
3773
.pdf
Погрешности установки при обработке в приспособлениях, имеются в табл. 61,63 . Погрешность индексации (поворота зажимных устройств при обработке заготовок на многопозиционных станках) принимается равной 0,05 мм [1, с. 83] .
Припуски на механическую обработку отливок представлены в табл. 39 и 40. Пространственные погрешности отверстий, полученных сверлением, находятся из табл. 53. Качество наружной поверхности проката приведено в табл. 51, а качество деталей из проката, в зависимости от метода обработки - в табл. 49. Пространственные погрешности проката представлены в табл. 48, а допуски на горячекатаный прокат круглый обычной точности /В/ - в табл. 38. Допуски на горячекатаный прокат повышенной точности /Б/ имеются в источнике [4, с. 43], а на сталь калиброванную круглую в источнике [1, с.27]. Диаметры заготовок в зависимости от длины детали, изготовленной из круглого сортового проката с учетом припусков, допусков и кривизны проката представлены в табл. 36. Припуски на разрезку и обработку торца проката приводятся в табл. 5, а качество торцовой поверхности и точность резки проката по упору в источнике [3, с. 167]. Припуски на переход при обработке плоскостей в табл. 28.
7. МЕТОДИКА РАСЧЕТА ОБЩЕГО И ОПЕРАЦИОННЫХ ПРИПУСКОВ НА ОБРАБОТКУ НАРУЖНОЙ ЦИЛИНДРИЧЕСКОЙ ПОВЕРХНОСТИ ТЕЛА ВРАЩЕНИЯ
7.1. Исходные данные: деталь - вал (табл. 43, рис. 12) общей длиной L = 300 мм. Материал детали – сталь 45 . Обработке подле-
жит |
крайняя ступень |
вала lk = 100 мм до диаметра |
|
DД |
50 |
0,025 мм и среднего арифметического отклонения про- |
|
филя R a |
=1,25 мкм. Тип производства среднесерийный. |
||
|
7.2. Заготовка - |
штамповка на ГКМ выбрана по табл. 33, |
группа точности - 2 [2, с. 27-28]. Масса заготовки 9 кг. Экономическое обоснование выбора заготовки производится по методике, изложенной в п. 2.4.
7.3. Технологический маршрут обработки поверхности 50-0,025 мм назначается по табл. 66 и состоит из обтачивания черно-
40

вого и чистового и шлифования предварительного и окончательного. На этих технологических операциях ступень вала обрабатывается при установке вала на передний и задний центры.
7.4. Припуск под черновое обтачивание после штамповки
(табл. 65)
2Zв. min 2(Rz |
Ta1 |
a1 ) 2(240 250 2712) 6404мкм, |
|
a1 |
|
где Rza 1 |
=240 мкм, Ta1 = 250 мкм, табл. 57, т.к. масса 9 кг, после пес- |
|||||||||||||
коструйной обработки. |
|
|
|
|
|
|
|
|
|
|
||||
|
Пространственное отклонение заготовки (табл. 46) |
|||||||||||||
|
|
|
|
|
|
|
|
|
|
|
|
|
|
|
|
|
ρa1 |
|
ρсм2 |
ρкор2 |
. ρц2 |
1, 22 |
22 |
1,3852 |
|
||||
|
|
|
|
|
2,712 мм |
2712 мкм, |
|
|
||||||
ρсм |
1, 2 мм (табл.59), |
т.к. масса 9 |
|
кг, тип производства среднесе- |
||||||||||
рийный. |
|
|
|
|
|
|
|
|
|
|
|
|
|
|
ρкор. |
2 |
к lк |
2 10 100 |
2000 мкм [3, |
с. 166] |
при установке в |
||||||||
центрах (а при консольном закреплении ρкор. |
1 |
к lк ). |
||||||||||||
к |
5 мкм/мм (табл. 59), т.к. средний диаметр ступенчатого вала |
|||||||||||||
|
|
|
|
|
|
|
|
|
|
|
|
|
|
|
равен [1, с.72]: |
|
|
|
|
|
|
|
|
|
|
|
|
||
|
|
|
|
|
Dср. |
|
|
Dili |
|
50 мм, |
|
|
|
|
|
|
|
|
|
|
L |
|
|
|
|
||||
|
|
|
|
|
|
|
|
|
|
|
|
|
где lк = 100 мм - расстояние от сечения, для которого определяется кривизна, до опоры при установке в центрах при lк 0,5L
[3, с. 166].
