
3595
.pdf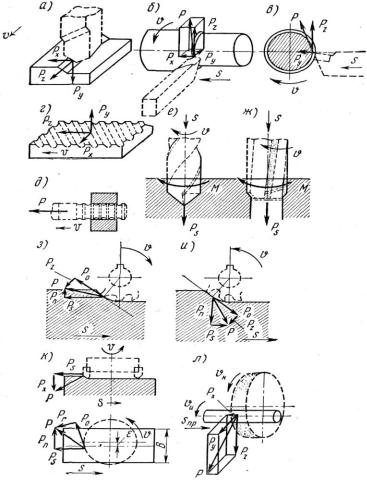
Рис. 1. Движения и усилия резания при различных методах обработки
В станках часто одновременно можно наблюдать сочетание различных движений и методов управления. Применение тех или иных методов движений и управления характеризует специфику станка и влияет на компоновку и конструкцию отдельных узлов. Например, применение методов программного управления на базе электроники и компьютеров приводит нередко к необходимости выделять эти узлы в виде шкафов или агрегатов управления, входящих в автономную (дл одного модуля) или цеховую автоматизированную систему управления. Часто, имея одинаковую принципиальную компоновку отдель-
11
ных узлов и модулей, станок в зависимости от метода осуществления движений включает узлы совершенно различной конструкции с своеобразной компоновкой в них деталей и механизмов.
Большинство современных систем представляет собой сложные комплексы, в которых сочетаются электрические, пневматические, измерительные и другие цепи с механическими цепями или передаточными механизмами. От качества механизма в значительной степени зависит и качество всего станочного комплекса.
Основное назначение механизма в машине заключается в передаче энергии от двигателя к рабочему органу с одновременным преобразованием скоростей движения звеньев; в металлорежущих станках передаточные механизмы выполняют дополнительные функции:
- преобразование перемещения первичного преобразователя движений к вторичному и передачу их на исполнительный орган;
-преобразование характеристик механического сигнала (перемещения, скорости, ускорения) в перемещения, воздействующие на электрические, гидравлические или иные преобразователи и рабочие органы;
-обширный ряд эксплуатационных операций (включение или выключение узлов станка, переключение диапазонов регулирования, ручную или автоматическую настройку, дистанционное управление процессом формообразования, измерительной системой и др.;
-вычислительные математические операции (суммирование, логарифмирование, дифференцирование и т. п.);
-обеспечение взаимосвязей подсистем станка с СЧПУ и другие. К конструкциям передаточных механизмов станков предъяв-
ляют следующие требования:
-заданной точности преобразования движения рабочих органов по заданной функциональной зависимости;
-высокие показатели прочности и жесткости элементов механизмов и станка в целом при передаче усилий и моментов;
-технологичности конструкции, невысокой материалоемкости, минимальных габаритных размеров и массы;
-простоты и надежности регулировки, высокого КПД, малой чувствительности к температурным изменениям и вибрациям и колебательным процессам;
-наименьшей стоимости проектирования и изготовления.
12
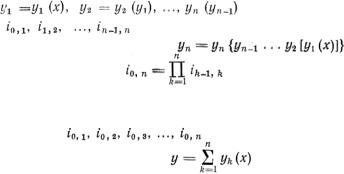
При разработке конструкции передаточного механизма необходимо иметь в виду, что выполнение всех перечисленных требований затруднительно, так как некоторые из них могут противоречить одно другому. Например, повышение точностных характеристик всегда приводит к увеличению стоимости проектирования и изготовления; повышение прочности и жесткости отдельных звеньев - к увеличению габаритных размеров и массы; нечувствительность к температурным изменениям достигается за счет введения специальных компенсационных узлов, что, безусловно, усложняет механизм.
Разработка оптимальных вариантов конструкций узлов и станка в целом может быть выполнена только применительно к конкретной задаче с учетом условий реализуемого метода формообразования, изготовления станочной системы и еѐ эксплуатации.
Анализ всего многообразия реальных передаточных механизмов, оборудования показывает, что их кинематические цепи состоят из простейших, как правило, трехили четырехзвенных механизмов, соединенных между собой.
Наиболее распространено последовательное соединение п меха-
низмов (рис. |
2, а) с функциями |
перемещения ведомого звена |
|
и |
передаточными отношениями |
( |
), а для всей цепи |
|
Параллельное соединение п механизмов с функциями перемещения и передаточными отношениями
;
показано на рис.2, б.
Встречно-параллельное соединение двух механизмов с функциями перемещения и
и передаточными отношениями
и
, а для всей двухэлементной ячейки
;
приведено на рис.2, в.
