
3011
.pdf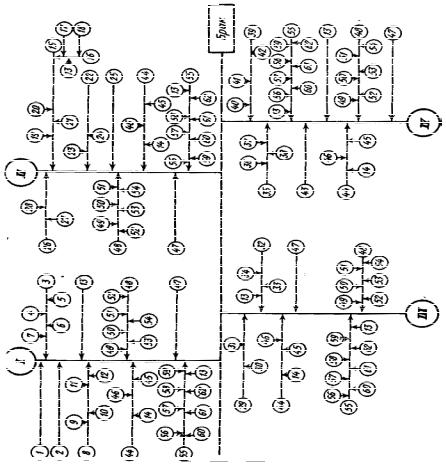
Рис. 9.3. Причинно-следственная диаграмма для анализа дефектов СБИС: Большие «кости» причинных факторов: I — этап проектирования и изготовления фотошаблонов; II — этап переноса, совмещения и проявления рисунков фотошаблонов на подложки СБИС; III — этап 1-й и 2-й термообработок; IV —
этап травления топологии и удаления фоторезиста маски
91
Продолжение подписи под рис. 9.3:
Средние и малые «кости» причинных факторов на рис. 9.3: 1 — ошибки в техническом задании ТЗ); 2 — невнимательность проектировщика; 3 — сбои в работе оборудования; 4 — сбои в работе генератора изображения; 5 — искажение объектива; 6 — сбои координатного стола фотоповторителя; 7 — сбои в работе ЭВС; 8 — низкое качество фотопластин; 9 — скрытые дефекты в стекле; 10 — некачественный фотоэмульсионный слой; 11 — несоответствие контрастности, разрешающей способности и т. д. фотопластин техническому условию (ТУ); 12 — нарушение условий хранения, транспортировки и т. д. фото пластин; 13 — недостаточная производственная чистота; 14 — погрешность контрольно-измерительного оборудования; 15 — снижение качества фотошаблонов в процессе эксплуатации; 16 — загрязнение фотошаблонов; 17 — осколки кремниевых пластин; 18 — загрязнение используемыми химическими реактивами; 19 — износ фотошаблонов; 20 — повреждение маскирующего слоя при отмывке фотошаблонов; 21 — проявление заложенных скрытых дефектов фотошаблонов; 22
— погрешности контактной фотолитографии; 23 — недостаточный зазор при совмещении; 24 — слишком плотный контакт; 25 — пропущенный брак фотошаблонов; 26 — нарушение режимов проявления и экспонирования; 27 — переэкспонирование; 28 — перепроявление; 29 — несоблюдение режимов термообработок; 30 — повышенная температура 2-й сушки (расплывание фоторезиста); 31 — превышение времени сушки (растрескивание и т. д.); 32 — загрязнение подложек;
33 — попадание на подложки окалины из оборудования для сушки; 34 — несоблюдение оператором технологических норм; 35 — нарушение технологических режимов травления и удаления фоторезиста, 36 — перетравление; 37 — несоблюдение концентрации травителя; 38 — износ оборудования; 39 — ошибки технологов и операторов; 40 — ошибка в выборе методов травления и удаления фоторезиста;
92
41 — ошибка в выборе травителя; 42 — ошибка в выборе режимов; 43 — проявление скрытых дефектов, заложенных на предыдущих операциях; 44 — контроль, 45 — погрешности оператора; 46 — погрешности методик контроля; 47 — случайные факторы; 48 — уровень профессионализма обслуживающего персонала; 49 — обучение и практика, 50 — работает постоянно или временно; 51 — уровень мастерства; 52
—стаж работы, 53 - одежда; 54 — личные достижения; 55 — подготовка рабочего места; 56 — уборка, 57 — индикация безопасности; 58 — вентиляция; 59 — шум; 60 — освещение; 61
—температура, 62 — уровень дизайна.
3.Разбить весь процесс жизненного цикла изделия на основные этапы, влияющие на появление групп дефектов А и В.
4.Построить причинно-следственную диаграмму выбранных групп дефектов.
5.Рассортировать причины на устранимые, трудноустранимые и неустранимые.
6.Подготовить и реализовать план мероприятий по исключению устранимых и уменьшению влияния трудноустранимых причин.
7.Собрать данные (за определенный срок после выполнения плана мероприятия), имеющие отношение к браку изделий; выявить количество дефектов, отнесенных ранее к группам А и В подсчитать сумму потерь, соответствующую каждому из этих видов дефектов.
8.Построить вновь диаграмму Парето и проверить эффективность проведенных улучшений.
Для примера можно рассмотреть процесс фотолитографии, влияющий, как видно из рис. 8.1, в большей степени, чем другие процессы изготовления кристалла, на дефектность ИС.
