
Chainov_Ivashenko_Konstr_dvs / Чайнов Иващенко - Конструирование ДВС
.pdf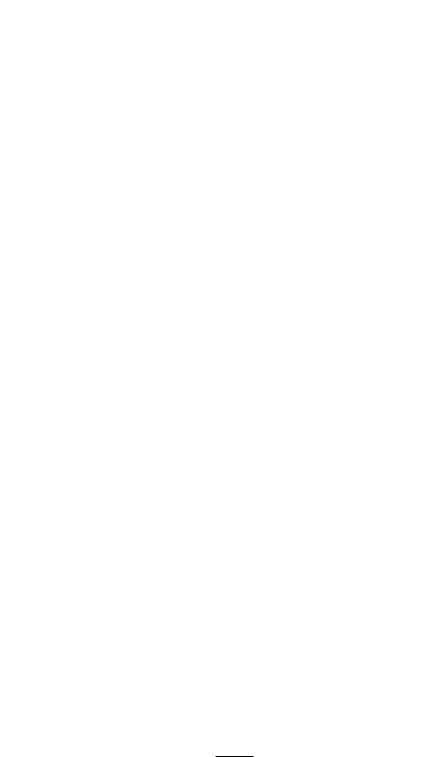
Рис. 4.38. Схема для расчета напряженно де формированного состояния поршня с плоским днищем:
а – гладкое плоское днище; б – днище, под крепленное цилиндрическими ребрами
постановке применима теория тон ких круглых пластин, колец и ци линдрических оболочек. На основе этой теории, кроме простейшего случая (рис. 4.38, а), получены реше ния для поршней с днищем, подкре пленным одним (рис. 4.38, б) или несколькими цилиндрическими реб рами, с различным положением опорной поверхности.
Ниже рассмотрен случай, когда днище сопряжено только с корпусом поршня, находящегося под действи ем давления рz и температурного по ля, определенного в разделе 4.6.2. В соответствии с выбранным направ лением оси z положительные внеш ние силы направлены вверх.
При действии тепловой нагрузки могут появиться значительные уси лия в срединной плоскости днища (z = 0), которые следует учитывать. Если не учитывать влияние сжатия растяжения днища на его изгиб, что допустимо для поршней двигателей, общая задача расчета напряженно деформированного состояния дни
ща состоит из задачи о плоском на пряженном состоянии и задачи из гиба круглой пластины – днища. Основные соотношения для реше ния обеих задач представлены ниже в удобном для использования виде.
Плоское напряженное состояние днища. Разрешающее уравнение от носительно радиального ur переме щения имеет вид
d 2u |
r |
|
|
1 du |
r |
|
|
u |
r |
(1 −) |
d+ |
т |
, |
(4.26) |
||||||||||||||
dr 2 |
|
r |
|
dr |
|
r 2 |
|
|
|
|
||||||||||||||||||
|
|
|
|
|
|
|
|
|
dr |
|
|
|
|
|
||||||||||||||
где |
|
|
|
|
|
|
|
|
|
|
|
|
|
|
|
|
|
|
|
|
|
|
|
|
|
|
|
|
|
|
|
|
|
1 0,5t |
|
|
|
|
|
|
|
|
|
|
|
|
t 2 |
|
|
|
|||||||
+ |
т |
|
|
|
|
|
|
|
|
т |
Td |
z |
|
T |
0 |
|
|
|
T |
2 |
. |
|||||||
|
|
|
|
|
|
|||||||||||||||||||||||
|
|
|
t |
|
|
|
|
|
|
|
|
т |
|
|
|
12 |
|
|
||||||||||
|
|
|
|
|
0,5t |
|
|
|
|
|
|
|
|
|
|
|
|
|
|
|||||||||
|
|
|
|
|
|
|
|
|
|
|
|
|
|
|
|
|
|
|
|
|
|
|
|
|
(4.27) |
При этом положительное значе ние ur считается от оси цилиндра. Радиальная Nr и окружная N) силы, отнесенные к единице длины на срединной поверхности, определя ются через радиальную +r = dur/dr и окружную +) = ur/r деформацию с помощью закона Гука:
|
Et |
|
|
|
|||
N r |
|
|
|
![+ r −+ ) (1 |
−)+ т ], |
||
|
|
− |
2 |
||||
1 |
|
|
|
||||
|
Et |
|
|
|
|
||
N ) |
|
|
|
![+ ) −+ r (1 −)+ т ]. |
|||
|
|
|
|
||||
1 − 2 |
|
|
|
||||
|
|
|
|
|
|
|
(4.28) |
Интегрируя, получают общее ре шение уравнения (4.26)
|
|
|
r |
2 |
|
|
|
|
|
|
u |
r |
cr |
(1 −) |
|
|
|
+ |
т |
d , (4.29) |
|
|
|
|||||||||
|
2 |
|
|
|
|
|
||||
|
|
|
|
|
0 |
|
|
|
||
|
|
|
|
|
|
|
|
|
|
где с – постоянная интегрирования.
