
3863
.pdf3.Назовите основные виды рабочих органов машин для разработки грунтов.
4.Опишите конструкцию рабочего органа рыхлителя.
5.Опишите конструкцию рабочего органа бульдозера.
6.Опишите конструкцию рабочего органа скрепера.
7.Опишите конструкцию рабочего органа экскаватора.
ЛАБОРАТОРНАЯ РАБОТА №2
ИЗУЧЕНИЕ РАБОЧЕГО ПРОЦЕССА И КОНСТРУКЦИИ РЫХЛИТЕЛЕЙ
2.1. ЦЕЛЬ РАБОТЫ
Цель работы заключается в изучении рабочего процесса, конструкции и определении производительности рыхлителей.
2.2. ТЕОРЕТИЧЕСКИЕ СВЕДЕНИЯ
Рыхлители применяют для послойного рыхления грунта и некоторых горных пород на отдельные куски или глыбы с размерами, удобными для по- грузки или последующей разработки. С помощью рыхлителей можно удалять из грунта крупные камни, взламывать различные покрытия и разрабатывать мёрзлый грунт. Рыхлить грунт механическим способом обычно экономически выгоднее, чем буровзрывом.
Рабочим органом рыхлителя являются стойки-зубья, погружаемые в грунт и рыхлящие его при движении. До недавнего времени эти машины вы- пускали только прицепными. Они имели большую массу, облегчающую вне- дрение зубьев в грунт, но маломаневренные и малопроизводительные – могут работать с базовыми тягачами без дополнительных видов рабочего оборудова- ния.
В последние годы выпускают только навесные рыхлители, свободные от указанных недостатков. Их вес передаётся на базовый тягач, чем увеличивается тяговое усилие его по сцеплению. Эти рыхлители имеют большую маневрен- ность, их можно агрегатировать с бульдозерным или погрузочным оборудова- нием, что повышает универсальность машины.
Рыхлители навешиваются на тракторы различных классов, чем обеспечи- вается выполнение разнообразных работ. Глубина рыхления изменяется в преде- лах 0,4…1,0 м, иногда даже до 1,5 м. Конструкция рыхлительного оборудования определяется схемой его подвески к базовой машине.
Трехзвенная подвеска (рис. 2.1, а) отличается простотой конструкции и малой металлоёмкостью. Вместе с тем существенный недостаток её – зависи-
11
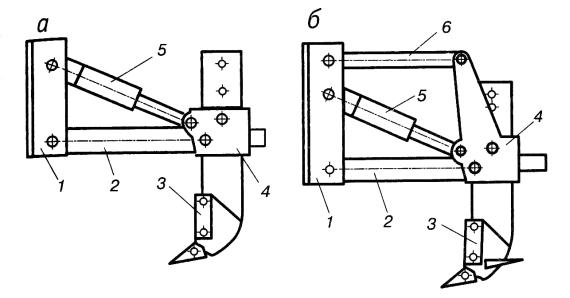
мость угла резания зубьев от заглубления: он изменяется от максимального в начале заглубления до минимального на полной глубине рыхления.
Четырёхзвенная подвеска рыхлителя (рис. 2.1, б) отличается большей ме- таллоёмкостью, но применяют её чаще, так как угол резания остаётся почти по- стоянным, что увеличивает срок службы наконечников рабочих органов. Суще- ственным преимуществом такой подвески является и то, что рабочий орган при опускании на грунт отодвигается от базового тягача, вследствие чего исключа- ется заклинивание кусков породы между рабочим органом и гусеничным ходо- вым оборудованием. Четырёхзвенная подвеска позволяет разрушать грунт при подъёме рабочего органа, что невозможно при подвеске трёхзвенной.
