
3042
.pdfпокрытия с минимальным припуском на механическую обработку, широкого применения при восстановлении деталей он не получил из-за ряда недостатков. Процесс напыления с оплавлением является трудоемким и по производительности уступает процессам получения покрытий наплавкой и электролитическими способами. Применение дорогих самофлюсующихся порошков повышает себестоимость восстановления. Нагрев покрытия и детали при оплавлении достигает 1100 °С, что выше температур фазовых превращений, и все недостатки, характерные для наплавки, присущи и этому способу.
Оплавление напыленных поверхностей крупногабаритных деталей сложной формы (коленчатые валы) из-за неравномерности нагрева отдельных частей не позволяет получать качественных покрытий: образуются трещины, отслоения.
3.3. Газопламенное напыление
Газопламенное напыление осуществляется за счет теплоты, образуемой в результате сгорания различных горючих газов (ацетилена, пропан-бутана, и др.) в среде кислорода.
В зависимости от применяемого материала газопламенное напыление подразделяют на два вида: напыление проволокой (прутком) и порошковое напыление. В первом случае пруток или проволока с помощью механизма подачи проволоки направляются через центральное отверстие горелки в высокотемпературную зону пламени, где расплавляются, распыляются сжатым воздухом и переносятся на поверхность детали.
Для восстановления деталей предпочтительное применение получило напыление порошками, которые позволяют в более широких пределах по сравнению с проволоками регулировать состав наносимых покрытий, что способствует повышению прочности сцеплений с основой.
В зависимости от места подвода порошка в горелку и его транспортирования в зону пламени газопорошковое напыление подразделяют на два способа.
101

1. Порошок из питателя (рис. 3.3) поступает в центральный канал горелки, захватывается транспортирующим газом и подается в факел пламени, струей которого оплавляется и направляется на поверхность детали, образуя слой покрытия.
2. Порошок из бункера (рис. 3.4) подается с внешней стороны мундштука в зону пламени, где его частицы оплавляются и направляются газовым потоком на поверхность напыляемой детали.
Рис. 3.3. Схема газопламенного |
Рис. 3.4. Схема напыления с |
напыления транспортирующим |
внешним вводом порошка в |
газом: 1 – сопло; 2 – пламя; |
зону пламени: 1 – пламя; |
3 – покрытие; 4 - напыляемая |
2 – трубка, подводящая |
деталь; 5 - кислород и горючий |
порошок; 3 – мундштук; |
газ; 6 – транспортирующий газ; |
4 - наконечник |
7 – напыляемый порошок |
|
Применение в первом способе транспортирующего газа, обычно инертного, для подачи порошка позволяет уменьшить его окисление. Второй способ также имеет этот недостаток, но его оборудование проще и облегчает выбор оптимального режима.
При восстановлении деталей для получения износостойких покрытий в основном применяются порошковые сплавы системы Ni-В-Сг-Si, а для напыления подслоев - экзотермические сплавы. Для напыления стальных и чугунных деталей, работающих в условиях трения, применяют также стальные проволоки с содержанием 0,3 - 0,8 % С, хромистые с содержанием 13 % Сг, аустенитные, хромоникелевые и др.
102
При газопламенном и плазменном напылении технологические операции, касающиеся подготовки детали и порошка, аналогичны и выполняются на одном и том же оборудовании. Наиболее качественные покрытия получаются при первоначальном напылении подслоя термореагирующим порошком толщиной 0,05 - 0,15 мм, а затем основного слоя износостойким порошковым сплавом толщиной 2 мм. Подслой и основной слой наносят при одних и тех же режимах напыления.
Мощность пламени выбирают в зависимости от размеров детали. При напылении применяют восстановительное или науглероживающее пламя. Перед началом напыления деталь подогревают до температуры 50 - 100 °С. В процессе напыления необходимо следить, чтобы поверхность напыляемой детали не нагревалась выше 250 °С.
Процесс газопламенного напыления с последующим оплавлением практически выполняется так же, как и аналогичный плазменный процесс.
Напыление с одновременным оплавлением возможно лишь газовым пламенем.
