
- •Лекция 1
- •Цели и задачи курса
- •Контрольные вопросы к лекции 1.
- •Лекция 4.
- •Конструкторско-технологические разновидности ПП.
- •Конструкционные материалы для изготовления ПП
- •Основные конструкционные материалы для производства ПП
- •Основные составляющие слоистых пластиков для изготовления ПП
- •Лекция 5
- •Основные этапы изготовления ПП
- •Ручная химическая и электрохимическая подготовка поверхности проводится в ваннах с различными растворами при покачивании заготовок и последующей их промывкой, а механизированная – на автооператорных линиях модульного типа по заданной программе.
- •Увеличение шероховатости диэлектрических поверхностей и клеевых композиций (слоев адгезива, например, в виде акрилбутадиенстирольного каучука) достигается механической (гидроабразивной) или химической обработкой.
- •Продолжение табл.5.1.
- •Окончание табл.5.1.
- •Для придания диэлектрику способности к металлизации (то есть каталитических свойств) и обеспечения адгезии химически осаждаемого металла на диэлектрик, производят сенсибилизацию и активацию его поверхности.
- •Таблица 5.2.
- •Сравнительные характеристики пленок химически осажденной
- •и гальванической меди
- •* По отношению к фольге, получаемой прокаткой, и соответствует 2-м перегибам на 180
- •Однако, гальваническое осаждение возможно только на электропроводящие поверхности и разброс по толщине осаждаемых пленок заметно больший, чем при химическом осаждении.
- •Офсетная печать состоит в изготовлении печатной формы, на поверхности которой формируется рисунок слоя (рис. 5.1).
- •Рис.5.1. Схема установки офсетной печати: 1 – диэлектрик; 2 – медная фольга; 3 – основание установки; 4 – печатная форма; 5 – офсетный цилиндр; 6 – валик для нанесения краски; 7 – краска; 8 – прижимной валик.
- •Рис.5.2. Принцип трафаретной печати: 1 – рама; 2 – фиксатор подложки; 3 – фольгированный диэлектрик; 4 – основание; 5 – трафаретная краска; 6 – трафарет;7 – напечатанный рисунок; 8 – ракель.
- •Проявление, окрашивание и задубливание жидких фоторезистов проводят в конвейерных струйных установках модульного типа, оснащенных устройствами подачи растворов с их фильтрацией и регулировкой давления; роликовым конвейером, соединяющим все модули.
- •Контроль качества изготовленной ПП осуществляют визуально и с помощью специальных контрольно-измерительных средств, при этом определяют:
- •Основные технологии изготовления печатных плат.
- •В зависимости от технологий формирования слоев металлизации и получения рисунка коммутирующих элементов различают следующие технологии изготовления ПП:
- •Лекция 6
- •Общие сведения о сборке и монтаже электронных устройств
- •Подготовка конструктивов к сборке и монтажу ячеек ЭВС
- •Лекция 9
- •Контактолы в виде ненаполненных полимеров.
- •Лекция 10
- •Лекция 11
- •Специфика регулировки микропроцессорных устройств
- •Герметизирующие конструкции и методы их герметизации. Технологические требования, предъявляемые к качеству герметизации.
- •Герметизирующие конструкции с учетом методов герметизации можно условно разделить на две группы:
- •Вне зависимости от метода герметизации для обеспечения качества и эффективности защиты электронных устройств (ЭУ) необходимо выполнять следующие условия:
- •- процессы приготовления герметизирующих смесей не должны загрязнять исходные материалы. Растворители в составе защитных лаков и эмалей следует удалять полностью при полимеризации полученных покрытий.
- •Выбор оптимального технологического процесса (ТП) герметизации ЭВС зависит от степени устойчивости изделия к влиянию климатических факторов, от условий эксплуатации изделия и от экономических факторов.
- •Общая структурная схема реализации ТП герметизации ЭРК, сборочных единиц и ЭУ приведена на рис.14.1. Важно рассмотреть входящие в состав ТП основные его этапы.
- •При входном контроле оцениваются технологические и другие характеристики и (или) параметры используемых материалов и конструктивов герметизируемых изделий.
- •Удаление влаги из герметизируемых изделий происходит путем их нагрева выше температуры кипения воды. В этом случае влага перемещается от зоны с большей влажностью к менее увлажненной и от зоны с большей температурой к менее нагретой.
- •В зависимости от способа нагрева герметизируемых изделий различают: конвекционную, радиационную и индукционную сушки.
- •Защиту изделий органическими материалами также осуществляют разными методами, например, пропиткой и обволакиванием, заливкой, опрессовыванием, переносом капли и др.
- •Рис. 14.4. Схема установки для вакуумной пропитки
- •Рис. 14.5. Схема установки для нанесения полимерных покрытий в электростатическом поле.
- •Рис. 14.6. Примеры герметизации с использованием капсул и жидкого компаунда (а); прессованной таблетки (б): 1 - капсула; 2 – основание платы микросборки; 3 - герметизирующий компаунд; 4 - выводы
- •Основные этапы ТП изготовления вакуумплотного корпуса, общая сборка и монтаж, а также герметизация конструктивов МЭА в корпусе приведены на рис.14.8.
- •Рис. 14.8. Основные этапы изготовления деталей вакуумплотных корпусов, сборка, монтаж и герметизация в них.
- •Рис. 14.9. Методы получения герметичных выводов в герметичных корпусах: а - сваркой; б - пайкой; в - спеканием.
- •Стабилизация параметров внутрикорпусной среды.
- •- испытание диэлектрика на пробивное напряжение проводится до и после термоциклов и циклов пребывания во влажной атмосфере. На тестовые образцы подается синусоидальное напряжение 1500 В частотой 50 Гц в течение 60 с;
- •После испытаний изделия проверяют на наличие: обрывов и коротких замыканий токопроводящих элементов; следов коррозии; различных дефектов в полимерных покрытиях.
- •Контрольные вопросы к лекциям 14 и 16.
- •1. Какие критерии используют при выборе материалов для герметизации?
- •2. Составьте типовую структуру ТП герметизации ЭВС и их конструктивов.
- •3. Приведите примеры и дайте технологическую характеристику органическим материалам, укажите методы герметизации с их применением.
- •4. Охарактеризуйте неорганические материалы и приведите примеры их использования для герметизации изделий электронной техники.
- •5. Какие и с какой целью осуществляют подготовительные операции перед герметизацией с использованием органических и неорганических материалов?
- •6. Какие методы пропитки применяют в производстве МЭА? Каким образом они реализуются?
- •7. Как производят заливку и обволакивание изделий?
- •8. Перечислите основные виды изделий, опрессовываемых пластмассой. Изложите суть изготовления монолитных пластмассовых корпусов.
- •9. В каких случаях используют и как осуществляют герметизацию изделий в металлополимерных корпусах?
- •10. Назовите методы герметизации изделий в вакуумплотных корпусах и кратко их охарактеризуйте.
- •11. Изобразите схему основных этапов герметизации МЭА в вакуумплотных корпусах с учетом изготовления корпусов, сборки и монтажа конструктивов в корпусе и контроля герметичности.
- •12. С какой целью и какими средствами обеспечивают стабилизацию параметров внутрикорпусной среды?
- •13. Как контролируют качество герметизации?
- •15. Составьте последовательность разных видов испытаний герметизирующих полимерных покрытий на ПП ответственных конструкций.
- •Лекция 15
1
Лекция 7. Лекция 8.
Общие сведения о сборке и монтаже электронных устройств
Технологический процесс (ТП) сборки электронных устройств (ЭУ) реализуется с целью получения механических соединений между конструктивами ЭУ для придания неподвижности конструктивам на этапе монтажа и (или) для обеспечения прочностных свойств изделия на весь его жизненный цикл. В то же время ТП монтажа реализуется с целью создания электрических соединений между конструктивами ЭУ. Прочность электрических соединений, как правило, нормирована для каждого метода монтажа. Сборка всегда предшествует монтажу, но на отдельных этапах всего ТП изготовления ЭУ(например, общая механическая сборка конструктивов в корпусе разъемной, негерметичной конструкции) может осуществляться без монтажа. В то же время монтаж без сборки не осуществляется, даже если в некоторых ТП сборка и монтаж выполняются совместно (например, при монтаже БИС с шариковыми выводами).
Повторяемость (цикличность) сборочных и монтажных технологических операций (ТО) зависит от:
уровня изготавливаемого модуля (ячейки, блока и т.д.);
степени сложности и разнообразия конструкций корпусов компонентов и самих компонентов (их габаритов и массы, формы выводов и их расположения относительно корпуса, потребности в теплоотводах и т.д.), а также других конструктивов;
потребности в одноили двухсторонней сборке и монтаже на печатной плате;
совместимости технологических режимов сборочных ТО для различных конструктивов, и (или) монтажных ТО для разных конструктивов (при несовместимости – повторяемость сборочных и (или) монтажных ТО увеличивается);
степени и уровня автоматизации ТП сборки и монтажа (степень автоматизации оценивается отношением количества ТО, выполняемых автоматами к общему количеству ТО данного ТП и выражается в процентах; уровень автоматизации характеризуется количеством ТО либо переходов, одновременно выполняемых автоматами в единицу времени).
На сборку, а затем на монтаж , например, ячеек ЭВС, обычно поступают
следующие конструктивы: навесные компоненты (НК) – дискретные пассивные и активные электрорадиокомпоненты (ЭРК), интегральные схемы и прочие изделия электронной техники (ИЭТ); узлы (печатные платы (ПП), объемные соединители, а иногда поступают и контактные панельки, гибкие шлейфы и др.), а в некоторых случаях и детали (рамки, теплоотводы, крепеж и т.д.)