Рис. 2.1. Конструктивные схемы навесных рыхлителей:
а – трёхзвенного; б – четырёхзвенного; 1 – опорная рама; 2 – нижняя тяговая рама; 3 – рыхлящий зуб; 4 – рабочая балка; 5 – гидроцилиндр подъёма/опускания рыхлителя; 6 – верхняя тяговая рама
Известны (рис. 2.2) четырех- и многозвенные рыхлители со ступенчатым регулированием угла рыхления. В четырехзвенных конструкциях угол рыхления регулируют, изменяя длину одной из тяговых рам, в трехзвенных – поворотом зуба на нижнем пальце. Существуют четырехзвенные конструкции, в которых верхняя тяговая рама имеет отверстия для шарнирного соединения с рабочей балкой. Палец шарнирного соединения соединён со штоком гидроцилиндра од- ностороннего действия и переставляется дистанционно.
Гидроцилиндр, установленный вместо верхней тяговой рамы, позволяет дистанционно регулировать угол рыхления (рис. 2.2, в). Основной недостаток такой схемы – в ограничении диапазона регулирования угла рыхления величи- ной ≈ 30°, что сужает возможности эффективного использования рыхлителей на разработке сезонно-мерзлых грунтов в стесненных условиях городского строительства.
12

Рис. 2.2. Варианты четырёх и многозвенных конструкций рыхлительного обо- рудования:
а – трансформируемый в трёхзвенный; б – с переносом шарнира крепления верхней тяги; в – с гидроцилиндром регулировки угла рыхления вместо верхней тяги; г и д – с отдельным механизмом регулировки угла рыхления; е, ж, з, и – с регулировкой угла рыхления и сложным законом его изменения по глубине рыхления.
Использование механизма рыхлительного оборудования с плечами раз- ной длины (рис. 2.2, б, е, и) обеспечивает изменение угла рыхления в начале за- глубления от 44 до 61°, что позволяет более точно подстраивать рыхлитель под свойства грунтов. Расстояние между шарнирами опорной рамы можно умень- шать, передвигая верхнюю тяговую раму в нижнее положение (рис. 2.2, б), и тем самым, увеличивая угол рыхления в момент заглубления и просвет под зу- бом в транспортном положении. Это облегчает рыхление откосов, улучшает маневренность бульдозерно-рыхлительного агрегата и снижает опасность за- клинивания материала между зубом, трактором и нижней тяговой рамой. Су- ществуют механизмы, которые можно трансформировать из четырёхзвенного в трёхзвенный и наоборот. Это достигается совмещением оси вращения верхней и нижней тяговых рам в двукратном нижнем шарнире (рис. 2.2, а). Для дистан-
13
ционного управления процессом трансформации проушину шарнира крепления верхней тяги к опорной раме располагают в вертикальных ползунах и переме- щают в крайние положения гидроцилиндром.
Значительными возможностями располагают рыхлители с регулируемым углом рыхления и сложной траекторией движения наконечника зуба (рис. 2.2, е, ж, з, и), позволяющие реализовать наиболее рациональные режимы разработки мерзлых и разборно-скальных грунтов при максимально возможном использо- вании тяговых возможностей базового тягача. Также известны многозвенные механизмы, в которых угол рыхления регулируется отдельным механизмом (рис. 2.2, г, д), присоединённым к четырехзвенной навеске. При этом гидроци- линдры регулирования угла устанавливают между шарниром в верхней части рабочей балки и двукратным шарниром соединения верхней (или нижней) тя- говых рам с трёхшарнирным звеном четырехзвенного механизма. Опорная рама оборудования рыхлителя крепится к корпусу заднего моста трактора. Если кор- пус моста изготовлен из чугуна, опорную раму крепят к раме трактора с помо- щью специально привариваемых к ней проушин. К опорной раме шарнирно крепятся нижняя и верхняя (при её наличии) тяговые рамы, а также гидроци- линдры подъёма/опускания рыхлителя. Гидроцилиндры подъёма/опускания обычно устанавливают по диагонали и штоками вниз (для повышения напор- ных усилий). Обычно они имеют одинаковый диаметр с гидроцилиндрами из- менения угла рыхления, но разную величину хода штока. Известно значитель- ное количество вариантов механизма изменения угла рыхления.