В то же время, как показывает отечественный и зарубежный опыт, основными видами дефектов в результате этого процесса являются систематические дефекты
93
(отклонения от заданного топологического рисунка), дефекты совмещения, ошибки топологии (пропуск на фотошаблоне элементов и т. п.) и случайные дефекты (выступы, островки, разрывы, пробелы, царапины, грязь, твердые частицы и т. п.).
Основными и сравнительно автономными этапами фотолитографии, которые в свою очередь могут влиять на указанные дефекты, являются проектирование и изготовление фотошаблонов, перенос, совмещение и проявление рисунков шаблона на подложку СБИС, первая и вторая термообработки, удаление фоторезиста маски. Причинно-следственная диаграмма зависимости указанных дефектов СБИС и причин, соответствующих этапам фотолитографии, приведена на рис. 9.3. Аналогичные причинно-следственные диаграммы могут быть построены отдельно для каждого вида дефекта.
На рис. 9.4 с использованием данных рис.9.3 построена причинно-следственная диаграмма для дефектов отклонений от заданного топологического рисунка.
Номера больших, средних и малых «костей» причинных факторов на рис. 9.4 аналогичны номерам, указанным на рис. 9.3.
94
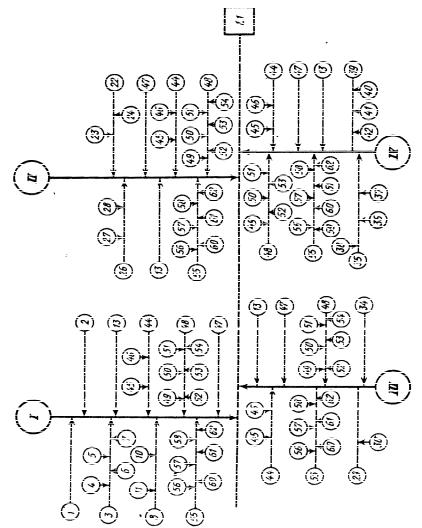
Рис. 9.4. Причинно-следственная диаграмма для анализа отклонений от заданного топологического рисунка: 1.1 – дефекты в виде отклонений от заданного топологического
рисунка
95
10. ДИАГРАММА РАЗБРОСА
Диаграмма разброса применяется для исследования зависимости (корреляции) между двумя видами данных. Поэтому диаграмму разброса часто называют полем корреляции. Диаграмма разброса используется также для выявления причинно-следственных связей показателей качества и влияющих факторов при анализе причинноследственной диаграммы.
Так, например, с помощью диаграммы разброса очень удобно наблюдать характер изменения параметров качества во времени при воздействии тех или иных факторов. В этом случае по оси абсцисс откладывают начальные значения изучаемого параметра качества, например обратный ток p-n- перехода
однотипных полупроводниковых структур (Iобр) перед постановкой эксперимента по изучению влияния определенных факторов (например, температуры, влажности) на данный параметр качества. В результате будем иметь упорядоченный ряд значений x1 ,x2 , х3 , ..., хп параметра качества полупроводниковых структур в момент времени t=0, которые наносят на ось абсцисс.
Замерив значения параметра качества у тех же самых полупроводниковых структур по окончании эксперимента, получим ряд значений параметра качества через время t=ti ,представленных в виде упорядоченного ряда y1 ,у2 ,…, уп ,который наносят соответственно на ось ординат. Тогда значение параметра качества каждого изделия до и после эксперимента будет обозначаться точкой в системе указанных координат. Следовательно, все п изделий, подвергшихся эксперименту, будут изображаться разбросанными по координатному полю точками. Эта совокупность точек образует диаграмму разброса (поле корреляции) (рис. 10.1). Если разброс значений изучаемого параметра качества составляет несколько порядков, то удобно применять логарифмический масштаб по обеим осям. Если на одну и ту
96
же точку графика попадает несколько значений параметра, то они обозначаются как точка в круге или в нескольких кругах или возле точки проставляется число данных.
Диаграмма разброса позволяет наглядно показать характер изменения параметра качества во времени.
Для этого проведем из начала координат биссектрису. Если все точки лягут на биссектрису, то это означает, что значения данного параметра не изменились в процессе эксперимента. Следовательно, рассматриваемый фактор (или факторы) не влияет на параметр качества.
Если основная масса точек лежит под биссектрисой, то это значит, что значения параметра качества за прошедшее время уменьшились. Если же точки ложатся выше биссектрисы (как в нашем случае на рис. 10.1), то значения параметра за рассматриваемое время возросли.
Проведя лучи из начала координат, соответствующие уменьшению и увеличению параметра на 10, 20, 30, 50, 80%, можно путем подсчета точек между прямыми выяснить частоту значений параметра в интервалах 0...10%, 10...20% и т. д.
Пример 1. Требуется выяснить влияние термообработки интегральных микросхем (ИС) при Т= 120 °С в течение времени t = 24 ч на уменьшение обратного тока р - n-перехода (Iобр). Для эксперимента было взято 25 интегральных схем (п = 25) и замерены значения Iобр (10-9 А), которые приведены в табл. 10.1.
