
книги / 813
.pdf
На рис. 5, а изображена специальная усталостная машина для проведения испытаний осесимметричных образцов в условиях двуосного нагружения. Машина обеспечивает жесткое кинематическое нагружение образца при одновременном синхронном циклическом кручении и изгибе с синусоидальной формой цикла и частотой 20 Гц. Эта машина обеспечивает возможность синхронного управления параметрами цикла и снабжена механическим счетчиком числа циклов нагружения. Образцы порошкового железа закреплялись в специальном приспособлении (рис. 5, б) под углом α к оси вращения подвижного захвата. При изменении положения образца относительно оси вращения подвижного захвата – угла α, соответственно менялось соотношение изгибной и крутильной составляющей нагружения так, что при α=0° образец испытывает только циклическое кручение, а при α = 90° – только циклический изгиб (см. рис. 5, б). В данном случае образцы с одинаковой технологией компактирования (давление прессования шихты 600 МПа, без повторной обработки давлением) были разделены на три группы (партии) в зависимости от угла α расположения образцов в приспособлении при испытании: под углом α = 15° к оси вращения (образцы партии 1), под углом =30° к оси вращения (образцы партии 2), под углом α = 45° к оси вращения (образцы партии 3).
а |
б |
Рис. 5. Машина для испытаний образцов в условиях двуосного циклического нагружения: а – общий вид, б – схема крепления образца в специальном приспособлении: 1 – образец, 2 – подвижный захват, 3 – неподвижный захват, 4 – прижимная планка, 5 – вал подвижного захвата, совершающий обратновращательное движение, α – угол разворота образца, ØD = 12 мм – диаметр захватной части образца, Ød = 8 мм минимальный диаметр образца в галтели
21

Испытания также проводились на специализированной сервогидравлической двухосевой системе Instron 8850 (рис. 6), которая позволяет сочетать растяжение-сжатие и кручение образца. Испытательная система Instron 8850 оборудована линейным исполнительным механизмом, обеспечивающим осевое перемещение привода, и поворотным исполнительным механизмом для вращения привода. Линейный исполнительный механизм применяется для приложения осевой нагрузки на испытываемый образец. Точное управление движением и направлением перемещения поршня и прикладываемой силой осуществляется командными электрическими сигналами, передаваемыми к сервоклапану. По аналогичному принципу осуществляется управление системы поворотного исполнительного механизма. Использование сервосистемы позволяет повысить точность позиционирования захватов и приложение нагрузки к образцу и свести к минимуму отклонение от заданного закона нагружения или деформирования.
Рис. 6. Сервогидравлическая двухосевая (растяжение-сжатие, кручение) испытательная система Instron 8850 (100 кН/1000 Нм)
Описанная испытательная система Instron 8850 позволяет проводить квазистатические испытания на растяжение/сжатие и кручение, испытания на двуосное, сложное нагружение, так же и в условиях усталости с частотой до 30 Гц. Нагрузка (или перемещения) в осевом направлении и крутящий момент (или угол закручивания) могут задавать-
22

ся независимо друг от друга. Нагружение может быть задано в виде простых траекторий или сложных законов. В данном случае проводились усталостные испытания осесимметричных (см. рис. 1, б) образцов порошкового железа при варьировании амплитуд осевого и углового движений подвижного захвата в заданном соотношении, форма цикла – синусоида, оба движения подвижного захвата синхронизированы (угол запаздывания равен нулю), частота цикла деформирования 20 Гц.
Для испытаний в условиях двухосевого нагружения на Instron 8850 применялись те же осесимметричные образцы порошкового железа, что и ранее на машине-качалке. Образцы закреплялись в гидравлических захватах (рис. 7). Для обеспечения крутящего момента на захватной части образцов выполнялась лыска, глубина которой рассчитывалась исходя из соображений соосности гидравлических захватов и образца при условии применения в захватах губок для осесимметричных образцов, с одной стороны, и плоских губок – с другой (рис. 7, б).
