
3258
.pdf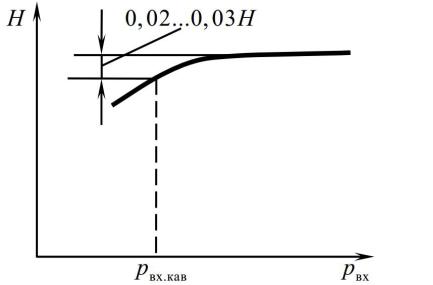
2) баки располагаются выше к головной части РН. Поскольку давление в баках ограничивается прочностью их конструкции, его повышением воспользоваться нельзя. Поэтому используются: 1) наддув баков; 2) установка шнековых или струйных преднасосов. Увеличение числа лопаток рабочего колеса приводит к уменьшению доли сил давления, приходящейся на каждую лопатку, т.е. к уменьшению проф Но при этом уменьшается проходное сечение колеса, что приводит к возрастанию скоростей при том же расходе, а следовательно, к возрастанию проф. Поэтому число лопаток выбирают в диапазоне 6…12. При большем числе лопаток некоторые из них выполняются укороченными. По кавитационным условиям оптимальными оказываются углы атаки i = +5 …+12 .
Рис. 2. Срывная характеристика центробежного насоса
Подводя итоги можно сделать вывод, что при работе системы подачи топлива ЖРД кавитация в насосах недопустима. Расчет срывных и кавитационных характеристик насосов и максимально допустимых скоростей вращения рабочих колес, а также подбор
70
конструктивных параметров позволяют предупредить возникновение кавитации.
Литература
1 Алпатов А.В. Лопаточные машины в жидкостных ракетных двигателях: учеб.пособие/ А.В. Алпатов.– СПб.: ВКА им. А.Ф. Можайского, 2010.–133с
2 Карелин В.Я. Износ лопастных гидравлических машин от кавитации и наносов, 1970 г, 184 с.
3 Пылаев Н.И., Эдель Ю.У. Кавитация в гидротурбинах, 1974.-
356.
УДК 621.454
ОКИСЛИТЕЛИ РАКЕТНОГО ТОПЛИВА
И. И. Исаков,ВГТУ, студент
А. В. Белокопытов, ВГТУ,студент Б. А. Спиридонов, ВГТУ, студент
Д.П. Шматов, ВГТУ, канд. техн. наук, доц., тел. +7(910)-349-6266
Современная реактивная техника является чрезвычайно сложной и дорогой, поэтому важнейшим требованием, предъявляемым к ней - это высокая надежность, долговечность и безопасность при эксплуатации. В основном это зависит от качества ракетных топлив. Наиболее широкое применение получили жидкостные реактивные двигатели (ЖРД), которые создают рабочую тягу за счет вытекания струн продуктов сгорания жидкого реактивного топлива (ЖРТ) - окислителя и горючего, имеющихся на борту летательного аппарата [1].
ЖРТ по способу применения в двигателях подразделяют на однокомпонентные и двухкомпонентные. Однокомпонентные ракетные топлива по химическому составу делят на мономолекулярные и смесевые. К мономолекулярным относят
71
вещества, в молекуле которых содержаться как горючие элементы, так и необходимый для горения кислород. Такими соединениями являются, например, сложные эфиры азотной кислоты и различных спиртов, тринитроглицерин С3Н5(ONO2) метилнитрат СН3ОNО2 и др. К однокомпонентным топливам относят и эндотермические соединения, выделяющие при своем распаде большое количество тепла и газообразных продуктов (например, гидразин N2На, пероксид водорода Н202 и др.).
Двухкомпонентные жидкие реактивные топлива, в которых каждый из компонентов подается в камеру сгорания раздельно, состоят из горючего и окислителя.
Ракетные окислители по химической природе делят на следующие: кислородные - жидкий кислород O2 и озон O3, пероксид водорода Н202; азотные - концентрированная азотная кислота HNO3, оксиды азота, тетранитрометан; фторные - жидкий фтор и кислородные соединения фтора; хлорные - жидкий хлор, хлорная кислота и оксиды хлора.
Ракетные горючие по химическому составу подразделяют на следующие: водородные - жидким водород; углеводородные; гидразинные - гидразин и его производные, например.диметилгидразин (СНЗ)2N-NН2; аминные - жидкий аммиак, амины; бороводородные - соединения типа боранов, например диборан В2Н6 и др.
