
Turbin_2009_3
.pdfsτ к |
= ru2 + |
Scл |
; |
(6.2) |
|
2pyd |
|||||
|
|
|
|
где Σсл — сумма центробежных сил лопаток и промежуточных тел,
закрепленных на барабане, н; y, d — соответственно ширина и толщина барабана, м.
Если отношение толщины барабана к его диаметру больше величины 0,4 ¸ 0,45, то расчет ведут по формулам, полученным для диска.
6.2. Расчет дисков
Напряжения, возникающие в диске, при прочих равных условиях зависят от формы диска. В специальной литературе [1], [3], [4] [7] приведена методика расчета дисков постоянной толщины, конического и диска равного сопротивления. Однако любой профиль полотна можно заменить ступенчатым профилем и рассчитывать как диск постоянной толщины.
С этой целью полотно разбивают на ряд участков с таким расчетом, чтобы скорость соседних участков отличалась менее чем на 10¸20 м/с. (рис 6.1).
Поставленную задачу решают методом двух расчетов. Известными должны быть геометрические размеры диска и радиальные напряжения на внутренней и наружной поверхностях диска. В диске без отверстия радиальные и тангенциальные напряжения в центре равны между собой. В диске с отверстием напряжение на внутренней поверхности ступицы равно натягу и обычно составляет: 5 — 16 МН/м2. Радиальные напряжения на внешнем диаметре sza вызываются центробежными силами лопаток и частью обвода, отмеченной пунктиром на рис. 6.1.
srа = Scл + 2 / 3×со б , |
(6.3) |
2pXa Ya |
|
где соб — центробежная сила обода, Н.
Расчет ведут для каждого участка с постоянной толщиной профиля от внутреннего радиуса к наружному.
Радиальные и тангенциальные напряжения на внешней границе первого участка (наружной поверхности ступицы) определяют по формуле:
sr1 = ar ×sri + aτ × sr j + ai × T
(6.4)
sτ1 = br ×sri + bτ × sr j + bi × T.
Радиальные напряжения на внутреннем участке принимаются равным натягу, а величину тангенциальных напряжений принимают произвольно.
Коэффициенты a и b являются функциями отношений радиусов
11
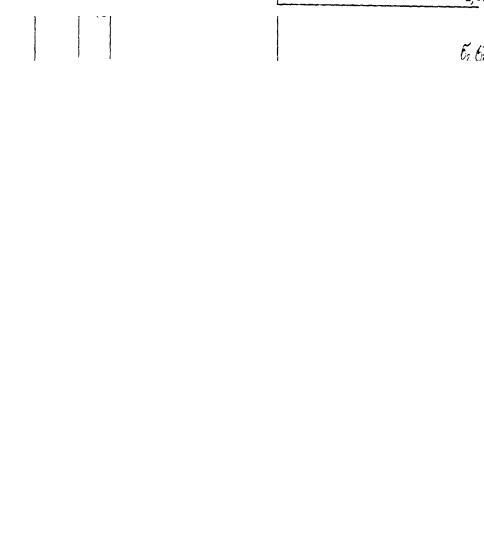
αr |
= βτ |
= |
1 + m2 |
; αc = βz = |
1 − m2 |
; |
||||||
|
|
|||||||||||
|
|
|
2 |
|
|
|
|
|
2 |
|
||
αc = −2,74(3,3 − 2,6m2 − 0,7m4 ); |
||||||||||||
β |
c |
|
( |
− 2,6m2 − |
0,7m4 |
) |
|
|||||
|
= −2,74 1,8 |
; |
|
|||||||||
|
|
|
|
|
|
|
|
n |
2 |
|
||
|
|
|
|
|
T = d2 |
|
|
|
; |
|
||
|
|
|
|
|
|
|
|
|||||
|
|
|
|
|
|
|
1000 |
|
|
|
d = 2x.
