
2835.Проблемы разработки месторождений углеводородных и рудных полезных и
..pdf
Секция 2. Бурение нефтяных и газовых скважин
ЗАКОЛОННЫЕ ПЕРЕТОКИ И АНАЛИЗ ПРИЧИН ИХ ПОЯВЛЕНИЯ
А.И. Пискунов
Научный руководитель – д-р техн. наук, профессор А.А. Яковлев Национальный минерально-сырьевой университет « Горный»
В настоящее время в России в результате появления заколонных перетоков требуют капитального ремонта или даже ликвидации сотни скважин. Это происходит вследствие появления заколонных перетоков, которые приводят к преждевременному обводнению скважин, неподтверждению начальных запасов углеводородов, а также создают угрозу для окружающей среды и безопасности людей.
Ключевые слова: скважина, цементирование, заколонные перетоки, градиент давления, эксцентриситет колонны.
В настоящее время большинство исследователей склоняется к тому, что силой, побуждающей пластовый флюид к движению в заколонное пространство
впериод ожидания затвердевания цемента (ОЗЦ), является градиент давления, действующий по направлению из пласта в скважину, который возникает вследствие снижения с течением времени первоначального давления столба тампонажного раствора [1, 6].
Заколонные движения флюидов из пласта начинаются еще при ОЗЦ, в процессе формирования цементного камня. Газ и жидкость могут проникать из пласта
вцементное кольцо за обсадной колонной и мигрировать в нем только при условии превышения давления в продуктивном пласте над давлением за колонной, которое может быть только гидростатическим. Гидростатическое давление за обсадной колонной может быть создано только столбом жидкости или текучего вещества, но не камня. Миграция газа начинается при ОЗЦ в результате уменьшения гидростатического давления, создаваемого столбом цементного раствора при его затвердевании. Градиент гидростатического давления уменьшается сначала до давления, создаваемого жидкостью затворения цемента, и становится равным нулю по окончании схватывания цемента, поскольку цементный камень не имеет текучести [5].
Таким образом, в какой-то момент давление столба цементного раствора становится ниже пластового давления и флюид из пласта начинает двигаться по заколонному пространству. Анализируя причины появления этих каналов, можно условно их разделить на две группы: появляющиеся во время ОЗЦ и после ОЗЦ.
Причины появления каналов в заколонном пространстве во время ОЗЦ.
В процессе ОЗЦ в цементном камне образуются каналы, главные причины появления которых приведены на рис. 1 и 2.
Осложнения, возникающие при спуске и цементировании обсадной колонны, могут привести к возникновению условий, ведущих к нарушению разобщенности продуктивных зон. Одной из самых распространенных проблем является эксцентриситет колонны из-за неправильного размещения центраторов. Как и все жид-
141
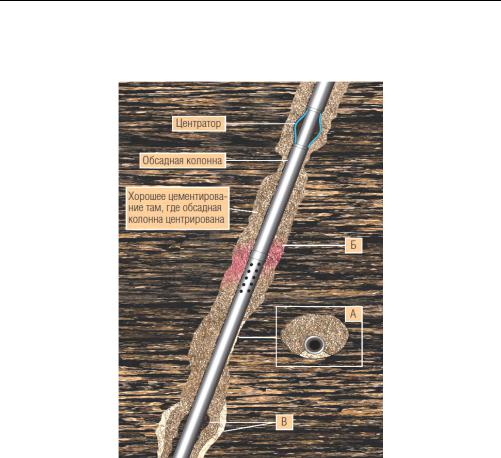
Проблемы разработки месторождений углеводородных и рудных полезных ископаемых
кости, цементный раствор при вытеснении ищет путь наименьшего сопротивления и течет по более широкой части заколонного пространства, оставляя незаполненным сужение между колонной и пластом.
