
- •Лекция 1
- •Цели и задачи курса
- •Контрольные вопросы к лекции 1.
- •Лекция 4.
- •Конструкторско-технологические разновидности ПП.
- •Конструкционные материалы для изготовления ПП
- •Основные конструкционные материалы для производства ПП
- •Основные составляющие слоистых пластиков для изготовления ПП
- •Лекция 5
- •Основные этапы изготовления ПП
- •Ручная химическая и электрохимическая подготовка поверхности проводится в ваннах с различными растворами при покачивании заготовок и последующей их промывкой, а механизированная – на автооператорных линиях модульного типа по заданной программе.
- •Увеличение шероховатости диэлектрических поверхностей и клеевых композиций (слоев адгезива, например, в виде акрилбутадиенстирольного каучука) достигается механической (гидроабразивной) или химической обработкой.
- •Продолжение табл.5.1.
- •Окончание табл.5.1.
- •Для придания диэлектрику способности к металлизации (то есть каталитических свойств) и обеспечения адгезии химически осаждаемого металла на диэлектрик, производят сенсибилизацию и активацию его поверхности.
- •Таблица 5.2.
- •Сравнительные характеристики пленок химически осажденной
- •и гальванической меди
- •* По отношению к фольге, получаемой прокаткой, и соответствует 2-м перегибам на 180
- •Однако, гальваническое осаждение возможно только на электропроводящие поверхности и разброс по толщине осаждаемых пленок заметно больший, чем при химическом осаждении.
- •Офсетная печать состоит в изготовлении печатной формы, на поверхности которой формируется рисунок слоя (рис. 5.1).
- •Рис.5.1. Схема установки офсетной печати: 1 – диэлектрик; 2 – медная фольга; 3 – основание установки; 4 – печатная форма; 5 – офсетный цилиндр; 6 – валик для нанесения краски; 7 – краска; 8 – прижимной валик.
- •Рис.5.2. Принцип трафаретной печати: 1 – рама; 2 – фиксатор подложки; 3 – фольгированный диэлектрик; 4 – основание; 5 – трафаретная краска; 6 – трафарет;7 – напечатанный рисунок; 8 – ракель.
- •Проявление, окрашивание и задубливание жидких фоторезистов проводят в конвейерных струйных установках модульного типа, оснащенных устройствами подачи растворов с их фильтрацией и регулировкой давления; роликовым конвейером, соединяющим все модули.
- •Контроль качества изготовленной ПП осуществляют визуально и с помощью специальных контрольно-измерительных средств, при этом определяют:
- •Основные технологии изготовления печатных плат.
- •В зависимости от технологий формирования слоев металлизации и получения рисунка коммутирующих элементов различают следующие технологии изготовления ПП:
- •Лекция 6
- •Общие сведения о сборке и монтаже электронных устройств
- •Подготовка конструктивов к сборке и монтажу ячеек ЭВС
- •Лекция 9
- •Контактолы в виде ненаполненных полимеров.
- •Лекция 10
- •Лекция 11
- •Специфика регулировки микропроцессорных устройств
- •Герметизирующие конструкции и методы их герметизации. Технологические требования, предъявляемые к качеству герметизации.
- •Герметизирующие конструкции с учетом методов герметизации можно условно разделить на две группы:
- •Вне зависимости от метода герметизации для обеспечения качества и эффективности защиты электронных устройств (ЭУ) необходимо выполнять следующие условия:
- •- процессы приготовления герметизирующих смесей не должны загрязнять исходные материалы. Растворители в составе защитных лаков и эмалей следует удалять полностью при полимеризации полученных покрытий.
- •Выбор оптимального технологического процесса (ТП) герметизации ЭВС зависит от степени устойчивости изделия к влиянию климатических факторов, от условий эксплуатации изделия и от экономических факторов.
- •Общая структурная схема реализации ТП герметизации ЭРК, сборочных единиц и ЭУ приведена на рис.14.1. Важно рассмотреть входящие в состав ТП основные его этапы.
- •При входном контроле оцениваются технологические и другие характеристики и (или) параметры используемых материалов и конструктивов герметизируемых изделий.
- •Удаление влаги из герметизируемых изделий происходит путем их нагрева выше температуры кипения воды. В этом случае влага перемещается от зоны с большей влажностью к менее увлажненной и от зоны с большей температурой к менее нагретой.
- •В зависимости от способа нагрева герметизируемых изделий различают: конвекционную, радиационную и индукционную сушки.
- •Защиту изделий органическими материалами также осуществляют разными методами, например, пропиткой и обволакиванием, заливкой, опрессовыванием, переносом капли и др.
