
- •Оглавление
- •ВЕДЕНИЕ
- •ЛАБОРАТОРНАЯ РАБОТА 2 МЕТАЛЛОГРАФИЧЕСКИЙ МИКРОСКОП
- •ЛАБОРАТОРНАЯ РАБОТА 3 МИКРОСКОПИЧЕСКИЙ АНАЛИЗ (МИКРОАНАЛИЗ)
- •ЛАБОРАТОРНАЯ РАБОТА 4 ОПРЕДЕЛЕНИЕ КРИТИЧЕСКИХ ТОЧЕК СПЛАВОВ СВИНЕЦ–СУРЬМА
- •ЛАБОРАТОРНАЯ РАБОТА 5 ПОСТРОЕНИЕ ДИАГРАММЫ СОСТОЯНИЯ СВИНЕЦ–СУРЬМА. АНАЛИЗ ДИАГРАММ СОСТОЯНИЯ ДВОЙНЫХ СПЛАВОВ
- •ЛАБОРАТОРНАЯ РАБОТА 7 ИЗУЧЕНИЕ МИКРОСТРУКТУРЫ ЧУГУНОВ
- •ЛАБОРАТОРНАЯ РАБОТА 8 ЗАКАЛКА УГЛЕРОДИСТОЙ СТАЛИ
- •ЛАБОРАТОРНАЯ РАБОТА 9 ОТПУСК УГЛЕРОДИСТОЙ СТАЛИ
- •ЛАБОРАТОРНАЯ РАБОТА 12 МИКРОСТРУКТУРА АЛЮМИНИЕВЫХ СПЛАВОВ
- •ЛАБОРАТОРНАЯ РАБОТА 13 МИКРОАНАЛИЗ МЕДИ, ЛАТУНЕЙ И БРОНЗ
- •БИБЛИОГРАФИЧЕСКИЙ СПИСОК

ЛАБОРАТОРНАЯ РАБОТА 5 ПОСТРОЕНИЕ ДИАГРАММЫ СОСТОЯНИЯ СВИНЕЦ–СУРЬМА. АНАЛИЗ ДИАГРАММ СОСТОЯНИЯ ДВОЙНЫХ СПЛАВОВ
Цельработы
1) на конкретном примере усвоить принцип построения диаграмм состояния, изучить простейшие типы диаграмм, изучить микроструктуру сплавов систем Рb–Sb; 2) изучить основные типы диаграмм состояния двойных систем; приобрести практические навыки изучения превращений, протекающих при кристаллизации сплавов; проанализировать полученные данные и определить возможности их использования на практике.
Приборы, материалыиинструмент
Микроскоп МИМ-7; комплект микрошлифов сплавов; диаграммы состояния.
Краткиетеоретическиесведения
Свойства сплава зависят от многих факторов, но прежде всего они определяются составом фаз и их количественным соотношением.
Эти сведения получают из анализа диаграмм состояния. По диаграмме состояния можно представить полную картину формирования структуры, определить оптимальную температуру заливки любого сплава в литейную форму, оценить жидкотекучесть выбранного сплава и возможности получения химической неоднородности, выбрать сплавы и условия для их обработки давлением.
Для построения диаграммы состояния необходимо взять несколько сплавов с разной концентрацией компонентов, а также сами компоненты.
Используя метод термического анализа, для каждого компонента и сплава, строятся кривые охлаждения. На них определяются положения критических точек. Зная критические точки большого числа сплавов, приступают к построению диаграммы состояния в координатах температура– химический состав сплава. Кривые охлаждения для двух компонентов и трех сплавов показаны в левой части рис. 5.1.
Материаловедение. Лаб. практикум |
-37- |
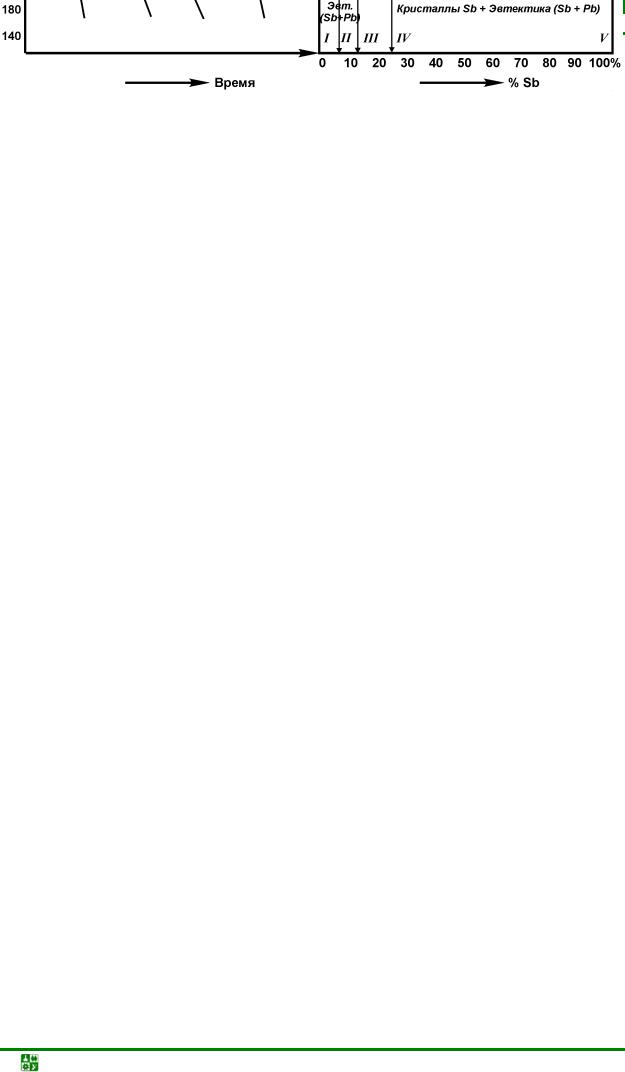
ЛАБ. Р. 5 ПОСТРОЕНИЕ ДИАГРАММЫ СОСТОЯНИЯ СВИНЕЦ–СУРЬМА. АНАЛИЗ ДИАГРАММ СОСТОЯНИЯ 2ЫХ СПЛАВОВ
Краткие теоретические сведения
Рис. 5.1. Построение диаграммы состояния Pb–Sb по критическим точкам
Техника построения диаграммы состояния сплавов свинец–сурьма по критическим точкам показана на рис. 5.1.
На горизонтальной оси откладывают концентрацию одного из двух компонентов, образующих сплав. В нашем случае отложена концентрация
Sb.
В точке, где 0 % Sb, сплав будет однокомпонентным – чистый свинец. Ордината, проведенная через точку 100 % Sb, также отвечает составу чистого компонента – сурьмы.
Затем на оси концентраций находят точки, соответствующие составу каждого сплава. Через эти точки проводят вертикальные прямые, на которых проектируют полученные значения критических температур. На диаграмме эти вертикали обозначены цифрами II, III, IV и т. д.
Экспериментально построенные диаграммы состояния проверяют по правилу фаз, дающему возможность теоретически обосновать направление процессов превращения для установления равновесного состояния системы.
Общие закономерности существования устойчивых фаз, отвечающих условиям равновесия, выражены в математической форме правилом фаз Гиббса. Правило фаз дает возможность предсказать и проверить процессы, происходящие в сплавах при нагреве и охлаждении. Оно показывает, происходит ли процесс кристаллизации при постоянной температуре или в интервале температур и какое число фаз может одновременно существовать в системе.
Материаловедение. Лаб. практикум |
-38- |
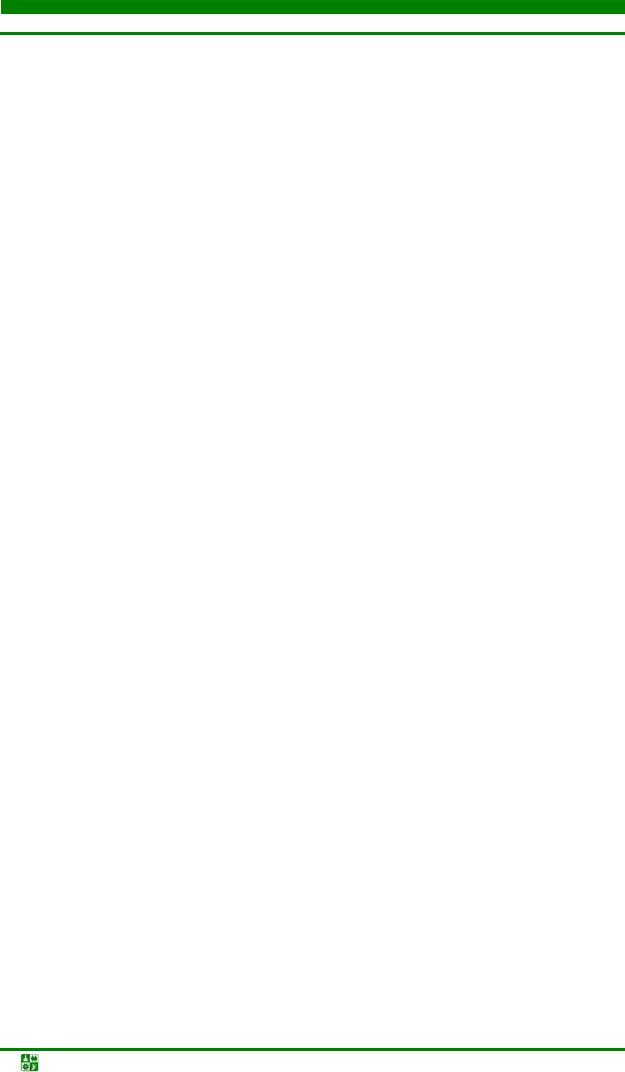
ЛАБ. Р. 5 ПОСТРОЕНИЕ ДИАГРАММЫ СОСТОЯНИЯ СВИНЕЦ–СУРЬМА. АНАЛИЗ ДИАГРАММ СОСТОЯНИЯ 2ЫХ СПЛАВОВ
Краткие теоретические сведения
Диаграммы состояния обычно строят при постоянном атмосферном давлении, и правило фаз выражается уравнением
С = К + 1 – Ф,
где С – число степеней свободы (вариантность) системы, под которым понимают число внешних и внутренних факторов (температура, давление и концентрация), которое можно изменять без изменения числа фаз в системе; К – число компонентов в системе; Ф – число фаз.
Проанализируем построенные кривые охлаждения, чтобы установить фазовый состав на отдельных их участках.
Кривая охлаждения I относится к чистому свинцу. При температурах выше точки 1 (327 °С) свинец находится в жидком состоянии. На горизонтальном участке кривой 1–1′ идет кристаллизация свинца. Ниже точки 1′ (ниже 327 °С) идет охлаждение твердого слитка
Кривая II относится к сплаву с 94 % Pb и 6 % Sb. Кристаллизация начинается в точке 1 (296 °С), из жидкости выделяются кристаллы свинца. Это согласуется с правилом фаз, т. е. число степеней свободы в этом случае равно единице. В данном случае компонентов – два, фазы – две (жидкость и кристаллы свинца). Число степеней свободы в точке 1
С1 = К – Ф + 1 = 2 – 2 + 1 = 1.
Так как на участке кривой 1–2 из жидкости с понижением температуры выделяются кристаллы свинца, жидкость обогащается сурьмой.
В момент начала выделения кристаллов свинца в точке 1 жидкость сплава содержала 6 % Sb, в точке 2 жидкость уже содержит 13 % Sb и 87 % Рb. Как только достигается это соотношение компонентов, выделение и рост кристаллов свинца прекращаются, а оставшаяся жидкость сплава кристаллизуется в виде смеси мелких кристаллов Рb и Sb.
Реакция, в результате которой из жидкого сплава при постоянной температуре образуются кристаллы двух фаз, записывается и читается сле-
дующим образом: Жс 246→Э(Рb + Sb). Жидкая фаза сплава состава точки
С при t = 246 °С кристаллизуется в виде смеси кристаллов свинца и сурьмы – эвтектики. В период эвтектического превращения в равновесии находятся три фазы: жидкая, кристаллы свинца и кристаллы сурьмы, поэтому на участке 2–2′ число степеней свободы
С = К – Ф + 1 = 2 – 3 + 1 = 0.