Погрешность зацентровки (табл. 46)
|
|
ρц |
0, 25 |
δ2з |
1 мкм, |
||
|
|
|
|
|
|
|
|
ρ |
ц |
0, 25 |
5, 452 |
1 |
1,385 мм. |
||
|
|
|
|
|
|
|
Допуск на заготовку (табл. 56)
δ3 Нед. Иш Ку.с. = 3500 + 1900 + 50 = 5450 мкм = 5,45 мм.
41
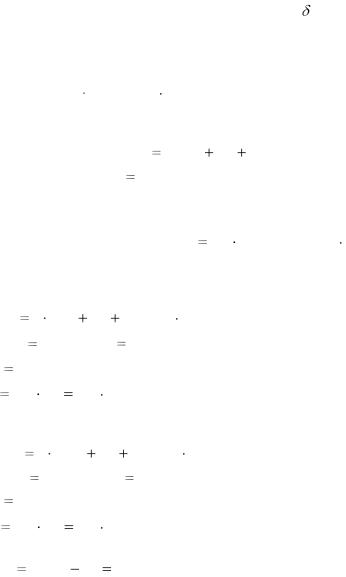
Суммарные значения расчетных допусков |
3 |
можно округ- |
|
|
лять с точностью до 0,1 мм для 1 и 2 групп точности и до 1,0 мм для 3 группы точности штампованных заготовок [1, с.85].
Н ед. = 3500 мкм, Иш = 1900 мкм (табл. 56).
Кус. =1(мкм/мм) DД (мм) = 1 50 = 50 мкм (табл. 56).
7.5.Припуск под чистовое обтачивание после чернового обтачивания, мкм, (табл. 65)
2Z в.min 2(Rza2 Ta2 ρa2 ) ,
2Z в.min 2(50 + 50 + 163) = 526 мкм,
где Rza 2 = 50 мкм, Ta 2 = 50 мкм, (табл. 60), т.к. обрабатывается после чернового обтачивания наружная поверхность вала ступенчатого.
Ку1 = 0,06 (табл. 58). ρa 2 Ку1 ρa1 = 0,06 |
2712 = |
=163 мкм, [3, с.181].
7.6.Припуск под черновое шлифование после чистового обтачивания (табл. 65)
2Zв.min 2 (Rz |
Ta3 |
ρa3 ) = 2 (25 + 25 + 108) = 316 мкм, |
|||
|
|
|
a3 |
|
|
где Rza 3 |
25 мкм, Ta3 |
25 мкм, (табл. 60); |
|||
Ку2 |
0,04 , (табл. 58). |
|
|||
ρa 3 |
Ку 2 |
ρa1 |
0,04 2712 = 108 мкм. |
||
|
7.7. Припуск под чистовое шлифование после чернового |
||||
шлифования (табл. 65) |
|
||||
2 Zв.min |
2 (R za 4 |
Ta 4 |
ρa 4 ) = 2 (10 + 20 + 54) = 168 мкм, |
||
где Rza 4 |
10 мкм; Ta 4 |
20 мкм, (табл. 60); |
|||
Ку3 |
0,02 (табл. 58). |
|
|||
ρa 4 |
Ку3 |
ρa1 |
0,02 2712 = 54 мкм. |
||
|
7.8. Наименьший предельный размер детали |
||||
DД.min |
DД.max |
δД |
50000 – 25 = 49975 мкм. |
||
|
7.9. Верхнее отклонение (плюс) [1, с. 83] |
42
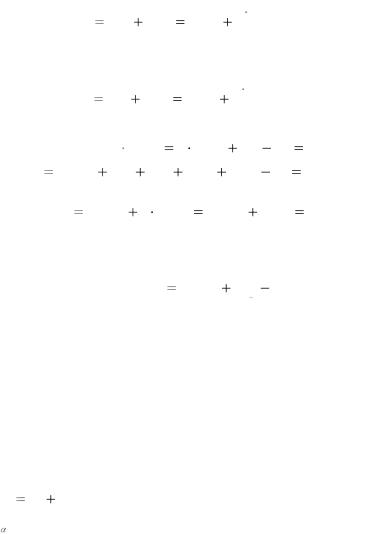
В |
Н |
|
К |
ус. |
3500 |
1 50 |
=3525 мкм. |
ед |
|
|
|
||||
|
|
|
|||||
