
3258
.pdf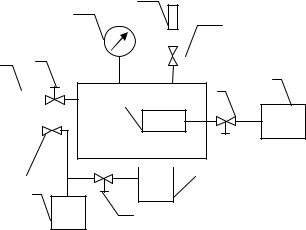
где к.т – поток пробного газа через контрольную течь, Вт.
11
10
1
13 8 9
3
2
|
|
|
|
|
|
|
|
|
|
|
|
|
|
|
|
|
|
|
|
|
|
|
|
|
|
|
|
|
|
|
|
|
|
|
|
|
|
|
|
|
|
|
|
|
|
|
|
|
|
|
|
|
|
|
|
|
|
|
|
|
|
|
|
|
|
|
|
|
|
|
|
|
|
|
|
|
|
|
|
|
|
|
|
|
|
|
|
|
|
|
|
|
|
|
|
|
7 |
|
|
|
|
|
|
|
|
|
|
|
|
|
4 |
|
|
|
|
|
|
|
|
|
|
|
|
6
5
1 – испытываемое изделие; 2, 5, 7, 9, 12 – вакуумные вентили; 3 – воздушно-гелиевый пульт; 4 – течеискатель;
6 – механический насос; 8 – паромасляной насос; 10 – датчик давления; 11 – ЭКТ; 13 – вакуумная камера
Рис. 4. Принципиальная схема испытаний на герметичность ВГС методом «вакуумирования»
Степень негерметичности объекта испытаний по контрольному газу определяется по формуле
|
|
|
|
− |
′ |
100 |
|
|
|
см |
|
кт |
|
|
|||
|
|
кт |
|
|
|
|
||
|
|
|
|
|
|
|
|
|
где кт – реакция |
течеискателя на поток гелия от контрольной течи, |
|||||||
|
= |
|
|
|
∙ |
мВ;
′- фон гелия после отключения контрольной течи, мВ;
–реакция течеискателя на поток гелия из течей объекта испытаний и фон гелия, мВ;
кт – поток гелия через контрольную течь, Вт;
– концентрация гелия в смеси, %.
При испытании на герметичность ВГС существенную роль в обеспечении качества и надежности испытаний играет
110

равномерность заполнения испытываемых полостей контрольным газом. Заполнение осуществляется следующими способами:
-раздельная подача гелия и воздуха (азота);
-подача смеси гелия и воздуха (азота).
Заполнение изделий без применения смесительных устройств рекомендуется проводить, когда:
-из-за конструктивных особенностей недопустимо откачивать внутреннюю полость изделия;
-изделие не имеет сложной внутренней поверхности и разветвленной системы трубопроводов, в связи с чем не требуется длительной выдержки, для образования равномерной смеси гелия с воздухом (азотом) по всему объему.
Раздельное заполнение изделий контрольным газом проводят с соблюдением рекомендаций:
-при заполнении полостей через штуцер, расположенный в верхней точке изделия, первым подается газ с меньшей молекулярной массой, например, гелий;
-при заполнении полостей через штуцер, расположенный в нижней точке изделия, первым подается газ с большей молекулярной массой, например, воздух (азот);
-давление гелия определяют по формуле
г = ∙( см ат),
где г – избыточное давление гелия, кгс/см2; см – избыточное давление контрольного газа, кгс/см2;
– концентрация гелия, %; ат – атмосферное давление, кгс/см2.
- после заполнения контрольным газом изделие выдерживают заправленным в течение времени, необходимого для образования равномерной смеси гелия с воздухом по всему объему.
Определение времени выдержки до образования равномерной концентрации гелия с воздухом (азотом) по всему объему изделия проводят технологическим путем, измеряя концентрации гелия на входе в изделие и в наиболее удаленной от входа точке.
Процесс образования равномерной смеси считается законченным, если значения концентраций гелия во всех точках измерения отличаются друг от друга и от заданной по КД не более, чем на 10%. Допускается и более 10%, если это оговорено в КД.
111
В целях сокращения времени образования равномерной концентрации гелия в контрольном газе рекомендуется изделие заполнять следующим образом:
-ступенями (порциями) по схеме: гелий – воздух, гелий – воздух и т.д;
-продувкой внутренней полости изделия гелием до необходимой концентрации;
-поочередным наддувом изделия избыточным давлением гелия, выдержкой в течение установленного времени и сбросом давления.
