
Технология материалов: лабораторный практикум. Орлов А.С., Рубцова Е.Г
.pdfМинистерство образования и науки Российской Федерации
Федеральное государственное бюджетное образовательное учреждение высшего образования
«Воронежский государственный технический университет»
А.С. Орлов Е.Г. Рубцова А.С. Померанцев
ТЕХНОЛОГИЯ МАТЕРИАЛОВ
Лабораторный практикум
для студентов, обучающихся по направлениям подготовки бакалавров 23.03.02 «Наземные транспортно-технологические комплексы», 23.03.03 «Эксплуатация транспортно-технологических машин и комплексов» ,
по специальности 23.05.01 «Наземные транспортно-технологические средства»
Воронеж 2017
УДК 621.791.69(075) ББК 34.64
О-664
Рецензенты:
П.И. Золотухин, заведующий кафедрой «Оборудование и процессы машиностроительных производств» ФГБОУ ВО
«Липецкий государственный технический университет»; М.П. Смирнов, генеральный директор Российского общества инженеров-строителей
Орлов, А.С.
О-664 Технология материалов: лабораторный практикум для студентов, обучающихся по направлениям подготовки бакалавров 23.03.02 «Наземные транспортно-технологические комплексы», 23.03.03 «Эксплуатация транспортно-технологических машин и комплексов», по специальности 23.05.01 «Наземные транспортнотехнологические средства» / сост.: А.С. Орлов, Е.Г. Рубцова, А.С. Померанцев; ВГТУ. - Воронеж, 2017. – 94 с.
Рассмотрены основные способы обработки материалов: сварка, литье, обработка резанием, с учетом особенностей их применения, достоинств и недостатков. Описаны основные способы контроля изделий, возможные дефекты и причины их возникновения.
Изложена методика подготовки и выполнения лабораторных работ. Даны указания по оформлению работ, форме представления полученных данных и сдаче отчетов по выполненным работам. Приведен список рекомендуемой учебно-методической литературы.
Издание соответствует требованиям Федерального государственного образовательного стандарта высшего образования по дисциплине «Технология конструкционных материалов».
Ил. 45. Табл. 21. Библиогр.: 13 назв.
УДК 621.791.69(075) ББК 34.64
Рекомендовано к изданию учебно-методическим советом ВГТУ
© Орлов А.С., Рубцова Е.Г., Померанцев А.С., 2017 © Оформление. ВГТУ, 2017
ВВЕДЕНИЕ
При конструировании и изготовлении машин и приборов, организации их эксплуатации и ремонта инженер-механик в повседневной работе сталкивается с машиностроительными материалами и их использованием. Для успешного решения многих практических задач необходимы сведения о современных способах получения и обработки материалов, их свойствах и рациональных областях применения. Технология конструкционных материалов является комплексной дисциплиной, в которой рассматриваются основные сведения о способах производства машиностроительных материалов и их обработки с целью получения деталей с заданными свойствами и конфигурацией, пригодных для использования в машинах и конструкциях.
Цель изучения дисциплины – получение студентами необходимой общеинженерной технологической подготовки, знаний, необходимых как при работе на производстве, так и в научно-исследовательских и проектных институтах.
Задачи освоения дисциплины – формирование у будущих специалистов системы знаний о технологии производства, рациональном выборе необходимых материалов, степени точности, качестве поверхности и назначении технических условий деталей и узлов строительных, дорожных машин и подъемнотранспортного оборудования.
Студенты должны знать:
-основные характеристики и принципы выбора конструкционных материалов для изготовления деталей наземных транспортно-технологических систем и комплексов;
-основы технологии заготовительного и металлообрабатывающего производства.
Студенты должны уметь:
-назначить вид сварки, подобрать необходимые сварочные материалы, режимы сварки, обеспечивающие высокую производительность и качество сварных изделий;
-назначить вид механической обработки, подобрать тип инструмента и оборудования, выбрать рациональную технологию обработки конструкционных материалов;
-оценить технологичность конструкции детали, выбрать наиболее экономичный способ изготовления отливки, литейную оснастку, методы заливки для получения качественных отливок.
