
Chainov_Ivashenko_Konstr_dvs / Чайнов Иващенко - Конструирование ДВС
.pdf
Рис. 7.8. Значения эксцентриситета c в функции коэффициента нагруженности:
а – Λ = 0,20–0,80; б – Λ > 0,80
С учетом зависимости (7.5) выра жение (7.7) можно представить в виде
|
Qтр |
(−2d 2l)Cт 2Ε, |
(7.8) |
|||||
|
|
|
|
|
|
|
|
|
где С |
= |
|
|
0,438ΛФ 1 |
Λ 2 . |
|||
|
|
|
||||||
|
|
|
||||||
|
т |
|
Λ 2 |
|
|
|
|
|
|
1 |
|
|
|
|
На рис. 7.9 дана зависимость ко эффициента Ст от относительного эксцентриситета Λ при различных отношениях l/d.
Количество теплоты Qм, отводи мой от подшипника с маслом,
Qм cм мVм (Tвых Tвх ), (7.9)
где cм – удельная теплоемкость мас ла – (1,7–2,1)103 Дж/(кг3К); м –
плотность масла (870–890) кг/м3; Tвых, Tвх – температура масла соответст венно на выходе и входе из подшип ника, С; Vм – объемный расход мас ла, прокачиваемый через подшип ник, м3/с.
Полный расход масла Vм опреде ляют как сумму расходов соответ
ственно для нагруженной и нена груженной частей подшипника:
Vм V1м V2м , |
(7.10) |
где V1м = 0,5Τld 2 q1; V2м = 0,5Τld 2 q2.
Рис. 7.9. Зависимость коэффициента сопро тивления при вращении шейки вала от относи тельного эксцентриситета:
1 и 5 – l/d = 0,7; 2 и 6 – l/d = 0,6; 3 и 7 – l/d = = 0,4; 5 и 8 – l/d = 0,3
281

Рис. 7.10. Зависимость коэффициента объем ного расхода масла b от относительного экс центриситета для различных углов обхвата j
Коэффициенты расхода опреде ляются по формулам
q |
|
0,3(0,2 Λ) |
105, Λ 0,08(1 d)2 |
; |
1 |
|
|||
|
105, Λ 0,43(1 d)2 |
|
||
|
|
# |
||
q2 ΦФ(d 1)2 pвх p, |
|
|||
|
(7.11)
где рвх – давление масла на входе в подшипник; Φ – коэффициент объ емного расхода масла, определяе мый в зависимости от угла обхвата по графикам на рис. 7.10.
Доля количества теплоты, от водимой через вал и корпус под шипника, невелика, и при расче тах ею часто пренебрегают, как и количеством теплоты, отводимым с маслом, вытекающим через то рец нагруженной части подшип ника.
При расчете задаются давлени ем рвх и температурой масла Твх на входе в подшипник. Для автомо бильных двигателей принимают рвх = 0,3–0,4 МПа и Твх = 70–75 С для двигателей с принудительным воспламенением; рвх = 0,4–0,6 МПа и Твх = 75–80 С для дизельных двигателей.
Для тракторных двигателей давление масла на входе в глав
ную масляную магистраль со ставляет 0,25–0,45 МПа. Повы шение давления масла в масля ной магистрали не сильно сказы вается на работе подшипников. При работе на холостом ходу давление масла должно быть не менее 0,07–0,10 МПа.
Для форсированных дизельных двигателей специального назначе ния рвх = 0,6–1,5 МПа, для мало оборотных рвх = 0,08–0,18 МПа. В тепловозных дизельных двигателях рвх = 0,45–0,5 МПа. Максимальная допускаемая температура масла на входе в двигатель 75–88 С.
