
2899
.pdf
потоке воды. Их производительность до 60 тонн смеси в час. Кроме них применяются комплексы пневматической (рис.1.4) и термической регенерации.
Рис. 1.4. Оборудование для пневматической регенерации смесей
Процесс приготовления смеси состоит из дозирования всех компонентов смеси, загрузки их в смесители в определенной последовательности, перемешивания для обеспечения однородности и заданных свойств готовых смесей. Для этих целей применяются преимущественно литейные чашечные смесители.
Основной способ получения литейных форм – машинная формовка. По сравнению с ручной она обладает более высокой производительностью, меньшей трудоемкостью, позволяет получать отливки более высокой точности, улучшает условия труда. К основным способам уплотнения формовочных смесей относятся встряхи-
вание, прессование, пескометание, пескодувное и пескодувнопрессовое уплотнение, импульсное, гравитационное, вакуумно-
прессовое уплотнения. Все способы осуществляются с применением формовочных литейных машин.
При верхнем прессовании (рис. 1.5,а) опока 6 устанавливается на модельную плиту с моделью 4, прикрепленную к столу 5 формо-
11

вочной машины. Перед наполнением опоки смесью 3 на нее ставится наполнительная рамка 2, так как необходимый объем рыхлой смеси больше объема уплотненной в опоке смеси. Затем в цилиндр машины подается сжатый воздух, поршень поднимает стол машины 5 с плитой, опокой, рамкой. Прессующая колодка 1 входит в наполнительную рамку, вытесняя из нее смесь в опоку и уплотняя смесь.
а б Рис. 1.5. Основные способы уплотнения смеси при машинной формовке
Основным рабочим органом пескомета (рис.1.5, б) является метательная головка 2, представляющая собой закрытый кожухом ротор, вращающийся на горизонтальной оси со скоростью 1500 об/мин и имеющий одну-три лопатки (ковша) 5. Смесь в головку подается транспортером 1, попадает на лопатку 5, предварительно уплотняется на ней центробежной силой, а затем выбрасывается вниз порциями 3 в опоку 4. За каждый оборот лопатки выбрасывается один комок, а в минуту – 1400-1500 комков. Вследствие большой скорости комки с силой ударяют о поверхность смеси в опоке и уплотняют ее, действуя как трамбовка. Чтобы иметь возможность направлять поток смеси в разные места по всей площади опоки, формовщик может перемещать метательную головку над опокой в горизонтальной плоскости.
12

Состав оборудования и оснастки для производства стержней зависит от серийности, размеров, конструкции стержней и требований по их прочности, точности и качеству поверхности. В единичном и мелкосерийном производстве формы для изготовления стержней - стержневые ящики - делают из дерева, смесь уплотняют вручную или пневматическими трамбовками. При достаточно большом объеме производства применяют металлические стержневые ящики. Мелкие и средние стержни, имеющие сложные очертания, которые невозможно изготовить целиком, изготовляют по частям, а затем склеивают.
Для плавки чугуна в литейных цехах широко применяются вагранки (рис. 1.6) – это шахтные печи, выложенные огнеупорным шамотным кирпичом 1 внутри металлического кожуха.
Рис. 1.6. Вагранка
В нижнюю часть вагранки через коллектор 2 и фурмы 3 подается подогретый воздух (дутье), нагнетаемый воздуходувками. У самого дна находится отверстие для выпуска металла (летка) и желоб 4. Загрузка материалов (шихты) производится сверху через бункер 7 загрузочного приспособления 6. Кокс, флюс (известняк), чуш-
13
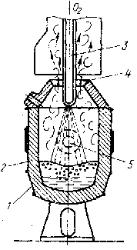
ковый чугун и лом загружаются слоями. При сгорании кокса выделяется теплота, плавящая металл. Горячие газы, поднимаясь вверх, нагревают завалку и отсасываются через патрубок 5. Они сжигаются для подогрева дутья. Для большей эффективности плавки дутье обогащают кислородом. Шихта по мере течения плавки опускается вниз. Для контроля ее уровня имеется уровнемер 8. По мере необходимости производится загрузка новых порций шихты. Роль флюса состоит в переводе в шлак золы, серы, фосфора и других примесей. Кроме описанной выше коксовой вагранки имеются коксогазовые и газовые вагранки, экономящие дефицитный кокс. Самый дешевый чугун дают газовые вагранки.
Современные отечественные ваграночные комплексы 95111 ...
95116 имеют производительность от 4 - 6 до 25 - 36 т/ч. Модель 95111 – коксовая, остальные – коксогазовые. Температура выпуска 1400 – 1500 °С. Автоматизированный ваграночный комплекс ВЛК1015 имеет производительность 10 - 15 т/ч, а ВЛК2030 20 -30 т/ч.
Кислородный конвертер (рис. 1.7) является одним из самых современных сталеплавильных устройств.
Рис. 1.7. Кислородный конвертер
Конвертеры представляют собой грушевидные сосуды, металлические кожухи 1 которых выложены изнутри огнеупорами 2. Для заливки жидкого чугуна и выпуска стали они могут поворачиваться
14