Захват
Образец
а |
б |
Рис. 7. Размещение образца в захвате: а – общий вид, б – геометрическое представление схемы расположения образца в захватах машины
При установке образцов в испытательные машины производился индивидуальный контроль геометрических параметров каждого образца, расположения образца в захватах машины, а также соответствующих параметров нагружения. Для измерения амплитуд перемещений характерных точек использовался индикатор стрелочного типа с точностью измерения до 10 мкм, геометрические размеры измерялись штангенциркулем с точностью до 50 мкм. Контролируемыми парамет-
23
рами нагружения для испытаний в условиях кинематического изгиба являются: амплитуда прогиба конца стержня и амплитудное значение угла поворота крайнего сечения рабочей части образца. При этом угол поворота определялся через величину перемещения оси подвижного захвата испытательной машины (см. рис. 2, б). Параметром нагружения для силового изгиба (изгиб при вращении на УКИ-10) является сила тяжести груза, закрепленного на свободном конце образца (см. рис. 3). Параметром нагружения для кинематического кручения являлась величина амплитуды угла закручивания подвижного захвата, которая определялась через амплитуду размаха флажка, закрепленного на образце рядом с подвижным захватом (см. рис. 4, б). Контролируемым параметром при испытаниях в условиях двуосного нагружения на машине-качалке (см. рис. 5) являлась амплитуда перемещения точки пересечения поверхности разрезной планшайбы и перпендикуляра к оси вращения подвижного захвата при фиксируемом радиусе, а также угол α положения оси образцов относительно оси подвижного захвата при закреплении. Величина амплитуды перемещения при этом определялась исходя из результатов пробных испытаний и необходимости попадания в диапазон долговечностей от 104 до 3·106 циклов. Амплитудное значение прогиба и угла закручивания крайнего сечения рабочей части образца определялись расчетным путем. Аналогичным образом, но в обратном порядке определялись параметры нагружения: в виде амплитуды осевого перемещения и угла закручивания образца, при испытаниях в условиях двуосного нагружения на специализированной сервогидравлической двухосевой системе Instron 8850.
Таким образом, усталостные испытания проводились при симметричной синусоидальной форме цикла, путем определения усталостной долговечности образцов при различных амплитудах цикла нагружения. При этом прикладываемые напряжения изменялись таким образом, чтобы разрушение образцов происходило в диапазоне от 104 циклов нагружения до принятого базовым числом в 3·106 циклов нагружения, соответствующего многоцикловой усталости. Для обеспечения равномерного распределения результатов испытаний в пределах заданного диапазона партия образцов разбивалась на подгруппы, которые испытываются на различных уровнях амплитудных значений параметров нагружения. Результаты прямых усталостных испытаний представляют собой для каждого образца набор данных о геометриче-
24
ских параметрах и параметрах нагружения, а также соответствующие числа циклов нагружения до разрушения. Определение значений амплитудных напряжений, приводящих к разрушению образцов, является самостоятельной расчетной задачей для каждого конкретного типа испытаний.
Оценка напряженно-деформированного состояния образцов при испытаниях
Обработка результатов испытаний проводилась с использованием моделей механики деформирования и разрушения макроизотропных структурно неоднородных материалов для циклического нагружения [2] и включает анализ напряженно-деформированного состояния на макроскопическом и структурном уровнях образцов порошкового композита. Макродеформированное состояние образцов при циклическом изгибе и кручении, связанное с определением амплитудных значений тензора деформации в образце, исследовалось в рамках моделей механики стержней переменного сечения в условиях плоского изгиба или при кручении. При постановке краевых задач использовалась модель Тимошенко для изгиба и техническая теория кручения стержней, при этом граничные условия задавались полностью в перемещениях: однородные условия соответствуют неподвижному захвату, воздействие активного захвата задавалось значениями амплитуды прогиба и угла поворота нормали при изгибе образца или амплитудой угла закручивания при кручении.
