02 |
0.02 |
0.01 |
0 |
0.03 |
0.01 |
0 |
|
General |
|
|
|
|
|
|
|
|
|
|
Heat of Combustion, MA |
9230 |
8995 |
8520 |
8640 |
8912 |
8566 |
8693 |
8711 |
8354 |
|
Sulfur, lbs/mmBTU |
0.245 |
0.068 |
0.035 |
0.07 |
0.023 |
0.012 |
0.07 |
0.035 |
0.012 |
|
|
|
|
|
|
|
|
|
|
|
|
|
|
|
|
|
|
|
|
|
|
|
|
|
|
|
|
|
|
|
|
|
|
Ignited as |
Oxide |
|
|
|
|
|
|
|
|
|
Aluminum O |
XRF |
|
|
|
|
|
|
11.72 |
5.9 |
12.62 |
Barium Oxid |
XRF |
|
|
|
|
|
|
0.15 |
0.13 |
0.445 |
Calcium Oxi |
XRF |
|
|
|
|
|
|
18.23 |
24.29 |
24.97 |
Iron Oxide, I |
XRF |
|
|
|
|
|
|
4.35 |
1.99 |
5.86 |
Magnesium |
XRF |
|
|
|
|
|
|
4.98 |
7.3 |
6.54 |
Phosphorus |
XRF |
|
|
|
|
|
|
3.15 |
4.89 |
3.06 |
Potassium |
XRF |
|
|
|
|
|
|
11.27 |
17.83 |
12.02 |
Silicon Oxid |
XRF |
|
|
|
|
|
|
33.3 |
24.35 |
23.39 |
Sodium Oxi |
XRF |
|
|
|
|
|
|
0.9 |
0.47 |
0.38 |
Sulfur Trioxi |
XRF |
|
|
|
|
|
|
11.49 |
12.67 |
10.09 |
Strontium O |
XRF |
|
|
|
|
|
|
0.086 |
0.065 |
0.137 |
Titanium Ox |
XRF |
|
|
|
|
|
|
0.44 |
0.12 |
0.53 |
46
Appendix 2: Measured Wood Mix Densities
|
fiber |
needles |
% |
sp |
|
Wood |
gravity |
||
Wood |
short fiber |
clean |
100% |
0.359558 |
|
|
|
|
0.379305 |
|
|
|
|
0.327962 |
|
|
|
|
|
|
|
Whole |
|
|
|
long fiber |
tree |
100% |
0.291101 |
|
|
|
|
0.25029 |
|
|
|
|
0.258189 |
|
|
|
|
|
|
|
Whole |
|
|
|
production |
tree |
100% |
0.273986 |
|
|
|
|
0.297683 |
|
|
|
|
0.367457 |
|
|
|
|
|
Blends |
0% Wood |
|
0% |
0.872986 |
|
|
|
|
|
|
short fiber |
clean |
10% |
0.820326 |
|
|
|
|
|
|
short fiber |
clean |
15% |
0.790047 |
47

Appendix 3: Plant Gadsden Mill Performance Curve
48
Appendix 3 – Sanders Engineering Report
49
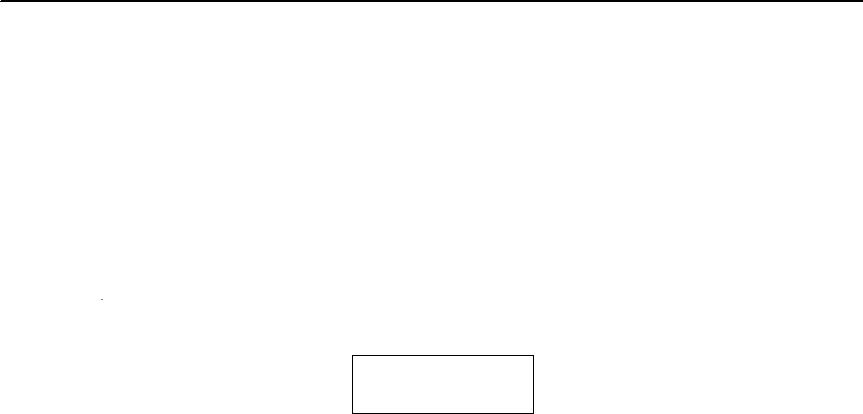
50
|
|
|
|
|
|
|
|
|
|
|
|
|
|
|
|
|
|
|
|
|
% wood |
|
|
|
0 |
0 |
0 |
0 |
0 |
0 |
10 |
10 |
10 |
10 |
10 |
10 |
8 |
8 |
|
|
Test # |
|
|
|
1 |
2 |
3 |
4 |
5 |
6 |
7 |
8 |
9 |
10 |
11 |
12 |
13 |
14 |
|
|
Dry Basis |
|
|
|
0 |
|
|
|
|
|
0 |
|
|
|
|
|
0 |
|
|
|
Ash, Dry |
|
|
|
12.28 |
13.04 |
12.51 |
15.49 |
14.53 |
15.21 |
14.69 |
10.63 |
11.02 |
10.21 |
12.46 |