Так как промежуток времени между подготовкой конструктивов и сборкой должен быть минимальным, то обычно подготовительные операции относят к ТП сборки ячеек ЭУ.
Подготовка конструктивов к сборке и монтажу ячеек ЭВС
Перед сборкой на ПП конструктивы (обычно после входного контроля) должны быть подготовленными с удостоверенным уровнем качества (в соответствии с технологической документацией (ТД)) для качественного выполнения сборки и монтажа).
Подготовка НК, предназначенных для сборки и монтажа в отверстиях ПП, т.е. традиционно-монтируемых компонентов (ТМК) включает: распаковку ТМК, рихтовку, зачистку, формовку, обрезку, флюсование и лужение выводов, размещение НК в технологической таре для сборки либо на ленте, нередко рассчитанных на загрузочные узлы сборочных автоматов.
Распаковка сводится к извлечению компонентов из установочной тары и, в зависимости от формы поставки НК, может выполняться до входного контроля НК (если упаковочная тара не рассчитана на выполнение контрольных операций), либо непосредственно перед подготовкой выводов НК. В этих случаях НК перекладывают из
2
упаковочной тары (из магазинов, пеналов, специальных тар-спутников, упаковочных лент и т.д.) в различные промежуточные технологические тары (кассеты) часто с применением унифицированных модулей распаковки в составе автоматической линии подготовки НК.
Исключение могут составлять поверхностно-монтируемые компоненты (ПМК), поставляемые на специальных пластиковых двухслойных лентах (несущей, ячеистой и перфорированной, и защитной, антистатической покровной и перфорированной), пригодных для автоматизированного входного контроля и для сборки на поверхности ПП с применением сборочных автоматов. Такие ПМК чаще всего поставляются подготовленными к сборке и после входного контроля (включающего в том числе оценку паяемости) распаковываются на сборочном автомате. В этом случае распаковывание является одной из операций процесса сборки.
Формовку и предшествующие ей (при необходимости) операции рихтовки (выпрямления) и зачистки выводов НК выполняют с целью увеличения расстояний между выводами, что обеспечивает их совмещение с монтажными отверстиями ПП (для ТМК) либо контактными площадками знакомест (для ПМК), а также придания выводам необходимой формы (конфигурации), чтобы обеспечить их закрепление (фиксацию) на ПП во время сборки и, при необходимости, фиксировать расстояния от корпуса НК до платы. В сущности, формовка – это гибка выводов НК, причем радиус гибки и механическое воздействие на выводы НК не должны нарушать форму сечения вывода и его покрытия, а также не повреждать сам компонент.
Существует большое разнообразие приспособлений и технологического оборудования, включая автоматическое, для индивидуального и последовательно-совмещенного (в одной подготовительной установке) выполнения рихтовки, зачистки и формовки выводов, а иногда и следующих подготовительных операций. В частности, рихтовка, зачистка, формовка и обрезка аксиальных и радиальных выводов НК осуществляется на групповой, чаще всего автоматизированной, технологической оснастке, представляющей собой штамп (формующий, отрезной) с пневматическим приводом и набором сменных насадок пуансонов и др. деталей. Производительность такого оснащения во многом определяется механизмом подачи НК (при ручной подаче – 1500…3000 НК/ч, из вибробункера – 5…10тыс НК/ч, с ленты – до 20тыс НК/ч). Автомат для комплексной подготовки ТМК, после их распаковки, входного контроля и загрузки из технологической тары в вибробункер, схематически показан на рис.7.1, его производительность составляет 50 НК/мин.
Подготовка НК (в частности, ИС с планарными выводами) может осуществляться и на автоматической линии, включающей унифицированные модули распаковки, формовки и обрезки выводов, флюсования и лужения, а также укладки в технологические кассеты. Каждый модуль линии оснащен комплектами кассет для загрузки и выгрузки (например, в линии ГГМ2.247.020 используется 18 кассет с 50 ИС в кассете; производительность линии составляет 900 ИС/ч).
Обрезка выводов НК необходима для получения требуемой по ТД длинывыводов, так как обычно предприятия-изготовители поставляют НК с удлиненными выводами. Обрезать их можно на разных этапах технологического процесса сборки и монтажа ЭУ, например, сразу после формовки в одном штампе, снабженном ножами (или гильотинными ножницами), что наиболее часто используется; перед формовкой, что гораздо реже используется так как в этом случае труднее выдерживать нужный размер выводов; на последующих этапах, т.е. во время сборки вручную либо на полуавтоматах, например, когда НК сначала выкусываются из липкой лентыносителя , облуживаются, а затем окончательно обрезаются после закрепления НК на ПП, либо после их монтажа на ПП, что требует повышенного расхода материалов для флюсования и лужения.
Лужение (облуживание) выводов представляет собой процесс нанесения, чаще всего, расплавленного припоя на выводы НК для обеспечения их хорошей паяемости при монтаже ЭУ. Качество облуживания выводов обеспечивается не только физико-химической совместимостью материала вывода с материалом припоя, но и засчет предварительного (перед нанесением припоя) флюсования выводов (нанесением жидкого флюса, например, окунанием выводов в спиртовой раствор канифоли).
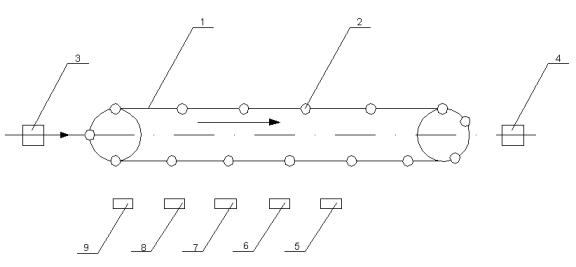
3
Рис.7.1. Схема автомата для комплексной подготовки компонентов с аксиальными выводами; 1 – транспортер; 2 – ЭРК; 3 – вибробункер; 4 – механизм рихтовки; 5 – механизм зачистки; 6 – механизм обрезки; 7 – механизм флюсования и облуживания; 8 – механизм формовки; 9 – механизм разгрузки.
Флюс способствует удалению оксидов и прочих загрязнений с поверхностивыводов и, тем самым, улучшению смачивания и растекания припоя по поверхности выводов.
Операция облуживания состоит в погружении выводов в ванну с расплавленным
припоем, нагретым до 200-230°С, т.е. до температуры, близкой к температуре пайки (при этом на г ранице раздела вывод-припой образуется интерметаллическое соединение толщиной 0,3-0,8 мкм, обеспечивающее наилучшую адгезию припоя к выводу). Минимальное расстояние от поверхности расплавленного припоя до корпуса ТМК должно быть не менее 1,3 мм. Если припой по каким-либо причинам нельзя наносить из расплава в ванне или с помощью паяльника, то облуживание осуществляют путем
холодной напрессовки припоя на выводы (например, в виде полосок сечением 0,3×0,8 мм, или специально формованных заготовок припоя в виде кусочков лент, шайбочек и др.), либо дозированным нанесением припойной пасты. Наиболее эффективны способы лужения: путем погружения в ванну с расплавленным припоем (или в волну припоя), что обеспечивает лучшую паяемость выводов НК, по сравнению с другими способами, и более длительную сохранность паяемости; а также путем дозированного переноса припоя с использованием припойной пасты, вспомогательной неметаллизированной платы (на которую паста в форме знакомест наносится трафаретной печатью), а выводы компонентов устанавливаются на знакоместа из припойной пасты, после чего паста оплавляется (ИК-нагревом, горячим инертным газом и т.п.), припой и флюс в пасте оплавляются и облуженные выводы компонентов легко отделяются от вспомогательной платы. Достоинства последнего способа аналогичны лужению из расплава припоя в ванне и, кроме того, включают возможность высокоточной дозировки припоя, что позволяет в дальнейшем существенно повысить прочность паянных соединений и точность сборочномонтажных работ (последнее в большей степени относится к ПМК).
Иногда после облуживания выводы НК очищают от оставшихся на них продуктов взаимодействия флюса с припоем и материалом выводов, причем очиститель чаще всего выбирают в виде смеси полярного и неполярного органических растворителей, а технология очистки зависит от типа производства, конструкции НК и разновидности материала флюса, используемого при облуживании выводов.
Для повышения производительности процесса сборки, особенно при помощи автоматов, НК после их подготовки упаковываются в технологические кассеты для сборки либо вклеиваются в липкую ленту, причем тип компонентов и последовательность
4
приклейки задается программой сборки. В последнем случае применяются комплектующие автоматы приклейки НК, производительность которых колеблется от 2 до 15тыс НК/ч в зависимости от типа НК. Отечественный автомат приклейки НК (например, ГГМ1.137.001) характеризуется параметрами: длина корпуса вклеиваемого ЭРК – 6…20мм; диаметр корпуса – 2…8 мм; длина вывода – 20…25 мм; диаметр вывода – 0,6…1,0 мм; ширина ленты – 60…80 мм; ширина вклейки 53, 63, 75 мм; шаг вклейки 5, 10, 15 мм; число программируемых ЭРК – 20.
Подача на сборку НК из магазинов является более дешевым способом (из-за многократного использования), но подача с ленты более универсальна, так как совместима с загрузочными устройствами большинства сборочных автоматов и удобна для контроля функциональных параметров НК.