При замещении воздуха в изделии на пробный газ поочередным наддувом и сбросом давления гелия количество заполнений изделия гелием должно быть не менее величины «П», которая определяется по формуле
П |
|
2 −lg(100 − ) |
|
|
|
+98) −1,9912 |
|
= lg( |
изб |
||
|
|
|
где П – количество заполнений изделия пробным газом давлением изб для создания в нем концентрации ;
– концентрация гелия, которой необходимо заполнить изделие, %;
изб – избыточное давление, которым возможно заполнить изделие при замещении воздуха на контрольный газ, кПа.
Заполнение контрольным газом изделий, допускающих откачку внутренних полостей до давления 0,665-1,33 кПа, можно проводить готовой смесью или чистым гелием. При этом измерение концентрации гелия в изделии можно не проводить. Если изделие заполняется чистым гелием, то в расчетах значения негерметичности принимать концентрацию гелия равной 90%.
Фактически, в производственных цехах заполнение гелием агрегатов и их составных элементов проводится продувкой внутренних полостей гелием до необходимой концентрации, поочередным наддувом полостей избыточным давлением гелия и сбросом его или вакуумированием испытываемой полости с последующим заполнением ее приготовленной воздушно-гелиевой смесью.
После полной сборки двигатель подвергают испытаниям на герметичность методом «мундштука»: необходимо еще раз
112
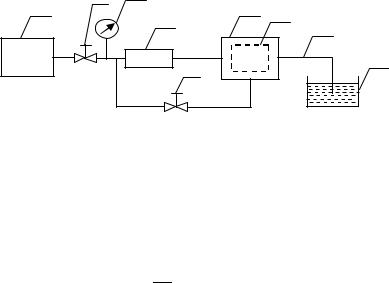
проверить герметичность всех агрегатов и места их стыковки. Не становится исключением и мембранный клапан.
Метод «мундштука» относится к числу самых простых и распространенных методов испытаний на герметичность уплотнительных элементов агрегатов, мембран и диафрагм. Недостатком этого метода является зависимость чувствительности испытаний от объема накопления, глубины погружения отводной трубки (мундштука) в жидкость и его диаметра, типа жидкости, изменения атмосферного давления и температуры окружающей среды.
Принципиальная схема контроля герметичности изделий методом «мундштука» приведена на рис. 5.
2 3
1 |
5 |
4 6
7
8
9
1 – пневмопульт; 2, 9 – вентиль; 3 – манометр 4 – испытываемое изделие; 5 – объем накопления;
6 – наполнитель (если применяется); 7 – отводная трубка; 8 - емкость с жидкостью
Рис.5.Принципиальная схема контроля герметичности изделий методом «мундштука»:
Чувствительность |
контроля |
герметичности |
методом |
||||||
«мундштука» определяется выражением |
|
||||||||
д = 3 |
|
1,33∙10 |
б |
∆ |
+ |
|
|
+1,33∙10 ∆ б +10 |
|
|
|
|
где – объем полости, заключенной между концом мундштука
иконтролируемым элементом (объем накопления), м3;
–время регистрации спада давления, с;
б– барометрическое давление, мм рт.ст.;
–диаметр выходного отверстия мундштука, м;
∆– изменение температуры изделия за время испытаний, К;
–температура в помещении при испытаниях, К;
113

– коэффициент поверхностного натяжения жидкости, в которую опущен мундштук, Н/м;
- глубина погружения мундштука в жидкость, м;
– плотность жидкости, кг/м3;
д– чувствительность испытаний, м3·Па/с.
Время испытаний находится в диапазоне от 3 до 10 мин. Считая, что за это время барометрическое давление и температура
практически не изменяютсяд , принимают ∆ б = 0 и ∆ = 0, тогда |
|
= 3 |
+10 |
Таким образом, чувствительность испытаний зависит в основном от объема накопления, коэффициента поверхностного натяжения жидкости и глубины погружения мундштука в жидкость.
В таблице приведены коэффициенты поверхностного натяжения и плотности различных жидкостей.
