
2802.Трещиностойкость железоуглеродистых сплавов
..pdf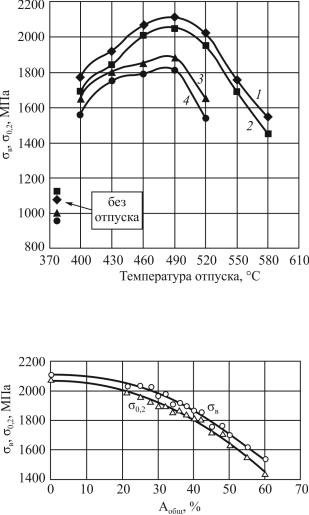
пытания выше 40 оС ударная вязкость меняется значительно. Когда структура включает мартенсит + Аост (см. рис. 6.22, 3) или мартен-
сит + Аост+ Арев (см. рис. 6.22, 4), изменение ударной вязкости имеет экстремальный характер с максимумом при температуре испытания
в интервале +20…– 40 оС.
Рис. 6.18. Влияние температуры отпуска на предел прочности (1, 3) и предел текучести (2, 4) стали 03Н18К9М5Т с исходной мартенситной (1, 2) и мар- тенситно-аустенитной (3, 4) структурой
Рис. 6.19. Влияние общего количества аустенита (Аобщ) на характеристики прочности стали 03Н18К9М5Т
381
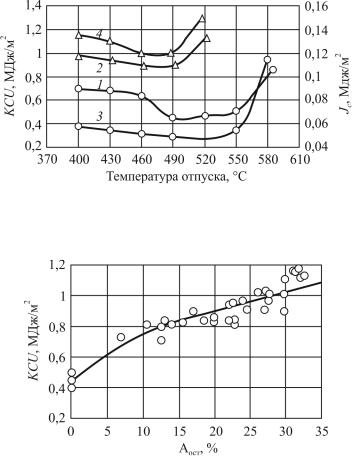
Рис. 6.20. Влияние температуры отпуска на ударную вязкость (1, 2) и вязкость разрушения (3, 4) стали Н18К9М5Т с исходной мартенситной (1, 3)
и мартенситно-аустенитной (2, 4) структурой
Рис. 6.21. Влияние количества Аост на ударную вязкость стали Н18К9М5Т после отпуска при 490 °С
Результаты оценки степени превращения γ→α в процессе определения ударной вязкости представлены на рис. 6.22, б. Видно, что Арев не претерпевает превращения даже до температуры жидкого азота (см. рис. 6.22, 2), в то время как в случае, когда в структуре при охлаждении образуется Аост, его превращение начинается при температуре +100 оС, чтобы достигнуть 100 % при –196 оС (см. рис. 6.22, 3). В стали, содержащей два типа аустенита (% Аост ≈ % Арев), интенсивность превраще-
382
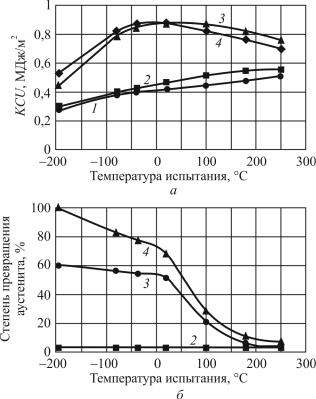
ния в процессе проведения ударных испытаний в жидком азоте примерно 60 % (см. рис. 6.22, 4). Это дает основание считать, что в стали 03Н18К9М5Т деформационное γ→α превращение претерпевает только Аост, в то время как Арев разрушается без превращения.
Рис. 6.22. Влияние температуры испытания на ударную вязкость (а) и степень превращения аустенита (б) стали 03Н18К9М5Т с различной структурой: 1 – мартенсит; 2 – мартенсит + ревертированный аустенит (40 %); 3 – мартенсит + остаточный аустенит (35 %); 4 – мартенсит + остаточный аустенит (20 %) + ревертированный аустенит (20 %)
Чтобы оценить микромеханизм разрушения исследуемой стали, проведен электронно-фрактографический анализ (рис. 6.23). Изучали центральные участки изломов ударных образцов, разрушенных при
383
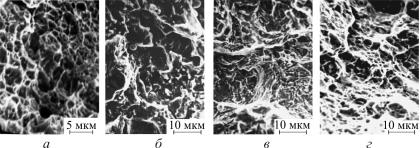
температуре +250, +20 и –196 оС. На поверхности изломов образцов с мартенситной структурой, испытанных при 250 оС, наблюдаются только ямки небольшой глубины, которые определяют относительно небольшую энергоемкость разрушения. Снижение температуры испытания до комнатной (+20 оС) является причиной появления в изломе параллельно с ямками фасеток квазискола. При испытании в жидком азоте (–196 оС) этот вид фасеток становится доминирующей рельефной составляющей изломов образцов с мартенситной структу-
рой (рис. 6.23, а).