С помощью приведенных за висимостей можно расчетным пу тем в первом приближении оце нивать работоспособность под шипников скольжения. Для этого должны быть заданы: диаметр d и длина l шейки, частота вращения n вала, средняя за рабочий цикл радиальная нагрузка Рrср, высота неровностей поверхностей шейки hв и вкладыша hп после чистовой обработки, диаметральный зазор, давление масла на входе в под шипник рвх, марка масла и зави симость динамической вязкости масла − от температуры масла Тм. Задаваясь несколькими значения ми температур Тм, определяют соответствующие значения вязко сти масла − (рис. 7.11). Подсчи тывают коэффициент нагружен ности Ф, затем по графикам (см. рис. 7.8) и принятому значе нию l/d находят относительный эксцентриситет Λ и минимальную толщину масляного слоя hmin для выбранных значений Тм. Иско мые численные значения пара метров при работе подшипника должны обеспечить его тепловой
баланс Qтр = Qм, по которому оп ределяют действительную сред
нюю температуру масла в под
282

Рис. 7.11. Зависимость вязкости моторных ма сел от температуры:
1 – М – 16 – Г2(к); 2 – М – 63/14 – Г; 3 – М – 63; 4 –М–16 – 53/10 – Г1; 5 – М – 8 – Г2(к); 6 – М – 43/6 – В1
Рис. 7.12. Определение средней температуры масла в подшипнике
шипнике (рис. 7.12) и соответст вующее ей действительное значе ние hmin, которое сравнивают с высотой неровностей hв + hп и находят коэффициент безопасно сти S по толщине масляного
слоя: S = hmin/(hв + hп), который должен быть не менее 2.
Нагрузка на подшипник порш невых двигателей переменна по ве личине и направлению и имеет пе
Рис. 7.13. Траектория движения центра шатун ной шейки коленчатого вала тепловозного дви гателя 10 ДН 20,7/2 25,4 на различных пози циях контроллера
риодический характер на устано вившемся режиме работы двигате ля. При этом ось шейки коленчато го вала движется в пределах зазорапо замкнутой траектории, зави сящей от нагрузки и частоты вра щения двигателя (рис. 7.13). При этом границы области обеспечения несущей способности подшипника могут изменяться. Толщина масля ного слоя при некоторых положе ниях шейки вала может оказаться меньше критической (значение Λ приближается к единице). Однако эти критические положения, когда режим работы подшипника пере ходит от гидродинамического к по лужидкостному, могут быть не опасны, если длительность их не велика (не более 20 % продолжи тельности цикла).
Рассмотренная математиче ская модель не учитывает ряд факторов, влияющих на работу
283

подшипников скольжения. Буду чи одномерной, она не позволяет оценить изменение давления (см. рис. 7.1) по длине подшип ника. Кроме того, не учитывается в полной мере переменность на грузки за рабочий цикл подшип ника и влияние напряженно де формированного состояния опор подшипника (кривошипной го ловки шатуна, подвески корен ных шеек коленчатого вала) на толщину масляного слоя в под шипнике; не принимается во внимание изменение температу ры масла в пределах масляного клина и др. Поэтому существуют более точные математические мо дели. Для учета изменения давле ния масла по длине подшипника применяется модель, предусмат ривающая решение уравнения Рейнольдса для нестационарного режима работы подшипника в двумерной постановке. В частном случае при параллельности оси подшипника и вала и постоянной вязкости в пределах подшипника уравнение Рейнольдса имеет вид:
|
p |
|
|
p |
|
|
|||
|
h3 |
|
|
h3 |
|
|
|||
|
|
|
|||||||
x |
x |
|
z |
z |
|
|
|
||
6−(v0 v1 ) |
h 12− h |
, |
(7.12) |
||||||
|
|
|
|
x |
|
|
|
|
где v0 – окружная скорость шей ки вала; v1 – окружная скорость подшипника, для коренных под шипников v1 = 0; z – продольная координата вдоль оси подшип ника.
Второй член в правой части уравнения (7.12) связан с вытесне нием масла вследствие радиального перемещения шейки в подшипни ке (Λ 5 const).