Система безвариантна (нонвариантна), т. е. температура и число фаз должны оставаться постоянными. Наличие горизонтального участка на кривой охлаждения отражает постоянство температуры. Температура остается постоянной до полного исчезновения одной из фаз – жидкости.
У сплава III, содержащего сурьмы 13 %, из жидкости при постоянной температуре 246 °С (на участке 1–1′ кривой охлаждения) выделяются два вида кристаллов Рb и Sb в виде равномерной смеси. Сплав III называют эвтек-
Материаловедение. Лаб. практикум |
-39- |
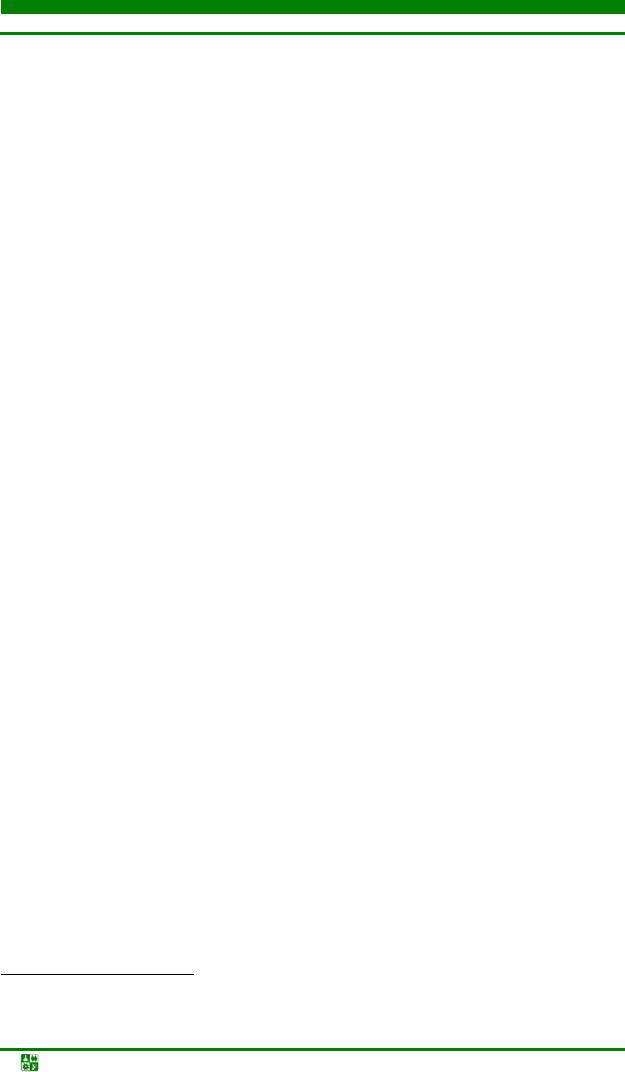
ЛАБ. Р. 5 ПОСТРОЕНИЕ ДИАГРАММЫ СОСТОЯНИЯ СВИНЕЦ–СУРЬМА. АНАЛИЗ ДИАГРАММ СОСТОЯНИЯ 2ЫХ СПЛАВОВ
Краткие теоретические сведения
тическим, он имеет самую низкую температуру кристаллизации (слово эвтектика означает легкоплавкая).
В сплаве с содержанием сурьмы более 13 % (IV) в точке 1 начинают выделяться кристаллы сурьмы из жидкости (C = 2 – 2 + 1 = 1), а сплав обогащается свинцом. Когда температура снизится до 246 °С (точка 2), жидкость будет содержать 13 % Sb, и при постоянной температуре образуется эвтектика:
С= К – Ф + 1 = 2 – 3 + 1 = 0.
Урассмотренных пяти сплавов значения точек начала и конца кристаллизации наносятся на диаграмму.
Диаграмма состояния представляет собой графическое изображение фазового состава сплавов данной системы в функции температуры и химического состава сплавов.
На диаграмме состояния системы Рb−Sb линия АСВ – линия ликвидуса, т. е. геометрическое место всех точек, которые определяют температуру начала кристаллизации сплавов. Линия солидуса DСЕ соответствует точкам, определяющим температуру конца кристаллизации сплавов.
Сплавы, расположенные левее точки С и имеющие концентрацию сурьмы менее 13 %, называются доэвтектическими. Процесс их кристаллизации начинается с выделения кристаллов свинца, имеющего избыточную концентрацию по отношению к эвтектике.
Сплавы, содержащие более 13 % сурьмы и лежащие правее точки С на диаграмме состояния, называются заэвтектическими. Процесс их кристаллизации начинается с выделения сурьмы. У всех сплавов системы Рb−Sb процесс кристаллизации заканчивается при постоянной температуре с образованием эвтектики. Поэтому диаграмма состояния, показанная на рис. 5.1, – одна из простейших для сплавов, образующих эвтектические смеси из чистых компонентов .
Знание диаграмм состояния различных систем, характеризующих превращения в сплавах, и умение анализировать эти превращения позволяют оценить свойства сплавов и в конечном итоге рационально выбрать материал для тех или иных изделий в зависимости от предъявляемых к ним требований.
Диаграммы состояния изображаются в координатах температура– содержание компонентов. Линии, соединяющие критические точки аналогичных превращений в системе, разграничивают области существования равновесных фаз. Любая точка на диаграмме определяет фазовый и химический составы сплава, а также его структуру при данной температуре. Вертикальная линия соответствует определенному химическому составу сплава.
В сплаве в процессе кристаллизации могут присутствовать следующие твердые фазы: исходные компоненты; твердые растворы; химические соединения.
Для практического пользования диаграммой удобней выделить сплавы, малорастворимые в твердом состоянии, в отдельную группу и принять растворимость равной нулю.
Материаловедение. Лаб. практикум |
-40- |
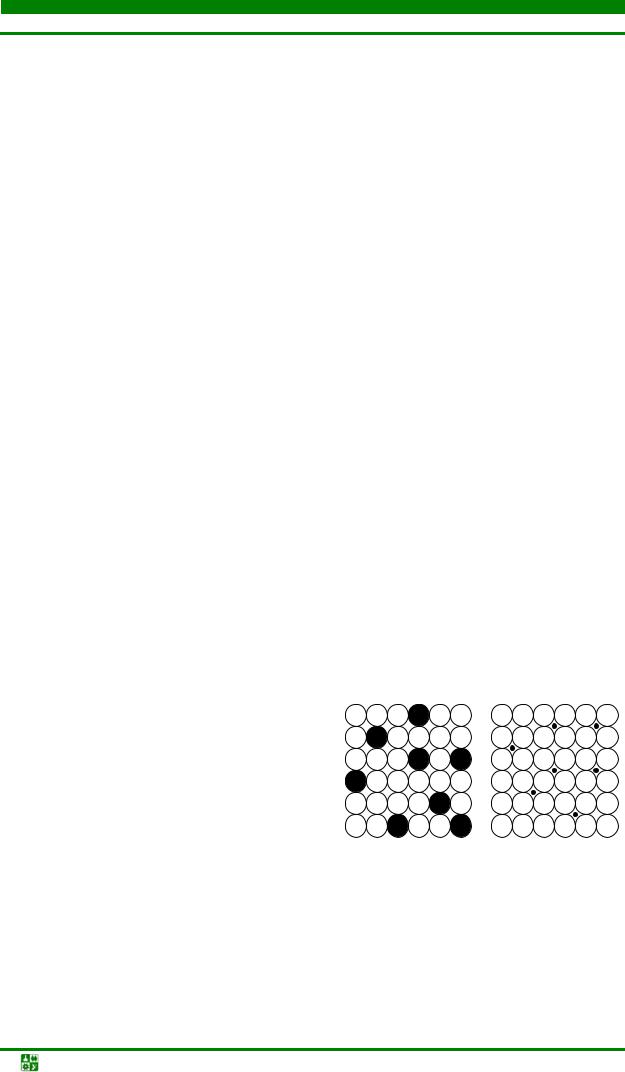
ЛАБ. Р. 5 ПОСТРОЕНИЕ ДИАГРАММЫ СОСТОЯНИЯ СВИНЕЦ–СУРЬМА. АНАЛИЗ ДИАГРАММ СОСТОЯНИЯ 2ЫХ СПЛАВОВ
Краткие теоретические сведения
Исходные компоненты, образующие сплав, могут не вступать в соединения и химические реакции друг с другом в твердом состоянии. В этом случае каждый компонент после кристаллизации сохраняет свою кристаллическую решетку. Структура сплава представляет собой смесь из зерен отдельных компонентов с пренебрежимо ничтожной взаимной растворимостью.
Твердые растворы – это кристаллы, образовавшиеся в результате распределения атомов одного компонента в кристаллической решетке другого компонента. У твердого раствора кристаллическая решетка одного из компонентов (растворителя) сохраняется, а атомы растворенного компонента располагаются в его решетке, изменяя только ее параметры. Кристаллическая решетка твердых растворов может состоять из атомов двух или нескольких компонентов. Различают твердые растворы замещения, когда атомы растворенного компонента замещают часть атомов растворителя в узлах кристаллической решетки, и твердые растворы внедрения, когда атомы растворенного компонента располагаются в междоузлиях решетки растворителя.
Твердые растворы замещения бывают неограниченные и ограниченные, а твердые растворы внедрения, как правило, с ограниченной растворимостью (рис. 5.2).
Химические соединения – это соединения, которые имеют:
– свою кристаллическую решетку, отличную от решеток исходных компонентов;
–кратное массовое соотношение элементов, что позволяет выразить их
состав формулой АтВп, где А и В – компоненты сплава, а т и п – простые числа;
–постоянную температуру плавления (диссоциации).
Вотличие от твердых растворов, химические соединения обычно образуются между компонентами, имеющими большое различие в электронном строении атомов и кристаллических решеток.
Рис. 5.2. Атомно-кристаллическая структура |
|
|
твердого раствора: а – твердый раствор заме- |
|
|
щения; б – твердый раствор внедрения |
а |
б |
Если образующиеся в сплавах химические соединения оказываются стойкими веществами, не диссоциирующими при нагреве вплоть до температуры плавления, то их принято рассматривать в качестве самостоятельных компонентов, способных образовывать сплавы с химическими элементами.
Большое число химических соединений, образующихся в металлических сплавах, отличается по некоторым особенностям от типичных химиче-
Материаловедение. Лаб. практикум |
-41- |
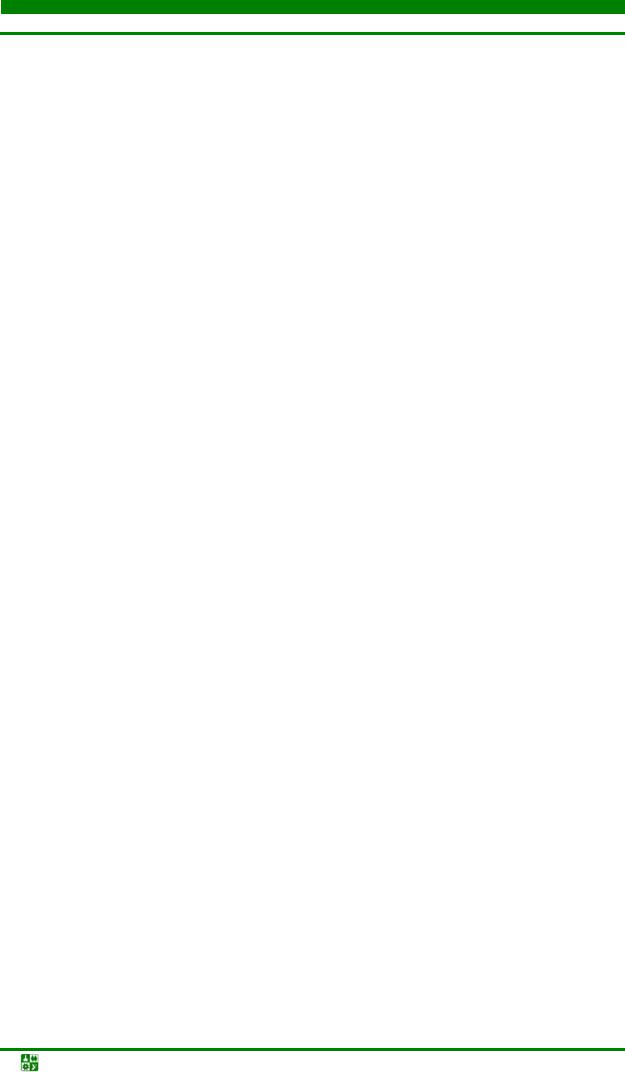
ЛАБ. Р. 5 ПОСТРОЕНИЕ ДИАГРАММЫ СОСТОЯНИЯ СВИНЕЦ–СУРЬМА. АНАЛИЗ ДИАГРАММ СОСТОЯНИЯ 2ЫХ СПЛАВОВ
Краткие теоретические сведения
ских соединений, так как не подчиняется законам валентности и не имеет постоянного состава.