Наплавку напылением с одновременным оплавлением рекомендуется выполнять в такой последовательности: подогреть всю деталь до температуры 250 - 300 °С; на восстанавливаемые поверхности для их защиты от последующего окисления напылить слои толщиной 0,2 - 0,3 мм; напыленный участок поверхности нагреть до состояния «запотевания», что характерно для процесса оплавления; на предварительно оплавленный слой нанести новый, доводя его до состояния оплавления.
Последовательность наплавки других участков зависит от формы детали и расположения на ней изношенных поверхностей. Важно, чтобы в процессе оплавления не допустить перегрева напыленного слоя до состояния жидкой ванны, а после оплавления обеспечить медленное охлаждение детали (в песке, асбесте, печи). Для восстановления деталей этим способом наиболее рационально применять порошковые сплавы ПГ-
103
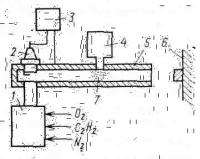
10Н-01, ПГ-10Н-03, ПГ-СР3, ПГ-СР4. Толщина наплавленного слоя до 3 мм.
Из описанной технологии видно, что процесс трудноконтролируемый, поэтому наплавку, как правило, ведут вручную, и качество получения покрытий в значительной мере зависит от квалификации сварщика, его визуального контроля. Совмещение операций при этом способе позволяет сократить время на восстановление детали. Он применим, главным образом, для деталей небольших размеров в условиях единичного и мелкосерийного ремонтного производства. Таким способом восстанавливают, например, кулачковые валы топливных насосов тракторных двигателей. Этот способ отличается высоким качеством получения покрытий; припуск на механическую обработку не превышает 0,5 - 0,7 мм, прочность сцепления 300 - 400 МПа, вполне достаточная для деталей, работающих в условиях знакопеременных нагрузок.
3.4. Детонационное напыление
Отличительная особенность детонационного напыления - циклический характер подачи порошка на поверхность обрабатываемой детали со скоростью, превышающей скорость звука. Циклический процесс напыления получают с помощью детонационных установок, принципиальная схема которых представлена на рис. 3.5.
Рис. 3.5. Схема установки для детонационного напыления
104
В общем виде детонационные установки состоят из блока 4 подачи напыляющего порошка, включающего порошковый питатель и дозирующее устройство; блока 1, служащего для образования требуемых газовых смесей и заполнения ими ствола детонационной установки с заданной скоростью; блока поджига 3 и воспламенителя 2, предназначенных для инициирования взрыва рабочей смеси; ствола 5, представляющего собой трубу диаметром 20 - 50 мм, длиной 1 - 2,5 м и предназначенного для направленного распространения взрывной волны в сторонуоткрытого конца ствола.
Принцип действия установки состоит в следующем. Из блока 1 газовая смесь подается в ствол 5. Одновременно из порошкового питателя через дозирующее устройство (блок 4) заданными порциями вдувают газом - азотом или воздухом - мелкодисперсный порошок в газовую смесь непосредственно перед ее зажиганием, затем воспламенителем 2 поджигают газовую смесь. В результате воспламенения и перемещения по каналу горючей смеси происходит ее взрыв с выделением значительного количества теплоты и образованием детонационной волны, которая ускоряет и переносит через ствол на поверхность детали 6 напыляемые частицы 7 со скоростью, определяемой геометрией ствола и составом газа.
3.4.1. Основы процесса формирования покрытия
Процесс формирования покрытий детонационным напылением сложный и недостаточно изучен. Во многом он сходен с процессом плазменного напыления. Сходство заключается в том, что сцепление частиц с подложкой и между собой может происходить в расплавленном, оплавленном и твердом состояниях. Прочность сцепления обеспечивается, главным образом, за счет напыления расплавленными и оплавленными частицами, которые растекаются и кристаллизуются на поверхности подложки за счет химического взаимодействия. В то же время детонационный процесс напыления в отличие от непрерывного
105
плазменного является цикличным, сообщающим частицам порошка более высокие скорости, что определяет особенности механизма формирования покрытий.
