
3631
.pdfУглы в плане:
Главным углом в плане ϕ называют угол между проекцией главной режущей кромки на основную плоскость и направлением продольного перемещения резца (движение подачи Ds). Вспомогательным углом в плане ϕ1 называют угол между проекцией вспомогательной режущей кромки на основную плоскость и направлением, обратным движению продольного перемещения резца.
Углы в главной секущей плоскости:
Главным передним углом γ называют угол между передней поверхностью резца и плоскостью, проходящий через главную режущую кромку перпендикулярно к плоскости резания. Главным задним углом α называют угол, образованный главной задней поверхностью резца и плоскостью резания. Углом заострения β называют угол между передней и главной задней поверхностями резца.
Углом наклона главной режущей кромки λ называется угол между главной режущей кромкой резца и плоскостью, проведенной через вершину параллельно основной плоскости. В том случае, когда вершина резца является наивысшей точкой главной режущей кромки, угол λ считается отрицательным. Если вершина резца является низшей точкой главной режущей кромки, λ - положительны. Если же главная режущая кромка параллельна основной плоскости, то λ=0.
Влияние углов режущей части на процесс резания
Главный передний угол оказывает большое влияние на процесс резания. С увеличением угла уменьшаются деформации срезаемого слоя, улучшаются условия схода стружки; уменьшаются силы резания; повышается качество обработки. Однако чрезмерное увеличение угла приводит: к уменьшению прочности режущего лезвия; увеличению износа режущего лезвия; вследствие выкрашивания, к ухудшению теплоотвода от инструмента.
Наличие главного заднего угла уменьшает трение между обработанной и главной задней поверхностями, что увеличивает стойкость инструмента. Однако чрезмерное увеличение угла приводит к уменьшению прочности режущего лезвия.
Главный угол в плане определяет параметры переходного конуса между обрабатываемыми цилиндрами и угол фасок, т.е. определяется конструктором. В основном, угол влияет на шероховатость обработанной поверхности. С уменьшением угла уменьшаются: шероховатость, сила и температура резания, приходящиеся на единицу длины режущей кромки, но резко увеличивается сила резания в направлении перпендикулярном оси заготовки.
Вспомогательный угол в плане влияет на шероховатость обработанной поверхности (с уменьшением угла она уменьшается).
71
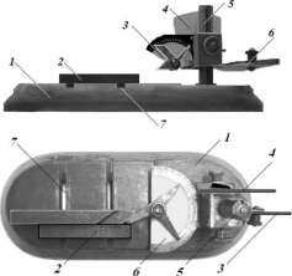
С увеличением угла наклона режущей кромки ухудшается качество обработанной поверхности. Но чаще всего, выбор величины и знака угла определяется направлением схода стружки. При отрицательных углах, стружка сходит по направлению движения подачи, что безопасно при работе на универсальных станках. При положительных углах, стружка сходит по направлению против движения подачи, что безопасно при работе на станках с автоматическим и полуавтоматическим циклом. Положительные углы применяются при обработке отверстий, для того, что бы стружка выходила из отверстия.
Техника измерения углов с помощью универсального угломера
Универсальный угломер (рис. 9.8) состоит из основания 7, в пазах 7 которого устанавливается и может перемещаться направляющая линейка 2. На основании жестко установлена стойка 5, по которой вращаются и могут быть закреплены в требуемое положение три угломера для измерения различных углов.
Для измерения углов, лежащих в главной секущей плоскости угломер (рис. 9.9) оснащен неподвижной шкалой 3 и шаблоном 4 со стрелкой, шаблон имеет две взаимно-перпендикулярные рабочие поверхности - материальные грани, предназначенные для измерения главного переднего γ (грань 5) и главного заднего угла α (грань 6). Резец 9 устанавливается на основании 11 и подводится к шаблону 4 в положение, при котором плоскость шаблона перпендикулярна главной режущей кромке 11.