Студенты должны владеть:
-навыками правильного выбора материалов для изготовления, модернизации, ремонта наземных транспортно-технологических машин и комплексов с учетом их физико-механических свойств, обеспечивающих высокую надежность и долговечность в условиях эксплуатации изделий;
-инженерной терминологией в области технологий изготовления, ремонта и восстановления транспортно-технологических средств.
3
Лабораторная работа № 1
ЛИТЬЕ В МЕТАЛЛИЧЕСКИЕ ФОРМЫ (КОКИЛИ)
1.1.Цель работы
Изучить технологию и сущность способа литья в металлические формы – кокили.
1.2.Оборудование, приборы и материалы
1.Нагревательные электрические печи с температурой нагрева до 9501250оС.
2.Термопары хромель-алюмелевые и хромель-копелевые типов ТХА, ТХК.
3.Потенциометры или другие приборы для контроля, регулирования и записи температуры с точностью + 10-15оС.
4.Набор кокилей.
5.Набор инструмента для плавки, рафинирования и заливки расплава.
6.Электронагреватель для подогрева кокилей.
7.Шихтовые материалы для приготовления сплава АК12.
8.Набор слесарного инструмента.
9.Спецодежда.
1.3.Краткие теоретические сведения
Литье в металлические формы (кокили) получило большое распространение. Этим способом получают более 40 % всех видов отливок из алюминиевых и магниевых сплавов, отливки из чугуна, стали и других сплавов.
Сущность литейного производства состоит в получении отливок – литых металлических изделий путем свободной заливки расплавленного металла или сплава в литейную форму.
Литейная форма – это система элементов, образующих рабочую полость, при заливке которой расплавленным металлом формируется отливка.
Кокиль – металлическая форма многократного использования, которая заполняется расплавом под действием силы тяжести. Кокили изготавливают из чугуна или стали, в некоторых случаях из цветных металлов или их сплавов
Способ литья в кокиль имеет ряд преимуществ перед литьем в песчаные формы: металлическая форма является многоразовой; отливки, полученные в кокиле, имеют большую точность размеров и высокую чистоту поверхности, что дает возможность на 40-50 % снизить припуск на механическую обработку; структура металла отливки получается более мелкозернистой, вследствие чего повышается ее плотность и механические свойства; устраняется необходимость в формовочной смеси; улучшаются технико-экономические показатели производства и его экологическая чистота.
4
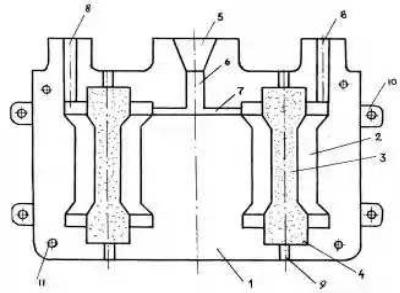
К недостаткам способа относятся высокая трудоемкость изготовления кокилей; большая стоимость изготовления формы; повышенная теплопроводность формы, что может привести к пониженной заполняемости форм расплавленным металлом вследствие быстрой потери его жидкотекучести; возможное образование отбеленного поверхностного слоя в отливках из чугуна, что затрудняет их механическую обработку.
Литье в кокиль ограничено возможностью изготовления крупногабаритных кокилей (до 2000 кг).
Кокиль для простых отливок изготавливают из двух разъемных частей, соответствующих верхней и нижней полуформам (рис. 1.1). Для сложных отливок форму изготавливают из нескольких разъемных частей. Наиболее распространены кокили с вертикальным разъемом, с горизонтальным разъемом и неразъемные (вытряхные). Неразъемные кокили применяют для отливок, имеющих внешние очертания без выступающих частей.
