
Chainov_Ivashenko_Konstr_dvs / Чайнов Иващенко - Конструирование ДВС
.pdf
Максимальное значение уско рения jmax = 3 12 e(c 3) достигается при Ε, равном 0 и 180 , а мини
мальное ускорение jmin = 3 12 e(c 3) при Ε, равном 90 и 270 .
Среднее ускорение вершин ро тора определяется из выражения
jcp 3 12 e9 c 2 .
где 2b = a3 – длина хорды, соеди няющей вершины ротора (рис. 3.31).
Индикаторная диаграмма РПД рассчитывается аналогично индика торной диаграмме двигателя с кри вошипно шатунным механизмом.
Геометрическая сумма сил от давления газов, действующих на цилиндр,
|
|
|
|
|
|
|
|
|
|
|
|
|
|
P |
P 2 |
P 2 |
P 2 |
P P |
о |
P P |
о |
P |
о |
P |
о |
. |
(3.137) |
о |
1о |
2о |
3о |
1о 2 |
1о 3 |
2 |
3 |
|
|
||||
|
|
|
|
|
|
|
|
|
|
|
|
|
|
Если уплотняющие пластины в вершинах ротора расположены ра диально, то для анализа их работы необходимо знать тангенциальное jt и нормальное jн ускорения вершин ротора
|
|
2 |
|
|
|
|
|
|||
jt |
|
|
3 1 e2c sin2Ε |
|
|
|||||
|
|
|
|
|
|
; |
|
|
||
|
|
|
|
|
|
|||||
|
|
|
|
|
|
|||||
|
|
|
1 c 2 2ccos2Ε |
|
|
|||||
|
|
|
3 2 e(3 c 2 |
|
|
|
#(3.135) |
|||
|
|
|
4ccos2Ε) |
|||||||
jн |
1 |
|
|
|
|
|
. |
|||
|
|
|
|
|
|
|
|
|||
|
|
|
1 c 2 2ccos2Ε |
|||||||
|
|
|
|
|
|
На каждую грань ротора дейст вуют силы от давления газов, сдви нутые по фазе на 120 угла поворо та ротора
Piг 2bHpiг , |
(3.136) |
Рис. 3.31. Силы, действующие на ротор
Проекции на оси координат сил от давления газов
Pгx [(1 2)P1г (1 2)P2 |
г P3г |
]cosΕ |
||
|
|
|
|
|
3 2(P1г P2г )sinΕ ; |
|
|||
|
|
|||
Pгy [(1 2)P1г (1 2)P2 |
|
# |
||
г P3г ]sinΕ |
||||
|
|
|
|
|
3 2(P1г P2г )cosΕ . |
|
|||
|
|
|||
|
|
|
|
(3.138) |
Тогда угол, образуемый векто ром сил от давления газов с осью абсцисс, определится из выраже
ний cosΦ = Pгx/Pг или sinΦ = Pгy/Pг. Тангенциальная сила, дейст
вующая на эксцентрик,
T Pг sin(Φ 3ΕΑ. (3.139)
Радиальная сила, действующая на эксцентрик,
Z Pг cos(Φ 3ΕΑ. (3.140)
Индикаторный крутящий мо мент, действующий на эксцентрик,
M кр г Te Pг e sin(Φ 3Ε). (3.141)
Для получения диаграммы кру тящего момента многосекционного РПД необходимо диаграмму одной секции сдвинуть по фазе на неко торый угол в зависимости от по
121

рядка работы секций и моменты просуммировать.
Кроме сил от давления газов, на эксцентрик действует также центробежная сила инерции ро тора
P |
m |
p |
e 2 |
, |
(3.142) |
сp |
|
2 |
|
|
где mр – суммарная масса ротора и охлаждающей жидкости, если используется охлаждаемый ро тор.