В зависимости от того, как взаимодействуют компоненты сплавов между собой в твердом состоянии (обладают различной взаимной растворимостью и образуют твердые растворы, химические соединения, эвтектические смеси), различают несколько типов диаграмм состояния.
На рис. 5.3 представлена диаграмма состояния сплавов, компоненты которых ограниченно растворимы в твердом состоянии и образуют эвтектику. Линия АСВ рассматриваемой диаграммы является линией ликвидуса. Линия АDCFB – солидус. Ниже линии солидус в интервале концентрации от нуля до точки Е устойчив твердый раствор компонента В в А (α). В интервале концентрации от точки Е до точки К в твердых сплавах присутствуют кристаллы двух фаз – α- и β-твердые растворы. При концентрации компонента В больше, чем в точке К устойчива одна фаза – раствор компонента А в В (β).
В доэвтектических сплавах при охлаждении от линии АС до температуры Тэ из жидкости выделяются кристаллы α-твердого раствора. В сплавах, содержащих компонента В больше, чем в точке С, при охлаждении ниже линии СВ до температуры Тэ выделяются кристаллы β-твердого раствора.
Точка D характеризует предельную растворимость компонента В в А, а точка F – компонента А в В при температуре Тэ, а точки Е и К характеризуют предельную растворимость, соответственно, компонентов В в А и А в В при комнатной температуре.
Линия DE определяет предельную растворимость компонента В в А, которая не изменяется с понижением температуры, также не изменяется растворимость компонента А в В, что показывает линия FK.
Сплав, соответствующий точке С (50 % В), затвердевает при постоянной температуре Тэ, при этом из жидкого раствора выделяются предельно насыщенные кристаллы твердых растворов αD и βF, образуя эвтектическую смесь.
Рассмотрим для доэвтектического сплава 1 (рис. 5.3) процесс формирования структуры. Построим кривую охлаждения для сплава 1 (35 % В) от жидкого состояния до комнатной температуры, учитывая, что в точках пересечения вертикали с любой линией фазового равновесия происходит превращение, сопровождающееся тепловым эффектом.
Материаловедение. Лаб. практикум |
-42- |
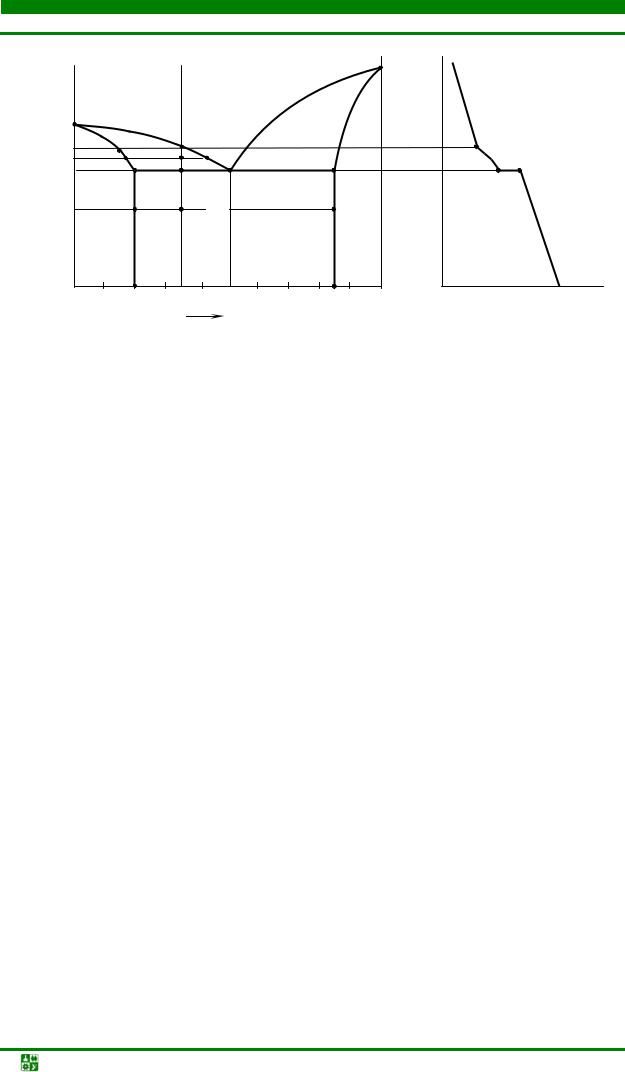
ЛАБ. Р. 5 ПОСТРОЕНИЕ ДИАГРАММЫ СОСТОЯНИЯ СВИНЕЦ–СУРЬМА. АНАЛИЗ ДИАГРАММ СОСТОЯНИЯ 2ЫХ СПЛАВОВ
|
|
|
|
|
|
Краткие теоретические сведения |
||||||
Т, °С |
|
|
|
I |
|
|
|
|
|
|
|
Т, °С |
|
|
|
|
|
|
|
|
|
|
|
|
|
|
|
|
|
|
|
Ж |
|
|
|
|
|
|
TЖ |
|
|
|
|
1 |
|
|
|
β + Ж |
|
|
|
|
1' |
α + Ж |
h |
|
|
|
|
|
|
|||
t1 |
|
|
a |
|
|
|
|
|
|
|
||
|
d |
|
|
|
|
|
|
|
|
|||
Tэ |
|
|
|
2 |
|
|
|
|
|
|
|
|
α |
|
|
|
) |
|
|
|
|
β |
|
||
t2 |
|
|
|
|
|
|
|
|
|
|||
|
m |
b |
|
+ β |
|
|
|
|
n |
|
||
|
|
|
|
α + эвт. |
α |
|
|
β + эвт. |
|
|
|
|
|
|
|
|
эвт( |
|
|
|
|
|
|||
|
|
|
|
|
|
|
|
|
|
|
|
|
|
|
E |
|
|
|
|
|
|
|
K |
|
|
0 |
10 |
|
20 |
30 |
40 |
50 |
60 |
70 |
80 |
90 |
100 |
|
|
|
|
|
|
|
|
В, % |
|
|
|
|
Ж
1
22' α + Ж
α+ эвт.
(α + β)
t, с
Рис. 5.3. Диаграмма состояния сплавов с постоянной ограниченной растворимостью компонентов в твердом состоянии
При некотором переохлаждении ниже температуры Tж, жидкость становится насыщенной по отношению к α-твердому раствору, который будет выделяться до температуры Тэ, при этом состав жидкой фазы будет изменяться по ликвидусу от точки 1 до точки С, а состав твердой фазы – по солидусу от точки 1' до точки D.
На кривой охлаждения при температуре Tж отмечается перегиб, связанный с уменьшением скорости охлаждения вследствие выделения скрытой теплоты кристаллизации. Процесс выделения кристаллов α-твердого раствора из жидкого сплава идет в интервале температур, так как система имеет одну степень свободы:
С = К + 1 – Ф = 2 + 1 – 2 = 1.
При достижении эвтектической температуры Тэ кристаллы α достигают предельной концентрации αD (точки D), а жидкая фаза получает эвтектический состав Жс (точки С).
В этих условиях из жидкой фазы кристаллизуются предельно насыщенные твердые растворы αD и βF, образуя эвтектику:
Жс → Э (αD + βF).
Эвтектическая реакция протекает изотермически и при постоянном составе реагирующих фаз, так как в двухкомпонентном сплаве одновременно сосуществуют три фазы (Жс, αD и βF). Число степеней свободы системы равно нулю:
С = K + 1– Ф = 2 + 1 – 3 = 0,
поэтому на кривой охлаждения (рис. 5.3) образуется площадка.
После затвердевания сплав I состоит из первичных кристаллов α и эвтектики (α + β).
Материаловедение. Лаб. практикум |
-43- |
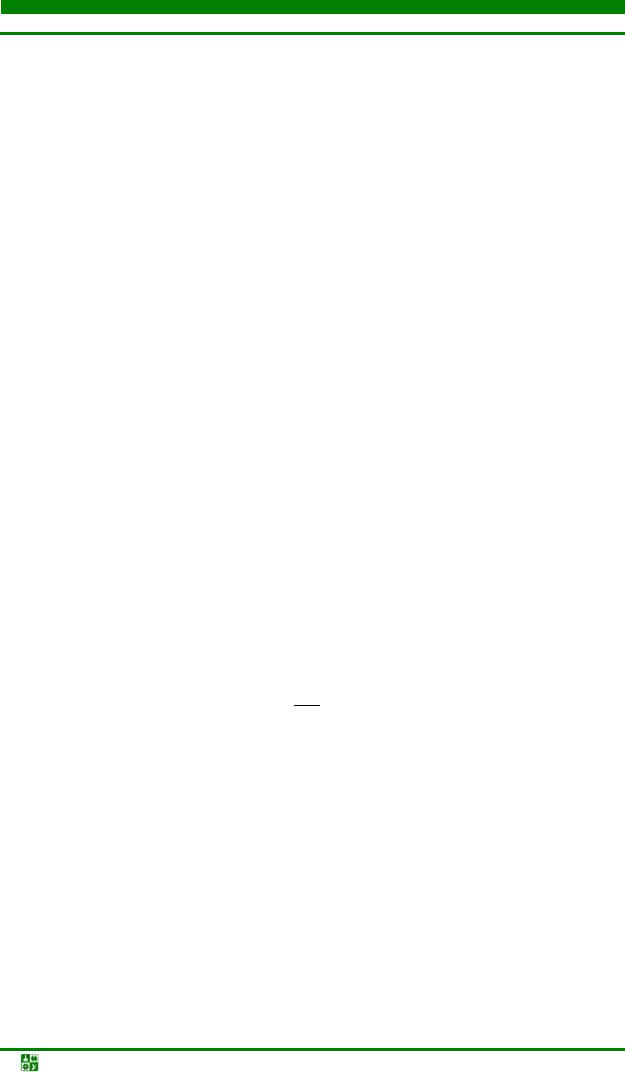
ЛАБ. Р. 5 ПОСТРОЕНИЕ ДИАГРАММЫ СОСТОЯНИЯ СВИНЕЦ–СУРЬМА. АНАЛИЗ ДИАГРАММ СОСТОЯНИЯ 2ЫХ СПЛАВОВ
Краткие теоретические сведения
В любой точке на диаграмме состояния, которая показывает фазовый состав сплава при данной температуре, можно определить весовое количество фаз. Если такая точка попадает в область однофазного состояния, то весовое количество данной фазы составляет 100 %, а её состав соответствует исходному составу сплава. Если точка попадает в область двухфазного равновесия, то здесь для определения состава фаз через эту точку необходимо провести горизонталь (коноду). Проекции точек пересечения на ось концентрации и дают состав фаз.
Для определения весового состава фаз в двухфазной области необходимо воспользоваться правилом рычага. Согласно правилу отрезки, которые получают на горизонтали между данной точкой сплава и точками пересечения горизонтали с линиями диаграммы состояния, обратно пропорциональны количеству фаз.
