
3834
.pdf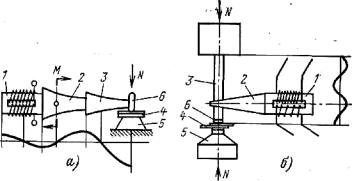
УДК 621. 396
В.С. Скоробогатов, Ю.М. Данилов
ЗАВИСИМОСТЬ РАЗРУШАЮЩЕЙ НАГРУЗКИ ОТ ПАРАМЕТРОВ РЕЖИМА УЛЬТРАЗВУКОВОЙ СВАРКИ
Приводится формула зависимости разрушающей нагрузки от параметров режима ультразвуковой сварки и контурная номограмма построенная с помощью программы "MathCAD 7.0"
Ультразвуковая сварка металлов давлением основывается на введении механических колебаний ультразвуковой частоты в зону шва, что приводит к пластической деформации зоны контакта, разрушению и удалению поверхностных пленок с созданием ювенильных поверхностей, интенсифицирует процесс образования активных центров и тем самым создает прочное сварное соединение без большой деформации свариваемых деталей. Схемы сварки приведены на рис. 1.
Рис. 1. Схемы ультразвуковой сварки.
а — инструментом с продольными колебаниями; б — инструментом с изгибными колебаниями; 1 — магнитостриктор; 2 — волновод; 3 — концентратор; 4 — свариваемые детали; 5 —опора;
6 — рабочий наконечник
Наиболее часто применяются продольные колебания в плоскости, сварки, но тем не менее не исключается возможность использования колебаний крутильного типа. Режим сварки при заданной частоте определяется главным образом тремя параметрами
— амплитудой колебаний инструмента А, мкм, усилием сжатия, Р,
61
кгс, временем сварки τ, с. Амплитуда колебаний зависит от режима работы генератора и магнитострикционного либо пьезокерамического преобразователя, коэффициента усиления волновода, определяемого его формой, и величины усилия сжатия. Увеличение времени сварки повышает прочность сварного соединения за счет роста суммарной площади узлов схватывания. Однако чрезмерная продолжительность сварки может привести к разрушению образовавшегося соединения.
Различают два типа процесса: с общим скольжением в контакте свариваемых деталей и без него. Увеличение усилия сжатия снижает амплитуду колебаний инструмента и может прекратить общее скольжение, которое является предпочтительным вариантом проведения ультразвуковой сварки. Однако, если при отсутствии общего скольжения амплитуда смещения одной детали относительно другой приближается к пороговому значению, т. е. к переходу в режим общего скольжения, также образуется качественное соединение, даже с несколько повышенной прочностью.
При испытаниях сварных точек на деталях толщиной 0,8—1 мм происходит разрушение и сварная точка отрывается, при меньших толщинах разрушение происходит по периферии точки.
Зависимость прочности от режима отражена на рис. 2. Исследовалось влияние амплитуды колебаний инструмента А,
мкм, и усилие сжатия Р, кгс, на разрушающую нагрузку Рраз, кгс, при сварке нержавеющей стали. По результатам исследований рассчитано уравнение зависимости разрушающей нагрузки от амплитуды колебаний инструмента и усилие сжатия, представляющее собой гиперболический параболоид выпуклостью вверх
Рраз = - 822 + 4,8 · Р + 50 ·А – 0,0275 · Р2 – 0,875 · А2.
Методом частных производных были найдены оптималь-ные значения амплитуды и усилия сжатия: А = 28,57 мкм,
Р = 87,27 кгс. При этих значениях разрушающая нагрузка составит Рраз = 101,74 кгс.
На основании уравнения с помощью программы "MathCAD 7.0" была построена контурная номограмма, представленная на рис. 2.
62
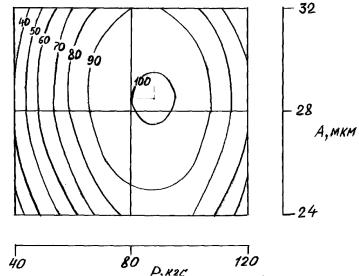
Рис. 2. Контурная номограмма зависимости разрушающей нагрузки от амплитуды колебаний инструмента и усилие сжатия
Анализируя контурную номограмму и варьируя значениями параметров режима сварки (амплитудой и усилием сжатия), можно получить требуемые значения разрушающей нагрузки.