на цапфах 5. Сталь выплавляется продувкой кислорода водоохлаждаемой фурмой 3 по поверхности жидкого чугуна, в результате чего избыток углерода, кремния, марганца и других элементов окисляется и удаляется в виде газов через горловину 4, а сера и фосфор шлакуются. Конвертер характеризуется высокой скоростью плавки (0,5 ч) и высокой производительностью. Недостаток: невозможность работать на твердой завалке - конвертер загружается жидким чугуном.
Дуговые сталеплавильные с поворотным сводом печи (рис. 1.8) ДСП-0,5 ... ДСП-50 (цифры указывают на номинальную емкость в тоннах) плавят металл за счет теплоты трех электрических дуг, горящих между графитовыми электродами 6 и шихтой 5.
Рис. 1.8. Дуговая сталеплавильная печь
Длина дуг поддерживается в заданных пределах системой автоматического регулирования. Свод 5 при поднятых электродах, поворачиваясь относительно вертикальной оси, открывает печь сверху для загрузки шихты. Для выпуска металла по желобу 2 и удаления шлака ванна печи 1 может поворачиваться на роликах приводом 8. Рабочее окно 7 служит для удаления шлака, наблюдения за ходом плавки, проведения необходимых операций в ходе плавки (взятия
15
проб, введения легирующих присадок, и др.) и заправки стен и порогов. Огнеупорная кладка 4 печи заключена в кожух из стального листа. Дуговые печи позволяют получать разнообразные стали и чугуны, а также создавать в области дуг высокие температуры, необходимые для восстановления оксидов, расплавления тугоплавких металлов и отделения металлов от тугоплавких шлаков. По сравнению с индукционными печами они имеют более высокий КПД (80 - 85 % при расплавлении), осуществляют быстрый подъем температуры, более дешевы и производительны (на 20 - 30 %) при одинаковой емкости. Их недостатками являются более низкий КПД при перегреве (не более 20 %), значительные дымление и шум, больший угар и большая неравномерность температуры металла. Расход электроэнергии для ДСП-6 ... ДСП-50 составляет 500 - 440 кВт-ч/т, продолжительность плавки 2,8 - 5,7 ч. В литейных цехах дуговые печи являются основным типом сталеплавильного оборудования.
Дуговые медеплавильные качающиеся печи ДМК-0,1 ...
ДМК-2,0 производят плавку за счет дуги косвенного действия, горящей между двумя графитовыми электродами. Для слива сплава эти печи могут наклоняться на роликах. Применяются для плавки медных сплавов; нежелательна плавка в них алюминиевых бронз и латуней из-за местного перегрева в зоне дуги, приводящего к испарению летучих элементов и загрязнению металла оксидами. У ДМК- 2,0 производительность равна 1,3 - 1,5 т./ч, расход электроэнергии
180 - 230 кВт-ч/т.
Индукционные тигельные плавильные печи характеризуются непосредственным нагревом (теплота генерируется прямо в шихте), отсутствием контактных устройств (что облегчает автоматизацию и создание вакуума или защитных сред), улучшенными условиями труда. Разогрев металла происходит в тигле за счет переменного электрического тока, возбуждаемого токами в индукторе печи, образованном полой медной трубкой, охлаждаемой проточной водой. Для слива металла печь может наклоняться.
Индукционные канальные печи имеют по сравнению с ти-
гельными более высокий КПД -75 % (у тигельных 50 %); коэффициент мощности выше в 3 раза, поэтому меньше расход энергии и мощность конденсаторной батареи. Применяются для плавки медных и алюминиевых сплавов.
Для плавки алюминиевых сплавов применяют электрические отражательные печи сопротивления камерные САК-0,15 и САК-
16
0,25 и наклоняемые САН-0,ЗА ... САН-ЗА. Угар металла в этих печах невысок (около 1 %). Расход электроэнергии в печах емкостью 1,5 - 2 т около550кВт-ч/т. Расходэлектроэнергии уэтихпечей 550-600кВт-ч/т.
Электропечи сопротивления для плавки алюминиевых сплавов позволяют лучше рафинировать сплавы и получать высококачественные отливки, однако обладают низкой производительностью, низкой стойкостью нагревателей (нихромовых или других) и кладки. При получении ответственных отливок применяют вакуумнодуговые, индукционно-дуговые, плазменно-дуговые, электроннолучевые печи, электрошлаковый переплав и т. д.
Заливка форм сплавами в индивидуальном и мелкосерийном производстве выполняется на плацу, а в поточном массовом и крупносерийном – на конвейере.
Широко распространена заливка литейных форм из ковшей (рис. 1.9, а - в). Ковши представляют собой конические и цилиндрические металлические сосуды 1, облицованные (футерованные) изнутри огнеупорами 2, цапфы которых укреплены на подвеске 3 и снабжены механизмами наклона ковшей 4. Заливка из ручных ковшей сопряжена с опасным и тяжелым ручным трудом и поэтому крайне нежелательна. Она может быть заменена заливкой с помощью манипуляторов. Широко применяются монорельсовые конические ковши емкостью 100 -800 кг и крановые: конические емкостью 1 - 20 т и барабанные емкостью 1 - 5 т.
Барабанные ковши (рис. 1.9, а) хорошо сохраняют температуру сплава, поэтому их применяют при производстве тонкостенных мелких и средних отливок из бронзы, стали и чугуна и в качестве раздаточных, для наполнения более мелких ковшей. Они также могут обеспечить наименьшую высоту падения струи металла при заливке; недостатком их является трудность футеровки. Чайниковые (рис. 1.9, б) и стопорные (рис. 1.9, в) ковши обеспечивают заливку форм металлом из нижней части ковша, что предотвращает попадание в форму шлака. В чайниковых ковшах шлак 2 задерживается перегородкой 1. Широко применяются обычные конические ковши (без перегородки 1). Стопорные ковши применяют при заливке стали и высокопрочного чугуна. Разливка из них осуществляется через огнеупорный стакан 1, вставляемый в дно. Отверстие в стакане открывают и закрывают облицованным огнеупорными втулками стопором 2 с помощью рычажного механизма 3.
17