o |
|
2 |
|
2 |
|
||
|
|
|
|
|
7.10. Нижнее отклонение (минус) [1, с. 84]
Н0 |
Иш |
Кус. |
1900 |
1 50 |
= 1925 мкм. |
|
2 |
2 |
|||||
|
|
|
|
7.11. Общий номинальный припуск на заготовку [1, с. 64]
2 Zо.ном 2 Zo.min Ho δД
( 6404 526 316 168 ) 1925 25 9314 мкм. 7.12. Номинальный диаметр заготовки [1, с. 94]
Dз.ном. DД.ном. 2 Zо.ном 50000 9314 59314 мкм.
7.13. Выполненные расчеты сводятся в табл. 44 (А), для которой производится проверка правильности расчетов по всем технологическим операциям по формуле [1, c. 64]:
2Zi.max |
2Zi.min |
δD |
δD , |
|
|
i 1 |
i |
Например, для последней операции (шлифование чистовое) проверка: 193 мкм = 168 мкм + 50 мкм - 25 мкм.
8. МЕТОДИКА РАСЧЕТА ОБЩЕГО И ОПЕРАЦИОННЫХ ПРИПУСКОВ НА ОБРАБОТКУ ОТВЕРСТИЯ ТЕЛА ВРАЩЕНИЯ
8.1. Исходные данные: деталь - обойма (табл. 43, рис. 13) общей длиной L = 200 мм. Диаметр фланца Dфл. = 100 мм, высота
фланца Нфл. =120 мм. Материал детали - сталь 45. Обработке подле-
жит |
цилиндрическое |
отверстие |
обоймы |
до |
диаметра |
DД |
50 0,050 мм и |
среднего |
арифметического |
отклонения |
R=1,25 мкм. Тип производства - серийный.
8.2.Заготовка - штамповка на ГКМ выбрана по табл. 33, группа точности - 2. Масса заготовки 2 кг. Экономическое обоснование выбора заготовки производится по методике, изложенной в п.
2.4.
43
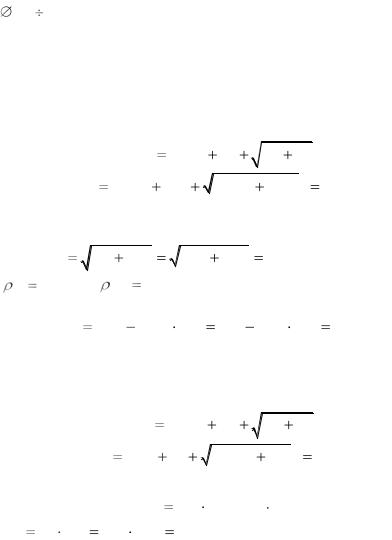
8.3. Технологический маршрут обработки поверхности 50 0,050 мм назначается по табл. 68 и состоит из зенкерования чернового и получистого и развертывания чернового и чистового. Набор инструментов и их диаметры для обработки отверстий приведены в тaбл. 69, 70. Обработка отверстия производится на токарноревольверном станке при одном закреплении (без переустановки) в
3-х кулачковом самоцентрирующем патроне с пневмоприводом.
