
1757
.pdf
основе щипаной природной смолы, тонкие пластины которой склеены между собой различного рода связующими веществами (полиэфирная смола, шеллак, глифталевая смола, аммоний фосфорнокислый двузамещенный и др.). Как следует из изложенного выше, миканитовые детали в коллекторе несут значительную нагрузку на сжатие. Поэтому важной их технологической характеристикой является усадка под действием постоянной механической нагрузки. Величина усадки напрямую связана с содержанием в материале связующего вещества. По этой причине его количество выбирается минимальным, необходимым для решения конструктивно-технологических задач.
Миканиты, предназначенные для изготовления коллекторных прокладок, содержат минимальное количество связующих и получили название «коллекторные». Процентное содержание связующих в коллекторных миканитах колеблется от 1,1 % (марка КФА) до 4,5 % (марка КФП, КФШ, КФГ и др.), что обеспечивает минимальную их усадку при прессовке.
Миканиты, предназначенные для изготовления коллекторных манжет, содержат повышенное количество связующих, что обеспечивает при изгибе в процессе формовки проскальзывание пластинок слюды друг относительно друга и придает материалу формовочные свойства.
Миканиты выпускаются листами толщиной 0,4 1,5 мм и с размерами сторон 215х400 мм. Следует отметить, что для изготовления манжет целесообразно выбирать формовочный миканит возможно меньшей толщины, что позволяет выполнить деталь в несколько слоев со сдвигом стыков отдельных сегментов и тем самым повысить электрическую прочность.
На основе измельченных отходов слюды, а также миканитов, выпускаются более дешевые материалы, нашедшие применение в коллекторах: слюдопласт и слюдинит /27/. Из слюдинитовой бумаги с применением органических и кремнийорганических связующих лаков с подложками из тканей и пленок изготавливают слюдиниты: гибкий, формовочный, коллекторный и прокладочный. По суммарной усадке формовочный и коллекторный слюдиниты не уступают миканитам. Наряду с этим они обладают повышенными формовочными возможностями, что позволяет получать детали с малыми радиусами закруглений, что важно для мелких коллекторов.
В последние годы все более широкое применение в коллекторах получают слюдопласты, которые представляют собой пропитанную различными составами (шеллак, глифталевый лак, эпоксидные компаунды и т.п.) слюдопластовую бумагу, отпрессованную в горячем состоянии в листы заданной толщины. Опытным путем установлено, что по механической прочности слюдопласты не уступают миканитам, а порой и превосходят их. Слюдопласты отличаются однородной толщиной листов и высокой электрической прочностью. В настоящее время для производства корпусной изоляции коллекторов применяют композиции на основе формовочных слюдопластов ФСФША и ФИП, армированных пропитанной стеклотканью
81

марки ПС-ИФ/ЭП-70. Такая композиционная изоляция получила название стеклослюдопласта.
Вконструкциях монолитного коллектора в качестве материала для корпусной и межламельной изоляции применяется электроизоляционный асбест, который в собранном коллекторе пропитывают эпоксидным компаундом.
Вконструкциях современных коллекторов широко используются пластмассы. Пластические массы – это материалы на основе природных или синтетических смол и компаундов с добавлением различного рода наполнителей для придания специальных свойств. Различают пластмассы термопластичные и термореактивные. Последние отверждаются при нагревании необратимо. При повторном нагреве они не размягчаются, оставаясь твердыми. Они обладают повышенной нагревостойкостью и термостабильностью. Поэтому они нашли применение в коллекторах с пластмассовым корпусом. Наибольшее распространение здесь получила фенолформальдегидная смола с наполнителем в виде стекловолокна (марка АГ- 4). Пластмасса АГ-4 обладает приемлемыми механическими и изоляционными характеристиками, которые сохраняются в значительном интервале температур. Известны две модификации этого материала:
АГ-4В – наполнителем является предварительно нарезанное (2 10 см) и распущенное стекловолокно;
АГ-4С – наполнителем является ориентированное стекловолокно в виде длинных нитей (d = 6 7 мк), равномерно покрытых связующим.