Рис. 1.9. Оборудование для заливки форм
При заливке на плацу емкость ковшей выбирают достаточной для заливки 4 - 10 мелких форм или 2 - 4 крупных форм. При конвейерной заливке емкость ковша выбирается достаточной для заливки 5 - 20 форм. Особо крупные формы заливают из двух и более ковшей.
Магнитодинамическая установка (МДУ) МДН-6 (рис. 1.9, г)
представляет собой индукционную канальную печь с электрическим насосом. Ее тигель 1 имеет крышку 10 и механизм наклона. Магнитопроводы 3 с их катушками 2 создают в трубах 7 и 4, наполненных жидким сплавом токи, разогревающие металл. При включении обмотки 5 С-образного магнитопровода 6 электромагнитные силы вызывают движение сплава из тигля по трубам 4, 7, 8 через сливной металлопровод 9 в форму.
18
МДУ 99411 и 99413 предназначены для поддержания температуры и дозированной заливки чугуна в неподвижные формы, кокильные машины и другие агрегаты в цехах массового и серийного производства. Оптимальный развес отливок 5 - 150 кг и 50 - 350 кг соответственно. У этих установок в процессе заливки ванна наклоняется относительно оси, проходящей через точку слива, путем движения люльки по круговым рельсам под действием двух качающихся гидроцилиндров для поддержания постоянства положения струи и расхода.
Основным видом оборудования для выбивки литейных форм и стержней являются выбивные решетки грузоподъемностью до 40 тонн, применяются в единичном и мелкосерийном производстве. Под действием вибрации и ударов форма разрушается, смесь проваливается сквозь ячейки решетки на транспортер, доставляющий ее в землеприготовительное отделение на переработку, а отливка снимается с решетки и отправляется на обрубку. Для выбивки особо круп-
ных форм предназначены установки литейные выбивные, пред-
ставляющие собой счетверенные решетки грузоподъемностью до
160 тонн.
Обрубка заключается в отделении от отливок элементов литниковой системы, удалении заливов по разъему формы и неровностей поверхности. Обработка отливок массой до 100 кг производится в галтовочных барабанах, отрезка литниковых систем осуществляется также дисковыми пилами трения, газокислородной резкой, воздушно-дуговой резкой, резкой абразивными кругами. Литники мелких отливок удаляют на ленточно-отрезных станках. В крупносерийном и массовом производстве литники отламывают на прессах. Выпускаются механизированные установки ОС500 для абразивной отрезки литников и прибылей, и механизированный комплекс модели 98516, снабженный манипуляторами. Очистка литья происходит в очистных галтовочных барабанах, дробеметными, дробеструйными и гидропескоструйными аппаратами, а также с помощью очистных вибрационных машин.
Барабаны очистные галтовочные (рис. 1.10, а) предназначе-
ны для очистки мелкого и среднего литья. Барабаны периодического действия загружаются отливками через крышку 2 металлического цилиндрического барабана 1, установленного в подшипниках на основании 4. После закрытия крышки барабан начинает вращаться под действием привода 3. Одновременно включается отсос пыли 5. От-
19

ливки перекатываются друг по другу и очищаются. Для лучшей очистки в барабан вместе с отливками могут загружаться звездочки из белого чугуна размером 20-65 мм, которые своими острыми углами скребут поверхность отливок. Барабан модели 41114 имеет производительность по чугуну 5,25 т/ч.
Рис. 1.10. Оборудование для очистки литья
Широкое применение находит очистка поверхности отливок от пригара и окалины потоком стальной или чугунной дроби. При дробеструйной очистке (рис.1.10, б) дробь направляется на отливку потоком сжатого воздуха. В дробеметных аппаратах (рис.1.10, в) поток дроби создается за счет центробежных сил, возникающих при подаче дроби на радиально направленные лопатки вращающегося диска. Дробеметная очистка в 10 раз эффективнее дробеструйной при значительно меньшем расходе электроэнергии.
20