Воронежский государственный технический университет
63
УДК 621. 396
В.С. Скоробогатов, Ю.М. Данилов РАСЧЕТ РЕЖИМА ПРИ ЭЛЕКТРОДУГОВОЙ СВАРКЕ
Приводится методика и формулы для назначения условий электродуговой сварки
Режим сварки определяется диаметром электрода d , мм, величиной сварочного тока J , А, и длиной дуги ld, мм.
Диаметр электрода d выбирают в зависимости от толщины металла или катета шва h, мм, и типа сварного соединения.
d 4.1 |
1.3 |
, мм . |
(1) |
|
|||
|
h |
|
Сила сварочного тока зависит от катета шва, типа соединения, скорости сварки, положения шва в пространстве, толщины и вида обмазки электрода, диаметра электрода и его рабочей длины. Практически силу тока определяют
J k d. |
(2) |
При сварке стальным электродом коэффициент k = 45 62 |
|
А/мм , при сварке графитовом электродом k = 18 22 |
А/мм, при |
сварке угольным электродом k = 5 8 А/мм. Обычно J >50 А. |
|
Чем короче длина дуги ld, тем выше качество наплавленного |
|
металла |
|
ld =0,5∙d+1d |
(3) |
При J > 50 A напряжение горения дуги U , в, зависит от длины дуги ld
U l d . |
(4) |
Для стальных электродов коэффициент, характеризующий падение напряжения на электродах, 10 12, для угольных35 38. Коэффициент, характеризующий падение напряжения на 1 мм длины дуги β = 2 ÷ 2,5 (длина воздушной среды).
64
Напряжение зажигания дуги U3 = 40 – 60 в для постоянного
тока, а для переменного тока U3 = 50 – 70 в. |
|
|
|
||
Производительность |
сварки |
Т, |
ч, |
зависит |
от |
продолжительности горения дуги t0 , |
ч, и коэффициента загрузки |
сварщика k = 0,4 ÷ 0,3 (в зависимости от характера выполняемой работы) [1, с. 269]
T |
t0 |
. |
(5) |
|
|||
|
k |
|
Продолжительность горения дуги зависит от количества наплавленного металла Qn , г, сварочного тока J , A, коэффициента наплавления kn (т.е. количества наплавленного электродного
металла в граммах в течении 1 ч, приходящееся на 1 А сварочного тока, с учетом марки электрода, потери металла на угар и разбрызгивание). Для тонкообмазанных электродов kn = 7 – 8 г/А∙ч, а
для толсто-обмазанных электродов kn = 10 - 12 г/А∙ч и более
t0 |
|
Qn |
. |
|
|
|
|
(6) |
J kn |
|
|
|
|
|
|||
Количество наплавленного металла, с учетом коэффициента |
||||||||
расплавления, равного kp = 8 – 14, определяют по формуле |
||||||||
Qn |
k p |
J t0 . |
|
|
|
(7) |
||
Линейную скорость сварки, при длине шва L , м, |
определяют |
|||||||
по формуле |
|
|
|
|
|
L |
|
|
|
|
|
V |
св |
|
. |
(8) |
|
|
|
|
|
|||||
|
|
|
|
|
t0 |
|
Суммарный расход электродов на угар, разбрызгивание и огарки составляет 25 % массы электрода.
Расход электроэнергии определяют на 1 м шва или на 1 кг наплавленного металла. При ручной сварке на постоянном токе в среднем он составляет 7 – 8 кВт∙ч/кг, а на переменном – 3,5
кВт∙ч/кг.
Оборудование рабочего места для ручной сварки состоит из сварочного аппарата, стола, стеллажа, предохранительного щита, электродержателя, защитной одежды и различных сборочно-сварных
65
приспособлений. Рабочий пост сварщика находится в изолированной кабине, куда подводится ток.