Свойства некоторых жидкостей
Жидкость |
, дин/см |
, кг/м3 |
Вода |
73,1 |
1,0 |
Керосин |
24 |
0,82 |
Спирт |
22 |
0,789 |
Данные, приведенные в таблице, показывают, что повышение чувствительности испытаний можно достигнуть, например, используя вместо воды спирт или керосин. Формула Н показывает, что определяющее влияние оказывает объем накопления. Поэтому уменьшение объема накопления или его исключение приводит к существенному повышению чувствительности испытаний. С этой целью внутрь объема накопления устанавливают наполнители, подают газ до появления пузырьков на срезе мундштука.
Диаметр отводной трубки рекомендуется принимать 4–6 мм, длину – не более 600 мм, глубину погружения среза – не более 10 мм.
При этих условиях время выдержки до появления первых пузырьков определяется по формуле
= 1000 ,
где – время выдержки до появления первых пузырьков, с;
114
–объем накопления, м3;
–допустимая величина утечки, л·мкм рт.ст/с.
Объем накопления состоит из свободной полости испытываемого агрегата за уплотнительным элементом и технологической оснастки. При равенстве составляющих объема, необходимо ограничить вторую его часть.
После проведения испытаний результаты анализируются, и делается заключение о степени их соответствия установленным нормам, а так же о пригодности изделия для дальнейшей эксплуатации.
В данной работе была рассмотрена методика испытаний на герметичность на примере клапана пуска мембранного типа, изложены основные стадии и методы испытаний, наиболее подходящие для данного агрегата. Помимо указанных методов, так же существуют и другие, реализуемые на предприятии. По возможности рекомендуется применять самые простые из них и легко осуществимые, но окончательный выбор зависит от специфики конкретного агрегата, сложности его конструкции и допустимой степени негерметичности.
УДК 621.455.4
АНАЛИЗ ЛАБОРАТОРНЫХ СТЕНДОВ, ИСПОЛЬЗУЮЩИХСЯ ДЛЯ ИСПЫТАНИЙ ЭРД
С.О. Ломтев, студент группы РД-111, тел.+7-(909)-211-9730
Криовакуумная установка или вакуумная камера предназначена для наземной экспериментальной отработки ЭРД. Вакуумная камера состоит из конструктивных зон:
1)Основная зона, где производятся испытания двигателей.
2)Предкамерная зона, в которой располагается тягоизмерительное устройство(тягомер).
Например, КВУ-90, объемом вакуумной камеры 90 м3 имеет производительность высоковакуумной ступени откачки 73 м3/ с, что позволяет испытывать двигатели мощностью до 6 кВт. В конструкции вакуумной камеры предусмотрена возможность наращивания производительности криогенной системы откачки
115

(путем установки дополнительных насосов) до 200 м3/с, что делает возможным проведение испытаний холловских ЭРД мощностью до
15…20 кВт.
Рис.1. Вакуумная камера
Стоит отметить, что основная и предкамерная зона в вакуумной камере разделены - вакуумным затвором. Рабочим телом в КВУ может являться ксенон, аргон и азот, но чаще всего используется ксенон, по причине своей высокой эффективности применения в ЭРД.[1]
Что же касается испытаний высокочастотных ионных двигателей, то лаборатория ВЧИД, расположенная в МАИ,содержит три экспериментальных стенда: 2ИУ-2В, 2ИУ-3В,У-2В. Характеристика стендов представлена в таблице[2].
Тягоизмерительное устройство (ТИУ) работает по принципу автоматической компенсации усилия, действующего на подвижную платформу с установленным на ней двигателем. Компенсация этого усилия осуществляется с помощью следящей системы с жесткой отрицательной обратной связью. Выходной сигнал системы компенсации усилия служит выходным сигналом ТИУ, поступающим на регистрирующие приборы. В конструкции ТИУ КВУ-90 используется электромагнитная система компенсации усилия, обеспечивающая практическую линейность его градуировочных характеристик.