Рис. 6.23. Рельеф поверхности ударных образцов стали МС-200 после испытаний в жидком азоте: а – мартенсит; б – мартенсит + 25 % Арев;
в – мартенсит + 20 % Аост; г – мартенсит + 20 % Аост + 20% Арев
В изучаемой стали, при наличии в ней Арев, уже при температуре испытания + 250 оС, одновременно с ямками, которые преобладают на поверхности излома, наблюдаются и фасетки квазискола, окруженные по периферии сильно деформированными волнообразными участками, которые и являются причиной большей вязкости стали с Арев. С понижением температуры количество фасеток квазискола становится преобладающим (рис. 6. 23, б). Кроме того, на поверхности излома появляются гладкие фасетки неправильной формы, которые, по всей вероятности, образуются при передвижении трещины по границам мартенситных пакетов.
Для изломов образцов из стали 03Н18К9М5Т с Аост при температуре +250 оС характерен рельеф, состоящий из мелких плоских ямок,
но наряду с ними наблюдаются и крупные ямки размером 10–15 мкм,
384
которые, однако, глубокие и имеют конусную форму (рис. 6.23, в). Этот вид ямок, образовавшихся в результате ярко выраженной пластической деформации, определяет высокий уровень ударной вязкости стали с А ост. Для образцов, испытанных при 20 оС, сохраняется волокнистый характер излома, но в отдельных случаях начинают появляться и фасетки, волнообразно окруженные сильно деформированными границами. При испытании образцов при –196 оС в изломе образуются фасетки, окруженные специфической сеткой волнообразного рельефа, полученного в результате микропластической деформации. Ячейки этой сетки имеют размер 20–40 мкм, что наводит на мысль, что они образуются по границам бывших аустенитных зерен. Внутри фасеток наблюдается хорошо развитая инфраструктура, состоящая из закономерно расположенных, часто почти параллельных ступенек или волнообразных частиц. В связи с тем что в данном случае интенсивность γ→α-превращения достигает 100 %, можно предположить, что созданный характерный излом является результатом деформационного превращения Аост в мартенсит.
В случаях когда в структуре присутствуют оба типа аустенита (Аост и Арев), ямочный рельеф на поверхности излома является доминирующим, независимо от температуры испытания. При температуре испытания +20 оС на внутренней поверхности конусообразных ямок может наблюдаться микрорельеф в виде выпуклостей и языков. При температуре жидкого азота (–196 оС) конусообразные ямки встречаются реже, но вместо них появляются участки плато (рис. 6.23, г). Возможно, этот рельеф появляется в результате деформационного превращения Аост в условиях преимущественно вязкого разрушения. Результаты, полученные при изучении циклической трещиностойкости, представлены на рис. 6.24. Они показывают, что присутствие в структуре высокопрочной стали известного количества одного или другого аустенита не особенно сильно повышает циклическую трещиностойкость. Этот эффект более заметен в припороговой области, при этом бóльшие значения ∆Kth наблюдаются при наличии в структуре Арев. С увеличением ∆K разница в циклической трещиностойкости сталей с чисто мартенситной структурой и со структурой, содержащей различные типы аустенита, практически исчезает.