Интеграл + т d в выражении
0
(4.29) понимается как сумма инте гралов по участкам днища, в преде
171
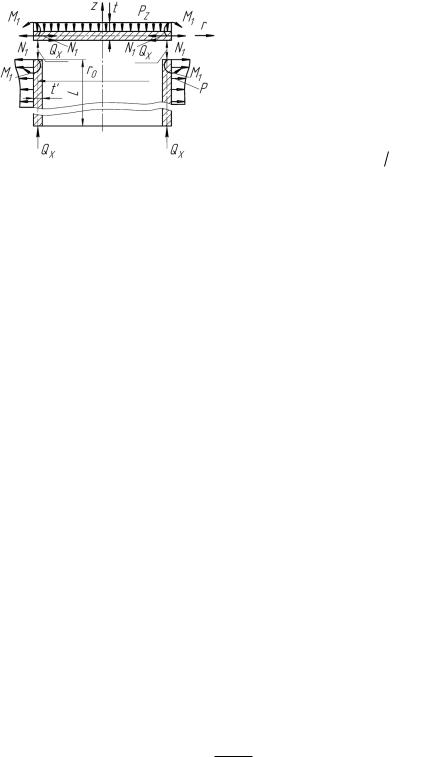
Рис. 4.39. Схема расчета напряжений в порш не с плоским днищем
лах которых условия теплообмена не изменяются.
Постоянную интегрирования оп ределяют из условия равенства нулю силы Nr на боковой поверхности
днища при = 1 |
|
|
||||
c (1 −); |
|
|
|
|
|
|
|
1 |
N |
|
|
|
|
|
+ т d |
1 |
|
|
|
|
; |
|
0,5[1 |
− (1 −) 02 |
]#, |
||
|
|
|||||
|
0 |
Et |
|
|
||
|
|
|
|
|
(4.30)
где 0 = r0/r2.
Неизвестные силовые факторы (рис. 4.39) определяются ниже.
Положительными считаются уси лия, вызывающие растяжение. Вы ражения нормальных усилий Nr и N) для отдельных участков днища име ют вид
0 < < 0 N r |
|
Ar ; N ) A) ; |
(4.31) |
||||||||||
0 < < 1 N r |
Ar N1Ε rm ; |
(4.32) |
|||||||||||
N ) A) N1 Τ)m , |
|
|
|
|
|
|
|
|
|||||
|
|
|
|
c |
|
|
|
|
1 |
|
|
|
|
где A) Et |
|
|
|
+ |
т |
|
+ т d |
|
|||||
|
1 |
− |
2 |
|
; |
||||||||
|
|
|
|
|
0 |
|
|
||||||
|
|
|
|
|
|
|
|
|
|
|
|
||
|
|
|
|
c |
|
|
1 |
|
|
|
|
|
|
Ar Et |
|
|
|
|
|
+ |
т d |
|
|
||||
|
1 |
− |
2 |
; |
|
||||||||
|
|
|
0 |
|
|
|
|
||||||
|
|
|
|
|
|
|
|
|
|
|
|
|
|
|
r |
0 |
|
|
2 |
|
|||
|
|
|
|
|
||||||
Ε rm |
0,5 1 − (1 −) |
|
|
|
|
|
!; |
|||
|
r |
|
|
|
||||||
|
|
|
|
|
|
|
! |
|||
|
|
r |
0 |
|
2 |
|||||
Ε )m |
0,5 1 − (1 |
−) |
|
|
|
!. |
||||
|
r |
|||||||||
|
|
|
|
|
! |
Нормальные напряжения r, ) в плоскости днища от сил Nr, )
r,) N r,) t . |
(4.33) |
Изгиб днища. Разрешающее урав нение изгиба днища при действии давления рz и тепловой нагрузки имеет вид