В дальнейшем исследовались структурные напряжения в неоднородном материале и определялись осредненные разрушающие напряжения. Рассматривалось напряженно-деформированное состояние в представительном объеме порошкового пористого железа при заданных значениях компонент тензора макродеформаций, соответствующих предельным амплитудным деформациям образца при усталостном разрушении. Неоднородная среда моделировалась конечно-элементной структурой со случайным равномерным распределением элементов нулевой жесткости, моделирующих пористость. Количество таких элементов определяется объемным содержанием пор в соответствующем образце. Остальные элементы структуры моделируют частицы порошка и обладают свойствами литого чистого железа, упругопластическое поведение которого описывалось в рамках гипотезы единой
25
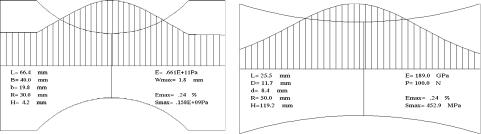
кривой деформирования. Перемещения точек границы представительного объема пористого железа связывались с макроскопической деформацией, а для определения напряжений в компонентах структуры проводилось решение краевой нелинейной задачи микромеханики с использованием процедуры метода конечного элемента. Практически применялась итерационная процедура решения упругопластической краевой задачи по алгоритму редуцирования жесткостей конечных элементов. В результате определялись поля структурных напряжений в порошковом пористом железе, а осреднение по представительному объему материала позволяет определить уровень напряжений в месте излома образца [3].
Численная реализация расчета макродеформированного состояния образцов при циклическом изгибе, растяжении и кручении, связанная с определением амплитудных значений тензора деформации в образце, осуществлялась методом конечных элементов в двух вариантах: с кусоч- но-линейной аппроксимацией полей деформаций в стержневом элементе переменного сечения [4] и с использованием объемных конечных элементов средствами расчетного пакета ANSYS [5].
Типичные эпюры распределения продольных напряжений в плоском и осесимметричном образцах при расчете стержневыми конечными элементами приведены на рис. 8, а, б соответственно. Штриховка эпюр соответствует разбивке на конечные элементы, кроме того, на рисунках приведена форма рабочей части образцов и вертикальной линией отмечено место расположения излома.
а |
б |
Рис. 8. Эпюра распределения продольных напряжений в плоском (а) и в осесимметричном образце (б)
Для расчёта амплитудных значений напряжений образцов с помощью расчетного пакета ANSYS [5] была построена геометрическая модель образца. Построенная модель была разбита на конечные эле-
26

менты типа SOLID 73 и всего содержала 19652 элемента и 20295 узлов. Изображение геометрической модели образца и схемы, разбитой на конечные элементы, приведено на рис. 9.
а |
б |
Рис. 9. Модель осесимметричного образца, построенная в ANSYS (а), и схема разбиения этой модели на конечные элементны (б)
Используя принцип суперпозиции, многоосное нагружение разделили на два простых – составляющие изгиба и кручения при использовании машины-качалки (см. рис. 5) и растяжения и кручения при испытаниях на специализированной сервогидравлической двухосевой системе Instron 8850 (см. рис. 6). А при расчете НДС средствами ANSYS были выделены соответствующие компоненты многоосного нагружения (рис. 10).
а |
б |
в |
Рис. 10. НДС образца в опасном сечении для составляющей изгиба (а), растяжения (б) и кручения (в)
Результаты испытаний и их анализ
Обработка экспериментальных данных при проведении «простых» испытаний (кинематический изгиб плоских образцов, силовой изгиб осесимметричных образцов и кручение осесимметричных образцов) проводилась в рамках серий образцов с одинаковой технологией изготовления, при этом были построены вероятностные кривые уста-
27

лости. Так, например, на рис. 11, а приведены усталостные кривые (амплитуда интенсивности макронапряжений – число циклов нагружения в логорифмической форме) для партии образцов порошкового железа, изготовленных из крупнодисперсного порошка (100 мкм), Ос.Ч.6-2 при давлении прессования 200 МПа и испытанных в условиях кинематического и силового циклического изгиба. На рис. 11, б изображены аналогичные кривые усталости для партии образцов порошкового железа изготовленных из крупнодисперсного порошка Ос.Ч. 6-2 при давлении прессования 400 МПа.