8.4. Припуск под черновое зенкерование после штамповки
(табл.65)
|
|
|
|
|
2Z |
в.min |
2(R |
|
|
T |
ρ2 |
ε2 ), |
||||||
|
|
|
|
|
|
|
|
z |
a |
|
a |
a |
|
в |
|
|||
|
|
|
|
|
|
|
|
|
|
|
|
1 |
1 |
2 |
|
|||
|
|
|
|
|
|
|
|
|
|
|
|
1 |
|
|
|
|
|
|
|
|
|
|
|
|
|
|
|
|
|
|
|
|
|||||
|
2Z |
в.min |
2(160 200 |
|
35902 |
2102 ) |
7912 мкм, |
|||||||||||
|
|
|
|
|
|
|
|
|
|
|
|
|
|
|
|
|||
где Rza =160 мкм, Ta |
=200 мкм, табл. 57, масса 2 кг, после пескост- |
|||||||||||||||||
|
1 |
|
|
|
|
|
1 |
|
|
|
|
|
|
|
|
|
|
|
руйной обработки. |
|
|
|
|
|
|
|
|
|
|
|
|
|
|||||
|
|
|
|
|
|
|
|
|
|
|
||||||||
|
ρ |
|
|
ρ2 |
ε2 |
0,82 |
3,52 |
3,59 мм = 3590 мкм, |
||||||||||
|
а |
|
|
|
см |
|
эксц |
|
|
|
|
|
|
|
|
|
||
|
1 |
|
|
|
|
|
|
|
|
|
|
|
|
|
|
|
|
|
см |
0,8 мм; |
|
эксц |
|
3,5 мм (табл. 59) длина поковки 200 мм, тип |
|||||||||||||
|
|
|
|
|
|
|
|
|
|
|
|
|
|
|
|
|||
производства – серийный. |
|
|
|
|
|
|
|
|
|
|||||||||
|
εв |
|
εтабл |
|
|
(εтабл |
0,3) |
300 |
(300 0,3) |
210 мкм, |
||||||||
|
|
2 |
|
|
|
|
|
|
|
|
|
|
|
|
|
|
|
|
так как патрон с пневмоприводом снижает погрешность установки на 20-40 % (табл. 63).
8.5. Припуск под получистовое зенкерование после чернового зенкерования (табл. 65)
|
|
|
|
2Z |
в.min |
2(R |
|
T |
ρ2 |
ε2 |
) , |
|
|
|
|
|
|
za |
|
a |
a |
в |
|
||
|
|
|
|
|
|
|
2 |
2 |
2 |
3 |
|
|
|
|
|
|
|
|
|
|
|
|
|
||
|
|
2Z |
в.min |
2(50 |
50 |
179,52 |
102 |
) |
560 мкм, |
|||
|
|
|
|
|
|
|
|
|
|
|
|
|
где Rza |
=50 мкм, Ta |
|
=50 мкм, табл. 55, |
|
|
|
||||||
|
2 |
|
|
|
2 |
|
|
|
|
|
|
|
Ку1 = 0,05 (табл. 58); |
ρa |
Ку1 |
ρa = 0,05 3950 = 179,5 мкм; |
|||||||||
|
|
|
|
|
|
2 |
|
1 |
|
|
|
|
εв |
εв |
Ку1 |
210 0,05 |
10 мкм (так как нет переустановки заго- |
||||||||
4 |
2 |
|
|
|
|
|
|
|
|
|
|
|
товки).