Рассмотрим сплав I в точке а (рис. 5.3) при температуре t1. Для этого проведем горизонтальную прямую dh через точку а. Ее левая точка d лежит на линии солидус и определяет состав твердой фазы при температуре t1. Справа точка h, лежащая на линии ликвидус, показывает состав жидкости, находящейся в равновесии с α-фазой. Используя правило рычага, можно определить количество кристаллов твердой фазы в точке а:
Qα = hadh100 %,
а количество жидкой фазы в этой точке – по формуле
Qæ = dadh100 %.
Также правило рычага используют для определения количественного соотношения фаз в точке b (при температуре t2). Тогда весовое количество твердого раствора α составит
Qα = mnbn 100 %,
а количество твердого раствора β
Qβ = bmmn100 %.
Состав твердого раствора α при температуре t2 определится проекцией точки m, асостав твердого раствора β – проекцией точки n на ось концентраций.
Материаловедение. Лаб. практикум |
-44- |

ЛАБ. Р. 5 ПОСТРОЕНИЕ ДИАГРАММЫ СОСТОЯНИЯ СВИНЕЦ–СУРЬМА. АНАЛИЗ ДИАГРАММ СОСТОЯНИЯ 2ЫХ СПЛАВОВ
Порядоквыполненияработы
1.Используя данные, полученные в лабораторной работе 4, построить диаграмму состояния Рb−Sb. Температура кристаллизации чистых металлов для Рb – 327 °С, для Sb – 631 °С.
2.Для изучения микроструктуры пяти исследуемых сплавов использовать микроскоп МИМ-7. Микрошлиф установить на предметном столике микроскопа. Наводку на фокус осуществить микрометрическим винтом, расположенным справа в верхней части микроскопа. Микрошлифы зарисовать в кружках d 25 или 50 мм. На микрошлифе стрелками указать структурные составляющие.
3.Начертить диаграмму состояния, построить кривую охлаждения из области жидкого состояния до комнатной температуры (с применением правила фаз).
4.Описать фазовые превращения при охлаждении и структуру сплава при комнатной температуре.
5.Пользуясь правилом отрезков, определить состав и количественное соотношение фаз для любой температуры, лежащей между линиями ликвидуса и солидуса.
Пункты 3–5 выполнять в соответствии с индивидуальным заданием по указанию преподавателя. Ниже приведены вид диаграмм и состав спла-
вов (рис. 5.4, рис. 5.5, рис. 5.6, рис. 5.7, рис. 5.8, рис. 5.9, рис. 5.10, рис. 5.11, рис. 5.12, рис. 5.13):
№ п/п |
Диаграмма |
Состав |
№ п/п |
Диаграмма |
Состав |
1 |
Al–Cu |
0,7 % Cu |
14 |
Pb–Sn |
5 % Sn |
2 |
Al–Cu |
5 % Cu |
15 |
Pb–Sn |
30 % Sn |
3 |
Al–Cu |
15 % Cu |
16 |
Pb–Sn |
90 % Sn |
4 |
Cd–Zn |
8 % Zn |
17 |
Mg–Cа |
40 % Cа |
5 |
Cd–Zn |
50 % Zn |
18 |
Mg–Cа |
60 % Cа |
6 |
Cu–Ag |
5 % Ag |
19 |
Al–Si |
10 % Si |
7 |
Cu–Ag |
15 % Ag |
20 |
Al–Si |
45 % Si |
8 |
Cu–Ag |
30 % Ag |
21 |
Al–Si |
70 % Si |
9 |
Cu–Ag |
85 % Ag |
22 |
Cd–Zn |
90 % Zn |
10 |
Cu–Ag |
95 % Ag |
23 |
Mg–Cа |
10 % Cа |
11 |
Cu–As |
2 % As |
24 |
Mg–Cа |
90 % Cа |
12 |
Cu–As |
10 % As |
25 |
Cd–Zn |
3 % Zn |
13 |
Cu–As |
25 % As |
|
|
|
Материаловедение. Лаб. практикум |
-45- |
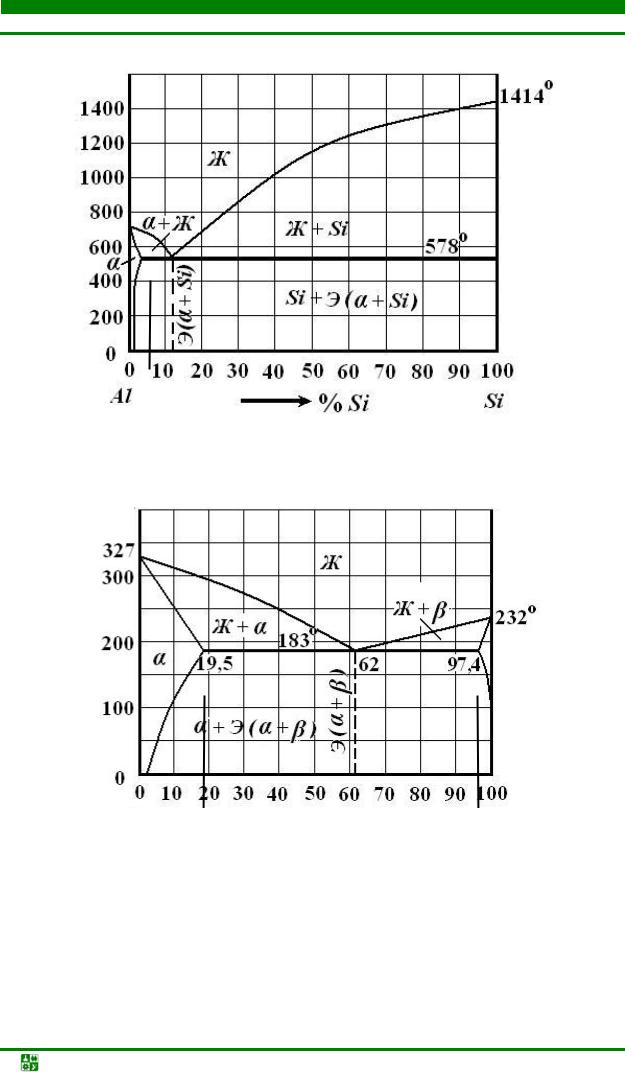
ЛАБ. Р. 5 ПОСТРОЕНИЕ ДИАГРАММЫ СОСТОЯНИЯ СВИНЕЦ–СУРЬМА. АНАЛИЗ ДИАГРАММ СОСТОЯНИЯ 2ЫХ СПЛАВОВ
Порядок выполнения работы
Т, оС
Al |
→ % Si |
Si |
|
|
|
Рис. 5.4. Диаграмма состояния системы Al–Si
Т, оС
Pb |
→ % Sn |
Sn |
Рис. 5.5. Диаграмма состояния системы Pb–Sn
Материаловедение. Лаб. практикум |
-46- |
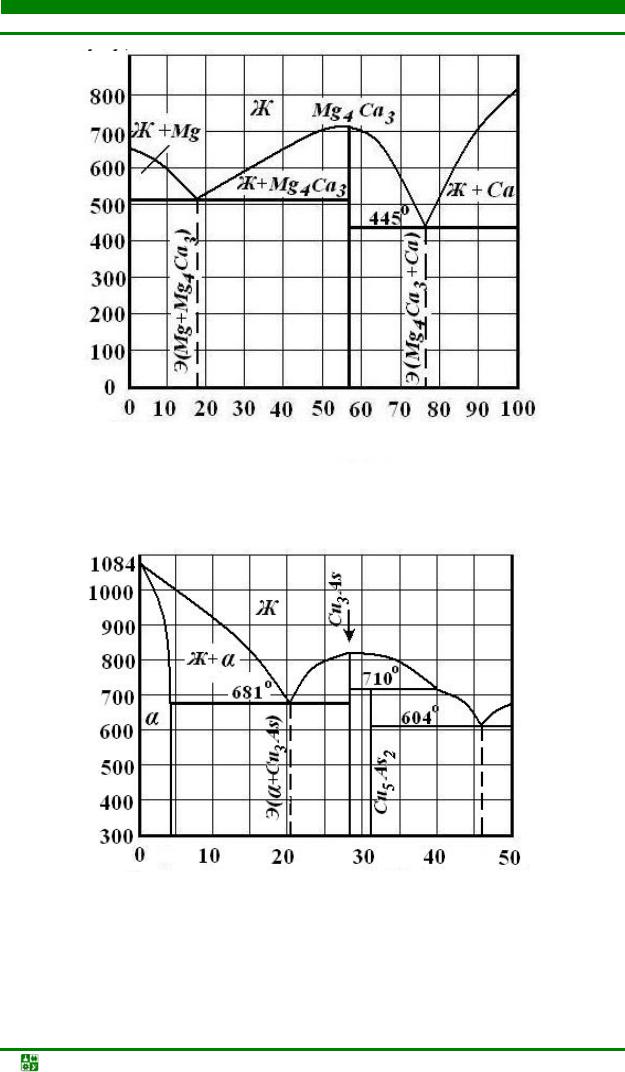
ЛАБ. Р. 5 ПОСТРОЕНИЕ ДИАГРАММЫ СОСТОЯНИЯ СВИНЕЦ–СУРЬМА. АНАЛИЗ ДИАГРАММ СОСТОЯНИЯ 2ЫХ СПЛАВОВ
Порядок выполнения работы
Т, оС
Mg |
→ % Ca |
Ca |
Рис. 5.6. Диаграмма состояния системы Mg–Ca
Т, оС
Cu |
→ % As |
As |
Рис. 5.7. Диаграмма состояния системы Cu–As
Материаловедение. Лаб. практикум |
-47- |
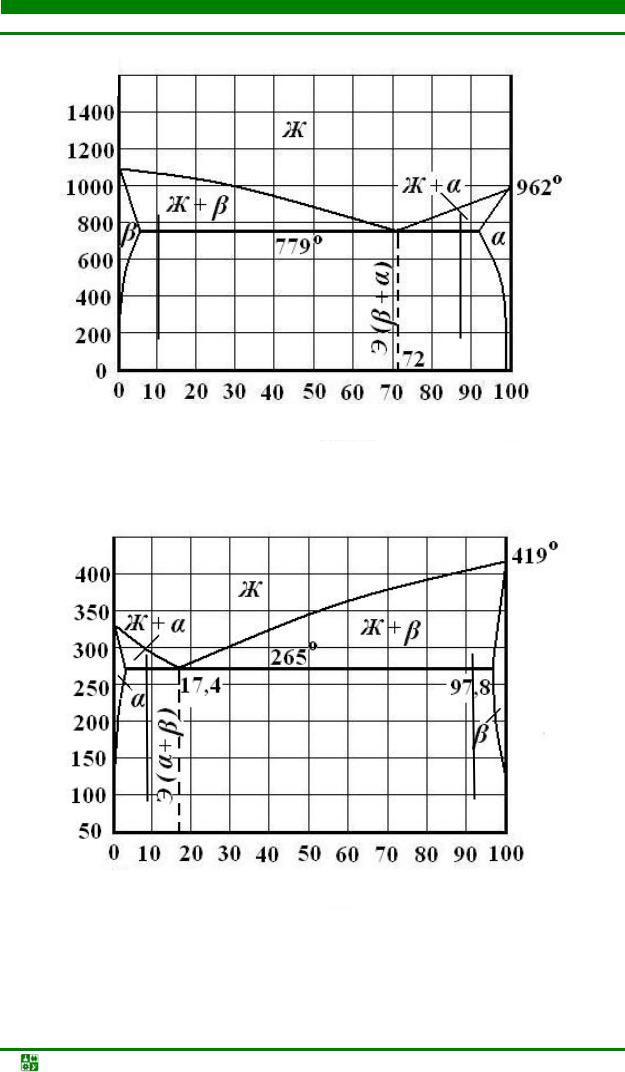
ЛАБ. Р. 5 ПОСТРОЕНИЕ ДИАГРАММЫ СОСТОЯНИЯ СВИНЕЦ–СУРЬМА. АНАЛИЗ ДИАГРАММ СОСТОЯНИЯ 2ЫХ СПЛАВОВ
Порядок выполнения работы
Т, оС
Cu |
→ % Ag |
Ag |
Рис. 5.8. Диаграмма состояния системы Cu–Ag
Т, оС
Cd |
→ % Zn |
Zn |
Рис. 5.9. Диаграмма состояния системы Cd–Zn
Материаловедение. Лаб. практикум |
-48- |

ЛАБ. Р. 5 ПОСТРОЕНИЕ ДИАГРАММЫ СОСТОЯНИЯ СВИНЕЦ–СУРЬМА. АНАЛИЗ ДИАГРАММ СОСТОЯНИЯ 2ЫХ СПЛАВОВ
Порядок выполнения работы
Т, оС
Al |
→ % Cu |
CuAl2 |
Рис. 5.10. Диаграмма состояния системы Al–Cu
Т, оС
Cu |
→ % Ni |
Ni |
Рис. 5.11. Диаграмма состояния системы Cu–Ni
Материаловедение. Лаб. практикум |
-49- |

ЛАБ. Р. 5 ПОСТРОЕНИЕ ДИАГРАММЫ СОСТОЯНИЯ СВИНЕЦ–СУРЬМА. АНАЛИЗ ДИАГРАММ СОСТОЯНИЯ 2ЫХ СПЛАВОВ
Порядок выполнения работы
T, °C
1000
900
800
700
658
600
500
|
|
|
α |
Ж + |
α |
|||
400 |
|
|||||||
|
2,8 |
|||||||