Полуформы центрируют штифтами 11. Расплав заливают через литнико- во-питательную систему (ЛПС) – систему каналов и устройств для подвода в определенном режиме жидкого металла в полость формы (5, 6, 7), а питание массивных узлов осуществляется из прибыли (в данной схеме прибыль совмещена с литниковой чашей). Кокили раскрываются с помощью ручек или специальных гидравлических, механических приводов. Поворот полуформ вокруг оси осуществляется с помощью кронштейна. Каналы 9 служат для вывода воздуха из полости кокиля. Внутренние полости в отливках выполняют металлическими и песчаными стержнями 3.
Рис. 1.1. Эскиз сечения собранной металлической формы
1 – корпус кокиля; 2 – литейная форма; 3 – |
стержень; 4 – |
знак стержня; |
|
5 – литниковая чаша; 6 – |
стояк; 7 – |
питатель; 8 – |
выпор; |
9 - вентиляционный канал; 10 – |
прилив; 11 – центрирующий штифт |
||
|
5 |
|
|
Для увеличения срока службы и снижения величины усадочных напряжений в отливках кокили перед заливкой различными сплавами нагревают до 250-400 ºС. Перед этим на рабочие поверхности металлической формы наносят слой огнеупорного покрытия – облицовки или краски. Огнеупорное покрытие резко уменьшает теплоотвод и облегчает удаление отливки из формы. Этим широко пользуются для замедления кристаллизации металла в прибылях и узлах, оформляющих тонкие ребра. Составы облицовок и красок зависят от типа заливаемого металла: для алюминиевых сплавов используют мел и графит, для сталей и чугунов – асбест, маршалит, пылевидный кварц, в качестве связующих веществ используют жидкое стекло и воду. Толщина слоя облицовки зависит от требуемой скорости охлаждения отливок: чем толще слой огнеупорного покрытия, тем медленнее охлаждаются отливки. На стенки кокиля, оформляющие литниковые каналы и прибыли, наносят более толстый слой краски (до 1 мм), чтобы уменьшить интенсивность охлаждения расплава. Краску наносят пульверизатором.
Подвод металла в кокили осуществляется сверху, снизу (сифоном) или сбоку через щелевые питатели. Заливку металла осуществляют разливочными ковшами или автоматическими заливочными устройствами.
Масса расплавленного металла (М) для заливки в кокиль определяется по формуле:
M = ρ (VO + VЛ + VВ + VУ ) ,
где ρ – плотность металла, кг/м3; VO – объем отливки, м3;
VЛ – объем литниково-питательной системы, м3; VВ – объем выпора (прибыли), м3;
VУ – объем припуска на литейную усадку, м3.
Припуски на литейную усадку обычно определяют в зависимости от вида сплава, массы и размеров отливки. При разработке технологии изготовления отливок можно использовать приведенные ниже значения линейной усадки сплавов по спиральной пробе, %:
Серый чугун – 1,3-0,6 Углеродистые стали – 2,35-1,79 Легированные стали – 3,8-1,8
Бронзы – 2,4-1,3 Латуни – 2,4 -1,5
Алюминиевые сплавы – 1,7-1,3.
Отливку извлекают из кокиля еще горячей при температуре, равной 0,6-0,8 температуры солидуса сплава, и охлаждают на воздухе или в специальных камерах.
К числу финишных операций относят выбивку, очистку, обрубку, зачистку отливок, их термическую обработку, контроль и исправление дефектов.
6
1.4.Порядок выполнения работы
1.Тщательно ознакомиться с устройством кокилей. Особое внимание обратить на механизм разъема формы, устройство вентиляционных каналов.
2.Произвести контрольную сборку и разборку кокилей в целях установления правильности и надежности взаимодействия их частей.
3.Подогреть кокили электронагревателем до температуры 130 ºС.
4.Расплавить 3 кг сплава АК12, довести температуру до 750 ºС.
5.Изготовить отливки литьем в кокиль.
6.Извлечь отливки из кокилей, охладить их до нормальной температуры.
7.Оценить качество поверхности отливки.
1.5.Содержание отчета
1.Название и цель работы.
