
2802.Трещиностойкость железоуглеродистых сплавов
..pdf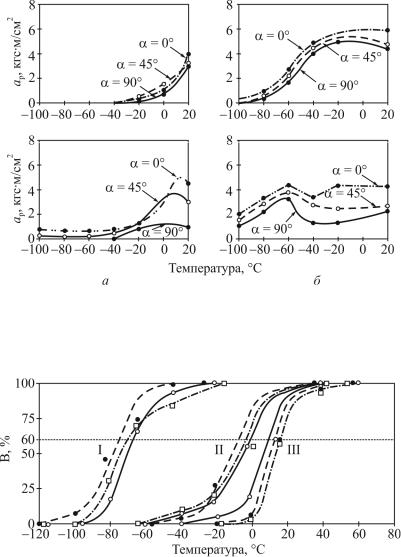
Рис. 3.72. Зависимость работы зарождения aз и развития ap трещины для
стали 17ГС от температуры испытания: а – после горячей прокатки; б – после термоулучшения (закалка +отпуск при 600оС); α = 90о – поперечные
образцы, α = 45 о, α= 0 о – продольные образцы
Рис. 3.73. Зависимость вида излома (В, %) для стали 17ГС от температуры испытания: I – после термоулучшения (закалка + отпуск при 600 оС);
II – после нормализации; III – после прокатки; α = 90о – поперечные образ-
цы (сплошная линия); α = 45 о – штриховые линии; α = 0 о – продольные образцы (штрих-пунктирные линии)
281
горячей прокатки – минус 20 оС, после нормализации – минус 60 оС и в улучшенном состоянии – минус 100 оС. Следовательно, эффект от подходящего расположения листового материала в данной конструкции по отношению к действующим усилиям при отсутствии трещин можно ожидать только при температуре Т > Ткα.
Проведенные исследования показывают, что трещиностойкость листовой низкоуглеродистой стали при ударном нагружении в данном случае практически не зависит от ориентации плоскости движения самой трещины по отношению к направлению прокатки.
3.12. Влияние размера зерна, количества перлита и игольчатых структур на трещиностойкость углеродистых сталей
Измельчение зерна является одним из эффективных факторов, благоприятствующих повышению трещиностойкости низкоуглеродистых и низколегированных сталей. Особенно важно то обстоятельство, что увеличение трещиностойкости сопровождается одновременным повышением предела текучести материала. На рис. 3.74 [39]
показано снижение критической температуры Tê12àð , °С, при уменьше-
нии диаметра d ферритного зерна с 6 до 14 номера. Эта зависимость имеет вид
T ap |
= 50,44 − 11,20 d −1/2 . |
(3.1) |
к12 |
|
|
Необходимо отметить, что с уменьшением размера зерна интенсивность, с которой снижается указанная критическая температура, растет. Так, например, измельчение зерна с 6 до 7 номера и с 11 до 12 номера снижает критическую температуру на 10 и 25 оС соответственно.
Зависимость предела текучести σ0,2 , МПа, от диаметра зерна d представлена на рис. 3.75 [39] и описывается уравнением
σ0,2 = 178 + 26 d −1/2 . |
(3.2) |
282
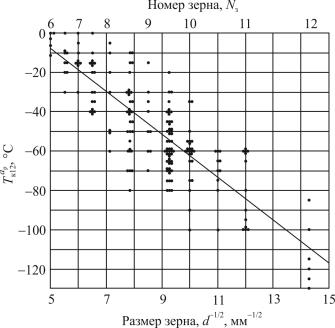
Рис. 3.74. Влияние размера ферритного зерна в низкоуглеродистых сталях на критическую температуру хрупкости
Уменьшение размера зерна и в этом случае является причиной немонотонного роста предела текучести. Так, увеличение номера зерна от 6 до 7 и от 11 до 12 ведет к возрастанию σ0,2 соответственно
на 25 и 60 МПа.