Подготовка ПП включает их распаковку и размещение в технологической таре, входной контроль, обезжиривание, оплавление припойного покрытия (если оно имеется) в нагретом теплоносителе (например, в глицерине) или ИК-излучением, очистку, а также маркировку и контроль паяемости. Если припойное покрытие на ПП отсутствует, то обязательно выполнение операции флюсования и облуживания с использованием волн флюса и припоя, либо обычного окунания в жидкий флюс и расплавленный припой, либо способов переноса материалов для пайки на ПП с помощью различных инструментов. При наличии среди НК поверхностно-монтируемых компонентов подготовительные работы могут включать операции по формированию припойных покрытий (например, припойной пасты, наносимой трафаретной печатью) на коммутационных элементах ПП (подлежащих облуживанию) с предварительным выполнением очистки (например, в трихлорэтане), либо легкого протравливания (просветления) в слабом травителе.
Маркировочные знаки на ПП наносят с применением трафаретной либо переносной (офсетной) печати.
Подготовка прочих конструктивов (объемных соединителей, гибких шлейфов и др.) осуществляется в соответствии с ТД на каждую операцию и может включать: распаковку; удаление изоляции (при необходимости); зачистку; очистку (обезжиривание) поверхностей, подлежащих монтажу; обрезку по нужному размеру; флюсование и лужение с последующей очисткой (при неоходимости) и др. Средства реализации этих ТО выбираются в зависимости от степени сложности конструктива, типа производства и эффективности применяемого способа.
Контроль паяемости элементов конструктивов
Паяемость, по сути, является мерой способности монтируемой поверхности смачиваться припоем и определяется не только физико-химическими свойствами контактируемых при монтаже материалов технологической среды и самих конструктивов, но и качеством подготовки паяемых поверхностей до осуществления сборки и монтажа ЭУ. Хорошая паяемость закладывает основу для реализации высококачественного монтажа, так как с ней связаны основные аспекты процесса пайки:
возможность припоя создавать паянные соединения;
обеспечение высокой смачиваемости паяемых поверхностей;
тепловые характеристики сопрягаемых при пайке материалов конструктивов (в том числе их устойчивость к температурным воздействиям);
выбор оптимальных условий выполнения монтажа.
Для контроля паяемости существует более 10 различных методов ее косвенной оценки по различным критериям качества.
В частности, степень смачиваемости паяемых поверхностей припоем характеризуется значением краевого угла (или угла смачивания) θ паяемых элементов конструктивов (рис.7.2, а-
г), значение которого должно соответствовать θ ≤ 20 для обеспечения хорошей паяемости.
При определении угла смачивания используют контрольные (тестовые) контактные площадки ПП или образцы-свидетели реальных изделий, либо образцы-имитаторы,
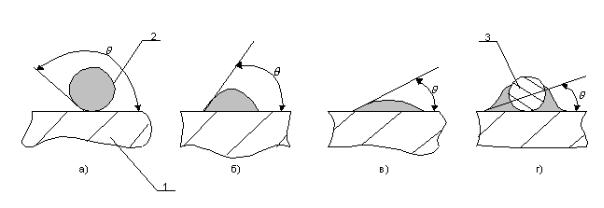
5
изготавливаемые из материалов реальных объектов производства и подготавливаемые аналогично рабочей партии изделий, а затем непосредственно перед контролем припаивают вывод-имитатор НК к контактной площадке платы-имитатора (или свидетеля) в реальном технологическом режиме, после чего делают срез образца и замеряют угол смачивания (см.рис.7.2,г).
Рис.7.2. Смачиваемость паяемых поверхностей припоем; а – отсутствие смачиваемости (угол смачивания θ >180 ); б – частичное смачивание в – полное смачивание (θ < 45 ,θ ≈ 20 ); г – определение угла смачиваемости; 1 – контактная площадка платы; 2 – припой; 3 – сечение вывода компонента.
Если контроль паяемости осуществляется по площади смачивания то образей погружают в расплавленный припой на время, соответствующее времени облуживания или пайки, а затем визуально определяют качество и площадь смачивания припоем поверхности образца (более 95% от всей площади поверхности образца должно быть однородно покрыто припоем). Благодаря
простоте реализации, этот метод получил наибольшее распространение.
Контроль паяемости по площади растекания дозы припоя по образцу позволяет выявить зависимость паяемости от небольших изменений действующих факторов в процессе облуживания или пайки. Паяемость плоских поверхностей может быть оценена по коэффициенту
растеканияКр , который характеризуется отношением площади S p , |
занимаемой |
||
припоем после расплавления и растекания, к площадиS0 , занимаемой (θ≥ 45о); |
дозой припоя в |
||
исходном состоянии (т.е. до оплавления и растекания): |
|
||
Кp = |
S p |
. |
|
|
|
||
|
S0 |
|
Паяемость считается удовлетворительной, если Кp ≥ 0,9, а высота расплавленной дозы
припоя H ≤ 0,6 мм (рис.7.3). Метод более трудоемок, чем предыдущий, но может быть пригоден
для отработки режимов пайки, выбора припоя, флюса и т.д. и требует дозировки припойного материала.
Оценка паяемости по времени смачивания (метод рассечения капли) заключается в определении времени смачивания образца, погружаемого в каплю припоя. На нагретом столике расплавляют дозу припоя, до образования капли. В каплю припоя погружают вывод НК или другой требуемый проводник так, чтобы он рассек каплю на две части, и начинают отсчет времени. Пока вывод не успел нагреться, он припоем не смачивается и делит каплю припоя на две части. По мере нагрева вывода припой начинает его смачивать и обтекать. В момент полного смачивания вывода припой касается зонда датчика, и отсчет времени прекращается. Время смачивания в этом случае должно быть нормированным.
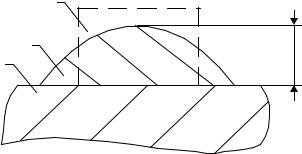
6
|
3 |
1 |
2 |
H |
Рис.7.3. К определению коэффициента растекания; 1 – тестовая контактная площадка образца; 2 – припой после растекания; 3 – исходная доза припоя (до оплавления и растекания).
Менискометрический контроль паяемости заключается в измерении высоты мениска,
поднявшегося по выводу НК над поверхностью расплавленного припоя в ванне под действием сил поверхностного натяжения. Чем лучше паяемость выводов, тем больше высота мениска. Высоту мениска измеряют с помощью специальной оптической головки или бинокулярного микроскопа, а затем сравнивают с нормированным значением высоты мениска.
Контроль паяемости металлизированных отверстий по времени их заполнения припоем осуществляется следующим образом. На нагретом столике расплавляют дозу припоя, затем контролируемый образец ПП (с отверстием и установленным на нем зондом датчика, связанным с таймером) приводят в контакт с расплавленным припоем, при этом таймер включается и начинается отсчет времен. Постепенно, смачивая стенки отверстия, припой поднимается вверх и касается зонда. В этот момент реле автоматически прекращает отсчет времени. Прибор снабжен принтером и стандартным интерфейсом для выдачи данных в автоматизированную систему контроля и управления ТП.
Метод менискографии (или балансный метод) рекомендуется для исследований, в
частности, при поиске причин плохой паяемости изделий в условиях производства; при определении свойств материалов для пайки, включая различные покрытия; для оценки влияния различных факторов на качество пайки и т.п. Данный метод основан на оценке паяемости по величине сил, действующих между образцом и припоем при погружении образца в расплавленный припой, и их измерении во времени. В этом случае можно получить большую информацию о процессах, происходящих при облуживании или пайке, чем в случаях использования других методов. Прибор – менискограф оснащен датчиками и пишущими устройствами, что позволяет получить кривую смачивания и тем самым регистрировать динамику исследуемого процесса (рис.7.4). Вначале, пока торец образца 1 не касается припоя, силы в системе отсутствуют и сигнала датчика нет. При подъеме ванны торец образца погружается в припой. Пока образец не успел нагреться, смачивания нет, мениск припоя вогнут вниз. На образец действует только сила его
выталкивания из припоя F1 (см. рис.7.4). В следующий момент времени образец прогревается и
начинает смачиваться припоем, возрастающая сила поверхностного натяжения (смачивания) припоя начинает все больше уравновешивать силу выталкивания (см. ход кривых 3 и 4 до появления горизонтального (балансного) участка на рис.7.4). При полном нагреве образца кривая
смачивания выходит на горизонтальный участок, где значение силы смачивания равно F2 , а положительный мениск припоя на образце достигает максимальной высоты. При извлечении образца из припоя сила взаимодействия между припоем и образцом может достигать величины F3
с учетом гидравлической выталкивающей силы, пропорциональной массе припоя, вытесненного образцом. Мерой паяемости в данном методе служит значение силыF2 и времени t2 , за которое она достигает этого значения.
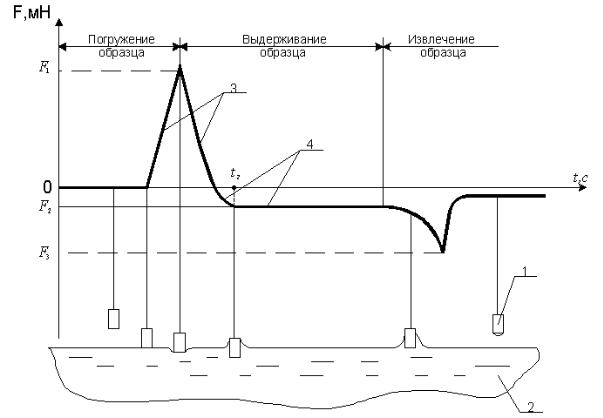
7
Рис.7.4. Схема принципа реализации контроля паяемости выводов НК с применением менискографии; 1 – образец; 2 – припой; 3 – характер изменения выталкивающей силы; 4 – характер изменения силы поверхностного натяжения.