где n — частота вращения, об/мин.
m = ri , r1
где ri, r1 — внутренний и наружный радиусы первого участка
К расчету диска произвольного профиля
Рис. 6.1
Напряжения σr2 , στ2 на том же радиусе второго участка (внутренний радиус второго участка) рассчитанного по формулам:
σr |
|
= σr |
Yn |
, |
(6.5) |
|
|
|
|||||
|
2 |
1 |
Y |
+1 |
|
|
|
|
|
n |
|
|
12
|
|
|
|
|
|
Y2 |
|
|
στ |
|
= στ |
|
+ μσr |
|
−1 , |
(6.6) |
|
|
|
Y |
||||||
|
2 |
|
1 |
1 |
|
|
|
|
|
|
|
|
|
|
1 |
|
|
где μ=0,3 — коэффициент Пуассона; Y2, Y1 — соответственно ширина второго и первого участка, м.
Аналогично находят напряжения на внешнем диаметре второго участка, используя формулу (6.4). Величина m определяется как отношение внутреннего радиуса и наружного радиуса второго участка, а напряжения σri и στ j есть напряжения, определенные по формулам (6.5 и 6.6).
Таким образом, определяют напряжения на границах каждого участка до тех пор, пока не найдут напряжения на внешнем радиусе диска σrа .
Если оказалось, что найденное напряжение σrа совпадает с истин-
ным, определенным по формуле (6.3), то это означает, что было правильно выбрано тангенциальное напряжение на внутреннем участке в начале расчета. Как правило, при первом расчете этого не происходит. Поэтому необходимо выполнить второй расчет, в котором следует принять n=0 и σri =0 (диск неподвижен и не нагружен), а величину στ j опять выбрать
произвольно. Расчет проводят в том же порядке. как и первый, до тех пор пока не определят напряжения σrа на внешнем радиусе.
Находят коэффициент
K = |
σ |
ra |
− σI |
|
|
|
ra |
. |
(6.7) |
||
|
|
|
|||
|
|
|
σII |
|
|
|
|
|
ra |
|
где σ |
ra |
, σI |
, σII — радиальные напряжения на внешнем участке, рассчи- |
|
ra |
ra |
танные соответственно по формуле (6.1) и полученные в результате первого и второго расчетов.
Умножив на полученный коэффициент напряжения второго расчета и сложив их с соответствующими напряжениями первого расчета, получают истинные напряжения на границах рассматриваемых участков. По найденным значениям строят эпюру напряжений. При расчете дисков с температурой металла ниже 430 оС критерием прочности является предел текучести σ0,2. При более высоких температурах необходимо учитывать предел длительной прочности σдл и предел ползучести σпл. Допускаемые напряжения находят по формулам:
σдо п = |
σ0,2 |
, |
σдо п = |
σдл |
, |
σдо п = |
σлл |
. |
|
|
|
||||||
|
K т |
|
Кдл |
|
Кп л |
|||
Коэффициенты запаса прочности принимают равными: |
|
|
||||||
Кт =1,8 ÷ 2,2; |
Кдл = 1,65; |
Кпл = 1,25 |
|
|
13

По найденным значениям допускаемых напряжений выбирают материал или для выбранного материала определяют запас прочности. Характеристики металлов и рекомендуемые материалы дисков приведены в справочной литературе [ 1 ], [ 3 ].
7. РАСЧЕТ ВАЛА НА ПРОЧНОСТЬ
На вал турбины действуют крутящий момент от усилий на лопатках, изгибающий момент от собственного веса и осевое усилие от давления пара.
Крутящий момент вычисляют так:
|
M кр = |
|
Ni |
|
|
, |
|
|
(7.1) |
||
|
|
w |
|
|
|
|
|||||
|
|
|
|
|
|
|
|
|
|
||
где Ni — внутренняя мощность ступеней, расположенных до рас- |
|||||||||||
сматриваемого сечения вала, кВт; ω — |
|
|
частота вращения, 1/с. |
|
|||||||
Касательное напряжение от скручивания: |
|
||||||||||
|
t = |
Мкр |
, |
|
|
|
|
|
(7.2) |
||
|
|
|
|
|
|
|
|||||
|
|
2Wр |
|
|
|
|
|
|
|||
где W — момент сопротивления, м3. |
|
||||||||||
р |
|
|
|
|
|
|
|
|
|
|
|
|
pd3 |
|
|
d |
0 |
|
4 |
|
|||
W = |
|
× 1 - |
|
|
|
. |
(7.3) |
||||
|
|
|
|
||||||||
p |
32 |
|
|
|
|
d |
|
|
|
||
|
|
|
|
||||||||
|
|
|
|
|
|
|
|
|
|
|
Здесь d, d0 — наружный диаметр вала и диаметр отверстия в нем, м. Изгибающий момент Миз в любом сечении может быть найден по формулам изгиба балок, нагруженных распределенной или сосредоточен-
ной нагрузками.