Суммарная сила, действующая на эксцентрик,
Q T 2 (Z Pcp )2 . (3.143)
Векторную диаграмму сил, дейст вующих на эксцентрик, строят ана логично векторной диаграмме сил двигателя с кривошипно шатунным механизмом. Сначала по формулам (3.139)–(3.142) определяют измене ние сил Т, Z и Pcp по углу поворота эксцентрика, а затем строят вектор ную диаграмму (рис. 3.32, а). Период изменения сил составляет 360 .
Если эксцентрик поворачивается на угол = 3Ε, ротор поворачивает ся относительно эксцентрика на угол 2Ε, поэтому каждую точку век торной диаграммы сил, действую щих на эксцентрик, поворачивают на угол, равный 2Ε, против направ ления вращения эксцентрика. В ка честве примера на рис. 3.32, б при ведена векторная диаграмма сил, действующих на подшипник экс центрикового вала.
Развертка векторной диаграм мы, необходимая для расчета под шипников, приведена на рис. 3.33.
На коренные шейки эксцентри кового вала будет действовать цен тробежная сила Pc не только от массы mр ротора, но и от неуравно вешенной массы mэ эксцентрика
Pc (mp mэ )e 22 mвр e 22 . (3.144)
Центробежную силу Pc уравно вешивают при помощи двух проти вовесов, располагаемых на эксцен триковом валу. Если массы проти вовесов одинаковы и расположены
Рис. 3.32. Векторная диаграмма сил, действующих:
а – на эксцентрик; б – на подшипник эксцентрика
122
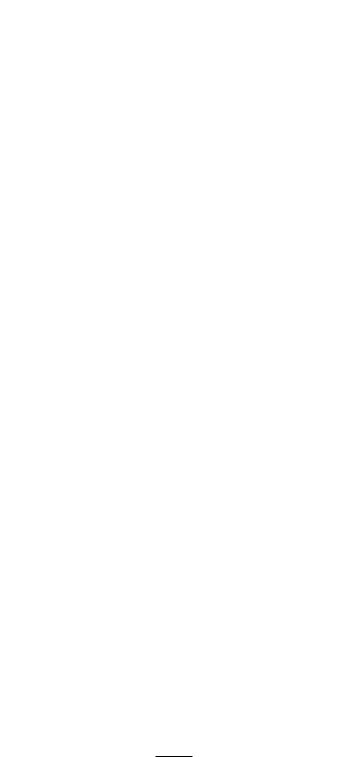
Рис. 3.33. Зависимость суммарной силы, действующей на эксцентрик, от угла поворота
симметрично относительно ротора, то масса одного из них
mпp 0,5mвр erпр , (3.145)
где rпр – расстояние от центра масс противовеса до оси вращения.
Из за переменного количества охлаждаемой жидкости в роторе и влияния температуры на ее плот ность РПД с охлаждаемым ротором менее уравновешен, чем РПД с не охлаждаемым ротором.
Уравновешивание многосекци онных РПД производится анало гично уравновешиванию двигате лей с коленчатым валом.
3.4. Виброактивность, шум двигателей и методы их снижения
Обеспечение умеренного уровня шума и снижение виброактивности является важным требованием, предъявляемым к вновь создаваемым двигателям всех типов и назначений. Особенно остро такая проблема свя зана с созданием новых и модерниза цией существующих быстроходных транспортных двигателей. Законода тельные нормы по уровню шума не прерывно ужесточаются, требуя по нижения уровня внешнего шума от транспортных средств до 80 дБА.
Причиной шума, создаваемого при работе поршневого двигателя,
являются рабочие процессы, про текающие в цилиндре двигателя и его системах.
При движении по впускному тру бопроводу свежий заряд, взаимодей ствуя с элементами конструкции, создает шум "впуска". Процессы сжа тия, сгорания и расширения в ци линдре вызывают вибрацию деталей, образующих камеру сгорания двига теля, с последующей передачей энер гии колебаний на наружные стенки элементов корпуса двигателя.