Рис. 9.8. Универсальный угломер: 1 - основание; 2 - направляющая линейка; 3 - блок измерения углов (угломер) в главной секущей плоскости;
4 - блок измерения углов в плане; 5 -стойка; 6 - блок измерения угла наклона главной режущей кромки; 7 - пазы
72
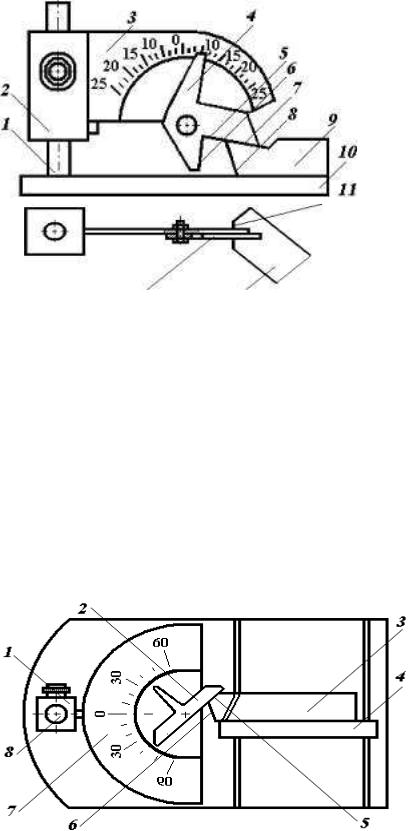
Рис. 9.9. Схема измерения углов в главной секущей плоскости:
1 - стойка; 2 - корпус угломера; 3 - шкала; 4 - шаблон; 5 -грань для измерения угла γ; 6 - грань для измерения угла α; 7 - передняя поверхность; 8 - задняя поверхность; 9 - резец; 10 - основание; 11 - главная режущая кромка
Далее шаблон мерительной гранью 5 совмещается с передней поверхностью резца или мерительной гранью 6 с главной задней поверхностью резца. При этом соответствующий угол поворота отмечен стрелкой шаблона в различных направлениях от нулевого положения шкалы 3, на которой регистрируются значения углов.
Для измерения углов в плане угломер (рис. 9.10) оснащен неподвижной шкалой 7 и шаблоном 2 со стрелкой.
Рис. 9.10. Схема измерения угла наклона главной режущей кромки: 1 - основание; 2 - шкала; 3 -стойка; 4 - шаблон; 5 - главная режущая
кромка; 6 - грань шаблона; 7 - резец
73
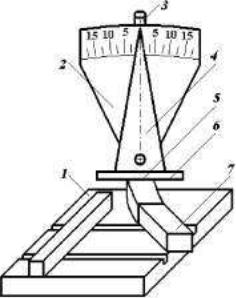
При установке корпуса угломера 1 на шпонку, он может перемещаться в вертикальном направлении по стойке 8, а его рабочая грань 5 будет перпендикулярна направляющей линейке 4. Обязательным условием, обеспечивающим точность измерений главного и вспомогательного углов в плане, является установка резца по направляющей линейке боковой стороной.
Рабочую грань шаблона, расположенного в горизонтальной плоскости, совмещают с главной или вспомогательной режущей кромкой резца путем вращения вокруг стойки, после чего по показаниям стрелки шаблона регистрируют значение углов по шкале 7.
Для измерения угла наклона главной режущей кромки угломер (рис. 9.11)
оснащен неподвижной шкалой 2 и шаблоном 4 со стрелкой.
Резец устанавливается на основание 1 таким образом, чтобы главная режущая кромка 5 находилась в плоскости шаблона. Поворотом шаблона вокруг оси совмещают грань шаблона 6 с главной режущей кромкой. Стрелка шаблона укажет угол наклона главной режущей кромки в градусах на шкале.
Рис. 9.11. Схема измерения углов в плане:
1 - корпус угломера; 2 - шаблон; 3 - резец; 4 - направляющая линейка; 5 - грань шаблона; 6 - главная режущая кромка; 7 - шкала; 8 -стойка
9.4.Порядок выполнения работы
1.Произвести замер углов лезвий трех различных по геометрии резцов. Измерение каждого угла повторить 3 раза и определить среднеарифметическое для записи в отчет.
2.На основании результатов измерений сделать выводы о возможном применении резцов. Данные занести в таблицу 9.2.