Несмотря на информативность, метод менискографии не пригоден для оценки паяемости выводов ПМК малой массы (из-за существенного снижения чувствительности метода с уменьшением массы компонентов). Для контроля паяемости выводов ПМК разработан метод совместного использования принципов менискографии и капли припоя с подбором дозы припоя при оценке паяемости ПМК с разной формой выводов.
Варианты сборки и монтажа ячеек ЭВС, в том числе с применением техники поверхностного монтажа
Для правильного выбора разновидностей и последовательности сборочномонтажных технологических операций при изготовлении ячеек ЭВС важно знать конструкторско-технологические варианты их реализации. В настоящее время изготовление ячеек ЭВС немыслимо без применения техники поверхностного монтажа (ТПМ) компонентов, которая способствует дальнейшей миниатюризации ЭУ при увеличении их функциональных возможностей, улучшении функциональных параметров и повышении эксплутационной надежности готовых изделий. Эти преимущества ТПМ обеспечиваются за счет:
применения ПМК в микрокорпусах и типа чип-конструкций (с шагом выводов 1,25 мм и менее); кристаллодержателей СБИС (УБИС) с ленточными выводами либо выводными площадками, в том числе матричными (с шагом 0,6 мм и менее);
использования коммутационных плат (КП), преимущественно многослойных, с шириной проводящих дорожек и расстояниями между ними 0,2 мм и менее;
самых перспективных технологий сборки и монтажа, реализуемых с помощью гибкоавтоматизированных технологических модулей (или линий) со встроенными средствами контроля и работающих по программе.

8
По мере освоения и внедрения техники поверхностного монтажа (ТПМ) в производство ЭВС при изготовлении ячеек наметились три варианта реализации их сборки и монтажа с применением ТПМ (варианты I – III, рис. 7.5) и только один вариант иногда используется без применения ТПМ (вариант IV, рис. 7.5):
первый (I) – чисто поверхностный, когда поверхностно-монтируемые компоненты (ПМК) устанавливаются и монтируются с одной или с двух сторон КП (см. рис.7.5, вариант 1,а и б);
второй (II) – смешанно-разнесенный, когда с одной стороны платы устанавливаются и монтируются только простейшие ПМК, а с другой – только традиционно-монтируемые компоненты (ТМК), т.е. те, которые предназначены для сборки и монтажа в сквозных отверстиях КП (см. рис. 7.5, вариант II);
третий (III) – полностью смешанный, когда сборка и монтаж ПМК и ТМК (без ограничения, либо с ограничением по сложности конструкции) осуществляются с одной либо с двух сторон платы (см. рис. 7.5, вариант III). Он имеет наибольшее количество разновидностей реализации (см. рис. 7.5, вариант III, а – г), зависящих в основном от степени сложности конструкций ПМК, количества монтажных поверхностей, разнообразия методов и средств реализации сборки и монтажа. На рис.7.6 представлен общий алгоритм реализации всех трех вариантов сборки и монтажа ЭУ с применением ТПМ (в том числе с учетом их разновидностей);
четвертый (IV) – чисто традиционный, когда ТМК (без ограничения по сложности)
устанавливаются и монтируются с одной стороны платы, либо, что крайне редко, с двух сторон ПП, причем с обратной стороны устанавливают только единичный ТМК (см. рис.7.5, а, б), но в любом случае вариант IV неэффективен и, следовательно, неперспективен. Это связано не только с потребностью в монтажных отверстиях (при этом существенно возрастают массогабаритные показатели и ограничиваются функциональные возможности ЭУ), но и с потенциально большими затратами на сборочно-монтажные операции, т.к. стоимость автоматов для их выполнения существенно превышает затраты на автоматизацию данных операций в ТПМ. Поэтому целесообразность выбора варианта IV может быть в некоторых случаях оправданна дефицитностью ПМК, либо потребностями макетирования ЭУ.
Вариант I характеризуется максимальной плотностью компоновки и степенью миниатюризации (особенно двухсторонний поверхностный монтаж (ПМ)); самым высоким уровнем автоматизации высокоточной сборки при высокой воспроизводимости и малом разбросе
электрофизических параметров ЭУ; одноступенчатым , автоматизированным, групповым процессом пайки; повышенной эксплуатационной надежностью и улучшенными выходными характеристиками ЭУ; потенциально низкими затратами на изготовление (а, следовательно, низкой себестоимостью изделий) и высоким выходом годных ЭУ; уменьшением объема ЭУ на 40 – 75% в сравнении с техникой
Под одноступенчатым процессом пайки следует понимать технологию получения паянных соединений с использованием одного способа пайки, технологического режима, среды и типа оборудования либо инструмента (в рамках одного технологического цикла пайки независимо от количества паянных соединений)
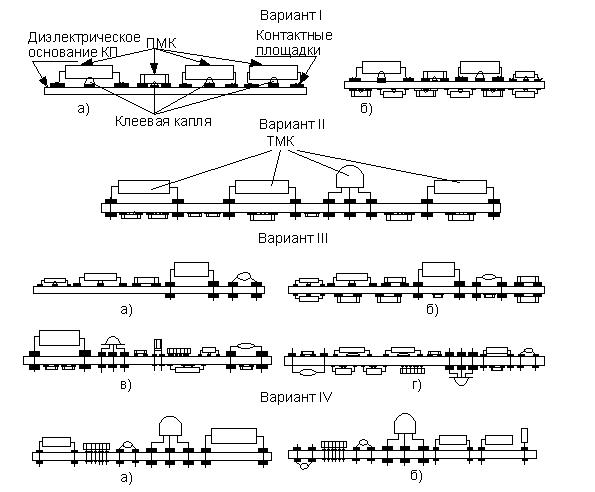
9
Рис.7.5. Варианты сборки и монтажа ячеек ЭУ; I – сборка и монтаж любого набора компонентов только на поверхность платы на одной ее стороне (а) и с двух сторон (б); II – смешанно-разнесенные сборка и монтаж, т.е. ТМК с лицевой стороны платы, а простейшие ПМК – с обратной стороны платы; III – полностью смешанные сборка и монтаж, т.е. ТМК и ПМК – с лицевой стороны платы (а), ТМК и ПМК – с лицевой стороны платы и только простейшие ПМК – с обратной стороны платы (б), любой набор ПМК – с двух сторон платы и ТМК с одной стороны платы (в); любой набор ПМК и ТМК с двух сторон платы (в том числе и специальных компонентов) (г); IV – традиционные сборка и монтаж, т.е. все ТМК
– с одной стороны платы (а) и большая часть ТМК с лицевой стороны, а единичные ТМК с обратной стороны платы (б).
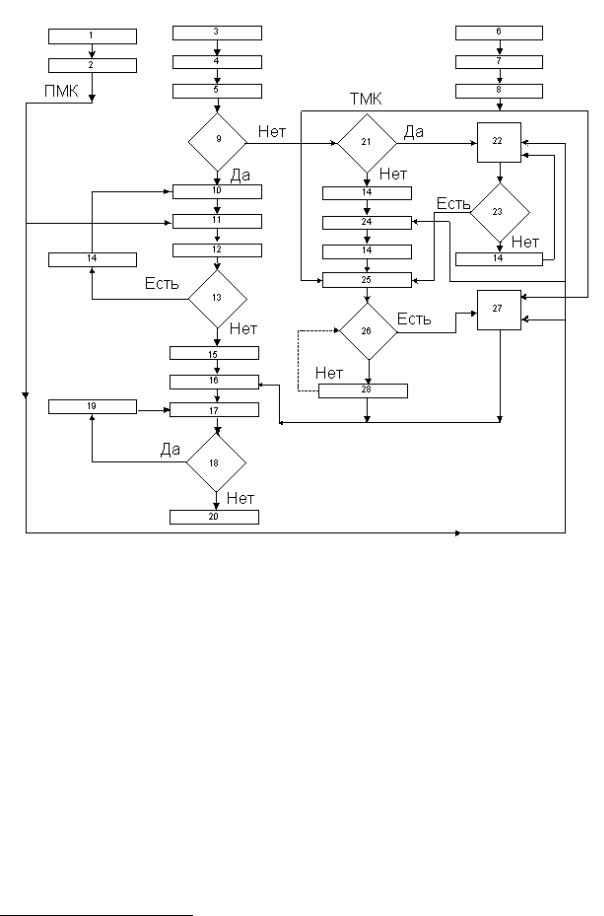
10
Рис.12.1. Алгоритм реализации I-III вариантов технологий сборки и монтажа с применением ТПМ; 1 – комплектация ПМК и загрузка в накопители; 2 – входной контроль ПМК; 3 – комплектация КП и загрузка в накопители; 4 – очистка КП; 5 – входной контроль КП; 6 – комплектация ТМК и загрузка в накопители; 7 – входной контроль ТМК; 8 – подготовка ТМК; 9 – реализация сборки и монтажа по варианту I; 10 – нанесение припойной пасты и контроль качества трафаретной печати; 11 – установка (позиционирование) ПМК на КП; 12 – контроль качества (КК) позиционирования; 13 – потребность в сборке ПМК с другой стороны КП; 14 – переворот КП; 15 – монтаж
ПОДП ; 16 – очистка смонтированного изделия; 17 – контроль качества смонтированной ячейки; 18 – наличие дефектов у смонтированного изделия; 19 – анализ и устранение дефектов; 20 – передача на приемосдаточные испытания; 21 – реализация сборки и монтажа по вариантам II либо III, начиная с лицевой стороны КП; 22 – нанесение припойной пасты и (или) клея, установка ПМК, ПОДП (при необходимости); 23 – потребность в сборке и монтаже ТМК на этой же стороне КП; 24
– нанесение клея, позиционирование ПМК на КП; 25 – установка ТМК; 26 – потребность в сборке и монтаже ТМК и ПМК, включая специальные; 27– возможные ручные сборка и монтаж ТМК, сложной конструкции ПМК, специальных
компонентов с переворотом КП или без него, а также монтаж ПОДП и ПДВП ; 28 – монтаж ПДВП.