d 1 d(&r) |
(1 −) |
dΛ |
т |
|
|||||||
|
|
|
|
|
|
|
! |
|
|||
|
|
|
|
|
|
|
|||||
dr r |
dr |
|
|
dr |
|
||||||
|
1 |
r |
|
|
|
|
|
||||
|
pz rdr 0, |
|
|
(4.34) |
|||||||
Dм r |
|
|
|||||||||
|
0 |
|
|
|
|
|
где & = dw/dr – угол поворота нор мали к срединной поверхности дни ща; w – прогиб срединной поверх ности днища;
|
|
|
|
12 |
0,5t |
|
|
|
|
|
|
||
Λ т |
|
тTzdz тT1 . |
(4.35) |
||||||||||
|
|||||||||||||
|
|
|
|
t 3 |
|
|
|
|
|
|
|||
|
|
|
|
|
0,5t |
|
|
|
|
|
|
||
В |
|
результате интегрирования |
|||||||||||
уравнения (4.34) |
|
|
|
||||||||||
|
|
|
(1 −)r2 |
|
|
|
|
||||||
& |
Λ т d |
|
|
||||||||||
|
|
|
|
||||||||||
|
|
|
|
|
0 |
|
|
|
|
|
|||
|
|
|
|
|
|
|
|
|
|
|
|
||
|
|
pz r23 3 |
|
|
|
c |
|
|
|||||
|
|
|
|
|
|
|
|||||||
|
|
|
|
|
|
|
0,5c r2 |
|
. |
(4.36) |
|||
|
|
|
|
|
r2 |
||||||||
|
|
16Dм |
|
|
|
|
|
||||||
|
|
|
|
|
|
|
|
|
|
|
|||
Интеграл |
Λ т d в выражении |
||||||||||||
|
|
|
|
|
|
|
0 |
|
|
|
|
|
(4.36), так же как и ранее интеграл
+ т d в выражении (4.29), понима
0
ется как сумма интегралов по участ
172

кам днища, в пределах которых ус ловия теплообмена не меняются.
Выражения радиального Мr и тангенциального М) моментов, от несенных к единице длины на сре динной поверхности, с учетом теп ловой нагрузки имеют вид
|
d& |
|
|
& |
|
|
|||||
M r |
Dм |
|
|
|
|
− |
r |
(1 −)Λ т ! |
|||
|
|
|
|
||||||||
|
dr |
|
|
|
, (4.37) |
||||||
|
|
& |
|
|
|
d& |
|
||||
M ) |
Dм |
|
|
− |
|
|
|
(1 −)Λ т ! |
|||
|
|
dr |
|||||||||
|
r |
|
|
|
|
|
|||||
где Dм |
|
|
|
|
Et 3 |
|
– цилиндриче |