При детонационном напылении скорость частиц в отличие от плазменного напыления (100 - 200 м/с) достигает 400 - 1000 м/с. Поэтому кроме термической активации, существенное влияние на механизм и кинетику формирования напыленных слоев оказывает пластическая деформация в зоне соударения частиц и подложки. Однако основной вклад в формирование покрытий при напылении вносит термическая активация. Опыт применения различных способов напыления, в том числе детонационного, показывает, что для получения удовлетворительного сцепления частиц порошка с основой необходимо, чтобы их значительная часть транспортировалась на подложку в расплавленном или оплавленном состоянии. Экспериментальные исследования по процессу формирования покрытий детонационным напылением показывают, что состояние частиц, находящихся в двухфазном потоке, неоднородно. В начале и середине потока они находятся в расплавленном или оплавленном состоянии и температура в контакте с подложкой достигает температуры их плавления. При этом за счет теплоты, выделяемой при ударе о подложку частиц, имеющих скорость 400 м/с, температура в зоне контакта повышается примерно на
100 °С.
При напылении порошковыми материалами с температурой плавления, превышающей температуру плавления основного металла, происходит подплавление последнего. Так, например, при нанесении покрытий из оксида алюминия Аl2О3 и порошковыми твердыми сплавами типа ВК на коррозионностойкие стали последние подплавляются и перемешиваются с напыляемыми расплавленными частицами порошка, повышая тем самым прочность сцепления. Повышению адгезии, как и при других способах газотермического напыления, способствует предварительная дробеструйная обработка напыляемой
106
поверхности. В этом случае возможно получать прочные связи между напыляемым материалом и подложкой, имеющей твердость выше НRС 60. При напылении первого слоя возможно возникновение пор. При напылении второго слоя частицы порошка деформируют и уплотняют кристаллизующийся первый слой, что способствует устранению или уменьшению пористости. Это явление характерно для детонационного напыления и называется эффектом горячего ударного прессования.
Более крупные частицы из конца (хвоста) менее концентрированного потока обладают меньшей скоростью и наносятся на поверхность подложки чаще всего в нерасплавленном виде. При формировании покрытия такие частицы играют двоякую роль: полезную - удаляют дефектные участки ранее нанесенного покрытия, повышая его плотность и физикомеханические свойства; вредную - при значительном повышении кинетической энергии крупных частиц в покрытии могут появиться трещины и даже полное его отслоение. Эти явления можно регулировать, изменяя режим скорострельности установки и грануляцию напыляемого порошка.
3.4.2. Влияние параметров процесса на характер формирования покрытия
С точки зрения применяемых материалов и оборудования процесс детонационного напыления весьма простой. Основными факторами, определяющими характер детонационного напыления, являются газовая смесь, порошки, ствол установки.
Однако использование этих факторов в технологическом процессе напыления связано с изменением и управлением ряда характерных для каждого из них параметров. Для газовой смеси это состав газовой смеси; доза газовой смеси за один выстрел; состав газовой смеси в стволе между выстрелами.
Для порошка - химический состав порошка; грануляция напыляемого порошка; расположение порошка в стволе в момент поджига смеси; распределение частиц по размерам. Ствол
107

характеризуется геометрическими параметрами: диаметром и длиной.
В свою очередь, перечисленные параметры порождают другие параметры, характеризующие конечное состояние процесса: концентрация, температура и скорость частиц; химический состав среды; температура поверхности подложки.
Таким образом, технологический процесс детонационного напыления является сложным, и качество формирования покрытий зависит от совокупности многочисленных параметров, их поддержания в оптимальных пределах. Рекомендуемые режимы детонационного напыления для некоторых материалов представлены в табл. 3.2.