Главным недостатком указанных материалов является их токсичность изза выделения стеклянной пыли при загрузке в пресс-форму. Перспективными являются пластмассы с наполнителями из кварцевой пудры, слюды, двуокиси кремния и др., в зависимости от требуемых характеристик. Так, например, для сближения температурных коэффициентов линейного расширения металла и пластмассы в последнюю иногда добавляют бор /27/.
5.3. Изготовление коллекторных пластин
Специфика изготовления коллекторных пластин состоит в том, что при этом решается две задачи: обеспечение требуемой геометрии и точности деталей; экономия дорогостоящего материала – меди. Причем, особенностью экономного расходования меди является не только минимизация отходов, но и получение отходов по возможности не измельченными. При измельчении отходов меди увеличиваются потери при переплавке. Эти требования часто входят в противоречие, что приводит к необходимости искать в каждом конкретном случае оптимальное решение, учитывая при этом и другие производственные издержки.
82

Коллекторная медь поступает в виде полос длиной до 3,5 м. Для производства коллекторных пластин большей длины ( 150 200) рационально при заказе точно определять длину полосы:
L n |
(n 1) , |
(19) |
где: - длина пластины с учетом припуска на обработку торцев; n – число пластин, получаемых с полосы; - технологический припуск, величина которого зависит от толщины полосы.
Выполнение этого требования позволит исключить немерные отходы меди. Способ получения пластин из полос зависит от габарита коллектора. Распространен способ вырубной штамповки пластин с одновременным оформлением «ласточкиных хвостов» и с минимальными припусками на последующую обработку торцев коллекторного пакета. Отходы меди при таком решении получают в виде кусочков. Однако с уменьшением размеров пластин происходит соответствующее измельчение отходов, в связи, с чем представляется целесообразным упростить производство и снизить затраты. Поэтому для мелких коллекторов полосу рубят на заготовки прямоугольной формы, а окончательную конфигурацию пластины приобретают при обточке собранного и спрессованного коллекторного пакета. Потери от измельчения меди в стружку при такой технологии оказываются меньше той выгоды, которая достигается за счет удешевления самой операции.
Коллекторные пластины крупных коллекторов (а 10 мм) выполняют резкой полосы на горизонтально-фрезерных или специальных станках. Часто оказывается целесообразным уменьшить материалоемкость крупных коллекторных пластин. С этой целью в теле пластины выполняют отверстие (рис. 43), а полученные при этом отходы - утилизируются.
Рис. 43. Форма коллекторной пластины тягового двигателя НБ-418К
После штамповки, рубки или резки на пластинах образуются заусенцы, кривизна, другие дефекты. Заусенцы удаляют обработкой ребер. Кривизна в виде изгибов, скручивания («винт») и т.п. удаляется специальной правкой (рихтовкой), которая выполняется вручную или под штампом на фрикционном прессе.
83

Ручная правка коллекторной пластины выполняется на стальной плите ударами молотка через прокладку, исключающую появление на детали забоин. В качестве прокладки могут использоваться медная, алюминиевая или свинцовая пластина. Деформацию скручивания («винт») иногда приходится устранять специальным воротком. Пластину при этом вставляют концом в специальный паз в плите, а на другой ее конец надевают вороток. Дефект устраняют поворотом воротка в противоположном «винту» направлении. Качество правки пластины при этом проверяют на стальной плите на просвет. Следует отметить, что ручная правка коллекторных пластин трудоемка и требует высокой квалификации рабочего. Поэтому в крупносерийном и массовом производстве эту операцию механизируют, используя, как отмечалось, специальные «вафельные» штампы, устанавливаемые на фрикционные прессы.
«Вафельный» штамп содержит две части: матрицу (неподвижную) и пуансон. Они обращены друг к другу своими плоскими рабочими поверхностями. Таким образом, активные элементы его выполнены в виде стальных плит, одна из которых крепится на столе пресса, а вторая – на ползуне. На рабочих поверхностях матрицы и пуансона выполнены продольные выступающие острые гребни высотой 0,3 мм с шагом 5 мм. При ударе острые гребни внедряются в тело пластины, растягивая наружный слой металла, что способствует более точной рихтовке.