||||
|
|
|
|
|
|
|
|
|
|||
|
|
12(1 − 2 ) |
ская жесткость изгиба днища. Постоянные интегрирования в
выражении (4.36) находятся из ус ловия равенства нулю угла поворо та & в центре днища при = 0 и ра венства нулю радиального момента Мr на наружном радиусе = 1 (r = r2). Из первого условия следует c = 0, из второго условия с учетом дейст вия на = 0 момента М1, радиаль ной силы N1 и поперечной силы
|
|
|
|
|
|
p |
|
r 2 |
|
|
|
|
|
|
|
|
|
|
|
|
Q |
|
|
|
|
|
z |
2 |
находится постоянная c |
|
|||||||||||
|
|
|
|
|
|
|||||||||||||||
1 |
|
|
2r0 |
|
|
|
|
|
|
|
|
|
|
|
||||||
|
|
|
|
|
|
|
|
|
|
|
|
|
|
|
|
|
|
|||
|
|
|
|
|
|
|
|
|
|
1 |
|
|
(3 −)p |
r |
2 |
|
|
|
||
|
|
|
|
|
|
|
|
|
|
|
|
|
|
|
|
|||||
c |
2(1 −) Λ |
т d |
|
z |
|
2 |
|
|||||||||||||
|
|
|
|
|||||||||||||||||
|
|
|
|
|
|
|
|
|
|
0 |
|
|
8(1 −)Dм |
|||||||
|
M1 N1t 2 |
[1 − (1 −) 2 |
] |
|
||||||||||||||||
|
|
|||||||||||||||||||
|
|
|
|
|
(1 −)Dм |
|
0 |
|
! |
|
|
|
|
|||||||
|
|
|
|
|
|
|
|
|
|
|
|
|
||||||||
|
|
|
|
|
p |
z |
r 2 |
|
|
|
|
|
|
|
|
|
|
|
||
|
|
|
|
|
|
2 |
|
[(1 −)(1 02 ) (1 −)ln 02 ]. |
||||||||||||
|
|
|
|
|
|
|
|
|||||||||||||
|
|
|
4(1 −)Dм |
|
|
|
|
|
|
|
|
|||||||||
|
|
|
|
|
|
|
|
|
|
|
|
|
|
|
|
|
(4.38) |
Положительному значению мо мента соответствует растяжение на поверхности z = 0,5t. Выражения из гибающих моментов Мr и М) для от дельных участков днища имеют вид
0 < < 0 M r Br ; M ) B) ; (4.39)
0 < < 1 M r Br M1Ε rm pz r22Ε rp ;
M ) B) |
|
|
|
|
|
|
|
|
|
|
|
|
|
(4.40) |
|||||||||||||||||
M1Ε )m pz r22Ε )p , |
|