8.6. Припуск под черновое развертывание после получистового зенкерования (табл. 65). Черновая развертка жестко закреплена
44

|
|
|
|
|
2Z |
в.min |
2(R |
T |
|
ρ2 |
ε2 ), |
|||||||
|
|
|
|
|
|
|
za |
|
a |
|
a |
в |
||||||
|
|
|
|
|
|
|
|
|
3 |
3 |
3 |
|
4 |
|
||||
|
|
|
|
|
|
|
|
|
|
|
|
|
|
|
|
|||
|
|
|
2Zв.min |
|
2(30 |
40 |
182 |
12 ) |
176 мкм, |
|||||||||
где Rza |
|
=30 мкм, Ta |
=40 мкм, табл. 55, |
|
|
|
|
|
|
|||||||||
|
|
3 |
|
|
|
3 |
|
|
|
|
|
|
|
|
|
|
|
|
Ку2 = 0,005 (табл. 58); |
|
|
|
|
|
|
|
|
|
|
|
|||||||
ρa |
К |
у2 ρa |
= 0,005 3590 =18 мкм; |
|
|
|
|
|
|
|||||||||
3 |
|
|
1 |
|
|
|
|
|
|
|
|
|
|
|
|
|
|
|
εв |
εв |
|
Ку2 |
|
210 0,005 |
1 мкм (так как нет переустановки заго- |
||||||||||||
4 |
2 |
|
|
|
|
|
|
|
|
|
|
|
|
|
|
|
|
|
товки). |
|
|
|
|
|
|
|
|
|
|
|
|
|
|
|
|
|
|
|
8.7. Припуск под чистовое развертывание после чернового |
|||||||||||||||||
развертывания (табл. 65).Чистовая развертка жестко закреплена |
||||||||||||||||||
|
|
|
|
|
|
|
|
|
|
|
|
|
|
|
|
|||
|
|
|
|
|
2Z |
в.min |
2(R |
T |
|
ρ2 |
ε2 ) , |
|||||||
|
|
|
|
|
|
|
za |
|
a |
|
a |
в |
||||||
|
|
|
|
|
|
|
|
|
4 |
4 |
4 |
|
5 |
|
||||
|
|
|
|
|
|
|
|
|
|
|
|
|
||||||
|
|
|
2Z |
в.min |
|
2(10 |
20 |
72 |
0,52 ) |
74 мкм; |
||||||||
|
|
|
|
|
|
|
|
|
|
|
|
|
|
|
|
|
|
|
где Rza4 |
= 10 мкм, Ta4 |
= 20 мкм (табл. 55), |
|
|
||||||||||||||
Ку3 = 0,002 (табл. 58); |
|
|
|
|
|
|
|
|
|
|
|
|||||||
ρa |
К |
у3 ρa |
= 0,002 3590=7 мкм; |
|
|
|
|
|
|
|||||||||
4 |
|
|
1 |
|
|
|
|
|
|
|
|
|
|
|
|
|
|
|
εв |
εв |
|
Ку3 |
|
210 0,002 |
0,5 мкм (так как нет переустановки за- |
||||||||||||
5 |
2 |
|
|
|
|
|
|
|
|
|
|
|
|
|
|
|
|
|
готовки). |
|
|
|
|
|
|
|
|
|
|
|
|
|
|
|
|||
|
8.8. Допуск на заготовку [1, с. 83] |
|
|
|||||||||||||||
|
|
|
δ3 |
Нед. Иш |
Ку.с. = 1400 + 600 + 50 = 2050 мкм, |
|||||||||||||
где Н ед. |
= 1400 мкм, Иш |
= 600 мкм, табл. 56, |
|
|
Кус. = 1(мкм/мм) DД (мм) = 1 50 = 50 мкм, табл. 56.
8.9.Нижнее отклонение (минус) [1, с. 84]
Н0 |
= Иш |
+ |
Кус. |
= 1400 + |
1 мкм/мм |
50 мм |
=1425 мкм = 1,425 мм. |
||||||
2 |
2 |
|
|
||||||||||
|
|
|
|
|
|
|
|
|
|
|
|
||
|
8.10. Верхнее отклонение (плюс) [1, с. 83] |
|
|||||||||||
В = Н |
|
+ |
Кус. |
|
= 600 + |
1 |
мкм/мм |
50 мм |
= 625 |
мкм = 0,625 мм. |
|||
ед |
|
|
|
|
|
|
|
||||||
0 |
|
|
2 |
|
|
|
|
2 |
|
|
|
|
|
|
|
|
|
|
|
|
|
|
|
|
|
45
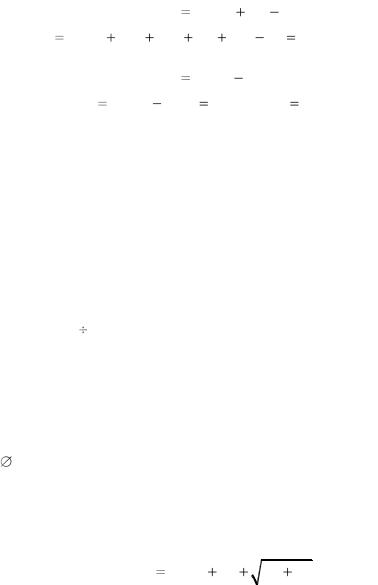
8.11. Общий номинальный припуск на заготовку [1, с. 64].