На акустическое излучение при сгорании влияет и теплота, подво димая к рабочему телу в цилиндре. Колебания двигателя на подвеске также дают акустическое излуче ние. Следует указать и на удары со прягаемых деталей механизма газо распределения, топливной аппара туры, а также на шум, создаваемый агрегатами двигателя.
Вибрация наружных поверхно стей является одной из главных причин акустического излучения в окружающее пространство и опре деляет так называемый структур ный шум двигателя.
Мощным источником шума явля ется процесс выпуска отработавших газов. В случае отсутствия глушите лей уровень шума при выпуске отра ботавших газов больше уровня всех остальных шумов при работе двига
123

теля. Однако наличие разнообразных вариантов глушителей и совершен ных конструкций впускных систем позволяет существенно ограничить уровень внешнего шума, связанного с процессом впуска свежего заряда и выпуска отработавших газов.
Непосредственный шум сгорания во многом зависит от количества то плива, находящегося в цилиндре к началу сгорания. Более поздний впрыск, меньшая задержка воспла менения, повышение температуры стенок камеры сгорания способству ют снижению уровня шума во время сгорания. Меньшим уровнем шума характеризуются двигатели с разде ленными камерами сгорания, но они имеют повышенный расход топ лива. Двигатели с принудительным воспламенением в целом отличают ся меньшим уровнем шума при ра боте по сравнению с дизелями.
При оценке уровня шума двига теля используется ряд показателей, характеризующих звуковое поле в пространстве, окружающем рабо тающий двигатель. К ним относят ся среднее квадратическое звуковое давление р, интенсивность звука I, звуковая (акустическая) мощность W. Причем уровень шума опреде ляют как двадцатикратный лога рифм отношения звукового давле ния к его пороговому значению:
Lp 20lg p , p0
где р0 = 2,10 5 Па.
Интенсивность звука определя ют как десятикратный логарифм отношения интенсивности звука к пороговому значению:
L1 10lg I ,
I 0
где I0 = 10 12 Вт/м2.
Звуковая мощность определяет ся как десятикратный логарифм отношения акустической мощно сти к пороговому значению:
LW 10lg W ,
W0
где W0 = 10 12 Вт.
При использовании приведен ных основных характеристик в сво бодном звуковом поле численные их значения даются в децибелах и оказываются идентичными незави симо от измеряемой величины.
Для числовых оценок уровня шума с учетом специфики воспри ятия человеком звука на различных частотах используют частотную ха рактеристику А шумомера. При этом уровень звука выражается в де цибелах по шкале А. Согласно стан дартам уровень шума работающего двигателя измеряют в акустических октавах со среднегеометрическими частотами 63, 125, 250, 500, 1000, 2000, 4000 и 8000 Гц. Важной харак теристикой акустического излуче ния является спектр шума, показы вающий распределение звуковой энергии по частотам. Различают дискретные составляющие – набор гармоник и непрерывную, сплош ную область спектра шума.
При проектировании двигателя его конструкция должна быть проанализирована для определе ния составляющих шума путем составления акустического балан са с последующим определением путей снижения уровня шума. В данном разделе основное внима ние уделяется связи виброактив ности двигателя с конструкцией корпусных деталей.
Шум, производимый колебания ми наружных поверхностей, называ ют структурным. Расчет уровня структурного шума включает чис
124

ленную оценку источника вибрации в диапазонах октав 63 Гц–8 кГц, расчет уровня вибрации элементов корпуса двигателя и звукового излу чения. Сложная форма корпусных деталей двигателя затрудняет ис пользование аналитических методов при расчете уровня вибрации и дела ет наиболее эффективными числен ные методы, к которым относятся прежде всего методы конечных эле ментов (МКЭ) и граничных элемен тов (МГЭ). Эффективные модели расчета уровня структурного шума сочетают применение обоих мето дов. МКЭ используется для опреде ления собственных частот и форм колебаний корпусных деталей дви гателя, МГЭ – при расчете излуче ния шума в окружающую среду.