385
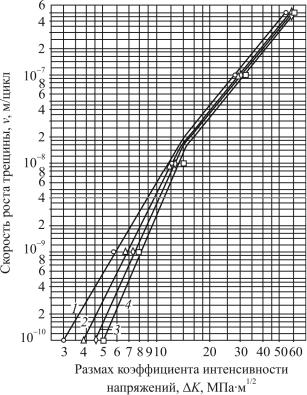
Рис. 6.24. Диаграммы циклической трещиностойкости стали 03Н18К9М5Т с различными типами аустенита: 1 – мартенсит (без аустенита); 2 – мартенсит + 40 % Арев; 3 – мартенсит + 30 % Аост; 4 – мартенсит + 23 % Аост + 23 % Арев
386
ГЛАВА 7 ТРЕЩИНОСТОЙКОСТЬ ВЫСОКОПРОЧНЫХ ФЕРРИТНЫХ ЧУГУНОВ
7.1. Трещиностойкость высокопрочных ферритных чугунов при однократном нагружении
Трещиностойкость чугунов не вызывала интереса исследователей, так как по традиции эти материалы считали неподходящими для производства ответственных деталей. Однако независимо от таких взглядов, благодаря созданной и хорошо усвоенной технологии получения чугунов со сферической формой графитных включений, так называемых сферографитных чугунов, (в России такие чугуны называют высокопрочными), они все чаще используются для производства отдельных деталей, ранее изготавливаемых из сталей. В связи с этим трещиностойкость чугунов в качестве конструкционного материала начинает вызывать интерес [275].
В [276] исследовано влияние легирования углеродом, кремнием, марганцем, никелем, медью и фосфором на трещиностойкость ферритных сферографитных чугунов. Химический состав чугунов представлен в табл. 7.1. Выплавку пробных партий чугунов производили в печи с кислой футеровкой. Внепечная обработка чугуна для сфероидизации графита проведена модификаторами: Fe – 50 % Si – 7 % Mg – 1 % РЗМ и Fe – 75 % Si. Режим плавления: перегрев жидкого металла до температуры 1480–1500 оС, выдержка при этой температуре 15–20 мин. Первичное модифицирование производили по методу «сэндвич», а вторичное «на зеркало жидкого металла». Отливали специальные клинообразные пластины (ГОСТ 2176-77), из которых вырезали образцы для механических испытаний. Термическую обработку чугунов проводили в камерной печи электросопротивления по следующему режиму: нагрев до 930 оС, выдержка 2 ч, охлаждение до 710 оС, выдержка от 2 до 5 ч (в зависимости от химического состава чугуна), охлаждение с печью до 650 оС, охлаждение на воздухе.
387
|
|
|
|
|
|
|
|
Таблица |
7 . 1 |
||
Химический состав и критические температуры хрупкости T ap |
|||||||||||
|
|
|
|
|
|
|
|
|
|
к12 |
|
|
|
исследованных сферографитных чугунов |
|
||||||||
|
|
|
|
|
|
|
|
|
|
|
|
C |
Si |
Mn |
S |
P |
Cr |
Cu |
Ni |
|
Mg |
|
Tкa12p |
1,96 |
1,70 |
0,11 |
0,006 |
0,030 |
0,050 |
0,06 |
0,020 |
|
0,030 |
|
–48 |
2,83 |
1,55 |
0,13 |
0,006 |
0,030 |
0,050 |
0,04 |
0,030 |
|
0,040 |
|
–60 |
3.52 |
1,54 |
0,08 |
0,003 |
0,026 |
0,050 |
0,03 |
0,010 |
|
0,044 |
|
–65 |
4,01 |
1,60 |
0,10 |
0,004 |
0,050 |
0,050 |
0,02 |
0,010 |
|
0,036 |
|
–80 |
4,06 |
1,27 |
0,10 |
0,011 |
0,050 |
0,050 |
0,04 |
0,020 |
|
0,037 |
|
–93 |
3,97 |
1,64 |
0,10 |
0,002 |
0,050 |
0,050 |
0,02 |
0,020 |
|
0,036 |
|
–80 |
4,00 |
2,31 |
0,10 |
0,009 |
0,050 |
0,050 |
0,03 |
0,020 |
|
0, 046 |
|
–58 |
3,74 |
2,91 |
0,09 |
0,005 |
0,050 |
0,060 |
0,02 |
0,020 |
|
0,044 |
|
–10 |
3,70 |
3,75 |
0,13 |
0,006 |
0,030 |
0,054 |
0,05 |
0,020 |
|
0,028 |
|
– |
3,68 |
1,52 |
0,07 |
0,003 |
0,016 |
0,054 |
0,03 |