|
|
|
|
|
|
|||
|
|
|
|
|
|
|
|
|
|
|
|
|
|
|
α + Э |
||
300 |
|
|
|
|
||||
|
α+ Ge |
|
+ Ge |
|||||
|
|
|
|
|||||
|
|
|
|
|
|
|||
200 |
|
|
|
|||||
|
0 |
|
10 |
20 |
Al
959°
Ж
Ж + Ge
|
|
|
|
|
424° |
|
|
|
|
|
|
|
|
|
||
|
|
|
|
|
|
|
|
|
|
|
|
|
|
|
|
|
+ α) |
|
|
|
|
|
|
|
|
|
|
|
|
|
|
|
|
|
|
Ge + Э(Ge + α) |
|
|
|
|
|
|||||||||
Э(Ge |
|
|
|
|
|
|
|
|
|
|
|
|
|
|
|
|
|
|
|
|
|
|
|
|
|
|
|
|
|
|
|
|
|
|
|
|
|
|
|
|
|
|
|
|
|
|
||||
30 |
40 |
|
50 |
60 |
70 |
80 |
90 |
100 |
||||||||
|
|
→ % Ge |
|
|
|
|
|
|
Ge |
Рис. 5.12. Диаграмма состояния системы Al–Ge
T, °C
600
500
Ж + α
400 |
|
|
|
|
|
|
|
|
|
327 |
|
|
|
|
|
|
|
|
|
300 |
|
|
|
|
250° |
|
|||
|
α |
|
|
|
|
|
|
|
|
|
|
|
|
|
|
|
|
||
200 |
|
|
|
|
) |
|
|
|
|
|
|
|
|
|
|
2 |
|
|
|
|
|
|
|
|
|
PbMg |
|
|
|
|
|
|
|
|
|
|
|
|
|
100 |
|
|
|
|
|
|
|
||
|
|
|
|
Э(α + |
|
|
|
||
|
|
|
|
|
|
|
|
|
|
|
0 |
|
|
|
|
|
|
|
|
|
|
|
|
|
|
|
|
|
|
|
|
0 |
|
|
10 |
|
20 |
Pb
Ж |
650° |
|
PbMg2
468° Ж + β
β
|
+ β) |
|
|
|
|
|
|
|
|
|
|
|
|
|
||
|
2 |
|
|
|
|
|
|
|
|
|
|
|
|
|
|
|
|
Э(PbMg |
|
|
|
|
|
|
|
|
|
|
|
|
|
||
|
|
|
|
|
|
|
|
|
|
|
|
|
|
|
|
|
|
32 |
|
|
|
|
|
|
|
|
|
|
|
|
|
|
|
|
|
|
|
|
|
|
|
|
|
|
|
|
|
|
|
|
30 |
40 |
% |
50 |
60 |
70 |
80 |
90 |
100 |
||||||||
|
|
→ |
Mg |
|
|
|
|
|
|
|
|
Mg |
Рис. 5.13. Диаграмма состояния системы Pb–Mg
Материаловедение. Лаб. практикум |
-50- |

ЛАБОРАТОРНАЯ РАБОТА 6 ИЗУЧЕНИЕ МИКРОСТРУКТУРЫ
И СВОЙСТВ УГЛЕРОДИСТЫХ СТАЛЕЙ
Цельработы
Изучить превращения в сплавах системы железо–цементит и структуры сталей различного состава в равновесном состоянии. Определить содержание углерода в исследуемых сталях и их марки.
Приборы, материалыиинструмент
Микроскоп МИМ-7; комплект микрошлифов сталей.
Краткиетеоретическиесведения
Микроструктуру сталей изучают в равновесном состоянии, когда процессы фазовых превращений полностью закончились, что достигается только при очень медленном охлаждении. Структурные составляющие железоуглеродистых сплавов в равновесном состоянии определяют по диаграмме состояния железо–цементит. Особенность диаграммы – наличие на оси составов двух шкал, показывающих содержание углерода и цементита (рис. 6.1).
Железоуглеродистые сплавы, содержащие углерода менее 2,14 %, на-
зываются сталями, а более 2,14 % – чугунами.
Структура стали в равновесном состоянии, зависит от содержания в ней углерода. После полного отжига в углеродистой стали присутствуют следующие фазы и структурные составляющие: феррит, цементит, перлит.
Феррит (Ф) – твердый раствор углерода в α-железе. Он является продуктом диффузионного превращения аустенита при его охлаждении ниже температур линии GPSK (рис. 6.1).
Под микроскопом феррит наблюдается в виде светлых зерен неодинаковой яркости (рис. 6.2). Последнее объясняется неодинаковой травимостью вследствие анизотропии свойств феррита. Растворимость углерода в феррите изменяется с изменением температуры, что отражает на диаграмме состояния (рис. 6.1) линия GPQ. Максимальное содержание углерода в феррите при комнатной температуре достигает 0,006 %.
Феррит является пластичной фазой. Его относительное удлинение δ = 50 %, твердость зависит от концентрации углерода и других растворенных примесей и изменяется в пределах НВ 450–800.
Феррит обладает ферромагнитными свойствами, в парамагнитное состояние переходит при температуре 768 °С.
Материаловедение. Лаб. практикум |
-51- |
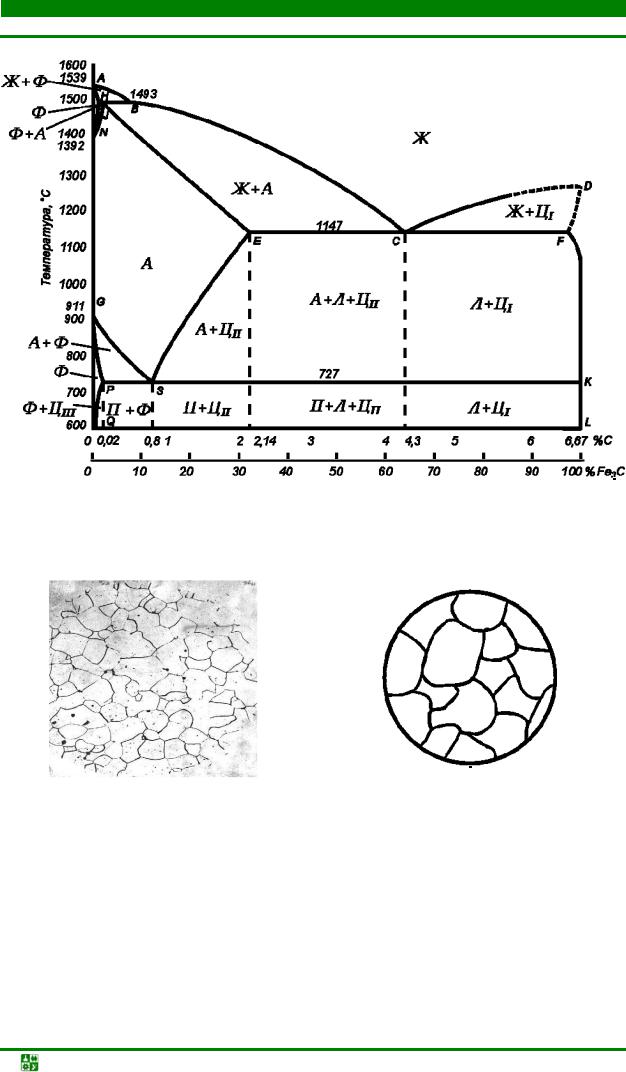
ЛАБОРАТОРНАЯ РАБОТА 6 ИЗУЧЕНИЕ МИКРОСТРУКТУРЫ И СВОЙСТВ УГЛЕРОДИСТЫХ СТАЛЕЙ
Краткие теоретические сведения
Рис. 6.1. Диаграмма состояния сплавов системы железо–углерод
а |
б |
Рис. 6.2. Структура феррита: а – фотография микроструктуры; б – схема зарисовки
Цементит (Ц) – химическое соединение углерода с железом – карбид железа Fe3C. Кристаллическая решетка цементита очень сложная ромбическая. Цементит обладает металлическим блеском, тепло- и электропроводностью, малыми магнитными свойствами до температуры 210 °С.
Температура плавления при атмосферном давлении у цементита не установлена, так как он является неустойчивым химическим соединением и
Материаловедение. Лаб. практикум |
-52- |
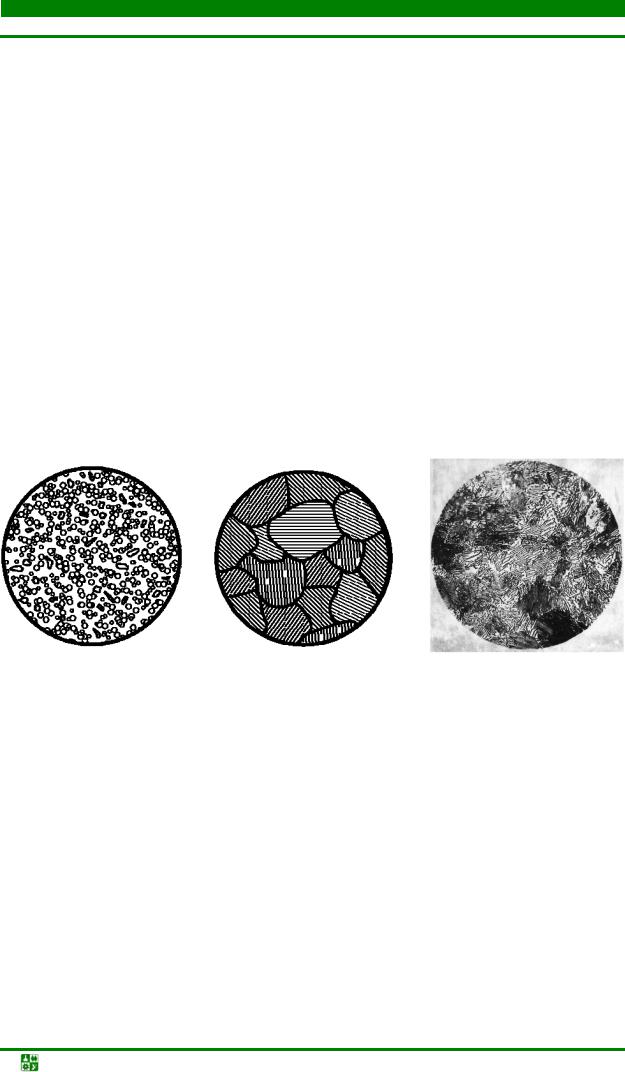
ЛАБОРАТОРНАЯ РАБОТА 6 ИЗУЧЕНИЕ МИКРОСТРУКТУРЫ И СВОЙСТВ УГЛЕРОДИСТЫХ СТАЛЕЙ
Краткие теоретические сведения
при высоких температурах распадается на железо и углерод. В зависимости от условий охлаждения аустенита, цементит может иметь зернистую или пластинчатую форму.