Рабочее оборудование крепят к раме базового тягача или к корпусу его заднего моста (рис. 2.3). Крепление к балкам гусеничных тележек менее рацио- нально из-за повышенной металлоёмкости, увеличения габаритов машины, ус- ложнения обслуживания ходовой части из-за плохого прохождения комьев раз- рушенного грунта или породы под охватывающей рамой.
В зависимости от назначения рыхлителя и вида выполняемых работ чис- ло зубьев может быть от 1 до 5. На тяжёлых работах при рыхлении горных по- род и мёрзлых грунтов применяются одностоечные рыхлители; для рыхления тяжёлых грунтов можно применять пятизубые рыхлители. Зубья выполняют прямыми или изогнутыми и обычно снабжают съёмными наконечниками. Подъём и заглубление рабочего органа производятся гидроцилиндрами.
Основными параметрами рыхлителя являются: наибольшее тяговое уси- лие базовой машины по сцеплению РТ.СЦ, наибольшая глубина рыхления hР, число зубьев z, ширина наконечника стойки bН, угол резания α, расстояние lР от низшей точки рамы до опорной поверхности машины при максимальной глу- бине рыхления, расстояние lН от наконечника зуба в крайнем нижнем положе- нии до оси ведущей звёздочки трактора, шаг зубьев t.
Как правило, рыхлительное оборудование монтируют на гусеничных бульдозерах, а получающиеся в итоге машины называют бульдозерно- рыхлительными агрегатами (рис. 2.3). Технические требования к базовым трак- торам для рыхлителей обусловлены функциональными качествами этих машин
14

с учетом наиболее распространенной технологии производства работ, грунто- вых и эксплуатационных условий и общей сферы применения машин.
Рис. 2.3. Бульдозерно-рыхлительный агрегат:
1 – рабочее оборудование рыхлителя, 2 – гусеничный промышленный трактор, 3 – бульдозерное оборудование
В зависимости от условий эксплуатации операции рыхления бульдозер- но-рыхлительного агрегата составляют 10...40% (в среднем 30%) общего вре- мени его работы. Типовая работа рыхлителя состоит из внедрения рабочего ор- гана (рыхлящих зубьев) в грунт или породу, рабочего хода с рыхлением на длину, определяемую размерами рабочей площадки, извлечения зубьев из грунта, разворота или остановки и движения задним ходом в исходное для сле- дующего рабочего хода положение, а также маневрирования. Каждый после- дующий рабочий ход производится на определенном расстоянии от предыду- щего. При работе перекрестным способом (т. е., когда часть рабочих проходов в определённой последовательности совершается под углом к предыдущим) после рыхления площадки в одном направлении требуется смена исходного по- ложения для работы в перпендикулярном направлении. При движении на подъ- ём рыхление не производится.
2.3.ПОРЯДОК ПРОВЕДЕНИЯ РАБОТЫ
2.3.1.Используя лабораторный практикум, плакаты и кинофильм, изучить общее устройство и назначение рыхлителей.
2.3.2.Определить основные параметры и производительность рыхлителя по исходным данным варианта (табл. П 1), используя выражения (2.1) и (2.2).
Техническая производительность рыхлителя:
15
ПТ = |
|
B hР LРХ kТ |
|
, м3/ч, |
(2.1) |
||
|
LРХ |
+ |
tР |
|
|||
|
|
|
|
|
|||
|
|
1000VРХ |
3600 |
|
|
|
|
|
|
|
|
|
|
где В – ширина захвата при рыхлении, м; hР – средняя глубина рыхления, м; LРХ – средняя длина рабочего хода в одну сторону, в расчётах принимаем LРХ = 100 м; kТ – коэффициент, учитывающий потерю времени на подход толкача и увеличе- ние рабочей скорости, kТ = 0,8…0,95; VРХ – средняя скорость рабочего хода, км/ч; tР – время одного разворота в конце участка, tР = 15…20 с.