Следующим этапом изготовления коллекторной пластины являются работы по выполнению «петушка». Если конструкция предусматривает его выполнение за одно целое с пластиной, то полученные заготовки пластин направляют на фрезеровку шлицов, предназначенных для закладки выводов якорной обмотки. Операция выполняется дисковыми фрезерами. Иногда практикуют фрезеровку шлицев в «петушках» после сборки коллектора. Такое решение может быть оправдано только в обоснованных случаях, так как брак одного шлица приведет к выбраковке всего коллектора. Более вероятно появление брака при фрезеровке тонких пластин. Из-за смещения фрезы в этом случае резко утоньшается щечка «петушка», как показано стрелкой на рис. 44. Здесь шлиц, выполненный со смещением от оси, показан пунктиром. Место утоньшения стенки показано стрелкой.
Рис. 44. Смещение щлица в петушке
84

Для обеспечения качественной пайки выводов, заложенных в шлицы коллекторных пластин, стенки шлицев подвергают горячему лужению. С этой целью пластины подвешиваются на цепном транспорте. Перемещаясь вдоль технологической линии, пластины погружают петушки в ванны с флюсом, а затем – с расправленным припоем. Боковые поверхности пластин для предотвращения покрытия припоем предварительно покрывают водно-меловой эмульсией и подсушивают.
Из изложенного видно, что выполнение петушка заодно с коллекторной пластиной порождает ряд проблем: увеличивает расход меди, погрешности формы и размеров петушка приводят к выбраковке всей пластины или даже коллекторного пакета и др. Поэтому в ряде случаев петушки коллектора выполняются в виде отдельных деталей, которые потом пайкой, сваркой или другим способом соединяются с коллекторными пластинами.
5.4. Изготовление коллекторных прокладок и манжет
Изоляционные коллекторные прокладки изготавливают из коллекторного миканита или его заменителей: слюдопласта или слюдинита. Эти материалы имеют высокую стоимость. Поэтому при изготовлении прокладок важное значение имеет выбор технологичной формы прокладки. Решение этой задачи затруднено, так как форма прокладки должна быть согласована также с формой коллекторной пластины.
Второй путь экономики материала – выбор рациональной карты раскроя. На рис. 45. даны для примера варианты рационального раскроя коллекторного миканита. Получаемые отходы измельчаются и используются для изготовления других изоляционных материалов.
Рис. 45. Варианты раскроя миканита при изготовлении коллекторных подкладок
Коллекторные прокладки для мелких коллекторов получают в виде прямоугольников порезкой листа на рубочных штампах. Для крупных коллекторов прокладки получают путем вырубной штамповки, при этом им придается окончательная форма. При штамповке прокладок важное значение
85

имеет состояние их кромок. Миканиты являются слоистыми материалами, способные при нарушениях режимов штамповки расслаиваться на кромках вырубки. Поэтому при их изготовлении большое значение имеет состояние режущих кромок и регулировка рабочих зазоров штампов.
Следует особо отметить, что прокладки для конкретного коллектора изготавливают из материала одинаковой толщины. Даже при выполнении этого условия только за счет допуска на толщину листа (от 0,04 до 0,08 мм) при сборке коллекторного пакета могут накапливаться недопустимые погрешности. Особого внимания в коллекторном производстве заслуживает изготовление коллекторных манжет, изолирующих медные пластины от нажимных конусов. В качестве материала используются формовочный миканит или формовочный слюдинит. Коллекторная манжета в сечении имеет довольно сложный профиль, который плохо сочетается с технологическими свойствами применяемых материалов. Вариант геометрии профиля манжеты показан на (рис. 46, а) Для получения детали такой конфигурации из указанных материалов удобно использовать заготовки в виде сегментов, имеющих форму, показанную на (рис. 46, б). Размеры сегмента хорошо согласуются с размерами манжеты и могут быть определены несложными геометрическими расчетами /2/. Сегменты размещаются по окружности манжеты в несколько слоев, что обеспечивает требуемую толщину стенок манжеты.
а)
б)
Рис. 46. Общий вид коллекторной манжеты (а) и заготовки (б)
Сегмент можно вырезать вручную по выкройке. С увеличением программы переходят на вырубную штамповку.