74
|
|
|
|
|
|
|
Таблица 9.2 |
|
|
|
Результаты замеров |
|
|
||
|
|
|
|
|
|
|
|
Номер |
|
|
|
Угол, град |
|
|
Назначение |
резца |
α |
γ |
|
ϕ |
ϕ1 |
λ |
резца |
|
|
|
|
|
|
|
|
9.5. Содержание отчёта
1.Название, цель работы.
2.Описать разновидности режущих инструментов.
3.Указать основные инструментальные материалы.
4.Описать технику измерения углов с помощью универсального угломера.
5.Заполнить таблицу 9.1.
6.Сделать выводы по работе.
9.6. Вопросы для самоконтроля
1.Какие поверхности можно выделить на заготовке в процессе резания?
2.Какая плоскость называется основной?
3.Какую плоскость называют плоскостью резания?
4.Какой угол называют передним углом γ?
5.Какой угол называют главным задним углом α?
6.Какой угол называют главным углом в плане ϕ?
7.Какой угол называют углом наклона главной режущей кромки резцаλ?
8.Как измеряют углы, лежащие в главной секущей плоскости?
9.Как измеряют угол наклона главной режущей кромки резца?
10.Как измеряют углы резца в плане?
11.Из каких материалов изготавливают лезвия резцов?
Литература
[1, 2, 3, 11, 12]
Лабораторная работа № 10
ОБРАБОТКА ЦИЛИНДРИЧЕСКИХ ПОВЕРХНОСТЕЙ
10.1. Цели работы
Ознакомление с методами лезвийной обработки цилиндрических поверхностей, с устройством и компоновкой универсальных станков токарной и сверлильной группы.
75
10.2. Оборудование и материалы
Токарно-винторезный станок 1А62, 1К62, 1616. Вертикально-сверлиль- ный станок модели 2А125. Заготовки из стали 45 для точения и сверления. Сверла, зенкеры, развертки, резцы. Приспособления для закрепления заготовок.
10.3. Краткие теоретические сведения
Точение
Точением называется метод лезвийной обработки резанием цилиндрических и торцовых поверхностей, главное движение (Dv) - вращательное, придается заготовке, движение подачи (Ds) - прямолинейное, поступательное, придается инструменту под углом к оси вращения главного движения.
К технологическому режиму точения относятся:
Скорость главного движения, м/мин (скорость резания Vр) - путь, пройденный точкой на обрабатываемой поверхности заготовки относительно инструмента в единицу времени. Величину скорости резания определяют по формуле
Vр = (πd3n3)/1000,
где: d3 - диаметр заготовки, мм; п3 - частота вращения заготовки, мин-1. Скорость движения подачи (подача s) - перемещение режущего инстру-
мента в минуту (минутная подача sM, мм/мин) или за один оборот заготовки (подача на оборот s0, мм/об).
Глубина резания t, мм - расстояние по нормали между обработанной и обрабатываемой поверхностями. Глубина резания определяется по формуле:
t = 0,5(d3 - dд), где: d3 - диаметр обрабатываемой поверхности (диаметр заготовки), мм; dд - диаметр обработанной поверхности (диаметр детали), мм.
Технологические возможности токарной обработки
1.Материал обрабатываемого изделия. Возможна обработка практически всех известных материалов. В настоящее время, с появлением резцов из алмаза и эльбора ограничений по твердости обрабатываемого материала не существует. В обычных производственных условиях токарным методом обрабатываются заготовки из незакаленных сталей, цветных металлов, дерева.
2.Форма и размеры. Особенности кинематики процесса позволяют получать только поверхности вращения, спиральные и винтовые поверхности. Размеры обрабатываемых токарным методом изделий могут быть от 0,05 мм до 20 метров.
3.Точность при обработке на станках нормального класса точности, в экономически оптимальных условиях – 7-14 квалитет (см. Приложение).
4.Шероховатость поверхности во многом определяется выбранной подачей и геометрическими параметрами вершины резца. Она также существенно зависит от колебаний инструмента относительно заготовки в процессе обработки. При обработке на станках нормальной точности шероховатость об-
76

работанных поверхностей обычно находится в пределах Rz 80 – Rz – 5 ( см. Приложение).