Штучно-калькуляционное время на дуговую сварку
определяется по формуле |
|
Тшк = Тн.шк ∙ L∙ K + tвн , мин |
(9) |
Неполное штучно-калькуляционное время Тн.шк на один метр длины шва L, м, определяется по формуле (10) и учитывает величину катета шва h от 4 до 8 мм
Tн.шк = 15,9 – 3,9 ∙ h + 0,45 ∙ h2, мин (10)
Соотношение величины катета шва h от 4 до 10 мм и площади поперечного сечения шва F от 24 до 85 мм
F = 3,33 + 3,17∙ h + 0,5∙ h2, мм |
(11) |
Основное время горения дуги и наплавления металла электрода на 1 м шва
То = 10,6 – 2,45 ∙ h + 0,3 ∙ h2 , мин |
(12) |
Время на прихватку изделий зависит от толщины свариваемого металла t от 4 до 14 мм и длины одной прихватки Lпр от 20 до 40 мм. Время на очистку от шлака и брызг одной прихватки равно 0,03 мин.
Тпр = 0,05 + 0,002 · Lпр + 0,000125 · t · Lпр, мин |
(13) |
Поправочный коэффициент К зависит от коэффициентов: вида шва Квш, температуры окружающей среды КТ, положения шва в пространстве Кпш, условий выполнения сварочных работ Ку
К = Квш · КТ · Кпш · Ку |
(14) |
При короткометражном виде шва и длине шва L от 0,05 до 0,5 м, коэффициент Квш определяется по формуле (15), а при длине шва свыше 0,5 принимается Квш = 1. При криволинейном виде шва Квш
66
= =1,05, при прерывистом виде шва Квш |
= 1 |
|
Квш = 1,291 – 0,36 · |
L ─ 0,025 · L2 |
(15) |
Для помещения без обогревания и температуры наружного воздуха от 0 до – 11° С коэффициент температуры принимается КТ = 1,1, а при температуре ниже − 11° С принимается КТ = 1,2 .При нижнем положении шва в пространстве, для различных типов швов, коэффициент положения шва принимается Кпш = 1.
Для стыковых соединений без скоса кромок односторонних
швов с толщиной металла или катета шва |
h = 1 - 6 мм |
|
Кпш = 1 + 0,35∙ П ─ 0,05∙ П. |
(16) |
|
Для двухсторонних толщиной h = 3 мм |
|
|
Кпш = 1,3 ─ 0,25∙ П ─ 0,025∙ П2, |
(17) |
|
а толщиной h = 4-8 мм |
|
|
Кпш = 1,4 + 0,35∙ П ─ 0,05∙ П2. |
(18) |
|
Для швов, тавровых соединений без скоса кромок, |
||
односторонних и двухсторонних при h = 4-20 мм |
|
|
Кпш = 1,5 + 0,35∙ П ─ 0,05∙ П2. |
(19) |
|
В формулах (16) - (19) при |
вертикальном |
положении |
шва |
|
|
П = 1, при горизонтальном П = 2, при потолочном П = 3. Коэффициент, зависящий от условий работы, определяется
по формуле (20). В удобном положении У = 1, в неудобном У = 2, в закрытых свободных или полуоткрытых тесных объемах сечением не более 0,7 м2 с двумя днищами У = 3
Ку = 0,94 + 0,07 · У ─ 0,01 · У 2. |
(20) |
Вспомогательное время tв.и. зависящее от изделия, состоит из времени на установку в приспособление или на рабочее место
67
свариваемых изделий tв.у. |
вручную, поворот tв.п. вручную, снятие |
|||
и транспортировку вручную tв.с. |
при массе изделия Q, от 5 до 30 кг, |
|||
определяется по формулам (21) - (24) |
|
|
||
tв.и. = tв.у. + tв.п + tв.с. , мин; |
|
(21) |
||
tв.у = |
0,6 + 0,03· Q + 0,02· Q 2 , мин, |
(22) |
||
tв.п. = |
0,1 + 0,005· Q , мин, |
|
(23) |
|
tв.с. = |
0,02· Q |
, мин, |
|
(24) |
При массе изделия |
до 100 кг tв.у. |
= tв.п. = 1,6 |
мин, |
|
tв.с. = 1,1(транспортировка краном). |
|
|
||
Время на закрепление и открепление деталей tз прижимными |
||||
приспособлениями, при длине завертывания |
lз = 20 - 60 мм |
|||
стационарным винтовым прижимом, определяется по формуле |
|
|||
tз = 0,2 + 0,0025 · lз |
+ 0,000125· lз2, мин, |
(25) |
||
ручными тисками |
|
|
|
|
tз = 0,15 − 0,00125 · lз + 0,0000625 · lз 2 , мин, |
(26) |
|||
пневмоприжимом. |
tз =0,15 мин. |
|
|
Время на перемещение сварщика с инструментом и протягивание им провода к рабочему месту tп на расстояние lпс = 2 - 20 м, а также свободное перемещение
tп = 0,1 + 0,05 · lпс , мин . |
(27) |
Время обслуживания рабочего места и время перерывов на отдых и личные надобности (для ручной сварки включено в размере 9 % от оперативного времени).
