
В папку для зачета / CO-MILLING GREEN WOOD CHIPS (Сивков)
.pdf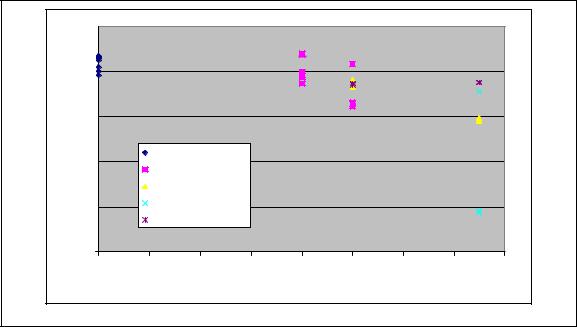
at 8% wood, but began to decrease at 10%. At 15% wood, maximum load was reduced by about 5% on average. These observed load reduction results are compatible with the mill performance curve prediction of derate due to increased moisture.
|
600 |
|
|
|
|
|
|
|
|
flow (klb/hr) |
550 |
|
|
|
|
|
|
|
|
500 |
|
|
|
|
|
|
|
|
|
steam |
|
|
|
|
|
|
|
|
|
|
coal |
|
|
|
|
|
|
|
|
load |
450 |
|
|
|
|
|
|
|
|
short fiber whole tree |
|
|
|
|
|
|
|||
|
|
|
|
|
|
|
|||
Maximum |
|
long fiber whole tree |
|
|
|
|
|
|
|
400 |
production |
|
|
|
|
|
|
||
short fiber clean chip |
|
|
|
|
|
|
|||
|
|
|
|
|
|
|
|||
|
350 |
|
|
|
|
|
|
|
|
|
0 |
2 |
4 |
6 |
8 |
10 |
12 |
14 |
16 |
% wood
Figure 20 Maximum load steam flow versus percent wood
Unit Control and Stability
The largest problem encountered in co-firing the wood chips in these tests involved controlling the unit. From the first co-firing test run at 10% wood chips, there was difficulty in getting the unit to settle out in automatic operation. Main steam pressure and mill feeders tended to swing widely, and took up to an hour or more to steady out at a test condition. Even at stable operation, the steam pressure swung more than desired. If a mill was taken out or cut back abruptly due to amps or mill temperature, this caused the unit main steam to swing broadly. Many of the early tests were involved in finding how to restore stability.
One suggestion for the source of the problems was that the lining of wood in the pulverizer bowl broke off periodically and went into the furnace in a large burst. This had been proposed as a potential problem by engineers at another Southern Company plant considering co-firing. During these tests, the mill potentiometers monitored roller displacement and therefore a measure of the thickness of material lining the bowl over time. The data from the mill pots plotted with time (Figure 21) show how the roller displacement increases with increased wood lining the bowl. However, the curves are very steady, varying in the order of only 2 or 3 hundredths of an inch. The wood cofiring roller displacement curves appear at least as stable as the curve for coal alone firing.
21

|
4.7 |
|
|
|
|
|
4.6 |
|
|
|
|
(") |
4.5 |
|
|
|
|
displacement |
|
|
|
|
|
4.4 |
|
|
|
|
|
4.3 |
|
|
full coal alone |
|
|
roller |
|
|
full 10% |
|
|
|
|
|
|
||
|
|
|
full 15% |
|
|
relative |
4.2 |
|
|
|
|
|
|
|
|
||
|
|
|
|
|
|
|
4.1 |
|
|
|
|
|
4 |
|
|
|
|
|
01 |
5 |
10 |
15 |
20 |
|
|
|
time |
|
|
Figure 21 Full load roller displacement for 15%, 10%, and 0% wood co-firing
Another potential instability cause was the possibility that the fuel was poorly mixed in the bunker, and that the mills were experiencing “slugs” of wood. Sudden high wood concentration would choke the mill with difficult-to-process wood, and would reduce the fuel heating value of that flow. The roller displacement data seem fairly steady over time, however, suggesting a fairly constant wood/coal ratio. Also, to address this, special tests were run with the mills’ feeders locked in constant flow, and MW unit output was recorded. With 10% and 15% wood, MW varied by only ±2%. With coal alone, MW variation was about half that, at about ±1%. Therefore, since the unit ran with fairly steady MW output while the feeders were in fixed manual control, fuel property variation did not seem to be the problem.