Ширина захвата при рыхлении находится по формуле
В = k |
b |
h |
+ 2h |
tgµ + t (z - 1) |
, м, |
(2.2) |
|
П Н |
Р |
Р |
|
|
|
где kП – коэффициент перекрытия, kП = 0,65…0,85; bН – ширина наконечника стойки, м; µ – угол скола грунта от вертикали, µ = 15…45°; t – шаг зубьев; z – количество зубьев.
2.4. ФОРМА ОТЧЁТА
1.4.1.Цель работы.
1.4.2.Описание назначения и устройства рыхлителей.
1.4.3.Определение основных параметров и производительности рыхлите- ля по формулам (1.1), (1.2) и варианту приложения (табл. П.1).
1.4.4.Формулирование кратких выводов по лабораторной работе.
КОНТРОЛЬНЫЕ ВОПРОСЫ
1.Поясните назначение рыхлителей.
2.Начертите конструктивную схему рыхлительного агрегата.
3.Начертите конструктивные схемы рыхлительного оборудования.
4.Объясните, в чём отличие трёхзвненной и четырёхзвенной подвески рыхлителя.
5.Как определить техническую производительность рыхлителя?
ЛАБОРАТОРНАЯ РАБОТА №3
ИЗУЧЕНИЕ РАБОЧЕГО ПРОЦЕССА И КОНСТРУКЦИИ БУЛЬДОЗЕРОВ
3.1. ЦЕЛЬ РАБОТЫ
Цель работы заключается в изучении рабочего процесса, конструкции и определении производительности бульдозеров.
16

3.2. ТЕОРЕТИЧЕСКИЕ СВЕДЕНИЯ
Бульдозер – землеройно-транспортная машина, представляющая собой базовый тягач 1, оснащенный отвальным навесным рабочим оборудованием, в которое входит отвал 3 с ножами 5 и козырьком 4, толкающие брусья 6, подко- сы 7 и гидроцилиндры 2 (рис. 3.1).
Рис. 3.1. Конструктивная схема бульдозера с неповоротным отвалом
Отвал изготовляют в виде коробчатой сварной конструкции с накладками жесткости, приваренными к тыльной стороне. Толкающие коробчатые брусья передними концами шарнирно соединяют с проушинами тыльной стороны от- вала, а задними – с упряжными шарнирами 8, плиты которых приварены к бал- кам гусеничных тележек трактора. Подкосы соединяют верхнюю часть отвала с проушинами толкающих брусьев; перестановкой подкосов можно изменять угол резания в пределах 45…60°. Вследствие трудоемкости операций по пере- становке подкосов их заменяют гидроцилиндрами.
Бульдозер послойно срезает грунт и одновременно перемещает его воло- ком по поверхности земли к месту укладки. Бульдозеры применяют для возве- дения насыпей из грунтов боковых резервов, разработки выемок, грубого пла- нирования поверхностей земляных сооружений, для засыпки рвов, траншей, обваловки сооружений, а также для подготовительных работ – валки отдельных деревьев, срезки кустарника, корчевания отдельных пней и камней. Бульдозеры
17
используют также для планирования грунтовых отвалов при работе экскавато- ров и землевозов, образования штабелей сыпучих материалов (песка, щебня) и их подачи к перерабатывающим агрегатам, для снегоочистки, формирования террас на косогорах, производства вскрышных работ в карьерах.
На базе гусеничных тягачей также серийно выпускают универсальные бульдозеры с поворотным отвалом. У бульдозера этого типа вместо толкающих брусьев установлена арочная рама, к вершине которой шарнирно присоединен отвал (рис. 3.2). Края отвала удерживают толкатели, соединенные ползунами с боковыми направляющими рамы. Последняя соединена с кронштейнами рамы трактора. Отвал поворачивают в плане гидроцилиндрами. Ползуны толкателей при этом изменяют положение на направляющих рамы и фиксируются заклад- ными штырями. Задние проушины толкателей можно переставлять по высоте относительно ползунов, изменяя таким образом угол резания. Опуская про- ушину одного толкателя и поднимая проушину другого, можно произвести по- перечный перекос oтвaлa.
