
3595
.pdf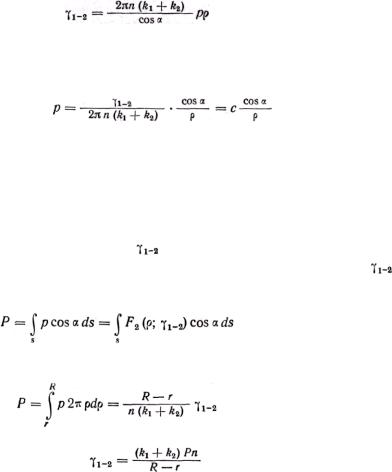
. (39)
Учитывая, что (рассматриваем период нормального износа), можно из (38) определить характер:
. (40)
Для абразивного изнашивания
. |
(41) |
|
Из полученной зависимости видно, что эпюра удельных давлений имеет неравномерный характер — на меньших радиусах вращения величина р больше (c=const).
Для дисков и конических поверхностей, где , эпюра удельных давлений при абразивном изнашивании имеет гиперболический характер. Числовые значения р можно определить лишь по-
сле того, как известна величина |
. |
|
3.2. Определение скорости |
изнашивания сопряжения |
. |
Внешняя сила Р связана с удельным давлением р, распределенным по поверхности трения s, и характеризуется зависимостью:
(42)
Например, для дисковых поверхностей ( = 0) из (42) и (41) по-
лучаем (см. рис. 11, б) |
|
, |
(43) |
откуда |
|
. |
(44) |
Из этой формулы видно, что и зависит от режимов работы сопряжения
, его размеров и износостойкости материалов
.
Зная скорость изнашивания сопряжения и предельно допустимые износы , можно определить срок службы данной пары по формуле (27).
3.3. Определение формы изношенной поверхности. Из совместного решения уравнений (34) и (35) получаем выражения для формы изношенной поверхности каждого из тел
51
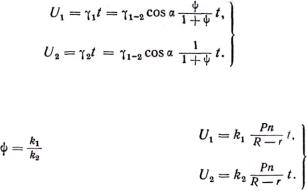
. |
(45) |
Например, при износе дисков ( = 0) в условиях абразивного изнашивания получим
и |
. |
(46) |
Таким образом, при данных законах изнашивания износ дисков равномерный (не зависит от ), а величина износа зависит от износостойкости материалов (
и
), режимов работы сопряжения (Р и n), размеров (ширина дисков R—r) и времени работы t.
Полученные и аналогичные формулы применяют для различных расчетов при конструировании и модернизации оборудования.
Если значение коэффициента износа k неизвестно, то формулы можно применять для сравнительных расчетов. Пусть, например, при проектировании новой модели станка с круговыми плоскими направляющими по сравнению с существующим аналогичным станком нагрузка увеличилась на 20% (т. е. ), скорость — на 30% (т.е.
), а материал направляющих имеет износостойкость выше на
15%.
Изменим ширину направляющих новых станков, чтобы их износостойкость по отношению к абразивному изнашиванию осталась прежней. Для решения используем формулу (44), приравняв значение для обоих случаев, то есть:
,
откуда , т. е. ширина направляющих должна быть на 35% больше.
При расчетах сроков службы по износу следует не только оценить средние значения коэффициентов износа материалов k (на основе лабораторных и эксплуатационных испытаний), но и их рассеивание в данных условиях эксплуатации.
При решении задач по износу деталей необходимо учитывать, что конструктивная схема сопряжения оказывает влияние на распре-
52
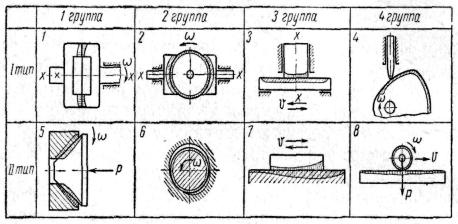
деление износа по поверхности трения и на характер взаимодействия изношенных поверхностей. Во многих случаях влияние конструктивных факторов на форму изношенной поверхности проявляется в большей степени, чем влияние закономерностей изнашивания материалов деталей.