|
2Zо.ном |
2Z0.min |
H0 |
δД , |
||
2Zо.ном (7912 |
560 |
176 |
74) 625 |
50 |
9297 мкм = 9,297 мм |
|
8.12. Номинальный диаметр заготовки [1, c. 94] |
||||||
|
Dз.ном |
DД.ном |
2Zо.ном. , |
|
||
Dз.ном |
50000 |
9297 40703 мкм |
40, 703 мм . |
8.13. Выполненные расчеты сводятся в табл. 44(Б), под которой проводится проверка правильности расчетов по всем технологическим переходам по формуле, приведенной в п. 7.13. Например, для последнего перехода (чистовое развертывание): 194 мкм = 74 мкм + 170 мкм - 50 мкм.
9. МЕТОДИКА РАСЧЕТА ОБЩЕГО И ОПЕРАЦИОННЫХ ПРИПУСКОВ НА ОБРАБОТКУ ЦИЛИНДРИЧЕСКОГО ОТВЕРСТИЯ КОРПУСА
9.1. Исходные данные: деталь - корпус (табл. 43, рис. 15). Материал детали – СЧ18. Обработке подлежит отверстие до диамет-
ра DД = 60 0,06 мм и среднего арифметического отклонения про-
филя Ra =1,25 мкм. Тип производства - серийный.
9.2.Заготовка - отливка в земляные формы 2 класса точности (табл. 41), массой 4 кг, выбрана по табл. 32. Экономическое обоснование выбора заготовки производится по методике, изложенной в п.
2.3.
9.3.Технологический маршрут обработки отверстия
60+0,06 мм назначается по табл. 68 и состоит из растачивания чернового и чистового, выполняемых при одной установке корпуса на плоскость основания размером 120х120 мм и два отверстия 10 Н7, изготовленных предварительно.
9.4. Припуск под черновое растачивание после отливки (табл.
65)
2Z |
в.min |
2(R |
T |
ρ2 |
ε2 |
) , |
|
za |
a |
a |
в |
|
|
|
|
1 |
1 |
1 |
2 |
|
46
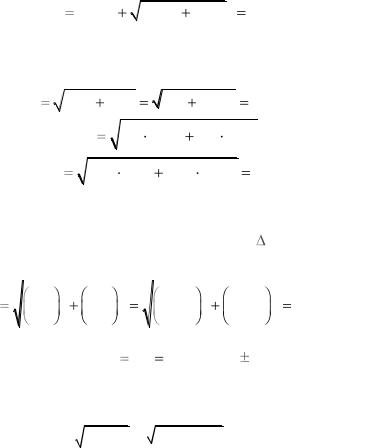
|
2Z |
в.min |
2(800 11352 |
126 2 ) 3384 мкм, |
|
|
|
|
|
где Rza |
+ Ta = 800 мкм (табл. 52), так как серийный тип производст- |
|||
1 |
1 |
|
|
|
ва, размер отливки до 1250 мм. По табл. 46 пространственное отклонение
ρa |
ρ2 |
кор. ρ2 |
см. |
942 |
11312 |
1135 мкм, |
||
|
1 |
|
|
|
|
|
|
|
|
|
|
|
|
|
|
|
|
|
ρкор. |
|
к DД |
2 |
к LД |
2 , |
|
|
ρкор. |
0, 7 60 2 |
|
0, 7 120 2 |
94мкм, |
||||||||||||||
где DД = 60 мм, длина отверстия LД |
= 120 мм. |
|
|
|
|
|||||||||||||||
Величина коробления отверстия корпуса учитывается как в |
||||||||||||||||||||
диаметральном, |
так |
и |
осевом |
его |
сечении, |
|
к |
|
= 0,7 мкм/мм, |
|||||||||||
|
|
|
|
|
|
|
|
|
|
|
|
|
|
|
|
|
|
|
|
|
табл. 50. Смещение ρсм |
[1, с.87]: |
|
|
|
|
|
|
|
|
|
|
|||||||||
|
|
|
|
|
|
|
|
|
|
|
|
|
|
|
|
|
||||
ρсм |
δ55 |
2 |
|
δ60 |
|
2 |
|
|
1600 2 |
1600 |
|
2 |
1131 мкм. |
|||||||
2 |
|
|
|
2 |
|
|
|
|
|
2 |
|
|
|
2 |
|
|
|
|||
|
|
|
|
|
|
|
|
|
|
|
|
|
|
|
||||||
Допуски на размеры 55 и 60 (расстояния от оси отверстия до |
||||||||||||||||||||
плоскостей заготовки): δ55 |
|
δ60 |
|
1600 мкм ( |
0,8 мм), табл. 41, так |
как DД < 120 мм и наибольший габарит корпуса менее 250 мм, се-
рийный тип производства. Погрешность установки εв2 [3, с. 24]
εв2 = εζ2 + ε2з =
382 +1202 = 126 мкм.