Уравнение (7.12) решается с учетом периодичности параметров
работы подшипников коленчатого вала во времени. Граничные усло вия для решения уравнения (7.12) имеют вид:
p(x, z Γl 2) 0; |
|
|||||
p |
|
p |
|
|
||
(0, z) |
( r, z) 0; |
|
||||
|
|
|
# (7.13) |
|||
x |
x |
|||||
|
|
|
||||
p(x, z) > p |
нп |
, |
|
|||
|
|
|
|
|
где pнп – давление упругости насы щенных паров масла.
Задача может быть решена про екционно сеточным методом. Об ласть, занимаемая подшипником, разбивается на N интервалов ( x по оси x) и М интервалов ( z по оси z). В качестве базисных функций ис пользуют функции Куранта &ij, представляющие пирамиды с вер шинами в точках ij (xi zj) единичной высоты с шестиугольным основа нием. Давление р(x, z) в подшипни ке представляется суммой базис ных функций
p(x, z) 6Pij &ij , |
(7.14) |
i, j |
|
где Рij – коэффициенты, подлежа щие определению.
Проецируя обе части уравне ния (7.12) на базисные функции, с помощью метода Галеркина с учетом формул (7.13) получают систему линейных алгебраических уравнений относительно значений гидродинамического давления в подшипнике. Решение задачи осу ществляется с помощью итера ций, при этом подбирают значе ния зазоров, которые уточняются до выполнения с заданной точно стью равенства результирующей внешней нагрузки на подшипник и реакции масляного слоя. На ка ждом шаге система алгебраиче ских уравнений решается методом Гаусса.
284

|
|
|
|
|
автомобильного двигателя типа |
|
|
|
|
|
|
ЧН10,2/12,2. |
|
|
|
|
|
|
На рис. 7.15 приведено рас |
|
|
|
|
|
|
пределение гидродинамического |
|
|
|
|
|
|
давления по поверхности под |
|
|
|
|
|
|
шипника (d = 72 мм, l = 32 мм). |
|
|
|
|
|
|
В окружном направлении по оси |
|
|
|
|
|
|
x протяженность |
подшипника |
|
|
|
|
|
разбита на 36 равных частей, а |
|
|
|
|
|
|
по оси z по длине подшипника |
|
|
|
|
|
|
выделено четыре участка. Про |
|
Рис. 7.14. Зависимость минимального зазора в |
верка результатов |
производится |
||||
шатунном подшипнике автомобильного двига |
сравнением суммарной силы ре |
|||||
теля типа ЧН10,2/12,2 от угла a |
|
акции, рассчитываемой по полу |
||||
Для реализации |
описанной |
ченному значению гидродинами |
||||
ческого давления, с заданной си |
||||||
методики расчета были разрабо |
лой, действующей на подшипник |
|||||
таны алгоритм и рабочая про |
и определяемой при динамиче |
|||||
грамма для нахождения значе |
ском расчете двигателя. |
|||||
ния |
зазоров |
и распределения |
Дальнейшее совершенствование |
|||
гидродинамического |
давления в |
методик расчета |
подшипников |
|||
сопряжении |
подшипник–шейка |
скольжения поршневых двигателей |
||||
вала. Значения зазоров и экс |
связано с учетом изменения формы |
|||||
центриситета |
выводят |
через |
постели подшипника в результате |
|||
один градус угла поворота ко |
действия переменной внешней на |
|||||
ленчатого вала. На рис. 7.14 в |
грузки и гидродинамического дав |
|||||
качестве примера показана зави |
ления, а также с уточненным ана |
|||||
симость минимального зазора от |
лизом теплового состояния под |
|||||
угла |
поворота коленчатого |
вала |
шипника и масляного слоя. |
Рис. 7.15. Распределение гидродинамического давления по поверхности подшипника автомобиль ного двигателя типа ЧН10,2/12,2
285

7.2. Подшипники качения в поршневых двигателях
Считают, что подшипники ка чения уменьшают трение и повы шают механический КПД двигате ля. Они не требуют обильной смаз ки, кроме того, подшипник и мас ло вследствие небольших потерь на трение меньше нагреваются. Одна ко подшипники качения при рабо те производят больший шум и обычно отличаются более сложным монтажом по сравнению с под шипниками скольжения.