При проектировании станков необходимо применять методы расчета на износ различных сопряжений, характерных для данного станка, чтобы обосновать выбор той или иной конструкции. Существует классификация сопряжений по условиям их изнашивания, она приведена на рис. 12 //. В зависимости от характера возможного сближения деталей при износе их поверхностей все сопряжения подразделяют на два типа.
Рис. 12. Классификация сопряжения по условиям их изнашивания
У сопряжений I типа имеются дополнительные неизнашивающиеся или малоизнашивающиеся направляющие, которые обеспечивают сближение деталей при износе только в направлении х—х.
В сопряжениях II типа происходит самоустановка изношенных деталей, и их взаимное положение зависит от формы изношенной поверхности. В таких сопряжениях износ обычно более сильно сказывается на служебных свойствах пары.
Кроме того, в классификации все сопряжения в зависимости от постоянства условий трения и износа поверхностей для расположен-
53
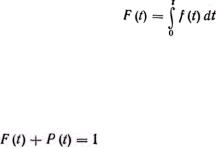
ных на одной траектории точек сопряженных тел разделены на четыре группы. У сопряжений 1-й группы точки, расположенные на одной траектории, имеют одинаковые условия изнашивания для каждого из двух тел (например, износ поверхностей вращения при центральной нагрузке). Ко 2-й группе отнесены сопряжения, у которых условия изнашивания сохраняются только для точек одного тела, лежащих на данной траектории (подшипники скольжения и колодочные тормозы). К 3-й группе отнесены сопряжения с низшими парами (направляющие станков, кулисные механизмы). К 4-й группе отнесены сопряжения с высшими парами (подшипники качения, кулачковые механизмы). У сопряжений 3 и 4-й групп условия изнашивания не сохраняются постоянными для всех точек обоих тел; в этом случае имеются большие возможности для возникновения неравномерного износа поверхностей. Принадлежность сопряжения к тому или иному типу и группе определяет методику его расчета на износ и позволяет связать создаваемую конструкцию сопряжения с характеристикой его вероятного износа.
3.4 Методы повышения надежности станков
Для определения коэффициента надежности , т. е. вероятности безотказной работы данного элемента, рассмотрим интегральную функцию распределения (см. рис. 9,в и 10,в):
(47)
.
Ординаты этой функции численно равны площади, отсекаемой абсциссой t на кривой , и характеризуют вероятность выхода из строя детали за период от 0 до t.
Вероятность безотказной работы относится к событию, противоположному появлению отказа (выходу из строя)
. Поэтому
или (48)
Для нормального закона распределения сроков службы, что характерно для постепенных (износовых) отказов из (26) и (47),
. (49)
54
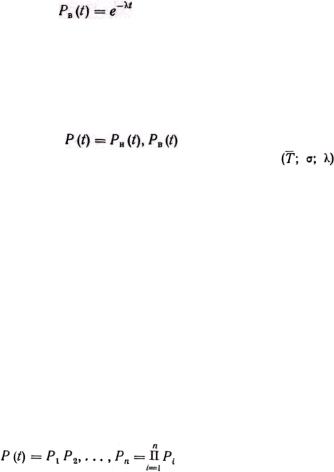
Для вычисления значений этой функции в теории вероятностей пользуются таблицами функции Лапласа.
При внезапных отказах, для которых характерен экспоненциальный закон распределения, из (28) и (47) получаем (рис. 10, в)
. (50)
При совместном действии износовых и внезапных отказов коэффициент надежности можно подсчитать по теореме умножения вероятностей, так как событие — вероятность безотказной работы элемента за время t —требует выполнения двух условий: безотказности от износовых повреждений и безотказности от внезапных выходов из строя
|
(51) |
Если известны параметры законов распределения |
, мож- |
но подсчитать вероятность безотказной работы элемента или узла. По известным значениям вероятности времени безотказной работы элемента необходимо подсчитать коэффициент надежности
сложной системы, состоящей из большого числа различным образом соединенных элементов.
Наиболее характерен случай, когда отказ одного элемента выводит из строя всю систему, как, например, при последовательном соединении элементов (рис. 13, а). Так, все приводы станков, механизмы и передачи подчиняются этому условию. Если, например, в коробке скоростей станка выйдет из строя любая шестерня, подшипник, муфта, рычаг управления, электродвигатель, насос смазки и т. п., то вся коробка перестанет функционировать.