Пайка оплавлением дозированного припоя.Пайка двойной волной припоя.

11
традиционного монтажа (ТМ). Однако полная реализация преимуществ этого варианта требует не малых первоначальных затрат (особенно на технологическое оборудование); решения проблем
согласования по ТКЛР материалов КП и компонентов, а иногда и теплоотвода, дефицита отдельных ПМК, а также переквалификации специалистов.
Технология реализации варианта I, даже для самой сложной ее разновидности (см. рис.7.5, вариант I, б), требует наименьшего времени выполнения всех технологических этапов (таких как нанесение прийной пасты на КП, сборка ПМК на КП, монтаж пайкой ОДП, очистка смонтированных ЭУ при учете всех видов технологического контроля) в сравнении с другими вариантами за счет преимущественного использования групповых автоматизированных процессов и средств их осуществления. Кроме того вариант I не требует ограничения по сложности конструкций ПМК, что существенно расширяет сферу применения ЭУ, изготовленных по данной технологии.
Вариант II отличается некоторым выигрышем по плотности монтажа в сравнении с ТМ; уменьшением объема ЭУ на 10 – 30% (по сравнении с ТМ); одноступенчатым автоматизированным, групповым процессом пайки, пригодным для ТМ и ПМ, что упрощает выбор технологического оборудования и снижает затраты на его приобретение (например, можно использовать имеющуюся для ТМ установку пайки волной припоя при некоторой ее модернизации). Кроме того, вариант II предусматривает наименьшее число технологических операций в сравнении с другими вариантами. Однако преимущество ТПМ при использовании этого варианта реализуются меньше чем на половину, главным образом из-за ограничений по степени сложности конструкций ПМК, по их нагревостойкости, по уровню дефектности паянных соединений после пайки волной (или двойной волной) припоя (так как волна припоя не обеспечивает его точного дозирования), а качество паек при этом во многом зависит от количества, шага и формы выводов ПМК, точности размеров клеевых соединений, плотности размещения и высоты посадки ПМК на КП, от расположения выводов (по одной, двум или четырем сторонам корпуса ПМК и др.). Не менее важны в этом случае и повышенные требования к адгезивам, касающиеся, например, их быстрого «схватывания». Рекомендуемыми для вариантаII типами ПМК (выдерживающих температуру волны расплавленного припоя) являются чипконструкции (резисторов, конденсаторов, индуктивностей и др.) с типоразмерами не менее 0805; SOT, SOD; SOIC с L-образными выводами (для ИС в количестве не более 14), а в исключительных случаях – кристаллодержатели с L-образными (либо планарными) выводами и ограниченным до 16 количеством выводов.
Для варианта III характерны: большой выбор ПМК и ТМК, в том числе с учётом оптимизации выбора по их стоимости, сложности конструкции, выходным функциональным параметрам, массогабаритным показателям, температурной совместимости с материалами КП, минимальному количеству сборочных автоматов и другим критериям; большая точность монтажа, чем при реализации варианта II; уменьшение объема ЭУ на 20 – 60% по сравнению с ТМ; возможность использования, наряду с новыми, традиционных средств для сборки и монтажа; возможность изготовления уникальных ЭУ (как в отношении конструкции, так и функциональных особенностей). Однако в отдельных разновидностях его реализация (например, вариантIII, в, г, см. рис. 7.5) невозможна без применения ручных процессов сборки и монтажа ТМК. Вместе с тем этот вариант требует дополнительных средств реализации сборочных и монтажных операций (при этом увеличивается парк технологического оборудования и количество разнообразной оснастки),
многоступенчатого процесса пайки, а также затрудняет выполнение операций контроля, испытаний и устранения дефектов сборки и монтажа смонтированных ЭУ. Таким образом, данный вариант сборки и монтажа является самым сложным и дорогим при реализации, особенно если речь идет о его наиболее сложных разновидностях в, г (см. рис.7.5, вариант III). И тем не менее, преимущественное использование разновидностей варианта III характерно для современных производств, адаптирующихся к требованиям и условиям ТПМ.
Выбор необходимого варианта сборки и монтажа в ТПМ пока еще во многом определяется элементной базой, но со временем этот критерий будет касаться только специальных СБИС (УБИС) во взаимосвязи с функциональными особенностями ЭУ и с учетом максимальной реализации преимуществ ТПМ. Критерий уменьшения объема ЭУ, изготовленных с применением
Температурный коэффициент линейного расширения
Многоступенчатый процесс пайки отличается от одноступенчатого разнообразием использования методов пайки и (либо)повторением некоторыхиз них в заданной последовательности.
12
ТПМ по сравнению с традиционно-монтируемыми изделиями, в конкретных производственных условиях может изменяться в более широком (чем указано ранее) диапазоне для каждого варианта даже между предприятиями-изготовителями ЭУ, но максимальное использование ТПМ позволяет получить большее значение этого критерия.
В заключение важно отметить, что стремительное развитие ТПМ связано, в первую очередь, с постоянным совершенствованием конструкторско-технологических разработок ПМК. Этим объясняется возрастающее разнообразие ПМК как в различном корпусном, так и бескорпусном исполнении, что приводит к увеличению разновидностей конструкторскотехнологических реализаций в пределах каждого из вариантов I – III (см. рис. 7.5).
В частности, стандартами IPC-7070, j-STD-013 и др. (США, Японии) предположена следующая классификация конструкторско-технологических разновидностей реализации современных ячеек ЭУ:
тип 1 – компоненты устанавливаются только на одной стороне печатной платы (ПП), т.е. односторонние сборка и монтаж НК;
тип 2 – компоненты устанавливаются на обе стороны ПП, т.е. двусторонние сборка и монтаж НК;
адля определения сложности проектирования конструкций ячеек и сборочно-монтажных ТП их
реализации, предложены дополнительно шесть классов, в которых отражена возможность использования как ТМК, так и ПМК в разных соотношениях, причем для ПМК оговаривается степень сложности их конструкторского исполнения:
класс A – используются только ТМК;
класс B – используются только ПМК;
класс C – используются смешанные наборы ТМК и ПМК, последние с ограничением по сложности конструкций (т.е. простые конструкции и конструкции средней сложности);
класс X – используются комплексно-смешанные наборы ТМК и ПМК, в том числе корпуса ПМК с мелкошаговыми выводами типа FQFP и с матричными выводными площадками типа
BGA;
класс Y – используются комплексно-смешанные наборы ТМК и ПМК, в том числе корпуса ПМК со сверхмелкошаговыми (ленточными) выводами типа QFTP и с шариковыми выводами типа CSP (размером с кристалл);
класс Z – используются комплексно-смешанные наборы ТМК и ПМК, в том числе ПМК типа
QFTP, а также бескорпусные СБИС (УБИС) типа СОВ, включая разнообразие организации их выводов (шариковые, ленточные на гибком носителе и др.), например, типа ТСР, т.е. ПМК самых сложных конструкций.
Указывая тип и класс, конструкторско-технологической разновидности реализации конкретной ячейки ЭУ, несложно найти его аналогию среди вариантов I – IV, рассмотренных ранее (см. рис. 7.5). Например, разновидность типа 1 класса А (т.е. 1А) соответствует варианту IVа; 1В – соответствует варианту Iа; 1С – варианту IIIа; 1X, 1Y, 1Z – варианту IIIа с соответствующим усложнением алгоритма реализации; 2А – варианту IVб, который как бесперспективный, используется крайне редко; 2В– варианту Iб; 2С – может соответствовать варианту II, либо IIIб, либо IIIв, либо IIIг в зависимости от компоновочной схемы ячейки и технологической совместимости сборочно-монтажных операций для ТМК и ПМК. Каждая из разновидностей 2X, 2Y, 2Z может соответствовать варианту IIIб, либо IIIв, либо IIIг с существенным усложнением алгоритма реализации сборочно-монтажных операций в зависимости от их технологической совместимости, связанной со степенью сложности конструкций ПМК и характером их размещения на плате. Типы 1 и 2 ячеек классов Y и Z в настоящее время осваиваются отечественной промышленностью.
Выбор метода внутри- и межблочного монтажа определяется требованиями к изготовлению электронной аппаратуры, ее сложностью, величинами помех, которые создает система проложенных проводников.
При выполнении внутри- и межблочного монтажа должно быть обеспечено выполнение требований:
минимальная длина электрических связей и стабильность этих связей при механических испытаниях;
высокая помехоустойчивость за счет применения экранирующих оплеток проводов, экранирующих слоев и заземления каждого экрана в отдельности;
13
надежность и долговечность электрических соединений;
наличие на оголенных участках электромонтажных материалов антикоррозионных
итехнологических покрытий под пайку;
допустимые расстояния между оголенными участками монтажных проводов и металлическими деталями каркасов и корпусов должен быть не менее 3 мм для цепей с напряжением U≤ 250 B и не менее 5 мм для цепей с U> 250 B;
монтажные соединения вблизи сильнонагретых деталей должны быть выполнены проводами в термостойкой изоляции;
к каждому контакту должно быть подсоединено не более 3-х монтажных
соединений;
доступ к отдельным компонентам для контроля, подстройки, регулировки и ремонта аппаратуры;
монтажные соединения не должны располагаться на острых кромках несущих
конструкций.
Технология проводного монтажа на печатных платах.