Наряду с жидким кислородом в качестве окислителя широкое применение получила азотная кислота [2]. Особенностью структуры НNО3 является образование четырех связей азота с тремя атомами кислорода и пятой дополнительной, которая равномерно и динамично распределена между двумя атомами кислорода и азота. Кроме этого, атомы водорода от одной молекулы кислоты отщепляются и прицепляются к соседним молекулам, образуя непрочные, но чрезвычайно химически активные агрегаты. Из-за этого в азотной кислоте обязательно образуются разного рода примеси.
72
В ракетной технике используют два типа азотнокислотных окислителей: белую и красную дымящие азотные кислоты. Первая представляет собой техническую азотную кислоту с концентрацией НNО3 не менее 97,4 %, а вторая - смесь азотной кислоты с четырехокисью азота. Введение в азотную кислоту четырехокиси азота (красная дымящая кислота) улучшает ее свойства как окислителя ракетного топлива, так как содержит несколько больше активного кислорода для окисления горючего [3]. Азотная кислота легко взаимодействует с многими конструкционными металлами, и особенно с железом, медью и их сплавами. Образующиеся в результате коррозии соли загрязняют окислитель. Под действием HNO3 разрушаются средства ее хранения и транспортирования [4].
Кроме того, азотная кислота не удовлетворяет требованиям совместимости с конструкционными материалами - под нее специально приходится подбирать металл для баков, труб, камер ЖРД. Даже самые стойкие сорта нержавеющей стали медленно разрушаются концентрированной азотной кислотой.
Несмотря на коррозионную агрессивность и токсичность азотная кислота широко применяется в ракетной текинке из-за низкой стоимости, доступности и способности самовоспламеняться со многими горючими.
Плотность ее заметно больше, чем у жидкого кислорода, хо главное се достоинство по сравнению с жидким кислородом состоит в том, что она не выкипает, не требует теплоизоляции, может неограниченно долго храниться в подходящей таре. Для уменьшения коррозионной активности азотной кислоты в нее добавляют фтористоводородную кислоту. Всего 0,5% фтористоводородной кислоты уменьшают скорость коррозии нержавеющей стали в десять раз. Для того, чтобы вещества, которые попадают в камеру сгорания ЖРД, сжигались, добавляют гиперголики.
Гиперголическими веществами называются те, которые самовоспламеняются при контакте. Идеальный гиперголь для
73
азотной кислоты - гидразин N2H4, который представляет собой бесцветную, дымящую на воздухе жидкость, сильно гигроскопичную и хорошо растворяющуюся в воде, спиртах, аминах. Для сгорания гидразина, протекающего с большимгазовыделением, требуется сравнительно немного окислителя. Гидразин имеет относительно невысокую температуру горения, в результате чего потери тепла на диссоциацию продуктов его сгорания невелики. Высока реакционная способность гидразина при взаимодействии с окислителями.относительно высокая плотность -1020 кг/м3, малая молекулярная масса продуктов сгорания и практически неограниченная сырьевая база выгодно отличают гидразин среди других соединений, используемых в качестве горючего для ЖРД. Разложение гидразина происходит, как правило, с разрывом связи N - N и может протекать по следующим направлениям:
3H2H4 = 4NH3 + N2,
N2H4 = N2 + 2H2,
2N2H4 = NH3 + N2 + H2.
Существенными недостатками гидразина, ограничивающими его широкое применение, являются высокая температура замерзания (2 °С), относительно низкая термическая стабильность и высокая токсичность.
Лучшими низкотемпературными свойствами обладают алкилпроизводные гидразина, например, несимметричный диметилгидразин (НДМГ). НДМГ - бесцветная прозрачная жидкость с резким неприятным запахом, характерным для аминов. Температура кипения +63.1°С, кристаллизации -58°С. Хорошо смешивается с водой, нефтепродуктами, спиртами и многими органическими растворителями [5]. Легко самовоспламеняется с окислителями на основе азотной кислоты, что обеспечивает легкий запуск и стабильную работу двигателей в широком диапазоне изменения окружающих условий.
74
В настоящее время пара «азотная кислота - НДМГ» используется на ракетах-носителях «Протон», РН «Космос», РН «Циклон», РН «Днепр», РН «Титан»; в двигательных установках пилотируемых кораблей, орбитальных и межпланетных станций, а также в некоторых баллистических ракетах.
Литература
1.Братков А. А. Химмотология ракетных и реактивных топлив /А. А. Братков, Е. П. Серегин, А. Ф. Горенков; под. Ред. А. А. Браткова. – М.: Химия, 1987. – 304с.