Вероятность безотказной работы такой системы по теореме умножения вероятностей независимых событий равна произведению вероятностей безотказной работы элементов, т. е.
(52)
Если причиной выхода из строя является только внезапный отказ и функция распределения сроков службы подчиняется экспоненциальному закону (50), то величина P(t) также будет подчиняться экспоненциальному закону с параметром
. (53)
55
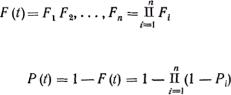
Простота подсчета надежности сложных систем при экспоненциальном законе приводит часто к тому, что этим правилом пользуются и в тех случаях, где причина выхода из строя — износовый отказ, но это совершенно недопустимо.
Сложные системы, состоящие из элементов высокой надежности, могут обладать низкой надежностью вследствие наличия большого числа элементов. Например, если узел состоит из 50 деталей, а коэффициент надежности каждой детали за выбранный промежуток времени составляет , то коэффициент надежности узла
.
Для повышения надежности сложных систем применяют резервирование, т. е. создают дублирующие элементы, которые выполняют одинаковые функции. Поэтому при выходе из строя одного из элементов дублер выполняет его функции и узел не прекращает своей работы. Резервирование значительно повышает надежность системы. При постоянном (нагруженном) резервировании, когда резервные элементы постоянно присоединены к основным и находятся в одинаковом с ними режиме работы (рис. 13, б), вероятность безотказной работы P(t) системы подсчитывают следующим образом.
Принимают, что за время t, вероятность появления отказа каж-
дого из элементов есть . Тогда отказ системы — это событие, которое происходит при условии отказа всех элементов, и вероятность совместного появления всех отказов:
. |
(54) |
Поэтому коэффициент надежности системы с параллельно резервированными элементами, учитывая (48), равен
(55)
Например, если надежность каждого элемента р=0,9, а n=3, то
.
56
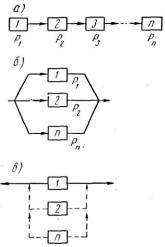
Рис. 13. Схема для определения коэффициента надежности сложных систем
Таким образом, надежность системы повышается и становится возможным создание надежных систем из ненадежных элементов.
Возможно также создание ненагруженного резервирования (резервирования замещением), когда резервные цепи находятся в отключенном состоянии и включаются лишь тогда, когда основная цепь (или элемент) отказывают (рис. 13,в).
В этом случае необходимы системы или приборы для обнаружения отказа и устройство для включения резерва. Резервирование хотя и повышает надежность систем, но приводит к их усложнению и удорожанию, поэтому целесообразность его применения должна быть оправдана экономически. Примеры резервирования в станках: автоматическая замена инструмента при его износе; замена целого узла — внутришлифовального шпинделя при износе его подшипников, увеличение опорных площадей (например, для направляющих) с целью уменьшения удельных давлений и, следовательно, уменьшения скорости изнашивания (происходит как бы распределение нагрузки на добавочные резервные поверхности).
Укажем основные методы повышения надежности станков //.
1. Создание надежных узлов и элементов путем рациональной конструкции и применения износостойких материалов. Большая со-
57

противляемость вредным воздействиям на узел уменьшает скорость потери его работоспособности, смещает кривую рассеивания сроков службы в область более высоких значений t и повышает вероятность безотказной работы за данный промежуток времени.
2. Повышение стабильности технологических процессов при изготовлении деталей станка. Это приводит к уменьшению рассеивания сроков службы. Поэтому даже при одинаковых средних значениях
сроков службы |
можно повысить надежность элемента , что |
видно из рис. 14,а. |
|
3. Обкатка станка и его узлов, что позволяет выявить те недостатки изготовления и сборки, которые приводят к повышенным внезапным отказам в первый период работы машины. Анализ параметра потока отказов (рис. 14, б) для экспоненциального закона показывает, что в первый период
внезапные отказы имеют повышенное значение и поэтому его надо исключить из периода нормальной эксплуатации станка.