В поршневых двигателях приме няются различные типы подшипни ков качения: шариковые, ролико вые и игольчатые. В качестве корен ных подшипников коленчатого вала
вмногоцилиндровых двигателях ис пользуют роликовые подшипники. Роликовые подшипники с коротки ми роликами успешно работают при повышенных радиальных на грузках. Их грузоподъемность выше грузоподъемности однорядных ша риковых подшипников.
Роликовые подшипники допус кают небольшое осевое взаимосме щение колец, что имеет важное значение при температурных де формациях вала и опор.
Роликовые подшипники надежны
вработе и позволяют уменьшить длину двигателя. Существует два ва рианта выполнения роликового под шипника – без внутренней обоймы, когда дорожкой качения роликов яв ляется непосредственно щека колен чатого вала, или с внутренней обой мой. Первый вариант считают более предпочтительным как обеспечиваю щий более высокую точность и ре монтопригодность. На рис. 6.3 при веден пример применения роликово го подшипника в качестве коренной опоры форсированного дизельного двигателя специального назначения.
На рис. 7.16 показана опора ко ренного подшипника автомобильно го дизеля 12 ЧН13/14. Радиальный роликовый подшипник (рис. 7.16, б) без внутреннего кольца установлен на щеке коленчатого вала. Ролики 2 диаметром dw = 2,3 мм и длиной lw = = 34 мм, выполненные из стали ШХ15СГ в количестве 24 шт., фик сируются на валу специальными буртиками. Наружное кольцо 1 за креплено в картере двигателя упруги ми кольцами с прорезями. Сепаратор 3, выполненный из латуни, препятст вует выпадению роликов, обеспечи вает их свободное вращение и сме щение до диаметра не менее 203,5 мм при монтаже сепаратора с роликами на коленчатый вал (рис. 7.16, в).
Подшипники качения рассчи тывают на долговечность. Крите рием их работоспособности являет ся отсутствие усталостного выкра шивания поверхностных слоев. Подшипники поршневых двигате лей работают при переменных ре жимах и при выборе подшипников качения их подбирают по эквива лентной нагрузке, вызывающей одинаковый с реально действую щими нагрузками уровень устало стных повреждений.
Долговечность Lh (ч) роликового подшипника определяют по экви валентной нагрузке Рr:
L |
h |
a a |
(C |
r |
P ) p |
, (7.15) |
|
1 23 |
|
r |
|
где р – показатель степени; для роли ковых подшипников по эксперимен тальным данным р = 10/3; Сr – дина мическая грузоподъемность (посто янная радиальная нагрузка, которую подшипник может выдержать в тече ние 106 оборотов при вероятности безотказной работы 90 %); a1 – коэф фициент, зависящий от заявленной надежности подшипника; при веро ятности безотказной работы 90 %
286

Рис. 7.16. Коренная опора дизелей на роликовых подшипниках:
а – дизеля 12 ЧН13/14; б – подшипник роликовый радиальный с короткими цилиндриче скими роликами; в – схема монтажа сепаратора с роликами на коленчатый вал; 1 – наруж ное кольцо; 2 – ролик; 3 – сепаратор
а1 = 1; a23 – коэффициент, учитываю щий условия эксплуатации; для ро ликовых подшипников при отсутст вии заметных перекосов и при нали чии масляной пленки в контактах принимают а23 = 0,8.
Зависимость (7.15) справедлива
при Рr < 0,5Cr.