116
Характеристики испытательных стендов
Наименован |
|
|
|
Объем |
Производительность и |
||||
Назначение |
вакуумной |
характеристики средств |
|||||||
ие стенда |
|||||||||
|
|
|
камеры |
откачки |
|
|
|||
|
|
|
|
|
|
||||
|
Испытания |
|
|
18600 |
л/c |
|
по |
||
|
ВЧИД |
|
|
|
ксенону(криосорбционн |
||||
|
мощностью |
|
|
ый |
|
|
и |
||
2ИУ-3В |
1.5…4 кВт |
|
2 м3 |
турбомолекулярные |
|
||||
|
|
|
|
|
насосы). |
Динамический |
|||
|
|
|
|
|
вакуум |
(1…2) |
x |
10-5 |
|
|
|
|
|
|
мм.рт.ст. при расходе |
||||
|
|
|
|
|
1.5 мг/c |
|
|
|
|
|
Зондовые |
и |
|
|
|
|
|
||
|
другие |
|
|
|
|
|
|
|
|
|
измерения |
в |
|
8400 л/спо |
ксенону |
||||
|
плазме |
|
ВЧ |
|
(турбомолекулярные |
||||
2ИУ-3В |
разряда |
|
0.3 м3 |
средства |
откачки). |
||||
|
источников |
|
|
Динамический |
вакуум |
||||
|
ионов |
|
с |
|
(1…2) x 10-5 мм.рт.ст. |
||||
|
мощностью |
|
|
при расходе 0.65 мг/c |
|||||
|
пучка |
ионов до |
|
|
|
|
|
||
|
0.7 кВт |
|
|
|
|
|
|
||
|
Испытания |
|
20 м3 |
До 230 тыс. л/c( |
|||||
|
ВЧИД |
|
|
подведенная |
крионасосы |
|
и |
||
|
мощностью |
5-35 |
электрическ |
турбомолекулярные |
|
||||
|
кВт, диагностика |
ая мощность |
насосы). |
Динамический |
|||||
У2В |
электромагнитно |
свыше 300 |
вакуум |
(1…2) |
x |
10-5 |
|||
|
го |
излучения |
кВт, |
мм.рт.ст. при расходе |
|||||
|
двигателей |
от 1 |
оснащен |
15 мг/c |
|
|
|
||
|
МГц до 20 ГГц |
безэховой |
|
|
|
|
|||
|
|
|
|
камерой |
|
|
|
|
Вконструкции прибора предусмотрено градуировочное
устройство, позволяющее дистанционно нагружать подвеску усилиями от мерных грузов в процессе работы ТИУ по команде рис.2[1].
117
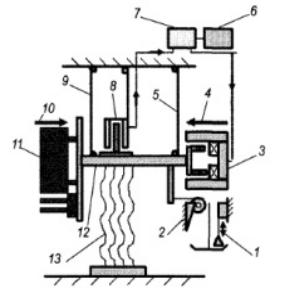
1-мерный груз,2-градуировочное устройство,3-система компенсации,4-усилие компенсации,5-задний подвес, 6-регистрирующий блок,7-блок усилителя преобразователя,8- емкостной датчик,9-передний подвес,10-тяга ЭРД,11-ЭРД,12- подвижная платформа,13-электрические и газовые гибкие подводы Рис.2. Принципиальная схема ТИУ компенсационного типа
В результате данного анализа можно сделать вывод о том, что КВУ – конструкция, позволяющая тестировать ЭРД различной мощности, диагностировать электромагнитное излучение, проводить зондовые и другие измерения в плазме.
Литература
1.Горшков О.А.Холловские и ионные плазменные двигатели для космических аппаратов, 2008 г.-280с.
2. Х.В. Лёб, Г.А. Попов, В.А. Обухов. Лаборатория высокочастотных двигателей Московского авиационного института
– новая форма Российско-Германского сотрудничества. Электронный журнал «Труды МАИ». Выпуск № 60,2012г.
118
Научное издание
РАКЕТНО-КОСМИЧЕСКАЯ ТЕХНИКА И ТЕХНОЛОГИЯ 2015
Тезисы докладов Российской научно-технической конференции,
посвященной 50-летию первого запуска РН «Протон» 16 июля 1965 года
(г. Воронеж, 23-24 апреля 2015 г)
В авторской редакции
Компьютерный набор С.О. Ломтева
Подписано к изданию 01.12.2015. Объем данных 3,6 Мб.
ФГБОУ ВО «Воронежский государственный технический университет»
394026 Воронеж, Московский просп., 14
119