Рис. 1. Причины некачественного разобщения пластов
Это пространство может стать каналом для миграции флюидов (см. рис. 1, А). Неправильно подобранная плотность раствора может стать причиной прорыва в ствол скважины (Б) пластового газа, который ослабит цемент или создаст
в нем зазоры. Цементный камень может начать разрушаться под действием напряжений, вызванных изменениями температуры и давления в скважине. Геометрия областей размыва (В) часто обусловливает недостаточные скорости потока при промывке скважины и повышенные отложения глинистой корки. Оставленные таким образом загрязнения в скважине создают ослабления в цементном кольце, которые при их большом количестве или объеме превращаются в каналы для заколонных перетоков [4].
Главные определяющие параметры в процессе цементирования приведены на рис. 2 в том порядке, в котором они обычно имеют место. Неправильно подобранная плотность может привести к нарушению гидростатического равновесия. Некачественное удаление бурового раствора и/или фильтрационной корки оставляет каналы, по которым флюид поднимается по затрубью. Преждевременное загустевание выражается в потере гидростатического давления. Чрезмерная водоот-
142
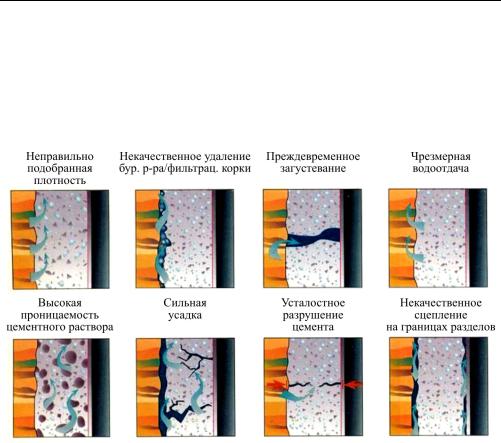
Секция 2. Бурение нефтяных и газовых скважин
дача создает свободное пространство в столбе цемента, в которое поступает флюид. Высокопроницаемые цементные растворы дают некачественную зоноизоляцию, оказывающую слабое сопротивление потоку флюида. Высокая объемная усадка цемента ведет к образованию микрокольцевого пространства. Усталостное разрушение цемента способствует разрыву цементного кольца. Плохое сцепление цемента может вызвать нарушения на границах раздела цемент – обсадная колонна и цемент – порода [5].
Рис. 2. Причины образования каналов в заколонном пространстве во время ОЗЦ
Причины появления каналов в заколонном пространстве после ОЗЦ.
Даже качественное цементирование может оказаться неэффективным из-за последующего изменения режима нагружения скважины, связанного с изменением температуры и давления; испытанием обсадных колонн на герметичность избыточным давлением, которое осуществляется после ОЗЦ; перфорацией обсадных колонн; ударами долота и бурильных труб о стенки обсадной колонны; воздействием тектонических напряжений.
Под действием тектонических напряжений и резкого увеличения давления или температуры в скважине цементное кольцо может треснуть или даже распасться на куски. Смещение обсадной колонны, вызываемое общей усадкой цементного камня или понижением температуры и давления в скважине, может привести к одновременному изменению касательных и радиальных напряжений и последующему разрушению цемента под действием растяжения или сжатия либо его отрыву от обсадной колонны или пород с образованием микрозазоров [4].
В работе [2] показано, что при испытании обсадных колонн на герметичность происходит разрушение цементного камня за колонной с образованием вертикальных микротрещин по всей длине цементного кольца.
143

Проблемы разработки месторождений углеводородных и рудных полезных ископаемых
Таким образом, можно сделать вывод, что основной причиной появления заколонных перетоков является градиент давления, действующий по направлению из пласта в скважину, который возникает вследствие снижения с течением времени гидростатического давления столба цементного раствора. В какой-то момент давление столба цементного раствора становится ниже пластового давления и флюид из пласта начинает двигаться по каналам в заколонном пространстве, которые могут образовываться как во время ОЗЦ, так и после ОЗЦ.
Список литературы
1.Куксов A.K., Черненко A.B. Заколонные проявления при строительстве скважин // ОИ. Сер.: Техника и технология скважин / ВНИИОЭН. – М., 1988. – 48 с.
2.Леонов Е.Г. Отчет по теме № 202-95. Разработка системы контроля качества строительства скважин на Заполярном ГНКМ с целью предотвращения межколонных газопроявлений. – М., 1996.
