
3334
.pdfОсновным элементом сушильной установки является рабочая камера 1 высотой 0,4 м, образованная внешней цилиндрической обечайкой диаметром 0,4 м и внутренней конической обечайкой с диаметром основания 0,2 м. В конической обечайке вырезаны окна для свободной подачи материала в рабочую камеру из загрузочного патрубка 2. Выгрузка материала осуществляется из оснащённых перегородками разгрузочных патрубков 3. Сушильный агент подаётся в рабочую камеру через входной участок 4, а отводится через выходной участок 5. В качестве газораспределительного устройства 6 в аппарате используется жалюзийная решётка [5], накрытая металлической сеткой.
Сушилка периодического действия с центробежным псевдоожиженным слоем имеет малые габариты, простую конструкцию и обладает незначительным гидравлическим сопротивлением, а интенсификация тепломассообмена осуществляется за счёт воздействия на частицы центробежных сил [3, 4]. Однако её применение оправданно только для «тонких» псевдоожиженных слоёв, толщиной не более 0,1 м [3].
Для проверки работоспособности сушилки и оценки интенсивности протекающих в ней процессов тепло– и массообмена на испытательном стенде, описанном в [6], была проведена первая (предварительная) серия экспериментов, посвящённая сушке силикагеля с диаметром частиц от 2,4 ± 0,2 мм. Согласно [7] регенерацию силикагелей возможно проводить уже при температуре 40 °C, осуществляя, таким образом, процесс низкотемпературной сушки. Поэтому температура сушильного агента (атмосферного воздуха) на входе в сушильную установку tг поддерживалась в диапазоне от
40 до 60 °C. При этом верхняя граница температурного диапазона выбрана по условиям эксплуатации датчиков влажности воздуха. Точность поддержания температуры составляла ±2 °C.
Остальные параметры режима сушки: масса материала в рабочей камере Mт 1 кг; скорость теплоносителя на входе в рабочую
камеру г – от 2,0 до 2,6 м/с; начальное влагосодержание силикагеля uн = 0,25; 0,32; 0,53; 0,82 кг/кг; соответственно высота псевдо-
ожиженного слоя H = 0,024; 0,021; 0,018; 0,015 м.
Время проведения опытов во всех режимах составляло 30 минут. При этом на ПК с периодичностью в 10 секунд фиксировались температура и относительная влажность сушильного агента: на
141
всасывающей стороне вентилятора – tг0 , °C и 0 , % (позволяющие отслеживать параметры воздуха в лаборатории); перед рабочей камерой – tг , °C и , %; после рабочей камеры – tг , °C и , %. Для измерения температуры силикагеля tт , °C применялась «ловуш-
ка», с помощью которой производилось изъятие небольших проб материала ( = 0, 2, 4, 6, 8, 10, 15, 20, 25 и 30 минут). Затем пробы помещались в анализатор влажности для определения текущего значения влагосодержания u , кг/кг.
По полученным экспериментальным данным были построены временные зависимости вышеперечисленных величин, основными из которых являются кривые сушки u f1 ( ) и нагрева tт f2 ( )
дисперсного материала [8]. Для проверки методики проведения эксперимента для каждого режима сушки опыт повторяли не менее трёх раз, при этом отклонение результатов измерений составило от 3 до 11 %. Было замечено, что при повторных опытах значительное влияние на результат измерений оказывает влажность воздуха в лаборатории.
Полученные временные зависимости для режима t 50 °C,
г
г 2,2 м/с, uн = 0,32 кг/кг представлены на рис. 2. Из него видно, что при этом режиме сушки силикагель достигает равновесного c воздухом влагосодержания uр 0,026 кг/кг к 15–й минуте процесса.
Зависимости t f |
3 |
( ) |
и f |
4 |
( ) демонстрируют единовремен- |
г |
|
|
|
ный минимум и максимум, отражающие максимальное насыщение воздуха водяным паром.
Кривая сушки имеет стандартный вид и позволяет выделить два периода – первый (период постоянной скорости сушки) и второй (период падающей скорости сушки) [8]. Критическое влагосодержание материала uкр , соответствующее переходу первого пери-
ода сушки во второй, при данном режиме составляет 0,12 кг/кг. Кривая нагрева демонстрирует рост температуры материала до
10 мин. с последующим её постоянством до окончания процесса сушки. Это не характерно для капиллярно–пористых тел, к которым относится силикагель [1, 8], и требует дальнейшего изучения.
142
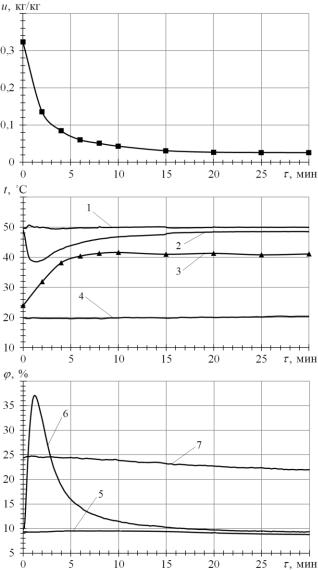
Рис. 2. Процесс сушки силикагеля при tг |
50 °C, г |
2, |
2 |
м/с, |
uн = 0,32 кг/кг: 1 – tг ; 2 – tг ; 3 – tт ; 4 – tг 0 |
; 5 – ; 6 |
– |
; |
7 – 0 |
На рис. 3–6 приведено сравнение кривых сушки и нагрева силикагеля и конечных параметров сушильного агента для следующих
143

режимов: г 2,6 м/с, uн = 0,82 кг/кг, tг = 40 °C (1), tг =50 °C (2),
tг =60 °C (3).