2.Неорганическая химия: учеб. Пособие для хим. и химикотехнол. спец. вузов /Б. Д. Степин, А. А. Цветков. – М.: Высш. шк., 1994.-608 с.
3.Алешков М.Н. Физические основы ракетного оружия /М.Н. Алешков, И.И. Жуков.- М.: Воениздат, 1965. -464 с.
4.Зрелов В.Н., Серегин Е.П. Жидкие реактивные топлива /В.Н.Зрелов, Е.П.Серегин. - М.: Химия, 1975. -320 с.
5.Ушакова В.Г. О. Н. Шпигун, О.И. Старыгин. Особенности химических превращений НДМГ и его поведение в объектах окружающей среды / О.Н. Шпигун, О.И. Старыгин //Ползуновский вестник. - 2004.- Н94.-С. 81-87.
УДК 681.518.54
ПРОМЫШЛЕННАЯ УСТАНОВКА ДЛЯ ВЫДЕЛЕНИЯ ВОДОРОДА ИЗ СМЕСИ ГАЗОВ
В.А. Бакаев, КБХА, инженер, тел. (473) 237-44-40
Г.И. Скоморохов, ВГТУ, д-р техн. наук, проф., тел. (473) 2376-484
В работе приводится принципиальная схема энергетической установки для получения водорода из смеси газов. Для выделения водорода используется диффузионный фильтр новой конструкции с металлической мембраной на основе палладия.
75
Ресурсы ископаемого топлива, которые в наше время удовлетворяют до 85% мировой потребности в энергоресурсах, ограничены и не возобновляются. Главное направление глобальной энергетической стратегии на долгосрочную перспективу обозначается довольно отчетливо: все более широкая замена ископаемого топлива альтернативными, возобновляемыми, экологически чистыми источниками энергии, к которым принадлежит и водородная энергетика, отходом использования которой является обыкновенная вода.
Среди альтернативных экологически чистых топлив водород является универсальным энергоносителем. Водород перспективен для использования в ракетных двигателях, в двигателях внутреннего сгорания, для выработки электроэнергии в топливных элементах, для производства синтетических жидких топлив и др. В связи с этим возникает задача поиска и исследования технологии крупномасштабного получения водорода, характеризующиеся высокими энергетическими, экологическими и экономическими показателями.
Водород практически весь находится в виде соединений, поэтому для его получения применяют химические методы. Следует отметить следующие основные способы получения водорода [1].
1)Паровая каталитическая конверсия легких углеводородов с подводом тепла в трубчатых печах. Этим способом конвертируются
природный газ, сжиженные газы и бензиновые фракции с температурой кипения до 20000С.
2)Автотермическая каталитическая конверсия легких углеводородов. Этим способом перерабатываются природный, коксовый, и некоторые другие газы.
3)Высокотемпературная кислородная конверсия различных типов углеводородного сырья. Процесс представляет собой неполное окисление углеводородов с образованием СО и Н2. В качестве сырья могут использоваться любые углеводороды, начиная от метана и кончая высокосернистыми мазутами.
4)Кислородная или парокислородная газификация твердого топлива. Процесс осуществляется в газогенераторах с неподвижным или движущимся слоем мелкозернистого топлива (угля, торфа, сланца).
76
5)Термоконтактные методы разложения углеводородов для
получения водорода. Сущность методов заключается в том, что при температуре порядка 13000С на инертной насадке или при 9009500С на катализаторах протекает термическое разложение углеводородного сырья до углерода и водорода. Метод достаточно экономичен, однако является периодичным и широкого распространения не получил.
6)Электролиз воды. Это единственный промышленный способ получения водорода, не основанный на использовании топлива. Электролиз выгодно отличается от других методов получения водорода простотой и надежностью технологической схемы. Например, при электролизе водных растворов солей:
2NaCl + 2H2O → H2↑ + 2NaOH + Cl2.
В настоящее время в ОАО «КБХА» создана станция получения технического газообразного водорода, которая выполнена на базе существующего электролизного участка криогенного производства двумя стационарными установками СЭУ-40 производительностью 40 м3/ч каждая. В процессе эксплуатации станции получения электролизного водорода была выявлена высокая энергоемкость процесса и как следствие, высокая себестоимость выходного продукта, что обуславливает поиск новых способов получения водорода.