Проводной монтаж экономичен в условиях макетирования, единичного и мелкосерийного производства, имеет широкие технические возможности. Разработано и используется программируемое автоматическое оборудование для его реализации, и имеются различные технологические варианты:
стежковый монтаж;
многопроводной монтаж с фиксированием проводов;
монтаж незакрепленными проводами.
Эти варианты отличаются плотностью монтажа (из-за многократного перекрещивания проводов на одной поверхности), упрощением процесса трассировки, минимизацией длины соединений (прокладка проводов по кратчайшим расстояниям), уменьшением взаимных помех, возможностью применения микросварки, сокращением сроков проектирования и изготовления, уменьшением числа требуемой технологической оснастки и “мокрых” технологических процессов.
Стежковый монтаж – это процесс трассировки электрических цепей по кратчайшим расстояниям на поверхности двухслойной печатной платы (ДПП), имеющей контактные площадки (КП) и монтажные отверстия, при помощи изолированных монтажных проводов, которые образуют в монтажных отверстиях петли, подпаиваемые к контактным площадкам. Технологический процесс (ТП) состоит из операций:
получение монтажной ДПП (по типовой технологии);
прокладка трасс и прошивка платы монтажными проводами по заданным адресам;
лужение петель;
распайка петель на КП;
контроль правильности выполнения соединений.
На рис. 8.1 показаны основные элементы платы и детали со стежковым монтажом. Диэлектрическим основанием может быть стеклотекстолит с толстым медным слоем, например марки СФ-2Н-50, что позволяет улучшить теплоотвод и исключить отслаивание КП при пайке на них петель. Монтаж осуществляют изолированными проводами, например марки ПЭВТЛК, диаметром 0,08-0,2 мм. Отверстия под петли располагаются с одной стороны и симметрично относительно КП, размеры отверстий на 0,2-0,3 мм больше размеров инструмента, используемого для монтажа.
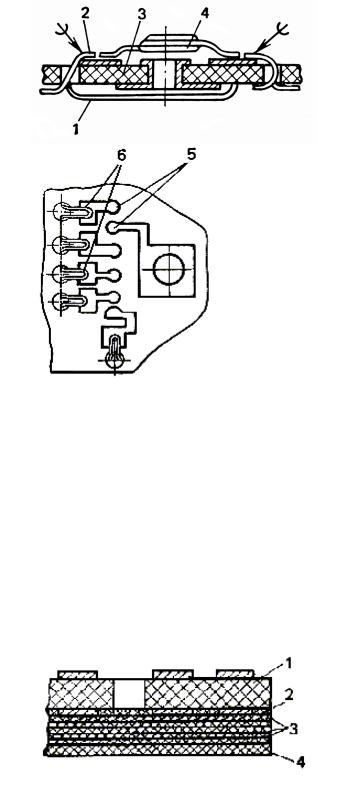
14
Рис.8.1. Основные элементы платы и детали при стежковом монтаже: 1– провод; 2 – петля; 3 – основание платы; 4 – компонент; 5 – КП для выводов компонента; 6 – петли.
Схема ТП стежкового монтажа представлена на рис 8.2. Изготавливаемая монтажная плата 1 собирается по базовым штырям в специальном приспособлении в пакет, состоящий из слоев кабельной бумаги 2, нескольких слоев эластичной резины 3 толщиной 0,5 мм и листа плотной резины 4 (рис. 8.2, а). Трассировка проводов и прошивка платы осуществляется пустотелой иглой 5 при ее возвратно-поступательном движении (рис 8.2, б). Диаметр иглы примерно на 0.1 мм превышает диаметр монтажного провода, у нее односторонний скос с углом заточки 50-75 градусов. А длина иглы 25-35 мм. Игла с проводом внутри проходит через монтажное отверстие, прокалывает эластичные слои резины, которые задерживают провод при обратном ходе иглы. Для укладки провода используются ручные прошивочные карандаши или станки с ЧПУ.
а)
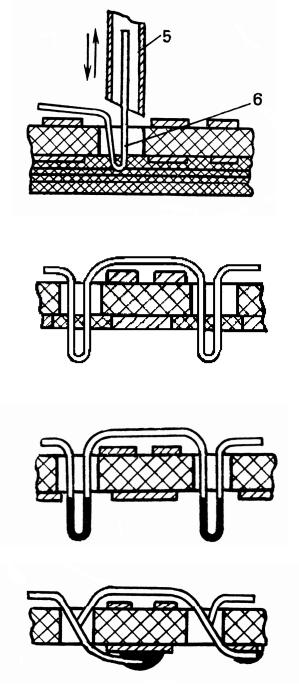
15
б)
в)
г)
д)
Рис.8.2. Схема технологического процесса стежкового монтажа.
После окончания прошивки со стороны проводов на плату накладывается и закрепляется металлическая пластина с губчатой резиной для поджатия проводов. С монтажного приспособления снимаются слои твердой и эластичной резины (рис. 8.2, в). Оставшийся слой кабельной бумаги защищает плату при лужении и удаляется после выполнения этой операции. Предварительное лужение петель (рис. 8.2, г) осуществляется паяльником с трубчатой насадкой, нагретой до 320-340°С или групповым способом (обработка флюсом ФКСп или ФКТ и погружение в ванну припоя). Подгибка и пайка петель на КП (рис. 8.2, д) осуществляется также вручную или на станке с ЧПУ.
Хотя отдельные операции стежкового монтажа и автоматизированы, в целом производительность и эффективность всего процесса невелика, т.к. на каждой операции необходима сборка и разборка различных приспособлений. Переход к специализированному оборудованию для выполнения всего комплекса работ или основной части работ позволит изменить ситуацию к лучшему. Совершенствование этого ТП происходит в направлениях
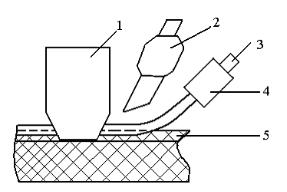
16
использования для контактирования петель с платой сварки и приклейки токопроводящими
композициями, присоединения монтажных проводов непосредственно к выводам ИС. Многопроводной монтаж с фиксированием основан на прокладывании изолированных
проводов по поверхности ДПП, на которую нанесен адгезивнный слой, фиксировании в этом слое и соединении с проводящими элементами платы. Для монтажа используются провода с высокопрочной полимерной изоляцией (например, ПНЭТ-имид) диаметром 0,1-0.2 мм. Фиксирующий адгезивнный слой состоит из клея ВК-32-200 (акронитрильный каучук с отвердителем) и прокладочной стеклоткани СПТ-3-0,025. Клей наносится поливом, окунанием, вытягиванием или через трафареты, он частично полимеризуется прессованием при 90-100°С и давлении 0,5 МПа, при этом охлаждение пресс-формы происходит без снятия давления. Схема выполнения монтажа по этому методу показана нарис. 8.3.
Рис.8.3. Схема реализации многопроводного монтажа с фиксированием.
Укладка монтажного провода 3 на плату 5 осуществляется (см. рис. 8.3) с помощью специальной головки, состоящей из ультразвукового прижима 1, ножа-отсекателя 2 и подающего устройства 4. Оптимальные режимы работы прижима: частота УЗ-колебаний 45 кГц, амплитуда 0,01 мм, давление 0,016-0,018 МПа. После укладки всех проводов их закрепляют в слое адгезива окончательным прессованием при 160-180°С и давлении 1 -1,5 МПа. Соединение проводов с элементами печатной платы (ПП) производится с использованием металлизированных монтажных отверстий, просверливаемых с высокой точностью (±0,05 мм) так, чтобы проводники были в плате по оси симметрии. Способ характеризуется низкой надежностью монтажных соединений проводов с металлизированными отверстиями из-за малой площади контактов (примерно 0,03 мм2 при многопроводном и 0,1-0,4 мм2 при печатном монтаже). Впрочем, этот недостаток устраняется при нанесении адгезивнного слоя через трафарет так, чтобы оставались открытыми КП платы, и последующем соединении пайкой утопленных в клее монтажных проводов с открытыми КП.
Монтаж незакрепленными проводами отличается тем, что проложенные проводники сразу соединяются с КП платы пайкой или сваркой. Сварка обеспечивает более надежное соединение элементов в условиях работы при вибрационных и ударных нагрузках. Механическая и коррозионная стойкость этих соединений достигаются использованием нагревостойких диэлектрических оснований плат, одножильных никелевых проводов диаметром примерно 0,2-0,3 мм во фторопластовой изоляции и выполнением монтажных площадок из Ni или нержавеющей стали. Для качественной сварки – импульсной (2,5 мс – длительность импульса) необходимо при ее реализации обеспечить теплоотвод, например за счет нанесения на внутреннюю поверхность платы слоя меди 40-50 мм толщиной.
Монтаж с использованием тканых устройств коммутации (ТУК).
ТУК представляют собой одноили многослойное изоляционное поле, с двух сторон которого во взаимно перпендикулярных направлениях проложены электропроводящие нити, образующие на наружных поверхностях в заданных точках контактные узлы, обеспечивающие электрические соединения между отдельными нитями (рис. 8.4). Для получения ТУК используются электропроводящие нити из меди марки ММ или провода в полиимидной изоляции марки ПЭВТЛК, а также диэлектрические нити из полиэтилена, стекловолокна или капрона диаметром 0,1-2,5 мм. Изготовление ведется на высокопроизводительных тканых автоматах,
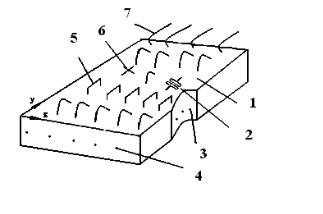
17
снабженных механизмами петлеобразования, подачи и натяжения нитей. Термофиксирование при Т=180-220°С осуществляют продувкой нагретым воздухом или паром для фиксации термопластичных нитей и переплетений.