Рис. 3. Кривые сушки силикагеля
Рис. 4. Кривые нагрева силикагеля
Рис. 5. Температура воздуха на выходе из сушилки
144

Рис. 6. Влажность воздуха на выходе из сушилки
Из данных зависимостей видно, что при увеличении температуры сушильного агента возрастает интенсивность удаления влаги из материала. При этом критическое и равновесное влагосодержания
имеют следующие значения: при tг = 40 °C uкр = 0,28 кг/кг, |
uр = |
0,042 кг/кг; при tг = 50 °C uкр = 0,38 кг/кг, uр = 0,036 кг/кг; при |
tг = |
60 °C uкр = 0,46 кг/кг, uр = 0,024 кг/кг. На рис. 6 также прослеживается совпадение значений конечной влажности воздуха, характерное для начальных этапов всех исследованных режимов сушки силикагеля.
Из полученных опытных данных можно сделать вывод, что разработанная установка позволяет осуществлять процесс низкотемпературной сушки силикагеля. При его максимальной начальной влажности uн = 0,82 кг/кг и температуре теплоносителя 60 °C про-
цесс сушки занимает не более14 минут. Также следует отметить, что методика проведения эксперимента в целом адекватна, но для облегчения анализа кривых сушки и нагрева требуется увеличение числа проб материала.
Результаты проведённых исследований позволят произвести верификацию математической модели, представленной в работе [9] и могут быть использованы при проектировании сушилок с псевдоожиженным слоем.
Литература 1. Муштаев, В.И. Сушка дисперсных материалов / В.И. Мушта-
ев, В.М. Ульянов. – М.: Химия, 1988. – 352 с.
145
2.Handbook of Industrial Drying / A.S. Mujumdar, J. Adamiec, J.Y. Hung et al; Edited by A.S. Mujumdar. – 4–rd edition. – Boca Raton: CRC Press, 2014. – 1348 р.
3.Агапов, Ю.Н. Оценка гидравлического сопротивления и межфазного теплообмена в центробежном псевдоожиженном слое / Ю.Н. Агапов, А.В. Бараков, А.В. Жучков, А.В. Санников // Химическая промышленность. – 1986. – Т. 63. – № 4. – С. 61–63.
4.Фалеев, В.В. Исследование межфазного теплообмена в регенеративном теплообменнике с дисперсной насадкой / В.В. Фалеев, А.В. Бараков // Промышленная энергетика. – 2003. – № 6. – С. 35–37.
5.Агапов, Д.Ю. Экспериментальное сравнение газораспределительных устройств для формирования центробежного слоя / Д.Ю. Агапов, А.А. Надеев, К.Н Родионов., В.Г. Стогней, И.Ю. Клейников
//Вестник Воронежского государственного технического университета. – 2012. – Т. 8. № 7–1. – С. 118–121.
6.Надеев, А.А. Экспериментальное исследование процесса сушки силикагеля в аппарате с центробежным псевдоожиженным слоем / А.А. Надеев, А.В. Бараков, В.Ю. Дубанин, А.Ю. Андреев // Вестник Воронежского государственного технического университета. – 2018. – Т. 14. – № 2. – С. 44–50.
7.The regeneration of silica gel desiccant by air from a solar heater with a compound parabolic concentrator / S. Pramuang, R.H.B. Exell // Renewable Energy. – 2007. – V. 32. – Is. 1. – P. 173–182.
8.Лыков, А.В. Теория сушки / А.В. Лыков. – М.: Энергия, 1968.
– 472 с.
9.Barakov A.V. The asymptotic solution of model equations for heat capacities of fluidized bed phases / A.V. Barakov, A.P. Byrdin, V.Y. Dubanin, A.A. Nadeev // Journal of Physics: Conference Series. – 2017.
– № 891. – Pp. 012325. – DOI: 10.1088/1742–6596/891/1/012325.
Воронежский государственный технический университет
146
УДК 62.69
И.Ю. Жеребятьев, студент
ПАРОГЕНЕРАТОРНАЯ УСТАНОВКА ДЛЯ ОЧИСТКИ ПАРОМ ТЕХНОЛОГИЧЕСКОГО ОБОРУДОВАНИЯ
Аннотация: в данной статье рассматривается описание работы парогенераторной установки, предназначенной для очистки паром агрегатов воздушного охлаждения (АВО) газа и масла, лопаток компрессоров газоперекачивающих агрегатов (ГПА), а также другого оборудования, механизмов и объектов
Ключевые слова: парогенераторная установка, очистка паром, редуктор, горелка
Областью применения парогенераторной установки (далее – ПГУ) является предприятия нефтегазовой промышленности по добыче, транспортированию и переработке природного газа, а также другие объекты народного хозяйства [1]. Она предназначена для работы, как на открытом воздухе, так и в помещении. В последнем случае должна быть предусмотрена возможность отвода продуктов сгорания в окружающую среду. На рис. 1 приведена схема ПГУ.