Решение задачи о нахождении собственных частот и форм колеба ний корпусных деталей сводится к определению собственных значенийj и соответствующих собственных векторов {, j }T [u j v j w j ] ли
нейного оператора [А]. Разрешаю щее матричное уравнение имеет вид:
[A]{,} {,Ν4 |
(3.146) |
где uj = ujacos( j ); vj = vjacos( jΑΟ wj = = wjacos( j ); j 2j ; [A] = [M]1[K];
[M] – матрица массы; [K] – матри ца жесткости.
Последовательность значений j в порядке возрастания значений называется спектром собственных частот. Формы главных колебаний ,j являются собственными вектора ми матрицы [А].
Для построения трехмерной ко нечно элементной модели корпус ных деталей в сборе создается твер дотельная модель с последующей генерацией конечно элементной сетки. На рис. 3.34 представлена объемная конечно элементная мо дель корпуса рядного четырехци линдрового автомобильного дизе ля, содержащая около 100 тыс. эле ментов и 40 тыс. узлов.
Рис. 3.34. Конечно элементная модель корпуса рядного четырехцилиндрового автомобильного дизеля
125

При расчете уровня структур ного шума двигателя выделяются усилия, оказывающие наиболь шее влияние на вибрацию кор пусных деталей и соответственно их шумоизлучение. В возникно вении вибрации и структурного шума участвуют воздействия от работы большинства механизмов
исистем двигателя, прежде всего силы, действующие в кривошип но шатунном механизме, в меха низме газораспределения, в при водах различных агрегатов, в топ ливной аппаратуре.
Сучетом логарифмической за висимости между громкостью, вос принимаемой человеческим ухом,
иэнергией шумового сигнала ис точники шума, уровень звукового давления которых ниже на 10 дБА наиболее громкого источника, можно не учитывать при расчетах и ограничиться учетом основных ис точников. Осевая сила Р (сила от давления газов, силы инерции), бо ковая сила N и опрокидывающий
момент Моп = Мкр относятся к ос новным силовым факторам, ини
циирующим структурный шум. Пе ременная по величине и направле нию сила N, воздействуя непосред ственно или через гильзу цилиндра на корпус двигателя, вызывает виб рацию его наружных поверхностей. Сила Р непосредственно воздейст вует на головки цилиндров, через опоры коленчатого вала – на ниж нюю часть картера, а также различ ные крышки, включая поддон двигателя.
Существенное влияние на виб рацию может оказывать вторичная динамика поршня, связанная с его перекладками в течение рабочего цикла двигателя. В общем случае каждое из рассматриваемых усилий F,j приводится к неподвижным точ кам их воздействия на корпус. Оп
ределяются гармонические коэф фициенты ряда Фурье. При анали зе виброакустических процессов вместо тригонометрических функ ций часто используют показатель ную функцию:
ei cos i sin1
Для нахождения отклика меха нической системы на возмущаю щие силы давления газов в ци линдре и силы инерции, возни кающие в кривошипно шатунном механизме, решается задача о вы нужденных колебаниях. Подле жащая решению система диффе ренциальных уравнений имеет вид:
|
2, |
|
, |
[K]{,} {Fб ( )} , |
|
[M] |
|
# |
[c] |
# |
|
|
2 |
|
|
|
|
|
|
|
|
|
(3.147) |
где [c] = [М] + Φ[К] – матрица
демпфирования; Fб{ } = |
(Cj + |
|||
+ iD)ei |
– гармоническая |
состав |
||
|
j |
|
|
|
ляющая возмущающей силы; ,j{ } = |
||||
= (A |
+ iB )ei – узловые перемеще |
|||
j |
|
j |
|
|
ния; i |
1 |
– мнимая единица. |
На каждой гармонике линейча того спектра прикладывается ам плитуда силового воздействия и с учетом демпфирования вычисляет ся отклик – перемещение и вибро скорость.