||||||||||||||||||||||||||||||
где |
|
|
|
|
|
|
|
|
|
|
|
|
|
|
|
|
|
|
|
|
|
|
|
|
|
|
|
|
|
|
|
|
|
|
|
|
|
|
|
|
|
|
1 |
− |
2 |
|
|
|
|
|
|
|
|
|
|
|
|||||||
|
Br |
Dм |
|
|
|
|
Λ т d |
|
|
|
|
||||||||||||||||||||
|
|
|
2 |
|
|
|
|
|
|
||||||||||||||||||||||
|
|
|
|
|
|
|
|
|
|
|
|
0 |
|
|
|
|
|
|
|
|
|
|
|
||||||||
|
|
|
|
|
|
|
|
|
|
|
|
|
|
|
|
|
|
|
|
|
|
|
|
|
|
|
|
|
|||
|
|
|
|
|
|
|
|
|
|
|
2 |
|
2 |
|
|
|
|
|
|
|
|
|
|
|
|
|
|
|
|||
|
|
|
|
|
|
|
|
|
|
|
|
|
|
c |
|
|
|
|
|
|
|
|
|||||||||
|
|
(3 −)pz r2 |
|
|
|
|
(1 −) |
|
; |
|
|
|
|
||||||||||||||||||
|
|
|
|
|
|
|
|
|
|
|
|
|
|
|
|||||||||||||||||
|
|
|
|
|
|
16Dм |
|
|
|
|
|
|
|
|
|
2 |
|
|
|
|
|
|
|
|
|
||||||
|
|
|
|
|
|
|
|
|
|
|
|
|
|
|
|
|
|
|
|
|
|
|
|
||||||||
|
|
|
|
|
|
|
|
|
|
|
|
|
|
|
|
|
|
|
|
|
|
|
|
|
|||||||
|
|
|
|
|
|
|
|
|
|
Λ т d |
|
! |
|
|
|
||||||||||||||||
|
|
|
|
|
|
|
|
|
|
|
|
|
|
||||||||||||||||||
|
|
|
|
|
|
|
|
|
|
|
|
|
|
|
|
|
|
|
|
|
|
! |
|
|
|||||||
|
|
|
|
|
|
|
|
|
|
|
|
|
|
|
|
|
|
|
|
|
|
|
|
|
|
||||||
B) Dм (1 − 2 ) |
0 |
|
|
|
|
|
|
|
Λ |
т |
! |
|
|||||||||||||||||||
|
|
|
2 |
|
|
|
|||||||||||||||||||||||||
|
|
|
|
|
|
|
|
|
|
|
|
|
|
|
|
|
|
|
|
! |
|
|
|
||||||||
|
|
|
|
|
|
|
|
|
|
|
|
|
|
|
|
|
|
|
|
|
|
|
|
|
|
|
|||||
|
|
|
|
|
|
|
|
|
|
|
|
|
|
|
|
|
|
|
|
|
|
! |
|
|
|
||||||
|
|
|
|
|
|
|
|
|
|
|
|
|
|
|
|
|
|
|
|
|
|
|
|
|
|
|
|
||||
|
|
|
|
|
|
|
|
|
|
|
|
|
|
|
|
|
|
|
|
|
|
|
|
|
|
|
|
|
|
|
|
|
|
(3− 1)pz r22 2 |
|
|
|
|
|
|
|
|
|
|
|
|
|
|
|
|
|
||||||||||||
|
|
|
|
|
c |
|
|
|
|
|
|
|
|
|
|
|
|||||||||||||||
|