Погрешность базирования εσ в данном случае возникает за
счет перекоса заготовки в горизонтальной плоскости при установке ее на штыре приспособления. Перекос при этом происходит из-за наличия зазоров между наибольшим диаметром установочных отверстий и наименьшим диаметром штырей [1, с.88].
εζ = LД × tgα = 120×0,00032 = 0,038 мм = 38 мкм.
Угол поворота заготовки на штырях равен отношению наибольшего зазора к расстоянию между базовыми штырями [1, с.88].
47
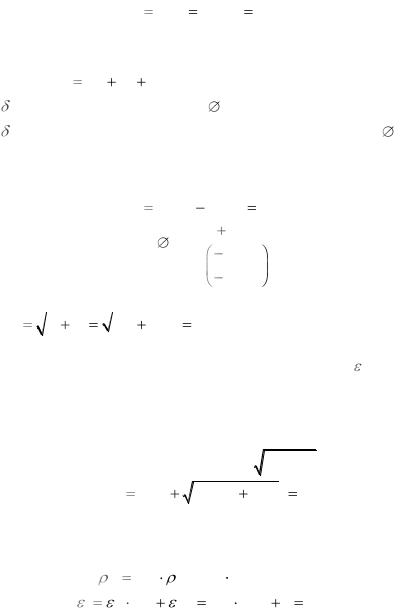
tgα |
Smax |
|
0, 043 |
0, 00032 . |
|
lшт. |
134,5 |
||||
|
|
Наибольший зазор между отверстиями и базовыми штырями определится [1, с. 88]
|
|
|
Smax |
|
δH7 |
|
δf7 |
Smax = 0,015 + 0,013 + 0,015 = 0,043 мм. |
||||||||
H |
|
=0,015 - допуск на отверстие |
10 H 7 , [15, с. 46-47]; |
|
|
|||||||||||
|
|
7 |
|
|
|
|
|
|
|
|
|
|
|
|
|
|
f |
|
= 0,013 – предельное отклонение на диаметр штыря |
10 f7 |
|||||||||||||
|
7 |
|
|
|
|
|
|
|
|
|
|
|
|
|
|
|
[15, с. 48-53]. |
|
|
|
|
|
|
|
|
|
|
||||||
|
|
|
Минимальный зазор между отверстием и диаметром штыря |
|||||||||||||
[15, с. 48-53] |
|
|
|
|
|
|
|
|
|
|
||||||
|
|
|
|
|
|
|
|
Smin |
0,028 |
0,013 0,015 мм, |
|
|
|
|||
|
|
|
|
|
|
|
|
|
10 |
H7 |
0, 015 |
. |
|
|
|
|
|
|
|
|
|
|
|
|
|
f7 |
0, 013 |
|
|
|
|||
|
|
|
|
|
|
|
|
|
|
|
|
|
|
|
||
|
|
|
|
|
|
|
|
|
|
|
0, 027 |
|
|
|
|
|
|
|
|
|
|
|
|
|
|
|
|
|
|
|
|
|
|
|
|
|
Расстояние |
между |
базовыми |
отверстиями |
||||||||||
|
|
|
|
|
|
|
|
|
|
|
|
|
|
|||
l |
|
|
|
l2 |
l2 |
902 |
1002 134,5 мм (размеры l |
и l |
2 |
брать по |
||||||
шт. |
1 |
2 |
|
|
|
|
|
|
|
1 |
|
|
табл. 43, рис. 15.