Main
Steam
Press
MW
Feeders
Cycle Time
Fig: 22 Typical feeder and steam pressure data – shown here for 15% wood – scale magnified
These fixed feeder tests did suggest, however, that the settings of the automatic controls required some tuning to accommodate the varying fuel properties of coal and coal wood mixes. In automatic, the unit instrumentation controls on changes in the main steam pressure to ±10psi. When the pressure strays from the set point, the controls adjust the fuel feeder to appropriately change fuel flow to return the main steam pressure to the desired level. At steady condition, the feeder and the main steam pressure cycle approximately 180° out of phase with each other (Figure 22). The amplitudes of the pressure and feeder cycles are magnified here for clarity. The time between cycles is a measure of the responsiveness of the system.
With green wood chips mixed with coal, the Btu per volume of the blended fuel drops
22

substantially. As a result, a given change of the feeder speed by the controller results in a smaller change in fuel Btu to the furnace than with coal alone, slowing the system response. It is further slowed by an increased volume of material in the mill due to the wood. Because of the high moisture and relatively large size and grinding properties of the wood chips, wood and coal are believed to accumulate in the mill, further slowing its response to change. This is shown in Figure 23 below, which gives a plot of feedersteam pressure cycle time as a function of percentage of wood co-firing.
As expected, full load shows the greatest impact of wood on response time. With no wood, the cycle time is about 200-300 seconds and is independent of load. At 10% wood, the full load cycle time approximately doubles to about 600 seconds, while full load response at 15% wood is about 900 seconds. These results confirm that the response of the controls when co-firing wood chips is considerably slowed. The effect also occurs at lower loads, but to a lesser degree.
|
1000 |
|
|
|
|
|
|
|
|
|
900 |
full load |
|
|
|
|
|
|
|
|
(65MW) |
|
|
|
|
|
|
|
|
|
800 |
low load |
|
|
|
|
|
|
|
|
(41MW) |
|
|
|
|
|
|
|
|
(s) |
700 |
50MW |
|
|
|
|
|
|
|
evening |
|
|
|
|
|
|
|
||
Time |
|
Poly. (full load |
|
|
|
|
|
|
|
600 |
(65MW)) |
|
|
|
|
|
|
|
|
Poly. (low |
|
|
|
|
|
|
|
||
Cycle |
|
|
|
|
|
|
|
|
|
500 |
load (41MW)) |
|
|
|
|
|
|
|
|
Poly. (50MW |
|
|
|
|
|
|
|
||
|
|
|
|
|
|
|
|
||
400 |
evening) |
|
|
|
|
|
|
|
|
Control |
|
|
|
|
|
|
|
||
|
|
|
|
|
|
|
|
||
300 |
|
|
|
|
|
|
|
|
|
|
|
|
|
|
|
|
|
|
|
|
200 |
|
|
|
|
|
|
|
|
|
100 |
|
|
|
|
|
|
|
|
|
0 |
|
|
|
|
|
|
|
|
|
0 |
2 |
4 |
6 |
8 |
10 |
12 |
14 |
16 |
% Wood
Figure 23: Feeder cycle time response
These issues were very much a surprise, as no such problems were indicated during tests co-firing green wood sawdust at Plant Gadsden Units 1 and 2 in 2004. The Unit 2 overall boiler control system, however, was newly installed, upgrading from a manual controller using pneumatic / hydraulic controllers to a digital controller using PLC’s and automatic digital valve positioners. This provided for much quicker response times to changes in the boiler outputs and the controls sensitivity played a major factor in producing a less stable boiler control.