Полученные заготовки (сегменты) закладывают в матрицу пресс-формы, предварительно подогретую до +1900С. Закладку заготовок в матрицу производят, как показано на рис.47 слева от оси. В матрицу 1 закладывают сегменты 3 так, чтобы соседние в слое заготовки в месте стыка перекрывали друг друга примерно на четверть ширины зубца. Сегменты закладывают в несколько слоев, в зависимости от соотношения толщины материала и готовой
86

детали. Стыки соседних слоев смещают друг от друга с таким расчетом, чтобы все стыки были равномерно распределены по окружности манжеты. Пуансон 2 пресс-формы опускают вниз и прессуют деталь на гидропрессе до тех пор, пока температура снизится до +400С. При таком режиме прессовки связующие материала сохраняют термопластичность, что важно при выполнении прессовки собранного коллектора.
2
3
1
Рис. 47. Прессовка манжеты: 1- матрица; 2- пуансон; 3- заготовки.
После окончания прессовки выступающие из пресс-формы края материала обрезают «заподлицо», открывают пресс-форму и извлекают готовую манжету. Следует помнить, что эта деталь требует осторожного обращения, поэтому ее транспортировка и хранение производится в специальной таре.
5.5. Сборка и обработка коллекторного пакета
Коллекторный пакет, состоящий из чередующихся медных пластин и миканитовых прокладок – активная часть коллектора. Его сборка и обработка требует особого внимания, так как даже незначительные отклонения от установленных технологических режимов может привести к браку готового коллектора или даже всего якоря. Важно, чтобы при сборке были обеспечены: заданное число и чередование медных пластин и миканитовых прокладок, требуемые размеры коллектора, равномерный шаг по коллектору. Затруднения с решением этих задач связаны с необходимостью сборки большого числа однотипных деталей, каждая из которых имеет собственные погрешности размеров и формы. Так если коллекторные пластины выполнены из сортамента
87

нормального класса точности (см. табл.), то погрешность толщины пластины может достигать 0,1 мм. Погрешность толщины миканитовой прокладки также может достигать 0,08мм. Поэтому наружный диаметр коллекторного пакета, собранного из таких деталей, будет иметь допуск, который определяется, как
|
(0,1 0,08)K |
. |
(20) |
|
|
||
d |
|
В абсолютном выражении представить эту погрешность нетрудно, достаточно задаться числом коллекторных пластин. Так, при K=200 получим
d - 11,45 мм, что нельзя считать приемлемым.
Дополнительно к изложенному следует обратить внимание, что требование электрической симметрии якоря предусматривает равное число катушек в параллельных ветвях при любом положении якоря относительно неподвижных щеток. Это условие приводит к требованию, чтобы между любой парой соседних щеток оставалось равное число коллекторных делений в любом положении коллектора при его вращении вокруг оси.
Все это приводит к выводу, что полная взаимозаменяемость медных пластин и прокладок коллекторного пакета возможна для коллекторов с малым числом пластин. Однако с их увеличением погрешность накапливается и в какой-то момент становится неприемлемой. Частично задачу можно решить, переходя на сортамент материала повышенного или высокого класса точности, но это полностью проблему не снимает.
В связи с изложенным для повышения точности коллекторного пакета применяют селективную сборку. Для этого медные пластины и изоляционные прокладки калибруют. С этой целью комплект пластин и прокладок, предназначенный для сборки коллектора, разбивают на несколько стопок с одинаковым числом деталей в каждой. Пластины одной стопки укладывают в приспособлении друг на друга, как показано на рис. 48.
1 |
2 |
3 |
|
P |
|
|
|
Н |
|
|
4 |
Рис. 48. Калибровка коллекторных пластин |
88
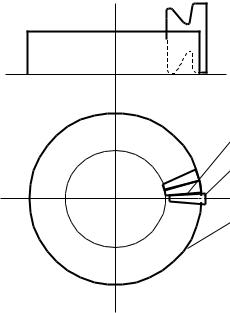
Стопку прессуют с усилием Р бокового распора и, не снимая усилия, измеряют ее высоту H. Подбором медных пластин (прокладок) обеспечивают требуемую высоту стопки. Стопки укладывают в ячейки тарного ящика, сопровождая их ярлыками с указанием фактической высоты. При сборке коллекторного пакета стопки чередуют так, чтобы отклонения их высоты по возможности компенсировали друг друга.
