
3834
.pdfузлом агрегата и поверхностью, через которую может передаваться вибрация, устанавливают прокладки или пружины; между
соударяющимися |
деталями |
— демпфирующие |
материалы, |
имеющие большое внутреннее |
трение (резина, пробка, |
войлок, |
фетр, асбест и т. п.). Однако применение демпфирующего материала дает эффект лишь в том случае, если материал плотно прижат к вибрирующей детали.
Для ослабления шума при обрубке металла делают специальные упругие прокладки с боковых поверхностей и под плитой или рельсом на которых производится обработка материала. В галтовочных барабанах интенсивность шума снижается на 20 дБ при облицовывании стенок барабана снаружи листовой резиной или войлоком.
Если изменить технологический процесс или конструкцию оборудования не представляется возможным, надо прибегать к звукоизоляции и звукопоглощению. При этом особо шумные цех и виды оборудования размещают в отдельных зданиях или в самостоятельных пролетах, отделенных капитальными стенами. Стены и потолки в производственных помещениях, в которых расположено такое оборудование, покрывают звукопоглощающими материалами (акустическая штукатурка, черепица, шерсть, войлок, торф, драпировка), что позволяет уменьшить уровни шума почти в
10 раз.
Сильный шум и сотрясение от машин значительно снижаются при установке их на специальные фундаменты из эластичных материалов. Фундаменты отделяют от других частей здания воздушными прослойками.
В некоторых случаях уменьшение шума достигается отсасыванием воздуха механической вытяжной вентиляцией (например, при резке металла). Согласно «Санитарным правилам организации технологических процессов и гигиеническим требованиям к производственному оборудованию» уже при проектировании машин и оборудования в их технические задания должны быть включены допустимые шумовые характеристики.
С целью унификации требований к изучению шума машин лабораторией шума и вибрации Института гигиены труда и профзаболеваний АМН совместно с Институтом физикотехнических радиоизмерений был разработан ГОСТ 8.055 «Машины. Методика выполнения измерений для определения шумовых
51
характеристик».
Наряду с перечисленными мероприятиями, которым принадлежит основная роль в борьбе с шумом, большое значение имеет рациональная организация труда и отдыха рабочих, а также использование средств индивидуальной защиты (противошумов) от воздействия шума. Ценным свойством противошумов является повышение их заглушающей способности по мере перехода от низких тонов к более опасным, высоким. Относительно слабое заглушение противошумами низкочастотных звуков удобно в том отношении, что в условиях шумного цеха сохраняется возможность слышать разговорную речь.
Заглушки из твердых материалов (эбонитовые) не следует применять длительное время, продолжительное пользование ими может привести к раздражению слухового аппарата с возникновением болевых ощущений. Противошумы из пластических материалов более удобны, так как подготовка их по размерам слухового прохода не представляет затруднений. Противошумы ФПШ просты по конструкции и снижают шум на 12—35 дБ по всему спектру.
Уменьшению воздействия шума на рабочих способствует регулярный кратковременный отдых во время работы в помещениях, изолированных от источников шума.
Указанные выше мероприятия должны быть отражены студентами при курсовом и дипломном проектировании оборудования в линиях электронной промышленности.
Воронежский государственный технический университет
52
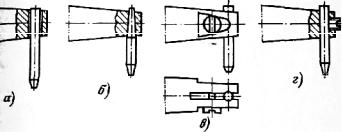
УДК 621.396.6:621.791.16
В.С. Скоробогатов, Ю.М. Данилов
РАСЧЕТ ПАРАМЕТРОВ КОНСТРУКЦИИ ИНСТРУМЕНТОВ ДЛЯ УЛЬТРАЗВУКОВОЙ МИКРОСВАРКИ
Приводятся формулы для расчета параметров конструкции инструментов используемых для ультразвуковой микросварки
Крепление инструмента к волноводной системе, с точки зрения высоких акустических свойств колебательной системы, наилучшим способом следует считать паяное или сварное соединение (рис.1, а). Однако при этом смена инструмента затруднена.
Рис. 1
Хорошо зарекомендовало себя крепление инструмента с помощью конуса (рис. 1, 6). Наибольшее распространение получило резьбовое крепление с боковым или торцевым прижатием (рис. 1, в и г) [1]. Для .получения качественных соединений большое значение имеют форма и размер рабочей части инструмента. Распространенной конструкцией ультразвукового сварочного инструмента (сварочной иглы) является стержень с конической частью. Коническая часть иглы, с помощью которой осуществляется контактирование с проволокой и передача давления на свариваемые элементы, имеет заданные радиусы закругления (рис. 2, а). Размеры рабочего торца выбираются в зависимости от диаметра dпр, мм, привариваемого проводника и рассчитываются по формулам. Диаметр торца d (или размер а) обычно составляет 3 ÷ 4 диаметра
53
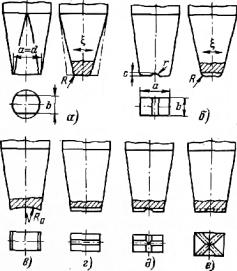
привариваемого проводника dnp. Это необходимо для уменьшения влияния неточности размещения проводника под инструментом (во избежание выскальзывания проводника).