Подготовительно-заключительное время Т п.з. на партию деталей: получение производственного задания, электродов, инструктажа для простой работы составляет 4 мин, а для работы
68
средней сложности - 6 мин. На ознакомление с работой на партию деталей простой сложности 2 мин, средней сложности - 4 мин. На сдачу работы простой сложности- 2 мин, средней сложности-3 мин. На подготовку рабочего места и приспособлений к работе средней сложности - 2 мин.
Простой работой считается сварка несложных изделий, не требующих изучения технологической документации, подготовки приспособлений и инструктажа мастера.
Сваркой средней сложности является сварка изделий, имеющих несколько швов в различных положениях, требующих изучения технологической документации, подготовки приспособлений и инструктажа мастера.
Литература
1. Данилов, Ю.М. Технология обработки конструкционных материалов [Текст]: учеб. пособие / Ю.М. Данилов. Воронеж: ГОУВПО "Воронежский государственный технический университет", 2007. - 245 с.
Воронежский государственный технический университет
69
УДК 621. 396
В.С. Скоробогатов, Ю.М. Данилов
РАСЧЕТ РЕЖИМА ДЛЯ КОНТАКТНОЙ СВАРКИ
Приводится методика и формулы для назначения условий контактной сварки
Контактной сваркой является процесс соединения деталей нагревом в месте их контакта с сильным сжатием для обеспечения взаимодействия атомов металла. При контактной сварке детали прижимаются одна к другой с определенным усилием и нагреваются проходящим в месте контакта электрическим током.
Высокую производительность при контактной сварке можно получить, используя стержни из углеродистой стали Ст3 и Ст5 и из низколегированной стали 25Г2С, 35ГС, 30ГС, а также при монтаже каркасов сеток и других арматурных конструкций.
Количество тепла Q, Дж, выделяющееся в месте контакта свариваемых деталей при прохождении электрического тока, прямо пропорционально квадрату силы тока J, А, сопротивлению
проводника R, Ом, и времени прохождения тока |
τ, с, и определяется |
|
по закону |
Джоуля-Ленца: |
|
|
Q = 0,24 · J2 · R · τ, |
(1) |
Сумма сопротивления двух свариваемых деталей 2R зависит от коэффициента условий растекания тока в деталях Кр, коэффициента неравномерности нагрева деталей Кн, толщины двух свариваемых деталей 2·h, удельных электрических сопротивлений материалов свариваемых деталей ρ1 и ρ2, диаметра рабочей поверхности электрода dэ и определяется по формуле:
2R = Кр∙ Кн∙ 2∙ h∙ (ρ1 + ρ2 )/(π∙ dэ 2 / 4 ). |
(2) |
Коэффициент Кр зависит от отношения диаметра рабочей поверхности электрода dэ мм, к толщине двух свариваемых деталей
2·h, мм
Кр ≈ 0,41875 + 0,205 · (dэ / 2·h) ─ 0,02375 · (dэ / 2·h )2 (3)
70