3.Обеспечение эффективного разобщения пластов после окончания эксплуатации скважины // Нефтегазовое обозрение. – 2008. – Т. 20, № 1. – С. 22–37.
4.Райкевич С.И. Межколонные давления и заколонные движения флюидов
вскважинах. Пути решения проблемы // Интенсификация добычи нефти: тр. междунар. технол. симпоз., г. Москва, март 2003 г. / Ин-т нефтегаз. бизнеса. – М.,
2003. – С. 579–587.
5.Сулейманов И.А. Причины заколонных проявлений и пути их предотвращения при креплении скважин на площади Муратханлы // Бурение глубоких нефтяных и газовых скважин в Азербайджане. – Баку: Азнипинефть, 1983. – С. 40–48.
6.Шахмаев З.М. Особенности технологии цементирования скважин при наличии проницаемых пластов с разными градиентами давления // Нефтегазовая геология, геофизика и бурение. – 1984. – Вып. 3. – С. 43–45.
144

Секция 2. Бурение нефтяных и газовых скважин
ИССЛЕДОВАНИЕ ВЛИЯНИЯ МИНЕРАЛЬНЫХ ДОБАВОК НА ПРОЧНОСТНЫЕ ХАРАКТЕРИСТИКИ ТАМПОНАЖНОГО КАМНЯ
Д.Ю. Русинов
Научный руководитель – А.А. Куницких Пермский национальный исследовательский политехнический университет
Рассмотрено влияние минеральных добавок на прочность цементного камня. Выявлено оптимальное содержание добавки, необходимое для достижения максимальной прочности.
Ключевые слова: крепление нефтяных скважин, растекаемость цементного раствора, технология цементирования, качество крепления, прочность цементного камня.
Тампонажный камень должен обладать, во-первых, низкой проницаемостью, во-вторых, хорошей адгезией к горным породам и обсадной колонне, в-третьих, высокими прочностными показателями.
На проницаемость и прочностные параметры тампонажного камня влияют как характеристики самого камня, так и условия, в которых происходит гидратация и твердение образцов.
Были проведены исследования со следующими минеральными добавками: кварцевая мука марки КМ-0,05 (ОАО ТД «Кварц»), диабазовая мука (ООО «Диабаз»), метакаолин марки MetaCem 85C (ООО «ХимПартнеры»), микрокремнезем неуплотненный марки МК-85, микрокремнезем уплотненный марки МКУ-85, ФАМ, ПОК (пудра оксида кремния) (ООО «МАН»).
Испытания проводились на цементе марки ПЦТ-I-G-CC-1 (ОАО «Сухоложскцемент»). В качестве базовой рецептуры использовался цементный раствор с В/Ц = 0,49, в который кроме цементного порошка входили гидроксиэтилцеллюлоза (0,2 % от массы вяжущего) и пеногаситель (0,03 % от массы вяжущего). Минеральные добавки вводились в сухую смесь в количестве 1; 1,5; 2; 3; 5; 7; 10 % от массы цементного порошка. Исследование прочности тампонажного камня на изгиб проводилось на образцах-призмах размером 20 × 20 × 80 мм, выдерживаемых при температурах 24 и 70 °С в ванне с пресной водой. Прочностные показатели камня определялись по результатам испытаний на изгиб как среднее арифметическое трех наибольших результатов из четырех [1]. Испытания проводились через 24; 48 и 72 ч твердения.
По данным проведенных исследований выявили, что оптимальный объем добавки кварцевой муки составляет 1 % для температуры 24 и 2 % для температуры 70 °С. Прирост прочности на изгиб относительно базовой рецептуры составил 8,2 и 23,7 % для температур 24 и 70 °С соответственно. Значительное повышение прочности цементного камня при повышенной температуре объясняется увеличением активности кварца (кварц становится активной добавкой при температурах выше 60 °С [2]) и, соответственно, его участием в структурообразовании.