13
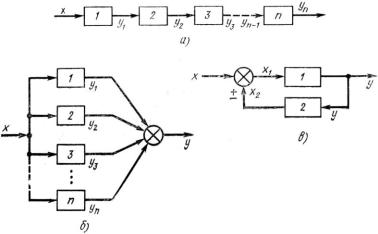
Рис. 2. Соединение механизмов: а — последовательное; 6 — параллельное; в — встречно-параллельное
1.4 Классификация передаточных механизмов
Все элементарные передаточные механизмы можно классифицировать по ряду признаков, например по конструктивному выполнению, кинематическим и динамическим параметрам, точности и т. д.
Наиболее важными из этих признаков являются конструктивный и кинематический. По конструктивному признаку все передаточные механизмы могут быть разделены на восемь групп (рис. 3). Все группы, кроме одной (винтовые механизмы), подразделяются на подгруппы.
Передаточные механизмы можно также классифицировать по виду преобразования движения и по преобразованию скорости.
По виду преобразования движений:
а) вращательного во вращательное -зубчатые (колесо - шестерня, сектор - шестерня), червячные, кулачковые с качающимся толкателем и др.;
б) вращательного в поступательное — кривошипно-ползунные, зубчатые (шестерня-рейка), винтовые, кулачковые с поступательно движущимся толкателем и т. п.;
в) поступательного во вращательное — синусные и тангенсные, зубчатые (рейка—шестерня) и др.;
14
г) поступательного в поступательное — двойные синусные или тангенсные.
По преобразованию скорости движения:
а) с постоянным отношением скоростей — зубчатые, фрикционные, червячные и т. п.;
б) с переменным отношением скоростей.
Характерная особенность механизмов с переменным отношением скоростей заключается в том, что одно из звеньев (ведущее или ведомое) находится в равномерном движении, в то время как скорость движения другого звена может подчиняться любому более сложному заданному закону (например, механизмы синусные и тангенсные, поводковые, кривошипно-ползунные, кулачковые и др.). К этой же группе относятся механизмы прерывистого движения, у которых равномерное движение ведущего звена преобразуется в пульсирующее (с остановками) движение ведомого (мальтийские и храповые механизмы).
15
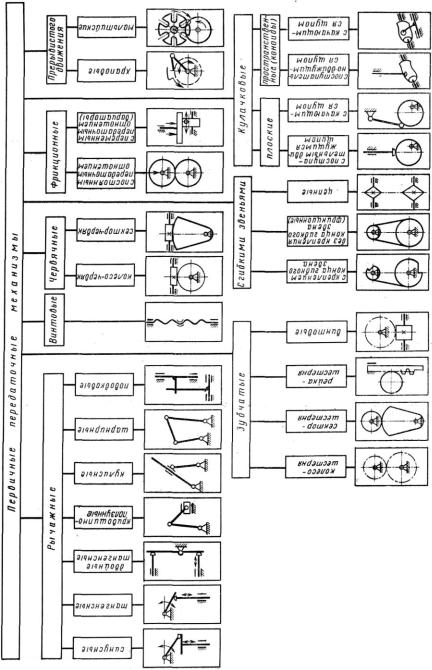
16
Рис. 3. Классификация передаточных механизмов
При рассмотрении кинематики механизмов условимся первое слово относить к ведущему звену, а второе — к ведомому. Например, если рассматривается передача колесо—шестерня, ведущим является колесо, и, наоборот, в передаче шестерня—колесо оно является ведомым. Таковы некоторые особенности теории общих вопросов конструирования станочных систем.
Глава 2 КРИТЕРИИ ОЦЕНКИ КАЧЕСТВА СТАНКОВ
Любой станок должен обладать высокими техническими характеристиками. Необходимо, чтобы его показатели качества, такие как геометрическая точность, жесткость, виброустойчивость и другие, находились в требуемых пределах в течение всего периода эксплуатации и обеспечивали выпуск продукции заданной точности. Поэтому необходимо оценить заложенные изначально в конструкцию статические показатели качества станка и установить их возможные изменения под влиянием разнообразных процессов, действующих на его элементы при эксплуатации станка.
2. 1 Статические показатели качества станков
Геометрическая и кинематическая точность станков. Станок в первую очередь должен обеспечивать необходимую геометрическую точность всех его элементов, так как вследствие неточного расположения узлов и деталей станка и неточности основных направляющих элементов происходит нарушение тех геометрических траекторий, по которым перемещаются основные рабочие органы станка. Например, из-за погрешностей подшипников шпинделя или овальности его шеек происходит радиальное биение шпинделя, что искажает форму обрабатываемой детали в поперечном направлении. Другой пример, непрямолинейность направляющих скольжения приводит к искажению траектории перемещения суппортов и столов станка, это также искажает форму обработанной поверхности.
Далее, взаимное расположение оси шпинделя и поверхности стола, двух шпинделей (например, с инструментом и заготовкой), их
17
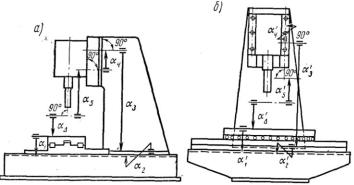
непараллельность или неперпендикулярность вызывают соответствующие погрешности при обработке детали.