- •Рис. 14.4. Схема установки для вакуумной пропитки
- •Рис. 14.5. Схема установки для нанесения полимерных покрытий в электростатическом поле.
- •Рис. 14.6. Примеры герметизации с использованием капсул и жидкого компаунда (а); прессованной таблетки (б): 1 - капсула; 2 – основание платы микросборки; 3 - герметизирующий компаунд; 4 - выводы
- •Основные этапы ТП изготовления вакуумплотного корпуса, общая сборка и монтаж, а также герметизация конструктивов МЭА в корпусе приведены на рис.14.8.
- •Рис. 14.8. Основные этапы изготовления деталей вакуумплотных корпусов, сборка, монтаж и герметизация в них.
- •Рис. 14.9. Методы получения герметичных выводов в герметичных корпусах: а - сваркой; б - пайкой; в - спеканием.
- •Стабилизация параметров внутрикорпусной среды.
- •- испытание диэлектрика на пробивное напряжение проводится до и после термоциклов и циклов пребывания во влажной атмосфере. На тестовые образцы подается синусоидальное напряжение 1500 В частотой 50 Гц в течение 60 с;
- •После испытаний изделия проверяют на наличие: обрывов и коротких замыканий токопроводящих элементов; следов коррозии; различных дефектов в полимерных покрытиях.
- •Контрольные вопросы к лекциям 14 и 16.
- •1. Какие критерии используют при выборе материалов для герметизации?
- •2. Составьте типовую структуру ТП герметизации ЭВС и их конструктивов.
- •3. Приведите примеры и дайте технологическую характеристику органическим материалам, укажите методы герметизации с их применением.
- •4. Охарактеризуйте неорганические материалы и приведите примеры их использования для герметизации изделий электронной техники.
- •5. Какие и с какой целью осуществляют подготовительные операции перед герметизацией с использованием органических и неорганических материалов?
- •6. Какие методы пропитки применяют в производстве МЭА? Каким образом они реализуются?
- •7. Как производят заливку и обволакивание изделий?
- •8. Перечислите основные виды изделий, опрессовываемых пластмассой. Изложите суть изготовления монолитных пластмассовых корпусов.
- •9. В каких случаях используют и как осуществляют герметизацию изделий в металлополимерных корпусах?
- •10. Назовите методы герметизации изделий в вакуумплотных корпусах и кратко их охарактеризуйте.
- •11. Изобразите схему основных этапов герметизации МЭА в вакуумплотных корпусах с учетом изготовления корпусов, сборки и монтажа конструктивов в корпусе и контроля герметичности.
- •12. С какой целью и какими средствами обеспечивают стабилизацию параметров внутрикорпусной среды?
- •13. Как контролируют качество герметизации?
- •15. Составьте последовательность разных видов испытаний герметизирующих полимерных покрытий на ПП ответственных конструкций.
- •Лекция 15
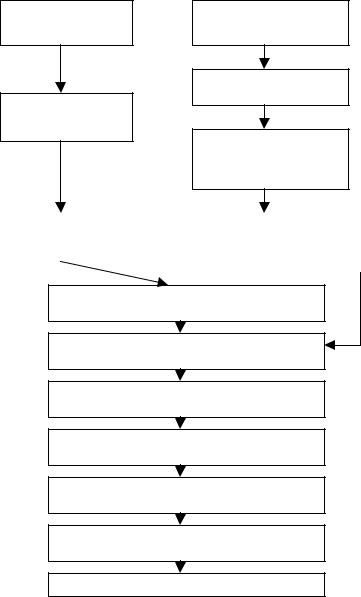
15
Изготовление
основания корпуса
Проверка
герметичности
Изготовление крышки
Нанесение
технологического
Герметичное крепление
проходных изоляторов, откачных трубок
Нанесение |
|
Проверка |
|
|
технологического |
|
герметичности |
|
|
покрытия |
|
|
|
|
|
|
|
|
|
Сборка и монтаж конструктивов МЭА в корпусе
Размещение прокладок и др. деталей;
закрепление крышки на основании корпуса
Герметизация корпуса пайкой, сваркой
или другими методами
Термовакуумная тренировка и проверка
герметичности
Заполнение корпуса инертным газом или др.
и заделка штенгеля
Контроль качества герметизации
Отделка, маркировка
Рис. 14.8. Основные этапы изготовления деталей вакуумплотных корпусов, сборка, монтаж и герметизация в них.