Цементитная сетка из пластинок, охватывающих зерна перлита в структуре заэвтектоидной стали, снижает ее пластичность и прочность и увеличивает твердость. Цементит – самая твердая составляющая, НВ = 8 000. Его пластичность практически равна нулю. Поэтому с возрастанием количества цементита в стали, при увеличении концентрации в ней углерода твердость стали возрастает, а пластичность падает.
Перлит (П) – эвтектоидная смесь из кристаллов цементита и феррита, образующаяся при диффузионном распаде аустенита в результате медленного охлажденияпоследнего. Содержаниеуглеродавперлите0,8 % (точка S, рис. 6.1).
При изготовлении шлифа пластинки цементита, более твердого, чем феррит, сошлифовываются меньше и поэтому выступают из остальной массы перлита. Феррит как мягкая составляющая сошлифовывается больше, что усиливается при травлении. Поэтому при косом освещении перлит под микроскопом просматривается в виде темных и светлых полосок.
а |
б |
в |
Рис. 6.3. Структура перлита: а – схема зарисовки зернистого перлита; б – схема зарисовки пластинчатого перлита; в – фотография микроструктуры пластинчатого перлита
В зависимости от формы цементита различают:
а) зернистый перлит, в котором цементит имеет форму зерен, расположенных в феррите (рис. 6.3, а);
б) пластинчатый перлит, в котором цементит и феррит имеют форму пластин; последние образуют смесь чередующихся пластин цементита (рис. 6.3, б, в) и феррита.
Форма и размер цементитных частиц в перлите существенно влияют на свойства стали. Так, например, зернистый перлит более пластичен и имеет меньшую твердость, чем пластинчатый. С уменьшением размера цементитных частиц твердость и прочность перлита возрастают.
Материаловедение. Лаб. практикум |
-53- |

ЛАБОРАТОРНАЯ РАБОТА 6 ИЗУЧЕНИЕ МИКРОСТРУКТУРЫ И СВОЙСТВ УГЛЕРОДИСТЫХ СТАЛЕЙ
Краткие теоретические сведения
Обыкновенный пластинчатый перлит имеет предел прочности σв = 820 МПа и относительное удлинение δ = 15 %, а крупнопластинчатый – σв = 550 МПа и δ = 5 %. Зернистый перлит имеет σв = 630 МПа и δ = 20 %.
Твердость пластинчатого перлита НВ 2000–2500, а зернистого – НВ 1600–2200.
На микрошлифе в обычном оптическом микроскопе при малом увеличении (до 200 крат) перлит наблюдается в виде темных зерен, в которых не видно ни пластин, ни зерен цементита, так как размер цементитных частиц очень мал.
Структура стали в равновесном состояния зависит от содержания в ней углерода.
Техническое железо содержит не более 0,02 % углерода и является как двухфазным, так и однофазным сплавом.
Технически чистое железо называют армко-железом. Его получают в больших количествах промышленным способом с суммарным содержанием примесей около 0,15 %.
Сплавы с содержанием углерода до 0,006 % состоят из феррита и в интервале концентрации 0,006–0,02 % – из феррита и цементита третичного, который выделяется по границам ферритных зерен вследствие изменения растворимости углерода в феррите при изменении температуры.
а |
б |
Рис. 6.4. Доэвтектоидная сталь, в структуре перлит и феррит: а – фотография микроструктуры; б – схема зарисовки
Доэвтектоидные стали содержат от 0,02 до 0,8 % углерода. Стали состоят из феррита (Ф) (светлые зерна) и перлита (П) (темные зерна) (рис. 6.4). Количество перлита увеличивается, а феррита – уменьшается пропорционально увеличению содержания углерода. По соотношению площадей, занимаемых в исследуемой структуре перлитом и ферритом, что с определенной степенью точности соответствует соотношению их объемов, можно
Материаловедение. Лаб. практикум |
-54- |
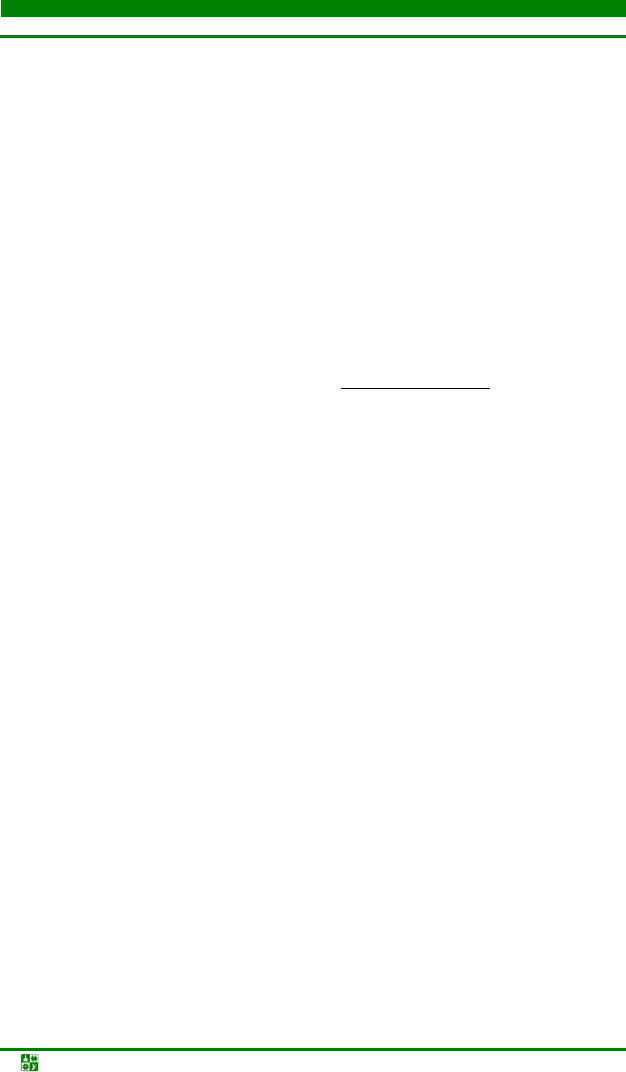
ЛАБОРАТОРНАЯ РАБОТА 6 ИЗУЧЕНИЕ МИКРОСТРУКТУРЫ И СВОЙСТВ УГЛЕРОДИСТЫХ СТАЛЕЙ
Краткие теоретические сведения
определить содержание углерода в стали. Для того чтобы подсчитать содержание углерода в доэвтектоидной стали, необходимо определить площадь fп, занимаемую перлитом на микрошлифе относительно всего поля зрения, и умножить на содержание углерода в перлите (0,8 % – см. рис. 6.1).
Пример: площадь, занятая перлитом, fп = 0,6 (относительно 1). Тогда содержание углерода в данном образце будет: 0,8·0,6 = 0,48 %.
Зная процентное содержание углерода, можно определить марку стали (табл. 6.1, табл. 6.2, табл. 6.3).
Таблица 6.1
Сталь углеродистая обыкновенного качества по ГОСТ 380-88
Марки стали |
Массовая доля элементов, % |
|
|||
|
|
|
|
|
|
углерода |
марганца |
|
|
кремния |
|
|
|
|
|||
|
|
– |
|
|
|
Ст0 |
Не более 0,23 |
|
|
– |
|
Ст1кп |
0,06–0,12 |
0,25–0,50 |
|
Не более 0,05 |
|
Ст1пс |
0,06–0,12 |
0,25–0,50 |
|
0,05–0,15 |
|
Ст1сп |
0,06–0,12 |
0,25–0,50 |
|
0,15–0,30 |
|
Ст2кп |
0,09–0,15 |
0,25–0,50 |
|
Не более 0,05 |
|
Ст2пс |
0,09–0,15 |
0,25–0,50 |
|
0,05–0,15 |
|
Ст2сп |
0,09–0,15 |
0,25–0,50 |
|
0,15–0,30 |
|
Ст3кп |
0,14–0,22 |
0,30–0,60 |
|
Не более 0,05 |
|
Ст3пс |
0,14–0,22 |
0,40–0,65 |
|
0,05–0,15 |
|
Ст3сп |
0,14–0,22 |
0,40–0,65 |
|
0,15–0,30 |
|
Ст3Гпс |
0,14–0,22 |
0,80–1,10 |
|
Не более 0,15 |
|
Ст3Гсп |
0,14–0,20 |
0,80–1,10 |
|
0,15–0,30 |
|
Ст4кп |
0,18–0,27 |
0,40–0,70 |
|
Не более 0,05 |
|
Ст4пс |
0,18–0.27 |
0,40–0,70 |
|
0,05–0,15 |
|
Ст4сп |
0,18–0,27 |
0,40–0,70 |
|
0,15–0,30 |
|
Ст5пс |
0,28–0,37 |
0,50–0,80 |
|
0,05–0,15 |
|
Ст5сп |
0,28–0,37 |
0,50–0,80 |
|
0,15–0,30 |
|
Ст5Гпс |
0,22–0,30 |
0,80–1,20 |
|
Не более 0,15 |
|
Ст6пс |
0,38–0,49 |
0,50–0,80 |
|
0,05–0,15 |
|
Ст6сп |
0,38–0,49 |
0,50–0,80 |
|
0,15–0,30 |
Примечания: 1. Буквы Ст обозначают «Сталь», цифры – условный номер марки в зависимости от химического состава стали, буквы кп, пс, сп – способ раскисления стали (кп
–кипящая, пс – полуспокойная, сп – спокойная сталь).
2.Способ раскисления, если он не указан в заказе, устанавливает изготовитель.
3.Массовая доля серы в стали всех марок, кроме Ст0, должна быть не более 0,05 %, фосфора не более 0,04 %, в стали марки Ст0 серы – не более 0,06 %, фосфора – не более
0,07 %.