Точность взаимного положения двух рабочих органов станка (например, шпинделя и стола) зависит от точности элементов той размерной цепи, которая связывает эти узлы. Так, отклонение оси шпинделя координатно-расточного станка от перпендикулярности к рабочей поверхности стола (рис. 4) зависит от соответствующих отклонений
сопрягаемых поверхностей узлов станка:
.
Размерные цепи на рис.4 рассмотрены в двух взаимно перпендикулярных плоскостях. отклонение оси шпинделя от перпендикулярности к плоскости стола зависит от следующих факторов: непараллельности плоскости стола и направляющих станины и
; непараллельности привалочной поверхности под стойку и направляющих станины
и
, неперпендикулярности плоскости стойки для соединения со станиной и плоскости под блок направляющих шпиндельной бабки
и
, непараллельности направляющих бабки и опорной поверхности блока
и
непараллельности оси шпинделя и направляющих бабки
и
.
Рис. 4. Размерные цепи координатно-расточного станка
Из схемы видно, что при высоком допуске на неперпендикулярность оси шпинделя столу к точности взаимного положения узлов
18
станка предъявляются еще более строгие требования. Часто для этой цели применяют пригонку одного из звеньев в собранном станке, например, шабрят плоскости стойки, превращая звено размерной цепи в компенсатор. Достижение высокой геометрической точности станков, особенно прецизионных, является сложной технологической задачей, тесно связанной с конструкцией станка.
На нормы точности металлорежущих станков имеется ГОСТ, в котором указаны допустимые отклонения (погрешности) в работе различных типов станков и методы проверки всех основных элементов станка. Эти проверки характеризуют лишь геометрическую точность станка, без учета действующих усилий резания.
Наряду с геометрической, различают также и кинематическую точность элементов станка. Последняя необходима для характеристики тех станков, в которых форма обрабатываемой поверхности зависит не только от траекторий относительного перемещения инструмента и заготовки, но и от скоростей их взаимного движения. Например, если на токарно-винторезном станке нарезается резьба и суппорт перемещается по строго прямолинейной траектории, а шпиндель не имеет биения, то основные неточности на изделии возникают, если нарушается передаточное отношение между числом оборотов и перемещением суппорта. Точность кинематической цепи, которая в первую очередь зависит от качества зубчатых передач и ходового винта, определит точность обработки.
Кинематические ошибки в зуборезных, винторезных, зубо- и резьбошлифовальных станках существенно влияют на точность обработки.
В зуборезных станках на кинематическую точность в основном влияют погрешности изготовления и монтаж червячного колеса и червяка делительного механизма и других пар цепи деления. В результате возникают накопленная погрешность окружного шага разрезаемого колеса, погрешность профиля зуба и другие погрешности, характеризующие качество обработки.
Большое влияние на точность обработки на координатнорасточных и других станках оказывает точность измерительных и отсчетных устройств, предназначенных для перемещения стола, суппорта с изделием или инструментальной головки.
19

Геометрическая и кинематическая точность станков является необходимым, но не достаточным условием для обеспечения высокого качества станка. Для этого надо учитывать также сопротивляемость его узлов и деталей действию внешних и внутренних сил.
2.2 Статическая прочность узлов станка
Все узлы и детали станка должны обладать высокой прочностью, чтобы в течение всего периода эксплуатации не происходило их поломок. Поломка является следствием неправильного расчета и подбора материала или недопустимых методов эксплуатации.
Примерами поломок деталей станков из-за недостаточной прочности, заложенной при конструировании, могут служить поломки корпусных деталей суппортов, кронштейнов, траверс. Поломки могут быть также из-за брака в литье, из-за неправильной конструктивной формы или неправильных методов эксплуатации оборудования.
При расчетах деталей станков на прочность необходимо учитывать характер нагрузок, действующих на деталь, так как от этого зависят вид разрушения детали и методы ее расчета. Надо также помнить, что поломки деталей из-за усталостной прочности нередко встречаются в шпинделях и валах, зубчатых колесах и носят аварийный характер.
Статическая прочность определяет размеры лишь некоторых деталей станков: медленно вращающихся валов и шестерен, крепежных винтов, кронштейнов, некоторых неответственных корпусных деталей. Расчет на статическую прочность ведут с учетом допускаемых напряжений , величины которых выбирают в зависимости от материалов. Так, для пластических материалов (стали) их назначают с учетом отношения к пределу текучести
,а для хрупких мате-
риалов (чугуна) - по отношению к пределу прочности |
. |
При |
|
|
этом коэффициенты запаса находятся обычно в пределах для термически необработанных и улучшенных сталей и
для деталей из чугуна, работающих на изгиб.
Выносливость или усталостная прочность детали определяет размеры большинства конструкций станка, так как наличие перемен-
20