Нормальное напряжение от изгиба и сжатия рассчитывают по формуле :
s = Миз ± |
P |
, |
(7.4) |
|
|||
Wp fв |
|
где Р — осевое усилие, Н; fв — поперечное сечение вала, м2. Наибольшее напряжение от изгиба и кручения определяется выражением:
|
1 |
|
|
|
|
|
tmax = |
|
s2 + 4t2 . |
(7.5) |
|||
|
2
Подсчитанное по (7.5) напряжение не должно превышать допустимого для выбранного материала. С учетом резкого возрастания нагрузок на вал при коротком замыкании запас прочности для валов принимают не ниже семи. Тогда для углеродистых сталей допускаемое напряжение должно быть выбрано не выше 40 МН/м2, а для легированных — не выше
60 ¸ 80 МН/м2.
14

8. ОПРЕДЕЛЕНИЕ ЧАСТОТЫ КОЛЕБАНИЙ РОТОРОВ ТУРБИН
Частоту колебаний роторов определяют для того, чтобы избежать резонанса при работе турбины. Частоту вращения, при которой наступает резонанс, называют критической. Если рабочая частота вращения ротора больше критической, то валы называют жесткими, если меньше - гибкими. Точное определение частоты колебаний реальных роторов представляет весьма трудоемкую задачу. Однако, допуская определенные упрощения реальной картины, можно найти критическую частоту вращения ротора с точностью, достаточной для технических расчетов.
Обычно критическую частоту рассчитывают по формуле:
n кр = 9,55 |
G jYj |
, |
(8.1) |
|
|||
|
Σm jYj |
|
|
где Gj — сила тяжести участка ротора, Н; mj — |
масса этого участка, |
кг; Yj — прогиб вала под центром тяжести этого участка, м. Расчет ведут в следующей последовательности.
Разбивают ротор на участки, границами которых могут быть диски, ступеньки вала, втулки и т.п. По объему и плотности материала каждого участка определяют массу этого участка mj и соответствующую силу тяжести Gj. Определяют центры тяжести рассматриваемых участков и находят величину прогиба вала каждого участка Yj (перемещение центра тяжести каждого участка относительно прямой оси ротора). При большом количестве участков определение прогибов встречает известные трудности. Обычно пользуются графоаналитическим методом. (рис. 6.1).
Вал вычерчивают в масштабе по длине 1:mg, т.е. 1 см на чертеже соответствует mg вала. Выбирают полюсное расстояние H1 и откладывают последовательно векторы сил Gj в масштабе сил mе, т.е 1 см на чертеже соответствует mH силы.
Соединив концы векторов Gi с полюсом О1, получают силовой многоугольник. Под валом на линии вектора реакции опоры выбирают точку а и проводят последовательно лучи, параллельные лучам силового многоугольника. Точки а и b соединяют и получают веревочный многоугольник. Ордината z веревочного многоугольника представляет собой в определен-
ном масштабе изгибающий момент в данном сечении: |
|
Миз = Н1 me mg z . |
(8.2) |
Для построения упругой линии вала полагают, |
что вал находится |
под нагрузкой, определяемой площадью эпюры изгибающих моментов. Делят эпюру на ряд участков (заштрихованных в противоположные стороны) и в центре тяжести каждого из ни прикладывают силу тяжести Rj, равную площади этого участка. С целью учета различия в диаметрах уча-
15
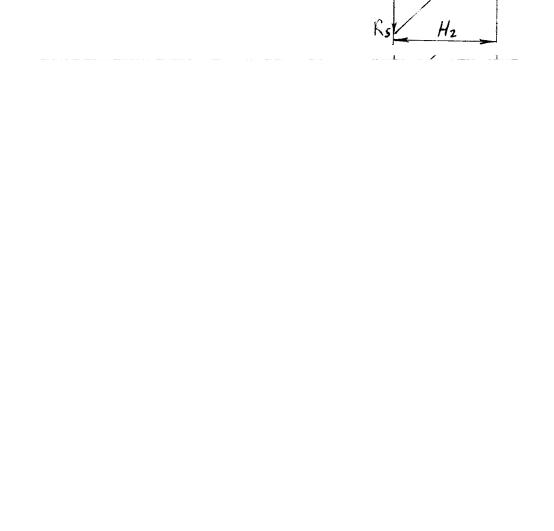
стков, участок с наибольшим диаметром выбирают за основной и увеличивают ординаты других участков в (d/dj)4 раз.