Apparently finer tuning was required on the newly installed controls. Problems were noted shortly after the co-firing tests when changing conditions with coal alone. To address this, gain was turned down on the boiler master response to main steam and on the mill hot air damper response to mill temperature. A brief test in April 2008 following these control modifications showed no further control stability problems when co-firing 10% green high moisture wood.
23

Boiler Gas and Air Temperatures
Combustion gas temperatures from the furnace and combustion air temperatures from the air heater dropped substantially with the addition of wood chips to the fuel. This can be seen in Figure 24, in which full load economizer exit gas temperature is plotted versus boiler O2, with wood percentage as a parameter. The temperature data are somewhat scattered, but the drawn curves are linear fits to the actual data. Highest exit gas temperatures were obtained with coal alone. Fuel with 8% to 10% wood was about 20 to 25 °F cooler. With 15% wood, the furnace exit gas temperature was between 20 and 40 °F below the coal alone results. Similar decreases were seen with the temperatures of the hot air (combustion air) exiting the air heaters. This air helps to heat the mills and dry the fuel in the pulverizers, so decreasing the hot air temperatures has implications for mill performance.
Temperature |
400 |
|
|
|
|
390 |
|
|
|
|
|
380 |
|
|
|
|
|
370 |
|
|
|
|
|
Exit |
|
|
|
|
|
360 |
|
|
|
|
|
Gas |
350 |
|
|
Coal |
|
|
|
8 - 10% Wood |
|
||
Load |
340 |
|
|
|
|
|
|
15% Wood |
|
||
|
|
Linear (Coal) |
|
||
330 |
|
|
|
||
|
|
|
|
||
Full |
|
|
Linear (8 - 10% Wood) |
|
|
|
|
Linear (15% Wood) |
|
||
320 |
|
|
|
||
|
|
|
|
||
|
|
|
|
|
|
|
3.5 |
4.5 |
5.5 |
6.5 |
7.5 |
|
|
|
O2 Wet (%) |
|
|
Fig. 24 Full Load Economizer Exit Gas Temperatures
The reason for the drop in gas and air temperatures is believed to be a large drop in adiabatic flame temperature (AFT) with the addition of the high moisture and low Btu wood chips. AFT is the calculated maximum flame temperature that fuel combustion products can attain in ideal conditions of no excess air and no heat losses. Calculated AFT for this coal with various percentages of green wood chips is shown in Figure 25. AFT drops linearly from 3,086 F for coal alone to 2,947 F at 15% wood, a drop of 149°F.
24

|
3500 |
|
|
|
|
|
|
|
|
|
|
|
3000 |
|
|
|
|
|
|
|
|
|
|
|
2500 |
|
|
|
|
|
|
|
|
|
|
Temperture |
2000 |
Adiabatic Flame |
|
|
|
|
|
|
|
|
|
|
Boiler Exit |
|
|
|
|
|
|
|
|
|
|
1500 |
AH Hot Air |
|
|
|
|
|
|
|
|
|
|
|
|
|
|
|
|
|
|
|
|
|
|
|
1000 |
|
|
|
|
|
|
|
|
|
|
|
500 |
|
|
|
|
|
|
|
|
|
|
|
0 |
|
|
|
|
|
|
|
|
|
|
|
0% |
10% |
20% |
30% |
40% |
50% |
60% |
70% |
80% |
90% |
100% |
|
|
|
|
|
|
% Wood |
|
|
|
|
|
Fig 25. Calculated flame temperature and measured gas and air temperatures as function of wood percentage
25

Efficiency
Results of boiler efficiency calculations are summarized with the other test results in Table 1 above. The efficiency results were calculated in accordance with the heat loss method, in which individual losses of energy from the boiler are determined. Boiler efficiency is calculated by subtracting the sum of the losses from 100%. It is generally recognized that this method gives a more accurate determination than an input - output method, in which relatively small errors in fuel or steam flow rate can result in large efficiency errors. It also allows better understanding of boiler efficiency changes. The sections below discuss in more detail the individual losses and their impact on the resulting efficiency.