В случае систем с большим чис лом степеней свободы, к которым относят корпусные детали двигате ля, решение системы (3.146) осу
ществляется |
методом разложения |
|||
по базису собственных векторов: |
||||
|
|
|
|
(3.148) |
, |
6 j , j i6Φ j , j ei . |
|||
|
m |
m |
|
|
Используя выражение (3.148), получают m систем уравнений для
126

нахождения
j и Φj:
M 2 K
|
j |
j |
|
Cj |
|||
|
|||
|
C j |
|
|
|
# . |
||
|
D j |
|
пар коэффициентов
Cj jM j 2 K j ! Φ j #
(3.149)
Для определения излучения зву ка корпусом двигателя решается волновое уравнение
2 p |
1 |
2 p |
, |
(3.150) |
||
c 2 |
|
2 |
||||
|
|
|
где р = р(x, y, z) – звуковое давле ние.
В качестве граничных условий используют изменение во времени давления на границе Г1 тела
Pг1 Ε(2, ) |
(3.151) |
или производную давления по нор мали n к границе тела Г2
p Π(2, ). (3.152)
nГ 2
Для нахождения производной в уравнении (3.152) используют гра ничное условие Гельмгольца
p |
|
2,n |
, |
(3.153) |
|
n |
2 |
||||
|
|
|
где – плотность воздуха. Решение волнового уравнения
(3.150) с граничными условиями
(3.151)–(3.153) производится МГЭ. На рис. 3.35 приведена гранично элементная модель корпуса рядно го четырехцилиндрового автомо бильного дизеля, содержащая 2000 четырехугольных граничных эле ментов.
Рис. 3.35. Гранично элементная модель корпусных деталей рядного четырехцилиндрового авто мобильного дизеля
127

Рис. 3.36. Конструкция корпуса четырехцилиндрового быстроходного автомобильного дизеля:
а – исходная; б – измененная
Изложенный подход с примене |
ных ребер жесткости был снижен |
|
нием МКЭ и МГЭ позволяет оце |
уровень структурного шума при |
|
нить влияние изменения конструк |
близительно на 3 дБА. В дальней |
|
ции корпусных деталей на вибро |
шем при рассмотрении основных |
|
акустические характеристики дви |
деталей двигателя будут рассмотре |
|
гателя. |
ны конкретные конструкторские |
|
На рис. 3.36 представлены ис |
мероприятия, направленные |
на |
ходная и измененная конструкции |
улучшение виброакустических |
ха |
корпуса четырехцилиндрового бы |
рактеристик современных двигате |
|
строходного автомобильного дизе |
лей, уровень шума которых не дол |
|
ля. За счет введения дополнитель |
жен превышать 90–95 дБА. |
|

Глава 4
ПОРШНЕВАЯ ГРУППА
4.1. Основы конструирования поршней
Поршневая группа (ПГ) двигате лей с тронковым КШМ включает поршень, поршневые кольца и поршневой палец. В двигателях с крейцкопфом в ПГ входит шток, не подвижно присоединенный к порш ню. Поршень воспринимает давле ние горячих газов в рабочем цилинд ре двигателя и передает усилие от этого давления через поршневой па лец и шатун на шатунную шейку ко ленчатого вала, где в результате соз дается крутящий момент. Крутящий момент, снимаемый с коленчатого вала, в зависимости от назначения двигателя передается трансмиссии автомобиля, трактора, на винт судна, самолета, ротору электрогенератора
идр. Поршень является наиболее характерной деталью ДВС, непо средственно реализующей его тер модинамический цикл.