Рис.8.4. Структура ТУК: 1 – изоляционное поле; 2 – контактная площадка (КП); 3,4 – электропроводящие нити; 5 – петли разной формы; 6 – контактные
узлы, образуемые нитями (3 и 4); 7 – удлиненные выводы для соединения платы с другими конструктивами (компонентами, соединителями и прочими).
Оплавление при температуре Т>Тплавления диэлектрического материала обеспечивает
более надежную изоляцию электропроводящих нитей, кромок структур и КП. Пластицифицирование – процесс заливки сеточной структуры пластическими массами
– повышает механическую прочность и жесткость ТУК. Формование – это термическая обработка ткани с целью придания ей пространственной формы и ее стабилизации.
Соединение электрических проводников в контактных узлах осуществляют через элементарные ячейки сетки контактной или диффузионной сваркой с последующей герметизацией зоны сварки.
ТКУ функционально делятся на сложные конструктивы, платы, кабели и соединители. Каждая структура может быть одноили многослойной с 2х-координатным внутримодульным, внутриблочным или межблочным расположением нитей. Провода делаются одинакового или разного диаметра. Равным или различным шагом и определенным числом нитей (1-3 и более). С одного края тканых кабелей располагают одну или несколько цветных кодовых нитей. Получают как гибкие и эластичные, так и жесткие коммутационные устройства плоской или объемной формы. Ввиду высокой производительности текстильных станков, изготовление ТУК в 5-6 раз дешевле, чем изготовление аналогичных по структуре ПП или плат с проводным монтажом. Монтаж ТУК применяется для связной электронной аппаратуры, в подвижных узлах ЭВС и др. Недостатки тканых устройств: невыявленость контактных структур над поверхностью ткани (для этого необходима химическая обработка), низкие точность и ремонтопригодность.
Основные технические характеристики ТУК:
электрическое сопротивление проводящих нитей не более 0,1 Ом;
прочность изоляции такова, что она выдерживает напряжение не менее 1000В;
диапазон рабочих температур -50 ÷ +65 °С;
паразитная межпроводная ёмкость – 33 ÷ 38 пФ.
Монтаж плоскими ленточными кабелями (ПЛК).
ПЛК – это одноили многоблочная структура, состоящая из многожильных ленточных проводов или гибких печатных токопроводящих шин и соединителей, с помощью которых кабели соединяются друг с другом и с остальными элементами монтажа.
Конструктивы ПЛК делятся на опрессованные, плетеные, тканые и печатные. Применяются они как для гибкого, так и для фиксированного монтажа.
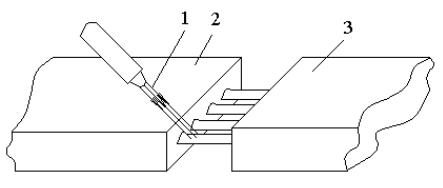
18
Токоведущие жилы проводов выполняются с круглым или прямоугольным сечением площадью от 0,02 до 0,35 мм² из меди, бериллиевой бронзы (имеют повышенную механическую прочность) и нихрома. Шаг – расстояние между центрами проводников стандартизирован и равен H=1,25 мм. Ориентация проводов при монтаже – по цветной жиле, жиле с увеличенным шагом или кодирующему выступу на кромке изоляции.
Использование ПЛК по сравнению со жгутовым монтажом позволяет:
уменьшить габариты и массу аппаратуры;
снизить трудоемкость сборочно-монтажных работ за счет их автоматизации и
механизации;
повысить качество и надежность соединений при климатических воздействиях.
ТП монтажа ПЛК включает операции:
подготовку ленточных проводов;
их сборку с различными соединителями:
трассировку кабелей на каркасах несущих конструкций аппаратуры (ЭВС);
их соединение с другими токоведущими элементами согласно заданной схеме
соединений.
Плоские провода поступают на сборку в рулонах, их разрезают на мерные участки
(линия реза перпендикулярна оси симметрии провода). С обоих концов без повреждения токопроводящих жил удаляют изоляционный слой, для чего используют механические, термомеханические, химические методы или лазерное излучение (рис. 8.5).
Рис.8.5. Схематическое изображение удаления лазером изоляции с ленточных проводов: 1 – луч лазера; 2 – ленточный провод; 3 – удаляемый слой изоляции.
При удалении лазером защита токопроводящих жил от разрушения обеспечивается высокой отражательной способностью покрытий, наносимых на их поверхность. С плетеных и тканых ленточных проводов изоляцию удаляют электрообжигом, после предварительного закрепления неудаляемой части слоем клея БФ-4, при этом выделяемые вредные газы удаляются с помощью приточно-вытяжной вентиляции.
Химическое удаление изоляции можно проводить у тех ленточных проводов, на токоведущие жилы которых наносят гальваническое покрытие. Полиэфирную изоляцию удаляют обычно в растворе серной кислоты при 100°С, а полиимидную – в растворе едкого натра при 110°С. После обработки в травящем растворе тщательно отмывают контактируемый с реактивами участок провода.
Для защиты токопроводящих жил от окисления и обеспечения хорошей паяемости или свариваемости на их поверхности наносят покрытия из металлов – никеля, золота, серебра, либо сплавов (AgSb, SnPb, SnBi). Сборка и монтаж ленточных проводов друг с другом и специальными соединителями осуществляется пайкой, сваркой, или механическими способами – обжатием, врезанием, накруткой. Токопроводящие жилы ПЛК обычно паяют паяльником с определенной формы жалом или групповым способом, при котором проводники с дозированным количеством припоя ориентируют и фиксируют относительно друг друга в приспособлении. А затем проводят оплавление одним из известных способов (в ПГС, ИК - излучением или др.).
Межкабельные паяные соединения получают с помощью термоусадочных паяльных муфт типа “термофит” (рис 8.6) или других приспособлений.
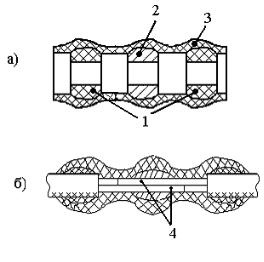
19
Рис.8.6. Конструкция термоусадочной паяльной муфты (а) и загерметизированное соединение ленточных проводов с ее помощью (б).
Муфта состоит (см. рис 8.6,а) из изоляционной оболочки 3, кольца припоя 2 с наполнителем из флюса и 2-х герметизирующих колец 1 из термопластичного материала. Оболочка готовится так, что она может выдерживать большие растяжения, а при нагревании возвращаться к первоначальным размерам. При введении токопроводящих жил 4 соединяемых ПЛК в муфты (см. рис. 8.6, б) и их термооблучении уплотнительные кольца размягчаются, имеет место усадка оболочки, деформация, оплавление и растекание припоя до уплотнительных колец. В результате соединение герметизируется.
Сварка по сравнению с пайкой позволяет получить более высокую прочность контактов, кроме того, не требует предварительного удаления изоляции (нагретые электроимпульсами участки изоляции оплавляются и под действием давления вытекают из зоны соединения). Проходящий через электроды сварочный ток расплавляет металл, обеспечивая прочный контакт. ПЛК с термопластичной изоляцией можно соединять под любым углом методом сварочной матрицы. Соединения после сварки герметизируют компаундом для защиты от климатических воздействий.
Механические способы соединений в ПЛК осуществляются с помощью специальных приспособлений и деталей, обеспечивающих электрический контакт за счет пластической или упругой деформации. Так жилы соединяются обжатием с применением металлической втулки. Отдельные провода коммутируются с элементами монтажа при помощи ножевых штампованных контактов, имеющих паз вдоль оси. Под давлением контакт прорезает изоляцию, и жила входит в паз. Эти методы применяют ограниченно из-за низкой надежности.
Собранные ленточные кабели поступают на монтаж блоков, панелей рам и стоек. Монтаж проводят по электромонтажным чертежам и таблицам раскладки, в которых указываются адреса присоединяемых кабелей, порядок их укладки на поверхностях конструкции и координаты перегибов. Для оптимизации трассировки предварительно проводят макетирование монтажа бумажными лентами. Уложенные кабели крепят быстросменными зажимами или клеевыми композициями к стенкам каркасов.
Монтаж жгутами.
Прокладываемые в одном направлении монтажные провода объединяют в жгуты, если это не приводит к повышению допустимого уровня наводок. Жгуты разделяют на плоские и объемные. Укладываемые в них провода должны быть близки по диаметру изоляции, иметь зачищенные, скрученные (для многожильных проводов) и облуженные концы. Проводники сильноточных цепей свивают (для уменьшения паразитных наводок) без скручивания парами с шагом 15 – 40 мм. В каждом жгуте предусматривают 5 – 10 %-ный запас свободных проводов, но не менее одного провода. Для изготовления жгутов применяют монтажные провода с различным типом изоляции. При повышенной температуре (до 250°С) и влажности используют провода с фторопластовой изоляцией (МГТФ), при низких температурах (-70°С) – провода в шланговой
20
оболочке из морозостойкой резины (марок РПД и РПШЭ). Сигнальные ВЧ–цепи для защиты от электромагнитных помех коммутируют экранированными проводами и кабелями с заземлением каждого экрана в одной (при длине до 100 мм) или 2–х точках (свыше 100 мм).
Требования к проводам для жгутового монтажа:
соответствие сечения жилы и изоляции расчетным значениям;
механическая прочность, гибкость и эластичность;
отсутствие повреждений (подрезов, поджогов);
применение маркировочных знаков;
наличие запаса по длине (для повторных перепаек).