|
|
|
|
|
|
|
|
|
|
|
|
|
|
|
|
|
|
|
(1 |
−) |
; |
|
|
|
|
|||||
|
|
|
16Dм |
|
|
|
|
|
|
2 |
|
|
|
|
|
||||||||||||||||
|
|
|
|
|
|
|
|
|
|
|
|
|
|
|
|
|
|
|
|
|
|
|
|||||||||
|
|
|
|
|
|
|
|
|
|
|
|
|
|
|
|
|
|
|
|
|
|
|
|
|
|
|
|
|
|
|
|
|
|
|
|
|
|
|
|
|
|
|
|
|
|
|
|
|
|
|
|
|
|
|
|
|
|
|
|
|
|
|
|
Ε rp 0125,; |
|
|
|
|
|
|
|
|
|
|
|
|
|
|
|
|
|
|
|
|
|
|
|
||||||||
|
|
|
|
|
|
r 2 |
|
|
|
|
|
|
|
|
|
|
|
|
r |
0 |
|
2 |
|
||||||||
; (1 −) 1 |
|
|
0 |
|
|
(1 −)ln |
|
|
|
!; |
|||||||||||||||||||||
|
|
|
|
|
|
||||||||||||||||||||||||||
|
|
|
|
|
|
r 2 |
|
|
|
|
|
|
|
|
|
|
|
|
|
r |
|
|
|
||||||||
|
|
|
|
|
|
|
|
|
|
|
|
|
|
|
|
|
|
! |
|||||||||||||
Ε )p 0125,; |
|
|
|
|
|
|
|
|
|
|
|
|
|
|
|
|
|
|
|
|
|
|
|||||||||
|
|
|
|
|
|
|
|
|
r |
2 |
|
|
|
|
|
|
|
|
|
|
r |
0 |
|
2 |
|||||||
; (1 |
−) 1 |
|
0 |
|
|
(1 −)ln |
|
|
!; |
||||||||||||||||||||||
|
|
|
|
|
|
||||||||||||||||||||||||||
|
|
|
|
|
|
|
|
|
r |
2 |
|
|
|
|
|
|
|
|
|
|
|
r |
|
|
|
||||||
|
|
|
|
|
|
|
|
|
|
|
|
|
|
|
|
|
|
|
! |
||||||||||||
|
|
|
|
|
|
|
M1 0,5tN. |
|
|
|
|
|
|
||||||||||||||||||
|
|
|
|
|
M1 |
|
|
|
|
|
|
Радиальные и окружные напря жения изгиба в днище изг r,) опре
деляются по формуле |
|
||
изг r,) Γ |
6M r,) |
. |
(4.41) |
|
|||
|
t 2 |
|
Суммарные напряжения 6 в днище определяются с учетом зна ков как сумма
6 r) изг r,) . (4.42)
173
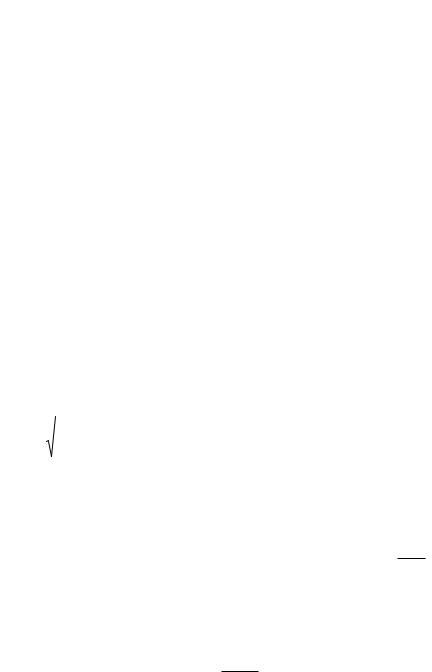

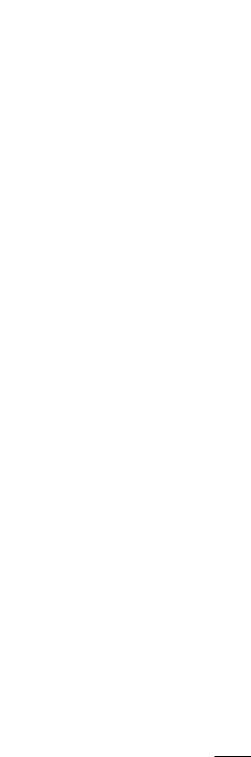
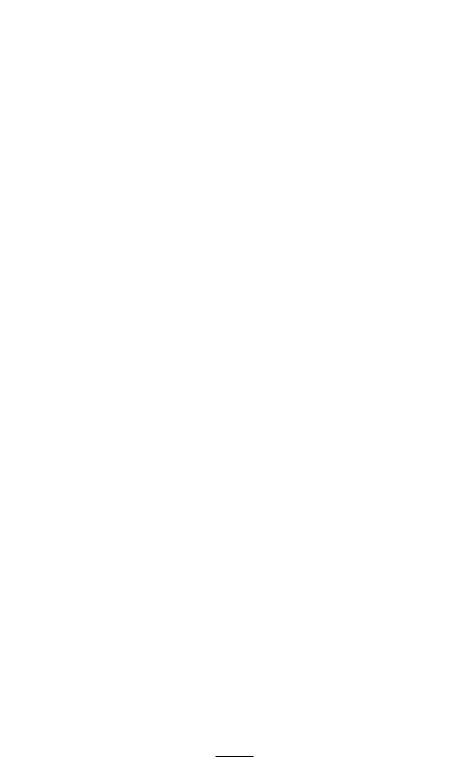
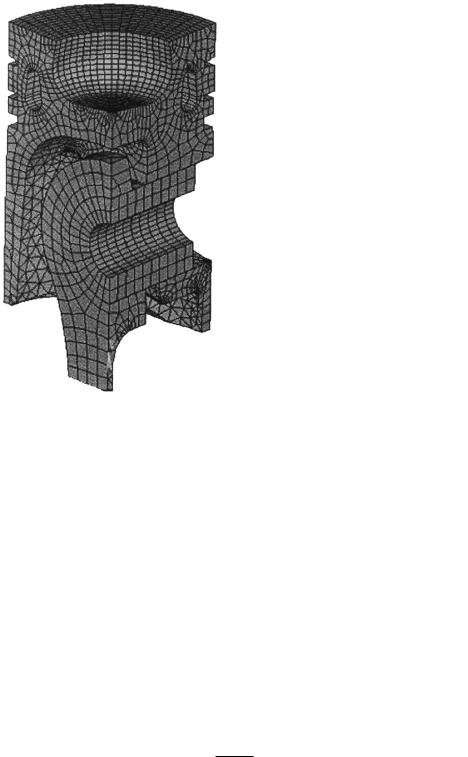

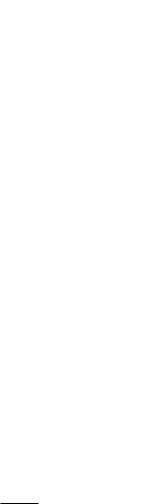