145

Проблемы разработки месторождений углеводородных и рудных полезных ископаемых
Оптимальное содержание диабазовой муки в тампонажном растворе составило 1 % для 70 и 1,5 % для 24 °С. Повышение прочности составило 0,6 и 10,9 % соответственно для 24 и 70 °С. Увеличение прочностных параметров в «горячих» условиях можно объяснить родственным химическим составом диабазовой муки и портландцемента. Как и в случае с кварцевым песком, рост прочности при повышенных температурах обусловлен увеличением активности добавки.
Наибольшие прочностные показатели на изгиб с добавкой метакаолина получили при его содержании в смеси 10 и 7 % соответственно для «горячих»
и«холодных» условий. Прирост прочности на изгиб составил 22,6 и 21,4 % для 70 и 24 °С соответственно. По химическому составу метакаолин представляет собой аморфный силикат алюминия, что обусловливает его участие в формировании структуры камня. Обладая высокой удельной поверхностью и высокой пуццоланической активностью, метакаолин повышает плотность структуры твердеющего раствора и связывает гидратную известь, что улучшает прочностные параметры камня.
По результатам исследования прочностных показателей цемента с добавкой ФАМ наибольший эффект получили при вводе 1 % добавки. Прирост прочности 2,1 % для «горячих» условий. В условиях низких температур наблюдается снижение прочности относительно базового состава на 2,4 %.
Весьма эффективно повышает прочность тампонажного камня добавка микрокремнезема марок МК-85 и МКУ-85. Наилучшие показатели с добавкой МК-85 достигнуты при его содержании в тампонажной смеси в количестве 3 и 10 % для 70 и 24 °С соответственно. Повышение прочности составило 9,1 % для «горячих»
и10,1 % для «холодных» условий. В случае с добавкой МКУ-85 прирост прочности составил 4,8 % для условий низких температур при объеме добавки 7 и 11,3 %, для условий высоких температур при объеме добавки 3 %. Ввиду высокой дисперсности микрокремнезема он обладает значительной водопоглощающей способностью. Для сохранения необходимой подвижности тампонажного раствора при содержании микрокремнезема более 5 % дополнительно вводили поликарбоксилатный пластификатор в количестве 0,08 % от массы цемента. Основным компонентом микрокремнезема является диоксид кремния аморфной модификации. Рост прочности камня объясняется мелким гранулометрическим составом (2 мкм)
ивесьма высокой пуццолановой активностью микрокремнезема, что способствует его взаимодействию с гидроксидом кальция, образующимся при затворении цемента, и значительному уплотнению структуры камня.
Наилучшие результаты показала добавка ПОК. Максимальные значения предела прочности на изгиб достигнуты при вводе в тампонажную смесь 5 и 10 % соответственно для температур 24 и 70 °С. Относительно базового состава прочность выросла на 39,1 % для «холодных» и 50,4 % для «горячих» условий. ПОК представляет собой ультрадисперсный порошок, состоящий из наносферических частиц размером менее 0,5 мкм. В его составе содержится не менее 85 % аморфного оксида кремния. Высокие значения увеличения проч-
146

Секция 2. Бурение нефтяных и газовых скважин
ности тампонажного камня на изгиб связаны прежде всего с размером частиц и повышением активности ПОК при умеренных температурах. ПОК обладает высокой водопоглощающей способностью, поэтому для обеспечения требуемых значений растекаемости при содержании ПОК более 5 % в тампонажный раствор дополнительно вводили поликарбоксилатный пластификатор в количестве 0,16 % от массы цемента.
Очевидно, что для получения максимальной прочности тампонажного камня в цементе должны присутствовать добавки различного гранулометрического состава, поэтому дальнейшие эксперименты будут направлены на исследование влияния комбинаций представленных минеральных добавок на прочность цементного камня.
Список литературы
1.Булатов А.И. Формирование и работа цементного камня в скважине. – М.:
Недра, 1990. – 409 с.
2.Данюшевский В.С., Алиев Р.М., Толстых И.Ф., Справочное руководство по тампонажным материалам. – 2-е изд., перераб. и доп. – М.: Недра, 1987. – 373 с.