7) Окислительная конверсия метана плазмохимическим методом [2]. С целью снижения капитальных затрат и энергопотребления в технологическом процессе получения газообразного водорода был разработан плазмохимический реактор для разложения метана в водородной плазменной дуге и одновременным парциальным окислением продуктов реакции водяным паром. Конечным продуктом реакций является синтез-газ состоящий из Н2, С2Н2, СН4, СО, СО2, который затем может компримироваться для дальнейшего выделения газообразного водорода на металлических мембранах. При этом себестоимость получения газообразного водорода сокращается в 5-6 раз по отношению к другим методам.
8) Извлечение водорода как побочного продукта процессов нефтепереработки и нефтехимии. Во многих процессах
77
нефтепереработки и нефтехимии имеются отходящие газы со значительным содержанием водорода. В настоящее время уделяется серьезное внимание этому источнику водорода. В процессе каталитического реформинга образуется водород в количестве 0,7- 2,3 мас.% от исходного сырья.
К настоящему моменту в ОАО «КБХА» завершены работы по проектированию и изготовлению установки для получения синтезгаза плазмохимическим методом паровой конверсией водорода. Основным узлом установки является пароконверсионный плазмохимический реактор, включающий в себя двухструйный плазмотрон, камеру смешения метана и пара с потоком водорода и реактор, где происходит конверсия метана. В процессе экспериментальной отработки был обеспечен выход 200-220 нм3/ч синтез-газа, содержащего 60-65% водорода.
Особенностью получения синтез-газа на данной установке является то, что процесс парциального окисления проходит в смесительной камере плазмохимического реактора при температуре 1600-18000С и избыточных давлениях около 0,01-0,02 МПа, что позволяет выполнить его без присутствия катализаторов и значительно уменьшить сажеобразование.
Водород, получаемый промышленным способом, находится в составе газовых смесей содержащих такие газы как СО, СО2, N2. CH4. Для использования водорода в качестве ракетного топлива или в качестве топлива для энергетических установок необходима высокая чистота водорода. Известны различные способы выделения водорода из газовой смеси, основными из которых являются:
1.Адсорбционный [1]. Процесс очистки водорода методом короткоцикловой адсорбции основан на адсорбции цеолитами всех имеющихся в смеси газов (СО, СО2, СН4, Н2О, N2), кроме водорода.
2.Низкотемпературный (криогенный) способ. Процесс заключается в разделении жидкой смеси на компоненты, основанный на различной температуре кипения отдельных веществ,
входящих в состав смеси [3]. Процесс выделения проходит при температуре минус 190-2000С. Степень извлечения водорода составляет 80-98% [4].
3.Диффузионное выделение на мембранах. Практический интерес представляет выделение водорода на металлических и
78
полимерных мембранах. При разделении на полимерных мембранах достигается чистота фракции 90-96% [4].
Для выделения водорода из смеси газов в промышленных масштабах применение металлических мембран на основе палладия является наиболее целесообразно, так как не требуется энергоемких процессов.
Для исследования процесса разделения водорода от попутных газов, получаемых плазмохимическим методом разложения метана [2], разработана энергетическая установка для разделения газовых компонентов диффузионным фильтром (ДФ). Принципиальная схема экспериментальной установки представлена на рисунке.
Водород от баллонной рампы через редуктор КР3 поступает в коллектор смешения газов. Расход водорода измеряется дроссельной шайбой ДРН4. Азот через редуктор КР4 поступает так же в коллектор смешения газов. Из коллектора смешения газовая смесь, состоящая из водорода и азота поступает через отсечной клапан К5 в диффузионный фильтр. Давление на входе в диффузионный фильтр контролирует датчик давления ДД3 (МД60ТС).
Из коллектора смешения газовая смесь поступает в диффузионный фильтр, в котором происходит разделение газовой смеси. Температура в ДФ контролируется двумя поверхностными датчиками температуры ДТП1, ДТП2 (ТП033-01). Температура водорода на выходе из ДФ контролируется датчиком температуры ДТС4 (ТТ149).
Очищенный водород охлаждается в теплообменнике АТ2 до 25-500С и через клапан К4 подается на компрессор и затем поступает потребителю. Расход спектрально чистого водорода определяется ротаметром РМ1. Давление и температуру водорода после мембраны ДФ контролируют датчик давления ДД2 (МД-6ТС) и датчик температуры ДТС4 (ТТ149).
Отбор газа после мембраны на химический анализ осуществляется через вентиль ВН2.
Температура газовой смеси (N2, Н2) на выходе из ДФ контролируется датчиком температуры ДТС5 (ТТ149). Газовая смесь охлаждается в теплообменнике АТ1 до 25-500С и выбрасывается в атмосферу за пределами испытательного стенда. Расход газовой смеси определяется дроссельной шайбой ДРН1.
79