Герметизацию герметичных корпусов выполняют с применением уплотнительной резиновой прокладки и стяжки болтами с последующей защитой герметиком (клеем) мест уплотнения; прокладки и проволоки с пайкой; различных способов сварки (рис. 14.11) и др. Метод а (см. рис. 14. 11) применяется для аппаратуры с малым сроком хранения. При изготовлении МЭА наиболее универсальным и надежным методом является герметизация паянным либо сварным соединением. При реализации метода б (см. рис. 14.11) в зазор между крышкой и основанием сначала укладывается прокладка из термостойкой резины, которая препятствует проникновению паров припоя и флюса в герметизируемый объем во время герметизации пайкой. На прокладку по всему периметру накладывается стальная
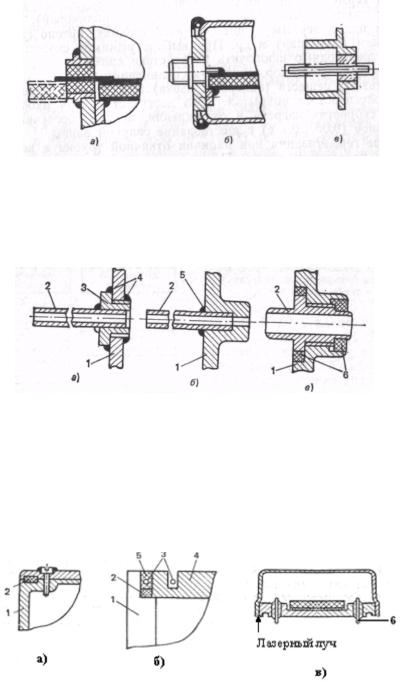
16
Рис. 14.9. Методы получения герметичных выводов в герметичных корпусах: а - сваркой; б - пайкой; в - спеканием.
Рис. 14.10. Методы закрепления узлов откачки: а - наиболее часто используемый вариант; б - применяется в литых корпусах; в - в блоках со значительным внутренним объёмом: 1– корпус; 2 – трубка (штенгель); 3 – втулка; 4 – паянный шов; 5
– сварной шов; 6– компаунд.
Рис. 14.11. Методы герметизации вакуумплотных корпусов: с применением прокладок (уплотнителей), стяжки болтами и герметика (а); прокладки, проволоки и пайки (б); лазерной сварки (в); 1- корпус; 2 - уплотняющая прокладка; 3 - проволока; 4 - крышка; 5 - припой; 6 - гермоввод.
17
облуженная проволока, диаметр которой выбирается на 0,1...0,2 мм меньше ширины зазора в пазах основания и крышки корпуса. Пайка выполняется низкотемпературным припоем (ПОС-61 или др.) с применением соответствующего флюса. Для удобства разгерметизации на концах проволоки делаются петли, которые выводятся из зазора через предусмотренный паз в крышке корпуса. Для герметизации корпусов широко используются также методы сварки: контактная (конденсаторная, роликовая), электронным или лазерным лучом (см. рис. 14.11, в), аргоно-дуговая, давлением (холодная) и др. При выборе режимов сварки плавлением необходимо исключить воздействие сильного нагрева на ЭРК и образование пор в сварном соединении за счет выделения газообразных веществ (водорода, азота и др.) из основного материала и технологических покрытий. Это достигается работой на малых скоростях нагрева и охлаждения объекта, либо за счет использования импульсного режима сварки.
После герметизации при наличии откачной трубки в корпусе создают разрежение до 1,3 Па и проверяют его герметичность. Если корпус герметичен, то его заполняют сухим азотом или аргоном до давления 0,1...0,15 МПа. Откачную трубку обжимают и запаивают или заваривают (заделка штенгеля, см. рис. 14.8).
Заготовки металлостеклянных корпусов изготавливают прессованием стекломассы (порошок стекла и пластификатор) с последующим спеканием в графитовых или керамических тиглях в конвейерных печах с контролируемой атмосферой. Металлическая арматура, используемая для гермовыводов и последующего герметичного соединения отдельных их частей, а также деталей металлостеклянных корпусов, изготавливается обычно из ковара, имеющего ТКЛР, близкий к ТКЛР стекла. Арматура заливается стекломассой с последующим прессованием, либо спекается со стеклом в специальных формах в результате частичного растворения оксида металла и стекла.
Керамические корпуса отличаются от металлостеклянных большей химической устойчивостью и легко поддаются металлизации. Их изготавливают аналогично металлостеклянным, но с использованием специальных токопроводящих паст на основе Мо-Мn, благородных металлов, которые наносят на детали через трафареты. После высокотемпературного (700...1000°С) обжига на поверхности керамики образуется металлический слой, обеспечивающий герметичное соединение основания с металлической крышкой корпуса пайкой. Соединения деталей получают также при помощи стеклоцемента.