а = (7 +4 · dпр – 0,01· dпр2) ± 10. |
(1) |
Рис. 2. Форма рабочей части инструмента
Длина деформируемого при сварке участка проводника, определяемая размером b , мм, выбирается равной (2 ÷ 3) · dпр.
b = (- 124 + 8,6 dпр – 0,05· dпр2) ± 10. |
(2) |
Размеры с и r рекомендуется определять по формулам (3, 4):
c = (0.25 ÷0.3) |
· dпр, |
(3) |
r = (0,5 ÷ 0,6) |
· dпр. |
(4) |
Радиус закругления R определяется по формуле
R = 2 + 0,33 · dnp 0,0005 dпр2. |
(5) |
54
Увеличение длины b до 4 · dnp способствует повышению прочности сварного соединения, однако это не всегда удается сделать из-за малых размеров контактных площадок микросхем. Повышению прочности соединения также способствует небольшой паз в центре рабочей части вдоль привариваемой проволоки (рис. 2, б). Этот паз ограничивает деформацию проводника, повышает эффективность передачи энергии в зону сварки. Однако необходимость тщательной центровки проволоки относительно паза (канавки) и нестабильность обрыва проволоки после второй сварки несколько сдерживает применение инструмента с продольным пазом.
На рис. 2, в показана конструкция рабочей части инструмента со слегка вогнутой поверхностью торца, которая позволяет получить качественные соединения при неплоских контактных площадках или расположенных под углом к торцу инструмента. Эта конструкция может также успешно применяться, если корпус прибора или подложка недостаточно устойчивы к ультразвуковым колебаниям, При сварке плоским инструментом происходит смещение проволочного вывода или чрезмерная деформация его.
Рабочая поверхность инструмента должна обеспечивать эффективную передачу ультразвуковых колебаний, что достигается хорошим сцеплением с привариваемым проводником. С этой целью на рабочей поверхности инструмента делают поперечную канавку (рис. 2, г). Во время деформирования проводника материал затекает в эту канавку, обеспечивая хорошее сцепление с инструментом. Недостаток инструмента с поперечной канавкой - уменьшение фактической площади сварного соединения, так как под канавкой соединение обычно не образуется.
В ряде случаев (сравнительно толстые проволочные выводы и большие размеры контактных площадок) целесообразно применять инструменты с поперечной и продольной канавками (рис. 2, д).
Наиболее эффективно и качественно происходит процесс ультразвуковой сварки при применении инструмента с крестообразным расположением канавок (рис. 2, е), особенно при сварке плоских выводов.
Хорошее сцепление инструмента с проводником обеспечивается при соответствующей обработке рабочей поверхности инструмента. Поверхность инструмента должна быть грубее поверхности, к которой присоединяется проводник, т. е. быть
55
рельефной. Необходимый микрорельеф (микронасечки) можно получить электроэрозионным способом. Удовлетворительные результаты дает шлифованная поверхность, причем если шлифовка производится в направлении, перпендикулярном направлению колебаний инструмента. Закругленная часть инструмента обязательно должна быть полированной.
Рассмотренные конструкции рабочей части инструмента предполагают ручную или механизированную подачу проводника под рабочую поверхность с помощью отдельного устройства с направляющей дюзой (капилляром). Наибольшее распространение при ультразвуковой микросварке круглых тонких проводников получил инструмент с боковым капиллярным отверстием (рис. 3)
Отверстие служит для подачи привариваемой проволоки под рабочую часть инструмента. Обычно диаметр отверстия составляет (1,5 ÷ 2) · dnp. Расположение отверстия должно быть таким, чтобы проволока, с одной стороны, свободно проскальзывала под рабочей частью, когда ее подают вперед, а с другой — не изгибалась на острой кромке выходного отверстия при перемещении инструмента назад при создании проволочной перемычки.
Такая форма инструмента позволяет легко автоматизировать подач; и отрыв проволоки и исключить влияние оператора на точность совмещения проволоки с торцом инструмента. Параметры инструмента изображенного на рис. 3 определяются по формулам ( 6 ÷ 12 ):
а = 43,23 + 1,67 · dnp, |
(6) |
||
б = 4 · dnp, |
|
(7) |
|
с = 0,2 · dnp, |
|
(8) |
|
д0 = 16,67 +1,33 |
· dnp, |
(9) |
|
е = 7 + 0,2 |
· dnp, |
(10) |
|
R = dnp, |
|
|
(11) |
r = - 6,75 + |
0,47 |
· dnp. |
(12) |
56 |
|
|
|
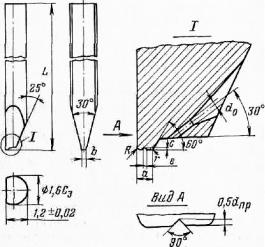
Рис. 3. Инструмент для ультразвуковой микросварки с боковым отверстием для подачи проволоки. Вид А — второй вариант
Длина инструмента рекомендуется [ 1 ]: L = 15 ± 0,2 или
L = 21 ± 0,2.