Таблица 3.2
Режимы нанесения детонационных покрытий
Материал |
О |
Глубиназагрузкипорошка, мм |
Дистанция напыления, мм |
Навескапорошка, мг |
Грануляция, мкм |
Длинаствола, м |
Диаметр ствола, мм |
|
2 |
|
|
|
|
|
|
|
Н |
|
|
|
|
|
|
|
2 |
|
|
|
|
|
|
|
С/ |
|
|
|
|
|
|
|
2 |
|
|
|
|
|
|
|
|
|
|
|
|
|
|
Аl2О3 |
2,5 |
750 |
150 |
50 |
20-40 |
2 |
20 |
WС+Со |
1,2 |
300 |
150 |
200 |
1-5 |
1,6 |
16 |
Сr2С3+NiCr |
1,2 |
300 |
100 |
200 |
40-50 |
2 |
20 |
В серийном производстве поддержание оптимальных режимов многопараметрического процесса возможно при условии работы установки в автоматическом режиме. Автоматическая детонационная установка имеет систему электроуправления детонационным оборудованием, состоящую из блоков управления, определяющих последовательность технологических операций и безопасность работы оператора.
При детонационном напылении можно получать покрытия из любых материалов, тугоплавких соединений, оксидов и др. Для получения износостойких покрытий с целью восстановления деталей применяют оксид алюминия Аl2О3, самофлюсующиеся сплавы ПГ-СР, СНГН, ВСНГН (65 % WС и 35 % СНГН). Для повышения износостойкости используют кар-
108
биды вольфрама WС, титана ТiС, хрома Сг2С3, борид хрома СгВ2 с добавками 8 - 20 % Ni или Со.
При детонационном напылении практически можно получить слои значительной толщины, но наибольшей прочностью сцепления обладают напыленные покрытия толщиной 0,2 - 0,4 мм (130 - 160 МПа). Поэтому наиболее рационально восстанавливать детали с небольшими износами. Скорострельность детонационного напыления составляет 1 - 5 выстрелов в секунду. Толщина покрытия в центре металлизационного пятна, наносимого за один выстрел, зависит от дозы порошка, подаваемого в ствол, и обычно составляет 8 - 20 мкм при площади покрытия 4 - 6 см2. При напылении самофлюсующимися сплавами обычно применяют порошки с диаметром частиц 7 - 70 мкм. Шероховатость после нанесения детонационных покрытий составляет, как правило, Rа = 3 - 4 мкм.
Производительность детонационного напыления ниже плазменного. Повышение производительности связывают с дальнейшим совершенствованием процесса детонационного напыления и его оборудования. Применение диаметра ствола свыше 25 мм влечет за собой снижение качества формирования покрытий, а использование диаметра ствола свыше 50 мм не рекомендуется по соображениям техники безопасности.
За счет уменьшения длины ствола, а следовательно, сокращения времени его заполнения рабочей смесью можно повысить скорострельность. Однако сокращение времени заполнения ствола и уменьшение его длины (до 400 мм) возможно при использовании легкоплавких металлических порошков. Для получения качественных покрытий напылением более тугоплавкими сплавами требуется длина ствола 2000 мм.
За счет применения многоствольных установок производительность можно повысить в несколько раз. В то же время из-за технических трудностей, связанных с управлением сразу несколькими стволами, эти установки пока что не нашли практического применения.
109

Детонационное напыление применяют для упрочнения различных видов инструмента, штампов, коленчатых валов и блоков цилиндров двигателей. Для восстановления изношенных деталей детонационное напыление пока применяют ограниченно, главным образом для нанесения покрытий на посадочные места под подшипники. Отдельные исследования по восстановлению коленчатых валов автотракторных двигателей пока не дали желаемых результатов. В то же время испытания ряда упрочненных и восстановленных деталей в условиях эксплуатации, а также опыт зарубежных фирм показывают, что более широкое внедрение детонационного напыления в производство позволит получить значительный техникоэкономический эффект.
3.5. Дуговое напыление
Сущность процесса дугового напыления заключается в том, что подающим механизмом 2 через наконечник 3 непрерывно подаются под углом две изолированные, находящиеся под напряжением проволоки 7, при соприкосновении которых возникает электрическая дуга (рис. 3.6). Расплавленный в ней электродный металл распыляется струей сжатого воздуха, подводимого под давлением 0,4 - 0,6 МПа через сопло 4 в зону дуги, ускоряется и направляется на поверхность детали 5, образуя напыленный слой.
Рис. 3.6. Схема дугового напыления
110