Кроме давления горячих газов, превышающего часто 10–15 МПа, на поршень действуют тепловые на грузки, связанные с отводом в пор шень при работе двигателя значи тельного количества теплоты от го рячих газов и выделяющейся в ре зультате трения при движении эле ментов поршневой группы. В быст роходных двигателях заметной вели чины достигают инерционные на грузки, вызываемые возвратно по ступательным характером движения поршня с переменным по величине
инаправлению ускорением. При высоком уровне перечисленных на грузок поршни современных дви гателей должны надежно функцио нировать наряду с другими элемен
тами двигателя в пределах заданного достаточно продолжительного срока службы. Причем не допускается по явление усталостных или термоуста лостных трещин, а также значитель ных износов канавок поршневых ко лец, боковой поверхности корпуса поршня, отверстия под поршневой палец. Поэтому поршни современ ных двигателей изготовляются из ка чественных материалов (главным образом металлов) с достаточно вы сокими механическими, теплофизи ческими и технологическими харак теристиками.
Поршни быстроходных двигате лей, в первую очередь автомобиль ных, мотоциклетных, авиационных, тракторных и некоторых других ти пов должны иметь меньшую массу и изготавливаться, как правило, из алюминиевых сплавов, обладающих достаточно высокими прочностны ми свойствами и износостойкостью. Однако при росте среднего эффек тивного давления при использовании газотурбинного наддува, особенно в двигателях больших размеров, жаро прочность алюминиевых сплавов часто оказывается недостаточной. Несмотря на применение специаль ной системы охлаждения поршня (главным образом, с помощью мас ла), температуру в отдельных местах днища поршня не удается удержать на приемлемом для алюминиевых сплавов уровне. В таком случае для всего поршня или его наиболее на гретой части (головки) используются более жаропрочные материалы: чу гуны, легированные стали. В послед нее время возрос интерес к нетради ционным материалам: конструкци онной керамике, композитам, ин
129

Рис. 4.1. Геометрические соотношения элементов поршня из алюминиевого сплава автомобильно го дизеля (в долях диаметра цилиндра D):
1 – кромка камеры сгорания; 2 – наружная кромка; 3 – вставка; 4 – зона бобышки
терметаллидам, превосходящим по некоторым показателям применяе мые обычно металлические сплавы.
На рис. 4.1 приведена типичная конструкция поршня, широко применяемая в различных вариан тах в автомобильных и тракторных дизелях. Там же даны геометриче ские соотношения для элементов поршня известной по производству поршней фирмы Mahle.
Поршень можно условно разде лить на три пояса в направлении оси цилиндра:
•верхний (жаровой) длиной Н0, соответствующий головке поршня
изанимающий место от верхней кромки днища до первого поршне вого кольца;
•уплотнительный (место рас положения поршневых колец) дли
ной Н1;
• опорный длиной Н2, соответ ствующий юбке поршня и месту расположения поршневого пальца в тронковых двигателях.
От значения длины указанных поясов поршня зависят его осевой размер, масса, силы инерции и мно гие важные показатели работы дви гателя. Так, приближение верхнего компрессионного кольца к кромке днища поршня уменьшает вредный (мертвый) объем и способствует
улучшению экономических и эколо гических показателей двигателя. Од нако в данном случае условия рабо ты поршневых колец становятся бо лее тяжелыми. Сокращение длины уплотнительного и опорного поясов ведет к уменьшению высоты порш ня и двигателя в целом. Но при чрез мерном уменьшении перемычек ме жду кольцевыми канавками их проч ность может оказаться недостаточ ной. Сокращение длины опорного пояса может ухудшить условия рабо ты сопряжения юбки поршня с ци линдром, в том числе повысить удельные нагрузки, уровень вибра ции, привести к увеличению расхода смазочного масла. Кроме длины опорного пояса, т.е. длины юбки, важна и форма ее поверхности. Ци линдрическая форма юбки поршня, особенно в случае поршня из алю миниевого сплава, не является бла гоприятной для работы сопряжения поршень цилиндр.
Поршни современных двигателей выполняются с различными профи лями боковой поверхности: сту пенчатыми, состоящими из несколь ких сопряженных конусов (отклоне ния от прямолинейной образующей, равные сотым долей миллиметров), криволинейными, в частности, с бочкообразным профилем.
130