При наличии разнозернистости в структуре раньше всего начинают охрупчиваться самые крупные зерна, и они лимитируют верхний порог хладноломкости по виду излома (В, %). При дополнительном снижении температуры начинают хрупко разрушаться все более мелкие зерна. Таким образом, начало процесса хрупкого разрушения определяется не средним размером зерна, а размером крупных зерен.
Из представленных на рис. 3.76 данных видно, что увеличение содержания перлита в структуре уменьшает трещиностойкость стали, повышая критические температуры. Аналогичное влияние оказывает и появление игольчатых структур в нормализованных низкоуглеродистых сталях (рис. 3.77).
283
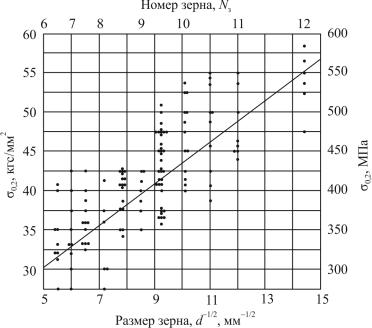
Рис. 3.75. Влияние размера ферритного зерна
внизкоуглеродистых сталях на предел текучести
Всвязи с изучением влияния размера зерна в низколегированных сталях на их трещиностойкость интересно обратить внимание на результаты, полученные в [192].
Исследовали зависимость между размером действительного ферритного зерна и трещиностойкостью низколегированных нормализованных литых и катаных сталей. Изучали литые стали 20Л, 20ГЛ
и20ГСЛ. Образцы вырезали из специально отлитой плиты переменного сечения размером 20(45) х 260 х 400 мм после того, как была отрезана массивная прибыль. Размеры этой прибыли и клинообразное сечение обеспечивало получение плотного литого металла.
Катаные стали содержали 0,2 % С, 0,2 % Si и 1,2 % Mn. Определяли
работу, израсходованную на развитие трещины ар, по методике Отани при испытании стандартных образцов на трехточечный ударный изгиб.
Были построены сериальные зависимости ар ≈ f оС, на которых по критериальным значениям ар = 15 Дж/см2 определяли критические темпера-
284
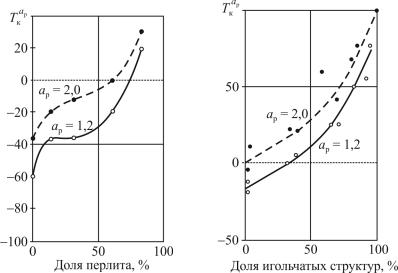
туры Tê15ap . Полученные результаты представлены на рис. 3.78. На
рис. 3.78, а, б показаны экспериментальные точки, полученные соответственно для катаных и литых сталей, а также соответствующие линейные регрессионные зависимости, которые на рис. 3.78, в представлены совместно. Видно, что при одном и том же размере зерна литые стали имеют лучшую трещиностойкость. Этот, в известном смысле, неожиданный результат связан, вероятно, с тем обстоятельством, что в литом металле приграничные области соседних зерен значительно проникают одна в другую и при соответствующей пространственной разориентировке этих зерен граница, сформированная таким образом, оказывает большее сопротивлениеразвивающейся трещине.
Рис. 3.76. Влияние доли перлита на критическую температуру хрупкости
Рис. 3.77. Влияние количества иглообразных структур в низкоуглеродистых легированных сталях на критическуютемпературухрупкости
Прокатка, дробя, с одной стороны, грубую структуру литого металла, увеличивает его трещиностойкость, но, с другой стороны, ликвидируя это взаимное проникновение в приграничных областях соседних зерен, «сглаживая» границы между ними до известной степени, уменьшает трещиностойкость металлической матрицы. Вероятно,
285
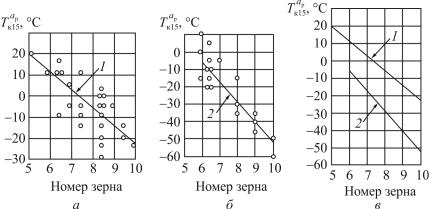
разница в состоянии границ является причиной того, что при одном и том же размере зерна литые стали обладают лучшей трещиностойкостью, чем катаные.