Калибровка является трудоемкой операцией. Поэтому постоянно подыскиваются пути ее упрощения. Положительные результаты дают подбор пластин с помощью измерительных скоб или использование так называемых уравнительных прокладок. Последние отличаются по толщине, их равномерно распределяют по всем стопкам. Уравнительные прокладки также равномерно распределяются по высоте стопки.
Сборка коллекторного пакета выполняется в специальном пружинном кольце, а с увеличением габарита или класса напряжения – на сборочном диске. Применение одного из вариантов пружинного кольца показано на рис. 49. Здесь стальное кольцо 1 разрезано с одной стороны. В разрез вставлена коллекторная пластина 2, которая удерживается упругими силами кольца. Далее к пластине 2 прижимают прокладки 3, потом следующую пластину и т.д. Набирают весь пакет, строго чередуя медные пластины и миканитовые прокладки. После окончания сборки окончательно проверяют количество пластин, и полученный пакет перевязывают по окружности отожженной проволокой.
3
2
1
Рис.49 Сборка коллекторного пакета в пружинном кольце
Комплектование коллекторного пакета на сборочном диске показано на рис.50. Приспособление собрано из двух дисков 1 и 2, сориентированных друг относительно друга с помощью штифтов 3. Оно предназначено для сборки коллектора только одного типоразмера. На верхней поверхности дисков 1 и 2 выполнены радиальные пазы, число которых равно числу коллекторных пластин. В эти пазы вставляют миканитовые прокладки, между которыми
89
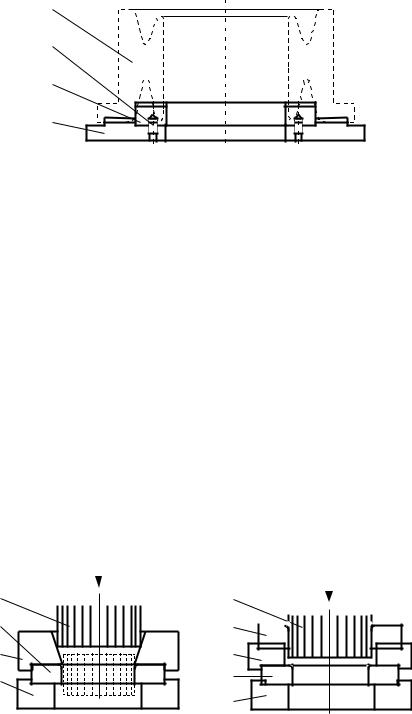
размещают медные пластины. Собранный пакет бандажируют мягкой проволокой.
4
3
2
1 |
Рис.50 Сборочный диск: 1 и 2-диски с радиальными пазами; 3 – штифт; 4 – коллекторная прокладка
В собранном коллекторном пакете необходимо создать усилие бокового распора для чего нужно ко всем коллекторным пластинам приложить усилие, направленное к оси пакета. Эта задача решается прессовкой пакета в кольцах на гидропрессе. Конструкция прессовочных колец зависит от конфигурации коллекторных пластин и габарита коллектора.
Коллекторные пакеты диаметром до 60 мм, не имеющие выступающих петушков, прессуют в цилиндрических кольцах. Для достижения требуемого распора пластин диаметр пакета в результате прессовки приходится изменять значительно. Поэтому во избежание повреждений (задиров, смятия) пластин используют несколько прессовочных колец (до трех). Каждое последующее кольцо выполнено с меньшим диаметром отверстия. Обычно изменение диаметра не превышает 0,6 мм.
а) |
|
|
б) |
||||
|
|
Р |
|||||
|
|
||||||
1 |
|
|
|
|
|
|
Р |
|
1 |
|
|
||||
|
|
|
|
||||
2 |
2 |
|
|
|
|
||
|
|
|
|
||||
|
|
|
|
3 |
5 |
4 |
6 |
|
|
|
4 |
Рис. 51. Прессовка в цилиндрических кольцах: 1-коллекторный пакет; 2-первое кольцо; 4 -опора; 5 – проставка; 6-второе кольцо
Операция опрессовки в цилиндрических кольцах показана на рис. 51., где показано (а) запрессовка пакета 1 в первое кольцо 2, а затем (б) – перепрессовка его в последующее кольцо. Первая прессовка выполняется при нормальной
90