Бульдозеры классифицируются следующим образом.
По назначению бульдозеры делятся: бульдозеры общего назначения; бульдозеры специального назначения. Бульдозеры общего назначения предна- значены для выполнения землеройно-планировочных и строительных работ. Бульдозеры специального назначения предназначены для чистки снега, разра- ботки торфа и др.
По мощности двигателя Nе и номинальной силе тяги ТН:
|
Nе, кВт |
ТН, кН |
- малогабаритные |
до 15 |
до 25; |
- легкие |
15,5…60 |
26…75; |
- средние |
60…108 |
80…145; |
- тяжелые |
110…220 |
150…300; |
- сверхтяжелые |
более 220 |
более 300. |
По рабочему оборудованию: различают бульдозер с неповоротным отва- лом, который расположен под углом 90° к продольной оси машины; бульдозер с поворотным отвалом, у которого можно изменять угол установки отвала в го- ризонтальной плоскости.
По ходовому оборудованию: гусеничные; колесные.
По системе управления: с канатно-блочной системой управления; с гидрав- лической системой управления; с комбинированной системой управления.
По размещению рабочего органа на базовой машине: с передним распо-
ложением; с задним расположением.
18
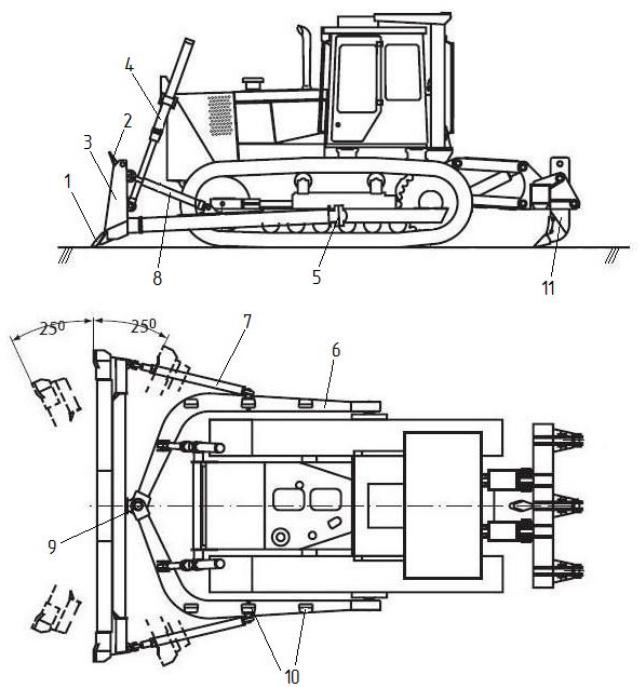
Рис. 3.2. Бульдозер с поворотным отвалом (вид сбоку и сверху):
1 – ножи; 2 – козырек; 3 – отвал; 4 – гидроцилиндры подъема и опускания отва- ла; 5 – опорный шарнир; 6 – универсальная рама; 7 – раскосы перекоса отвала; 8 – подкосы; 9 – штырь; 10 – крепление раскоса; 11 – зуб-стойка рыхлителя
В зависимости от условий работы применяют различные отвалы бульдо- зеров (рис. 3.3).
19

Рис. 3.3. Формы отвалов бульдозера:
а – прямой; б – универсальный; в – сферический; г – с боковыми рыхлящими зубьями; д – совковый для уборки: е – короткий толкающий; 1 – лобовой лист вместе с козырьком; 2 – боковые щитки; 3 – боковые ножи; 4 – угловые ножи; 5 – средние ножи; 6 – открылки; 7 – выдвижные зубья
На рис. 3.4 представлен общий вид бульдозера Б-10М.
Рис. 3.4. Общий вид бульдозера на базе трактора Б-10М
20