а |
б |
Рис. 11. Кривые усталости плоских (1) и осесимметричных (2) образцов порошкового железа при давлении прессования 200 МПа (а) и 400 МПа (б)
а |
б |
Рис. 12. Кривые усталости плоских (1) и осесимметричных (2) образцов порошкового железа при давлении прессования 800 МПа (а) и давлении прессования
и допрессовки 800 МПа (б)
28

На рис. 12, а изображены кривые усталости для партии образцов порошкового железа, изготовленных из мелкодисперсного (20 мкм) порошка Ос.Ч. 6-2 при давлении прессования 800 МПа, испытанных в условиях кинематического и силового циклического изгиба. На рис. 12, б изображены аналогичные кривые усталости для партии образцов порошкового железа, изготовленных из мелкодисперсного порошка Ос.Ч. 6-2 прессованием при давлении 800 МПа и последующей допрессовкой.
Аналогичные партии образцов выделялись и при испытаниях на кручение. Так, на рис. 13 изображены кривые усталости образцов порошкового железа Ос.Ч. 6-2 при кручении.
Рис. 13. Экспериментальные кривые усталости порошкового железа при кручении: 1 – партия образцов, полученная при давлении прессования 200 МПа,
2 – при давлении прессования 400 МПа,
3 – при давлении прессования 800 МПа,
4 – при давлении прессования и допрессовки 800 МПа
В общей сложности были проведены испытания 154 образцов на изгиб (кинематический и силовой) и 100 образцов на кручение при циклическом нагружении с различными амплитудами прогибов или углов закручивания, при этом объемное содержание пор в образцах охватывало диапазон 0...30 %. Здесь и далее статистическая обработка экспериментальных данных и построение кривых усталости проводились с использованием линейного регрессионного анализа [6]. Аппроксимация разброса экспериментальных точек проведена кривой с вероятностью разрушения 50 % (сплошная линия). Доверительный
29

интервал пятидесятипроцентной кривой усталости с вероятностью Р = 0,9 обозначен на графиках кривых усталости пунктирными линиями. Различие кривых усталости, построенных для инвариантов амплитуд макронапряжений (см. рис. 11–13), показывает несправедливость гипотезы единой кривой деформирования для представительного объема порошкового пористого железа и требует для его феноменологического описания проведения как минимум двух независимых видов механических испытаний.
При проведении усталостных испытаний в условиях двуосного нагружения на специальной машине-качалке (см. рис. 5) всего в эксперименте было использовано 85 образцов порошкового железа марки ПЖР 3.200.28. Образцы при испытаниях были разбиты на партии в зависимости от угла α расположения в приспособлении. Используя принцип суперпозиции, многоосное нагружение разделили на два простых – составляющие изгиба и кручения, и при расчете НДС средствами ANSYS были выделены соответствующие компоненты. В результате статистической обработки результатов экспериментов были построены усталостные кривые порошкового железа ПЖР3.200.28. На рис. 14, а, б приведены кривые усталости образцов порошкового железа первой партии (α = 15°) для составляющих изгиба и кручения. При этих условиях испытано 30 образцов.
σ, |
|
σ, |
МПа |
|
МПа |
|
lg N |
|
lg N |
а |
б |
Рис. 14. Кривые усталости образцов партии 1 (α = 15°) для изгибной (а) и крутильной (б) составляющей двуосного нагружения на машине-качалке
На рис. 15 а, б и рис. 16 а, б приведены аналогичные кривые для образцов порошкового структурно неоднородного материала ПЖР3.200.28 второй (α = 30°) и третьей (α = 45°) партии. Всего было испытано 28 образцов второй партии и 27 образцов – третьей.
30