2.Краткое описание сущности литья в кокиль.
3.Изобразить эскиз сечения собранной металлической формы (кокиля).
4.Краткое описание качества поверхностей отливок.
5.Сделать вывод.
Контрольные вопросы
1.В чем преимущества литья по сравнению с другими методами получения заготовок деталей машин?
2.В чем сущность способа литья в кокиль?
3.Как температуры подогрева кокиля и заливаемого в него металла влияют на структуру и свойства отливок?
4.Из каких материалов изготавливаются кокили?
5.В чем состоят преимущества литья в кокиль?
6.Каким методом литья можно получить отливку станины станка длиной 10 м и массой 10 тонн?
7.Какой метод литья обеспечивает получение отливок наиболее сложной формы?
8.Из каких соображений металлическую форму подогревают перед заливкой?
Литература
[1, 2, 3]
7
Лабораторная работа № 2
РУЧНАЯ ЭЛЕКТРОДУГОВАЯ СВАРКА
2.1. Цели работы
Ознакомление с сущностью и технологическими особенностями процесса ручной дуговой сварки покрытыми электродами и оборудованием для ее осуществления; определение технико-экономических показателей ручной электродуговой сварки.
2.2. Оборудование, приборы и материалы
Пост для ручной электродуговой сварки (стол, вытяжка, источник питания, токопроводящие провода, эдектрододержатель, щиток, молоток, зубило, металлическая щетка).
Контрольно-измерительные приборы (амперметр, вольтметр, секундомер, весы с разновесами, линейка измерительная 0-500 мм с ценой деления 1 мм), пластины для наплавки, электроды с различными типами обмазки.
2.3. Краткие теоретические сведения
Ручная электродуговая сварка (РДС) покрытыми электродами - один из способов сварки плавлением. Источником нагрева при этом способе служит электрическая дуга, возбуждаемая между штучным электродом и свариваемыми деталями.
Схема процесса ручной дуговой сварки представлена на рис.2.1. Электрод закрепляется в электрододержателе. Под действием тепла дуги происходит плавление электродного стержня и кромок свариваемых деталей. Расплавленный металл кромок изделия и капли жидкого металла, образующиеся при плавлении стержня, сливаются в общую сварочную ванну. Вместе со стержнем плавится и покрытие электрода, образуя защитную атмосферу вокруг дуги и жидкий шлак на поверхности расплавленного металла и каплях. По мере перемещения дуги вдоль свариваемых кромок происходит кристаллизация жидкого металла сварочной ванны и формирование сварного шва. Жидкий шлак, затвердевая, образует на поверхности шва шлаковую корку.
Электрическая дуга является мощным разрядом электричества в атмосфере ионизированных газов, образующихся при плавлении покрытий электродов и флюсов. Процесс зажигания дуги при сварке можно разделить на 3 этапа: короткое замыкание электрода на деталь с целью разогрева торца электрода и участка детали, отвод электрода на расстояние 3-6 мм от детали для создания эмиссии (испускание) электронов с разогретого торца и ионизации молекул газов и паров металлов при столкновении с быстролетящими электронами; возникновение дугового разряда, т.е. устойчивой электрической дуги между дета-
8
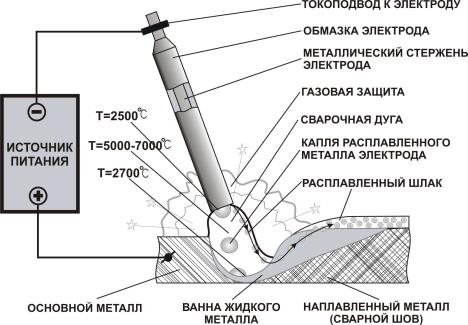
лью и электродом. Температура столба дуги достигает 7000 °С, а катодного и анодного пятен – в пределах 2000-3000 °С.