9.54 |
12.77 |
13.04 |
|
|
Heat of Combustion, Dry |
|
|
12930 |
12990 |
13046 |
12557 |
12824 |
12711 |
12381 |
13118 |
12962 |
13221 |
12669 |
13363 |
12948 |
12613 |
|
|
|
Carbon, Dry Basis |
|
|
72.07 |
71.91 |
72.13 |
69.74 |
70.92 |
70.35 |
68.89 |
72.99 |
71.25 |
73.13 |
69.94 |
73.52 |
71.33 |
69.67 |
|
|
|
Hydrogen, Dry Basis |
|
|
4.8 |
4.82 |
4.83 |
4.64 |
4.67 |
4.67 |
4.65 |
4.97 |
4.92 |
5.02 |
4.86 |
4.96 |
4.79 |
4.83 |
|
|
|
Nitrogen, Dry Basis |
|
|
1.51 |
1.45 |
1.49 |
1.42 |
1.43 |
1.45 |
1.45 |
1.49 |
1.46 |
1.52 |
1.45 |
1.53 |
1.38 |
1.42 |
|
|
|
Oxygen, Dry Basis |
|
|
7.7 |
7.19 |
7.42 |
7.1 |
6.65 |
6.8 |
8.79 |
8.43 |
9.77 |
8.49 |
9.42 |
8.91 |
8.36 |
9.64 |
|
|
|
Carbon Fixed, Dry |
|
|
56.29 |
55.3 |
55.81 |
54.46 |
55.67 |
55.51 |
52.2 |
56.15 |
54.65 |
55.97 |
53.17 |
56.56 |
55.94 |
53.67 |
|
|
|
Volatiles, Dry Basis |
|
|
31.43 |
31.66 |
31.68 |
30.05 |
29.8 |
29.28 |
33.11 |
33.22 |
34.33 |
33.82 |
34.37 |
33.9 |
31.29 |
33.29 |
|
|
|
Sulfur, Dry Basis |
|
|
1.64 |
1.59 |
1.62 |
1.61 |
1.8 |
1.52 |
1.53 |
1.49 |
1.58 |
1.63 |
1.87 |
1.54 |
1.37 |
1.4 |
|
|
|
As Received |
|
|
|
|
|
|
|
|
14.28 |
|
|
|
|
|
0 |
|
|
|
|
Moisture, Total |
|
|
5.46 |
6.77 |
5.89 |
7.96 |
6.62 |
6.22 |
9.67 |
9.3 |
10.62 |
8.39 |
8.9 |
6.75 |
9.92 |
10.74 |
|
|
|
Ash, As Received |
|
|
11.61 |
12.16 |
11.77 |
14.26 |
13.57 |
14.26 |
13.27 |
9.64 |
9.85 |
9.35 |
11.35 |
8.9 |
11.5 |
11.64 |
|
|
|
Heat of Combustion, As |
|
Received |
12224 |
12111 |
12278 |
11557 |
11975 |
11920 |
11184 |
11898 |
11585 |
12112 |
11541 |
12461 |
11664 |
11258 |
|
|
|
AppendixCarbon, As Received5 Fuel |
|
Analyses |
(cont)68.13 |
67.04 |
67.88 |
64.19 |
66.23 |
65.97 |
62.23 |
66.2 |
63.68 |
66.99 |
63.72 |
68.56 |
64.25 |
62.19 |
|
|
|
|
|
|||||||||||||||||
|
Hydrogen, As Received |
|
|
4.54 |
4.49 |
4.55 |
4.27 |
4.36 |
4.38 |
4.2 |
4.51 |
4.4 |
4.6 |
4.43 |
4.63 |
4.31 |
4.31 |
|
|
|
Nitrogen, As Received |
|
|
1.43 |
1.35 |
1.4 |
1.31 |
1.34 |
1.36 |
1.31 |
1.35 |
1.3 |
1.39 |
1.32 |
1.43 |
1.24 |
1.27 |
|
|
|
Oxygen, As Received |