Основные схемы обработки поверхностей точением
В зависимости от вида обработанной поверхности различают: обтачивание (обработка наружных поверхностей) и растачивание (обработка внутренних поверхностей). В зависимости от направления движения подачи различают: продольное точение (рис. 10.1, а) - движение подачи направлено вдоль оси вращения заготовки; поперечное точение (рис. 10.1, б) - движение подачи направлено перпендикулярно оси вращения заготовки; точение конусов (рис. 10.1, в) - движение подачи направлено под углом к оси вращения заготовки); точение фасонных поверхностей.
Рис. 10.1. Основные схемы обработки поверхностей точением:
а - продольное точение; б - поперечное точение; в - точение конических поверхностей; г - осевая обработка; д - нарезание резьбы;
Dр - главное движение резания; Ds - движение подачи;
Dsпрод - движение продольной подачи; Dsпоп - движение поперечной подачи
Продольным обтачиванием обрабатывают цилиндрические шейки валов с одновременной обработкой конических, фасонных или плоских переходных по-
77
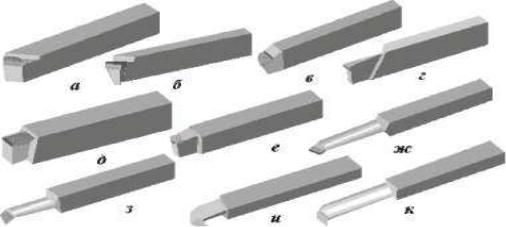
верхностей. Поперечным обтачиванием подрезают торцы, протаивают прямые или фасонные канавки, отрезают готовую деталь.
Продольным растачиванием обрабатывают гладкие или ступенчатые сквозные отверстия с конической переходной поверхностью. Если в конце рабочего хода резцу придать поперечное движение подачи, то можно получить плоскую переходную поверхность.
Обработка конических поверхностей может проводиться несколькими способами: Широкими токарными резцами с продольным или поперечным движением подачи. Таким способом получают поверхности с длинной образующей не более 30 мм. Используют способ при снятии фасок с обработанных цилиндрических поверхностей. Перемещением токарного резца под углом к оси вращения заготовки. Таким способом получают поверхности с длинной образующей не более 150 мм. Смещением оси вращения заготовки на угол равный половине угла при вершине обрабатываемого конуса. Таким способом обраба-
тывают длинные конические поверхности с углом конуса не более 8°. Смещение равно: h = Lsinα, где: h - смещение, в мм; L - полная длина заготовки, в мм,
α - половина угла конуса.
При использовании вместо токарного резца осевого инструмента (сверла, зенкера, развертки) возможно получение глухих или сквозных отверстий (рис. 10.1, г) Нарезание резьбы (рис. 10.1, д) проводится специальными резьбовыми резцами.
Режущий инструмент и рабочие приспособления
В зависимости от вида работы различают резцы: проходные прямой, отогнутый и упорный (рис. 10.2, а, б, в); отрезной (рис. 10.2, г); канавочные прямой и радиусный (рис. 10.2, д, е); расточные и радиусный (рис. 10.2, ж, з, и, к): проходной, упорный, канавочный, резьбовой.
Рис. 10.2. Токарные резцы:
а, б, в- проходные: прямой, отогнутый и упорный; г - отрезной; д, е- канавочные: прямой и радиусный; ж, з, и, к- расточные: проходной,
упорный, канавочный, резьбовой
78
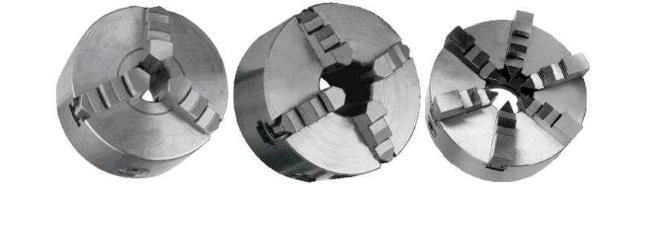
Характер базирования и закрепления заготовки в рабочих приспособлениях токарных станков зависит от типа станка, вида обрабатываемой поверхности, типа заготовки (вал, диск, кольцо, некруглый стержень), отношения длины заготовки к ее диаметру, требуемой точности обработки и т.д. При обработке круглых стержней на универсальных токарных станках чаще всего применяется трех, четырех или шести кулачковые патроны (рис. 10.3).