Динамическая грузоподъемность однорядных роликовых подшипни ков
Cr f0 (lw cos )79 z3
4 dw29
27 , (7.16)
где – номинальный угол контакта между направлением силы, дейст
вующей на ролик, и плоскостью, перпендикулярной оси подшипни ка; f0 – коэффициент пропорцио нальности, зависящий от отношения (dwcos )/d0; dw, lw – соответственно диаметр и длина ролика; d0 – диа метр окружности, проходящей через центры роликов; z – число роликов.
Коэффициент f0 для простых цилиндрических роликов, завися щий от размеров, точности изго товления, материалов, выбирают по таблицам в зависимости от от ношения (dwcos )/d0. При измене нии (dwcos )/d0 в пределах 0,1–0,2 величина f0 изменяется от 7,53 до
287
7,98. Для "бомбинированных" ро |
циент вращения, равный 1 при вра |
|||||||
ликов f0 увеличивают на 20–30 %. |
щении внутреннего кольца относи |
|||||||
Эквивалентная нагрузка для под |
тельно направления нагрузки и 1,2 |
|||||||
шипников с короткими цилиндри |
при вращении |
наружного кольца; |
||||||
ческими роликами |
|
|
|
|
K – коэффициент безопасности, |
|||
|
|
|
|
|
|
|
учитывающий |
динамичность на |
P |
VF |
r |
K K |
т |
, |
(7.17) |
грузки [К = 1,3–1,5 при умеренных |
|
r |
|
|
|
|
толчках и кратковременных пере |
|||
|
|
|
|
|
|
|
||
где Fr – средняя радиальная нагруз |
грузках (150 %)]; Кт – температур |
|||||||
ка, определяемая по векторной диа |
ный коэффициент; Кт = 1,05–1,10 |
|||||||
грамме сил, действующих на корен |
при повышении рабочей температу |
|||||||
ную опору двигателя; V – коэффи |
ры до 125–150 С. |

Глава 8
МЕХАНИЗМ ГАЗОРАСПРЕДЕЛЕНИЯ
Поршневые двигатели выпуска ются с клапанным, золотниковым или смешанным газораспределением.
Вчетырехтактных двигателях используют клапанный механизм газораспределения, основным пре имуществом которого является вы сокая уплотняющая способность камер сгорания вследствие непод вижности клапанов в период повы шения давления газов в цилиндре. Кроме того, давление газов исполь зуется для прижатия клапанов к посадочным седлам.
Вдвухтактных двигателях приме няют как золотниковое, так и сме шанное газораспределение. Первое применяют в двигателях с петлевой схемой газообмена, а второе – в дви гателях с клапанно щелевой схемой, при которой впуск свежего заряда осуществляется через окна во втулке цилиндра, а выпуск отработавших газов – через выпускные клапаны в крышке (головке) цилиндра.
Всвязи с возросшими требова ниями к технологическому уровню вновь создаваемых двигателей ме ханизм газораспределения (МГР) должен обеспечивать не только по ступление необходимой массы све жего заряда в цилиндры и их свое временную очистку, но и изменять фазы газораспределения и высоту подъема клапанов в зависимости от режима работы двигателя.
Таким образом, механизм газо распределения оказывает непосред ственное влияние на формирование основных характеристик двигателя
вшироком диапазоне изменения скоростных и нагрузочных режимов работы.
При создании системы газооб мена в целом и в первую очередь МГР требуется обеспечить наряду с эффективной заменой рабочего те ла в цилиндре надежность всех звеньев МГР на различных режи мах работы, длительную стабиль ность параметров системы с учетом износа ее элементов и усложнения конструкции МГР вследствие рас ширения его функций по управле нию работой двигателя. В связи с широким внедрением электронных систем управления современные конструкции МГР претерпевают существенные изменения по срав нению с традиционными.