Рис. 2.1. Схема процесса ручной электродуговой сварки
Покрытые электроды, используемые при ручной дуговой сварке, представляют собой металлический стержень, покрытый обмазкой (рис 2.1). Электроды изготовляются обычно диаметром от 2 до 6 мм (диаметром электрода считается диаметр металлического стержня). Толщина покрытия составляет 0,5 - 2 мм на сторону. Покрытие электрода обеспечивает: легкое зажигание и устойчивое горение дуги; защиту расплавленного металла от взаимодействия с кислородом и азотом воздушной атмосферы; получение металла шва требуемого химического состава; равномерное расплавление стержня и покрытия электрода при небольших потерях электродного металла на угар и разбрызгивание; легкую отделяемость шлаковой корки от поверхности шва.
Один из концов стержня освобожден от покрытия для его зажатия в электрододержателе с обеспечением электрического контакта. Второй конец только слегка очищен для облегчения зажигания дуги посредством контакта с изделием.
В состав покрытия входят следующие компоненты: стабилизирующие, газообразующие, шлакообразующие, раскисляющие, легирующие, связующие и наполнители.
Стабилизирующие вещества (соединения калия и натрия) облегчают ионизацию в дуге и увеличивают устойчивость её горения. Газообразующие: ве- щества (карбонаты), целлюлоза при нагреве разлагаются и образуют газовую атмосферу, (преимущественно СО2), что препятствует проникновению кисло-
9
рода и азота воздуха в дугу и сварочную ванну. Шлакообразующие состав- ляющие (полевой шпат, марганцевая руда и др.) при расплавлении образуют жидкий шлак на поверхности расплавленного металла. Шлак защищает расплавленный металл ванны и капель присадочной проволоки, а также является средой, через которую проводится раскисление и легирование металла шва. Раскисляющие составляющие (ферросилиций FeSi, ферромарганец FeMn ), изза их большего сродства к кислороду, чем у железа, обеспечивают восстановление окислов железа, находящегося в сварочной ванне. Легирующие состав- ляющие (феррохром, ферромолибден и др.) служат для получения требуемого химического состава и механических свойств металла шва. Связующие вещест- ва (жидкое натриевое стекло) связывают порошкообразные составляющие покрытия, соединяют его с металлическим стержнем. Наполнители (преимущественно железный порошок) обеспечивают повышение производительности плавления электродов.
Все электроды для ручной сварки можно разделить на следующие группы по ГОСТ 9466-75:
«В» - для сварки легированных конструкционных сталей повышенной и высокой прочности с пределом прочности свыше 600 МПа – 49 типов;
«Л» - для сварки углеродистых и низколегированных сталей с пределом прочности до 500 МПа, когда к металлу сварных швов предъявляют повышенные требования по пластичности и ударной вязкости – 5 типов;
«Т» - для сварки легированных теплоустойчивых сталей с пределом прочности от 500 до 600 МПа – 9 типов;
«У» - для сварки углеродистых и легированных сталей с пределом прочности до 500 МПа;
«Н» - для наплавки поверхностных слоев с особыми свойствами – 44 типа.
Электроды обозначаются буквой «Э», затем следуют цифры, указы- вающие прочностные характеристики наплавленного металла. Например, обо-
значение Э42 указывает, что электроды этого типа обеспечивают минимальный предел прочности 420 МПа. Если в обозначении после цифр стоит буква «А», то это означает, что этот тип электрода обеспечивает более высокие пластические свойства наплавленного металла. Электроды различают по маркам, которые указаны в их паспорте. Одному и тому же типу электродов может соответствовать несколько марок. К примеру, электродам типа Э46 соответствуют марки АНО-4, МР-3 и др.; электродам типа Э42 соответствуют марки УОНИ-
13/45 и СМ-11.
Электрододержатель – приспособление для закрепления электрода и подвода к нему тока. Среди всего многообразия применяемых электрододержателей наиболее безопасными являются пружинные, изготавливаемые по требованиям и классификации ГОСТ 14651-78Е. Эти электрододержатели выдерживают без ремонта 8-10 тыс. зажимов. Время замены электрода не превышает 3-4 с.
10