Рис. 10.3. Токарные патроны
Универсальный токарно-винторезный станок
На универсальном токарно-винторезном станке (рис. 10.4) обрабатывают детали различных классов (круглые и некруглые стержни, кольца, диски, корпусные детали). Станина 1 станка - массивная базовая чугунная деталь имеет две тумбы 18: переднюю и заднюю. В передней тумбе установлен главный электродвигатель.
Верхняя часть станины имеет две пары направляющих 9 и 10 для базирования и перемещения подвижных элементов станка. Передняя бабка 3 закреплена на левой части станины. В корпусе передней бабки расположена коробка скоростей со шпинделем. На правом резьбовом конце шпинделя устанавливается технологическая оснастка (патрон 4) для базирования и закрепления заготовок. Шпиндель получает вращение (главное движение Dр) от главного электродвигателя через клиноременную передачу, систему зубчатых колес и муфт, размещенных на валах коробки скоростей. Задняя бабка 8 установлена на правой части станины с возможностью перемещения по ее внутренним направляющим. Задняя бабка необходима для повышения жесткости закрепления длинных валов. Внутри задней бабки размещается выдвижная пиноль 7, в конусное отверстие которой вставляются различные центра. При обработке длинных валов передний конец заготовки устанавливается в патрон, закрепленный на шпинделе, а задний конец поджимается центром, установленным в пиноли задней бабки. При обработке коротких заготовок, заготовок типа "некруглый стержень", или корпусных заготовок в конусное отверстие пиноли устанавливается осевой инструмент, что позволяет производить осевую обработку центрального отверстия в заготовке. Движение подачи при этом осуществляется
79
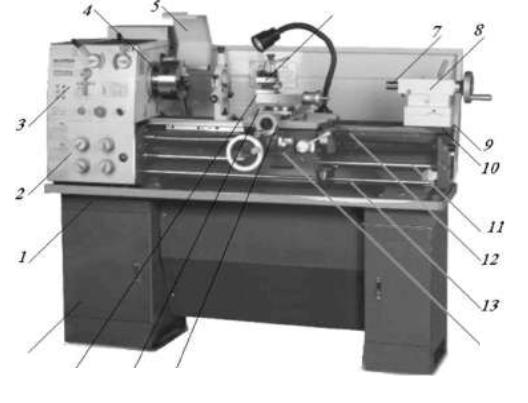
вручную вращением маховика задней бабки. На наружных направляющих станины размещается суппорт, состоящий из резцедержателя 6, поворотных 17, поперечных 16 и продольных 15 салазок. В резцедержателе устанавливаются режущие инструменты - токарные резцы. Поворотные салазки установлены с возможностью поворота и фиксации вокруг вертикальной оси, что позволяет обрабатывать короткие (до 150 мм) конусные поверхности с большими углами конусности (до 45°). При обработке длинных конусных поверхностей с малыми углами конусности (до 5°) смещают ось вращения заготовки, перемещая заднюю бабку перпендикулярно направляющим станины. Поперечные салазки позволяют придать режущему инструменту движение подачи (Ds) под углом 90 ° к оси вращения заготовки (поперечная подача). Продольные салазки позволяют придать режущему инструменту движение подачи (Ds) вдоль оси вращения заготовки (продольная подача). Движение подачи осуществляется вручную или автоматически. На передней стенке станины закреплена коробка подач 2, кинематически связанная со шпинделем. Коробка подач передаёт движение на ходовой вал 13 и ходовой винт 11. Ходовой винт служит для обеспечения автоматической подачи только при нарезании резьбы. Для обеспечения автоматической подачи при других работах служит ходовой вал.
14
18
17 16 15
Рис. 10.4. Универсальный токарно-винторезный станок: 1 - станина; 2 - лицевая панель коробки подач; 3 - передняя бабка; 4 - патрон; 5 - защитный кожух; 6 - резцедержатель; 7 - пиноль; 8 - задняя бабка;
9, 10 - наружные и внутренние направляющие; 11 - ходовой винт; 12 - рейка; 13 - ходовой вал; 14 - фартук; 15 - продольные салазки;
16- поперечные салазки; 17 - поворотные салазки; 18 - тумба
80