97
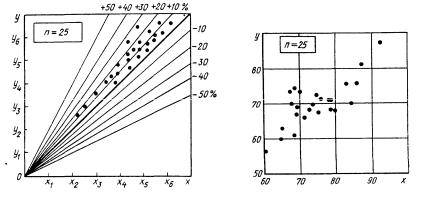
Рис. 10.1. Диаграмма разброса |
Рис. 10.2. Диаграмма |
|
разброса данных табл. 10.1 |
1.По таблице находят максимальные и минимальные значения х и у: максимальные значения x=92, y=88; минимальные значения х = 60, у = 57.
2.На графике (рис. 10.2) на оси абсцисс откладывают значения х, на оси ординат — значения у. При этом длину осей делают почти равной разности между их максимальными и минимальными значениями и наносят на оси деления шкалы. На вид график приближается к квадрату. Действительно, в рассматриваемом случае разность между максимальными и минимальными значениями равна 92 — 60 = 32 для х и 88 — 57
=31 для у, поэтому промежутки между делениями шкалы можно делать одинаковыми.
3.На график наносятся данные в порядке измерений и точки диаграммы разброса.
4.На графике указываются число данных, цель, наименование изделия, название процесса, исполнитель, дата составления графика и т.д. Желательно также, чтобы при регистрации данных во время измерений приводилась и сопровождающая информация, необходимая для дальнейших исследований и анализа: наименование объекта измерения, характеристики, способ выборки, дата, время измерения, температура, влажность, метод измерения, тип измерительного
98
прибора, имя оператора, проводившего измерения (для данной выборки), и др.
С помощью диаграммы разброса можно сравнительно быстро выяснить, имеется ли между двумя рассматриваемыми параметрами корреляционная связь, и, построив методом наименьших квадратов кривую, определить вид этой связи.
Характер корреляционной зависимости, который определяется видом диаграммы разброса, дает представление о том, каким изменениям будет подвержен один из параметров
при определенных изменениях другого. Однако если, как, например, в предыдущем случае (рис. 10.1 и 10.2), для выяснения характера изменения значений параметра качества достаточным было бы число данных порядка 10, то в случае выяснения их корреляционной связи число должно быть значительно больше. Если данных мало, четкую зависимость установить трудно, поэтому желательно, чтобы число пар данных было не меньше 30. Так, на диаграмме рис. 10.3 виден не только характер изменений у в зависимости от изменения х, но и определяется форма связи рассматриваемых признаков в виде уравнения регрессии. На рис. 10.3 четко просматривается прямая корреляция между х и у. В этом случае при осуществлении контроля за причинным фактором х можно управлять значением параметра качества у.
На рис. 10.4 приведен пример легкой прямой корреляции. При увеличении х увеличивается также и у, но разброс у велик по отношению к определенному значению х. С помощью контроля причинного фактора х можно до некоторой степени держать под контролем характеристику у, но необходимо также иметь в виду и другие факторы, оказывающие влияние на у.
На рис. 10.5 показан пример обратной (отрицательной) корреляции. При увеличении х характеристика у уменьшается. Если причинный фактор х находится под контролем, характеристика у остается стабильной.
99
Таблица 10.1 Значения обратного тока р - n-перехода до и после
термообработки ИС
|
До |
После |
|
До |
После |
Номер |
термо- |
термо- |
Номер |
термо- |
термо- |
ИС |
обработк |
обработк |
ИС |
обработк |
обработк |
|
и, x |
и, у |
|
и, x |
и, у |
1 |
68 |
61 |
14 |
75 |
71 |
2 |
71 |
67 |
15 |
73 |
70 |
3 |
65 |
63 |
16 |
69 |
68 |
4 |
78 |
70 |
17 |
73 |
73 |
5 |
75 |
74 |
18 |
73 |
69 |
6 |
85 |
76 |
19 |
83 |
76 |
7 |
86 |
82 |
20 |
70 |
73 |
8 |
84 |
70 |
21 |
68 |
70 |
9 |
74 |
68 |
22 |
79 |
69 |
10 |
65 |
60 |
23 |
78 |
71 |
11 |
78 |
68 |
24 |
78 |
71 |
12 |
92 |
88 |
25 |
73 |
69 |
13 |
60 |
57 |
|
|
|
На рис. 10.4 приведен пример легкой прямой корреляции. При увеличении х увеличивается также и у, но разброс у велик по отношению к определенному значению х. С помощью контроля причинного фактора х можно до некоторой степени держать под контролем характеристику у, но необходимо также иметь в виду и другие факторы, оказывающие влияние на у.
На рис. 10.5 показан пример обратной (отрицательной) корреляции. При увеличении х характеристика у уменьшается. Если причинный фактор х находится под контролем, характеристика у остается стабильной.
100