0,010 |
|
0,044 |
|
–80 |
3,88 |
1,61 |
0,10 |
0,002 |
0,050 |
0,060 |
0,04 |
0,020 |
|
0,040 |
|
–70 |
3,72 |
1,50 |
0,12 |
0,003 |
0,096 |
0,056 |
0,03 |
0,010 |
|
0,054 |
|
+24 |
3,56 |
1,70 |
0,18 |
0,004 |
0,160 |
0,057 |
0,02 |
0,020 |
|
0,038 |
|
– |
3,40 |
1,60 |
0,09 |
0,004 |
0,050 |
0,050 |
0,02 |
0,020 |
|
0,039 |
|
–80 |
3,19 |
1,73 |
0,06 |
0,006 |
0,030 |
0,050 |
0,01 |
0,620 |
|
0,040 |
|
–74 |
3,23 |
1,65 |
0,06 |
0,007 |
0,030 |
0,050 |
0,02 |
1,240 |
|
0,040 |
|
–65 |
3,14 |
1,54 |
0,07 |
0,005 |
0,040 |
0,060 |
0,01 |
1,860 |
|
0,030 |
|
–48 |
3,27 |
1,76 |
0,08 |
0,008 |
0,050 |
0,060 |
0,01 |
2,490 |
|
0,040 |
|
–54 |
3,95 |
1,60 |
0,08 |
0,004 |
0,050 |
0,050 |
0,04 |
0,020 |
|
0,038 |
|
–80 |
4,01 |
1,46 |
0,03 |
0,006 |
0,060 |
0,060 |
0,35 |
0,020 |
|
0,027 |
|
–73 |
3,75 |
1,80 |
0,07 |
0,005 |
0,050 |
0,046 |
0,89 |
0,010 |
|
0,050 |
|
–50 |
3,85 |
1,61 |
0,07 |
0,006 |
0,050 |
0,060 |
1,56 |
0,017 |
|
0,038 |
|
–30 |
3,82 |
1,60 |
0,06 |
0,005 |
0,050 |
0,050 |
1,92 |
0,010 |
|
0,048 |
|
–22 |
Механические испытания проводили в интервале от +20 до –100 оС. Традиционные механические свойства при статическом нагружении – предел текучести σ0,2 , предел прочности σв , относительное удлинение
δ5 и относительное сужение ψ – определяли на цилиндрических об-
разцах диаметром 6 мм в соответствии с ГОСТ 1497–73. Трещиностойкость при статическом нагружении определяли в соответствии с [76] на образцах размером 15 х 30 х 140 мм. Записывали диаграмму «Нагрузка – деформация» иопределяли пределтрещиностойкости, Iс .
388
Таблица 7 . 1
Химический состав и критические температуры хрупкости Tê12ap исследованных сферографитных чугунов
C |
Si |
Mn |
S |
P |
Cr |
Cu |
Ni |
Mg |
TKa12p |
1,96 |
1,70 |
0,11 |
0,006 |
0,030 |
0,050 |
0,06 |
0,020 |
0,030 |
–48 |
2,83 |
1,55 |
0,13 |
0,006 |
0,030 |
0,050 |
0,04 |
0,030 |
0,040 |
–60 |
3.52 |
1,54 |
0,08 |
0,003 |
0,026 |
0,050 |
0,03 |
0,010 |
0,044 |
–65 |
4,01 |
1,60 |
0,10 |
0,004 |
0,050 |
0,050 |
0,02 |
0,010 |
0,036 |
–80 |
4,06 |
1,27 |
0,10 |
0,011 |
0,050 |
0,050 |
0,04 |
0,020 |
0,037 |
–93 |
3,97 |
1,64 |
0,10 |
0,002 |
0,050 |
0,050 |
0,02 |
0,020 |
0,036 |
–80 |
4,00 |
2,31 |
0,10 |
0,009 |
0,050 |
0,050 |
0,03 |
0,020 |
0, 046 |
–58 |
3,74 |
2,91 |
0,09 |
0,005 |
0,050 |
0,060 |
0,02 |
0,020 |
0,044 |
–10 |
3,70 |
3,75 |
0,13 |
0,006 |
0,030 |
0,054 |
0,05 |
0,020 |
0,028 |
– |
3,68 |
1,52 |
0,07 |
0,003 |
0,016 |
0,054 |
0,03 |
0,010 |
0,044 |
–80 |
3,88 |
1,61 |
0,10 |
0,002 |
0,050 |
0,060 |
0,04 |
0,020 |
0,040 |
–70 |
3,72 |
1,50 |
0,12 |
0,003 |
0,096 |
0,056 |
0,03 |
0,010 |
0,054 |
+24 |
3,56 |
1,70 |
0,18 |
0,004 |
0,160 |
0,057 |
0,02 |
0,020 |
0,038 |
– |
3,40 |
1,60 |
0,09 |
0,004 |
0,050 |
0,050 |
0,02 |
0,020 |
0,039 |
–80 |
3,19 |
1,73 |
0,06 |
0,006 |
0,030 |
0,050 |
0,01 |
0,620 |
0,040 |
–74 |
3,23 |
1,65 |
0,06 |
0,007 |
0,030 |
0,050 |
0,02 |
1,240 |
0,040 |
–65 |
3,14 |
1,54 |
0,07 |
0,005 |
0,040 |
0,060 |
0,01 |
1,860 |
0,030 |
–48 |
3,27 |
1,76 |
0,08 |
0,008 |
0,050 |
0,060 |
0,01 |
2,490 |
0,040 |