На каждый жгут методом макетирования разрабатывается чертеж, по которому изготавливается плоский или объемный шаблон и составляется таблица соединений. На шаблоне трассы укладки проводов ограничиваются шпильками или штырями. Штыри устанавливаются также в местах изгибов и ответвлений, на начальных и конечных точках трасс. ТП жгутового монтажа имеет следующие этапы:
разделка монтажных проводов и кабелей;
сборка и вязка жгута на шаблоне;
соединение с контактными элементами;
трассировка и закрепление на несущей конструкции;
контроль качества выполнения.
Основной объем работ при изготовлении жгутов занимают подготовительные операции: разрезка проводов и кабелей на мерные участки, разделка концов и закрепление изоляции, удаление окисной пленки, свивание, лужение и маркировка.
Уменьшение трудоемкости сборочно-монтажных работ и количества неправильно выполненных соединений, а также облегчение нахождения неисправностей и ремонта достигаются маркировкой проводов. Она осуществляется изменением расцветки изолированных проводов, с применением липких лент с кодами, трубчатых бирок либо нанесением знаков прямо на изоляцию проводов.
Сборка жгутов в соответствии чертежом и таблицей монтажных соединений проводится вручную, с применением электрофицированного шаблона или на станках с ЧПУ.
Уложенные в жгут провода, не снимая с шаблона, обвязывают нитками, лентой шириной 10 ÷ 15 мм, либо термоусадочной пленкой, кожей или опрессовывают резиной (т.е. производят бандажирование). Шаг вязки определяется сечением проводов, их числом в жгуте и его диаметром. На криволинейных участках шаг уменьшается в 1,5 - 2 раза. Вязку бандажными нитками выполняют вручную или с помощью пневматических приспособлений.
Итак, из приведенного описания ТП видно, что при серийном производстве возможны два варианта изготовления жгутов:
-с автоматической подготовкой проводов к монтажу и ручной сборкой на шаблоне;
-с автоматической раскладкой проводов и их ручной подготовкой к монтажу.
Выбор оптимального варианта делают с учетом реальных условий по минимуму трудозатрат.
Далее изготовленный жгут проверяют на правильность раскладки и качество выполнения подготовительных операций. Сборка жгута с соединителями, переключателями, другими контактными узлами, а также укладка на каркас конструктивов и крепление проводятся аналогично этим действиям с ПЛК.
Структура технологического процесса общей сборки и монтажа ЭВС.
Отдельные сборочные единицы (ячейки и др.) и блоки, прошедшие операции контроля и регулировки, а также детали поступают на общую сборку и монтаж. Схема типового ТП общей сборки и монтажа ЭВС приведена на рис. 8.7.
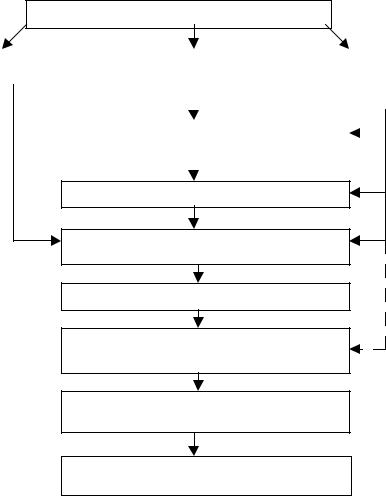
21
Комплектация конструктивов ЭВС
Подготовка модулей |
|
Сборка несущих |
|
|
Подготовка проводов, |
|||||
первого уровня (ячеек) |
|
конструкций корпусов |
|
|
кабелей и дргих |
|||||
|
|
|
|
|
|
|
конструктивов. |
|||
|
|
|
|
|
|
|
||||
|
|
|
|
|
|
|
Изготовление жгутов. |
|||
|
|
|
|
|
|
|
|
|
||
|
|
|
|
|
|
|
|
|||
|
|
Установка направляющих переключателей, |
|
|
|
|
||||
|
|
|
|
|
|
|||||
|
|
|
соединителей, ручек и т.п. |
|
|
|
|
|||
|
|
|
|
|
|
|
|
|
|
|
|
|
|
|
|
|
|
|
|
|
|
Размещение, крепление и монтаж жгутов в корпусах
Сборка и монтаж блоков. Межблочные сборка и
монтаж.
Контроль качества сборки и монтажа
Функциональный контроль и регулировка изделий (и
ремонт при необходимости)
Термотренировка (термоэлектротренировка при
необходимости), маркировка и др.
Выходной контроль качества ЭВС (включая
функциональный контроль)
Рис. 8.7. Типовой технологический процесс общей сборки и монтажа ЭВС (с учетом заключительных этапов их изготовления).
Схема ТП (см. рис. 8.7) включает сборку несущего каркаса (основания, панели, рамы, стойки, т.е. несущих конструкций корпуса ЭВС) и монтаж при помощи жгутов и кабелей. Несущие конструкции собирают с применением разъемных и неразъемных соединений. На плоскостях каркаса согласно монтажной схеме (или маршрутной карте) укладывают жгуты, устанавливают соединители, контактные колодки и другие конструктивы. Жгут на каркасе крепится металлическими скобами с установкой под ними изоляционных трубок или прокладок из лакоткани. Расстояние между скобами (200.. .500 мм) зависит от диаметра жгута. При размещении жгутов учитывают требования технологичности при ремонте аппаратуры.
Одновременно с |
укладкой жгута разводят концы одиночных проводов |
и |
кабелей к |
соответствующим |
контактам с последующим контактированием пайкой |
или |
накруткой. |
Допускается наложение жгутов или их участков друг на друга. Для предохранения жгутов из неэкранированных проводов от механических повреждений в местах их прокладки через отверстия в стенках металлических шасси или экранов предусматривают изоляционные трубки.
В собранный и смонтированный каркас изделия последовательно вставляются отдельные блоки (с ячейками), которые сочленяются через соединители с остальными конструктивами устройства. После выполнения сборочно-монтажных работ все модули устройства укрепляются на каркасе при помощи винтовых соединений. Заканчивается общая сборка и монтаж закреплением органов регулировки, управления, индикации и др., а также установкой кожухов и соединителей питания, после чего, выполняется контроль качества сборки и монтажа. Далее следуют заключительные этапы изготовления ЭВС (см. рис.8.7).
22
Контрольные вопросы.
1.В чем состоит цель сборки и ее отличие от монтажа? Какова последовательность их реализации?
2.Назовите и охарактеризуйте разновидности конструктивов, поставляемых на сборку.
3.От каких факторов зависит цикличность сборочных и монтажных ТО?
4.Перечислите операции по подготовке компонентов к сборке и монтажу. Укажите назначение этих операций.
5.В чем заключается подготовка печатных плат и прочих конструктивов к сборке и монтажу?
6.С помощью каких средств осуществляют подготовку конструктивов для сборки и монтажа?
7.По каким критериям оценивают степень и уровень автоматизации ТО или ТП?
8.Охарактеризуйте различные способы облуживания выводов НК.
9.Какие факторы являются определяющими при обеспечении паяемости? Поясните важность оценки паяемости.
10.Назовите методы контроля паяемости, оценочные критерии и возможности применения методов.
11.Каковы преимущества применения ТПМ по сравнению с традиционной техникой при создании перспективных ЭВС? Охарактеризуйте основные особенности ТПМ.
12.С какой целью, и по каким признакам классифицируют ячейки ЭУ по конструкторскотехнологическим вариантам сборки и монтажа?
13.Охарактеризуйте вариант I сборки и монтажа и приведите алгоритм его реализации для разновидности Iб, используя рис. 7.6.
14.Используя общий алгоритм ТП реализации сборки и монтажа ячеек ЭУ (см. рис.7.6), изобразите алгоритм реализации варианта II, назовите его особенности и возможности.
15.Какие особенности присущи варианту III и его разновидностям? Изобразите алгоритм реализации варианта IIIа, пользуясь общим алгоритмом ТП сборки и монтажа ячеек ЭУ
(см. рис. 7.6).
16.Охарактеризуйте вариант IV и приведите алгоритм его реализации для самой типичной его разновидности (IVа).
17.Назовите признаки, положенные в основу зарубежной классификации конструкторскотехнологических вариантов (типов и классов) реализаций сборки и монтажа ячеек ЭУ, найдите их аналогии среди вариантов I – IV.
18.В каких случаях и в модулях какого уровня используют стежковый и многопроводной монтаж?
19.Приведите технологическую последовательность выполнения стежкового монтажа.
20.Как производят многопроводной монтаж ЭВС?
21.Укажите возможности применения и недостатки монтажа ткаными устройствами коммутации.
22.В чем заключается технология изготовления ТУК?
23.Что собой представляют плоские ленточные кабели и каковы преимущества их использования?
24.Какие технологические операции необходимо выполнить, чтобы осуществить монтаж плоскими ленточными кабелями (ПЛК)?
25.Дайте технологическую характеристику операциям подготовки монтажных проводов.
26.Охарактеризуйте процесс получения межкабельных соединений с помощью термоусадочных паяльных муфт.
27.Охарактеризуйте получение контактных соединений сваркой и механическими способами. Сравните их с получением этих соединений пайкой.
28.Охарактеризуйте конструкции и разновидности жгутов. Какая изоляция используется в монтажных проводах, входящих в жгуты?
29.Назовите этапы ТП жгутового монтажа.
30.С какой целью и с помощью каких средств осуществляют бандажирование жгутов?
31.Какие два варианта изготовления жгутов возможны при серийном производстве и как правильно выбрать лучший из них?
32.Назовите и проанализируйте основные этапы общей сборки и монтажа ЭВС.
23