Стабилизация параметров внутрикорпусной среды.
Стабилизация параметров внутрикорпусной среды (давления, состава и его содержания, температуры и др.) необходима для стабильной и надежной работы МЭА в экстремальных условиях и для избежания преждевременной разгерметизации корпусов, и, тем самым, различных видов отказов изделий. Средствами стабилизации параметров внут-
рикорпусной среды являются: термообработка конструктивов перед их сборкой и монтажом в герметичном корпусе (с целью удаления паров воды и других составляющих газовыделений); проведение самого процесса герметизации в строго контролируемых условиях (например в специальных скафандрах с осушенной атмосферой); продувка внутреннего объёма изделия осушенным инертным газом перед его герметизацией; размещение во внутреннем объёме герметизируемого изделия расчётного количества предварительно обезвоженного влагопоглотителя - геттера (цеолита, силикагеля и др.); проведение термовакуумной тренировки собранных и смонтированных в корпусе всех конструктивов МЭА в контролируемом и заданном для данного изделия режиме.
Контроль качества герметизации.
Важным условием получения высокого качества герметизации является хорошо организованный технический контроль этих работ. Он включает систематическую провер-
18
ку состояния герметизируемых материалов, автоматическое поддержание оптимальных технологических режимов отдельных операций, операционный и выходной контроль, а также определение герметичности. Методы выходного контроля разделяются на две группы: визуальный (обычно с применением микроскопов) и аналитический (с применением специального оборудования для поиска возможных течей, оценки остаточных напряжений в герметизирующем шве, оценки функционирования изделия и др.). К первой группе относятся: контроль внешнего вида на отсутствие пор, трещин, сколов, газовых и других инородных включений в месте герметизации, определение геометрических параметров и др. при необходимости.
Для оценки герметичности разработан ряд методов (жидкостной, массспектрометрический, галогенный, радиоактивный, электронного захвата и др.), каждый из которых характеризуется своей чувствительностью. Выбор метода контроля определяется требованиями к степени герметичности, направлением и величиной газовой нагрузки на оболочку, веществами для контроля (пробными), допустимыми к применению, и экономичностью.
Процедура испытания строится на последовательной отбраковке изделий с большими течами и переходе на контроль малых течей. Определение больших течей с чувствительностью 10-6 м3·Па/с производится жидкостным методом. Контролируемое изделие погружается в жидкость (керосин либо этиленгликоль), находящуюся в рабочей емкости с прозрачными стенками, затем создают в емкости разрежение (давление 0,3 – 3 Па) и по окончании откачивания воздуха из емкости наблюдают появление пузырьков из корпуса изделия. По скорости образования и размерам пузырьков судят о нахождении течи и ее размерах.
Более высокой чувствительностью (порядка 5·10-13 м3·Па/с) обладает массспектрометрический метод. Он основан на обнаружении, с помощью массспектрометрической установки, газа (гелия), вытекающего из корпуса, содержащего течи и предварительно заполненного этим газом под давлением (4...6)·105 Па. Выпускаемые гелиевые течеискатели (ПТИ-7,-9,-10, ТИМ-1П и др.) имеют возможность работы с различными пробными газами, легко встраиваются в автоматические установки разбраковки изделий по герметичности. Повышение производительности достигается введением микропроцессорного управления.
Испытания позволяют в реальных (или имитирующих реальные) условиях оценить и прогнозировать качество герметизации. Выбор режимов испытаний определяется техническими требованиями к изделию. Для ПП (с защитным покрытием) ответственных конструкций используются следующие разновидности испытаний, осуществляемые в последовательности:
-температурный цикл (-55°С, в течение 30 мин; 25°С - 10...15 мин; +85 °С - 30 мин; 25°С - 10...15 мин), который повторяется 3 - 5 раз;
-проверка сопротивления изоляции на тестовых образцах после10 - 14 циклов
пребывания в условиях влажной атмосферы. Во время циклов к контактным площадкам прикладывается постоянное напряжение 100 В;
- испытание диэлектрика на пробивное напряжение проводится до и после термоциклов и циклов пребывания во влажной атмосфере. На тестовые образцы подается синусоидальное напряжение 1500 В частотой 50 Гц в течение 60 с;
-контроль вибростойкости при воздействии ударных нагрузок, низко- и высокочастотных вибраций. После каждого испытания покрытие исследуется на растрескивание;
-испытания на износоустойчивость и гибкость.