Efficiency - Dry Gas Losses
Dry gas losses represent the sensible heat of the dry flue gas that exits the stack. A plot of these losses with economizer outlet O2 is shown in Figure 26. As expected, the dry gas losses increased with increased combustion air.
|
9.5 |
|
|
|
|
|
|
|
|
|
9 |
|
|
|
|
|
|
|
|
(%) |
8.5 |
|
|
|
|
|
|
|
|
|
|
|
|
|
|
|
|
|
|
Loss |
8 |
|
|
|
|
|
|
|
|
|
|
|
|
|
|
|
0 full |
|
|
Gas |
7.5 |
|
|
|
|
|
|
|
|
|
|
|
|
|
|
10% full |
|
||
Dry |
|
|
|
|
|
|
|
|
|
|
|
|
|
|
|
|
8% full |
|
|
|
7 |
|
|
|
|
|
|
|
|
|
|
|
|
|
|
|
15% full |
|
|
|
|
|
|
|
|
|
|
|
|
|
6.5 |
|
|
|
|
|
|
10% clean |
|
|
|
|
|
|
|
|
15% clean |
|
|
|
|
|
|
|
|
|
|
|
|
|
6 |
|
|
|
|
|
|
Linear (0 full) |
|
|
|
|
|
|
|
|
|
|
|
|
3 |
3.5 |
4 |
4.5 |
5 |
5.5 |
6 |
6.5 |
7 |
Economizer Out O2
Fig 26. Dry gas losses – full load for whole tree (WT) and clean chips
26

Dry gas losses were lower when co-firing wood chips than for coal alone operation. The stack exit gas temperature is greatly reduced when the high moisture wood is part of the fuel mix. This reduces the energy loss up the stack. The linear curve on Figure 26 is a plot for the coal only points. The 15% wood/coal mix had the lowest dry gas loss, about 0.8% less than coal alone. The 10% wood tests were in general between the two. Why the 8% wood tests had such low dry gas losses is not understood. Similar results were obtained testing at low load conditions.
Efficiency - Unburned Combustible Losses
Bottom Ash - Ash samples were taken from the furnace bottom in each test to determine the amount of unburned material and how it changed with test configuration. These ash samples were analyzed in the laboratory to determine carbon content. From these data, the unburned combustible content of the bottom ash was determined. Unburned combustible data for the bottom ash are shown plotted with Economizer Outlet O2 in Figure 27.
At full load, the carbon content of the bottom ash for coal only was fairly consistent, running between 5% and 8%, and is represented with the linear curve in the figure. In general, co-firing 10% wood chips gave bottom ash with about the same or slightly higher carbon content. For 15% wood chips, the unburned carbon in bottom ash tended
|
18 |
0 full |
|
|
|
|
|
|
|
|
|
|
|
|
|
|
|
|
|
Load |
16 |
10% full |
|
|
|
|
|
|
|
14 |
8% full |
|
|
|
|
|
|
|
|
15% full |
|
|
|
|
|
|
|
||
Full |
|
|
|
|
|
|
|
|
|
12 |
10% clean |
|
|
|
|
|
|
|
|
(%) |
10 |
15% clean |
|
|
|
|
|
|
|
Ash Carbon |
Linear (0 full) |
|
|
|
|
|
|
|
|
|
|
|
|
|
|
|
|
||
8 |
|
|
|
|
|
|
|
|
|
6 |
|
|
|
|
|
|
|
|
|
Bottom |
4 |
|
|
|
|
|
|
|
|
|
|
|
|
|
|
|
|
|
|
|
2 |
|
|
|
|
|
|
|
|
|
0 |
|
|
|
|
|
|
|
|
|
3 |
3.5 |
4 |
4.5 |
5 |
5.5 |
6 |
6.5 |
7 |
|
|
|
|
Economizer Out O2 (%) |
|
|
|
Figure 27: Bottom ash unburned carbon – full load
27

to run higher, between 8% and 15%. This could be visually observed in the samples during the testing. In many of the 15% tests, small pieces of wood and of pine needles could be seen in the bottom ash sample. Those samples often gave off the smell of wet burning wood.