Материаловедение. Лаб. практикум |
-55- |
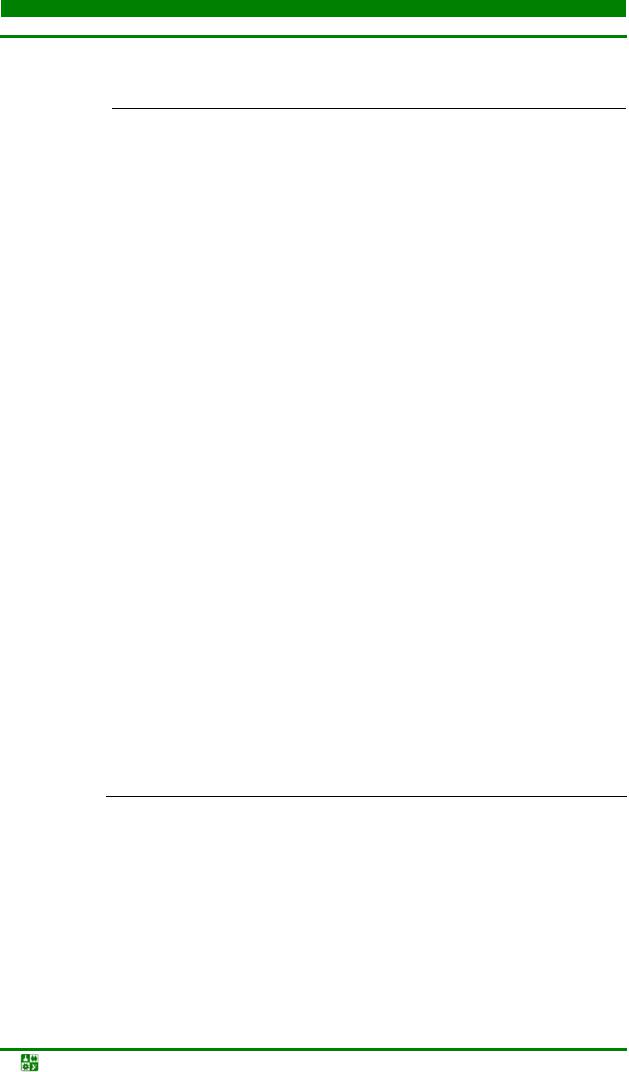
ЛАБОРАТОРНАЯ РАБОТА 6 ИЗУЧЕНИЕ МИКРОСТРУКТУРЫ И СВОЙСТВ УГЛЕРОДИСТЫХ СТАЛЕЙ
Краткие теоретические сведения
Таблица 6.2 Сталь углеродистая качественная конструкционная по ГОСТ 1050-88
Марка стали |
|
Массовая доля элементов, % |
|
||
|
|
|
|
||
углерода |
кремния |
марганца |
хрома, не более |
||
|
|||||
|
|
|
|
|
|
05кп |
Не более 0,06 |
Не более 0,03 |
Не более 0,40 |
0,10 |
|
08кп |
0,05–0,12 |
Не более 0,03 |
0,25–0,50 |
0,10 |
|
08пс |
0,05–0,11 |
0,05–0,17 |
0,35–0,65 |
0,10 |
|
08 |
0,05–0,12 |
0,17–0,37 |
0,35–0,65 |
0,10 |
|
10кп |
0,07–0,14 |
Не более 0,07 |
0,25–0,50 |
0,15 |
|
10пс |
0.07–0.14 |
0,5–0,17 |
0,35–0,65 |
0,15 |
|
10 |
0,07–0,14 |
0,17–0,37 |
0,35–0,65 |
0,15 |
|
11кп |
0,05–0,12 |
Не более 0,06 |
0,30–0,50 |
0,15 |
|
15кп |
0,12–0,19 |
Не более 0,07 |
0,25–0,50 |
0,25 |
|
15пс |
0,12–0,19 |
0,05–0,17 |
0,35–0,65 |
0,25 |
|
15 |
0,12–0,19 |
0,17–0,37 |
0,35–0,65 |
0,25 |
|
18кп |
0,12–0,20 |
Не более 0,06 |
0,30–6,50 |
0,15 |
|
20кп |
0,17–0,24 |
Не более 0,07 |
0,25–0,50 |
0,25 |
|
20пс |
0,37–0,24 |
0,05–0,17 |
0,35–0,65 |
0,25 |
|
20 |
0,17–0,24 |
0,17–0,37 |
0,35–0,65 |
0,25 |
|
25 |
0,22–0,30 |
0,17–0,37 |
0,50–0,80 |
0,25 |
|
30 |
0,27–0,35 |
0,17–0,37 |
0,50–0,80 |
0,25 |
|
35 |
0,32–0,40 |
0,17–0,37 |
0,50–0,80 |
0,25 |
|
40 |
0,37–0,45 |
0,17–0,37 |
0,50–0,80 |
0,25 |
|
45 |
0,42–0,5 |
0,17–0,37 |
0,50–0,80 |
0,25 |
|
50 |
0,47–0,55 |
0,17–0,37 |
0,50–0,80 |
0,25 |
|
55 |
0,52–0,60 |
0,17–0,37 |
0,50–0,80 |
0,25 |
|
58(55пс) |
0,55–0,63 |
0,10–0,30 |
Не более 0,20 |
0,15 |
|
60 |
0,57–0,65 |
0,17–0,37 |
0,50–0,80 |
0,25 |
Примечания: 1. Цифры в обозначении марки показывают среднюю массовую долю углерода в сотых долях процента.
2. Массовая доля серы в сталях должна быть не более 0,040 %, фосфора – не более
0,035 %.
|
|
|
|
|
|
Таблица 6.3 |
|
|
Инструментальная нелегированная сталь по ГОСТ 1435-90 |
||||||
|
|
|
Массовая доля элемента, % |
|
|||
Марка стали |
|
|
|||||
|
|
|
|
|
|||
углерода |
кремния |
марганца |
серы |
фосфора |
|||
|
|
||||||
У7 |
|
0,65–0,74 |
0,17–0,33 |
0,17–0,33 |
0,028 |
0,030 |
|
У8 |
|
0,75–0,84 |
0,17–0,33 |
0,17–0,33 |
0,028 |
0,030 |
|
У8Г |
|
0,80–0,90 |
0,17–0,33 |
0,33–0,58 |
0,028 |
0,030 |
|
У9 |
|
0,85–0,94 |
0,17–0,33 |
0,17–0,33 |
0,028 |
0,030 |
|
У10 |
|
0,85–1,04 |
0,17–0,33 |
0,17–0,33 |
0,028 |
0,030 |
|
У11 |
|
1,05–1,14 |
0,17–0,33 |
0,17–0,33 |
0,028 |
0,030 |
|
У12 |
|
1,15–1,24 |
0,17–0,33 |
0,17–0,33 |
0,028 |
0,030 |
Материаловедение. Лаб. практикум |
-56- |
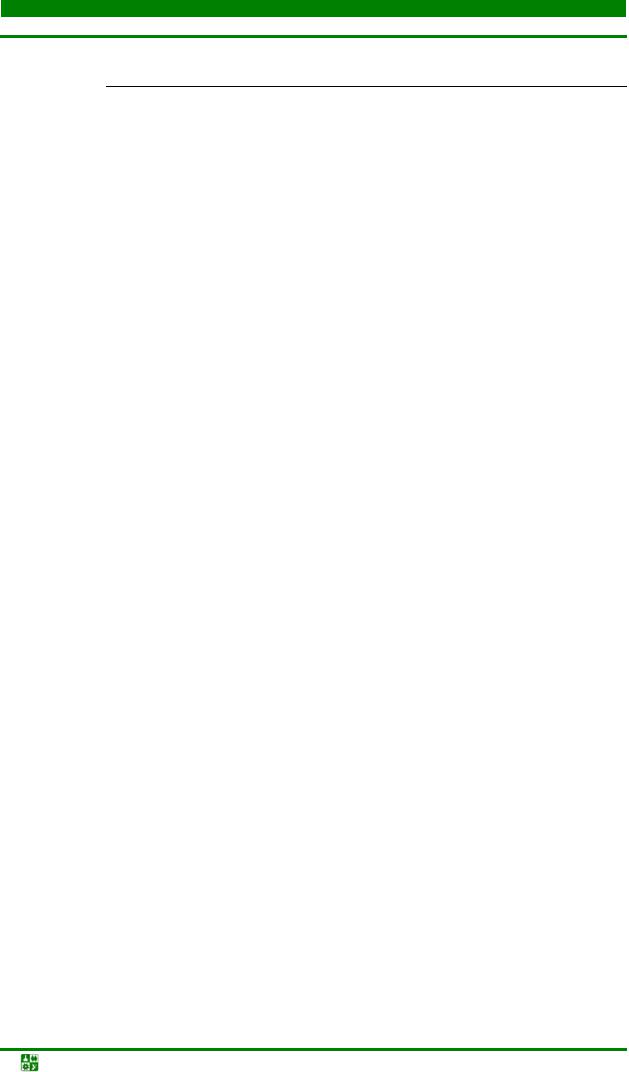
ЛАБОРАТОРНАЯ РАБОТА 6 ИЗУЧЕНИЕ МИКРОСТРУКТУРЫ И СВОЙСТВ УГЛЕРОДИСТЫХ СТАЛЕЙ
Краткие теоретические сведения
Продолжение табл. 6.3
Марка стали |
|
Массовая доля элемента, % |
|
|||
углерода |
кремния |
марганца |
серы |
фосфора |
||
|
||||||
У13 |
1,25–1,35 |
0,17–0,33 |
0,17–0,33 |
0,028 |
0,030 |
|
У7А |
0,65–0,74 |
0,17–0,33 |
0,17–0,28 |
0,018 |
0,025 |
|
У8А |
0,75–0,84 |
0,17–0,33 |
0,17–0,28 |
0,018 |
0,025 |
|
У8ГА |
0,80–0,90 |
0,17–0,33 |
0,33–0,58 |
0,018 |
0,025 |
|
У9А |
0,85–0,94 |
0,17–0,33 |
0,17–0,28 |
0,018 |
0,025 |
|
У10А |
0,95–1,04 |
0,17–0,33 |
0,17–0,28 |
0,018 |
0,025 |
|
У11А |
1,05–1,14 |
0,17–0,33 |
0,17–0,28 |
0,018 |
0,025 |
|
У12А |
1,15–1,24 |
0,17–0,33 |
0,17–0,28 |
0,018 |
0,025 |
|
У13А |
1,25–1,35 |
0,17–0,33 |
0,17–0,28 |
0,018 |
0,025 |
Примечание. В обозначении марки стали: буква У – углеродистая; следующая за ней цифра – средняя массовая доля углерода в десятых долях процента; Г – повышенная массовая доля марганца, А – высококачественная сталь.
Эвтектоидная сталь содержит 0,8 % углерода, в ее структуру входит только перлит (рис. 6.3).
Заэвтектоидные стали содержат углерода более 0,8 %. Они состоят из перлита и цементита вторичного, который расположен обычно в виде светлой сетки или светлых вытянутых зерен (цепочки) по границам зерен перлита
(рис. 6.5).
Содержание цементита вторичного в структуре заэвтектоидной стали возрастает с увеличением концентрации углерода от 3,4 % (при % С = 1 %) до 20,4 (при % С = 2 %) от всей массы сплава. Если известно относительное содержание вторичного цементита на микрошлифе, можно определить содержание углерода в данном образце. Для этого к углероду, содержащемуся в перлите, нужно добавить углерод, содержащийся во вторичном цементите. Например, площадь, занятая вторичным цементитом, fц = 0,04 (относительно 1), тогда площадь, занятая перлитом, fп = 0,96 относительно площади микрошлифа.
Содержание углерода определяют следующим образом: 0,04·6,67 % + 0,96·0,8 % = 1,1 %.
Влияние углерода на свойства стали в основном определяются свойствами цементита и связано с изменением содержания основных структурных составляющих – феррита и цементита. При увеличении углерода до 1,2 % (рис. 6.6) возрастают прочность σв, твердость HB, предел текучести σт, при этом снижаются вязкость KCU и характеристики пластичности – относительное удлинение (δ, %) и относительное сужение (ψ, %). Технологические свойства, такие как деформируемость, свариваемость и др., зависят также от содержания углерода. Хорошей свариваемостью и пластичностью отличаются низкоуглеродистые стали. Хорошими режущими свойствами обладают высокоуглеродистые стали.