147
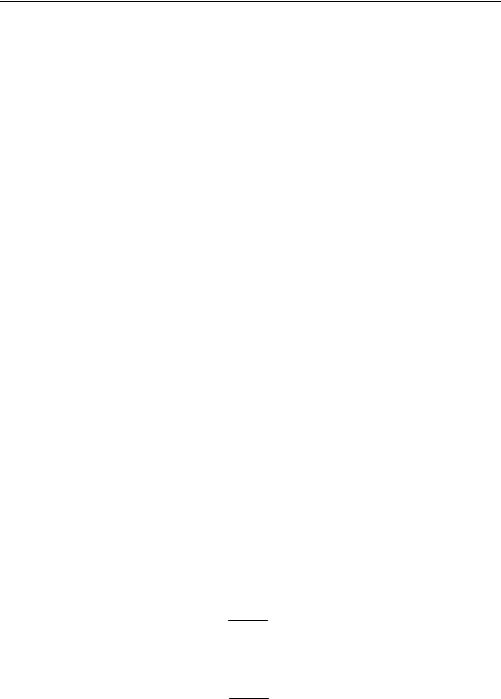
Проблемы разработки месторождений углеводородных и рудных полезных ископаемых
МОДЕРНИЗАЦИЯ ШЛАМОВОГО НАСОСА ПОВЕРХНОСТНОЙ ЦИРКУЛЯЦИОННОЙ СИСТЕМЫ ОЧИСТКИ БУРОВОГО НАСОСА
А.В. Селезнев
Научный руководитель – канд. техн. наук, доцент И.А. Пахлян
Армавирский механико-технологический институт (филиал) Кубанского государственного технологического университета
Рассмотрены вертикальные шламовые насосы. Представлена разработанная конструкция усовершенствованного шламового насоса.
Ключевые слова: очистка бурового раствора, поверхностная циркуляционная система, вертикальный шламовый насос, долговечность, надежность.
Вертикальные шламовые насосы широко используются в нефтегазовой промышленности. Данные насосы являются одной из составляющих буровой установки, которые влияют на работоспособность, от них зависит бесперебойная работа и производительность циркуляционного комплекса.
Одной из важных характеристик шламового насоса является его технический ресурс. Средний срок службы насоса составляет 20 000 ч, а наработок на отказ – 340 ч. Если сравнивать эти показатели с показателями другого оборудования, то они значительно меньше. В связи с вышеупомянутым ставится цель повысить надежность и долговечность шламовых насосов. Только повышение технического ресурса на 12 % позволит одному насосу работать бесперебойно дополнительно приблизительно 41 ч [1]. Определим, сколько за 41 ч труда насос будет иметь возможность дополнительно перекачивать рабочей жидкости, с помощью формулы
Q = g t, |
(1) |
где g – подача насоса, g = 150 м3/ч; t – дополнительный срок, t = 41 ч. После подстановки числовых значений в формулу (1) имеем
Q =150 41 = 6150 м3.
Количество технических обслуживаний до усовершенствования насоса
n1 = 20 000 =59. 340
Количество технических обслуживаний после усовершенствования насоса
n2 = 20 000 =53. 381
Если принимать во внимание, что срок технического обслуживания составляет 3 ч, то для выполнения технического обслуживания по старому варианту понадобится время
148

Секция 2. Бурение нефтяных и газовых скважин
T = n1 t , |
(2) |
где n1 – количество технических обслуживаний, n1 = 59; t – время технического обслуживания, t = 3 ч; после подстановки числовых значений в формулу (2) имеем
T = 59 3 =177 ч;
для выполнения технического обслуживания усовершенствованного насоса понадобится время
T =53 3 =159 ч.
Как видим, техническое предложение предоставит возможность уменьшить время технического обслуживания на 18 ч.
Патентная проработка осуществлялась на официальном сайте Федерального государственного бюджетного учреждения «Федеральный институт промышленной собственности» (http://www.1.fips.ru) по патентным документам [2, 3, 4 и др.].
Аналог был выявлен в изобретении [2]. Изобретение относится к насосостроению и может быть использовано для перекачки вод, содержащих абразивные частицы промывочного раствора. Изобретение направлено на повышение надежности работы и срока службы и расширение технологических возможностей.