Рис. 3.78. Зависимость критической температуры от размера ферритного зерна: 1 – катаные стали; 2 – литые стали
3.13.Циклическая трещиностойкость сталей
сферритомартенситной структурой
Стали с ферритомартенситной структурой являются относительно новым классом конструкционных материалов. Обычно это низкоуглеродистые, низколегированные стали, закаленные в воде после нагрева в межкритическом температурном интервале Ас1 – Ас3 (см. рис. 1.42). Образованное при этих температурах определенное количество аустенита в процессе закалки превращается в мартенсит. В результате в структуре присутствуют одновременно феррит и мартенсит. В зависимости от температуры нагрева под закалку их количество будет различным. При этом при более низких температурах нагрева аустенит содержит больше углерода, в результате чего образующийся мартенсит имеет пластинчатую структуру. Наоборот, при более высоких температурах (близких к Ас3) аустенит содержит меньше углерода, в результате чего полученный после закалки мартенсит является мартенситом реечного типа. Это хорошо видно нарис. 3.79.
286
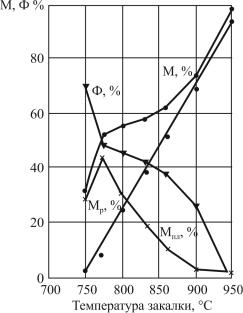
Рис. 3.79. Изменение количества феррита (Ф, %) и мартенсита (М, %) в стали 09Г2Д в зависимости от температуры закалки: Ф, % – количество феррита; М, % – количество мартенсита; Мр, % – количество реечного (пакетного)
мартенсита; Мпл, % –количество пластинчатого мартенсита
Типичные структуры, полученные при различных температурах закалки стали 09Г2С из межкритического интервала, представлены на рис. 3.80 [274]. Для этих структур характерна мартенситная оболочка вокруг ферритного зерна (рис. 3.80, а) при низких температурах закалки.
Литературных данных [269–271] о циклической трещиностойкости таких сталей не особенно много, и они очень противоречивы, что в известном смысле естественно, если иметь в виду сложный набор различного количества структурных составляющих, которые можно получить (см. рис. 3.79).
Рассмотрим некоторые результаты, полученные при исследовании циклической трещиностойкости сталей 06Г2АФ и 09Г2Д [268]. Их химический состав представлен в табл. 3.27.
287

Рис. 3.80. Микроструктура стали 09Г2Д после закалки от 750 °С (a); 800 °C (б) и 860 °C (в)
Таблица 3 . 2 7 Химический состав сталей 06Г2АФ и 09Г2Д
Марка |
C |
Si |
Mn |
Cu |
N |
V |
стали |
|
|
|
мас. % |
|
|
09Г2Д |
0,10 |
0,30 |
1,65 |
0,27 |
– |
– |
06Г2АФ |
0,08 |
0,24 |
1,32 |
– |
0,022 |
0,08 |
Термообработка состояла из закалки от температуры 750–950 °C, охлаждения в воде и отпуска при 200 °C в течение 2 часов. Испытывали поперечные образцы. Циклическую трещиностойкость изучали на компактных образцах (см. рис. 2.33) размером 62,5х60,0х10 мм. Испытания проводили с коэффициентом асимметрии R = 0,05 и частотой 14 Hz. Механические свойства представлены в табл. 3.28.