|
|
7.28 |
6.7 |
6.98 |
6.53 |
6.21 |
6.38 |
7.94 |
7.65 |
8.73 |
7.78 |
8.58 |
8.31 |
7.53 |
8.6 |
|
|
|
Carbon Fixed, As Received |
53.22 |
51.56 |
52.52 |
50.12 |
51.98 |
52.06 |
47.15 |
50.93 |
48.85 |
51.27 |
48.44 |
52.74 |
50.39 |
47.91 |
|
|||
|
Volatiles, As Received |
|
|
29.71 |
29.52 |
29.81 |
27.66 |
27.83 |
27.46 |
29.91 |
30.13 |
30.68 |
30.98 |
31.31 |
31.61 |
28.19 |
29.71 |
|
|
|
Sulfur, As Received |
|
|
1.55 |
1.48 |
1.52 |
1.48 |
1.68 |
1.43 |
1.38 |
1.35 |
1.41 |
1.49 |
1.7 |
1.44 |
1.23 |
1.25 |
|
|
|
General |
|
|
|
|
|
|
|
|
|
|
|
|
|
|
|
|
|
|
|
Heat of Combustion, MAF |
|
|
14938 |
14911 |
14859 |
15004 |
14991 |
14513 |
14678 |
14567 |
14724 |
14472 |
14772 |
14844 |
14504 |
|
||
|
Sulfur, lbs/mmBTU |
|
|
14740 |
1.224 |
1.242 |
1.282 |
1.404 |
1.196 |
1.236 |
1.136 |
1.219 |
1.233 |
1.476 |
1.152 |
1.058 |
1.11 |
|
|
|
|
|
|
|
1.268 |
|
|
|
|
|
|
|
|
|
|
|
|
|
|
|
|
|
|
|
|
|
|
|
|
|
|
|
|
|
|
|
|
|
|
|
|
|
|
|
|
|
|
|
|
|
|
|
|
|
|
|
|
|
|
|
Aluminum |
Oxide, Ignited |
|
Basis |
27.73 |
|
|
|
|
|
21.39 |
|
|
|
|
|
27.73 |
|
|
|
Barium Oxide, Ignited |
|
|
0.35 |
|
|
|
|
|
0.345 |
|
|
|
|
|
0.304 |
|
|
|
|
Calcium Oxide, Ignited |
Basis |
1.42 |
|
|
|
|
|
10.07 |
|
|
|
|
|
1.04 |
|
|
||
|
Iron Oxide, Ignited Basis |
|
|
12.48 |
|
|
|
|
|
9.91 |
|
|
|
|
|
9.59 |
|
|
|
|
Magnesium Oxide, Ignited |
|
Basis |
1.13 |
|
|
|
|
|
6.2 |
|
|
|
|
|
0.98 |
|
|
|
|
Phosphorus Oxide, Ignited Basis |
0.64 |
|
|
|
|
|
0.24 |
|
|
|
|
|
0.45 |
|
|
|||
|
Potassium Oxide, Ignited Basis |
2.78 |
|
|
|
|
|
2.17 |
|
|
|
|
|
2.89 |
|
|
|||
|
Silicon Oxide, Ignited Basis |
50.48 |
|
|
|
|
|
44.08 |
|
|
|
|
|
53.98 |
|
|
|||
|
Sodium Oxide, Ignited |
|
|
0.28 |
|
|
|
|
|
0.22 |
|
|
|
|
|
0.17 |
|
|
|
|
Sulfur Trioxide, Ignited |
|
|
1.26 |
|
|
|
|
|
4.44 |
|
|
|
|
|
1.09 |
|
|
|
|
Strontium Oxide, Ignited |
|
Basis |
0.144 |
|
|
|
|
|
0.067 |
|
|
|
|
|
0.098 |
|
|
|
|
Titanium Oxide, Ignited |
|
|
1.31 |
|
|
|
|
|
0.9 |
|
|
|
|
|
1.25 |
|
|
|
|
|
|
|
|
|
|
|
|
|
|
|
|
|
|
|
|
|
|
|
Appendix 5 Fuel Analyses