Погрешность закрепления принимается равной з = 120 мкм
(табл. 61), т.к. применяется приспособление с пневматическим приводом.
9.5. Припуск под чистовое растачивание после чернового растачивания (табл. 65)
2Z |
в.min |
= 2(R |
za |
|
+ T |
|
+ ρ2 |
|
+ ε2 ) , |
||||
|
|
|
|
2 |
a |
2 |
a |
2 |
в |
||||
|
|
|
|
|
|
|
|
|
3 |
||||
|
|
|
|
|
|
|
|
||||||
2Zв.min |
2(50 |
|
56, 752 |
6,32 ) |
214 мкм, |
||||||||
где Rza2 = 50 мкм (табл. 55), Ta2 |
|
= 0 не учитывается для чугуна после |
|||||||||||
первого технологического перехода (табл. 54). |
|
||||||||||||
a |
|
Ку1 |
a = 0,05 1135= 56,75мкм; |
||||||||||
2 |
|
|
|
1 |
|
|
|
|
|
|
|
|
|
3 в |
2 |
Ку1 |
инд. |
|
126 0,05 |
0 |
6,3 мкм; |
48
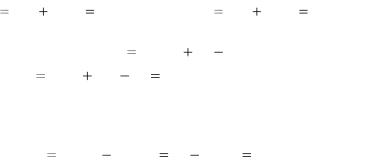
Ку1 = 0,05 (табл. 58).
Погрешность индикации εинд. = 0, т.к. черновое и чистовое
растачивание производится в одной установке [1, с. 88] . 9.6. Общие припуски на заготовку.
2Z0.min |
214 |
3884 |
4098 мкм; 2Z0.max |
354 |
5284 5638 мкм. |
|||
9.7. Общий номинальный припуск [1, с. 64] |
||||||||
|
|
2Zо.ном. |
2Z0.min |
Bз |
BД , |
|
||
|
|
4098 800 |
60 |
4838 мкм = 4,838мм, |
||||
где Вз и |
ВД - |
верхние предельные отклонения (плюс) заготовки и |
||||||
детали. |
|
|
|
|
|
|
|
|
9.8. Номинальный диаметр заготовки |
|
|||||||
|
Dз.ном. |
DД.ном. |
2Zо.ном |
60 |
4,838 |
55,162 мм. |
9.9.Выполненные расчеты сводятся в табл. 44(В), для которой проводится проверка правильности расчетов по всем технологическим переходам по формуле, приведенной в п. 7.13. Например, для последнего технологического перехода (чистовое растачивание):
354 мкм = 214 мкм + 200 мкм – 60 мкм.
10.МЕТОДИКА РАСЧЕТА ОБЩЕГО И ОПЕРАЦИОННЫХ ПРИПУСКОВ НА ОБРАБОТКУ ТОРЦОВОЙ ПОВЕРХНОСТИ
10.1.Исходные данные: деталь - диск (табл. 43, рис. 14) с наружным диаметром D = 160 мм, центральным отверстием d=30 мм и толщиной L = 100-0,1 мм. Материал детали – СЧ18. Необходимо обработать один торец диска до шероховатости обработанной поверх-
ности Ra = 20 мкм, выдерживая размер L = 100-0,1 мм. Тип производства - серийный.
10.2.Заготовка - отливка 2 класса точности табл. 41, массой 4,5 кг, выбрана по табл. 32. Экономическое обоснование заготовки производится по методике, изложенной в п. 2.3.
10.3.Технологический маршрут обработки торца диска назначается по табл. 67 и состоит из чернового и чистового точения при одном закреплении. При обтачивании заготовка базируется предварительно обработанной наружной цилиндрической поверхно-
49