Рис. 8.1.
Если площадь участка на чертеже равна f, тогда R= mcm2gf H . На ос-
нове сил R строят второй силовой многоугольник с полюсным расстоянием Н2. Для этого предварительно выбирают масштаб фиктивных сил mф, т.е. 1 см длины в многоугольнике фиктивных сил равен mф см2 эпюры моментов, измеренных на чертеже. В построенном на основе этого силового многоугольника веревочном многоугольнике ординаты Y представляют собой величину прогиба, а многоугольника — упругую линию вала в определенном масштабе. Действительная упругая линия вала будет получена тогда, когда полюсное расстояние Н2 будет выбрано по соотношению:
Н2 |
= |
|
EJ |
, |
(8.3) |
|
m |
m2 m Н |
|||||
|
|
|
|
|||
|
|
ф |
g c 1 |
|
|
где EJ — жесткость вала с наибольшим диаметром d.
16

Для ясности чертежа прогибы увеличивают в К раз (например, принимают К=100, 200, 500). Тогда полюсное рассеивание выбирают из условия:
Н2 = |
EJ |
|
|
|
. |
(8.4) |
|
|
|||
|
K mфmgmcH1 |
|
Если в расчетную формулу (8.1) вводить прогибы, взятые непосредственно из чертежа, то критическую частоту вращения необходимо опре-
делять из зависимости: |
|
|
|
|
|
n кр = 9,55 |
КΣσ jYj |
|
|
||
Σm jYj2 . |
(8.5) |
||||
|
|
Для нормальной работы турбины критическое число оборотов должно быть либо на 20 ÷ 25% выше рабочего числа оборотов, либо на 30 ÷ 40 % ниже рабочего числа оборотов. Если эти условия не выдерживаются, необходимо внести изменения в конструкцию ротора турбины.
Для многоцилиндровых турбин критические частоты определяются для каждого из роторов составных валопроводов и в случаях совпадения
nкрi либо кратного их совпадения изменяются конструкции роторов. Для
устранения взаимного влияния роторов используются соединительные полугибкие и гибкие муфты
ЛИТЕРАТУРА
1. Жирицкий Г.С. Конструкция и расчет на прочность деталей паровых и газовых турбин / Г.С. Жирицкий, В.А. Стрункин. М: Машинострое-
ние, 1988. — 520 с.
2. Щегляев А.В. Паровые турбины / А.В. Щегляев. Энергия, 1976. —
357 с.
3.Смоленский А.Н. Конструкция, прочность и металлы элементов паровых турбин / А.Н. Смоленский. — Киев,: Выща школа, 1979 г., 361 с.
4.Самойлович Г.С. Паровые турбины / Г.С. Самойлович, Б.Н. Трояновский. Сборники задач. М., 1957, 278 с.
5.Дейч М.Е. Атлас профилей решеток осевых турбин / М.Е. Дейч,
Г.А. Филиппов, Л.Я. Лазарев. М.: Машиностроение, 1965. — 95 |
с. |
6. Паровые и газовые турбины. Методические указания по выполне- |
|
нию курсового проекта для студентов специальности 0305. — |
Саратов, |
1983 — 24 с. |
|
7. Хрусталев В.А., Антропов П.Г. Основы теории и расчетов турбин ТЭС и АЭС / уч. пос. Саратов СГТУ, 2008г. – 250 с.
17