Правильный выбор профиля рабочей части во многом определяет надежность обрыва проволоки после создания перемычки. Большой радиус закругления режущей кромки (r >15 мкм) затрудняет отрыв проволоки, увеличивает длину деформированного участка проводника. Острая кромка (г ≤ 5 мкм) создает концентрацию напряжения в месте перехода от деформированного участка к недеформированному. Этого противоречия обычно избегают, применяя соответствующий наклон инструмента на 2—4° вперед при сварке первой точки, уменьшающий внедрение инструмента в районе режущей кромки. При сварке второго конца перемычки инструмент располагают перпендикулярно [или наклоняют на 1—2° в обратную сторону (рис. 4)], что обеспечивает прочное соединение и возможность легкого и четкого обрыва проволоки. Наиболее важно это при сварке алюминиевой проволоки, чувствительной к концентраторам напряжений.
57
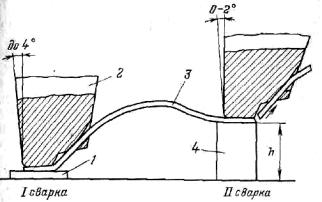
Рис. 4. Схема создания проволочной перемычки с изменением угла наклона инструмента. 1 — контактная площадка схемы; 2 — инструмент; 3 — перемычка; 4 — вывод корпуса.
Для ультразвуковой сварки также широко применяются инструменты с центральным капиллярным отверстием (рис. 5) для сварки встык с образованием шарика и внахлестку. Диаметр капиллярного отверстия dQ имеет допуск ± 3 ÷ 5 мкм, что обеспечивает свободное прохождение привариваемой проволоки и удержание шарика на контактирующей инструмента. Контактирующая площадка Ь относительно оси отверстия может располагаться концентрично с отклонением не более ±5 мкм. Такой жесткий допуск обусловлен тем, что контактирующий торец инструмента должен работать в любом направлении, а при разнотолщинности стенок длина сварных точек меняется, следовательно, меняется и прочность соединения.
Ответственным элементом в инструменте является внутренний радиус, который обрабатывается по 10-му классу шероховатости. Малейшие шероховатости кромки и другие дефекты приводят к нарушению целостности проволоки. Сопряжение конической заходной части отверстия с цилиндрическим рабочим отверстием должно быть также плавным. Параметры инструмента изображенного на рисунке 3 определяются по формулам (13 ÷ 17 ):
d0 = (- 26,7 +3,27 dпр – 0,027 · dпр2) ± 3, |
(13) |
58
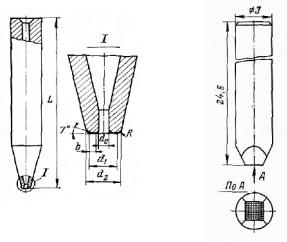
d1 = - 1,5 + 5,6 ·dпр – 0,018 · dпр2, |
(14) |
d2 = (- 17,5 + 7,2 ·dпр – 0,02 · dпр2) ± 5, |
(15) |
b = dпр, |
(16) |
R = dпр. |
(17) |
Длина инструмента рекомендуется [ 1 ]: L = 7 ± 0,2 или
L = 12 ± 0,8.
На рис. 5 показан инструмент для групповой ультразвуковой сварки, применяемый при соединении контактной рамки к кристаллу при «паучковой» технологии монтажа. Обычно инструмент имеет плоскую рабочую площадку, подвергаемую обработке (алмазной или электроэрозионной) для придания шероховатости с целью увеличения сцепления инструмента с выводами рамки.
На рис. 6 показан инструмент для групповой ультразвуковой сварки, применяемый при соединении контактной рамки к кристаллу при «паучковой» технологии монтажа. Обычно инструмент имеет плоскую рабочую площадку, подвергаемую обработке (алмазной или электроэрозионной) для придания шероховатости с целью увеличения сцепления инструмента с выводами рамки.
Рис. 5. Инструмент для ультразвуковой микросварки с центральным капиллярным
отверстием Рис. 6. Инструмент для групповой приварки выводов методом паучковой технологии
59
Материал инструмента для ультразвуковой микросварки должен обладать высокой износостойкостью, иметь минимальные акустические потери, малую склонность к адгезии с привариваемым материалом, высокую прочность, хорошую обрабатываемость.
Литература
Ультразвуковая сварка [Текст] /А.А. Грачев, А.П.,Кожевников, В.А. Лебига, А.А. Россошанский. -М.: «Энергия», 1977. 184 с.
Воронежский государственный технический университет
60