Результаты, полученные при исследовании циклической трещиностойкости, представлены на рис. 3.81 и 3.82. В начале координатной системы даны значения, полученные для горячекатаной структуры. Эти значения условно соединены пунктирной линией с результатами, полученными после закалки от 750 °C. Показаны изменения K в зависимо-
288
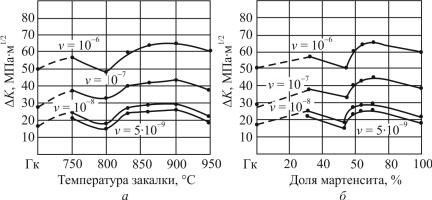
сти от температуры закалки (рис. 3.81, а и 3.82, а) и от процентного содержания мартенсита (рис. 3.81, б и 3.82, б) при данной скорости развития усталостной трещины (например, v = 10–8м/цикл).
Таблица 3.28 Механические свойства сталей 09Г2Д (A) и 06ГАФ(Б)
Режим |
Характеристики механических свойств |
|||||||
термообработки |
σ0,2 МПа |
σв МПа |
δ, % |
ψ, % |
||||
|
А |
Б |
А |
Б |
А |
Б |
А |
Б |
Горячекатаная |
325 |
425 |
575 |
520 |
28 |
28 |
64 |
70 |
Закалка от температуры, °C |
|
|
|
|
|
|
|
|
750 |
530 |
445 |
825 |
660 |
16 |
21 |
40 |
57 |
780 |
525 |
400 |
830 |
630 |
15 |
23 |
42 |
63 |
800 |
585 |
380 |
855 |
620 |
12 |
24 |
41 |
64 |
830 |
750 |
405 |
1020 |
650 |
7 |
24 |
38 |
65 |
860 |
855 |
460 |
1100 |
715 |
7 |
17 |
41 |
66 |
900 |
925 |
600 |
1120 |
745 |
8 |
20 |
41 |
62 |
950 |
930 |
520 |
1100 |
690 |
8 |
23 |
42 |
67 |
Рис. 3.81. Влияние температуры закалки (a) и процента мартенсита в структуре (б) на циклическую трещиностойкость стали 09Г2Д
Анализ этих данных показывает, что циклическая трещиностойкость стали 06Г2АФ во всех случаях больше, чем у стали 09Г2Д. При
этом наблюдаемая разница незначительна на низкоамплитудном участке диаграммы (около 3–5 МПа·м1/2 при v = 10–8 м/цикл), в то время как
289
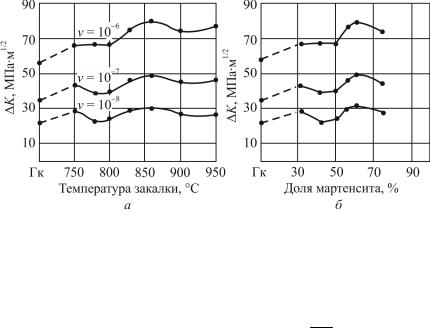
на высокоамплитудном (около 10–15 МПа·м1/2 при v ≈ 10–6 м/цикл) становится существенной. Появление ~30 % мартенсита в структуре (tзак = 750 °C) повышает циклическую трещиностойкость по сравнению с горячекатаным состоянием. Дальнейшее увеличение количества мартенсита в структуре примерно до 50 % (tзак = 800 °C) ведет к известному уменьшению трещиностойкости. Наиболее высокая трещиностойкость для исследуемых сталей получается при наличии 60–70 % мартенсита в структуре (tзак = 860–900 °C).
Рис. 3.82. Влияние температуры закалки (a) и процента мартенсита
вструктуре (б) на циклическую трещиностойкость стали 06Г2АФ
Взаключение необходимо отметить, что эти стали, закаленные из нижней части межкритического температурного интервала (750–
780 °C), имеют хорошие пластические свойства ( σ0,2 ≈ 0,6, ψ ≈ 50 %)
σв
при достаточно высокой прочности. Это является причиной, из-за которой они все шире применяются для глубокой вытяжки в автомобильной промышленности. Их использование в качестве конструкционного материала с высокой прочностью и циклической трещиностойкостью требует режимов термообработки из верхней области межкритического температурного интервала (860–900 °C), которые обеспечивают в структуре ~70 % мартенсита и ~30 % феррита.
290