4.Защита станка от случайных перегрузок или вредных воздействий. В реальных условиях всегда можно ожидать, что любая случайная функция (например, функция, характеризующая силу в механизме) даст «выброс» за допустимый уровень (рис. 14, в). Выброс, даже если он будет крайне редким, может привести к повреждениям, при которых машина выйдет из строя. Для того чтобы придать станкам защитные функции от таких случайностей, в них применяют механизмы, предохраняющие от перегрузки, которые размыкают кинематическую цепь, если нагрузка превышает допустимое значение.
5. Применение резервирования как метода создания надежных систем из элементов невысокой надежности.
6.Применение самовосстанавливающихся систем, которые при утрате начальных характеристик восстанавливают свои функции. Такие системы автоматической подналадки широко внедряют в конструкции станков, например, это автоматическая компенсация износа, автоматическое регулирование температурных параметров и др.
7. Упрощение системы и создание узлов с меньшим числом кинематических цепей и изнашивающихся элементов всегда приводят к повышению надежности машины. Создать более простую машину, выполняющую заданные функции, значительно труднее, чем сложную, так как это требует оригинальных, продуманных решений.
58
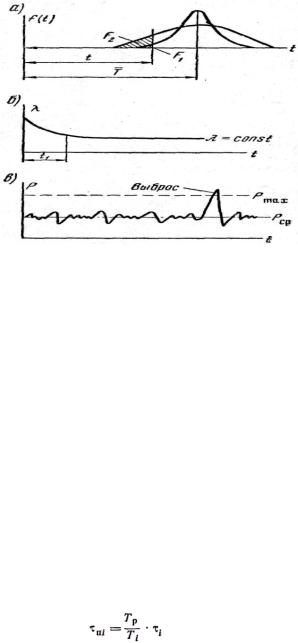
Рис. 14. Повышение надежности узлов: а — повышение стабильности технологического процесса изготовления деталей; б — обкатка узла; в — защита от повышенных режимов
3.5 Методы повышения долговечности станков
Исследуя (см. ранее) надежность и долговечность станков, установили, что основной характеристикой этих показателей является срок службы. Так как долговечность оборудования это – свойство сохранять работоспособность, до предельного состояния с необходи-
мыми перерывами для технического обслуживания |
и ремонта, то |
следует остановиться на оценке и методах повышения |
долговечно- |
сти. Показателем долговечности может быть срок службы Тсл или ресурс Тр. При этом различают срок службы до первого капитального (среднего) ремонта и межремонтный ресурс.
Для определения коэффициента долговечности необходимо установить его зависимость от сроков службы деталей станка. Считаем, что время простоя по причине ремонта данной детали или узла станка
равно |
|
, |
(56) |
59 |
|
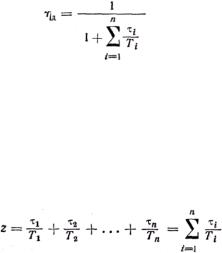
где — срок службы (долговечность) i-й детали (узла) станка;
— время (трудоемкость) ремонта i-й детали (узла), включая разборку, сборку и выверку.
Отношение показывает, сколько раз в течение периода, рав-
ного , ремонтировалась данная деталь.
Для определения необходимо брать тот период времени, когда имеются все виды простоев по вине станка, т. е. больше, чем срок службы
любой детали станка. В итоге получаем значение коэффициента долговечности, выраженное через сроки службы и трудоемкость ремонта деталей станка:
. |
(57) |
При периодических ремонтах, когда одновременно ремонтируется группа деталей, — время до очередного ремонта и
— его трудоемкость (в единицах времени).
Таким образом, из формулы (57) видно, что основным методом повышения долговечности станка является сокращение времени, затрачиваемого на ремонт и повышение сроков службы его деталей. Также видно, что коэффициент долговечности зависит от суммы, которая называется относительными ремонтными потерями:
(58)
.
Величина z — случайная, так как и Т и являются случайными величинами. Причем каждая из них характеризуется определенным рассеиванием значений. Основное влияние на рассеивание оказывает величина Т, так как величина
изменяется незначительно. Согласно теореме теории вероятностей математическое ожидание суммы случайных величин (как независимых, так и зависимых) равно сумме их математических ожиданий. Это значит, что для определения среднего
значения z надо взять средние значения каждого из слагаемых .
Если надо оценить возможные колебания значения z и соответственно , то следует определить дисперсию z по дисперсии слагае-
мых . Можно с достаточной степенью точности считать, что сла-
60