8.1. Основы конструирования механизма газораспределения
8.1.1. Схемы механизма газораспределения
В современных четырех и двух тактных (с клапанно щелевой схе мой газообмена) двигателях различ ного назначения применяется "верхнее" расположение клапанов в головке (крышке) цилиндров. В за висимости от расположения и при вода распределительного вала, чис ла клапанов в одном цилиндре и их привода существует много компо новочных схем МГР. Особенности расположения клапанов в головке (крышке) цилиндров будут рассмот рены в гл. 9, здесь лишь следует от метить, что число клапанов на один цилиндр изменяется от одного (ма лооборотные двухтактные двигате ли) до пяти шести (быстроходные четырехтактные двигатели). Повы
289
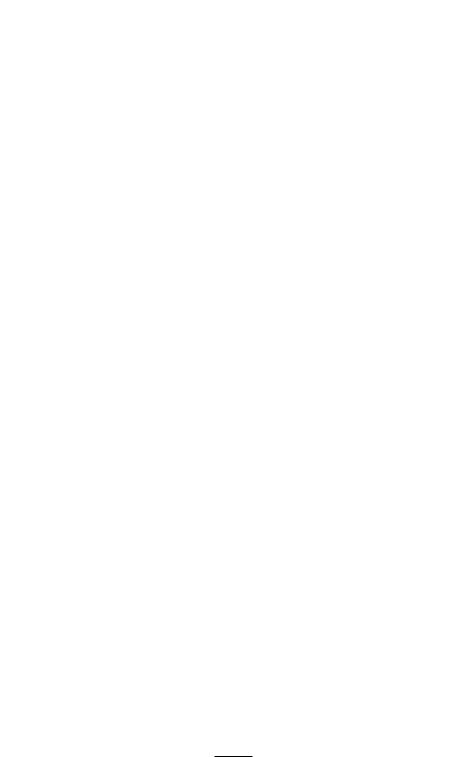
Рис. 8.1. Схемы шестеренчатого привода распределительного вала с шестернями:
а, б – цилиндрическими; в – коническими; 1 – шестерня коленчатого вала; 2 – шестерня распределительного вала; 3 – промежуточная шестерня; 4 – промежуточный валик с кони ческими шестернями
шение количества клапанов в ци линдре до четырех увеличивает сум марную площадь проходных сече ний и наполнение цилиндра све жим зарядом. С увеличением числа клапанов в цилиндре уменьшаются их размеры и масса подвижных де талей, что при прочих равных усло виях уменьшает тепловую напря женность клапанов и инерционные нагрузки в элементах их привода.
Внастоящее время для большин ства двигателей используют механи ческий привод клапанов от распре делительного (кулачкового) вала, приводимого во вращение от колен чатого вала двигателя. По мере по вышения номинальной частоты вра щения для уменьшения инерцион ной нагрузки и увеличения жестко сти элементов привода распредели тельный вал следует располагать ближе к клапанам, в частности, не посредственно на головке цилиндра.
Взависимости от типа двигателя
иместа расположения распредели тельного вала его связь с коленча тым валом может осуществляться с
помощью шестерен, цепной пере дачи, а также зубчатого ремня.
На рис. 8.1 показаны схемы шес теренчатого привода распредели тельного вала. В качестве шестерен (рис. 8.1, а, б) применяют цилинд рические косозубые шестерни. Для некоторых V образных двигателей специального назначения с распо ложением распределительных валов на головках цилиндров используют конические шестерни (рис. 8.1, в). При применении конической пере дачи обеспечивается компактность привода, однако существенно уве личивается стоимость изготовления и технического обслуживания при эксплуатации.
На рис. 8.2 показаны схемы при вода распределительного вала це пью, а на рис. 8.3 – с помощью зуб чатого ремня. В быстроходных авто мобильных двигателях с принуди тельным воспламенением цепной привод в прошлом заменил шесте ренчатый, недостатком которого является громоздкость и повышен ный уровень шума. Цепной привод,
290