Работа ПГУ осуществляется следующим образом. Природный газ под давлением 7,5 МПа по гибкому трубопроводу ТГ поступает в шкаф подготовки газа, проходит через фильтр Ф1 и поступает в редуктор КР1, где происходит понижение давления газа до 1,2 МПа. Далее газ поступает в регулятор давления газа РДУ, где редуцируется до давления 3 кПа, и через счётчик газа РМ поступает в газовую горелку.
При давлении подводимого природного газа до 1,2 МПа газ минует редуктор КР1 и через вентиль ВН2 поступает в регулятор давления газа РДУ и далее через счётчик газа РМ поступает в газовую горелку.
В случае повышения давления на выходе в РДУ до 3,5 кПа открывается предохранительный сбросной клапан ПСК, обеспечивая сброс газа в дренаж. При дальнейшем повышении выходного давления срабатывает предохранительный запорный клапан ПЗК1 и перекрывает вход газа в регулятор. При понижении входного давления до 0,01–0,05 МПа срабатывает предохранительный запорный клапан ПЗК2 и перекрывает вход газа в регулятор [2].
147

148
Рис. 1. Схема пневмогидравлическая принципиальная ПГУ: вентили (ВН1–ВН5); горелка газовая (ГГ); редуктора (КР1, КР2); манометры (МН1–МН4); насадок (НС); насадок теплоизолированный (НСТ); парогенератор (ПГ); предохранительные запорные клапана (ПЗК1, ПЗК2); предохранительный сбросной клапан (ПСК); регулятор давления универсальный (РДУ); счетчик газа (РМ); трубопровод гибкий (ТГ); указатель уровня (У1); шланг паровой (ШП).

Пуск регулятора в работу производится вручную после устранения причин, вызвавших срабатывание автоматического отключающего устройства регулятора РДУ.
Перед и после фильтра Ф1, после редуктора КР1 и регулятора давления РДУ установлены индикаторные манометры МН1–МН4.
Для заполнения магистралей перед горелкой газом установлен вентиль ВН3.
Вентиль ВН1 обеспечивает сброс давления газа из магистралей перед отсоединением гибкого трубопровода от источника газа. Вентиль ВН5 обеспечивает подачу газа в манометр МН4 и сброс давления газа из манометра.
Заправка бака водой осуществляется через заливную горловину, слив воды после завершения работы осуществляется с помощью вентиля ВН4. Уровень воды в баке определяется с помощью уровнемера У1.
Подвод пара к потребителю осуществляется с помощью парового шланга ШП и насадка теплоизолированного НСТ и насадка цилиндрического либо щелевого НС.
Рис. 2. Схема пневмоэлектрическая принципиальная горелки
149
Пуск горелки (рис. 2) происходит от пускового сигнала устройства управления 9. Начинает выполняться пусковая программа программного реле 8. Запускается двигатель горелки 4 и происходит предварительная продувка. Дифференциальное реле давления воздуха 5 контролирует давление воздуха, создаваемое вентилятором горелки. После предварительной продувки трансформатор зажигания 6 подаёт напряжение на электроды 7, между которыми возникает искровая дуга. Клапаны КЛ1 и КЛ2 в MultiBloc 1 открываются. Газ поступает в газовое сопло 2 и зажигается под влиянием искровой дуги.
Если давление газа перед горелкой ниже заданного регулятором давления РД, срабатывает реле давления PS, и горелка не запускается.
Пламя горелки нагревает паровой змеевик 10, находящийся в топке (рис. 3). Вода из бака через шаровой клапан 1, грязевик 2, регулировочный клапан 3 всасывается водяным насосом 5 и через регулятор потока 4, обратный клапан 8 подаётся в змеевик, где происходит её испарение.
Работа парогенератора регулируется прессостатом 14, который запускает и останавливает горелку и насос по параметрам давления пара. Ограничитель температуры 13 и предохранительный клапан 15, установленные на паровом трубопроводе, предохраняют парогенератор от перегрева и повышения давления пара. Для определения давления воды после насоса и давления пара после змеевика установлены манометры 7 и 12.Для слива воды из змеевика после работы установлен продувочный клапан 9. С помощью байпасного клапана 6 регулируется перепуск воды после насоса на вход в насос, при этом изменяется влажность пара на выходе из парогенератора. Для работы парогенератора на два выхода установлен паровой клапан 16. Пар из змеевика с помощью парового шланга ШП и насадка НСТ и НС (рис. 1) подводится к потребителю. В состав ПГУ входят четыре манометра МН1–МН4 (рис. 1) с помощью которых контролируется наличие давления газа в системе шкафа подготовки газа, а также теплоизолированный насадок, предназначенный для защиты рук от высокой температуры пара и цилиндрический и щелевой насадки.
150