Материаловедение. Лаб. практикум |
-57- |
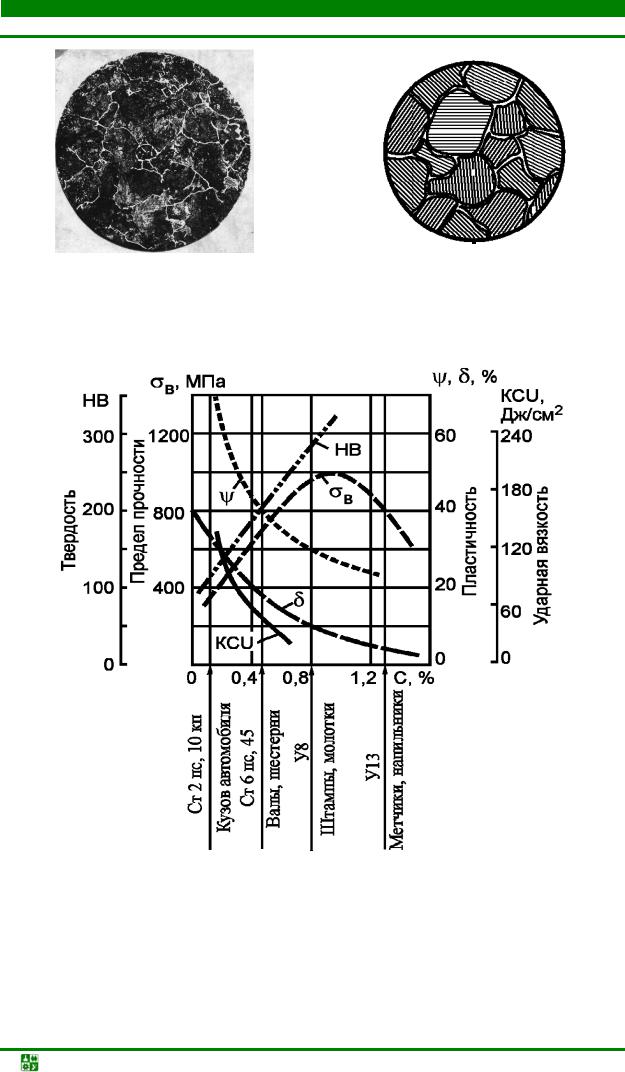
ЛАБОРАТОРНАЯ РАБОТА 6 ИЗУЧЕНИЕ МИКРОСТРУКТУРЫ И СВОЙСТВ УГЛЕРОДИСТЫХ СТАЛЕЙ
Краткие теоретические сведения
а |
б |
Рис. 6.5. Заэвтектоидная сталь, в структуре перлит и цементит: а – фотография микроструктуры; б – схема зарисовки
Рис. 6.6. Зависимость механических свойств сталей от химического состава и примерные марки сталей
Материаловедение. Лаб. практикум |
-58- |

ЛАБОРАТОРНАЯ РАБОТА 6 ИЗУЧЕНИЕ МИКРОСТРУКТУРЫ И СВОЙСТВ УГЛЕРОДИСТЫХ СТАЛЕЙ
Порядоквыполненияработы
Каждый студент получает коллекцию микрошлифов углеродистых сталей в равновесном отожженном состоянии, протравленных 4 %-м раствором азотной кислоты в спирте.
В работе нужно:
1)изучить и зарисовать микроструктуру каждого микрошлифа;
2)определить структурные составляющие стали и их объемную долю;
3)рассчитать по объемной доле структурных составляющих процентное содержание углерода в заданной стали.
Количество углерода определяют по формулам:
для доэвтектоидной стали, %, С = fп·0,8 %;
для заэвтектоидной стали, %, С = fп·0,8 % + fц·6,67 %,
где fц – площадь, занятая цементитом; fп – площадь, занятая перлитом.
По найденному значению количества углерода и в соответствии с табл. 6.1, табл. 6.2, табл. 6.3 в каждом образце определяют марку стали.
Содержаниеотчета
Отчет по лабораторной работе должен включать:
1)зарисовки всех микрошлифов полученной коллекции;
2)название марки стали по рассчитанному количеству углерода для всех образцов;
3)ответы на вопросы индивидуального задания.
Заданияклабораторнойработе
1.Вычертить диаграмму Fe–Fe3C, построить кривую охлаждения и описать процесс кристаллизации стали марки 20 из области жидкого состояния до комнатной температуры.
2.Привести классификации углеродистой стали по назначению и ка-
честву.
3.Вычертить диаграмму Fe–Fe3C, построить кривую охлаждения и описать процесс кристаллизации стали марки У12 из области жидкого состояния до комнатной температуры.
4.Привести классификацию и маркировку по ГОСТу углеродистых конструкционных сталей. Дать их характеристику.
5.Вычертить диаграмму Fe–Fe3C, описать превращения, протекающие
всплаве железа с 0,5 % С при медленном охлаждении от 1 600 °С до комнат-
Материаловедение. Лаб. практикум |
-59- |
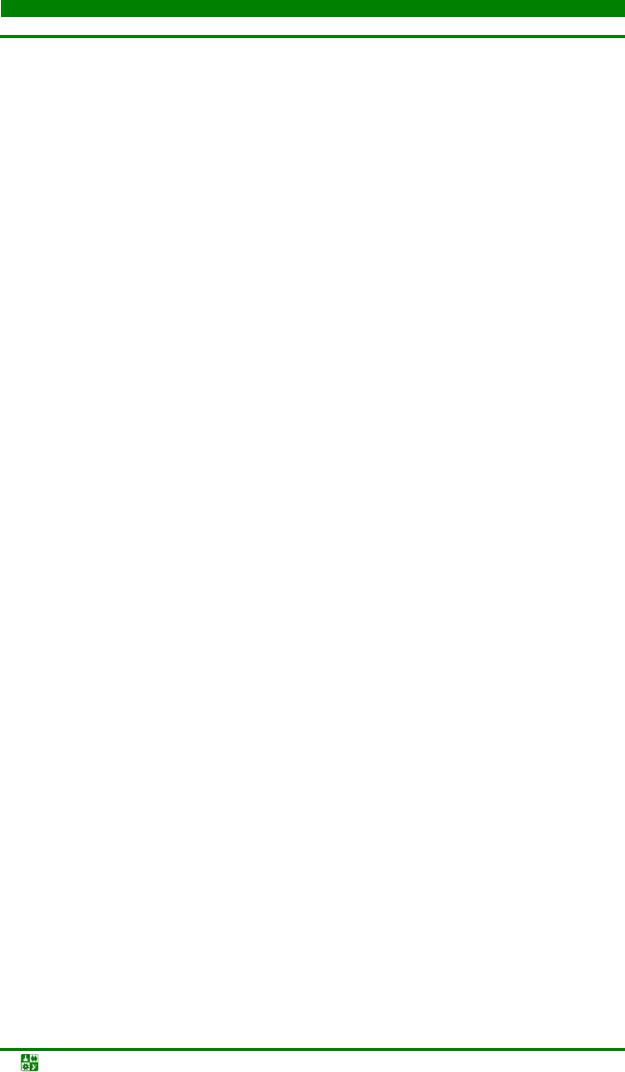
ЛАБОРАТОРНАЯ РАБОТА 6 ИЗУЧЕНИЕ МИКРОСТРУКТУРЫ И СВОЙСТВ УГЛЕРОДИСТЫХ СТАЛЕЙ
Задания к лабораторной работе
ной температуры. Построить для данного сплава кривую охлаждения. Что это за материал?
6.Привести классификацию и маркировку по ГОСТу углеродистых инструментальных сталей. Дать их характеристику.
7.Вычертить диаграмму Fe–Fe3C, описать превращения, протекающие
всплаве с 1,5 % С при медленном нагревании от 0 до 1 600 °С. Построить для данного сплава кривую нагревания.
8.Указать структурные составляющие в сплавах с содержанием углерода до 1,7 % при комнатной температуре и дать их характеристику.
9.Вычертить диаграмму состояния Fe–Fe3C, описать превращения, происходящие в сплаве с 1,3 % С при медленном охлаждении от 1 600 °С до комнатной температуры. Построить для данного сплава кривую охлаждения.
10.Полиморфизм железа. Привести кривые охлаждения и нагрева для железа и дать характеристику всех модификаций железа.
11.Вычертить диаграмму Fe–Fe3C, описать превращения, протекающие в сплаве с 0,8 % С при медленном нагревании от 0 до 1 600 °С. Построить кривую нагрева для данного сплава. Что это за сплав?
12.Описатьмеханизмиосновныепараметрыпроцессакристаллизации.
13.Вычертить диаграмму Fe–Fe3C, описать превращения при нагреве
ипостроить кривую нагрева для сплава, содержащего 1,0 % С в интервале температур от 0 до 1 600 °С.
14.Как изменяются структура, механические и технологические свойства стали при увеличении количества углерода. Привести конкретные примеры.
15.Вычертить диаграмму Fe–Fe3C, описать превращения при нагревании и построить кривую нагрева для сплава, содержащего 0,6 % С в интервале температур от 0 до 1 600 °С.
16.Перечислить все структурные составляющие, встречающиеся в сталях, и дать характеристику их свойств.
17.Вычертить диаграмму Fe–Fe3C, описать превращения, происходящие в стали марки У8 при медленном ее охлаждении от 1 600 °С до комнатной температуры. Построить для нее кривую охлаждения.
18.Указать структуру, маркировку и свойства углеродистых конструкционных сталей. Привести примеры.
19.Вычертить диаграмму Fe–Fe3C, описать превращения, происходящие в стали марки У10 при медленном ее нагревании от 0 до 1 600 °С. Построить для нее кривую нагрева.
20.Описать строение и дать характеристику свойств структурных составляющих стали: феррита, аустенита, перлита, цементита.
21.Вычертить диаграмму Fe–Fe3C, описать превращения при охлаждении и построить кривую охлаждения для сплава, содержащего 0,35 % С. Что это за сплав?
Материаловедение. Лаб. практикум |
-60- |
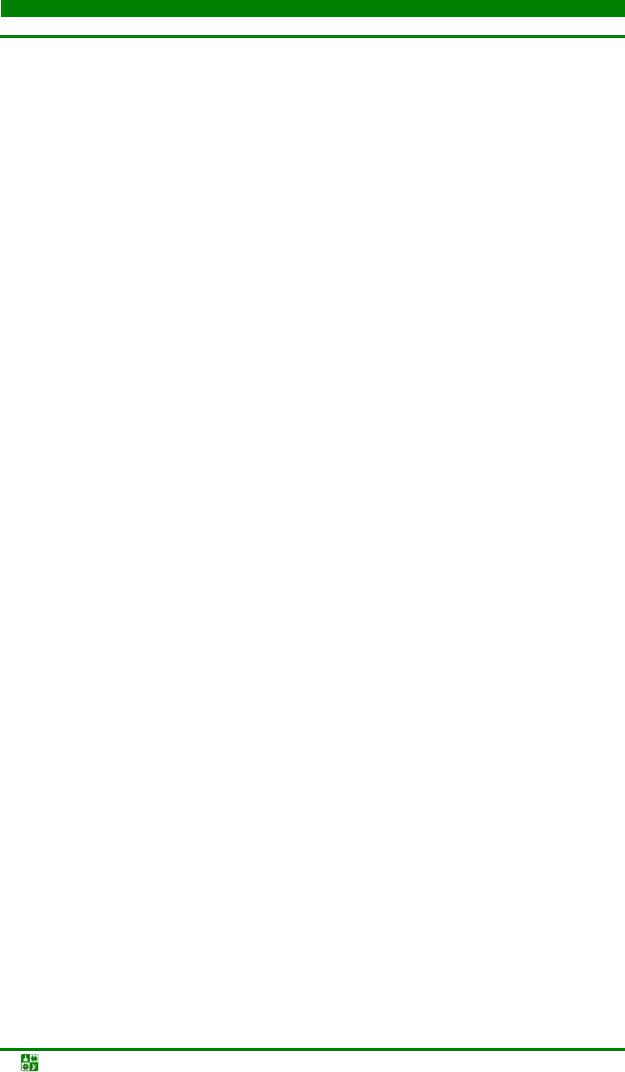
ЛАБОРАТОРНАЯ РАБОТА 6 ИЗУЧЕНИЕ МИКРОСТРУКТУРЫ И СВОЙСТВ УГЛЕРОДИСТЫХ СТАЛЕЙ
Задания к лабораторной работе
22.Указать структуру, маркировку и свойства углеродистых инструментальных сталей. Привести примеры.
23.Вычертить диаграмму Fe–Fe3C, описать превращения при нагреве
ипостроить кривую нагрева для сплава, содержащего 0,5 % С в интервале температур от 0 до 1 600 °С.
24.Какие стали называются доэвтектоидными, эвтектоидными, заэвтектоидными? Какова их структура и свойства?
25.Вычертить диаграмму Fe–Fe3C, описать превращения, происходящие в сплаве, содержащем 0,18 % С, при его медленном нагревании от 0 до 1 600 °С. Построить для него кривую нагрева. Что это за сплав?
Контрольныевопросыизадания
1.Привести классификацию углеродистой стали по назначению и ка-
честву.
2.Как изменяются структура, механические и технологические свойства сталиприувеличенииколичествауглерода? Привестиконкретныепримеры.
3.Перечислить все структурные составляющие, встречающиеся в сталях, и дать характеристику их свойств.
4.Какие стали называются доэвтектоидными, эвтектоидными, заэвтектоидными? Какова их структура и свойства?
Материаловедение. Лаб. практикум |
-61- |