Figure 28 shows that at low load, inclusion of wood in the fuel had a more pronounced effect on unburned carbon in bottom ash. The coal alone bottom ash carbon ranged between about 5 and 10%. For 10% whole tree wood, there was no difference between the two. However, for 10% clean chips, the carbon in bottom ash rose to about 14%. At 15% wood chips, for both whole tree and clean chips, there was a fairly large increase in bottom ash carbon, averaging about 20% carbon in bottom ash.
|
35 |
0 low |
|
|
|
|
|
|
|
|
|
|
|
|
|
|
|
|
|
|
30 |
10% low |
|
|
|
|
|
|
|
Load |
8% low |
|
|
|
|
|
|
|
|
|
|
|
|
|
|
|
|
||
|
15% low |
|
|
|
|
|
|
|
|
Low |
25 |
|
|
|
|
|
|
|
|
10% clean |
|
|
|
|
|
|
|
||
|
|
|
|
|
|
|
|
||
|
15% clean |
|
|
|
|
|
|
|
|
(%) |
20 |
|
|
|
|
|
|
|
|
Linear (0 low) |
|
|
|
|
|
|
|
||
Carbon |
|
|
|
|
|
|
|
||
|
|
|
|
|
|
|
|
||
15 |
|
|
|
|
|
|
|
|
|
Ash |
10 |
|
|
|
|
|
|
|
|
Bottom |
|
|
|
|
|
|
|
|
|
5 |
|
|
|
|
|
|
|
|
|
|
|
|
|
|
|
|
|
|
|
|
0 |
|
|
|
|
|
|
|
|
|
3 |
3.5 |
4 |
4.5 |
5 |
5.5 |
6 |
6.5 |
7 |
Economizer Out O2 (%)
Fig 28: Bottom ash unburned carbon – low load
Although these values appear alarming, they are somewhat mitigated by the bottom ash being only 20% of the overall ash. This has effect of reducing the impact of this unburned carbon on the overall boiler efficiency calculation. If the bottom ash has 20% unburned carbon, this is about 13% carbon higher than for coal alone. If all additional carbon loss were attributed totally to the wood itself, this represents less than one half percent of the input wood.
There is an effect on the appearance of the bottom ash with 15% green wood co-firing. Some consideration should be given to whether material in the bottom ash will float in the ash pond and whether this is a problem.
28

Fly Ash – The results of the unburned carbon in the fly ash are shown in Figure 29.
The unburned carbon-in-fly ash measurements for full load were essentially the same for coal alone and for all wood concentrations and wood type. The data show, as expected, a gradual increase in unburned carbon as O2 is decreased, and this was seen for both full and low load tests. For both 10% and 15% wood co-firing, the fly ash carbon was about the same as for coal alone. There may be a slight increase in wood co-firing fly ash carbon compared with coal at the lowest O2 levels.