Наиболее близкой по технической сущности является полезная модель «Насос шламовый вертикальный» [4]. Полезная модель относится к средствам, предназначенным для перекачивания сыпучих материалов (шламов) в напорном потоке жидкости.
Предлагаемая полезная модель решает задачу повышения надежности работы насоса в подземных выработках при значительных колебаниях концентрации и крупности шлама в гидросмеси, поступающей к насосу, а также надежного запуска его в условиях завала тем, что входной патрубок насоса огражден перфорированной решеткой, а рабочее колесо оснащено дополнительным валом, выходящим за решетку, на конце которого жестко установлен элемент, выполняющий роль рыхлителя шлама.
Также полезная модель решает задачу повышения надежности работы насоса в подземных выработках при значительных колебаниях концентрации и крупности шлама, поступающего к насосу, а также надежного запуска его в условиях завала.
На основании выполненной патентной проработки и выявленных недостатков аналога и прототипа была разработана конструкция усовершенствованного вертикального шламового насоса.
Вертикальные шламовые насосы являются одной из составляющих буровой установки, от которых зависит бесперебойная работа и производительность циркуляционного комплекса. Но условия, в которых они работают, очень сильно влияют на время бесперебойной работы насосов.
К основным факторам, которые снижают долговечность шламовых насосов, принадлежат:
– содержимое в растворе твердых абразивных примесей;
149
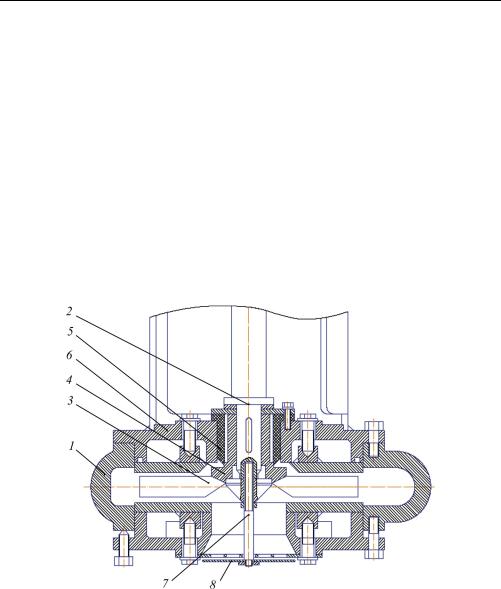
Проблемы разработки месторождений углеводородных и рудных полезных ископаемых
–неоднородность бурового раствора по фракционному составу;
–режим работы шламовых насосов;
–характер нагрузки шламовых насосов.
Разработанная конструкция шламового насоса, которая почти полностью устраняет указанные недостатки, представлена на рисунке.
Усовершенствование заключается в том, что насос шламовый вертикальный включает в себя корпус 1, внутри которого помещено посаженое на вал 2 рабочее колесо 3 со ступицей 4 и лопатками, при этом верхний конец вала насоса закреплен в подшипниковой опоре 5, установленной в станине насоса 6, а ступица 4 колеса 3 закреплена в подшипнике буксы насоса, причем рабочее колесо оснащено дополнительным валом 7, на конце которого жестко установлен элемент, исполняющий функцию рыхлителя шлама 8, а ступица рабочего колеса насоса размещена внутри втулки подшипника скольжения, жестко соединенного с упругими элементами демпфера, установленного в буксе насоса. Элемент рыхлителя выполнен двухлопастным и установлен симметрично относительно оси вала рыхлителя.
Рис. Усовершенствованная конструкция насоса ВШН-150: 1 – корпус; 2 – вал; 3 – рабочее колесо; 4 – ступица; 5 – подшипниковая опора; 6 – станина насоса; 7 – дополнительный вал; 8 – рыхлитель шлама
Такая конструкция вертикального шламового насоса поможет улучшить режим его работы за счет того, что при вращении приводного вала жидкость, которая находится во всасывающей части насоса, будет вспушиваться, а также будут разбиваться комки, что благотворно скажется на работе насоса. Это, в свою очередь, улучшит степень исключения шлама из шламонакопителя, т.е. позволит уменьшить расходы на утилизацию шлама, поскольку уменьшится периодичность чистки шламонакопителя.
150