–54 |
3,95 |
1,60 |
0,08 |
0,004 |
0,050 |
0,050 |
0,04 |
0,020 |
0,038 |
–80 |
4,01 |
1,46 |
0,03 |
0,006 |
0,060 |
0,060 |
0,35 |
0,020 |
0,027 |
–73 |
3,75 |
1,80 |
0,07 |
0,005 |
0,050 |
0,046 |
0,89 |
0,010 |
0,050 |
–50 |
3,85 |
1,61 |
0,07 |
0,006 |
0,050 |
0,060 |
1,56 |
0,017 |
0,038 |
–30 |
3,82 |
1,60 |
0,06 |
0,005 |
0,050 |
0,050 |
1,92 |
0,010 |
0,048 |
–22 |
Механические испытания проводили в интервале от +20 до –100 оС. Традиционные механические свойства при статическом нагружении – предел текучести σ0,2 , предел прочности σâ , относительное удлинение
δ5 и относительное сужение ψ – определяли на цилиндрических об-
разцах диаметром 6 мм в соответствии с ГОСТ 1497–73. Трещиностойкость при статическом нагружении определяли в соответствии с [76] на образцах размером 15 х 30 х 140 мм. Записывали диаграмму «Нагрузка – деформация» и определяли предел трещиностойкости, Iñ .
388
Исследование трещиностойкости чугунов при динамическом нагружении проводили по методу Шарпи на образцах размером 10 х 11 х 55 мм; усталостную трещину выращивали из V-образного надреза. Определяли работу, затраченную на развитие трещины, ар. С помощью диаграммы «Нагрузка – деформация», через значения
Pmaxä , рассчитывали предел трещиностойкости, Iñä .
На основании критериального значения ар = 12 Дж/см2 определяли критическую температуру Òê12àð (см. табл. 7.1). Для того чтобы облегчить рассмотрение графического материала, на соответствующих графиках зависимости σâ , ψ, Iñ и Iñä от температуры даны только
для минимального и максимального содержания исследованных легирующих элементов.
Влияние углерода. На рис. 7.1 показано влияние углерода и температуры испытания на σâ , ψ, Iñ и Iñä . Из рис. 7.1, а видно, что
прочность материала с понижением температуры испытания повышается, при этом несколько более интенсивно с увеличением содержания углерода. Относительное сужение постепенно уменьшается (рис. 7.1, б). Благоприятное влияние углерод оказывает на силовые
характеристики трещиностойкости Iс и Iñä при отрицательных тем-
пературах (рис. 7.1, в, г).
Это естественно, поскольку эти две характеристики при сохранении хорошей пластичности определяются прочностью материала, которая, как было отмечено, с понижением температуры устойчиво растет. Увеличение содержания углерода оказывает благоприятное влияние на динамическую трещиностойкость ар высокопрочных ферритных чугунов (рис. 7.2), что со своей стороны ведет к снижению критической темпе-
ратуры хрупкости Òê12àð (рис. 7.3). Этот важный и очень полезный для
практики результат зависит от двух причин. Первая связана с тем обстоятельством, что повышение содержания углерода увеличивает число включений благоприятной сферической формы. При своем движении трещина непрерывно встречает эти, по существу, сферические пустоты, которые ее затупляют и таким образом снижают концентрацию напряжений перед ее фронтом. Трещина, в известном смысле, останавливается, встречая на своем пути такие включения-пустоты, и каждый раз, чтобы продолжить свое движение, ей необходимо снова принять свою
389