|
2 5 |
|
|
|
|
|
0 |
fu ll |
|
|
|
|
|
|
|
|
|||
|
|
|
|
|
|
|
1 0 % |
fu ll |
|
Load |
2 0 |
|
|
|
|
|
8 % |
fu ll |
|
|
|
|
|
|
1 5 % |
fu ll |
|||
|
|
|
|
|
|
||||
|
|
|
|
|
|
1 0 % |
c le a n |
||
Full |
|
|
|
|
|
|
|||
|
|
|
|
|
|
1 5 % |
c le a n |
||
Fly Ash (%) |
1 5 |
|
|
|
|
|
|||
|
|
|
|
|
|
|
|
||
1 0 |
|
|
|
|
|
|
|
|
|
Carbon in |
|
|
|
|
|
|
|
|
|
5 |
|
|
|
|
|
|
|
|
|
|
|
|
|
|
|
|
|
|
|
|
0 |
|
|
|
|
|
|
|
|
|
3 . 5 |
4 |
4 . 5 |
5 |
5 . 5 |
6 |
6 . 5 |
7 |
7 . 5 |
|
|
|
|
E c o n o m i z e r O u t O 2 |
|
|
|
Figure 29: Fly ash carbon (%) versus O2 (%) - full load for whole tree (WT) and clean chips
Similar results were seen for low load operation as well (Figure 30). Fly ash carbon content for 8% -10% co-firing was essentially the same as coal alone. For 15% wood at
|
3 0 |
|
|
|
|
|
|
|
|
|
|
|
|
|
|
0 lo w |
|
|
2 5 |
|
|
|
|
|
1 0 % |
l o w |
Load |
|
|
|
|
|
8 % |
l o w |
|
|
|
|
|
|
|
|||
|
|
|
|
|
|
1 5 % |
l o w |
|
|
|
|
|
|
|
1 0 % |
c le a n |
|
Low |
2 0 |
|
|
|
|
|
||
|
|
|
|
|
1 5 % |
c le a n |
||
|
|
|
|
|
|
|||
(%) |
|
|
|
|
|
|
||
|
|
|
|
|
|
|
|
|
in Fly Ash |
1 5 |
|
|
|
|
|
|
|
1 0 |
|
|
|
|
|
|
|
|
Carbon |
|
|
|
|
|
|
|
|
5 |
|
|
|
|
|
|
|
|
|
|
|
|
|
|
|
|
|
|
0 |
|
|
|
|
|
|
|
|
3 . 5 |
4 |
4 . 5 |
5 |
5 . 5 |
6 |
6 . 5 |
7 |
|
|
|
|
E c o n o m i z e r O u t O 2 ( % ) |
|
|
|
Fig 30: Fly ash carbon (%) versus O2 (%) - low load for whole tree (WT) and clean chips
29

low load, the unburned carbon in fly ash was between 0% and 2% higher than for coal alone.
Combined Unburned Combustible Loss – The fly ash and bottom ash unburned carbon measurements were combined into a single value, based upon an assumed 80% fly ash/20% bottom ash split. This combined value was used to calculate boiler efficiency loss due to unburned combustibles.
The boiler efficiency losses associated with full load unburned combustibles are shown in Figure 31. The losses increase as combustion air decreases, with the increase becoming steeper between 4% and 5% O2.
At full load, the unburned combustible loss appears to be slightly higher for co-firing wood than for firing coal alone. Over most of the O2 range for full load, the combustible loss for co-firing 10% wood of either type and co-firing 15% whole tree chips is about 0.1 to 0.2 percentage points higher than for coal alone. Combustible losses with 15% clean chips were measured to be a little higher, between 0.2 and 0.6 percentage points higher than coal alone. Normal commercial full load operation is reflected by an economizer outlet O2 of about 4.0%. This value is based on dry gas analysis, and is roughly equal to a plant wet O2 reading of about 3.0% O2.
|
4 |
|
|
|
|
|
|
|
|
3.5 |
|
|
|
|
|
0 full |
|
|
|
|
|
|
|
10% full |
|
|
(%) |
|
|
|
|
|
|
|
|
3 |
|
|
|
|
|
8% full |
|
|
Loss |
|
|
|
|
|
|
15% full |
|
2.5 |
|
|
|
|
|
10% clean |
|
|
Carbon |
2 |
|
|
|
|
|
15% clean |
|
|
|
|
|
|
|
|
||
|
|
|
|
|
|
|
|
|
Unburned |
1.5 |
|
|
|
|
|
|
|
1 |
|
|
|
|
|
|
|
|
|
|
|
|
|
|
|
|
|
|
0.5 |
|
|
|
|
|
|
|
|
0 |
|
|
|
|
|
|
|
|
3.5 |
4 |
4.5 |
5 |
5.5 |
6 |
6.5 |
7 |
Economizer Out O2 (%)
Figure 31: Unburned carbon loss – full load for whole tree (WT) and clean chips
30